Top 1.9 Conveyor Rollers Manufacturers Reviewed
Conveyor rollers are a pivotal component in the automation and smooth operation of numerous industrial processes. These rollers facilitate the easy and efficient transport of goods across manufacturing floors, warehouses, and distribution centers, reducing the need for manual labor and enhancing workflow efficiency. This blog post specifically focuses on 1.9 conveyor rollers, which are widely recognized for their versatility and suitability in various applications. These rollers are particularly known for their optimal balance of size and strength, making them a preferred choice in industries looking to improve their material handling systems. We will explore the features, applications, and customization options of these essential industrial tools.
Key Features of 1.9 Conveyor Rollers
The 1.9 conveyor rollers are designed to provide a balance of efficiency, durability, and versatility in industrial conveyor systems. These rollers are essential for facilitating the smooth and efficient movement of goods, particularly in automated handling setups. Below, we explore the standard dimensions, specifications, and the materials used in manufacturing these rollers, emphasizing how these features contribute to their robust performance and reliability in various industrial settings.
Standard Dimensions and Specifications
The dimensional attributes and specifications of 1.9 conveyor rollers are engineered to meet the diverse needs of industry operations, ranging from light to medium load applications.
- Diameter: The 1.9-inch diameter is crucial for optimal load distribution, making it ideal for medium-weight materials and ensuring efficient operation.
- Length Options: These rollers are offered in various lengths to match different conveyor widths and configurations, providing flexibility in system design.
- Axle Size: Typically featuring a 7/16″ hex axle, these rollers are designed for easy integration and sturdy support within conveyor frames.
- Bearing Types: Available with non-precision or precision bearings to cater to different speed and load requirements, enhancing operational flexibility.
- Load Capacity: Designed to support substantial loads, often several hundred pounds per roller, suitable for a broad spectrum of industrial uses.
- Tube Material: Constructed primarily from steel, the tubes ensure durability and resistance to structural bending under load.
- Tube Thickness: The 16 gauge tube walls strike a balance between weight and structural integrity.
- Finish Options: Finish options include galvanized, painted, or powder-coated surfaces to meet various environmental and aesthetic needs.
Materials and Benefits
The choice of materials for manufacturing 1.9 conveyor rollers, particularly galvanized steel, plays a pivotal role in their longevity and performance in tough industrial environments.
- Galvanized Steel: This material is selected for its excellent resistance to rust and corrosion, which significantly extends the roller’s lifespan even in harsh conditions.
- High Durability: Galvanized steel withstands extreme environmental conditions, including high temperatures and exposure to chemicals.
- Low Maintenance: The durable finish of galvanized steel minimizes the need for frequent maintenance, reducing operational downtime.
- Cost-Effective: Galvanized steel offers a high-performance yet economical solution for conveyor systems, balancing cost and quality.
- Non-Marking: Ideal for environments where maintaining the integrity of conveyed materials is critical, as it prevents scuff marks and debris accumulation.
- Smooth Operation: The smooth finish reduces friction and operational noise, contributing to a more pleasant and efficient workplace.
- Environmentally Friendly: The recyclability of galvanized steel aligns with sustainable practices by reducing waste and resource consumption.
- Versatility: These rollers are adaptable to a variety of industrial applications, demonstrating their utility across multiple sectors.
- Ease of Customization: While standard finishes are typically adequate, galvanized steel can be customized with additional treatments to meet specific requirements, enhancing its applicability.
This detailed exploration of the key features and benefits of 1.9 conveyor rollers underscores their critical role in modern industrial systems, providing the reliability and adaptability needed to meet the demands of diverse operational environments.
Applications and Uses of 1.9 Conveyor Rollers
1.9 conveyor rollers are versatile components crucial for the automation of various industrial processes. Their design and specifications make them suitable for a broad range of applications, enhancing efficiency and productivity in numerous settings. Here we explore the diverse industrial applications and the unique advantages these rollers offer.
