Cost-Benefit Analysis of Implementing a 48 Belt Conveyor
Selecting the appropriate size for a conveyor belt is pivotal in industrial operations, where efficiency and productivity are at the forefront of operational success. The 48 belt conveyor stands out as a versatile and standard choice, catering to a wide array of material handling needs. Its width is ideally suited for the bulk movement of materials, offering a balance between speed and capacity that is crucial for maintaining a seamless flow of operations. This introduction to the 48-inch wide conveyor belt highlights its significance in optimizing material handling processes, underscoring its role as a fundamental component in the infrastructure of modern industrial systems. The adaptability and standardization of the 48 belt conveyor make it an indispensable tool in achieving operational efficiency and effectiveness in various sectors.
What are the Specifications of the 48 Belt Conveyor
The 48 belt conveyor represents a significant category in the conveyor belt market, known for its versatility and wide application across various industries. The specifications of these belts are crucial in determining their suitability for specific operational needs, ensuring that they meet the demands of the tasks they are designed to perform.
Length, Material, and Ply Construction
The length of a 48 belt conveyor can vary significantly, depending on the specific requirements of the material handling system it is designed for. These belts can range from short lengths suitable for compact systems to several hundred feet for large-scale operations. The material of the conveyor belt is another critical specification, with options including rubber, PVC, fabric, and steel cord, each offering different advantages in terms of strength, flexibility, and suitability for various environments. Ply construction refers to the number of layers of material that make up the belt, with higher ply counts indicating a stronger belt capable of handling heavier loads or more demanding conditions.
Significance of Conveyor Belt Size
The size of a conveyor belt, particularly its width, plays a vital role in its operational efficiency. A 48-inch wide belt is often chosen for its ability to handle significant volumes of material while maintaining a manageable speed and ensuring the safety of the operation. This width is considered a standard size, offering a balance between the capacity to move large amounts of material and the practicality of installation and maintenance. It is suitable for a wide range of applications, from mining and construction to packaging and distribution.
Operational efficiency is a key consideration in industrial settings. The 48-inch wide conveyor belt ensures a smooth flow of materials, reducing the need for multiple passes and optimizing the material handling process. The wider belt minimizes the risk of spillage and enhances the stability of conveyed materials, contributing to a safer and more efficient working environment. Additionally, the broader surface area allows for the incorporation of various accessories like cleats, guides, and scrapers, further enhancing the conveyor’s versatility.
The specifications of 48 belt conveyors are designed to meet a broad spectrum of industrial applications, providing a reliable solution for efficient material handling. Understanding these specifications is essential for selecting a conveyor belt that will perform effectively, offering the durability and performance required for the specific conditions of each operation.
Key Features and 5 Advantages of the 48 Belt Conveyor
The 48 belt conveyor stands as a cornerstone in the realm of industrial material handling, offering a blend of durability, performance, and versatility unmatched by narrower alternatives. This segment delves into the material and construction quality of 48-inch wide conveyor belts, alongside an analysis of their design features, which collectively optimize material handling across various industries.
Material and Construction Quality
The construction quality of a 48 belt conveyor is paramount, directly influencing its durability and ability to perform under the demanding conditions of industrial environments. These belts are typically made from high-grade materials such as heavy-duty rubber, reinforced nylon, or polyester fabrics, which are chosen for their strength, flexibility, and resistance to wear and tear. The multi-ply construction, involving several layers of these materials, provides added strength and durability, allowing the conveyor belt to handle heavy loads and resist the stresses of continuous operation.
Smooth Top Surface and Sliderback Design
A defining feature of the 48 belt conveyor is its smooth top surface, which facilitates the easy movement of materials across the belt, minimizing resistance and wear both on the belt itself and on the materials being transported. This smooth surface is crucial for maintaining the integrity of fragile or delicate items during transit. The sliderback design, or the bare back of the belt, allows for efficient operation on the conveyor bed, reducing friction and energy consumption, which is particularly beneficial in long-distance conveying applications.
5 Advantages of 48-Inch Wide Conveyor Belts
- Increased Capacity: The width of the 48 belt conveyor inherently allows for a larger carrying capacity compared to narrower belts. This increased capacity enables businesses to move more material in less time, significantly enhancing productivity and operational efficiency.
- Versatility in Applications: Thanks to their robust construction and optimal width, these conveyor belts are versatile enough to be used in a variety of industries, from mining and agriculture to manufacturing and distribution. Whether it’s transporting raw materials, finished products, or anything in between, the 48 belt conveyor can handle it.
- Improved Safety: The wider surface area provides stability for the materials being transported, reducing the risk of spillage or accidents. This feature, combined with the belt’s durable construction, makes the 48 belt conveyor a safer option for workers and materials alike.
- Energy Efficiency: The sliderback design of these conveyor belts minimizes friction against the conveyor bed, leading to lower energy consumption during operation. This efficiency is particularly beneficial for businesses looking to reduce their energy costs and environmental impact.
