Heavy Duty Options in 12 Roller Conveyor Models
A roller conveyor is an essential piece of equipment used in various industries to facilitate the easy movement and handling of goods. These conveyors consist of rollers mounted in a frame and are used in applications ranging from warehousing and distribution to packaging and manufacturing. The versatility of roller conveyors allows them to handle items of various sizes and weights, making them indispensable in production lines and assembly areas. Among the various sizes available, the 12 roller conveyor stands out as a popular choice due to its suitability for a wide range of applications. Its twelve-inch width offers ample space for handling standard-sized packages while maintaining a compact footprint, ideal for integrating into existing systems or for use in areas where space is at a premium. This size strikes a perfect balance, providing robust support and versatility without consuming excessive space.
Types of 12 Roller Conveyor
Roller conveyors are a pivotal component in material handling sectors, with the 12 roller conveyor being a widely recognized size due to its adaptability and efficiency. This size is particularly effective across a variety of settings, enhancing productivity and operational workflows. Below are four distinct types of 12 roller conveyors, each serving unique industry needs with specific characteristics:
Gravity Roller Conveyors
Gravity roller conveyors operate without an external power source, utilizing the force of gravity to move items along. Here’s how they stand out:
- Design Simplicity: These conveyors consist of a series of rollers mounted within a frame.
- Cost-Effective: With no need for power, they are cheaper to install and maintain.
- Ease of Installation: Simple setup means they can be readily integrated into existing systems.
- Versatility in Usage: Ideal for handling items of varying sizes and weights.
- Energy Efficiency: They consume no energy, making them environmentally friendly.
- Quiet Operation: Operates more quietly compared to powered options.
- Low Maintenance: Fewer moving parts reduce the need for regular maintenance.
- Safety Features: Typically equipped with manual stops and starts for safety.
Powered Roller Conveyors
Powered roller conveyors are equipped with motors, making them suitable for handling heavier loads over longer distances.
- Enhanced Productivity: Motors enable consistent and efficient movement of goods.
- Adjustable Speed: Speed can be controlled, allowing for a customizable flow of materials.
- Increased Load Capacity: Designed to handle heavier and more robust items.
- Longer Conveying Distances: Capable of transporting items over greater distances without manual intervention.
- Integration with Systems: Easily integrates with automated systems for synchronized operations.
- Diverse Applications: Suitable for a wide range of industrial applications.
- Reliability: Provides a more consistent operation compared to gravity conveyors.
- Sophisticated Controls: Often includes sensors and controllers to manage the flow of goods.
Heavy Duty Roller Conveyors
Heavy duty roller conveyors are built to withstand rigorous industrial environments and heavy loads.
- Robust Construction: Constructed with stronger materials to handle increased weights.
- Enhanced Durability: Designed to last longer under tough conditions.
- Higher Load Bearing: Capable of supporting substantially heavier products.
- Resistance to Wear: Components are made to resist wear from abrasive materials.
- Stability: Greater stability to handle uneven and heavy loads.
- Customizable Designs: Often customized to meet specific industrial requirements.
- Application Specific: Commonly used in manufacturing and heavy machinery industries.
- Efficient Handling: Facilitates the movement of heavy goods with minimal labor.
Small and Specialty Roller Conveyors
Small and specialty roller conveyors are designed for specific tasks where space and sensitivity are critical.
- Compact Design: Ideal for installation in limited spaces.
- Specialized Handling: Used for delicate or precision-required tasks.
- Flexibility: Easily reconfigured for temporary or changing setups.
- Lightweight Materials: Constructed with lightweight materials for easy maneuverability.
- Customizable Features: Can be tailored with various rollers to suit unique needs.
- Modular: Components can be added or removed as required.
- Sensitive Product Handling: Ensures careful handling of sensitive materials.
- Versatile Applications: Suitable for industries like electronics or pharmaceuticals where precision is crucial.
Each type of 12 roller conveyor is engineered to meet specific operational demands, ensuring that businesses can select the most suitable conveyor system for their logistic needs.
Key Features of the 12 Roller Conveyor
The 12 roller conveyor is a staple in many industries, recognized for its robust construction and versatility. This size of conveyor comes with specific features that make it suitable for a wide range of applications, from light distribution to heavy manufacturing. Below are ten key features that highlight the functionality and adaptability of the 12 roller conveyor:
- Roller Material and Design: Typically made from steel or aluminum, offering durability and corrosion resistance. The choice of material affects the conveyor’s strength and suitability for different environments. Roller diameters can vary, impacting the types of materials that can be efficiently conveyed.
- Roller Table Configurations: Available in straight, curved, and inclined configurations, allowing for customized layouts to navigate around obstacles and optimize workspace utilization.
- Load Capacity: Designed to handle varying weights, from lightweight packages to heavy bulk materials. The structure and material of the rollers determine the maximum load capacity, making it crucial to choose the right conveyor for the intended cargo.
