Advancements in 4 Conveyor Belt Technology and Use
Conveyor belts play a pivotal role in streamlining operations across various industries, from manufacturing and mining to packaging and transportation. These belts facilitate the efficient and continuous movement of goods, materials, and products, significantly enhancing productivity and operational efficiency. Among the diverse range of conveyor belts available, the 4 conveyor belt stands out for its specific applications, particularly in settings where space is limited or precise handling of smaller items is required. This blog post delves into the world of 4-inch conveyor belts, exploring their unique features, applications, and the value they bring to industrial operations. Whether used in intricate machinery or compact assembly lines, these belts prove to be an indispensable tool for modern industry.
What Is a 4 Conveyor Belt
A 4 conveyor belt is a specific type of conveyor belt that measures 4 inches in width, designed for specialized applications where space efficiency and precision handling of materials are paramount. This section will explore the defining characteristics and the industrial significance of this particular conveyor belt size.
Defining Characteristics of a 4-Inch Conveyor Belt
The 4-inch conveyor belt, distinguished by its narrow width, is engineered to meet specific operational needs. This segment delves into the intrinsic attributes that set the 4 conveyor belt apart, highlighting its design, functionality, and adaptability in various settings.
- Compact Design: The hallmark of the 4 conveyor belt is its 4-inch width, tailored for installations where space is constrained.
- Durable Construction: Crafted from robust materials such as reinforced rubber or synthetic fabrics, it withstands industrial rigors.
- Enhanced Flexibility: Its slender profile allows for more intricate routing and tighter turns in conveyor layouts.
- Load Capacity: Engineered to efficiently handle substantial weights despite its diminutive size, ensuring operational efficacy.
- Modular Nature: Often part of modular systems, it offers flexibility in configuration and easy expansion capabilities.
- Precision in Movement: Excelling in transporting small or delicate items with the need for precise control and placement.
- Variable Speeds: Capable of adjusting speeds to match specific process requirements, from slow assembly lines to rapid sorting processes.
- Ease of Maintenance: Its smaller scale simplifies upkeep and replacement, reducing downtime and maintenance costs.
Significance of the 4-Inch Width in Industrial Applications
The 4-inch width of this conveyor belt is not just a dimensional specification; it represents a solution to several industrial challenges. This section explores how the unique width of the 4 conveyor belt makes it an essential tool in various industrial landscapes.
- Optimal Space Utilization: In environments where every inch counts, the slim profile of the 4 conveyor belt maximizes the utility of limited spaces.
- Targeted for Precision Tasks: Its narrow width makes it indispensable in industries like electronics, where handling small, sensitive components is routine.
- Energy Conservation: The smaller belt size translates to lower energy consumption, aligning with sustainability goals and cost reduction.
- Seamless Integration: Its compact size allows for effortless incorporation into existing setups, enhancing system flexibility without extensive overhauls.
- Enhanced Safety Measures: The reduced width minimizes exposure to moving parts, facilitating safer operations and easier implementation of safety protocols.
- Economic Advantage: Offers a cost-effective solution due to lower initial outlay and operational costs, making it accessible for various scales of operations.
- Quieter Operation: Tends to produce less noise during operation, contributing to a more comfortable and less disruptive work environment.
- Adaptability for Specialized Uses: Particularly suited for applications in confined areas or specialized tasks that larger belts cannot accommodate, such as detailed inspection processes or precise sorting operations.
The 4-inch conveyor belt is a testament to the innovation in conveyor technology, offering solutions that are tailored to meet the unique demands of various industries, from electronics assembly to food processing and beyond. Its compact design and versatility make it an invaluable component in modern industrial operations.
Key Features of 4 Conveyor Belt
The 4 conveyor belt, with its unique 4-inch width, is designed to cater to specific industrial requirements, offering a blend of durability, precision, and versatility. This section delves into the nine key features that underscore the utility and adaptability of the 4-inch conveyor belts in various applications.
