Conveyor Belt Scale Calibration:Tutorial And Precautions
Conveyor belt scale calibration is essential for ensuring the accuracy and reliability of material measurement in various industrial settings.Conveyor belt scale calibration need periodic calibration; perform daily zero calibration by running an empty belt to ensure accuracy. Proper conveyor belt scale calibration allows for precise operational data, which is crucial for production decisions and maintaining efficiency. This blog post will explore the principles, methods, and importance of conveyor belt scale calibration, providing a comprehensive guide for industry professionals. By understanding the intricacies of conveyor belt scale calibration, you can enhance measurement accuracy, optimize operational processes, and ensure compliance with industry standards. Regular and accurate conveyor belt scale calibration is vital for maintaining the integrity of your weighing systems and ensuring seamless production workflows.
Mastering Conveyor Belt Scale Calibration Formulas
The Importance of Calibration Formulas
Calibration formulas are crucial mathematical expressions used in the conveyor belt scale calibration process. These formulas are designed to adjust and fine-tune the scales, ensuring they provide accurate weight readings. By applying these formulas, operators can compensate for any discrepancies that arise during the measurement process, which is essential for maintaining the precision and reliability of material measurements in industrial settings.
Accurate conveyor belt scale calibration is vital for companies like Siemens and Thermo Fisher Scientific, which rely on precise material measurements to control production processes and ensure product quality. For instance, in the mining industry, accurate weight readings are crucial for managing ore extraction rates and optimizing resource usage. Without proper calibration, weight readings could be skewed, leading to significant errors in production data and potentially causing substantial financial losses.
Key Calibration Formulas
- Zero Calibration Formula: The zero calibration formula is used to ensure that the scale reads zero when no material is present on the conveyor belt. This is a fundamental step in the conveyor belt scale calibration process, as it establishes a baseline measurement. For example, in a manufacturing plant, the zero calibration formula might be applied at the start of each shift to ensure the scales are correctly set before production begins.
- Span Calibration Formula: Span calibration involves setting the scale to accurately measure a known weight. This is done by placing a certified weight or test chain on the belt and adjusting the scale until the correct weight is displayed. The span calibration formula ensures that the scale provides accurate readings across its entire range. In industries such as agriculture, where accurate weight measurements of harvested crops are essential, span calibration helps maintain the integrity of the data collected by conveyor belt scales.
Applying Calibration Formulas
Applying conveyor belt scale calibration formulas is a critical practice for maintaining the accuracy of weight measurements. Regular application of both the zero and span calibration formulas is necessary to ensure the scales remain reliable over time. Here are some practical steps and examples of how these formulas are applied in real-world scenarios:
- Zero Calibration:
- Run the conveyor belt empty to ensure no material is present.
- Apply the zero calibration formula to adjust the scale to read zero.
- This process is often performed daily in facilities like bulk material handling plants, where accurate initial measurements are crucial for operational efficiency.
- Span Calibration:
- Use certified weights or test chains to perform span calibration. For instance, a 50 kg certified weight might be used to calibrate the scale.
- Adjust the scale until it displays the exact weight of the certified object.
- Companies such as Avery Weigh-Tronix provide calibration services and certified weights to ensure that span calibration is conducted accurately.
In a large cement manufacturing plant, for example, conveyor belt scales are used to measure the amount of raw material fed into the kilns. Regular application of span calibration formulas ensures that the scales provide precise measurements, which is critical for maintaining the correct mix of raw materials and producing high-quality cement. By using certified weights and performing routine calibrations, the plant can avoid discrepancies in material input, which could lead to product inconsistencies and increased operational costs.
The Role of Conveyor Belt Scale Calibration in Industry
Conveyor belt scale calibration is a vital practice across various industries, including mining, manufacturing, agriculture, and logistics. Companies like Siemens, Thermo Fisher Scientific, and Avery Weigh-Tronix have developed sophisticated calibration technologies and services to support accurate weight measurements in these sectors.
For example, in the mining industry, accurate weight measurements are crucial for managing the extraction and processing of ores. Miscalibrated scales can lead to incorrect data, affecting production efficiency and profitability. In agriculture, accurate weight measurements of harvested crops are essential for inventory management and sales. By regularly applying conveyor belt scale calibration formulas, farmers can ensure they are providing precise weight data to buyers, enhancing trust and business relationships.
