Innovative Uses for 3 Conveyor Roller in Industry
Conveyor systems are essential for efficient material handling in various industries, facilitating the smooth movement of goods. Among the key components of these systems are conveyor rollers, which support and guide items along the conveyor path. The 3 conveyor roller, in particular, stands out due to its versatility and robustness. These rollers are integral to numerous industrial applications, from warehousing and shipping to assembly lines. With a standard 3-inch diameter, they provide a reliable solution for handling lightweight to moderately heavy packages. Their relevance lies in their ability to enhance operational efficiency, reduce manual labor, and streamline processes across diverse industrial settings.
What Is 3 Conveyor Roller
3 conveyor rollers are crucial components in the mechanized movement of goods within numerous industrial environments. They are specifically designed with a diameter of three inches, optimized for a balance between versatility and efficiency in handling various loads. Their applications range from lightweight parcel movement in distribution centers to handling materials in manufacturing settings. This section will explore the defining characteristics, materials used, and key specifications of these rollers, each under its respective subheading.
Definition and Basic Description
The fundamental role of 3 conveyor roller is to facilitate the smooth transit of goods across an automated system. These rollers are pivotal in reducing labor costs, enhancing speed, and improving the overall efficiency of industrial operations.
- Core Function: Serve as the primary surface for moving items at varying speeds across a conveyor system.
- Design: Cylindrical in shape, designed to rotate around a central axis to minimize friction.
- Versatility: Suitable for diverse industries, from automotive assembly lines to retail distribution centers.
- Ease of Installation: Typically designed for quick integration into existing conveyor systems.
- Maintenance: Engineered for low maintenance requirements with easy access to parts for quick repairs or replacements.
- Energy Efficiency: Often used in systems that capitalize on gravity, reducing energy consumption.
- Safety Features: Built with safety in mind to prevent workplace injuries associated with manual material handling.
- Customization: Available in various sizes and materials to suit specific industrial needs.
Common Materials Used
The materials chosen for 3 conveyor roller depend on their intended application, environmental conditions, and required durability. Each material offers distinct advantages and potential limitations.
- Plain Steel: The go-to for most industrial applications due to its strength and cost-effectiveness.
- Galvanized Steel: Best for environments prone to moisture or chemical exposure, preventing rust.
- Stainless Steel: Ideal for sterile environments such as food processing or pharmaceuticals due to its resistance to corrosion and ease of cleaning.
- Plastic Rollers: Selected for lightweight applications or when noise reduction is a priority.
- Rubber Coated: Chosen to prevent slippage and protect delicate items during transport.
- Aluminum Rollers: Used when weight is a critical factor, often in aerospace or electronic industries.
- Composite Rollers: Developed for specialized applications that require rollers to be robust yet lightweight.
- Polyurethane Covered Rollers: Favored in applications requiring a high degree of traction and durability.
Typical Dimensions and Specifications
The dimensions and specifications of 3 conveyor roller are designed to meet the diverse needs of various industrial sectors. These specifications ensure that the rollers can handle the required loads and operate smoothly under different conditions.
- Standard Diameter: Uniformly set at 3 inches to match industry standards for a wide range of machinery.
- Wall Thickness: Typically 11-gauge, which provides an optimal balance between durability and flexibility.
- Length Options: Available in various lengths to accommodate different widths of conveyor systems.
- Bearing Types: Commonly equipped with sealed bearings to prevent dust ingress and ensure longevity.
- Axle Configurations: Often designed with spring-loaded axles for ease of maintenance and replacement.
- Load Ratings: Specifically rated to handle weights typical for the size and spacing of the conveyor setup.
- Temperature Resilience: Capable of operating in extreme temperatures, both high and low, without degradation.
- Custom Features: Can include options like anti-static materials or special coatings to meet unique operational demands.
This comprehensive overview provides a clearer understanding of 3 conveyor roller, their design principles, material composition, and essential specifications, underlining their indispensable role in modern industrial operations.
Types of 3 Conveyor Roller
3 conveyor rollers come in various types, each designed to meet specific operational needs and environmental conditions. These rollers are critical components in many industrial applications, offering solutions that range from standard use to specialized functions. In this section, we will delve into three main types of 3 conveyor rollers: Standard 3 Conveyor Rollers, 3 Conveyor Rollers with Covers, and 3″ Diameter Steel Conveyor Rollers. Each type has unique features, benefits, and applications that make them suitable for different industrial scenarios.
