24 Inch Conveyor Belts: Application Scenario
Conveyor belts are essential components in numerous industries, providing efficient material handling and transportation solutions. They streamline operations in sectors such as manufacturing, mining, agriculture, and logistics by moving materials seamlessly from one point to another. Among the various sizes available, the 24 inch conveyor belt stands out due to its versatility and suitability for a wide range of applications. This blog will delve into the specifics of the 24 inch conveyor belt, exploring its characteristics, types, applications, and benefits. By understanding these aspects, businesses can make informed decisions to optimize their material handling processes and improve overall productivity.
What is a 24 Inch Conveyor Belt?
A 24 inch conveyor belt is a material handling solution that features a belt width of 24 inches, making it an ideal choice for various industrial applications where moderate to large items need to be transported efficiently. Conveyor belts are a crucial component in many production and transportation processes, ensuring the smooth and continuous movement of materials.
Definition and Characteristics of a 24-Inch Wide Conveyor Belt
A 24 inch conveyor belt is designed to transport goods and materials across a fixed path, driven by pulleys or rollers. Its 24-inch width offers ample space for handling a diverse range of items, from bulk materials to packaged goods.
- Versatility: The 24 inch conveyor belt is suitable for a wide variety of industries, including manufacturing, food processing, mining, and logistics. Its width allows it to handle both lightweight and heavy materials efficiently.
- Durability: Made from robust materials, these belts are designed to withstand harsh industrial environments and heavy usage. The belts are resistant to wear, tear, and abrasion, ensuring a long service life.
- Flexibility: The 24 inch conveyor belt can be customized in terms of length, thickness, and surface texture to meet specific requirements. This flexibility makes it adaptable to different operational needs.
- Efficiency: With a wider surface area, the 24 inch conveyor belt can move a larger volume of materials at a time, improving the efficiency of material handling processes.
- Safety: Many 24 inch conveyor belts come with features such as anti-slip surfaces and edge guards to enhance safety during operation. These features help prevent accidents and ensure the smooth transportation of goods.
Different Types of Materials Used
Conveyor belts can be made from a variety of materials, each offering unique benefits and suitable for different applications. The 24 inch conveyor belt is no exception:
- Rubber: Rubber conveyor belts are widely used due to their excellent durability and flexibility. They are suitable for transporting heavy and abrasive materials such as minerals, ores, and rocks. Rubber belts are also resistant to impact and can operate in extreme temperatures.
- PVC (Polyvinyl Chloride): PVC conveyor belts are known for their strength and resistance to chemicals, oils, and fats. They are commonly used in the food industry, packaging, and warehousing. PVC belts offer a smooth surface and are easy to clean, making them ideal for hygienic applications.
- Polyurethane (PU): PU conveyor belts provide superior wear resistance and flexibility. They are suitable for applications requiring frequent bending and flexing, such as in the textile and garment industries. PU belts are also resistant to cutting and tearing.
- Nylon: Nylon conveyor belts offer high conveyor belt tensile strength and excellent elasticity. They are lightweight and can handle high-speed operations, making them ideal for industries like airport baggage handling and paper manufacturing. Nylon belts also have good resistance to abrasion and fatigue.
- Fabric: Fabric conveyor belts, often reinforced with polyester or cotton, provide a cost-effective solution for light to medium-duty applications. They are commonly used in agriculture, logistics, and light manufacturing. Fabric belts offer good flexibility and can be customized with various coatings for specific needs.
Each of these materials has its own set of advantages, making the 24 inch conveyor belt a versatile and essential tool in various industries.
Understanding the definition and characteristics of a 24 inch conveyor belt, along with the different types of materials used in its construction, is crucial for selecting the right belt for your specific application. Whether you need a durable rubber belt for heavy-duty mining operations or a hygienic PVC belt for food processing, the 24 inch conveyor belt offers a wide range of options to meet your needs. By choosing the appropriate material and design, you can ensure efficient and safe material handling, enhancing the overall productivity of your operations.
Types of 24 Inch Conveyor Belts
When selecting a 24 inch conveyor belt, it’s important to consider the material of the belt as it significantly impacts the belt’s performance, durability, and suitability for specific applications. Here, we will discuss the various types of materials used for 24 inch conveyor belts, focusing on rubber and synthetic materials like PVC.
Rubber Conveyor Belts: Features and Benefits
Rubber conveyor belts are among the most commonly used types in various industries due to their robustness and versatility. Here are five key features and benefits of rubber 24 inch conveyor belts:
- High Durability: Rubber conveyor belts are highly durable, making them suitable for heavy-duty applications. They can withstand significant wear and tear, making them ideal for industries such as mining, where they handle abrasive materials like coal and ore.
- Heat Resistance: Many rubber conveyor belts are designed to resist high temperatures, which is essential in industries such as metal processing and cement manufacturing where materials can be extremely hot.
- Flexibility: Rubber belts offer excellent flexibility, allowing them to bend around pulleys and conform to various conveyor system designs. This flexibility helps in maintaining a continuous flow of materials.
- Shock Absorption: Rubber belts provide good shock absorption, which is beneficial in applications where heavy or sharp objects are transported. This feature helps in protecting both the conveyor system and the materials being moved.
- Weather Resistance: Rubber belts can resist a wide range of environmental conditions, including extreme temperatures, moisture, and chemicals. This makes them suitable for outdoor applications and harsh industrial environments.
Examples of Rubber Conveyor Belts:
- General Purpose Rubber Belt: Ideal for transporting bulk materials in industries like agriculture and manufacturing.
- Heat Resistant Rubber Belt: Used in industries dealing with hot materials such as foundries and steel plants.
- Oil Resistant Rubber Belt: Suitable for transporting oily or greasy materials in recycling and automotive industries.
- Fire Resistant Rubber Belt: Designed for environments where fire safety is crucial, such as underground mining.