In the logistics industry, accurate weight measurements are necessary for calculating shipping costs and ensuring compliance with transportation regulations. Companies like FedEx and UPS rely on well-calibrated conveyor belt scales to determine the weight of packages and optimize their shipping processes. Regular calibration helps these companies maintain accuracy in their billing systems and avoid potential disputes with customers over weight discrepancies.
Conveyor belt scale calibration is an integral part of maintaining the accuracy and reliability of material measurement systems. By understanding and applying calibration formulas, industries can ensure precise weight readings, optimize their operations, and enhance overall efficiency. Regular calibration not only supports accurate data collection but also helps companies comply with industry standards and regulations, ultimately contributing to their success and sustainability.

How Do Conveyor Belt Scales Work
Conveyor belt scales are used to measure the weight of material being transported on a conveyor belt. Here’s a brief explanation of how they work:
- Load Cells: Conveyor belt scales are equipped with load cells, which are sensors that detect the weight of the material on the conveyor belt. These load cells are strategically placed under the conveyor belt to measure the force exerted by the material.
- Belt Speed Sensor: A speed sensor is used to measure the speed of the conveyor belt. This sensor ensures accurate weight calculations by providing real-time data on how fast the belt is moving.
- Integration: The load cell data and the belt speed data are sent to a digital integrator. The integrator processes these inputs to calculate the flow rate (i.e., the amount of material passing over the scale per unit of time) and the total weight of material that has been conveyed.
- Calibration: Conveyor belt scales must be calibrated to ensure accuracy. Calibration involves setting the scale to zero with no load and using test weights to verify its accuracy.
- Output: The processed data is displayed on a control panel, providing operators with real-time information on the weight and flow rate of the material. This information can also be transmitted to other systems for monitoring and control purposes.
Conveyor belt scales work by using load cells to measure the weight of the material, a speed sensor to monitor the belt speed, and an integrator to calculate the flow rate and total weight, ensuring accurate measurement of materials transported on the conveyor.
How to Calibrate Conveyor Belt Scales
Calibrating conveyor belt scales is essential for accurate weighing and maintaining efficiency in material handling operations. Here is a step-by-step guide to calibrating conveyor belt scales:
Tools and Equipment Needed:
- Calibration weights or a known material weight
- Wrenches and other tools as specified by the scale manufacturer
- Calibration test chain (if applicable)
- Scale manual and calibration certificate
Steps to Calibrate Conveyor Belt Scales:
Safety First:
- Ensure that the conveyor is turned off and locked out before beginning any calibration work.
- Follow all safety protocols to prevent accidents.
Prepare the Scale:
- Clean the belt and scale area to remove any debris or buildup that could affect calibration.
- Inspect the conveyor belt and scale for any signs of wear or damage. Repair any issues before proceeding.
Zero Calibration:
- Turn on the conveyor and let it run empty for a few minutes to ensure it’s operating normally.
- Access the scale’s control panel and select the zero calibration mode.
- Adjust the scale to zero with the belt running empty. This ensures that the weight of the belt itself is not factored into the measurement.
Span Calibration:
- Place the calibration weights or known material weight on the conveyor belt. The weight should be evenly distributed.
- Enter the known weight value into the scale’s control panel.
- The scale should now be adjusted to match the known weight, completing the span calibration.
Dynamic Calibration (if applicable):
- Some conveyor belt scales require dynamic calibration, which involves running a known weight (e.g., test chain) across the scale while the conveyor is in motion.
- Follow the manufacturer’s instructions for performing dynamic calibration.
Verify Calibration:
- After calibration, run a test by placing a known weight on the conveyor and compare the scale reading to the actual weight.
- If the readings match, the calibration is successful. If not, adjust the scale settings and repeat the process until accurate readings are achieved.
Documentation:
- Record the calibration results in the logbook or system. Include the date, time, calibration weights used, and any adjustments made.
- Ensure the calibration certificate is updated and kept for future reference.
Regular Maintenance:
- Schedule regular calibration checks based on the manufacturer’s recommendations and the operational environment.
- Periodically inspect the conveyor and scale system to ensure consistent accuracy.
Additional Tips:
- Environmental Factors: Consider temperature, humidity, and vibration, which can affect scale accuracy.
- Professional Help: If calibration seems complex or inaccurate readings persist, consult with a professional technician or the scale manufacturer.