- Durability and Material: The core of the 4 conveyor belt’s resilience lies in its construction material, typically high-grade rubber or synthetic compounds. This material choice provides exceptional wear resistance, ensuring longevity even in demanding industrial environments.
- Design and Specifications: A hallmark of the 4 conveyor belt is its meticulously engineered design, encompassing multiple ply layers and a robust tensile strength framework. This design ensures the belt can withstand substantial operational stresses while maintaining its integrity and performance.
- Customization Options: Recognizing the diverse needs of different industries, 4-inch conveyor belts are available in various custom sizes and configurations. This flexibility allows for tailored solutions, ensuring optimal integration and functionality within specific production lines or systems.
- Compact Profile: The narrow width of the 4 inch conveyor belt makes it an ideal choice for applications where space is limited, enabling efficient material handling in confined areas without compromising performance.
- High Load Capacity: Despite its compact size, the 4-inch conveyor belt is designed to support significant load capacities. This feature is crucial for industries that require the transportation of heavy or bulky materials over short distances.
- Speed Variability: These conveyor belts are engineered to operate at different speeds, accommodating a wide range of material handling requirements. This adaptability ensures that the belt can be seamlessly integrated into various stages of the production process.
- Ease of Installation: The 4 conveyor belt’s design facilitates straightforward installation, making it a convenient option for both new setups and upgrades to existing systems. This ease of installation translates to reduced downtime and quicker operational readiness.
- Low Maintenance: The materials and construction of the 4-inch conveyor belts are selected for their low-maintenance qualities. This feature ensures that the belts remain operational with minimal upkeep, reducing the total cost of ownership.
- Environmental Resistance: These belts are often treated or manufactured with materials that provide resistance to various environmental factors, such as chemicals, temperatures, and abrasion. This resilience is critical for maintaining operational efficiency in harsh industrial conditions.
The 4 conveyor belt stands out for its combination of durability, design precision, and adaptability, making it a valuable asset in a wide array of industrial applications. Its ability to meet specific operational demands while ensuring reliability and efficiency underscores its significance in the realm of material handling and conveyor systems.
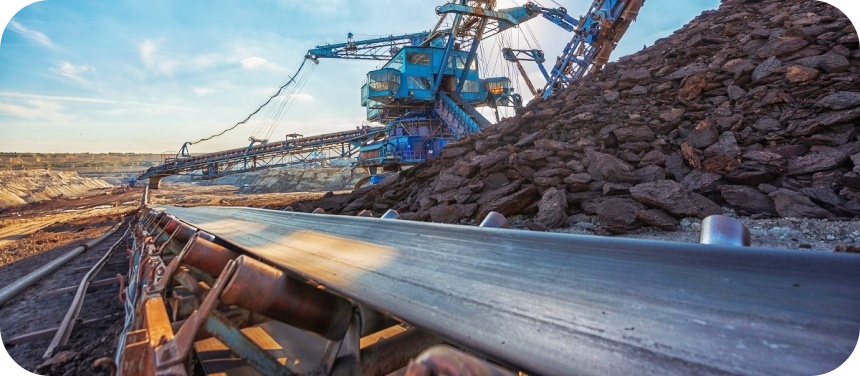
Applications of 4 Conveyor Belt
The versatility and efficiency of 4 conveyor belts make them an integral component in a myriad of industrial applications. Their compact size and robust design allow for precise material handling in various sectors, from intricate electronic assemblies to the fast-paced food processing lines. This section explores the broad spectrum of industries and machinery that leverage the unique advantages of 4-inch conveyor belts, followed by detailed case studies that illustrate their successful integration and impact on operational efficiency.
Industries and Machines Utilizing 4 Conveyor Belts
The adaptability of 4 conveyor belts to different industrial environments is a testament to their design and functionality. Here are some key areas where these belts are making a significant difference:
- Electronics Assembly Lines: In the precision-driven electronics industry, 4 conveyor belts are instrumental in the careful handling and assembly of small components, ensuring high throughput with minimal error rates.
