6 Roller Conveyor Systems | Advanced Material Handling
Roller conveyors are essential components in material handling, providing an efficient way to move products across various stages of production and distribution. These systems are widely used in industries such as warehousing, shipping, and assembly due to their simplicity and effectiveness. In particular, the 6 roller conveyor stands out for its versatility and efficiency. Designed with 6-inch diameter rollers, this conveyor type is ideal for handling lightweight to moderately heavy items, ensuring smooth and consistent movement. By focusing on the unique advantages of 6 roller conveyor, businesses can enhance their operational efficiency, reduce manual labor, and streamline their material handling processes.
What Is 6 Roller Conveyor
6 roller conveyors are integral components in many industrial processes, designed to facilitate the efficient and safe transport of goods. Primarily used in settings such as manufacturing plants, distribution centers, and warehouses, these conveyors simplify processes and improve productivity. Below, we will delve into the specifics of what 6-inch roller conveyors are, their typical dimensions and components, and their key specifications and features.
- Material Handling Systems: 6-inch roller conveyors are essential material handling systems used to transport items across various industrial and commercial settings.
- Six-Inch Diameter Rollers: They feature rollers that are specifically six inches in diameter, providing a balance between load capacity and smooth operation.
- Efficient Transportation: These conveyors are designed for efficient movement of goods, minimizing manual labor and increasing throughput.
- Versatility: Suitable for various applications including warehousing, assembly lines, and shipping departments, thanks to their adaptable design.
- Durable Construction: Constructed from robust materials like steel or aluminum, ensuring longevity and durability under heavy use.
- Low Maintenance: Designed for low maintenance with easily replaceable parts and durable components.
- Cost-Effective: Offer a cost-effective solution for transporting goods, reducing the need for forklifts and other handling equipment.
- Customizable Options: Available with various customization options such as different roller materials, lengths, and frame constructions to meet specific operational needs.
The Typical Dimensions and Components of a 6 Roller Conveyor
A 6 roller conveyor typically includes a variety of components that work together to move goods effectively. The dimensions are chosen to optimize the balance between the system’s capacity and its footprint in the facility.
- Dimensions: Typically, a 6 roller conveyor might have rollers that are 1.9 inches in diameter and a conveyor width ranging from 18 to 30 inches. Lengths can vary, with common options being 3, 5, or 10 feet.
- Frame: The frame is usually made of steel for maximum strength and durability, though aluminum frames are also available for lighter applications.
- Rollers: Made of steel, stainless steel roller, or plastic, chosen based on the environment and type of goods being conveyed. Each material has its specific advantages; for instance, steel rollers are highly durable and suitable for heavy loads, while plastic rollers are lightweight and resistant to corrosion. A stainless steel roller, on the other hand, offers a balance of durability and resistance to corrosion, making it ideal for environments that require both strength and hygiene, such as food processing or pharmaceuticals.
- Bearings: High-quality bearings are used to ensure smooth and efficient roller movement, reducing friction and wear.
- Drive System: Can be manual or motorized, with motorized options providing consistent speed and automation.
- Supports: Adjustable height supports are included to ensure the conveyor can be set to the optimal working height.
- Side Guards: Optional side guards to prevent items from falling off during transportation.
- End Stops: End stops can be added to control the flow of items and ensure they do not roll off the conveyor at the end.
Key Specifications and Features
The 6 roller conveyor comes with a range of specifications and features designed to meet the diverse needs of different industries. These specifications define the conveyor’s capacity, efficiency, and suitability for various applications.
- Load Capacity: Capable of handling loads up to 250 pounds per linear foot, suitable for a variety of goods from small packages to heavier items.
- Roller Material Options: Rollers can be made from steel, stainless steel, or plastic to cater to different operational environments and product requirements.
- Frame Material: Frames are typically constructed from high-strength steel or lightweight aluminum, depending on the application needs.
- Length Variations: Available in multiple lengths, generally starting from 3 feet up to 10 feet, to fit different operational spaces and needs.
- Height Adjustability: Many models offer adjustable heights to ensure ergonomic working conditions and easy integration into existing systems.