By following these steps, you can ensure that your conveyor belt scales are calibrated correctly and provide accurate weight measurements for your operations.

Understanding Conveyor Belt Scale Calibration
Components of a Belt Scale
- Load Cells: Load cells are the sensors that detect the weight of the material on the conveyor belt. They convert the mechanical force of the material into an electrical signal that can be measured and recorded. The accuracy and reliability of load cells are paramount in the conveyor belt scale calibration process. Companies like Siemens and Thermo Fisher Scientific offer advanced load cells designed to withstand harsh industrial environments while providing precise measurements.
- Speed Sensors: Speed sensors are devices that measure the speed of the conveyor belt. These sensors are typically installed at the conveyor’s tail pulley or other suitable locations to capture accurate speed data. The speed measurement is critical for calculating the material flow rate, a key parameter in conveyor belt scale calibration. For instance, a speed sensor failure in a cement plant could lead to significant discrepancies in the amount of raw material fed into the kilns, affecting the quality of the final product.
- Weigh Bridge: The weigh bridge is the structure that supports the load cells and transfers the weight of the material to them. It is an integral part of the conveyor belt scale system, ensuring that the load cells receive consistent and accurate weight data. The design and installation of the weigh bridge are crucial for effective conveyor belt scale calibration. Poor installation or misalignment can lead to erroneous weight measurements, compromising the entire calibration process.
Integrating Data for Accurate Measurement
The data collected from the load cells and speed sensors are integrated to calculate the total weight of the material passing over the conveyor belt. This integrated data is then used to provide accurate weight measurements, usually displayed in units such as tons per hour. The process of integrating these data points is a key aspect of conveyor belt scale calibration, ensuring that the measurements are reliable and precise.
For instance, in a large-scale agricultural operation, conveyor belt scale calibration ensures that the weight of harvested crops is measured accurately as they move from the fields to storage facilities. This accuracy is crucial for inventory management and sales, as any discrepancies in weight measurements can lead to financial losses and operational inefficiencies.
In the steel manufacturing industry, companies like ArcelorMittal rely on precise conveyor belt scale calibration to measure the weight of raw materials entering their furnaces. Accurate weight measurements are essential for maintaining the correct mix of materials, ensuring product quality, and optimizing production processes.
Conveyor belt scale calibration is a complex process that involves integrating data from load cells and speed sensors to provide accurate weight measurements. This process is critical for maintaining operational efficiency, ensuring product quality, and optimizing resource use in various industrial settings. By understanding the working principles and components involved in conveyor belt scale calibration, industry professionals can enhance the accuracy and reliability of their material measurement systems.
Understanding the Conveyor Belt Scale Calibration Weighing System
Components of the Weighing System
A thorough understanding of the conveyor belt scale calibration weighing system is essential for maintaining accurate and reliable weight measurements. The system comprises several key components that work together to measure the weight of materials moving along the conveyor belt. Regular calibration of these components is crucial to ensure precise measurements.
Integrator
The integrator is a critical device in the conveyor belt scale calibration weighing system. It processes signals from the load cells and speed sensors to calculate the material weight. The integrator receives electrical signals from the load cells, which measure the weight of the material, and from the speed sensors, which track the conveyor belt’s speed. By combining these signals, the integrator calculates the flow rate and total weight of the material passing over the conveyor belt.
For instance, Thermo Fisher Scientific offers advanced integrators like the Ramsey Micro-Tech 3000 series, which provide accurate processing of weight and speed data. These integrators are equipped with sophisticated algorithms that enhance the precision of the conveyor belt scale calibration, ensuring that even minor discrepancies are accounted for and corrected.
Display Unit
The display unit is another essential component of the conveyor belt scale calibration weighing system. It shows the weight measurements and other relevant data, allowing operators to monitor the system’s performance in real-time. The display unit typically includes an LCD or LED screen that presents data such as the current weight, totalized weight, and flow rate.
Siemens’ SIWAREX WT231 is an example of a high-quality display unit used in conveyor belt scale calibration systems. It provides clear and precise weight readings, which are crucial for making informed operational decisions. By regularly calibrating the display unit, operators can ensure that the weight data presented is accurate and reliable.
