4 Ply Conveyor Belt Thickness: 7mm to 12mm
A comprehensive PDF guide on 4 ply conveyor belt thickness is an invaluable resource for industry professionals. This guide provides detailed information on the construction, measurement, and applications of 4 ply conveyor belts. Understanding the 4 ply conveyor belt thickness is crucial for selecting the right belt for specific industrial needs, ensuring optimal performance and longevity. The PDF guide includes charts, diagrams, and specifications that help users make informed decisions, highlighting the significance of proper belt thickness in various operational environments. Access to this guide ensures that users have a thorough understanding of the critical aspects of 4 ply conveyor belts.
4 Ply Conveyor Belt Thickness in mm Explained
Understanding the thickness of a 4 ply conveyor belt is crucial for selecting the right belt for various industrial applications. The term “4 ply” refers to the construction of the belt, which includes four layers of synthetic fabric bonded together to provide increased strength and durability. The thickness of these belts, measured in millimeters, directly impacts their performance, load-bearing capacity, and suitability for specific tasks.
Measurement of 4 Ply Conveyor Belt Thickness in mm
The thickness of a 4 ply conveyor belt is typically measured in millimeters (mm). This measurement encompasses the total thickness, including the top cover, the four ply layers, and the bottom cover. The standard thickness range for 4 ply conveyor belts usually falls between 8 mm to 12 mm, depending on the specific requirements and applications.
Top Cover Thickness
The top cover of a 4 ply conveyor belt provides the primary layer of protection against wear and tear. It is designed to withstand the friction and impact of materials being transported. The thickness of the top cover generally ranges from 2 mm to 4 mm. The choice of thickness depends on the abrasiveness and weight of the materials being conveyed. Thicker top covers are used for more abrasive materials, providing enhanced durability and a longer lifespan.
Intermediate Ply Layers
The intermediate ply layers are the core of the conveyor belt, providing its strength and flexibility. Each ply layer is typically around 1 mm to 1.5 mm thick. With four ply layers, the combined thickness of the intermediate layers usually adds up to 4 mm to 6 mm. These layers are made from high-strength synthetic fabrics like polyester or nylon, which offer excellent tensile strength and resistance to stretching.
Bottom Cover Thickness
The bottom cover of the 4 ply conveyor belt serves to protect the ply layers from the conveyor system’s components, such as rollers and pulleys. The thickness of the bottom cover typically ranges from 2 mm to 3 mm. This cover ensures that the belt maintains its structural integrity while reducing wear and tear on the conveyor system itself.
Importance of Accurate Thickness Measurement
Accurate measurement of 4 ply conveyor belt thickness is vital for several reasons:
- Load Capacity: The thickness of the belt determines its load-bearing capacity. Thicker belts can handle heavier loads without stretching or deforming, making them suitable for demanding applications like mining and bulk material handling.
- Durability: A thicker belt offers better resistance to wear and tear, especially in abrasive environments. This increases the belt’s lifespan and reduces the frequency of replacements, leading to cost savings.
- Performance: The right thickness ensures that the belt performs efficiently, maintaining consistent speed and reducing the risk of slippage or misalignment.
- Safety: Ensuring the belt has the correct thickness is crucial for safe operation. A belt that is too thin may not support the required loads, increasing the risk of failures that could lead to accidents or downtime.
Factors Affecting 4 Ply Conveyor Belt Thickness
Several factors can influence the thickness of a 4 ply conveyor belt:
- Material Type: The type of material being transported affects the required thickness. Heavier, more abrasive materials necessitate thicker belts.
- Operating Environment: Harsh operating conditions, such as extreme temperatures or exposure to chemicals, may require belts with specific thicknesses to ensure durability and performance.
- Conveyor System Design: The design and layout of the conveyor system, including the size of the pulleys and the distance between rollers, can influence the optimal thickness of the belt.
- Application Requirements: Different applications have unique requirements that dictate the necessary belt thickness. For instance, belts used in food processing may need to meet specific hygiene standards that affect their construction and thickness.
Understanding and accurately measuring the 4 ply conveyor belt thickness in mm is essential for selecting the right belt for your industrial needs. By considering factors such as material type, operating environment, and application requirements, businesses can ensure they choose a belt that provides the necessary strength, durability, and performance. Properly selected and maintained conveyor belts contribute to improved efficiency, reduced downtime, and long-term cost savings.