- Pharmaceutical Packaging Stations: The pharmaceutical sector relies on 4-inch conveyor belts for the efficient and safe packaging of medicines, where precision and hygiene are paramount.
- Food Processing and Packaging: These belts are widely used in the food industry, especially for small-sized food items like snacks and candies, facilitating swift sorting and packaging processes.
- Jewelry Manufacturing: The delicate nature of jewelry pieces necessitates the use of 4 conveyor belts, which provide gentle handling to prevent damage during the manufacturing process.
- Automotive Parts Assembly: Small but critical automotive parts such as fasteners and electronic components are transported and assembled using 4-inch conveyor belts, enhancing the assembly line’s efficiency.
- Packaging Equipment: In packaging facilities, these belts are crucial for the precise movement and packaging of small items, ensuring they are ready for distribution.
- Laboratory and Testing Equipment: For automated lab processes, 4 conveyor belts facilitate the smooth and controlled movement of samples and reagents, contributing to accurate and reliable results.
Case Studies of Successful 4 Conveyor Belt Implementations
The practical applications of 4 conveyor belts across various industries highlight their role in enhancing operational efficiency and productivity. Here are some notable examples:
- High-Tech Electronics Factory: A leading electronics manufacturer revolutionized its assembly line by incorporating 4 conveyor belts, significantly improving the precision and speed of smartphone assembly.
- Advanced Pharmaceutical Facility: A state-of-the-art pharmaceutical plant achieved remarkable improvements in the packaging accuracy and speed of medicine bottles by integrating 4-inch conveyor belts into their packaging lines.
- Innovative Food Sorting System: A food processing company introduced 4 conveyor belts into their sorting systems, resulting in a substantial increase in the sorting accuracy and processing speed of confectionery items.
- Automotive Assembly Success: An automotive parts manufacturer utilized 4-inch conveyor belts to enhance the assembly process of small, precision components, leading to a marked reduction in production time and material waste.
- Luxury Watch Assembly Precision: A renowned watchmaker employed 4 inch conveyor belts in the delicate assembly process of luxury watches, ensuring the integrity and quality of each piece.
- Food Inspection Efficiency: By integrating 4-inch conveyor belts into their inspection systems, a food processing company significantly improved the detection rate of foreign objects in packaged food products, ensuring higher safety standards.
- Laboratory Automation Breakthrough: A research lab dramatically increased its sample processing capacity and consistency by incorporating 4 conveyor belts into their automated systems, streamlining the handling of numerous samples.
- Beverage Bottling Innovation: A beverage company successfully reduced spillage and improved the stability of small bottle transfers on their bottling line by implementing 4-inch conveyor belts, enhancing overall production efficiency.
These case studies underscore the adaptability and effectiveness of 4-inch conveyor belts in addressing specific operational challenges across various industries. The successful implementations highlight the belts’ role in enhancing precision, efficiency, and productivity in diverse applications.
Pricing and Availability of 4 Conveyor Belt
Navigating the market for 4 conveyor belts requires an understanding of the various factors that influence their pricing, as well as knowledge of where to find the best deals. Whether you’re in the market for new or used options, the price of a 4 conveyor belt can vary widely based on several key factors. Additionally, knowing the most reliable sources for purchasing these belts can significantly streamline your procurement process. Below, we delve into the intricacies of pricing dynamics and share valuable tips on sourcing 4-inch conveyor belts.
Factors Influencing the Price of 4 Conveyor Belts
The cost of 4 conveyor belts is not uniform across the board; it is shaped by multiple elements that can either drive the price up or bring it down. Understanding these factors is crucial for budgeting and making informed purchasing decisions:
- Material Composition: The type and quality of materials used in manufacturing 4 conveyor belt, such as high-grade rubber or advanced synthetic fabrics, play a significant role in determining their price.
- Production Intricacies: The complexity involved in producing belts with specific features, like enhanced durability or specialized coatings, can affect the cost.