- Abrasion Resistant Rubber Belt: Perfect for handling sharp and heavy materials like rocks and minerals.
PVC and Other Synthetic Materials: Comparison of Performance and Applications
Synthetic materials like PVC (Polyvinyl Chloride), PU (Polyurethane), and other composites are also widely used in conveyor belts. They offer unique advantages that cater to specific industrial needs. Below is a comparison of different synthetic materials used in 24 inch conveyor belts:
Examples of Synthetic Conveyor Belts:
- PVC Conveyor Belts:
- Smooth Surface PVC Belt: Ideal for food processing and packaging where cleanliness is crucial.
- Rough Top PVC Belt: Used in applications where items need to be held in place during transportation, such as in parcel handling.
- Polyurethane (PU) Conveyor Belts:
- PU Timing Belt: Commonly used in precise material handling applications in the textile and garment industries.
- PU Coated Conveyor Belt: Suitable for applications requiring high wear resistance and flexibility.
- Nylon Conveyor Belts:
- Nylon Flat Belt: Utilized in high-speed operations like paper manufacturing and airport baggage systems.
- Nylon Reinforced Belt: Offers extra strength for heavy-duty applications.
- Polyester Conveyor Belts:
- Polyester Fabric Belt: Used in agriculture and light manufacturing due to its strength and low stretch.
- Polyester Mesh Belt: Ideal for drying processes where airflow is required.
- Silicone Conveyor Belts:
- Silicone Coated Belt: Perfect for baking and food processing where non-stick properties are essential.
- Heat Resistant Silicone Belt: Used in high-temperature environments like the pharmaceutical industry.
Choosing the right material for a 24 inch conveyor belt is critical for ensuring optimal performance and longevity. Rubber belts offer excellent durability, heat resistance, and flexibility, making them suitable for heavy-duty applications. On the other hand, synthetic materials like PVC, PU, nylon, polyester, and silicone provide specialized benefits such as chemical resistance, high flexibility, and suitability for specific industries. By understanding the features and benefits of each type of material, you can select the most appropriate 24 inch conveyor belt for your specific needs, ensuring efficient and reliable material handling in your operations.
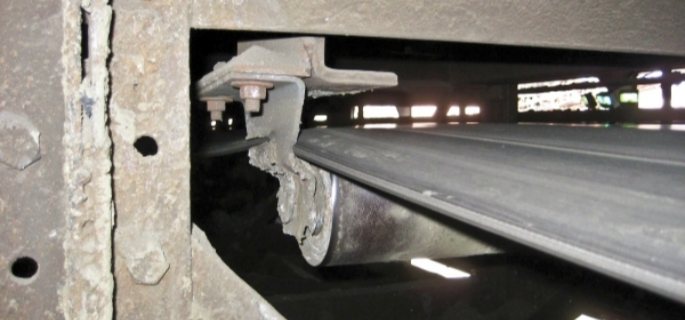
Applications of 24 Inch Conveyor Belts
The 24 inch conveyor belt is a versatile tool utilized across various industries due to its ability to handle a wide range of materials efficiently. This section will explore the common industries and scenarios where 24-inch belts are used and discuss special features like chevron and crescent tops that enhance material handling.
Common Industries and Scenarios Where 24-Inch Belts Are Used
Manufacturing Industry
- Assembly Lines: In manufacturing, 24 inch conveyor belts are commonly used on assembly lines for transporting components and finished products from one workstation to another. The width of the belt allows for handling a variety of items, from small parts to larger assemblies.
- Material Handling: These belts are essential for moving raw materials and finished goods within factories. They streamline operations, reduce manual handling, and increase productivity.
Mining Industry
- Material Transportation: In mining operations, 24 inch conveyor belts are used to transport extracted materials such as coal, ores, and minerals from the mining site to processing plants. Their robust construction allows them to handle heavy loads and harsh conditions.
- Crushing and Screening Plants: Conveyor belts are also used in crushing and screening plants to move materials between different stages of the processing line. The 24-inch width is ideal for handling large volumes of materials efficiently.
Food Processing Industry
- Food Production Lines: In food processing, 24 inch conveyor belts are used to transport ingredients and finished food products along production lines. The belts are often made from food-grade materials like PVC to ensure hygiene and safety.
- Packaging and Sorting: Conveyor belts are crucial in the packaging and sorting stages, where they move products to different packaging stations and sort them based on size, weight, or type.
Agriculture Industry
- Harvesting and Sorting: In agriculture, 24 inch conveyor belts are used to transport harvested crops from the field to sorting and packaging areas. They help in sorting crops based on size and quality, enhancing efficiency.
- Bulk Material Handling: Conveyor belts are used to handle bulk materials such as grains, seeds, and fertilizers. The wide surface area of the belt ensures that large quantities can be transported quickly and efficiently.
Logistics and Warehousing
- Sorting and Distribution: In logistics and warehousing, 24 inch conveyor belts are used to sort and distribute packages. They help in organizing packages by destination, size, or type, ensuring smooth operations.
- Loading and Unloading: Conveyor belts are also used in loading and unloading areas to move goods from trucks and containers to storage areas or vice versa. This reduces manual labor and speeds up the process.
Special Features for Material Handling
Chevron Top Conveyor Belts
- Design and Functionality: Chevron top conveyor belts feature a distinctive V-shaped pattern on the surface. This pattern provides excellent grip and prevents materials from slipping off the belt, especially when transporting goods at an incline.
- Applications: Chevron top belts are ideal for transporting loose or bulk materials such as sand, gravel, and agricultural products. They are commonly used in industries like agriculture, mining, and construction where materials need to be moved up steep inclines.
Crescent Top Conveyor Belts
- Design and Functionality: Crescent top conveyor belts have a pattern of crescent-shaped grooves on the surface. These grooves provide enhanced traction and prevent slippage, making them suitable for handling materials that are prone to rolling or slipping.