- Adjustable Speed Settings: Many 12 roller conveyors come with variable speed settings, enabling them to accommodate different production line speeds and improve process control.
- Ease of Integration: These conveyors are designed to integrate seamlessly with other conveyor systems and automated processes, enhancing efficiency and connectivity across operations.
- Energy Efficiency: Depending on the model, 12 roller conveyors can be highly energy-efficient, particularly models that utilize gravity or minimal power assistance to move items.
- Maintenance Requirements: The design and quality of materials influence the maintenance needs. Conveyors with sealed bearings and high-quality rollers, for instance, require less frequent maintenance.
- Customization Options: Options for customization include roller spacing, width adjustments, and side rails, allowing for a tailored solution to meet specific industry needs.
- Safety Features: Safety guards, emergency stops, and other protective features are crucial, particularly in models handling heavy or hazardous materials.
- Durability and Longevity: The construction quality, material choices, and design specifics like powder coating for rust prevention contribute to the overall durability and longevity of the conveyor.
These features collectively make the 12 roller conveyor a versatile and essential tool in many sectors, capable of adapting to various operational demands while ensuring safety and efficiency.
Benefits of Using a 12 Roller Conveyor
The 12 roller conveyor is a versatile and efficient solution for a variety of industrial and commercial settings, offering significant operational advantages. Here is an expanded look at the benefits of using this type of conveyor:
- Efficiency in Operations: The 12 roller conveyor enhances operational efficiency by automating the movement of goods. This automation minimizes the need for manual handling, reduces transit time within facilities, and increases throughput. Faster and more consistent material flow leads to quicker order fulfillment and improved overall productivity.
- Versatility: This conveyor is highly adaptable and finds use in diverse industries such as automotive, pharmaceutical, electronics, food and beverage, and more. Its ability to handle different sizes and weights of products makes it an indispensable tool across various manufacturing and distribution contexts.
- Customization Options: A key advantage of the 12 roller conveyor is its adaptability through customization. Facilities can modify aspects such as roller diameter, width, material, and spacing to meet specific needs. This flexibility allows the conveyor to handle a broader range of products or adapt to unique logistical challenges.
- Cost-Effectiveness: By automating the transport of goods, 12 roller conveyors significantly reduce labor costs and dependency. They also minimize handling which can reduce product damage and waste, translating into cost savings over time.
- Ease of Installation: These conveyors are engineered for ease of installation, allowing quick setup without extensive modifications to existing systems. Their modular design enables businesses to add or reconfigure as needed with minimal disruption.
- Space Optimization: The design of the 12 roller conveyor maximizes the use of vertical and horizontal space, crucial in facilities where floor space is at a premium. Configurations such as spirals or flexible curves make it possible to navigate tight spaces and optimize facility layout.
- Improved Worker Safety: By reducing the need for manual lifting and carrying, these conveyors lower the risk of workplace injuries. This not only improves safety but can also reduce costs associated with worker compensation and lost workdays.
- Enhanced Product Handling: The gentle handling of products on roller conveyors minimizes damage during transportation. This is particularly beneficial for industries where product integrity is critical, such as electronics or glassware manufacturing.
- Scalability: As business needs evolve, the 12 roller conveyor can easily be expanded or reconfigured with additional sections. This scalability ensures that businesses can continue to meet increasing demands without the need for entirely new systems.
- Reliability: Built for durability and continuous use, the 12 roller conveyor is designed to withstand the rigors of industrial environments. Its reliable performance means less downtime and maintenance, ensuring operations run smoothly and efficiently.
The 12 roller conveyor not only streamlines operations but also supports a safe and adaptable working environment, making it a valuable investment for businesses aiming to optimize their production and distribution capabilities.
Considerations When Choosing a 12 Roller Conveyor
When deciding on a 12 roller conveyor for your operational needs, there are several factors to consider to ensure you select the most suitable system. Here are ten key considerations:
- Application Needs: Assess the specific needs of your application, including the types of materials to be conveyed and the necessary conveyor speed. Ensure the 12 roller conveyor meets these operational requirements.
- Pricing Factors: The cost of a 12 roller conveyor can vary based on material quality, design complexity, and additional features like motorization or controls. Common pricing factors include the length of the conveyor, the type of rollers used, and the degree of customization required.
- Rental Options: Renting a 12 roller conveyor may be beneficial for short-term needs or if you wish to avoid the capital expense of purchasing. Rental can also be a good option to test different models before committing to a purchase.
- Environment Compatibility: Consider the environment in which the conveyor will operate. Factors such as exposure to harsh chemicals, extreme temperatures, or wet conditions can influence the choice of materials and design specifications.
- Load Capacity: It’s essential to choose a conveyor that can handle your expected load weight without risk of breakdown. Verify the maximum load capacity of the 12 roller conveyor to ensure it aligns with your needs.