Control System
The control system allows operators to adjust settings and calibrate the scale. It provides the interface through which calibration routines are initiated and managed. The control system includes software that facilitates zero and span calibration, ensuring that the weighing system maintains its accuracy over time.
METTLER TOLEDO offers comprehensive control systems like the IND560, which supports various calibration methods and provides advanced diagnostic features. These control systems are integral to the conveyor belt scale calibration process, enabling operators to fine-tune the weighing system for optimal performance.
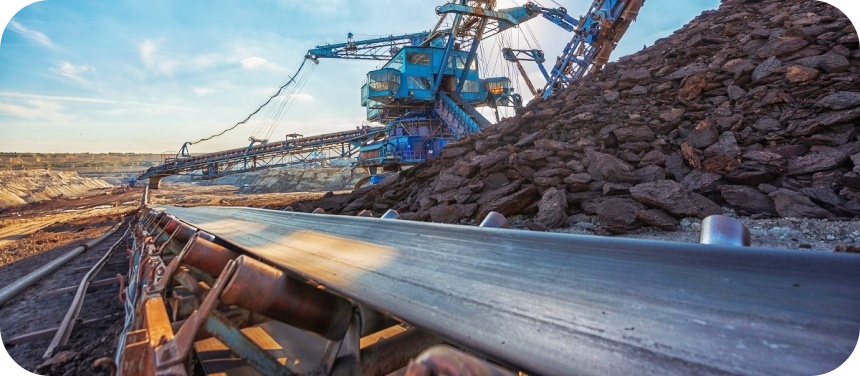
The Role of Calibration in Weighing Systems
Regular calibration is fundamental to the accuracy and reliability of the conveyor belt scale calibration weighing system. Calibration involves adjusting the system to account for any discrepancies in the weight measurements, ensuring that the data produced is precise and consistent. Without regular calibration, even minor errors can accumulate, leading to significant inaccuracies that can impact production and inventory management.
For example, in the food processing industry, where precise ingredient measurements are critical, an uncalibrated weighing system can result in inconsistent product quality and increased waste. Companies like Archer Daniels Midland (ADM) rely on regular conveyor belt scale calibration to maintain the accuracy of their material measurements, ensuring compliance with industry standards and optimizing their production processes.
Benefits of a Well-Calibrated System
A well-calibrated conveyor belt scale calibration weighing system offers several benefits, enhancing overall operational efficiency and accuracy.
Improved Accuracy in Material Measurement
Accurate material measurement is essential for various industrial applications. A well-calibrated weighing system ensures that the weight data is precise, reducing errors in production and inventory management. For instance, in the mining industry, accurate weight measurements are crucial for determining the quantity of extracted minerals, directly impacting profitability and resource management.
Enhanced Operational Efficiency
By maintaining accurate weight measurements, a well-calibrated weighing system helps streamline operations, reducing downtime and improving productivity. Regular calibration minimizes the risk of errors that could lead to costly disruptions, allowing companies to operate more efficiently.
Better Compliance with Regulatory Standards
Industries are often subject to strict regulatory standards regarding material measurement and reporting. A well-calibrated conveyor belt scale calibration weighing system ensures compliance with these standards, avoiding potential fines and legal issues. For example, the pharmaceutical industry must adhere to stringent regulations for ingredient measurements, making regular calibration critical for compliance and product quality.
Regular calibration of the conveyor belt scale calibration weighing system is essential for maintaining accurate and reliable weight measurements. By understanding the components and the role of calibration, industry professionals can ensure their weighing systems operate efficiently, enhancing accuracy, operational efficiency, and regulatory compliance.

How Often Should You Calibrate Your Conveyor Belt Scales?
Conveyor belt scales should be calibrated regularly to maintain accuracy and reliability. The frequency of calibration depends on several factors, including the operational environment, the type of material being weighed, and the manufacturer’s recommendations. Here are some general guidelines:
- Manufacturer’s Recommendations: Always follow the calibration schedule provided by the scale manufacturer. This is often the most reliable guide as it is based on the specific design and use of the equipment.
- Operational Environment: In harsh or variable environments, such as those with extreme temperatures, humidity, dust, or vibrations, more frequent calibration may be necessary. For less challenging conditions, the calibration interval can be longer.
- Usage Frequency: For conveyor belt scales in constant or heavy use, more frequent calibration is recommended. For scales used less frequently, the calibration intervals can be extended.