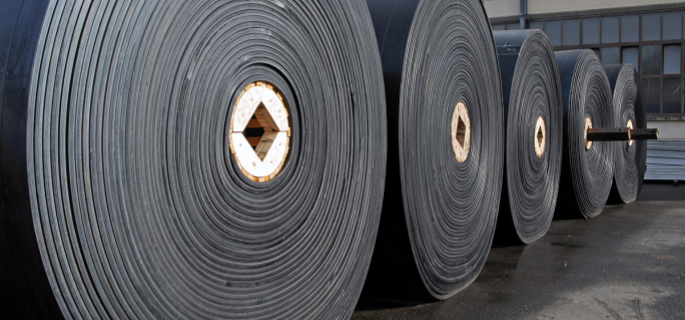
Features of 4 Ply Conveyor Belt Thickness
A 4-ply conveyor belt is a type of industrial belt used in various applications to transport materials. The thickness of the conveyor belt can vary depending on the specific requirements of the application, but generally, the features of a 4-ply conveyor belt in terms of thickness include:
Number of Layers (Plies):
- The term “4-ply” indicates that the belt has four layers of reinforcing fabric, typically made of materials like polyester, nylon, or cotton. These layers are embedded in the rubber to provide strength and durability.
Overall Thickness:
- The overall thickness of a 4-ply conveyor belt typically ranges from 7mm to 12mm. This thickness can vary based on the type of material being conveyed, the load, and the operating conditions.
Cover Thickness:
- Conveyor belts usually have top and bottom covers made of rubber or PVC. The thickness of these covers can vary, but a common configuration might include a top cover thickness of 3mm to 5mm and a bottom cover thickness of 1.5mm to 2mm.
Fabric Thickness:
- Each fabric ply contributes to the overall thickness of the belt. The thickness of each ply can vary, but it is typically around 1mm to 1.5mm per ply.
Flexibility and Rigidity:
- The thickness of the belt affects its flexibility and rigidity. Thicker belts tend to be more rigid, providing higher load-carrying capacity and better resistance to impacts and abrasions.
Applications:
- Due to their increased strength and durability, 4-ply conveyor belts are often used in heavy-duty applications such as mining, quarrying, and bulk material handling.
Abrasion Resistance:
- The rubber covers provide abrasion resistance, which is crucial for prolonging the belt’s lifespan, especially in harsh working conditions.
Temperature Resistance:
- The belt’s composition, including its thickness, can also influence its resistance to temperature extremes. Thicker belts may offer better thermal stability.
The specific thickness and features of a 4-ply conveyor belt can be customized to meet the needs of different industrial applications, ensuring optimal performance and longevity.
4 Ply Conveyor Belt Thickness: 3 Ply Conveyor Belt Thickness Information
A 3 ply conveyor belt is constructed with three layers of synthetic fabric, providing a balance of strength and flexibility for various industrial applications. The thickness of these belts is a critical specification that influences their performance and suitability for different tasks. Understanding the thickness measurements and applications of 3 ply conveyor belts helps in making informed decisions when selecting the right belt for your needs.
Measurement of 3 Ply Conveyor Belt Thickness
The thickness of a 3 ply conveyor belt is typically measured in millimeters (mm) and includes the combined thickness of the top cover, the three ply layers, and the bottom cover. The standard thickness range for 3 ply conveyor belts generally falls between 6 mm to 9 mm, depending on the specific application requirements.
Top Cover Thickness
The top cover of a 3 ply conveyor belt is designed to withstand the wear and tear caused by the materials being transported. The thickness of the top cover generally ranges from 1.5 mm to 3 mm. Thicker top covers are used for applications involving abrasive materials, providing enhanced durability and protection.
Intermediate Ply Layers
The intermediate ply layers form the core of the conveyor belt, offering strength and flexibility. Each ply layer is typically around 1 mm to 1.5 mm thick. With three ply layers, the combined thickness of the intermediate layers usually adds up to 3 mm to 4.5 mm. These layers are made from high-strength synthetic fabrics like polyester or nylon, ensuring excellent tensile strength and resistance to stretching.