- Mobility Options: Can be equipped with casters for easy movement and repositioning within a workspace, enhancing flexibility.
- Drive Systems: Available with manual drives, motorized rollers, or belt-driven systems to accommodate different speed and control requirements.
- Customizable Accessories: Can include side guards, end stops, and connecting brackets to tailor the conveyor to specific tasks and enhance functionality.
The 6 roller conveyor is a versatile and efficient solution for modern material handling needs, offering a range of customizable features and robust specifications to meet diverse operational requirements.
Types of 6 Roller Conveyor
6 roller conveyors are available in various configurations to meet the specific needs of different industries and applications. The primary types include straight conveyors, 90-degree curve conveyors, angle end stops, and side guards. Each type serves a unique purpose and offers specific advantages in a material handling setup.
Straight Conveyors
Straight 6 roller conveyors are the most common type, designed to move items in a linear path from one point to another. They are ideal for applications where goods need to be transported over a flat, straight distance without any changes in direction.
Key Features of Straight Conveyors
- Length Options: Available in multiple lengths, typically ranging from 3 to 10 feet, allowing for customization based on space requirements.
- Material Construction: Frames are usually made of durable steel or aluminum, providing strength and longevity.
- Roller Material: Rollers can be made from steel, stainless steel, or plastic, chosen based on the specific needs of the application.
- Load Capacity: Designed to handle a wide range of loads, often up to 250 pounds per linear foot.
- Height Adjustability: Many straight conveyors come with adjustable legs to set the optimal working height.
- Mobility: Some models feature casters for easy repositioning within a workspace.
- Ease of Installation: Straight conveyors are straightforward to install and integrate with existing systems.
- Cost-Effectiveness: They offer a cost-effective solution for simple material transport needs.
90-Degree Curve Conveyors
90-degree curve conveyors are designed to change the direction of the transported items by 90 degrees. This type is essential in spaces where the layout requires a turn, optimizing the use of available space.
Key Features of 90-Degree Curve Conveyors
- Space Utilization: Ideal for maximizing space efficiency in confined areas.
- Smooth Transition: Designed to ensure smooth and seamless transition of items around the curve.
- Robust Construction: Typically built with a sturdy frame to handle the forces exerted during directional changes.
- Customizable Radius: Available with different radius options to fit various layout needs.
- Roller Spacing: Close roller spacing ensures smaller items can navigate the curve without falling.
- Load Capacity: Capable of handling similar loads as straight conveyors, up to 250 pounds per linear foot.
- Integration: Easily integrates with straight conveyors to form a continuous system.
- Maintenance: Low maintenance due to durable components designed to withstand directional changes.
Angle End Stops
Angle end stops are accessories used at the end of a conveyor to prevent items from rolling off the edge. They are critical for maintaining control and safety in a conveyor system.
Key Features of Angle End Stops
- Safety: Prevents items from falling off the conveyor, enhancing safety.
- Easy Installation: Simple to install at the end of any conveyor segment.
- Material Options: Available in various materials such as steel or plastic.
- Adjustability: Some models offer adjustable angles to accommodate different item sizes and shapes.
- Compatibility: Designed to be compatible with various types of conveyors, including straight and curved models.
- Durability: Made from robust materials to withstand impact and repeated use.
- Cost-Effective: An affordable solution to enhance conveyor safety.
- Customizable: Can be tailored to specific requirements, including size and mounting options.
Side Guards
Side guards are used along the sides of a conveyor to keep items from falling off the sides. They are especially useful when transporting smaller items or when the conveyor is used at an incline.
Key Features of Side Guards
- Enhanced Safety: Keeps items within the conveyor path, preventing falls and ensuring safe transport.
- Material Construction: Typically made from steel, aluminum, or plastic, depending on the application.
- Height Options: Available in various heights to accommodate different item sizes.
- Adjustability: Some models offer adjustable side guards to fit various item widths.
- Ease of Installation: Simple to attach to existing conveyors with minimal tools.
- Durability: Built to withstand the demands of industrial environments.
- Customizable Lengths: Can be ordered in different lengths to match the conveyor system.