- Legal and Regulatory Requirements: In some industries, there may be legal or regulatory requirements that dictate calibration intervals. Ensure compliance with these standards.
- Performance Monitoring: Regularly check the performance of the scale. If there are noticeable drifts in accuracy or consistency, it may be a sign that more frequent calibration is needed.
- Typical Intervals:
- Monthly to Quarterly: For critical applications or harsh environments.
- Semi-Annually to Annually: For less demanding applications and stable environments.
In conclusion, while general guidelines can be followed, the best practice is to tailor the calibration frequency to your specific operational needs and conditions, regularly monitoring the scale’s performance and adjusting as necessary.
Leveraging PDF Resources for Effective Conveyor Belt Scale Calibration
Importance of Documentation
PDF resources play a crucial role in the successful implementation and maintenance of conveyor belt scale calibration. These documents provide comprehensive guidelines and detailed instructions that ensure accurate calibration and optimal performance of conveyor belt scales. Properly utilizing these resources helps industry professionals maintain the accuracy and reliability of their weighing systems, leading to improved operational efficiency and compliance with industry standards.
PDF resources are indispensable for anyone involved in conveyor belt scale calibration. Companies like Siemens and Thermo Fisher Scientific provide extensive documentation that covers every aspect of conveyor belt scale installation, calibration, and maintenance. These documents are designed to offer clear, step-by-step instructions that help users understand and execute calibration procedures accurately.
Key Topics Covered in PDFs
PDF resources on conveyor belt scale calibration typically cover a wide range of topics essential for the proper functioning of weighing systems. These topics include installation instructions, detailed calibration procedures, troubleshooting tips, and maintenance schedules.
Installation Instructions for Belt Scales
Proper installation is the first step in ensuring accurate conveyor belt scale calibration. PDF resources often include detailed installation guides that outline the best practices for positioning and securing belt scales on conveyor systems. These guides cover crucial aspects such as selecting the ideal location for the scale, ensuring stable mounting, and avoiding areas prone to excessive vibration or movement.
For example, Siemens’ comprehensive installation manuals emphasize the importance of placing the scale in a horizontal, even section of the conveyor to minimize measurement errors. These documents provide illustrations and diagrams to assist in the correct installation of components such as load cells, speed sensors, and integrators.
Detailed Calibration Procedures
Calibration is a critical process that ensures the accuracy of weight measurements. PDF resources provide detailed procedures for various calibration methods, including zero calibration and span calibration. These documents explain the importance of regular calibration and offer step-by-step instructions to achieve precise results.
Thermo Fisher Scientific’s calibration manuals, for instance, detail the process of zero calibration, which adjusts the scale to read zero when no material is present. They also cover span calibration, which involves setting the scale to measure a known weight accurately. These procedures are essential for maintaining the accuracy of the conveyor belt scale calibration over time.
Troubleshooting Tips and Maintenance Schedules
PDF resources also include troubleshooting sections that address common issues encountered during conveyor belt scale calibration. These sections provide practical solutions to problems such as inconsistent weight readings, sensor malfunctions, and calibration errors. By following these troubleshooting tips, users can quickly identify and resolve issues, minimizing downtime and maintaining operational efficiency.
Maintenance schedules outlined in PDF resources help users plan regular system checks and calibrations. These schedules ensure that all components of the weighing system are inspected and maintained regularly, preventing potential issues and extending the lifespan of the equipment. For example, METTLER TOLEDO’s maintenance guides recommend specific intervals for calibrating and inspecting load cells, speed sensors, and integrators to ensure optimal performance.
How to Use PDF Resources
Effectively utilizing PDF resources for conveyor belt scale calibration involves following the detailed procedures and guidelines provided in the documents. These resources are designed to be user-friendly, offering clear instructions and practical tips for achieving accurate calibration.
Follow Step-by-Step Calibration Procedures
The step-by-step calibration procedures outlined in PDF resources are essential for ensuring accurate and reliable weight measurements. By following these procedures meticulously, users can achieve precise calibration and maintain the accuracy of their weighing systems. For instance, using a certified test weight or calibration chain as specified in the PDF guides ensures that the span calibration is performed correctly.