Standard 3 Conveyor Rollers
Standard 3 conveyor rollers are the most commonly used type of rollers in industrial conveyor systems. They are designed to handle a wide range of products and are known for their durability and efficiency. These rollers are typically made from robust materials such as plain steel or galvanized steel, ensuring long-term performance in various environments.
Description and Uses:
- Widely used in warehousing, distribution centers, and assembly lines.
- Suitable for both powered and gravity-fed conveyor systems.
- Designed to transport lightweight to moderately heavy items.
- Can be used in permanent and temporary conveyor setups.
- Easily integrated into existing conveyor systems.
- Typically feature a smooth surface to reduce friction.
- Available in various lengths to fit different conveyor widths.
Load Rating and Capacity:
- Standard load capacity, typically around 272 lbs for common applications.
- Load rating depends on the spacing between rollers and the material used.
- Can support a variety of load weights with minimal pitch.
- Durable enough to handle continuous operation in busy industrial environments.
- Designed to distribute weight evenly across the conveyor.
- Compatible with different types of bearings to enhance load capacity.
- Can be customized to meet specific load requirements.
3 Conveyor Rollers with Covers
3 conveyor rollers with covers are specialized rollers that feature protective covers made from materials like polyurethane. These covers offer additional benefits, such as improved grip, reduced noise, and protection against harsh conditions. These rollers are ideal for applications where the conveyed items require extra care or where the operational environment is challenging.
Benefits of Polyurethane Roller Covers:
- Provide a non-slip surface to ensure items remain in place during transport.
- Reduce noise levels, making them ideal for quieter work environments.
- Protect both the roller and the conveyed items from damage.
- Extend the lifespan of the rollers by reducing wear and tear.
- Offer better handling of delicate or fragile items.
- Improve traction, especially in inclined or declined conveyor systems.
- Available in various thicknesses to suit different application needs.
Temperature Range and Application Scenarios:
- Suitable for a wide temperature range, typically from -80°F to 200°F.
- Ideal for environments with extreme temperature fluctuations.
- Used in food processing, pharmaceuticals, and other sterile environments.
- Beneficial in outdoor settings where weather conditions vary.
- Suitable for cleanroom applications due to their non-contaminating properties.
- Used in high-speed conveyor systems where stability is crucial.
- Can be tailored for specific industrial applications requiring high resilience.
3″ Diameter Steel Conveyor Rollers
3 diameter steel conveyor rollers are designed for heavy-duty applications where strength and durability are paramount. These rollers are made from high-quality steel, providing excellent load-bearing capabilities and longevity. They are equipped with advanced bearing and axle specifications to ensure smooth operation under demanding conditions.
Features of Steel Rollers:
- Made from high-strength steel to withstand heavy loads and harsh environments.
- Corrosion-resistant coatings available for enhanced durability.
- Can handle rough handling and frequent use without deformation.
- Suitable for high-temperature applications.
- Provide a smooth and consistent surface for efficient item movement.
- Low maintenance requirements due to robust construction.
- Available in various finishes to suit different industrial requirements.
Bearing and Axle Specifications:
- Equipped with ABEC-1 bearings for reliable performance and longevity.
- Bearings are grease-packed to ensure smooth and consistent operation.
- Axles are typically 1/2″ round, spring-loaded for easy installation and maintenance.
- Designed to handle significant axial and radial loads.
- Bearings housed in plastic or steel for added protection.
- Axle retention methods include spring-loaded or threaded options for secure fitting.
- Custom bearing configurations available to meet specific application needs.
Each type of 3 conveyor roller offers unique advantages and is designed to meet specific operational requirements. Understanding these differences can help in selecting the right roller for your conveyor system, ensuring optimal performance and efficiency.
Applications of 3 Conveyor Rollers
3 conveyor rollers are versatile components used in a wide range of industrial applications. Their robust construction and adaptability make them essential for improving efficiency and productivity in various sectors. Below are several real-world applications of 3 conveyor rollers, each showcasing their unique benefits and uses.