- Brand and Reputation: Well-known brands with a track record of reliability and quality often price their 4 conveyor belts higher, reflecting their market standing.
- Custom Features: Tailor-made solutions designed to meet unique operational requirements can lead to a higher price point due to the additional customization work involved.
- Market Dynamics: Fluctuations in supply and demand, influenced by factors like raw material scarcity or increased demand, can impact pricing.
- Innovative Technologies: Conveyor belts that incorporate cutting-edge technologies for superior performance may come with a premium price.
- Logistics Costs: The expenses associated with shipping, especially for international deliveries, can significantly influence the final purchase price.
- Compliance and Standards: Conveyor belts that adhere to stringent industry standards or regulatory requirements might carry a higher price due to the rigorous testing and certification processes they undergo.
Tips on Where to Find 4 Conveyor Belts for Sale
Securing a 4 conveyor belt that meets your specific needs at a competitive price requires exploring various sourcing avenues. Here are some effective strategies to help you find the right conveyor belt:
- Explore Industry Expos: Attending trade shows dedicated to industrial equipment can provide insights into the latest conveyor belt technologies and direct access to suppliers.
- Leverage Online Platforms: Utilizing online marketplaces and specialized e-commerce sites can offer a broad selection of 4 conveyor belts from diverse suppliers worldwide.
- Direct Manufacturer Purchases: Buying directly from conveyor belt manufacturers can sometimes yield cost savings and opportunities for customization.
- Seek Out Used Equipment Vendors: For budget-conscious projects, reputable sellers of used industrial machinery can be a valuable source of quality 4-inch conveyor belts at reduced prices.
- Participate in Auctions: Keeping an eye on industrial auctions can lead to great deals on both new and used conveyor belts.
- Engage with Local Suppliers: Building relationships with local distributors can offer benefits like personalized service and support, along with access to a range of products.
- Consider Refurbished Belts: Some vendors specialize in refurbishing conveyor belts, providing a cost-effective alternative to brand-new options.
- Network within Industry Circles: Tapping into industry forums and professional networks can yield recommendations and insider tips on where to find the best deals on 4 conveyor belts.
- Visit Specialty Retailers: Stores that specialize in conveyor systems often carry a selection of 4-inch belts tailored for various applications, offering both expertise and variety.
By carefully considering the factors that influence the price and exploring diverse sourcing options, you can effectively navigate the market for 4 conveyor belts and secure the best possible deal for your specific requirements.
Choosing the Right 4 Conveyor Belt
Selecting the appropriate 4 conveyor belt for your specific industrial application involves a comprehensive evaluation of various factors to ensure optimal performance, durability, and cost-efficiency. This section outlines key considerations to guide you in making an informed decision when choosing the right 4-inch conveyor belt for your needs.
- Quality Considerations: Assessing the quality of a 4 conveyor belt is paramount. Look for belts made from high-grade materials with a proven track record of durability. Check for manufacturer certifications and compliance with industry standards to gauge quality.
- Weight and Capacity: Utilize a conveyor belt weight calculator to match the belt’s weight capacity with your application’s requirements. Ensure the 4 conveyor belt you select can handle the expected load without compromising speed or efficiency.
- Special Features: Depending on your application, you may need a 4 conveyor belt with specific features such as heat resistance for high-temperature environments, chemical resistance for processing plants, or abrasion resistance for handling rough materials.
- Application Suitability: Consider the specific use case of the 4 conveyor belt within your operation. Whether it’s for delicate component handling in electronics manufacturing or rugged use in mining, the belt should be tailored to the application.
- Flexibility and Length: The operational layout might require a 4 inch conveyor belt that offers flexibility for navigating tight spaces or specific lengths to fit bespoke machinery setups.
- Maintenance Requirements: Opt for a 4 conveyor belt that promises ease of maintenance. Belts that are easier to clean, repair, or replace can significantly reduce downtime and maintenance costs.