Diverse Industrial Settings
1.9 conveyor rollers are employed across various sectors, demonstrating their adaptability and critical role in different industrial environments.
- Warehousing: Used extensively in the warehousing sector to facilitate the movement of boxes and pallets, streamlining inventory management and order fulfillment processes.
- Food and Beverage: In the food and beverage industry, these rollers are crucial for moving products through processing areas, especially in packaging and sorting operations.
- Pharmaceuticals: Essential for the delicate handling of pharmaceutical products, where precision and contamination prevention are paramount.
- Automotive Manufacturing: Supports the assembly line in automotive manufacturing, where parts need to be moved efficiently between different stations.
- Electronics: Used in the electronics industry to transport delicate components safely within clean rooms or assembly areas.
- Agriculture: Facilitates the transport of agricultural products and supplies in processing plants, helping in sorting and packaging tasks.
- Textile Manufacturing: Conveys fabric rolls, finished garments, and other materials through various stages of the textile production process.
- Recycling Facilities: Efficient in moving recyclable materials through sorting and processing stages, helping manage different types of waste effectively.
Specific Applications in Warehouses, Manufacturing Plants, and Distribution Centers
The robustness and reliability of 1.9 conveyor rollers make them ideal for specific tasks in large-scale industrial operations.
- Bulk Material Handling: Handles large volumes of raw materials in manufacturing plants, reducing the need for manual labor.
- Finished Product Assembly Lines: Moves assembled products through finishing processes like inspection and packaging.
- Order Picking Systems: Integrates into automated order picking systems in distribution centers to speed up the sorting and dispatch process.
- Loading and Unloading Zones: Utilized in loading docks to expedite the process of loading and unloading goods, enhancing turnaround times.
- Cross-Docking Operations: Supports cross-docking in logistics hubs, where quick transfer of goods from incoming to outgoing transport is crucial.
- Feed Lines: Feeds materials into production machines in manufacturing plants, maintaining a constant supply without interruptions.
Advantages for Handling Heavy Loads and Long Conveyor Systems
The structural integrity and design efficiency of 1.9 conveyor rollers offer significant advantages, particularly in handling heavy loads and extending over long conveyor systems.
- Load Distribution: Their optimal diameter helps distribute the weight of heavy loads evenly, reducing wear and tear on the system.
- System Longevity: Enhances the longevity of conveyor systems by minimizing stress on other components, leading to reduced maintenance costs and downtime.
- High Efficiency: Capable of moving heavy and bulky items efficiently, increasing throughput in industrial settings.
- Versatile Integration: Easily integrates with both powered and non-powered conveyor sections, offering flexibility in system design.
- Stability: Provides greater stability for items in transit, especially important in high-speed or long-distance conveyor systems.
- Reduced Energy Consumption: Their efficient operation can lead to lower energy consumption compared to other conveyor types.
- Customization: Available in various materials and finishes, these rollers can be customized to handle specific types of loads or environmental conditions.
- Scalability: Suitable for expansion or reconfiguration of existing systems, adapting easily to increased production demands.
- Cost-Effective: Offers a cost-effective solution for complex systems, reducing the overall investment in machinery and equipment.
Through this detailed exploration, it is evident that 1.9 conveyor rollers are fundamental in enhancing operational efficiency across a wide range of industries. Their specific advantages in handling heavy loads and adapting to long conveyor systems make them an indispensable tool in modern industrial applications.
Customization Options for 1.9 Conveyor Rollers
The flexibility in customizing 1.9 conveyor rollers is essential for adapting to the diverse needs of various industries. Customization can dramatically enhance the functionality and efficiency of conveyor systems, making them more suited to specific operational requirements. This section explores the various customization options available for 1.9 conveyor rollers.
Explore Custom Options Available
Customization allows 1.9 conveyor rollers to be precisely tailored to meet specific operational demands, optimizing performance in unique environments.