- Warehousing: 3 conveyor rollers are crucial in streamlining storage and retrieval processes. They facilitate the easy movement of goods within large warehouse spaces, reducing manual labor and increasing operational efficiency. These rollers are ideal for sorting and transporting items to different locations within the warehouse, ensuring a smooth and organized workflow.
- Shipping Departments: In shipping departments, 3 conveyor rollers enhance the handling and movement of packages. They help in the quick and efficient sorting of parcels, reducing processing times and improving throughput. This efficiency is vital for meeting tight shipping deadlines and maintaining customer satisfaction.
- Assembly Areas: 3 conveyor rollers play a significant role in assembly line operations by enhancing productivity. They enable the seamless transfer of components between different stages of the assembly process, ensuring that production lines operate smoothly and without interruptions. This application is particularly beneficial in automotive and electronics manufacturing.
- Temporary vs. Permanent Conveyor Lines: The flexibility of 3 conveyor roller makes them suitable for both temporary and permanent conveyor lines. They can be easily set up and dismantled, making them ideal for temporary projects or seasonal operations. Additionally, their durable construction ensures they can withstand continuous use in permanent installations.
- Packaging Industries: In packaging industries, 3 conveyor rollers assist in the efficient movement of products through various packaging stages. From filling and sealing to labeling and boxing, these rollers ensure a steady flow of goods, reducing bottlenecks and increasing overall productivity.
- Food Processing Plants: 3 conveyor rollers are also used in food processing plants where hygiene and efficiency are paramount. Stainless steel rollers, in particular, are favored for their corrosion resistance and ease of cleaning, helping maintain sanitary conditions while efficiently moving food products through different processing stages.
- Retail Distribution Centers: Retail distribution centers utilize 3 conveyor roller to handle a high volume of goods. They streamline the sorting and distribution process, ensuring that products are quickly and accurately dispatched to retail stores. This application is essential for maintaining inventory levels and meeting consumer demand.
- E-commerce Fulfillment Centers: With the rise of e-commerce, fulfillment centers rely heavily on 3 conveyor roller to manage the rapid movement and sorting of orders. These rollers help in organizing items for shipment, improving order accuracy, and speeding up delivery times, which are critical for customer satisfaction in the online shopping sector.
- Recycling Facilities: In recycling facilities, 3 conveyor rollers aid in the sorting and processing of recyclable materials. They facilitate the efficient transfer of items through various stages of the recycling process, from initial sorting to final processing, helping to improve the efficiency and effectiveness of recycling operations.
By understanding these diverse applications, it becomes clear how integral 3 conveyor rollers are to various industrial processes. Their ability to enhance productivity, streamline operations, and provide flexibility makes them a valuable asset in numerous sectors.
Buying Guide for 3 Conveyor Roller
When considering the purchase of 3 conveyor roller, it’s important to evaluate several factors to ensure you select the best option for your needs. This guide will help you navigate the decision-making process, covering the differences between new and used rollers, where to find 3 conveyor roller for sale, and the key dimensions and specifications to look for.
New vs. Used 3 Conveyor Rollers
Deciding between new and used 3 conveyor rollers can impact both your budget and operational efficiency. Understanding the advantages and disadvantages of each can help you make an informed choice.
3 Conveyor Rollers for Sale
Finding the right 3 conveyor rollers involves knowing where to look and understanding the factors that affect their cost. Here’s a guide on where to find these rollers and what to expect in terms of pricing.
Where to Find Them
- Online Stores: Websites like Amazon, eBay, and specialized industrial equipment retailers.
- Industrial Suppliers: Companies that specialize in conveyor systems and components, such as McMaster-Carr and Grainger.
- Manufacturer Websites: Direct purchase from manufacturers like Ultimation Industries and Titan Conveyors.
- Local Distributors: Industrial supply stores or local distributors that carry conveyor equipment.
- Trade Shows: Industry-specific trade shows and exhibitions where manufacturers showcase their products.
- Classified Ads: Online classified ads such as Craigslist or industrial forums where businesses sell used equipment.
Price Ranges and Factors Affecting Cost
- Material: Stainless steel rollers are generally more expensive than plain steel or plastic rollers.