- Applications: Crescent top belts are used in industries such as packaging and food processing, where items like boxes, cartons, and packages need to be transported securely. The crescent pattern ensures that items remain stable during transportation.
Rough Top Conveyor Belts
- Design and Functionality: Rough top conveyor belts have a textured surface that provides additional grip. This texture is particularly useful for transporting packaged goods and boxes, preventing them from slipping or sliding.
- Applications: Rough top belts are commonly used in the logistics and warehousing industries. They are ideal for moving goods on inclines and declines, ensuring that items remain secure during the transportation process.
Flat Conveyor Belts
- Design and Functionality: Flat conveyor belts have a smooth surface, making them ideal for transporting items that require a flat and stable surface. They are versatile and can be used in a variety of applications.
- Applications: Flat belts are used in manufacturing, food processing, and packaging industries. They are suitable for transporting light to medium-weight items that do not require additional grip or traction.
Modular Conveyor Belts
- Design and Functionality: Modular conveyor belts systems are made up of interlocking plastic modules, allowing for easy customization and repair. They offer flexibility in design and can be adapted to fit different conveyor configurations.
- Applications: Modular belts are used in industries such as automotive, packaging, and food processing. They are ideal for applications that require frequent cleaning or where the conveyor path needs to be changed regularly.
The 24 inch conveyor belt is a versatile and essential tool in various industries, including manufacturing, mining, food processing, agriculture, logistics, and warehousing. Its ability to handle a wide range of materials and its adaptability to different operational needs make it a valuable asset in any material handling process. Special features like chevron and crescent tops enhance the functionality of these belts, ensuring efficient and secure transportation of materials. By understanding the applications and features of 24 inch conveyor belts, businesses can make informed decisions to optimize their material handling operations and improve overall productivity.
Sizing and Measurement Guide for 24 Inch Conveyor Belts
Accurate sizing and measurement are critical for ensuring the optimal performance and longevity of a 24 inch conveyor belt. This guide will detail how to measure a conveyor belt, how to measure a roll of a 24 inch conveyor belt efficiently, and the importance of accurate measurements for achieving the best results.
How to Measure a Conveyor Belt
Proper measurement of a conveyor belt involves determining its length, width, and thickness. Here are the steps to measure these dimensions accurately:
Length Measurement:
- Static Length Measurement: For a conveyor belt that is not installed, lay the belt flat on a smooth surface. Use a measuring tape to measure the distance from one end to the other, ensuring the tape is taut and straight. Record the measurement.
- Installed Length Measurement: If the belt is installed, mark a starting point on the belt with a piece of chalk. Rotate the belt until the marked point returns, measuring the distance traveled. This gives the total length of the belt loop.
Width Measurement:
- Measure the width of the conveyor belt from one edge to the other using a measuring tape or a ruler. Ensure the tape is perpendicular to the belt’s edges to get an accurate measurement. For a 24 inch conveyor belt, this measurement should be 24 inches.
Thickness Measurement:
- Use a caliper to measure the thickness of the conveyor belt. Place the caliper on a flat section of the belt and record the reading. Thickness is important for determining the belt’s strength and flexibility.
How to Measure a Roll of a 24 Inch Conveyor Belt Efficiently
Measuring a roll of a 24 inch conveyor belt requires a different approach. Here’s a step-by-step guide:
Determine the Diameter of the Roll:
- Use a measuring tape to measure the diameter of the rolled belt from one side to the other. Make sure to measure across the center of the roll for accuracy.
Calculate the Length of the Belt in the Roll:
- Use the formula (L = \pi \times D \times N), where (L) is the length of the belt, (D) is the diameter of the roll, and (N) is the number of turns in the roll. To find (N), count the number of layers in the roll and multiply by the number of turns per layer.
Check the Core Diameter:
- Measure the diameter of the roll’s core (the inner cylinder around which the belt is wound). This helps in calculating the actual length of the belt more accurately.
Account for Belt Thickness:
- Adjust your calculations based on the thickness of the belt. Thicker belts will have fewer layers per given diameter compared to thinner belts.
Double-Check Measurements:
- Double-check all measurements to ensure accuracy. Small errors in measurement can lead to significant discrepancies in the calculated length.
Importance of Accurate Measurements for Optimal Performance
Accurate measurements of a 24 inch conveyor belt are crucial for several reasons. Here are five examples of the importance of precise measurements:
Ensuring Proper Fit:
- Accurate measurements ensure that the conveyor belt fits properly within the conveyor system. A belt that is too short or too long can cause operational issues, leading to downtime and increased maintenance costs.
Enhancing Efficiency:
- A properly sized belt enhances the efficiency of material handling operations. It ensures smooth movement of materials, reducing the risk of jams, slippage, or misalignment.
Reducing Wear and Tear:
- Correctly measured belts reduce excessive wear and tear on both the belt and the conveyor system. This extends the life of the belt and minimizes the need for frequent replacements.
Optimizing Performance:
- Precise measurements contribute to the optimal performance of the conveyor system. They ensure that the belt operates at the correct tension and speed, improving overall productivity.
Cost Savings:
- Accurate belt measurements prevent unnecessary expenses related to purchasing the wrong size belt or dealing with system malfunctions. This leads to cost savings in both materials and labor.
Measuring a 24 inch conveyor belt accurately is essential for maintaining optimal performance and longevity. Whether measuring a belt that is laid flat, installed, or rolled, attention to detail in length, width, and thickness is crucial. Understanding how to efficiently measure a roll of a 24 inch conveyor belt also ensures that you have the correct length and can avoid operational issues. The importance of accurate measurements cannot be overstated, as they ensure proper fit, enhance efficiency, reduce wear and tear, optimize performance, and lead to significant cost savings. By following the guidelines outlined in this section, you can ensure that your 24 inch conveyor belt operates smoothly and effectively in your material handling processes.