Refer to Troubleshooting Sections for Common Issues and Solutions
When encountering issues during conveyor belt scale calibration, referring to the troubleshooting sections in PDF resources can provide quick and effective solutions. These sections offer practical advice on diagnosing and resolving common problems, helping users maintain the accuracy and reliability of their weighing systems.
Use Maintenance Schedules to Plan Regular System Checks and Calibrations
Regular maintenance is crucial for the longevity and performance of conveyor belt scales. PDF resources include maintenance schedules that outline the recommended intervals for system checks and calibrations. By adhering to these schedules, users can ensure that their weighing systems remain in optimal condition, reducing the risk of unexpected failures and ensuring continuous, accurate measurements.
PDF resources are invaluable tools for industry professionals involved in conveyor belt scale calibration. By providing detailed installation instructions, comprehensive calibration procedures, troubleshooting tips, and maintenance schedules, these documents help ensure the accuracy and reliability of weighing systems. Utilizing these resources effectively can lead to improved operational efficiency, compliance with industry standards, and extended equipment lifespan.
Understanding the Role of Span Calibration in Conveyor Belt Scale Calibration
Definition and Purpose
Span calibration is a crucial aspect of conveyor belt scale calibration, ensuring that the scale provides accurate and consistent weight measurements. This process involves setting the scale to measure a known weight accurately, which helps maintain the precision and reliability of the weighing system. Span calibration compensates for any discrepancies that might arise due to environmental factors, wear and tear, or mechanical issues, ensuring the scale performs optimally.
In conveyor belt scale calibration, span calibration is particularly important because it directly impacts the accuracy of the weight measurements of materials moving on the conveyor belt. Companies like Siemens and Thermo Fisher Scientific emphasize the importance of span calibration in their documentation and training materials. Accurate span calibration ensures that the operational data derived from the weighing system is reliable, supporting critical production decisions and maintaining overall efficiency.
Steps in Span Calibration
Span calibration is a meticulous process that requires attention to detail and precision. Here are the essential steps involved in span calibration for conveyor belt scale calibration:
Use a Certified Weight or Test Chain
The first step in span calibration involves selecting a certified weight or test chain that is known for its accuracy. This weight serves as the reference point for the calibration process. For instance, a test chain provided by a manufacturer like Thermo Fisher Scientific is designed to meet industry standards and ensure precision.
Adjust the Scale Until It Reads the Correct Weight
Once the certified weight or test chain is in place, the next step is to adjust the scale until it accurately reads the weight of the reference object. This involves fine-tuning the scale’s settings to ensure that the displayed weight matches the known weight of the test object. This step might require several adjustments to achieve the desired accuracy.
Verify the Calibration by Comparing the Scale Reading with the Known Weight
After adjusting the scale, it is crucial to verify the calibration by comparing the scale reading with the known weight of the test object. This verification step ensures that the scale accurately measures the weight and that the calibration process has been successful. If the readings match, the span calibration is considered accurate. If not, further adjustments may be needed.
Significance of Span Calibration
Span calibration is significant for several reasons, all of which contribute to the overall effectiveness and reliability of conveyor belt scale calibration:
Maintains the Accuracy of Weight Measurements
The primary goal of span calibration is to ensure that the conveyor belt scale provides accurate weight measurements. This accuracy is essential for various industrial applications where precise material measurement is critical. For example, in mining operations, accurate weight measurements are necessary for inventory management, production planning, and cost control.
Ensures Compliance with Industry Standards and Regulations
Accurate span calibration helps companies comply with industry standards and regulations. Regulatory bodies often require periodic calibration of weighing systems to ensure that they meet specified accuracy standards. By maintaining accurate span calibration, companies can avoid penalties and ensure that their operations meet regulatory requirements.
Improves Overall Efficiency and Reliability of the Weighing System
A well-calibrated conveyor belt scale contributes to the overall efficiency and reliability of the weighing system. Accurate weight measurements enable better control over the production process, reducing material wastage and improving productivity. For instance, in the food processing industry, precise weight measurements are essential for maintaining product quality and consistency, which directly impacts customer satisfaction.
Real-World Examples and Data
To illustrate the importance of span calibration in conveyor belt scale calibration, consider the following examples:
- Siemens provides detailed calibration procedures in their manuals, emphasizing the use of certified test weights to achieve accurate span calibration. By following these procedures, companies can ensure that their weighing systems operate within the required accuracy range.