- Load Capacity: Higher load capacity rollers tend to cost more due to their enhanced durability.
- Dimensions: Longer or thicker rollers will have a higher price due to the increased material use.
- Bearing Type: Rollers with high-quality bearings (e.g., ABEC-1) will be pricier but offer better performance.
- Customization: Custom rollers made to specific dimensions or with special coatings will have higher costs.
- Brand: Established brands with a reputation for quality often have higher prices.
- Quantity: Bulk purchases usually come with a discount, reducing the cost per roller.
Important Dimensions and Specifications
Knowing the right dimensions and specifications is crucial when selecting 3 conveyor roller. This ensures compatibility with your existing systems and meets your operational requirements.
- Diameter: Confirm the roller diameter is exactly 3 inches to ensure it fits your conveyor system.
- Wall Thickness: Measure the thickness of the roller wall; 11-gauge is a common standard for durability.
- Length: Determine the required length based on your conveyor frame width.
- Bearing Type: Check if the roller uses sealed bearings (like ABEC-1) for longevity and smooth operation.
- Axle Size: Verify the axle size, typically 1/2″ round, and ensure it matches your conveyor’s specifications.
- Load Capacity: Assess the load capacity, usually specified per roller, to ensure it meets your needs.
- Surface Finish: Look for smooth or coated finishes based on the type of materials you’ll be transporting.
- Temperature Range: Ensure the rollers can operate within the temperature range of your working environment.
By considering these factors, you can select the appropriate 3 conveyor rollers that fit your operational requirements and budget, ensuring efficiency and reliability in your material handling processes.
Specialty 3 Conveyor Roller
Specialty 3 conveyor rollers are designed to meet specific industrial needs that standard rollers might not address. These rollers come in various sizes and configurations, each offering unique benefits and applications. In this section, we will explore three distinct types of specialty 3 conveyor roller: 3/4″ Diameter Conveyor Rollers, 3/4″ Replacement Conveyor Rollers, and 3-Foot Roller Conveyors. Each type serves different purposes and provides unique advantages in various industrial settings.
3/4″ Diameter Conveyor Rollers
3/4″ diameter conveyor rollers are smaller than the standard 3″ rollers and are used in applications where precision and lightweight handling are crucial. These rollers are typically used in systems that require finer control and smoother operation for smaller items or components.
Uses and Advantages:
- Precision Handling: Ideal for transporting small, delicate items that require gentle handling.
- Space Efficiency: Suitable for compact conveyor systems where space is limited.
- Cost-Effective: Generally less expensive due to their smaller size and material usage.
- Lightweight: Easier to install and maintain compared to larger rollers.
- Low Friction: Designed to reduce friction, ensuring smooth and efficient movement.
- Custom Applications: Often used in specialized machinery or equipment that requires smaller rollers.
- Versatile Materials: Available in various materials, including plastic and lightweight metals, for different industrial needs.
3/4″ Replacement Conveyor Rollers
3/4″ replacement conveyor rollers are essential for maintaining and upgrading existing conveyor systems. Ensuring compatibility and proper maintenance of these rollers can significantly extend the lifespan of your conveyor system and enhance its performance.
Importance of Compatibility and Maintenance:
- Compatibility: Ensuring replacement rollers match the specifications of the original ones is crucial for system integrity.
- Easy Replacement: Designed for quick and easy installation to minimize downtime.
- Cost Savings: Regular maintenance and timely replacement of worn-out rollers can prevent costly system failures.
- Enhanced Performance: New rollers can improve the overall efficiency and speed of the conveyor system.
- Extended Lifespan: Regularly replacing worn rollers helps in maintaining the longevity of the entire conveyor system.
- Improved Safety: Well-maintained rollers reduce the risk of accidents and damage to goods.
- Available Options: Replacement rollers come in various sizes and materials to match different system requirements.
3-Foot Roller Conveyors
3-foot roller conveyors are shorter sections of conveyor systems designed for specific applications that require limited space or modular setups. These shorter conveyors are highly versatile and can be easily integrated into existing systems or used as standalone units.
Applications and Benefits of Shorter Conveyor Sections:
- Space-Saving: Ideal for areas with limited space, providing efficient material handling without occupying much room.