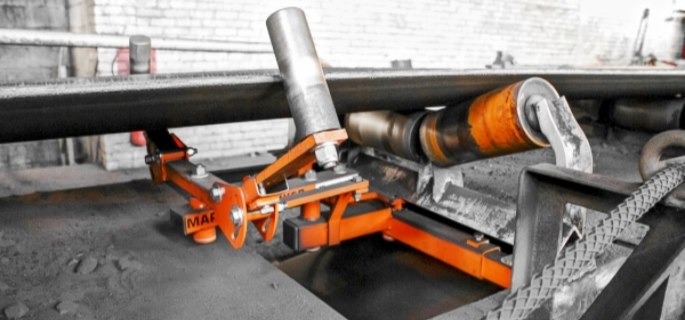
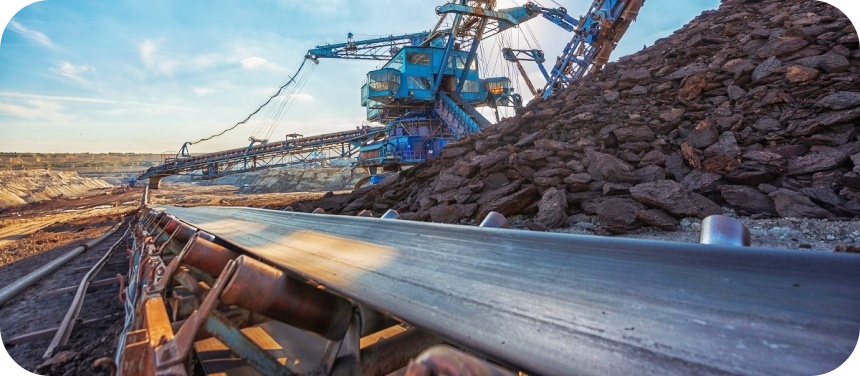
Available Variants and Their Specifications
When selecting a 24 inch conveyor belt, it’s essential to understand the various types available and their specific uses. 24 inch conveyor belt thickness typically ranging from 3 -15 mm, temperature range -20°C to +80°C,tensile strength100-630 N/mm. This section provides an in-depth look at different variants, including smooth top, chevron top, and crescent top conveyor belts. We will also discuss the importance of thickness and material options with specific gauges to help you choose the right belt for your application.
Smooth Top Conveyor Belts: Features and Specific Uses
Smooth top conveyor belts are among the most commonly used types due to their versatility and simplicity. They have a flat, smooth surface that allows for the easy movement of materials.
Low Friction Surface:
- Feature: The smooth surface reduces friction, allowing materials to glide easily over the belt.
- Use: Ideal for transporting packaged goods, boxes, and lightweight materials in industries such as warehousing and logistics.
Easy Cleaning:
- Feature: Smooth top belts are easy to clean and maintain, which is crucial for hygiene-sensitive industries.
- Use: Commonly used in the food processing and pharmaceutical industries, where cleanliness is paramount.
Versatility:
- Feature: These belts can handle a wide range of materials, making them suitable for various applications.
- Use: Employed in manufacturing plants for transporting components and finished products.
Cost-Effective:
- Feature: Smooth top belts are generally more affordable compared to specialty belts.
- Use: Preferred in budget-conscious operations that require reliable, basic material handling solutions.
Durability:
- Feature: Made from robust materials, smooth top belts can withstand regular wear and tear.
- Use: Used in light to medium-duty applications across different industries, including electronics and textiles.
Chevron Top and Crescent Top Conveyor Belts: Functionality and Industrial Application
Chevron top and crescent top conveyor belts are designed for specific industrial applications where enhanced grip and material handling are required.
Chevron Top Conveyor Belts
- Functionality:
- Design: Chevron top belts feature a V-shaped pattern that provides excellent grip, preventing materials from slipping off the belt.
- Material Handling: The raised pattern is particularly effective for transporting loose or bulk materials on inclines.
- Industrial Applications:
- Agriculture: Used for moving grains, seeds, and other bulk agricultural products up steep inclines.
- Mining: Ideal for transporting ores, rocks, and other mined materials in challenging environments.
- Construction: Suitable for moving construction materials such as sand and gravel.
Crescent Top Conveyor Belts
- Functionality:
- Design: Crescent top belts have a pattern of crescent-shaped grooves that provide enhanced traction and prevent slippage.
- Material Handling: These grooves offer superior grip, making them suitable for transporting items prone to rolling or slipping.
- Industrial Applications:
- Packaging: Used in packaging plants to transport boxes, cartons, and packages securely.
- Food Processing: Ideal for moving items that require stable transportation, such as bakery products.
- Logistics: Commonly used in distribution centers for sorting and transporting packages.
Guide to Thickness and Material Options with Specific Gauges
Choosing the right thickness and material for a 24 inch conveyor belt is crucial for ensuring its suitability for specific applications. Here is a guide to the available options:
Thickness Options:
- Light Duty: Typically 1-2 mm thick, suitable for lightweight materials and less demanding applications.
- Medium Duty: Ranges from 3-5 mm in thickness, ideal for general-purpose use in various industries.
- Heavy Duty: 6 mm and above, designed for heavy loads and harsh environments.
Material Options:
- Rubber: Durable and flexible, suitable for heavy-duty applications. Available in various thicknesses to handle different levels of wear and tear.
- PVC (Polyvinyl Chloride): Chemical-resistant and easy to clean, perfect for food processing and packaging industries. Comes in light to medium-duty thicknesses.
- PU (Polyurethane): Offers high flexibility and excellent wear resistance, ideal for textile and garment industries. Available in medium-duty thicknesses.
- Nylon: High tensile strength and elasticity, suitable for high-speed operations. Commonly used in airports and paper manufacturing, available in various thicknesses.
- Fabric: Reinforced with polyester or cotton for added strength, suitable for light to medium-duty applications. Fabric belts are flexible and can be coated for specific uses.