Bottom Cover Thickness
The bottom cover of the 3 ply conveyor belt protects the ply layers from the conveyor system’s components, such as rollers and pulleys. The thickness of the bottom cover typically ranges from 1.5 mm to 2.5 mm. This cover helps maintain the belt’s structural integrity and reduces wear and tear on the conveyor system.
Applications of 3 Ply Conveyor Belts
3 ply conveyor belts are used in various industries due to their strength and flexibility. Some common applications include:
- Material Handling: Used in warehouses and distribution centers for transporting boxes, packages, and other goods.
- Agriculture: Ideal for handling grains, seeds, and other agricultural products.
- Manufacturing: Used in manufacturing processes for moving components and finished products along production lines.
- Food Processing: Suitable for transporting food products in processing plants, ensuring hygiene and efficiency.
- Construction: Used for conveying construction materials such as sand, gravel, and concrete.
Importance of Accurate Thickness Measurement
Accurate measurement of 3 ply conveyor belt thickness is crucial for ensuring optimal performance and durability:
- Load Capacity: The thickness of the belt determines its load-bearing capacity. Thicker belts can handle heavier loads without stretching or deforming, making them suitable for demanding applications.
- Durability: A thicker belt offers better resistance to wear and tear, especially in abrasive environments. This increases the belt’s lifespan and reduces the frequency of replacements, leading to cost savings.
- Performance: The right thickness ensures that the belt performs efficiently, maintaining consistent speed and reducing the risk of slippage or misalignment.
- Safety: Ensuring the belt has the correct thickness is crucial for safe operation. A belt that is too thin may not support the required loads, increasing the risk of failures that could lead to accidents or downtime.
Factors Affecting 3 Ply Conveyor Belt Thickness
Several factors can influence the thickness of a 3 ply conveyor belt:
- Material Type: The type of material being transported affects the required thickness. Heavier, more abrasive materials necessitate thicker belts.
- Operating Environment: Harsh operating conditions, such as extreme temperatures or exposure to chemicals, may require belts with specific thicknesses to ensure durability and performance.
- Conveyor System Design: The design and layout of the conveyor system, including the size of the pulleys and the distance between rollers, can influence the optimal thickness of the belt.
- Application Requirements: Different applications have unique requirements that dictate the necessary belt thickness. For instance, belts used in food processing may need to meet specific hygiene standards that affect their construction and thickness.
Understanding and accurately measuring the 3 ply conveyor belt thickness is essential for selecting the right belt for your industrial needs. By considering factors such as material type, operating environment, and application requirements, businesses can ensure they choose a belt that provides the necessary strength, durability, and performance. Properly selected and maintained conveyor belts contribute to improved efficiency, reduced downtime, and long-term cost savings.
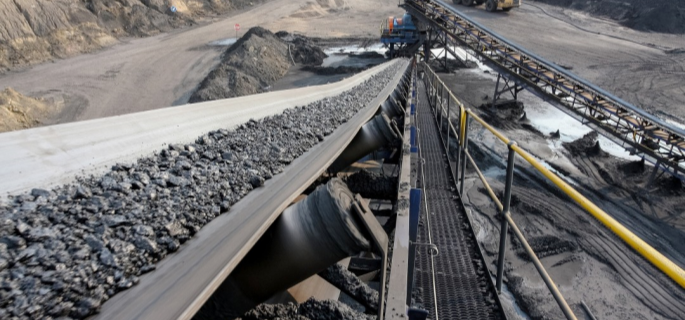
2 Ply vs 3 Ply vs 4 Ply Conveyor Belt Thickness
The choice between 2-ply, 3-ply, and 4-ply conveyor belts depends on the specific application and requirements such as load capacity, flexibility, and durability. Here’s a comparison of the thickness and features for each type:
The choice among 2-ply, 3-ply, and 4-ply conveyor belts should be based on the specific requirements of the operation, including the type of materials being conveyed, load capacity, conveyor length, and operating conditions.
4 Ply Conveyor Belt Thickness: EP Conveyor Belt Specification Details
EP (Polyester) conveyor belts are widely used in various industries due to their excellent tensile strength, flexibility, and resistance to stretching. These belts are constructed with layers of polyester fabric, providing a robust and durable solution for transporting materials. Understanding the technical specifications and features of EP conveyor belts is crucial for selecting the right belt for specific applications.