- Adjustable Roller Lengths: Rollers can be cut to exact lengths required for specific conveyor setups, ensuring a perfect fit within existing systems.
- Multiple Material Choices: Beyond galvanized steel, rollers are available in stainless steel, aluminum, or even thermoplastics for specific environmental conditions or weight requirements.
- Variety in Roller Diameter: While the standard diameter is 1.9 inches, slight variations can be manufactured to handle different load sizes or types.
- Surface Treatments: Options include coatings like Teflon for reduced friction, rubber for increased grip, or corrosion-resistant finishes for harsh environments.
- Bearing Options: Choose from sealed bearings for dusty environments, precision bearings for high-speed applications, or grease-free bearings for food processing areas.
- Shaft Configurations: Shafts can be spring loaded, fixed, or even threaded to suit different mounting requirements within conveyor systems.
- Color Coding: Rollers can be color-coded based on their place or purpose in the production line, aiding in quick visual identification.
- High-Impact Designs: For heavy-duty applications, rollers can be reinforced with thicker walls or designed for higher load capacities.
Custom Lengths, Materials, and Bearing Types
Tailoring the physical dimensions, materials, and bearings of 1.9 conveyor rollers to match specific industrial needs enhances their application scope and longevity.
- Length Precision: Custom lengths allow seamless integration into specialized machinery or compact spaces where standard sizes would not fit.
- Material Suitability: Selection of materials based on their reaction to environmental factors like moisture, temperature, or chemical exposure ensures long-term durability.
- Bearing Durability: Custom bearings can be designed to handle higher loads or speeds, extending the life of the rollers and reducing maintenance needs.
- Weight Considerations: Lighter materials such as aluminum can be used where roller weight is a concern, whereas heavier steels can be used for added strength and stability.
- Environmental Compatibility: Materials and finishes can be chosen based on the roller’s operating environment to prevent degradation and ensure safety.
- Specialized Bearings: Bearings tailored for specific tasks, such as high-precision or low-noise bearings, optimize the roller’s performance in critical applications.
How Customization Enhances Functionality and Efficiency
Customizing 1.9 conveyor rollers directly contributes to increased operational efficiency and functionality by addressing specific needs and challenges.
- Enhanced Productivity: Customized lengths and widths can lead to more efficient layouts, optimizing the flow of materials and reducing processing times.
- Reduced Wear and Tear: By selecting appropriate materials and bearings, the rollers can be made more resistant to the specific stresses they will face, decreasing the frequency of replacements.
- Improved Load Handling: Custom designs can handle specific weight distributions more effectively, preventing bottlenecks and improving overall system reliability.
- Increased System Longevity: Tailored materials and protective finishes can significantly extend the life of conveyor systems by reducing environmental impact.
- Greater Flexibility in Design: Customization allows for innovative system designs that can dynamically adapt to changing manufacturing processes or product lines.
- Optimized Material Flow: Custom surface treatments or roller types can minimize product damage during handling, enhancing quality control.
- Energy Efficiency: Properly configured rollers can reduce the power required to move goods, lowering energy costs.
- Quick Adaptation to New Technologies: As production technologies evolve, custom rollers can be designed to integrate seamlessly with new equipment.
- Safety Improvements: Custom features like non-slip surfaces or noise-reduction treatments can create a safer workplace.
Customization of 1.9 conveyor rollers not only enhances their practical application but also leads to significant improvements in efficiency, adaptability, and performance, directly impacting the productivity and operational success of industries.
Buying Guide for 1.9 Conveyor Rollers
When it comes to optimizing your industrial operations, selecting the right 1.9 conveyor rollers is crucial. This buying guide is designed to help you understand the key factors to consider and provide tips on choosing the most suitable manufacturer for your needs, ensuring you get the best performance and value from your 1.9 conveyor rollers.
Factors to Consider When Purchasing 1.9 Conveyor Rollers
Choosing the right conveyor rollers involves several critical considerations that can impact their efficiency and suitability for your specific application.