- Aesthetic Appeal: Provides a clean and organized appearance to the conveyor system, enhancing overall workplace aesthetics.
Each of these types of 6 roller conveyors and their accessories plays a crucial role in creating efficient, safe, and flexible material handling systems, tailored to meet the unique demands of various industrial applications.
Applications of 6 Roller Conveyor
6-inch roller conveyors are highly versatile and play a crucial role in improving operational efficiencies across a wide array of industries. From warehousing and shipping to manufacturing, these systems are designed to handle a variety of tasks with precision and speed. Their adaptability and reliability make them indispensable in modern industrial environments, ensuring continuous movement of goods and materials with minimal downtime.
Common Uses in Various Industries
6-inch roller conveyors are foundational in enhancing the efficiency and productivity of various industrial operations. Below, we detail their pivotal roles specifically within warehousing and shipping departments. The adaptability of these systems allows them to seamlessly integrate into existing operations, improving not only speed but also the overall quality of the workplace environment.
Warehousing
Warehousing operations depend significantly on the efficiency of material handling systems. 6-inch roller conveyors enhance this efficiency, facilitating better space management, safety, and productivity.
- Enhanced Storage Capacity: Optimizes warehouse space by allowing higher and more compact storage.
- Improved Retrieval Speed: Speeds up the process of picking and packing by providing smoother movement of goods.
- Reduced Labor Costs: Minimizes manual labor requirements by automating the transport of goods across the warehouse.
- Increased Safety: Lowers the risk of accidents by reducing the need for forklifts and manual handling of heavy items.
- Better Inventory Control: Integrates with inventory management systems to provide real-time tracking and management of goods.
- Streamlined Receiving and Shipping: Speeds up the processes of receiving new shipments and preparing goods for dispatch.
Shipping Departments
In shipping departments, 6 roller conveyors are essential for maintaining the pace and accuracy of outgoing shipments, ensuring that products are delivered on time and in good condition.
- Faster Order Processing: Reduces time between order receipt and dispatch, enhancing customer satisfaction.
- Improved Sorting Efficiency: Automatically sorts items based on destination or shipping method, reducing errors.
- Scalable Operations: Easily scales operations up or down based on seasonal demand fluctuations.
- Enhanced Tracking Capabilities: Works with systems designed to track parcels through the shipping process.
- Reduced Bottlenecks: Eliminates bottlenecks in packaging and dispatch areas, improving overall flow.
- Cost Efficiency: Lowers operational costs by improving the speed and efficiency of shipping processes.
Assembly Areas
In assembly areas, 6-inch roller conveyors are vital for maintaining a seamless flow of components and finished products, ensuring that assembly processes are as efficient as possible.
- Streamlined Production Lines: Enhances the speed and efficiency of production lines.
- Error Reduction: Reduces human error by automating the movement of parts to assembly stations.
- Flexibility in Manufacturing: Adapts easily to different product sizes and types, providing versatility.
- Improved Work Conditions: Reduces physical strain on workers by automating the transport of heavy or awkward items.
- Increased Output: Allows for higher production output by minimizing delays between assembly stages.
- Enhanced Quality Assurance: Facilitates better quality control by ensuring products pass through all required checks.
Specific Tasks Where 6 Roller Conveyor Excels
6 roller conveyors are not only fundamental components for general material handling but also excel in performing specific tasks that require precision, efficiency, and adaptability. In automated sorting systems, these conveyors demonstrate remarkable capabilities that streamline operations and enhance productivity. Below, we detail the specific advantages that 6 roller conveyors bring to automated sorting systems and how they transition into optimizing assembly line operations.
Automated Sorting Systems
Automated sorting systems greatly benefit from the integration of 6 roller conveyor, which improve sorting accuracy and speed.
- High-Speed Sorting: Capable of sorting products at high speeds based on size, type, or destination.
- Advanced Sensors Integration: Utilizes integrated sensors to sort products accurately, enhancing operational efficiency.
- Flexibility: Adapts to various product specifications and sorting criteria without needing extensive reconfiguration.
- Reduced Error Rates: Decreases the likelihood of errors in sorting, ensuring accurate order fulfillment.