- Modular Design: Can be easily added to or removed from existing conveyor lines, offering flexibility in layout design.
- Temporary Installations: Perfect for temporary setups in events, construction sites, or seasonal operations.
- Versatile Usage: Used in various industries, including manufacturing, packaging, and retail.
- Easy Installation: Simple to set up and dismantle, making them suitable for quick changes in production lines.
- Cost-Effective: Shorter sections are generally less expensive and can be a cost-effective solution for small-scale operations.
- Customization: Available in different widths and materials to suit specific needs, enhancing the adaptability of conveyor systems.
Specialty 3 conveyor rollers, including 3/4″ diameter rollers, 3/4″ replacement rollers, and 3-foot roller conveyors, each offer unique advantages and applications that cater to specific industrial requirements. Understanding these options can help in selecting the right components to enhance the efficiency, flexibility, and performance of your conveyor systems.
What Are Roller Conveyor Mechanisms
Roller conveyors are essential components in modern industrial and commercial operations. They are designed to move products efficiently and reliably, facilitating smooth workflows and enhancing productivity. Understanding how these systems work and their various uses can help businesses make informed decisions about implementing conveyor technology.
How Roller Conveyors Work
Roller conveyors operate on simple yet effective mechanical principles. They consist of a series of rollers mounted within a frame, and their operation can be powered by gravity or a motor. The design and functionality of these conveyors make them suitable for handling a wide range of materials and products.
- Gravity-Powered Operation: Gravity roller conveyors rely on the force of gravity to move items. These systems are typically inclined, allowing products to roll from a higher to a lower point without the need for external power.
- Motorized Rollers: In motorized roller conveyors, each roller or a group of rollers is powered by an electric motor, providing consistent and controlled movement of products.
- Roller Frame: The frame of the conveyor supports the rollers and can be constructed from various materials, including steel, aluminum, or plastic, depending on the application and load requirements.
- Roller Bearings: Bearings are integral to the function of rollers, reducing friction and allowing for smooth rotation. Common types include ball bearings and needle bearings.
- Axle and Shaft: Each roller is fitted with an axle or shaft that supports its rotation. These components need to be robust and well-maintained to ensure the system’s reliability.
- Load Capacity: The load capacity of a roller conveyor depends on the roller’s material, diameter, wall thickness, and the type of bearings used. Properly matched components ensure the system can handle the intended load.
- Speed Control: In motorized systems, speed controllers regulate the movement speed of products, allowing for precise handling and reducing the risk of damage.
- Modularity and Customization: Roller conveyors can be customized to fit specific needs, with options for varying roller spacing, sizes, and materials. This flexibility makes them adaptable to a wide range of industries and applications.
Roller Conveyor Uses
The versatility and efficiency of roller conveyors make them valuable assets across various industries. Their ability to handle different types of materials and products with minimal manual intervention enhances operational efficiency and reduces labor costs.
- Manufacturing: In manufacturing plants, roller conveyors streamline the movement of raw materials and finished products between different stages of the production process, improving overall efficiency.
- Warehousing: Roller conveyors facilitate the efficient handling and sorting of goods in warehouses, aiding in storage and retrieval processes and optimizing space utilization.
- Food and Beverage: In the food and beverage industry, roller conveyors help in the hygienic and efficient transportation of products through processing, packaging, and distribution stages.
- Automotive: Automotive assembly lines use roller conveyors to transport heavy components like engines and chassis, enhancing the precision and speed of assembly operations.
- Retail: In retail distribution centers, roller conveyors are essential for sorting and moving products from storage areas to shipping docks, ensuring timely deliveries and reducing order fulfillment times.
- E-commerce: E-commerce fulfillment centers rely on roller conveyors to handle high volumes of orders, improving sorting accuracy and speeding up the packaging and shipping processes.
- Recycling: In recycling facilities, roller conveyors assist in the sorting and processing of recyclable materials, enhancing the efficiency and effectiveness of recycling operations.
- Pharmaceutical: The pharmaceutical industry uses roller conveyors to move products through various stages of production, from packaging to distribution, maintaining high standards of safety and efficiency.