- Load Capacity: Ensure the rollers can support the weight of the materials they will carry. Overloading can cause premature wear and failure.
- Operating Environment: Consider the environmental conditions where the rollers will be used. Factors like temperature, humidity, and exposure to chemicals or corrosives can affect material choice.
- Roller Length: The length of the roller should be suitable for the width of the conveyors and the size of the products being transported.
- Material Compatibility: Choose a roller material that is compatible with the products on the conveyor to avoid contamination or damage.
- Speed Requirements: The rollers must be capable of handling the operational speed of the conveyor without compromising stability or efficiency.
- Durability: Assess the durability of the rollers, especially in demanding industrial environments, to ensure long service life and reduced maintenance.
- Ease of Maintenance: Consider how easy it is to perform maintenance on the rollers. Quick and easy access can significantly reduce downtime.
- Energy Efficiency: Some rollers are designed to reduce energy consumption by minimizing friction and resistance, which can be a cost-saving feature.
- Customization Options: Check if customization is available to meet specific requirements, such as special coatings or dimensions.
Tips on Selecting the Right Manufacturer and Understanding Product Specifications
Selecting the right manufacturer is just as important as the technical specifications of the conveyor rollers themselves.
- Industry Reputation: Look for manufacturers with a strong reputation in the industry for quality and reliability.
- Product Quality: Assess the quality of the products through reviews, testimonials, or by requesting samples.
- Technical Support: Ensure the manufacturer offers excellent technical support and customer service, which can be crucial for addressing any issues.
- Compliance with Standards: Check that the products meet relevant industry standards and regulations, which can affect safety and compatibility.
- Manufacturing Capabilities: Consider the manufacturer’s production capabilities to ensure they can handle your volume needs and offer timely deliveries.
- Warranty and Service Agreements: Look for favorable warranty terms and service agreements that protect your investment.
- Product Range: A manufacturer with a broad product range can offer more options and flexibility in fulfilling your specific needs.
- Innovation and R&D: Manufacturers that invest in research and development may provide more advanced and efficient solutions.
- Cost-Effectiveness: While not always the primary concern, evaluating the cost relative to the product features and longevity is important.
By considering these factors and tips, you can make an informed decision when purchasing 1.9 conveyor rollers, ensuring they are perfectly suited for your operational needs and contribute effectively to your production line’s efficiency and reliability.
Heavy Duty and Specialty Rollers: Features and Applications of 1.9 Conveyor Rollers
The 1.9 conveyor rollers are engineered to meet the needs of both standard and extreme industrial applications. This section focuses on heavy-duty versions designed for harsh environments, as well as specialty rollers tailored for unique operational demands. We will explore their distinct features and discuss their suitability for specific industrial operations.
Heavy Duty Versions of 1.9 Rollers for Extreme Conditions
Heavy duty 1.9 conveyor rollers are built to withstand the toughest conditions in industrial settings, ensuring reliability where standard rollers might fail.
- Enhanced Material Strength: Constructed from high-grade steel or reinforced composites to endure higher loads and more abrasive conditions.
- Thicker Walls: Roller tubes feature thicker walls to resist deformation and wear in demanding environments.
- Sealed Bearings: Equipped with sealed bearings to prevent ingress of dust, debris, and corrosive elements, which helps maintain functionality over time.
- High Impact Resistance: Capable of absorbing sudden shocks and impacts, which are common in heavy-duty material handling.
- Temperature Resilience: Designed to operate under extreme temperatures, both high and low, without loss of performance.
- Corrosion Resistance: Coated with materials like zinc or epoxy that provide additional resistance to rust and corrosion.
- Greater Load Capacity: Engineered to support heavier weights without compromising speed or efficiency, essential for heavy manufacturing processes.
Features of Specialty Rollers Like Small Diameter and Long Rollers
Specialty 1.9 conveyor rollers are adapted to serve specific functional needs beyond standard applications, including those that require small diameters and extended lengths.