Specific Gauges:
- 1.5 mm: Light duty, used for lightweight packaging and food processing.
- 3 mm: Medium duty, suitable for general manufacturing and warehousing.
- 5 mm: Heavy duty, ideal for mining, construction, and bulk material handling.
- 6 mm: Extra heavy duty, used in the most demanding environments, such as mining and heavy manufacturing.
Understanding the different variants and specifications of a 24 inch conveyor belt is essential for selecting the right belt for your specific application. Smooth top belts offer versatility and ease of use, making them suitable for a wide range of industries. Chevron top and crescent top belts provide enhanced grip and material handling capabilities for more specialized applications. By considering the thickness and material options, you can ensure that your conveyor belt meets the demands of your operational environment, leading to improved efficiency and productivity.
24 Inch Conveyor Belt: Friction Surface
A 24-inch conveyor belt with a friction surface is designed for specific industrial applications where grip and resistance are crucial to maintaining product stability during transport. Here’s an overview of key aspects related to this type of conveyor belt:
Key Features
- Width: The belt is 24 inches wide, making it suitable for medium to large-scale material handling tasks.
- Friction Surface: The friction surface on the belt provides added grip, preventing slippage of items during conveyance. This is particularly important in operations involving inclines, declines, or high-speed movement where maintaining the position of items is critical.
- Material Composition:
- The belt is typically made of durable materials such as rubber, polyurethane, or PVC. These materials are chosen for their resilience, flexibility, and ability to withstand different environmental conditions.
- The friction surface may feature textured patterns, such as diamond or rough top, to enhance grip.
Applications:
- Inclined Conveying: Ideal for applications where materials need to be moved at an incline or decline, as the friction surface helps keep items in place.
- Packaging Lines: Ensures stability of packaged goods, reducing the risk of shifting or toppling.
- Agriculture: Used in the transport of bulk materials like grains or produce, where maintaining consistent movement without slippage is necessary.
Maintenance and Durability:
- Regular inspection of the friction surface is important to ensure it remains effective over time.
- The belt should be cleaned regularly to prevent the buildup of debris, which can reduce friction and lead to slippage.
Advantages
- Enhanced Grip: The friction surface minimizes product movement, leading to fewer errors in product placement and reduced material loss.
- Versatility: Suitable for a wide range of industries, from manufacturing to food processing.
- Durability: Designed to withstand heavy loads and harsh operating conditions.
Considerations
- Compatibility: Ensure the conveyor system is compatible with a friction surface belt, as the added grip might require adjustments in tensioning and drive mechanisms.
- Speed: The added friction may affect the speed at which materials can be conveyed, so adjustments may be necessary based on specific operational requirements.
This type of conveyor belt is an essential component in systems where maintaining product orientation and stability is critical to the success of the operation.
Buying Options: New and Used 24 Inch Conveyor Belts
When looking to purchase a 24 inch conveyor belt, it’s important to consider various factors such as where to buy, whether to opt for new or used belts, and how to inspect used belts to ensure they are in good condition. This section will guide you through these considerations, helping you make an informed decision.
Where to Find 24 Inch Conveyor Belts for Sale
Finding the right 24 inch conveyor belt involves exploring multiple sources to compare options and prices. Here are some common places to find conveyor belts for sale:
Manufacturers and Suppliers:
- Many companies specialize in the production and supply of conveyor belts. Purchasing directly from manufacturers ensures you get high-quality belts that meet your specifications. Some well-known suppliers include Fenner Dunlop, ContiTech, and Habasit.
Industrial Equipment Retailers:
- Retailers that sell industrial equipment often stock a variety of conveyor belts. These retailers may offer belts from different manufacturers, allowing you to compare products and choose the best one for your needs.
Online Marketplaces:
- Websites like Amazon, eBay, and Alibaba have extensive listings of new and used conveyor belts. These platforms provide a wide range of options and competitive pricing. However, it’s essential to verify the seller’s credibility before making a purchase.
Local Distributors:
- Local distributors and dealers of industrial equipment can be a reliable source for purchasing conveyor belts. They often provide personalized service and may offer installation and maintenance support.
Auction Sites and Liquidation Sales:
- Auction sites and liquidation sales can be a good source for used conveyor belts at lower prices. These sales often include surplus or discontinued stock from businesses that are closing down or upgrading their equipment.
Pros and Cons of Buying New Versus Used Conveyor Belts
Deciding between new and used 24 inch conveyor belts depends on various factors, including budget, application, and desired lifespan. Here are five examples of the pros and cons of each option:
- Pros:
- Warranty and Support: New belts typically come with a warranty and technical support from the manufacturer, providing peace of mind and assistance if issues arise.
- Latest Technology: New belts incorporate the latest materials and technology, ensuring optimal performance and efficiency.
- Customization: Purchasing new allows for customization to meet specific operational requirements, such as size, material, and features.
- Reliability: New belts are less likely to have wear and tear, ensuring consistent performance and reducing downtime.
- Compliance: New belts are manufactured to meet current industry standards and regulations, ensuring safety and compliance.
- Cons:
- Higher Cost: New conveyor belts are more expensive than used ones, which can be a significant investment for some businesses.
- Lead Time: There may be a longer lead time for manufacturing and delivery, especially for customized belts.
Used Conveyor Belts:
- Pros:
- Cost Savings: Used belts are generally cheaper, providing significant cost savings, especially for short-term projects or limited budgets.
- Immediate Availability: Used belts are often available immediately, reducing wait times compared to ordering new ones.
- Eco-Friendly: Buying used is a sustainable option, reducing waste and promoting the reuse of materials.
- Sufficient for Less Demanding Applications: Used belts can be a practical choice for applications that do not require the highest levels of performance or durability.
- Negotiable Prices: Prices for used belts can often be negotiated, potentially leading to further cost savings.