- Space Constraints: Measure the available space in your facility to ensure the conveyor will fit without requiring major modifications to your existing setup.
- Maintenance Requirements: Understand the maintenance needs of the conveyor. Conveyors with simpler designs and fewer moving parts, like gravity conveyors, typically require less maintenance compared to more complex systems like powered conveyors.
- Expandability and Modularity: Consider whether the conveyor system needs to be expandable or modular. This allows for adjustments and expansions as your business grows or as operational needs change.
- Energy Efficiency: If choosing a powered model, consider the energy efficiency of the system. More efficient conveyors can reduce operational costs over time.
- Supplier Reliability: Evaluate the reliability of the supplier or manufacturer. Look for companies with good reputations for quality, customer service, and after-sales support.
Each of these considerations plays a critical role in ensuring that the chosen 12 roller conveyor will meet the specific needs of your business, providing a balance of functionality, cost-efficiency, and reliability.
Where to Buy or Rent a 12 Roller Conveyor
Choosing where to buy or rent a 12 roller conveyor is a significant decision that can impact your operation’s efficiency and cost-effectiveness. Here are detailed suggestions for sources to purchase and companies that offer rental services:
Sources for Purchase
When looking to purchase a 12 roller conveyor, whether new or used, consider the following sources:
- Manufacturers’ Websites:
Direct purchases from manufacturers ensure you receive a product that comes with full warranties and the potential for customization according to specific needs. - Industrial Equipment Distributors:
These distributors typically have partnerships with multiple manufacturers, offering a diverse selection of products along with expert advice based on your requirements. - Online Marketplaces:
Websites such as Alibaba, eBay, and Amazon provide a platform to find a wide array of both new and used conveyors from global sellers, often with customer reviews to guide your decision. - Local Industrial Machinery Dealers:
Local dealers provide the advantage of nearby customer service and the option to inspect machinery in person before making a purchase. - Trade Shows and Industrial Fairs:
Attending these events allows you to directly interact with manufacturers, view demonstrations, and negotiate pricing or terms on the spot. - Refurbished Equipment Specialists:
These businesses offer professionally restored equipment that meets original factory specifications at a lower cost than new models. - Factory Outlets:
Factory outlets may offer discounted prices on conveyors that are overstocked, discontinued, or cosmetically imperfect but fully functional. - Direct Sales from Other Businesses:
Buying directly from businesses that are upgrading their equipment can offer significant savings and first-hand usage history. - Specialist Conveyor Resellers:
Resellers can provide valuable insights into the selection of the right conveyor for your needs, often with added services like installation and maintenance.
Rental Services
For those who need a 12 roller conveyor temporarily or want to avoid the capital expense of buying, consider these rental options:
- General Equipment Rental Companies:
Major rental providers such as United Rentals and Sunbelt Rentals offer extensive inventories and the flexibility to rent for any duration. - Specialized Conveyor Rental Businesses:
These businesses focus specifically on conveyor systems, providing a depth of expertise and comprehensive support for your particular application. - Manufacturer Rental Programs:
Some manufacturers offer direct rental options which can include the latest models and comprehensive support directly from the source. - Industrial Equipment Leasing Firms:
Leasing may be an attractive option for longer-term needs, offering lower monthly payments and potential tax benefits. - Construction Equipment Suppliers:
These suppliers cater to the construction industry but also typically have conveyors that are rugged and suitable for industrial applications. - Online Rental Marketplaces:
These platforms connect you with a variety of rental options, enabling price and service comparison at a glance. - Local Industrial Supply Stores:
Provides an accessible and quick solution for short-term conveyor needs with the added convenience of local support. - Peer-to-Peer Rental Platforms:
This newer rental option allows businesses to rent equipment directly from each other, potentially lowering costs and increasing rental availability.
These extended descriptions and reformatted points should help in making a well-informed decision whether buying or renting a 12 roller conveyor, catering to various business scales and operational needs.
Last Updated on May 22, 2024 by Jordan Smith
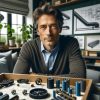
Jordan Smith, a seasoned professional with over 20 years of experience in the conveyor system industry. Jordan’s expertise lies in providing comprehensive solutions for conveyor rollers, belts, and accessories, catering to a wide range of industrial needs. From initial design and configuration to installation and meticulous troubleshooting, Jordan is adept at handling all aspects of conveyor system management. Whether you’re looking to upgrade your production line with efficient conveyor belts, require custom conveyor rollers for specific operations, or need expert advice on selecting the right conveyor accessories for your facility, Jordan is your reliable consultant. For any inquiries or assistance with conveyor system optimization, Jordan is available to share his wealth of knowledge and experience. Feel free to reach out at any time for professional guidance on all matters related to conveyor rollers, belts, and accessories.