Ply Construction and Thickness
EP conveyor belts are constructed with multiple layers of polyester fabric, known as plies. The number of plies and the thickness of each ply determine the overall strength and flexibility of the belt. The thickness of EP conveyor belts is typically measured in millimeters (mm) and varies depending on the number of plies and the application requirements.
Top Cover Thickness
The top cover of an EP conveyor belt provides protection against abrasion and impact from the materials being transported. The thickness of the top cover generally ranges from 1.5 mm to 4 mm. Thicker top covers are used for applications involving abrasive materials, providing enhanced durability and protection.
Intermediate Ply Layers
The intermediate ply layers are the core of the EP conveyor belt, offering strength and
flexibility. Each ply layer is typically around 1 mm to 1.5 mm thick. The combined thickness of the intermediate layers varies based on the number of plies, providing the necessary tensile strength and resistance to stretching.
Bottom Cover Thickness
The bottom cover of the EP conveyor belt protects the ply layers from the conveyor system’s components, such as rollers and pulleys. The thickness of the bottom cover typically ranges from 1.5 mm to 3 mm. This cover helps maintain the belt’s structural integrity and reduces wear and tear on the conveyor system.
Technical Specifications
The technical specifications of EP conveyor belts include several key parameters that determine their performance and suitability for different applications:
- Tensile Strength: EP conveyor belts are known for their high tensile strength, typically measured in newtons per millimeter (N/mm). This specification indicates the maximum stress the belt can withstand without breaking, ensuring it can handle substantial loads.
- Elongation at Break: This specification measures the belt’s ability to stretch under stress before breaking. EP conveyor belts generally have low elongation at break, ensuring minimal stretching and maintaining consistent performance.
- Adhesion Strength: Adhesion strength measures the bond between the polyester fabric layers and the rubber covers. High adhesion strength ensures the layers remain securely bonded, preventing delamination and ensuring durability.
- Abrasion Resistance: EP conveyor belts offer excellent abrasion resistance, ensuring long-lasting performance even in abrasive environments. This specification is typically measured using the DIN (Deutsches Institut für Normung) standard, with lower values indicating better resistance.
- Impact Resistance: Impact resistance measures the belt’s ability to absorb and withstand sudden shocks or impacts. EP conveyor belts have high impact resistance, making them suitable for demanding industrial applications.
- Flexibility: EP conveyor belts are highly flexible, allowing them to navigate tight turns and inclines without cracking or breaking. This flexibility is crucial for complex conveyor system designs.
- Temperature Range: EP conveyor belts can operate effectively within a wide temperature range, typically from -20°C to 100°C (-4°F to 212°F). This makes them suitable for various industrial environments, including those with extreme temperatures.
- Chemical Resistance: EP conveyor belts offer good resistance to a variety of chemicals, including oils, acids, and alkalis. This ensures long-term performance and prevents damage from chemical exposure.
Applications of EP Conveyor Belts
EP conveyor belts are used in a wide range of industries due to their versatility and durability. Some common applications include:
- Mining: Used for transporting minerals, ores, and other heavy materials in mining operations.
- Construction: Ideal for conveying construction materials such as sand, gravel, and concrete.
- Manufacturing: Used in manufacturing processes for moving components and finished products along production lines.
- Agriculture: Suitable for handling grains, seeds, and other agricultural products.
- Food Processing: Used for transporting food products in processing plants, ensuring hygiene and efficiency.
Importance of Accurate Specifications
Accurate specifications are essential for ensuring the optimal performance and durability of EP conveyor belts. By understanding the technical parameters and selecting the right belt for specific applications, businesses can achieve improved efficiency, reduced downtime, and long-term cost savings.
Understanding the technical specifications and features of EP conveyor belts is crucial for selecting the right belt for various industrial applications. By considering factors such as tensile strength, elongation at break, adhesion strength, abrasion resistance, impact resistance, flexibility, temperature range, and chemical resistance, businesses can ensure they choose a belt that provides the necessary performance and durability. Properly selected and maintained EP conveyor belts contribute to improved efficiency and long-term cost savings.