- Ease of Maintenance: The quality materials and construction of the 48 belt conveyor not only ensure its longevity but also make maintenance easier. The smooth top surface is simpler to clean, and the belt’s durability means that repairs are less frequent, reducing downtime and maintenance costs.
The 48 belt conveyor offers a comprehensive solution to material handling challenges across various sectors. Its construction quality, design features, and the advantages it brings to the table make it an indispensable tool for businesses aiming to optimize their operations, enhance safety, and achieve greater efficiency in their material handling processes.
The Cost Implications of Implementing 48 Belt Conveyor Systems
Implementing a 48 belt conveyor system in an industrial setting involves a thorough examination of various cost factors and an understanding of the investment value it brings. The initial cost of a 48 belt conveyor is influenced by several key factors, including the quality of materials used in its construction, the overall length of the conveyor, and any custom features or specifications required to meet specific operational needs.
Material Quality and Construction Costs
The material quality of a 48 belt conveyor plays a significant role in determining its price. High-quality materials such as reinforced rubber or specialized fabrics designed for durability and longevity tend to increase the cost. However, investing in a conveyor belt with superior wear resistance and strength can significantly reduce maintenance and replacement costs over time, leading to a better return on investment (ROI).
Length and Custom Features
The length of the 48 belt conveyor directly impacts the cost, with longer systems requiring more materials and engineering work, thus increasing the overall price. Additionally, custom features such as integrated sensors, variable speed controls, and specialized belt materials designed for specific types of cargo can further elevate the cost. These customizations, while increasing the upfront investment, can enhance operational efficiency, reduce downtime, and provide a level of automation that may significantly improve the conveyor system’s ROI.
Investment Value and ROI
The investment value of a 48 belt conveyor system extends beyond its initial purchase price. High-quality conveyor belts designed for specific industrial applications can lead to substantial operational efficiencies, including faster production times, reduced labor costs, and minimized product damage. These efficiencies translate into a tangible ROI, as the conveyor system can help to streamline operations, increase output, and ultimately contribute to higher profit margins.
Moreover, the durability and longevity of a well-designed 48 belt conveyor system reduce the need for frequent replacements or repairs, further enhancing its investment value. By carefully selecting a conveyor system that meets the specific needs of an operation, businesses can achieve a balance between upfront costs and long-term benefits, ensuring that the implementation of a 48 belt conveyor system is a financially sound decision.
While the cost implications of implementing a 48 belt conveyor system can be significant, the potential for improved operational efficiency, reduced maintenance costs, and a strong ROI make it a worthwhile investment for many industrial settings. By considering the factors that influence cost and focusing on the long-term benefits, businesses can make informed decisions that support their operational goals and financial health.
Standards and Safety Compliance for the 48 Belt Conveyor
Adhering to standards and safety compliance is critical in the design, selection, and operation of 48 belt conveyors. These regulations ensure that conveyor belts are safe for use and meet the required performance criteria, protecting both workers and materials during operation.
Overview of Standards and Regulations
Standards and regulations governing the use of 48 belt conveyors cover a wide range of aspects, including material quality, design specifications, and safety features. These standards are established by industry organizations and regulatory bodies to ensure that conveyor belts are manufactured to a consistent quality and safety level. Compliance with these standards is essential for manufacturers and users alike, ensuring that conveyor belts are safe, reliable, and suitable for the intended applications.
Importance of Safety and Compliance
Safety and compliance are paramount in the operation of conveyor belts, particularly in industries where the risk of injury or material loss is significant. Adhering to established standards and regulations helps prevent accidents and injuries, ensuring a safe working environment for employees. Compliance also ensures that conveyor belts perform as expected, reducing the risk of operational failures that could lead to downtime or damage to materials. Businesses must prioritize safety and compliance when selecting and operating 48 belt conveyors, ensuring that their equipment meets all relevant standards and regulations.
Standards and safety compliance are essential considerations for 48-inch wide conveyor belts, ensuring that they are manufactured and operated to the highest safety and performance standards. By adhering to these guidelines, businesses can ensure the safety of their operations and the reliability of their conveyor systems, contributing to the overall success of their material handling processes.
Selecting the Right 48 Belt Conveyor Belt for Your Application
Choosing the appropriate 48 belt conveyor for a specific application requires careful consideration of operational needs and material handling requirements. The right conveyor belt can significantly impact the efficiency and productivity of a material handling system, making it crucial to select a belt that is suited to the task at hand.
Guidelines for Selection
When selecting a 48 belt conveyor, several factors must be considered to ensure that the belt meets the specific needs of the application. These factors include the type of materials being conveyed, the environment in which the conveyor will operate, and the required speed and capacity of the system. The physical properties of the materials, such as weight, abrasiveness, and temperature sensitivity, can influence the choice of belt material and construction. Additionally, environmental factors such as exposure to chemicals, moisture, or extreme temperatures must be considered to select a belt that can withstand these conditions without degrading.