- Cons:
- Unknown Wear and Tear: Used belts may have hidden damage or wear that can lead to premature failure.
- Limited Warranty: Used belts may come with little to no warranty, increasing the risk if the belt fails.
- Potential for Reduced Performance: Older belts may not perform as efficiently as new ones, impacting productivity.
- Limited Customization: Options for used belts are limited to what is available, which may not meet specific needs.
- Higher Maintenance Costs: Used belts may require more frequent maintenance and repairs, leading to higher long-term costs.
Tips on Inspecting Used Conveyor Belts
When considering a used 24 inch conveyor belt, thorough inspection is crucial to ensure you are getting a quality product. Here are five tips for inspecting used conveyor belts:
Check for Surface Damage:
- Inspect the belt surface for cuts, tears, or gouges. Surface damage can weaken the belt and lead to premature failure.
Examine the Belt Edges:
- Look at the edges of the belt for fraying or cracking. Damaged edges can affect the belt’s tracking and lead to operational issues.
Assess the Splice:
- Check the splice (the joint where the belt ends are joined) for signs of weakness or separation. A faulty splice can cause the belt to break during operation.
Evaluate Belt Flexibility:
- Flex the belt to check for stiffness or brittleness, which can indicate aging or material degradation. A flexible belt is essential for smooth operation.
Review the Belt’s History:
- Ask the seller about the belt’s previous usage, including the types of materials it transported and the environment it operated in. This information can provide insights into the belt’s condition and expected lifespan.
Whether you choose to buy a new or used 24 inch conveyor belt, understanding the available options and conducting a thorough inspection is essential for making an informed decision. New belts offer reliability, customization, and the latest technology but come at a higher cost. Used belts provide significant cost savings and immediate availability but require careful inspection to ensure quality and performance. By considering these factors and following the inspection tips, you can select the right 24 inch conveyor belt that meets your operational needs and budget.
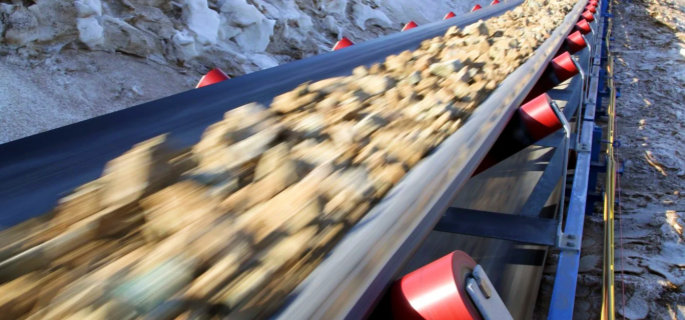
Pricing Insights for 24 Inch Conveyor Belts
Understanding the pricing of a 24 inch conveyor belt is crucial for budgeting and making informed purchasing decisions. Various factors influence the price of these conveyor belts, and there are strategies to get the best deals. This section will explore the key pricing factors and provide estimated price ranges along with tips for securing the best value.
Factors That Influence the Price of 24-Inch Wide Conveyor Belts
Several factors affect the cost of 24 inch conveyor belts. Here are five primary factors to consider:
Material Composition:
- Rubber: Rubber belts are generally more expensive due to their durability and resistance to harsh conditions. The cost can vary based on the type of rubber (e.g., natural, synthetic) and any special treatments (e.g., heat-resistant, oil-resistant).
- PVC: PVC belts tend to be less expensive than rubber belts. They are cost-effective for applications requiring chemical resistance and hygiene, such as food processing.
- Polyurethane (PU): PU belts are typically more expensive than PVC but offer superior flexibility and wear resistance, making them suitable for high-precision applications.
Belt Construction:
- Single Ply vs. Multi-Ply: Single ply belts are cheaper but may not offer the same strength and durability as multi-ply belts. Multi-ply belts, with two or more layers, provide additional support and longevity but at a higher cost.
- Special Features: Belts with special features like chevron or crescent tops, which provide enhanced grip and material handling capabilities, are more expensive than smooth top belts.
Thickness and Width:
- Thickness: Thicker belts are generally more expensive because they use more material and offer greater durability. The thickness required depends on the application and the weight of the materials being transported.
- Width: While we focus on 24 inch conveyor belts, belts wider than 24 inches can significantly increase in price due to the additional material and potential custom manufacturing requirements.
Customization and Special Orders:
- Customization: Customized belts tailored to specific needs, such as unique lengths, special materials, or added features, will be more expensive than standard, off-the-shelf options.
- Special Orders: Special orders, including non-standard widths or thicknesses, can also increase costs due to the additional manufacturing processes involved.
Market Conditions:
- Supply and Demand: Prices can fluctuate based on market conditions, including the availability of raw materials and overall demand for conveyor belts. High demand or limited supply can drive prices up.
- Economic Factors: Economic conditions, such as inflation, changes in currency exchange rates, and trade policies, can also impact prices.
Estimated Price Ranges and Tips for Getting the Best Deals
Understanding the price ranges and knowing how to secure the best deals can help you manage costs effectively. Here are some estimated price ranges and tips for purchasing 24 inch conveyor belts:
Estimated Price Ranges:
- Basic PVC Belts: $10 to $20 per foot. These are suitable for light-duty applications in food processing and packaging.
- Standard Rubber Belts: $20 to $50 per foot. These belts are used in general manufacturing and bulk material handling.
- Specialty Belts (e.g., Chevron, PU): $50 to $100+ per foot. These belts are designed for specific applications requiring enhanced durability, flexibility, or grip.
Tips for Getting the Best Deals:
- Buy in Bulk: Purchasing larger quantities can often result in discounts. Suppliers may offer reduced prices for bulk orders, lowering the overall cost per foot.
- Shop Around: Compare prices from multiple suppliers and manufacturers. Online marketplaces, local distributors, and direct purchases from manufacturers can offer varying prices and deals.