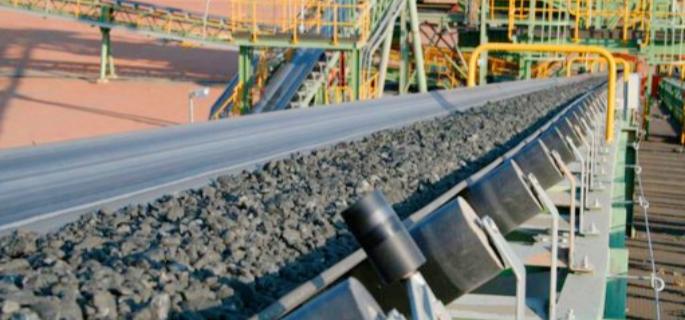
Materials Impacting 4 Ply Conveyor Belt Thickness
The materials used in the construction of a 4 ply conveyor belt play a significant role in determining its thickness and overall performance. The 4 ply conveyor belt thickness is influenced by the types of fabric and rubber compounds utilized, as well as the specific design requirements for the belt’s intended application.
Fabric Materials
- Polyester (EP): Polyester is a common material used in the plies of conveyor belts due to its excellent tensile strength, low elongation, and good impact resistance. When polyester fabrics are used, the belt generally has a uniform thickness and provides a high strength-to-weight ratio, which is crucial for heavy-duty applications.
- Nylon (NN): Nylon is another widely used material known for its high strength, flexibility, and resistance to wear and abrasion. Nylon-based plies tend to add to the overall thickness of the belt while enhancing its flexibility and load-bearing capabilities. Nylon’s flexibility makes it suitable for applications involving complex or sharp turns.
- Cotton (CC): Cotton fabric is used in some conveyor belts for its moderate strength and good flexibility. Cotton plies contribute to a softer and more pliable belt, which can be beneficial in applications requiring gentle handling of materials. However, cotton plies generally result in a thicker belt due to the material’s natural properties.
- Aramid (Kevlar): Aramid fibers, such as Kevlar, are used for their exceptional strength-to-weight ratio and resistance to impact and cutting. Aramid plies can be thinner than traditional materials while still providing superior strength, thereby potentially reducing the overall 4 ply conveyor belt thickness without compromising performance.
Rubber Compounds
- Natural Rubber: Natural rubber is known for its high elasticity and resilience. It is often used in the top and bottom covers of conveyor belts to provide flexibility and impact resistance. The thickness of the rubber layers significantly impacts the overall 4 ply conveyor belt thickness. Thicker rubber layers offer better protection but increase the belt’s total thickness.
- Styrene-Butadiene Rubber (SBR): SBR is commonly used for its durability, abrasion resistance, and cost-effectiveness. The use of SBR in the covers and skim layers can contribute to the belt’s thickness, providing a balance between durability and flexibility.
- Chloroprene Rubber (CR): Also known as Neoprene, this rubber is valued for its chemical resistance and strength. Chloroprene rubber layers can be thinner yet provide adequate protection, potentially reducing the overall thickness while maintaining performance.
- Ethylene Propylene Diene Monomer (EPDM): EPDM rubber is used for its excellent resistance to heat, ozone, and weathering. It is often employed in applications requiring high-temperature resistance. The thickness of EPDM layers impacts the belt’s overall thickness, with thicker layers providing enhanced thermal protection.
Skim Coats
Skim coats are the rubber layers between the plies that help bond them together. The thickness and type of rubber used for skim coats influence the overall 4 ply conveyor belt thickness. Skim coats must be carefully designed to ensure proper adhesion and flexibility without excessively increasing the belt’s thickness.
Impact of Material Combinations
The combination of different fabrics and rubber compounds in a 4 ply conveyor belt determines its final thickness. For instance, a belt with nylon plies and natural rubber covers will have different thickness characteristics compared to a belt with polyester plies and SBR covers. Manufacturers must consider the desired properties such as tensile strength, flexibility, abrasion resistance, and environmental resistance when selecting materials for a 4 ply conveyor belt.
Manufacturing Process of 4 Ply Conveyor Belt Thickness
The manufacturing process of a 4 ply conveyor belt is a meticulous procedure that involves several steps to ensure the correct thickness and quality. Each stage in the manufacturing process impacts the final 4 ply conveyor belt thickness.