- Thermo Fisher Scientific offers test chains specifically designed for span calibration, ensuring that users can achieve precise calibration results. These test chains are manufactured to meet stringent accuracy standards, providing reliable reference weights for the calibration process.
In a case study, a mining company using Siemens conveyor belt scales reported a significant improvement in measurement accuracy after implementing regular span calibration procedures. The company observed a 10% reduction in material wastage and a 15% increase in production efficiency, demonstrating the tangible benefits of accurate span calibration.
Span calibration is a vital component of conveyor belt scale calibration, ensuring that weighing systems provide accurate and reliable weight measurements. By following a systematic calibration process and using certified reference weights, companies can maintain the accuracy and efficiency of their weighing systems. This not only supports compliance with industry standards but also enhances overall operational effectiveness and productivity.

Performing Zero and Span Calibration Formula Adjustments for Conveyor Belt Scale Calibration
Understanding the Zero Calibration Formula
Zero calibration is a fundamental aspect of conveyor belt scale calibration. This process ensures that the scale reads zero when no material is present on the belt, establishing a baseline for accurate weight measurement. Zero calibration is crucial because any deviation from zero can lead to significant errors in the overall weight measurement.
Definition
Zero calibration involves adjusting the scale so that it reads zero when the conveyor belt is empty. This step is essential to eliminate any residual load or drift that might affect the accuracy of the scale.
Procedure
- Preparation: Ensure the conveyor belt is completely empty. Any residual material can affect the calibration process.
- Adjustment: Run the conveyor belt at its normal operating speed. Observe the scale reading, which should be zero.
- Fine-Tuning: If the scale does not read zero, adjust the scale settings until the reading is exactly zero. This might involve using the scale’s control system or manually adjusting the load cells.
- Verification: After making adjustments, recheck the scale reading to ensure it consistently reads zero. Repeat the process if necessary.
Exploring the Span Calibration Formula
Span calibration is another critical component of conveyor belt scale calibration. This process ensures that the scale accurately measures a known weight, maintaining precision across the entire range of operation.
Definition
Span calibration involves setting the scale to measure a known weight accurately. This process is vital for ensuring that the scale provides correct readings for various loads, from the lightest to the heaviest.
Procedure
- Select a Known Weight: Use a certified test weight or a test chain with a known weight. Companies like Thermo Fisher Scientific provide test chains that meet industry standards for accuracy.
- Placement: Place the known weight on the conveyor belt. Ensure the weight is evenly distributed and positioned correctly to avoid any discrepancies.
- Adjustment: Adjust the scale settings until the displayed weight matches the known weight. This may require several iterations to achieve precise calibration.
- Verification: After adjusting, remove the weight and reapply it to confirm the accuracy of the calibration. The scale should consistently display the correct weight.
Importance of Zero and Span Calibration
Zero and span calibration are integral to the accuracy and reliability of conveyor belt scale calibration. These processes ensure that the scale provides accurate readings across its entire operating range, compensating for any drift or changes in the system.
Ensuring Accurate Readings
Accurate zero and span calibration ensure that the conveyor belt scale measures materials precisely. This accuracy is crucial for various industrial applications, such as mining, manufacturing, and food processing, where precise weight measurements impact production efficiency and cost control.
For example, in a coal mining operation, accurate weight measurements are essential for inventory management and shipping logistics. A coal mine using Siemens conveyor belt scales reported a 5% improvement in measurement accuracy after implementing regular zero and span calibration procedures. This improvement translated to better inventory control and reduced shipping discrepancies.
Compensating for System Drift
Over time, conveyor belt scales can experience drift due to environmental factors, mechanical wear, or load cell fatigue. Regular zero and span calibration help compensate for these changes, maintaining the scale’s accuracy. Drift can lead to significant measurement errors if not corrected, affecting production quality and regulatory compliance.
Regulatory Compliance
Accurate calibration is also crucial for meeting industry standards and regulatory requirements. Many industries have stringent guidelines for weight measurement accuracy. Regular zero and span calibration help companies comply with these regulations, avoiding potential fines and ensuring product quality.
For instance, in the food processing industry, the FDA requires precise weight measurements for packaged goods. Companies like General Mills use regular conveyor belt scale calibration to ensure compliance with these regulations, maintaining product consistency and customer trust.