- Small Diameter Rollers: Ideal for handling smaller items or fitting into tight spaces where larger rollers would not be practical.
- Extended Length Rollers: These rollers can span wider areas without requiring intermediate supports, reducing system complexity and maintenance.
- Flexible Designs: Available in a variety of configurations to address unique transport challenges, such as curved paths or inclines.
- Lightweight Options: Made from materials like aluminum, which reduce overall weight for applications sensitive to load.
- Customizable Surface Treatments: Options like non-stick coatings or textured surfaces to handle unique products like glass or delicate electronics.
- Precision Bearings: For applications requiring very precise movements and speed control, especially in automated or robotic systems.
- Adaptable Mounting Options: Designed with versatile mounting features to integrate easily with existing systems or specialized machinery.
Suitability of These Rollers for Specific Industrial Operations
The versatility and robust construction of 1.9 conveyor rollers make them suitable for a range of specific industrial applications.
- Mining and Quarrying: Heavy-duty rollers are essential for moving large volumes of rock and ore.
- Automotive Assembly: Specialty rollers facilitate the smooth transportation of car parts along assembly lines.
- Food Processing: Small diameter rollers are used to handle delicate food products, maintaining hygiene and preventing damage.
- Pharmaceutical Manufacturing: Precision rollers ensure accurate positioning in environments where contamination control is critical.
- Packaging Industries: Long rollers support the extended conveyance paths needed in large packaging facilities.
- Aerospace: High-strength rollers capable of supporting the substantial weight of aerospace components.
- Logistics and Distribution: Flexible roller designs adapt to the varied package sizes and weights typical in distribution centers.
The design and customization of 1.9 conveyor rollers ensure that they meet the rigorous demands of various industrial sectors, proving essential in maintaining efficiency and durability in challenging operational contexts.
Replacement and Maintenance of 1.9 Conveyor Rollers
Ensuring the proper maintenance and timely replacement of 1.9 conveyor rollers is crucial for maintaining operational efficiency and preventing downtime in industrial settings. This section provides comprehensive guidelines on when and how to replace these rollers, offers maintenance tips to extend their lifespan, and underscores the importance of regular inspections and part replacements.
Guidelines on When and How to Replace 1.9 Conveyor Rollers
Knowing when and how to replace 1.9 conveyor rollers is key to keeping your conveyor system running smoothly and efficiently.
- Visual Inspection: Regularly inspect rollers for signs of wear, such as cracks, deformation, or significant accumulation of debris.
- Auditory Cues: Listen for unusual noises such as grinding or squeaking, which indicate bearing failures or misalignments.
- Operational Performance: Replace rollers if you notice sluggish conveyor movement or uneven roller spinning, which can affect product handling.
- Routine Schedule: Follow a routine replacement schedule based on manufacturer recommendations and past usage patterns.
- Post-Incident Replacement: Immediately replace rollers that have sustained damage from operational incidents to prevent further system damage.
- Preventative Replacement: Proactively replace rollers in critical areas of the conveyor system before major failures occur.
- Upgrade Considerations: Replace older rollers with newer, more efficient models as part of system upgrades.
- Installation Procedure: Ensure replacements are performed by trained personnel, using the correct tools and following safety protocols.
Maintenance Tips to Extend the Lifespan of 1.9 Conveyor Rollers
Proper maintenance is crucial in extending the operational lifespan of 1.9 conveyor rollers.
- Regular Cleaning: Keep rollers clean from dust, grime, and product residue to prevent buildup that can impair function.
- Lubrication: Adequately lubricate bearings according to the manufacturer’s specifications to ensure smooth operation and prevent wear.
- Alignment Checks: Regularly check and adjust the alignment of the rollers to avoid uneven wear and tear.
- Load Distribution: Ensure that loads are evenly distributed across the conveyor to prevent excessive stress on individual rollers.
- Environmental Controls: Maintain environmental conditions that are conducive to preserving the integrity of the rollers, such as humidity and temperature control.