Step 1: Material Selection
The process begins with selecting the appropriate materials for the plies and covers. The choice of fabric (polyester, nylon, cotton, or aramid) and rubber compounds (natural rubber, SBR, CR, or EPDM) is critical. The materials are chosen based on the belt’s intended application, considering factors like tensile strength, flexibility, and environmental resistance.
Step 2: Fabric Preparation
The selected fabrics are prepared by cutting them to the required size and treating them with bonding agents to enhance adhesion. This step ensures that the plies will bond properly during the lamination process.
Step 3: Calendering
Calendering is the process where rubber is applied to the fabric plies. The fabric passes through a series of rollers, which coat it with a layer of rubber on both sides. The thickness of the rubber coating applied during calendering plays a significant role in determining the overall 4 ply conveyor belt thickness.
Step 4: Assembly of Plies
The coated fabric plies are then assembled to create the multi-ply structure. For a 4 ply conveyor belt, four layers of fabric are stacked together, with rubber skim coats between each layer to ensure proper bonding and flexibility. The assembly process must be precise to maintain uniform thickness across the belt.
Step 5: Vulcanization
Vulcanization is a heat and pressure treatment that cures the rubber, creating a strong and durable bond between the plies and the rubber layers. The vulcanization process involves placing the assembled belt in a press and applying heat and pressure for a specified duration. The conditions of vulcanization, including temperature and pressure, significantly affect the final thickness and quality of the conveyor belt.
Step 6: Trimming and Finishing
After vulcanization, the conveyor belt is trimmed to the desired width and length. Any excess material is removed, and the edges are finished to ensure smoothness and prevent fraying. This final step ensures that the belt meets the required specifications for thickness and dimensional accuracy.
Step 7: Quality Control
Quality control checks are conducted throughout the manufacturing process to ensure that the belt meets the required standards for thickness, strength, and performance. This includes visual inspections, dimensional measurements, and testing for tensile strength and flexibility. Consistent quality control ensures that each 4 ply conveyor belt produced has uniform thickness and meets the performance requirements.
Applications Requiring Specific 4 Ply Conveyor Belt Thickness
High-quality 4 ply conveyor belt thickness, thickness 7-12mm, with four polyester fabric reinforcements, designed for durability and strength.Different industrial applications require specific 4 ply conveyor belt thicknesses to ensure optimal performance and durability. The choice of thickness is influenced by factors such as the type of material being transported, the operating environment, and the mechanical demands of the application.
Heavy-Duty Mining Operations
In heavy-duty mining operations, conveyor belts are used to transport large volumes of ore, coal, and other minerals. These applications require conveyor belts with significant thickness to handle the high loads and abrasive nature of the materials. A 4 ply conveyor belt with a thickness of 8 to 10 millimeters is typically used in mining operations to provide the necessary strength and durability.
Aggregate and Quarry Applications
Conveyor belts used in aggregate and quarry applications need to be thick enough to withstand the impact of sharp, abrasive materials like gravel, crushed stone, and sand. A 4 ply conveyor belt thickness of 7 to 9 millimeters is common in these environments, providing the required abrasion resistance and load-carrying capacity.
Cement and Concrete Manufacturing
The cement and concrete manufacturing industry requires conveyor belts that can handle heavy, abrasive materials such as limestone, clinker, and cement. A 4 ply conveyor belt with a thickness of 6 to 8 millimeters is often used in this industry to ensure longevity and reliable performance under harsh conditions.
Recycling and Waste Management
In recycling and waste management facilities, conveyor belts must handle a variety of materials, including metals, plastics, and paper. These belts need to be thick enough to resist tearing and puncturing from sharp objects. A 4 ply conveyor belt thickness of 5 to 7 millimeters is suitable for these applications, providing a balance between flexibility and durability.
Food Processing and Packaging
In the food processing and packaging industry, conveyor belts must meet strict hygiene standards while handling various food products. A 4 ply conveyor belt with a thickness of 4 to 6 millimeters is commonly used, offering sufficient strength for transporting food items while maintaining easy cleaning and sanitation.