Real-World Examples and Data
Real-world examples underscore the importance of zero and span calibration in maintaining conveyor belt scale accuracy. Thermo Fisher Scientific, a leading provider of industrial weighing solutions, emphasizes regular calibration in their training programs and product documentation. They report that clients who perform routine zero and span calibration experience fewer measurement errors and improved operational efficiency.
In another case, a manufacturing plant using Siemens conveyor belt scales documented a 7% increase in production accuracy after implementing a rigorous calibration schedule. This improvement led to better resource allocation and reduced production costs, highlighting the tangible benefits of regular zero and span calibration.
Performing zero and span calibration formula adjustments is vital for maintaining the accuracy and reliability of conveyor belt scales. By following systematic procedures and using certified reference weights, companies can ensure precise weight measurements, supporting efficient operations and regulatory compliance. Regular calibration not only improves measurement accuracy but also enhances overall system performance, driving operational success.
Ready to enhance your operations? Contact us now!
FAQs about Conveyor Belt Scale Calibration
Conveyor belt scale calibration involves a series of precise steps to ensure the accuracy of weight measurements. First, zero calibration is performed by running the conveyor belt empty and adjusting the scale to read zero, eliminating any residual load. Next, span calibration is conducted using a certified test weight or test chain. The known weight is placed on the belt, and the scale is adjusted until it displays the correct weight. This process is repeated to ensure consistency. Regular calibration checks are crucial for maintaining accuracy over time, compensating for factors like environmental changes and wear and tear. Documentation and adherence to manufacturer guidelines are essential throughout the calibration process to ensure compliance with industry standards.
Scales, including conveyor belt scales, are calibrated through a systematic process to ensure they provide accurate weight readings. Calibration typically involves two main steps: zero calibration and span calibration. Zero calibration sets the scale to read zero when no load is present, establishing a baseline measurement. Span calibration uses a known weight to adjust the scale for accuracy across its operational range. This known weight is placed on the scale, and adjustments are made until the scale accurately reflects the weight. Calibration should be performed regularly to maintain accuracy, considering factors like environmental conditions, mechanical wear, and sensor performance. Proper documentation and adherence to calibration procedures are vital for ensuring consistent and reliable measurements.
The equation for a conveyor belt scale typically involves the integration of load cell and speed sensor data to calculate the material flow rate. The basic formula is:
[ \text{Weight} = (\text{Load Cell Output}) \times (\text{Belt Speed}) ]
In this equation, the load cell output represents the weight of the material on the belt, and the belt speed measures the conveyor’s velocity. The integrator processes these signals to determine the material flow rate, usually displayed in units like tons per hour. For accurate measurements, both zero and span calibration are essential, ensuring the load cells and speed sensors provide precise data. Regular calibration helps maintain the accuracy and reliability of the belt scale, compensating for factors like mechanical wear and environmental changes.
The accuracy of a conveyor belt scale depends on several factors, including the quality of the scale, the calibration process, and the operating conditions. High-quality conveyor belt scales, such as those provided by Siemens and Thermo Fisher Scientific, can achieve accuracy levels of ±0.25% to ±0.5%. Regular calibration, including both zero and span calibration, is crucial for maintaining this accuracy. Environmental factors like temperature fluctuations, vibration, and mechanical wear can impact the scale’s performance, making routine maintenance and calibration essential. Proper installation and adherence to manufacturer guidelines also play a significant role in ensuring the scale’s accuracy over time. By following best practices, companies can achieve reliable and precise weight measurements, crucial for operational efficiency and regulatory compliance.
Last Updated on July 17, 2024 by Jordan Smith
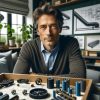
Jordan Smith, a seasoned professional with over 20 years of experience in the conveyor system industry. Jordan’s expertise lies in providing comprehensive solutions for conveyor rollers, belts, and accessories, catering to a wide range of industrial needs. From initial design and configuration to installation and meticulous troubleshooting, Jordan is adept at handling all aspects of conveyor system management. Whether you’re looking to upgrade your production line with efficient conveyor belts, require custom conveyor rollers for specific operations, or need expert advice on selecting the right conveyor accessories for your facility, Jordan is your reliable consultant. For any inquiries or assistance with conveyor system optimization, Jordan is available to share his wealth of knowledge and experience. Feel free to reach out at any time for professional guidance on all matters related to conveyor rollers, belts, and accessories.