- Consider Used Belts: For applications that do not require brand-new belts, consider buying used conveyor belts. These can be significantly cheaper and still meet your operational needs.
- Negotiate: Don’t hesitate to negotiate prices with suppliers, especially if you’re making a large purchase. Many suppliers are willing to offer discounts to secure a sale.
- Stay Updated on Market Trends: Keep an eye on market trends and economic factors that might affect prices. Purchasing during off-peak times or when market conditions are favorable can save money.
The price of a 24 inch conveyor belt is influenced by various factors, including material composition, belt construction, thickness, width, customization, and market conditions. By understanding these factors, you can better estimate costs and plan your budget. Additionally, knowing the price ranges and applying strategies to get the best deals—such as buying in bulk, shopping around, considering used belts, negotiating prices, and staying informed on market trends—can help you secure the best value for your investment. Making informed decisions will ensure that you get a high-quality conveyor belt that meets your needs without exceeding your budget.
24 Inch Conveyor Belt: The Width of The Conveyor Belt
The width of a conveyor belt can vary widely depending on the specific application, the type of material being transported, and the design of the conveyor system. Common conveyor belt widths range from small, narrow belts of around 300 mm (12 inches) to much wider belts that can exceed 2,000 mm (79 inches) or more.
Here are some typical width ranges based on common applications:
- Small Conveyors (Light-Duty): 300 mm to 600 mm (12 inches to 24 inches)
- Medium Conveyors (General Use): 600 mm to 1,200 mm (24 inches to 48 inches)
- Large Conveyors (Heavy-Duty, Industrial): 1,200 mm to 2,000 mm (48 inches to 79 inches)
- Extra-Large Conveyors (Bulk Material Handling): 2,000 mm to 3,000 mm (79 inches to 118 inches) or more
The specific width required for your application will depend on factors like the size of the material, the desired throughput, and the physical constraints of the installation area.
24 Inch Conveyor Belt: Width Choosing
When choosing the width of a conveyor belt, several factors need to be considered to ensure the belt meets the operational needs and is efficient in its function. Here’s a guide to help with the decision-making process:
1. Material Characteristics
- Size of the Material: The width of the conveyor belt should accommodate the maximum particle size of the material being transported. Ideally, the belt width should be at least 3 times the size of the largest material particle to avoid spillage.
- Bulk Density: Heavier and bulkier materials may require wider belts to prevent overflow and ensure stable transport.
2. Capacity Requirements
- Throughput: Calculate the required capacity in terms of volume per hour or tonnage per hour. The belt width should be sufficient to handle the desired capacity without overloading.
- Speed of the Belt: The belt width is also related to the speed at which it operates. Higher speeds may necessitate wider belts to maintain stability and prevent material loss.
3. Conveyor Length and Inclination
- Length of Conveyor: Longer conveyors may require wider belts to minimize the risk of material spillage during transit.
- Incline Angle: If the conveyor is inclined, a wider belt might be needed to accommodate the material’s tendency to shift or slide.
4. Type of Conveyor
- Belt Type: Consider the type of conveyor belt being used (e.g., flat belt, cleated belt, etc.), as different designs may have varying width requirements.
- Conveyor Design: The overall design of the conveyor system, including support structures, should accommodate the belt width chosen.
5. Operational Conditions
- Environmental Factors: Dusty, wet, or corrosive environments may influence the choice of belt width, requiring additional width to handle potential environmental impacts.
- Maintenance Accessibility: Ensure the width allows for easy access for maintenance and cleaning without compromising safety.
6. Industry Standards and Safety Regulations
- Compliance: The belt width should comply with industry standards and regulations, particularly in industries like mining, food processing, and manufacturing, where safety is paramount.
- Safety Margins: Incorporate safety margins to account for unexpected surges in material volume or changes in operational conditions.
7. Cost Considerations
- Material Costs: Wider belts are more expensive due to the additional material required, so balance the width against budget constraints.
- Operational Efficiency: While wider belts may increase initial costs, they can improve operational efficiency by reducing the likelihood of spillage and downtime.
8. Future Expansion
- Scalability: Consider future operational needs. If there’s a possibility of increased production, opting for a slightly wider belt now might save costs in the long run.
By carefully considering these factors, you can choose a conveyor belt width that meets your specific needs and ensures efficient, safe, and cost-effective operation.
Maintenance and Care for 24 Inch Conveyor Belts
Proper maintenance and care of a 24 inch conveyor belt are essential for ensuring its longevity and optimal performance. Regular upkeep can prevent costly repairs and downtime, extending the life of the conveyor belt and enhancing its efficiency. This section provides basic maintenance tips and emphasizes the importance of regular checks and balance adjustments.
Basic Maintenance Tips to Prolong the Life of Conveyor Belts
Effective maintenance routines are crucial for the longevity of your 24 inch conveyor belt. Here are five essential tips to keep your conveyor belt in excellent condition:
Regular Cleaning:
- Tip: Clean the conveyor belt regularly to remove dirt, debris, and residues that can cause wear and tear.
- Explanation: Accumulated debris can lead to increased friction, causing the belt to wear out faster. Regular cleaning prevents buildup and maintains smooth operation.
Proper Lubrication:
- Tip: Lubricate moving parts, such as rollers and bearings, to reduce friction and wear.
- Explanation: Proper lubrication ensures that all moving parts operate smoothly, reducing the strain on the conveyor belt and preventing premature wear.
Inspect for Damage:
- Tip: Conduct routine inspections to check for signs of damage, such as cuts, tears, or frayed edges.
- Explanation: Early detection of damage allows for timely repairs, preventing minor issues from escalating into major problems that can cause belt failure.
Maintain Correct Tension:
- Tip: Ensure the conveyor belt is properly tensioned to avoid slippage or excessive strain.
- Explanation: Incorrect tension can lead to slippage, misalignment, and increased wear. Regularly adjusting the tension helps maintain optimal belt performance.