By understanding the mechanisms and diverse applications of 3 conveyor roller, businesses can better appreciate their value and implement these systems to enhance productivity and streamline operations. Whether used in manufacturing, warehousing, or retail, the adaptability and efficiency of roller conveyors make them indispensable tools in modern industry.
Additional Considerations for 3 Conveyor Roller Systems
When working with 3 conveyor roller systems, it’s essential to understand various aspects of maintenance and customization to ensure optimal performance and longevity. Proper maintenance techniques and available customizations can significantly impact the efficiency and effectiveness of your conveyor system.
Conveyor Belt Tightening Techniques
Maintaining the correct tension in your conveyor belt is crucial for the smooth operation of the conveyor system. Proper belt tension ensures that the conveyor runs efficiently and reduces wear and tear on the rollers and other components.
- Regular Inspections: Routinely check the belt tension and condition. Look for signs of wear, fraying, or misalignment, and address these issues promptly to prevent further damage.
- Adjusting Tension: Use the tensioning mechanism to adjust the belt tension. Most systems have a built-in adjustment screw or bolt. Ensure that the belt is not too tight, as this can cause excessive wear on the rollers and bearings.
- Proper Alignment: Ensure the belt is aligned correctly with the rollers. Misalignment can cause uneven wear and reduce the lifespan of both the belt and the rollers.
- Lubrication: Regularly lubricate the moving parts, such as bearings and tensioning mechanisms, to reduce friction and wear.
- Cleaning: Keep the belt and rollers clean. Debris can cause the belt to slip or wear unevenly. Regular cleaning prevents build-up that can affect performance.
- Monitoring Load: Avoid overloading the conveyor system. Excessive weight can cause the belt to stretch or slip, leading to reduced efficiency and potential damage.
- Replacing Worn Parts: Replace worn or damaged rollers and belts immediately. Operating with compromised parts can lead to more significant issues and costly repairs.
- Using Belt Tracking Devices: Implement belt tracking devices to automatically adjust and keep the belt centered on the rollers, enhancing operational efficiency and reducing manual adjustments.
Customizations and Options
Customizing your 3 conveyor roller system can enhance its functionality and suitability for specific applications. Various modifications and options can tailor the system to better meet your operational requirements.
- Welded Sprockets: Adding welded sprockets to rollers can provide better drive control and synchronization, especially in motorized conveyor systems.
- Custom Roller Lengths: Adjusting the length of rollers to fit specific conveyor widths ensures a perfect fit and optimal performance.
- Special Coatings: Applying special coatings, such as anti-corrosion or high-friction materials, can extend the lifespan of rollers and improve handling characteristics.
- Heavy-Duty Rollers: For applications requiring higher load capacities, heavy-duty rollers with thicker walls and stronger materials can be used.
- High-Temperature Rollers: In environments with extreme temperatures, high-temperature-resistant rollers ensure reliable performance and prevent damage.
- Noise Reduction Features: Adding noise reduction features, such as rubber-coated rollers or sound-dampening mounts, can create a quieter work environment.
- Quick-Release Mechanisms: Implementing quick-release mechanisms allows for faster roller replacement and maintenance, reducing downtime.
- Adjustable Roller Centers: Customizing the spacing between rollers can accommodate different product sizes and improve the handling of various items.
By considering these additional factors and options, businesses can optimize their 3 conveyor roller systems for enhanced performance and efficiency. Proper maintenance and thoughtful customizations ensure that the conveyor system meets specific operational needs and continues to perform reliably over time.
Last Updated on May 17, 2024 by Jordan Smith
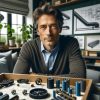
Jordan Smith, a seasoned professional with over 20 years of experience in the conveyor system industry. Jordan’s expertise lies in providing comprehensive solutions for conveyor rollers, belts, and accessories, catering to a wide range of industrial needs. From initial design and configuration to installation and meticulous troubleshooting, Jordan is adept at handling all aspects of conveyor system management. Whether you’re looking to upgrade your production line with efficient conveyor belts, require custom conveyor rollers for specific operations, or need expert advice on selecting the right conveyor accessories for your facility, Jordan is your reliable consultant. For any inquiries or assistance with conveyor system optimization, Jordan is available to share his wealth of knowledge and experience. Feel free to reach out at any time for professional guidance on all matters related to conveyor rollers, belts, and accessories.