- Environmental Conditions: Evaluate the working environment where the 4 conveyor belt will be used. Factors such as exposure to moisture, extreme temperatures, or corrosive substances will dictate the need for belts designed to withstand such conditions.
- Energy Efficiency: Consider the energy consumption of the conveyor system. A 4 conveyor belt designed for energy efficiency can contribute to lower operational costs and a reduced environmental footprint.
- Supplier Reputation: The reliability of the supplier or manufacturer of the 4 inch conveyor belt is crucial. Choose a supplier known for quality products and after-sales support to ensure you receive a belt that meets your expectations and service in case of issues.
By carefully considering these aspects, you can ensure that the 4 conveyor belt you choose not only meets the immediate needs of your application but also offers long-term reliability and efficiency, ultimately contributing to the smooth operation of your industrial processes.
Maintenance and Longevity of 4 Conveyor Belt
Maintaining the integrity and functionality of 4 conveyor belts is essential for the seamless operation of industrial processes. Proper care and regular maintenance not only extend the lifespan of these belts but also ensure they perform efficiently, minimizing the risk of downtime and operational disruptions. This section is dedicated to outlining the best practices for maintaining 4 conveyor belts and addressing common issues that may arise during their lifecycle, along with effective solutions.
Best Practices for Maintaining 4-Inch Conveyor Belt
To safeguard the longevity and performance of 4 conveyor belts, adhering to a set of maintenance best practices is crucial. These guidelines are designed to preemptively tackle potential problems and ensure the conveyor system operates smoothly:
- Scheduled Inspections: Implement a routine schedule for inspecting the 4 conveyor belt, focusing on signs of wear, damage, or any abnormalities that could affect performance.
- Maintain Cleanliness: Regular cleaning of the 4 inch conveyor belt and its components is vital to prevent the buildup of materials that could lead to damage or inefficiency.
- Proper Tensioning: Maintaining the correct tension on the 4 conveyor belt is key to avoiding slippage and ensuring optimal performance.
- Alignment Verification: Regular checks and adjustments to the conveyor belt’s alignment can prevent uneven wear and extend its service life.
- Lubrication Protocol: Ensuring that all moving parts in the conveyor system are adequately lubricated reduces friction and wear, contributing to smoother operation.
- Observance of Load Limits: It’s important to adhere to the specified load capacity of the 4 conveyor belt to prevent overloading, which can cause damage and reduce lifespan.
- Educate Operators: Providing comprehensive training for operators and maintenance personnel on the proper care and handling of the 4 inch conveyor belt enhances its maintenance.
- Quality Replacement Components: When repairs are necessary, using high-quality replacement parts helps maintain the system’s integrity and performance.
Common Issues with 4 Conveyor Belts and Solutions
Even with diligent maintenance, 4 conveyor belts can encounter a range of issues. Being aware of these common problems and knowing how to address them can help maintain operational efficiency:
- Belt Slippage: This issue can be rectified by adjusting the belt’s tension and ensuring that the conveyor is not overloaded.
- Misalignment: Regularly checking and correcting the conveyor’s alignment can prevent this issue, which can lead to uneven belt wear.
- Wear and Tear: Continuous monitoring and timely replacement of worn sections or the entire belt are necessary to maintain performance.
- Material Accumulation: Implementing a consistent cleaning schedule helps avoid buildup that can hinder belt movement.
- Edge Wear: Ensuring the conveyor is properly aligned and free from obstructions can prevent damage to the belt’s edges.
- Joint or Splice Failure: Regular inspection of belt joints or splices allows for early detection and repair, preventing further damage.
- Tracking Problems: Keeping the conveyor belt properly aligned and free from obstructions ensures it runs smoothly on the rollers.
- Environmental Damage: Using belts that are designed to withstand specific conditions, such as high temperatures or chemical exposure, and monitoring for signs of damage can mitigate this issue.
By implementing these maintenance best practices and being proactive in addressing common issues, the longevity and efficiency of 4 conveyor belt can be significantly enhanced, contributing to the overall productivity and reliability of industrial operations.