Align the Belt:
- Tip: Check and adjust the belt alignment to ensure it runs straight and true.
- Explanation: Misaligned belts can cause uneven wear and lead to operational issues. Proper alignment minimizes wear and tear, extending the belt’s life.
Importance of Regular Checks and Balance Adjustments
Regular checks and balance adjustments are vital for the efficient operation of a 24 inch conveyor belt. Here are five reasons why these practices are important:
Preventative Maintenance:
- Importance: Regular checks allow for the early detection of potential problems, enabling preventative maintenance.
- Example: Identifying a small tear early on allows for a simple patch repair, avoiding a complete belt replacement later.
Optimizing Performance:
- Importance: Regular adjustments ensure the conveyor belt operates at peak efficiency, reducing energy consumption and operational costs.
- Example: Adjusting the belt tension and alignment ensures smooth operation, preventing unnecessary strain on the motor and other components.
Safety Assurance:
- Importance: Regular inspections help identify and mitigate safety hazards, protecting workers and equipment.
- Example: Checking for loose or damaged parts can prevent accidents and injuries, ensuring a safe working environment.
Extending Belt Life:
- Importance: Consistent maintenance and adjustments prolong the life of the conveyor belt, reducing the frequency of replacements.
- Example: Regularly lubricating and cleaning the belt reduces wear, allowing it to function effectively for a longer period.
Reducing Downtime:
- Importance: Preventative maintenance minimizes unexpected breakdowns, reducing downtime and maintaining productivity.
- Example: Scheduling regular maintenance checks during planned downtime ensures that the conveyor system is always ready for operation.
Maintaining and caring for a 24 inch conveyor belt involves regular cleaning, proper lubrication, routine inspections for damage, maintaining correct tension, and ensuring proper alignment. These basic maintenance tips help prolong the life of the conveyor belt, enhance its performance, and reduce operational costs. Additionally, regular checks and balance adjustments are crucial for preventative maintenance, optimizing performance, ensuring safety, extending belt life, and reducing downtime. By implementing these practices, you can ensure that your 24 inch conveyor belt operates efficiently and reliably, providing long-term value for your investment.
Fill out this form for a detailed response and quote on our 24 Inch Conveyor Belts.
FAQs About 24 Inch Conveyor Belt
Conveyor belts come in various sizes to accommodate different industrial needs. However, the most commonly used sizes range from 18 to 72 inches in width. The standard size often depends on the application and industry. For instance, 24-inch conveyor belts are widely used in industries such as food processing, manufacturing, and logistics because they offer a good balance between handling capacity and versatility. The length of a conveyor belt can vary significantly, from a few meters to several kilometers, depending on the specific requirements of the operation. Standard conveyor belts can be custom-made to fit unique operational needs, ensuring they efficiently transport materials of various sizes and weights.
The term “M 24 conveyor belt” refers to a specific grade of rubber conveyor belt used in industrial applications. The “M” stands for “mining,” and “24” denotes the strength of the belt in terms of its tensile strength. An M 24 conveyor belt is known for its high tensile strength, typically around 24 Megapascals (MPa), making it suitable for heavy-duty applications such as mining, quarrying, and bulk material handling. These belts are designed to withstand harsh conditions, including abrasion, impact, and high loads. They are commonly made from durable materials like rubber and reinforced with layers of fabric or steel cords to enhance their strength and longevity.
The maximum length of a belt conveyor can vary widely depending on the design and intended use. In general, standard belt conveyors can be designed to run several hundred meters. However, with advanced engineering and technology, conveyors can extend much longer. For example, some mining and material handling operations utilize conveyor systems that stretch several kilometers. The longest belt conveyor system, which is located in the Western Sahara, stretches over 61 miles (98 kilometers). The length of a conveyor belt is often determined by the need to transport materials over long distances efficiently, reducing the reliance on trucks and other transportation methods, and improving operational efficiency.
The longest belt conveyor system in the world is located in the Western Sahara, running from the Bou Craa phosphate mine to the coastal port of El Aaiún. This conveyor belt stretches over an impressive 61 miles (98 kilometers). It is used to transport phosphate from the mining site to the port, where it is shipped worldwide. This system is a remarkable engineering achievement, showcasing the capability of conveyor belts to transport materials over vast distances efficiently. The conveyor operates continuously, moving thousands of tons of phosphate daily, significantly reducing the need for trucks and other transportation methods. This system not only exemplifies the efficiency of belt conveyors but also highlights their role in large-scale industrial operations.
There is no single “standard” length for conveyor belts, as they are typically custom-designed to meet the specific needs of the application. Conveyor belts can range in length from a few meters to several kilometers, depending on the industry and the material being transported. Shorter conveyor belts might be used in manufacturing facilities, while longer belts are common in mining and bulk material handling industries.
The longest conveyor belt in the world is located in the Western Sahara and is used to transport phosphate rock from the Bou Craa mine to the coastal city of El Aaiún. This conveyor belt stretches approximately 98 kilometers (61 miles) in length.
Last Updated on August 13, 2024 by Jordan Smith
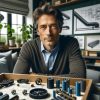
Jordan Smith, a seasoned professional with over 20 years of experience in the conveyor system industry. Jordan’s expertise lies in providing comprehensive solutions for conveyor rollers, belts, and accessories, catering to a wide range of industrial needs. From initial design and configuration to installation and meticulous troubleshooting, Jordan is adept at handling all aspects of conveyor system management. Whether you’re looking to upgrade your production line with efficient conveyor belts, require custom conveyor rollers for specific operations, or need expert advice on selecting the right conveyor accessories for your facility, Jordan is your reliable consultant. For any inquiries or assistance with conveyor system optimization, Jordan is available to share his wealth of knowledge and experience. Feel free to reach out at any time for professional guidance on all matters related to conveyor rollers, belts, and accessories.