- Energy Efficiency: Uses energy-efficient motors and controls to minimize power consumption during operation.
- System Integration: Seamlessly integrates with existing warehouse management systems (WMS) and other automation systems.
Assembly Line Operations
6 roller conveyors facilitate a variety of assembly line operations, from simple to complex, by ensuring materials flow smoothly between processes.
- Continuous Flow: Maintains a continuous flow of materials, essential for just-in-time manufacturing processes.
- Adaptive Interfaces: Interfaces with various machines and equipment along the assembly line, promoting a cohesive operation.
- Modularity: Offers the ability to reconfigure assembly lines quickly for different products or processes.
- Precision Handling: Delivers components to exact locations, reducing the need for manual adjustment.
- Downtime Reduction: Minimizes production downtime by ensuring a steady supply of materials to workstations.
- Labor Efficiency: Reduces the labor required for manual handling and transportation of materials across the assembly floor.
By enhancing these specific areas of operation, 6 roller conveyors ensure that industries not only meet their productivity goals but also improve their operational efficiencies and product quality, reinforcing their essential role in modern industrial operations.
Advantages of Using 6 Roller Conveyor
6 roller conveyors offer significant benefits across various industries due to their design, which emphasizes efficiency, versatility, and ease of installation. Here are the key advantages of using these conveyors:
- High Throughput: Capable of handling large volumes of products efficiently, ensuring high operational throughput.
- Energy Efficiency: Utilizes energy-saving components, reducing operational costs and environmental impact.
- Streamlined Operations: Minimizes the need for manual handling, speeding up processes and reducing labor costs.
- Adaptable to Various Products: Can convey a wide range of product sizes and weights, making it versatile for different industry needs.
- Modular Design: Allows for easy expansion or reconfiguration, providing flexibility as business needs change.
- Quick Installation: Designed for easy setup, which reduces downtime and speeds up integration into existing systems.
- Low Maintenance: Requires minimal maintenance, which lowers the total cost of ownership and reduces downtime.
- User-Friendly: Simple to operate, requiring minimal training for staff, which reduces operational complexity.
- Minimal Pitch Required: Efficiently moves products with minimal pitch, allowing for smoother transitions and less space required for inclines.
- Gentle Handling: Reduces potential damage to delicate products, ensuring they maintain their quality and integrity during transport.
- Reliable Transport: Offers consistent and reliable transportation of goods, maintaining steady workflow and productivity.
- Stable Movement: Provides stable and controlled conveyance, crucial for precision-dependent industries.
- Space Optimization: Its compact design optimizes facility space, essential in environments where floor space is at a premium.
- Vertical Handling Capability: Suitable for vertical transport solutions, maximizing vertical space utilization.
- Seamless System Integration: Easily integrates with other conveyor systems and automation technologies, enhancing overall system efficiency.
- Safety Features: Incorporates safety mechanisms that reduce the risk of workplace injuries, improving overall workplace safety.
- Ergonomic Design: Promotes better ergonomics, reducing strain and fatigue among workers, which can lead to increased productivity.
These advantages make 6 roller conveyors a valuable asset for businesses looking to improve their material handling processes, enhance safety, and increase efficiency.
Buying Guide for 6 Roller Conveyor
When purchasing a 6 roller conveyor, it’s essential to consider several key factors to ensure that you select the right system for your specific needs. This guide will help you understand the critical aspects to look at when choosing a 6 roller conveyor.
- Length Options: Consider the available lengths of the conveyor. Common lengths include 3 feet and 5 feet, but ensure that the chosen length fits your space and meets your operational requirements.
- Weight Capacity Options: Assess the weight capacity that the conveyor can handle. Typical capacities might range from 36 lbs to 55 lbs per foot. Choose a capacity that accommodates your heaviest loads without compromising system integrity.
- Material and Construction Quality: Evaluate the materials used in the construction of the conveyor. High-quality steel or aluminum offers durability and longevity, while the choice of roller material (plastic, steel, or stainless steel) can impact the conveyor’s suitability for different environments.