- Protective Coatings: Apply protective coatings to resist corrosion and abrasion, especially in harsh working environments.
- Spare Parts: Keep a stock of spare parts for quick replacements to minimize downtime.
- Professional Assessments: Schedule periodic assessments with professional maintenance teams for expert care and advice.
Importance of Regular Inspections and Part Replacements
Regular inspections and timely replacements of parts are vital to the safe and efficient operation of conveyor systems using 1.9 conveyor rollers.
- Safety: Regular inspections help identify potential hazards, preventing accidents and ensuring the safety of operational personnel.
- Efficiency: Inspections ensure all parts of the conveyor are working optimally, maintaining overall system efficiency.
- Cost Savings: Early detection of issues can lead to cost savings by preventing more severe damage and expensive repairs.
- Lifespan Extension: Regular part replacements as needed contribute to the overall lifespan of the conveyor system.
- Compliance: Ensure compliance with industry standards and safety regulations through up-to-date maintenance practices.
- System Reliability: Enhance the reliability of the conveyor system with consistent performance and reduced unexpected failures.
- Performance Optimization: Regular maintenance optimizes the performance of each roller, ensuring smooth and consistent material handling.
By following these comprehensive guidelines, maintenance tips, and recognizing the importance of regular inspections and replacements, businesses can ensure the long-term reliability and efficiency of their 1.9 conveyor roller systems.
List of Top Manufacturers and Suppliers of 1.9 Conveyor Rollers
When selecting 1.9 conveyor rollers, it is crucial to choose from reputable manufacturers and suppliers who can guarantee high-quality products and reliable service. This section provides an overview of leading manufacturers known for their excellence in producing 1.9 conveyor rollers and outlines what to consider when choosing a supplier.
Overview of Reputable Manufacturers of 1.9 Conveyor Rollers
The market offers a variety of manufacturers known for their high standards and consistent quality in producing 1.9 conveyor rollers.
- Ultimation Industries: Renowned for its broad range of conveyor solutions, including customized 1.9 rollers that cater to specific industry needs.
- Hytrol Conveyor Company: A leader in the conveyor system market, Hytrol offers innovative 1.9 rollers known for their durability and efficiency.
- Interroll Group: Globally recognized for their modular conveyor systems, Interroll provides robust 1.9 rollers suitable for various applications.
- Ashland Conveyor Products: Specializes in a comprehensive lineup of conveyor rollers, including 1.9 rollers that are versatile and economically priced.
- Conveyor Rollers by LEWCO, Inc.: Offers a range of conveyor rollers, including heavy-duty 1.9 options designed for tough industrial environments.
- Precision Pulley & Idler: Known for precision-engineered conveyor components, their 1.9 rollers are highly regarded for performance and reliability.
- Rexnord Industries: Offers a diverse range of conveyor solutions, including 1.9 rollers that excel in various operational conditions.
- Omni Metalcraft Corp.: Delivers customized 1.9 conveyor rollers that can be tailored to meet specific industrial requirements, emphasizing flexibility and innovation.
What to Look for in a Supplier
Choosing the right supplier for 1.9 conveyor rollers involves considering several key factors to ensure you receive the best products and services tailored to your operational needs.
- Certifications: Ensure the supplier has relevant industry certifications (like ISO 9001) that attest to their quality management and product standards.
- Customer Service: A supplier with a reputation for excellent customer service, including prompt responses and supportive after-sales service, is crucial.
- Product Range: Look for suppliers offering a broad range of products, which indicates their capability to provide various options and solutions.
- Technical Expertise: Suppliers with in-depth technical knowledge can offer valuable advice and customized solutions that meet specific operational challenges.
- Quality Assurance: Check for quality assurance processes in place to ensure the rollers meet stringent quality standards.
- Delivery and Logistics: Consider their ability to meet delivery timelines and handle logistics efficiently, which is essential for maintaining your production schedules.