Get in touch with us for custom 4 conveyor belt solutions by completing the form.
FAQs about 4 Conveyor Belt
The thickness of a 4 ply conveyor belt can vary depending on the specific materials used in each ply and the type of rubber cover applied. Generally, each ply in a conveyor belt adds to the overall thickness and strength of the belt. A typical 4 ply conveyor belt might have a thickness ranging from about 6 mm to over 15 mm. The exact thickness is determined by the requirements of the application, including the need for impact resistance, load capacity, and durability. For instance, a 4 ply belt designed for heavy-duty mining applications would be thicker and more robust compared to one intended for light agricultural use. It’s important to consult with the manufacturer or a conveyor belt specialist to determine the appropriate belt thickness for your specific needs, as this can significantly impact the belt’s performance and longevity.
Conveyor belts do not have a “one size fits all” standard size, as they are often customized to fit the specific needs of the operation or machinery they are used with. However, conveyor belts can be categorized by their width and length, which are typically measured in inches or millimeters. Common widths range from as narrow as 6 inches (about 150 mm) to as wide as 96 inches (about 2400 mm) or more, with lengths varying significantly based on the application. The size of a conveyor belt is determined by the size of the product being transported, the layout of the conveyor system, and the distance the items need to be moved. When selecting a conveyor belt, it’s crucial to consider the specific requirements of your operation, including the load capacity, the type of materials being conveyed, and the environmental conditions.
Conveyor belts can be broadly categorized into three main types based on their construction and intended application:
Flat Belt Conveyors: These are the most common type of conveyor belts, used in a wide variety of industries for transporting items from one point to another. They consist of a flat belt surface that moves over pulleys driven by motors. Flat belt conveyors are versatile and can be used for moving everything from small components to large boxes.
Modular Belt Conveyors: Modular belt conveyors are made of interlocking plastic pieces and are used in applications where the conveyor path may need to curve or where the belt surface requires a high degree of durability and resistance to damage. These belts are easy to clean and maintain, making them suitable for food processing and packaging applications.
Roller Bed Conveyors: Roller bed conveyors use a series of rollers to support and move the belt. This design reduces friction, making it easier to transport heavy loads or move items over long distances. Roller bed conveyors are commonly used in distribution centers, warehouses, and assembly lines.
Each type of conveyor belt has its unique advantages and is suited to specific applications based on factors such as the nature of the materials being conveyed, the required speed and efficiency, and the environmental conditions.
The cost of a conveyor belt can vary widely depending on several factors, including the type of belt, the materials used, the length and width of the belt, and any specialized features or customizations. Basic conveyor belts for light-duty applications might start at a few hundred dollars, while more complex systems designed for heavy-duty industrial use can cost thousands or even tens of thousands of dollars. The price is also influenced by the need for additional components such as motors, rollers, and control systems for a complete conveyor system. For an accurate estimate, it’s best to consult with conveyor belt manufacturers or suppliers who can provide a quote based on your specific requirements, including the type of materials to be conveyed, the operational environment, and any custom features needed for your application.
Last Updated on August 2, 2024 by Jordan Smith
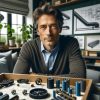
Jordan Smith, a seasoned professional with over 20 years of experience in the conveyor system industry. Jordan’s expertise lies in providing comprehensive solutions for conveyor rollers, belts, and accessories, catering to a wide range of industrial needs. From initial design and configuration to installation and meticulous troubleshooting, Jordan is adept at handling all aspects of conveyor system management. Whether you’re looking to upgrade your production line with efficient conveyor belts, require custom conveyor rollers for specific operations, or need expert advice on selecting the right conveyor accessories for your facility, Jordan is your reliable consultant. For any inquiries or assistance with conveyor system optimization, Jordan is available to share his wealth of knowledge and experience. Feel free to reach out at any time for professional guidance on all matters related to conveyor rollers, belts, and accessories.