Customization Options and Additional Features
48 belt conveyors offer a range of customization options and additional features that can enhance their functionality and efficiency. Customization options may include the addition of cleats or sidewalls to prevent slippage or spillage of materials, coatings or treatments to resist abrasion or chemical damage, and reinforced edges to increase durability. Additional features such as variable speed controls, reversible operation, and integrated sensors can also be incorporated to improve the versatility and performance of the conveyor system. Selecting the right combination of customization options and features requires a thorough understanding of the material handling process and the challenges that the conveyor system must overcome.
Selecting the right 48-inch wide conveyor belt for an application involves a detailed analysis of material handling requirements and operational conditions. By considering these factors and exploring customization options, businesses can ensure that their conveyor belt is perfectly suited to their needs, enhancing efficiency and productivity in their operations.
48 Belt Conveyor: Practical Applications and Case Studies
The 48 belt conveyor has found applications across a diverse range of industries, demonstrating its versatility and effectiveness in optimizing material handling processes. Real-world examples and case studies provide valuable insights into how businesses have leveraged these conveyor belts to achieve operational efficiencies and overcome material handling challenges.
Real-World Examples
In the mining industry, 48 belt conveyors are used to transport large volumes of raw materials over long distances, offering a reliable and efficient means of moving ore from the mine to processing facilities. In the agriculture sector, these conveyors are utilized for the bulk handling of grains and other commodities, streamlining the storage and distribution process. Manufacturing plants also benefit from the use of 48 belt conveyors, where they facilitate the movement of components and finished products through assembly and packaging lines, enhancing productivity and reducing manual labor.
Case Studies
One case study involves a logistics company that implemented a 48 belt conveyor system to optimize its warehousing and distribution operations. The conveyor system was designed to handle a wide range of package sizes and weights, improving the speed and accuracy of order fulfillment. The implementation of the conveyor system resulted in a significant reduction in processing times and operational costs, demonstrating the value of selecting the right conveyor belt for the application.
Another case study focuses on a food processing plant that utilized a 48 belt conveyor with a custom-designed, easy-to-clean surface to maintain hygiene standards while transporting food products. The conveyor’s design allowed for quick and thorough cleaning between batches, ensuring compliance with food safety regulations and minimizing downtime.
These practical applications and case studies highlight the impact of 48-inch wide conveyor belts on improving material handling processes across various industries. By carefully selecting and customizing conveyor belts to meet specific operational needs, businesses can achieve significant efficiencies and enhance their overall productivity.
The exploration of the 48 belt conveyor through specifications, features, cost implications, standards, selection guidelines, and practical applications offers a comprehensive understanding of their role in industrial operations. These insights underscore the importance of careful selection and customization of conveyor belts to meet the unique challenges of different material handling applications, ensuring operational efficiency and success.
FAQs about 48 Belt Conveyor
Belt conveyors come in a variety of sizes to accommodate different industries and applications. The standard widths typically range from 12 inches (300 mm) to 36 inches (900 mm) or more, with lengths varying based on the specific requirements of the system. However, custom sizes are also available to suit unique needs. Commonly used belt widths include 18 inches (450 mm) and 24 inches (600 mm), but these can be adjusted based on the intended use and the material being transported.
The term “M 24” refers to a specific type of conveyor belt. In this context, the “M” stands for the tensile strength of the belt material, and “24” indicates the tensile strength in megapascals (MPa). M 24 belts are designed for medium-duty applications, typically used in industries like mining, cement, and steel. These belts are suitable for conveying moderate loads and are known for their durability and resistance to abrasion.
To size a conveyor belt, you need to consider several factors, including the material type, weight, and dimensions of the load, as well as the conveyor’s speed and incline. The formula for calculating the belt size involves multiplying the length and width of the material being transported, factoring in any additional space needed for cleats, guides, or other accessories. It’s crucial to consult with engineering guidelines and standards to ensure proper sizing and functionality.
The standard length of a conveyor belt can vary depending on the application and industry standards. While there are common lengths, such as 100 feet (30 meters) or 200 feet (60 meters), conveyor belts can be customized to specific requirements. Some industries may require longer or shorter belts based on the layout of the production facility or the distance the material needs to travel. Standardization in length is essential for efficient manufacturing and system integration, but flexibility in length is also a key feature to meet diverse industrial needs.
Last Updated on February 6, 2024 by Jordan Smith
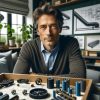
Jordan Smith, a seasoned professional with over 20 years of experience in the conveyor system industry. Jordan’s expertise lies in providing comprehensive solutions for conveyor rollers, belts, and accessories, catering to a wide range of industrial needs. From initial design and configuration to installation and meticulous troubleshooting, Jordan is adept at handling all aspects of conveyor system management. Whether you’re looking to upgrade your production line with efficient conveyor belts, require custom conveyor rollers for specific operations, or need expert advice on selecting the right conveyor accessories for your facility, Jordan is your reliable consultant. For any inquiries or assistance with conveyor system optimization, Jordan is available to share his wealth of knowledge and experience. Feel free to reach out at any time for professional guidance on all matters related to conveyor rollers, belts, and accessories.