- Innovative Capabilities: Opt for suppliers who invest in research and development to stay ahead with the latest technological advancements in conveyor systems.
- Financial Stability: Financially stable suppliers are likely to be reliable long-term partners, ensuring continuous supply and support.
- Environmental and Social Responsibility: Suppliers who practice environmental and social responsibility reflect a commitment to sustainable and ethical business practices.
By carefully evaluating these aspects, you can select a supplier that not only meets your needs for 1.9 conveyor rollers but also aligns with your company’s operational standards and ethical considerations, ensuring a beneficial and enduring partnership.
FAQs about 1.9 Conveyor Rollers
The standard size of a conveyor roller can vary widely depending on the specific application and industry requirements. However, common diameters for conveyor rollers typically range from about 1.9 inches to 3.5 inches. The length of the rollers can also vary significantly but is usually tailored to fit the width of the conveyor system where the roller is to be installed. For instance, roller lengths may extend from several inches to over a foot to match the conveyor’s width which could be anywhere from 12 inches to over 36 inches. It’s essential for users to refer to specific product specifications or consult with manufacturers to determine the most appropriate size of rollers for their particular conveyor system, as the “standard” size can differ based on factors like load capacity, type of material being handled, and the environment of operation.
Various types of rollers are used in conveyor systems, each designed to meet different industrial needs. The most commonly used rollers include gravity rollers, which rely on gravity to move items across the conveyor; drive rollers, which are powered by motors and are essential in powered conveyor systems; and impact rollers, which are placed at points where materials are loaded onto the conveyor, absorbing shock and reducing damage to both the conveyor belt and the material. Other specialized rollers include brake rollers, which control the speed of moving items on the conveyor, and taper rollers, which are designed for curves and help maintain the alignment of the items. Selecting the right type of roller depends on factors like the load weight, the speed of operation, the properties of the material being conveyed, and environmental conditions.
Conveyor rollers are measured based on their diameter and length. The diameter of the roller is typically measured across the middle of the roller, using a caliper or tape measure. This measurement is critical as it affects the roller’s ability to support the conveyor belt and the materials being transported. The length of the conveyor roller, often referred to as the “between frame” or “BF” measurement, is taken from the inside faces of the conveyor frame. This measurement determines how long the roller needs to be to fit correctly between the conveyor’s side frames and is crucial for the proper installation and function of the roller. When ordering new rollers or replacing old ones, it is important to ensure these measurements are accurate to prevent issues with roller installation and conveyor operation.
The distance between rollers in a conveyor, also known as roller pitch, is the measurement from the center of one roller to the center of the next. This distance can greatly affect the conveyor’s ability to smoothly and efficiently transport materials. If the pitch is too large, smaller items may sag or get stuck between rollers. Conversely, a very small pitch can increase the cost of the conveyor system without significant benefits for certain applications. The optimal roller pitch is determined based on the size and weight of the items being transported, the type of roller, and the specific requirements of the conveyor system. For example, lighter items and those that are significantly larger than the roller diameter typically require a closer roller pitch to ensure stability and reduce the risk of items tipping or getting damaged.
Last Updated on August 1, 2024 by Jordan Smith
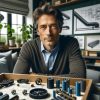
Jordan Smith, a seasoned professional with over 20 years of experience in the conveyor system industry. Jordan’s expertise lies in providing comprehensive solutions for conveyor rollers, belts, and accessories, catering to a wide range of industrial needs. From initial design and configuration to installation and meticulous troubleshooting, Jordan is adept at handling all aspects of conveyor system management. Whether you’re looking to upgrade your production line with efficient conveyor belts, require custom conveyor rollers for specific operations, or need expert advice on selecting the right conveyor accessories for your facility, Jordan is your reliable consultant. For any inquiries or assistance with conveyor system optimization, Jordan is available to share his wealth of knowledge and experience. Feel free to reach out at any time for professional guidance on all matters related to conveyor rollers, belts, and accessories.