Agricultural Applications
Conveyor belts used in agriculture must transport products like grains, seeds, and produce. These belts need to be thick enough to withstand the weight and volume of the materials while remaining flexible for handling. A 4 ply conveyor belt thickness of 5 to 7 millimeters is ideal for agricultural applications, ensuring durability and efficiency.
Warehouse and Distribution
In warehouse and distribution centers, conveyor belts are used to move packages, boxes, and pallets. These belts must be thick enough to support the weight and frequency of the loads. A 4 ply conveyor belt thickness of 6 to 8 millimeters is commonly used in these environments, providing the necessary strength and longevity for continuous operation.
Understanding the impact of materials on 4 ply conveyor belt thickness, the detailed manufacturing process, and the specific applications requiring various thicknesses is crucial for selecting the right conveyor belt. By considering these factors, industries can ensure that their conveyor belts meet the necessary performance standards, providing reliable and efficient material handling solutions. The 4 ply conveyor belt thickness plays a pivotal role in determining the belt’s durability, strength, and suitability for different industrial applications, making it an essential aspect of conveyor belt design and selection.
FAQs about 4 Ply Conveyor Belt Thickness
A 4 ply conveyor belt typically has a thickness ranging from 7 to 10 millimeters (0.28 to 0.39 inches). The exact thickness can vary based on the materials used in the plies and the intended application of the belt. In a 4 ply conveyor belt, each layer, or ply, consists of a fabric material that provides strength and durability. These layers are bonded together with rubber or another adhesive material to form a single cohesive belt. The combined thickness of these layers contributes to the overall durability and load-carrying capacity of the conveyor belt, making it suitable for heavy-duty applications.
A 3 ply conveyor belt typically has a thickness ranging from 4.8 to 7 millimeters (0.19 to 0.28 inches). Similar to a 4 ply belt, the thickness of a 3 ply belt can vary depending on the materials and specific construction used. Each ply in a 3 ply conveyor belt is a layer of fabric that provides tensile strength and flexibility. The plies are bonded together with a rubber or polymer material, resulting in a durable and versatile conveyor belt. The reduced thickness compared to a 4 ply belt makes it more flexible and suitable for applications where a lighter belt is sufficient to handle the load.
A 2 ply conveyor belt generally has a thickness ranging from 3 to 5 millimeters (0.12 to 0.20 inches). The thickness of a 2 ply belt is determined by the fabric layers used and the rubber or adhesive material that bonds them together. Each ply in the belt adds to the overall strength and flexibility, making a 2 ply belt suitable for lighter-duty applications compared to 3 or 4 ply belts. Despite its thinner construction, a 2 ply conveyor belt can still provide adequate durability and performance for various industrial uses, particularly where the load requirements are not as demanding.
Ply in a conveyor belt refers to the layers of fabric that are used to construct the belt. Each ply is a layer of material, typically made from textile fabrics such as polyester, nylon, or cotton, that provides the belt with tensile strength and flexibility. The plies are bonded together with a rubber or polymer material to form a single, unified conveyor belt. The number of plies in a belt indicates its strength and durability; more plies generally mean a stronger and thicker belt. Conveyor belts can have varying numbers of plies, such as 2 ply, 3 ply, or 4 ply, depending on the application’s load requirements and operational conditions. The plies work together to distribute the load and absorb impacts, ensuring the conveyor belt performs effectively in different industrial settings.
Last Updated on August 16, 2024 by Jordan Smith
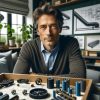
Jordan Smith, a seasoned professional with over 20 years of experience in the conveyor system industry. Jordan’s expertise lies in providing comprehensive solutions for conveyor rollers, belts, and accessories, catering to a wide range of industrial needs. From initial design and configuration to installation and meticulous troubleshooting, Jordan is adept at handling all aspects of conveyor system management. Whether you’re looking to upgrade your production line with efficient conveyor belts, require custom conveyor rollers for specific operations, or need expert advice on selecting the right conveyor accessories for your facility, Jordan is your reliable consultant. For any inquiries or assistance with conveyor system optimization, Jordan is available to share his wealth of knowledge and experience. Feel free to reach out at any time for professional guidance on all matters related to conveyor rollers, belts, and accessories.