- Price Considerations: Budget is always a crucial factor. Compare the price against the features and longevity provided. Remember that the cheapest option isn’t always the most cost-effective in the long run if it requires frequent repairs or replacements.
- Modular Design: Check if the conveyor offers modular design features. This allows for easier modifications and expansions in the future, which can be a cost-effective way to scale your system as your needs grow.
- Ease of Maintenance: Look for conveyors that are easy to maintain. Systems with easily accessible parts and simple assembly/disassembly processes reduce downtime and maintenance costs.
- Customization Options: Some conveyor systems offer customization options such as adjustable heights, reversible conveying, or special coatings for rollers that might be necessary for handling specific materials or operating in certain environments.
- Safety Features: Ensure that the conveyor includes necessary safety features such as emergency stops, guards, and handrails to protect users and maintain compliance with industry safety standards.
- Warranty and Support: Consider the warranty offered with the conveyor. A comprehensive warranty can provide peace of mind, while strong customer support can ensure quick resolution of any issues post-purchase.
By carefully considering these factors, you can make an informed decision that ensures the 6 roller conveyor you purchase will efficiently meet your operational requirements while offering the best value for your investment.
Price and Availability of 6 Roller Conveyor
When considering the acquisition of a 6 roller conveyor, it is crucial to have a clear understanding of the financial implications, the range of options available in the market, and strategies to secure the best possible deal. This guide is designed to help you navigate through the pricing landscape, identify the best places to shop for 6 roller conveyors, and provide practical tips for making the most economical purchase.
Overview of the Price Range for 6 Roller Conveyor
Pricing for 6 roller conveyors can vary significantly based on several factors including build quality, capacity, and additional features. Understanding the spectrum of prices available will help you budget effectively and choose a model that meets your needs without overspending.
- Entry-Level Systems: Typically priced between $200 to $400, these conveyors are basic, ideal for light applications, and generally have lower weight capacities.
- Standard Industrial Models: Ranging from $500 to $1,200, these models offer better build quality and can handle moderate to heavy usage, suitable for most industrial applications.
- High-Capacity Systems: For heavy-duty industrial use, these conveyors can cost anywhere from $1,500 to $3,000 or more, featuring robust construction and high weight capacities.
- Custom Solutions: Tailored to specific needs, custom conveyor systems can vary in price but typically start around $2,000 and can go much higher based on complexity and specifications.
- Additional Features: Add-ons like advanced control systems, adjustable speeds, and integrated sensors can increase the price but add significant value in terms of versatility and automation.
- Warranty and Support: Models that come with extended warranties and superior customer support might command a premium, reflecting the long-term reliability and service benefits.
Where to Find 6 Roller Conveyors for Sale
Finding the right supplier for a 6 roller conveyor is crucial as it affects not just cost but also the quality and reliability of your purchase. Here are several avenues where you can find these systems for sale:
- Manufacturer Direct: Purchasing directly from the manufacturer is often the best way to get a newly minted product with full warranty and support.
- Industrial Supply Companies: These companies stock a variety of models from different brands and offer a range of price points.
- Online Industrial Marketplaces: Platforms like ThomasNet, Direct Industry, or even Amazon Business can offer competitive prices and a broad selection.
- Second-Hand Machinery Dealers: A cost-effective option for many, especially if you require a high-end system without the new price tag.
- Local Machinery Auctions: Keep an eye out for auctions which can be a goldmine for bargains on industrial equipment.
- Trade Shows and Expositions: These events not only allow you to see the equipment in action but also to negotiate deals directly with suppliers.
Tips on Getting the Best Deals
Securing the best deal on a 6 roller conveyor involves more than just finding the lowest price; it requires strategic planning and timing. Below are strategies to ensure you maximize value:
- Bulk Purchase Discounts: If you need multiple units, look for bulk purchase discounts which can significantly lower the per-unit cost.
- End-of-Fiscal Year Sales: Many suppliers offer discounts at the end of their fiscal year as they look to clear inventory.
- Compare Quotes: Always get quotes from several suppliers to compare prices and package deals.
- Lease or Finance Options: Consider leasing or financing options which can ease upfront costs and offer tax advantages.
- Check for Overstock Deals: Suppliers might offer discounts on overstock items, particularly older models.
- Barter for Extras: When negotiating, don’t just focus on price. Try to get add-ons included such as installation or extended service.
- Sign Up for Newsletters: Often, the best deals are sent directly to subscribers before they are made public.
With these insights into price ranges, shopping avenues, and purchasing strategies, you are well-equipped to make an informed and cost-effective decision when buying a 6 roller conveyor.
FAQs about 6 Roller Conveyor
The standard size of a roller conveyor can vary widely depending on the application and industry it is intended for. Generally, roller conveyors come in a variety of widths and lengths. Common widths are typically between 12 inches and 36 inches, though conveyors can be custom-made to wider dimensions if required. Lengths of roller conveyors can be anything from a few feet for small operations to hundreds of feet for larger industrial uses. Each segment of a roller conveyor is usually a few feet long, and they are connected to form the needed total length. The roller diameter also forms an essential part of the conveyor’s size, with common diameters ranging from 1.5 inches to 3.5 inches. The size choice depends largely on the size and weight of items the conveyor will transport, as well as the overall layout of the area where the conveyor will be installed.
The capacity of a roller conveyor refers to the maximum weight it can handle while operating effectively. This capacity can greatly vary depending on the construction and design of the conveyor. Smaller roller conveyors might handle just a few pounds per roller, suitable for lightweight materials or small items, while larger, heavy-duty conveyors can handle several hundred pounds per roller. Capacity is also influenced by the spacing of rollers, material, and the type of bearings used. For instance, conveyors used in heavy industries such as automotive manufacturing or heavy appliance handling are designed to withstand substantial loads, often equipped with reinforced frames and thicker rollers. When selecting a roller conveyor, it’s crucial to consider the typical and maximum weight of the items to be conveyed to ensure optimal performance and longevity of the equipment.
Roller conveyors are categorized mainly by the method of actuation and load-handling capability. The primary types include:
Gravity Roller Conveyors: These utilize the force of gravity to move items across the horizontal or slightly inclined paths. They are ideal for situations where items need to be moved quickly over short to medium distances.
Powered Roller Conveyors: These conveyors use motorized rollers to move items along the conveyor path. They are suitable for a wide range of industrial applications, particularly where precise control of movement is required.
Accumulating Roller Conveyors: Designed to allow the conveyor to accumulate items in certain sections of the line. These systems are equipped with mechanisms to control the pressure exerted on the items to prevent damage.
Flexible Roller Conveyors: These are versatile and can be adjusted in length and routing. They are ideal for environments where conveyor paths might need to be changed frequently.
Each type serves different operational needs and is chosen based on factors like load type, volume, environmental conditions, and operational goals.
The rollers on a conveyor are cylindrical components that rotate to facilitate the movement of items along the conveyor belt or within the conveyor structure itself. They are a critical component of any conveyor system. Rollers are typically mounted within a frame and spaced at regular intervals to support and transport goods smoothly. They can be made from various materials including steel, aluminum, plastic, or even specialized composites, depending on the application. The choice of material affects the roller’s durability, friction, and impact resistance. Rollers can also be coated or treated to improve grip, reduce noise, or resist environmental challenges such as corrosion. The design and functionality of the rollers can significantly influence the efficiency and effectiveness of a conveyor system.
Last Updated on May 22, 2024 by Jordan Smith
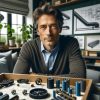
Jordan Smith, a seasoned professional with over 20 years of experience in the conveyor system industry. Jordan’s expertise lies in providing comprehensive solutions for conveyor rollers, belts, and accessories, catering to a wide range of industrial needs. From initial design and configuration to installation and meticulous troubleshooting, Jordan is adept at handling all aspects of conveyor system management. Whether you’re looking to upgrade your production line with efficient conveyor belts, require custom conveyor rollers for specific operations, or need expert advice on selecting the right conveyor accessories for your facility, Jordan is your reliable consultant. For any inquiries or assistance with conveyor system optimization, Jordan is available to share his wealth of knowledge and experience. Feel free to reach out at any time for professional guidance on all matters related to conveyor rollers, belts, and accessories.