Maintenance Tips for Conveyor Belt Drive Pulley
In the realm of material handling, conveyor belt drive pulleys play a crucial role. These integral components drive the conveyor belt and facilitate the smooth transportation of goods. This blog post will delve into various aspects of conveyor belt drive pulleys, including their types, specifications, and dimensions, as well as how to select and calculate the appropriate pulley for your conveyor system. Understanding the functionality and importance of a conveyor belt drive pulley can significantly enhance the efficiency and longevity of your conveyor system. Whether you are looking for detailed specifications or practical calculation methods, this comprehensive guide on drive pulley conveyor belts will provide valuable insights.
Comprehensive Conveyor Belt Drive Pulley Catalogue
Comprehensive Overview
Conveyor belt drive pulleys are fundamental components in material handling systems, essential for driving conveyor belts and ensuring the smooth transportation of goods. This comprehensive catalogue of drive pulley conveyor beltys includes a variety of types designed to meet diverse industry needs. From drive head pulleys to self-cleaning pulleys, each type is crafted for specific applications, providing unique benefits to enhance operational efficiency.
Introduction to the Different Types of Conveyor Belt Drive Pulleys Available in the Market
The market offers a wide array of drive pulley conveyor belts, each tailored to specific functions and operational environments. For instance, drive head pulleys are critical for initiating the movement of the conveyor belt, while tail pulleys are positioned at the end to maintain belt tension. Snub pulleys increase the wrap angle of the belt around the drive pulley, enhancing friction and drive efficiency. Bend pulleys, on the other hand, change the direction of the belt, and take-up pulleys maintain the proper tension in the belt system. Self-cleaning pulleys are designed to remove materials that might stick to the belt, ensuring continuous and smooth operation.
Detailed Descriptions of Each Pulley Type, Including Their Applications and Benefits
- Drive Head Pulleys: These pulleys are typically located at the discharge point of the conveyor system and are crucial for driving the belt. They often feature rubber or ceramic lagging to increase friction and reduce slippage, making them ideal for heavy-duty applications such as mining and aggregate industries.
- Tail Pulleys: Positioned at the loading end of the conveyor, tail pulleys help maintain belt tension and alignment. They can have a flat face or slatted profile, with the latter helping in cleaning the belt by dislodging materials that might stick to it.
- Snub Pulleys: Used to increase the wrap angle of the conveyor belt around the drive pulley, snub pulleys enhance the drive force and are especially beneficial in systems requiring high torque.
- Bend Pulleys: These are used to change the direction of the conveyor belt, often found in systems with complex routing. They are crucial for maintaining proper belt tension and alignment.
- Take-Up Pulleys: Essential for adjusting the belt tension, take-up pulleys ensure the belt operates smoothly without sagging or slipping. They are commonly used in systems where belt length changes due to thermal expansion or load variations.
- Self-Cleaning Pulleys: Featuring spiral or wing designs, these pulleys prevent material build-up on the belt, which can lead to slippage and wear. They are ideal for handling sticky or abrasive materials, ensuring minimal downtime for cleaning and maintenance.
Key Pulley Types
- Drive Head Pulleys
- Drive head pulleys are the main pulleys responsible for driving the conveyor belt. They are typically located at the discharge end of the conveyor system. Companies like Flexco and Martin Engineering manufacture drive head pulleys that are designed for durability and high performance. These pulleys often come with rubber or ceramic lagging to enhance grip and reduce slippage. For example, a Flexco drive head pulley with ceramic lagging can increase belt traction by up to 30%, making it suitable for heavy-duty applications such as mining, where reliability and efficiency are paramount.
- Tail Pulleys
- Tail pulleys, located at the loading end of the conveyor system, play a crucial role in maintaining belt tension and ensuring smooth operation. They can have a flat face or a slatted profile. The slatted design helps to dislodge materials that may stick to the belt, thus preventing build-up. Companies like Kinder Australia offer tail pulleys with a unique design that includes a winged structure to aid in self-cleaning and reduce maintenance needs.
- Snub Pulleys
- Snub pulleys increase the wrap angle of the conveyor belt around the drive pulley, enhancing friction and improving drive efficiency. This is particularly important in systems requiring high torque and heavy load handling. For instance, the snub pulleys manufactured by Fenner Dunlop are designed to optimize belt tension and reduce wear, ensuring a longer lifespan for both the belt and the pulley.
- Bend Pulleys
- Bend pulleys are used to change the direction of the conveyor belt, and are essential in complex conveyor systems with multiple directional changes. Companies like Rulmeca produce bend pulleys that are designed to handle high tension and are built with robust materials to withstand harsh conditions. These pulleys help maintain proper belt alignment and tension, crucial for systems in industries such as food processing and manufacturing.
- Take-Up Pulleys
- Take-up pulleys are vital for adjusting the tension of the conveyor belt. They ensure the belt remains taut, preventing sagging and slippage. In systems where the belt length changes due to temperature variations or load changes, take-up pulleys are essential. Dodge, a renowned manufacturer, offers take-up pulleys that are easy to adjust and maintain, making them a preferred choice in industries like packaging and distribution.
- Self-Cleaning Pulleys
- Self-cleaning pulleys, such as those with spiral or wing designs, are designed to remove materials that might stick to the belt. These pulleys are particularly useful in industries handling sticky or abrasive materials, such as cement or sugar processing. For example, PPI’s self-cleaning pulleys feature a wing design that effectively prevents material build-up, reducing the need for frequent cleaning and maintenance, thereby increasing operational efficiency.
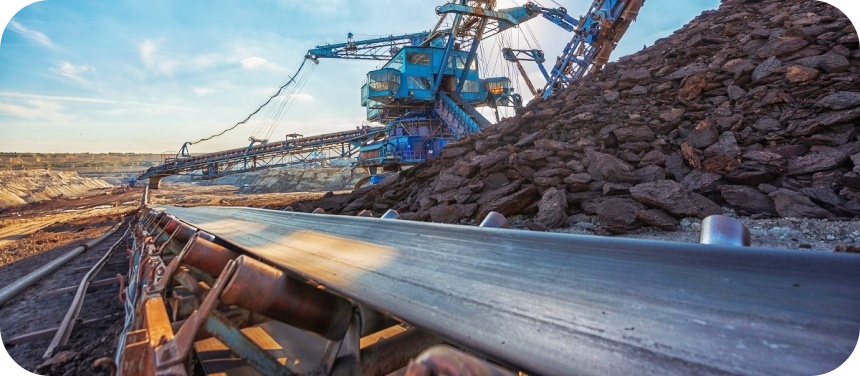
Benefits of a Well-Rounded Conveyor Belt Drive Pulley Catalogue
Ensures Availability of the Right Pulley for Specific Applications
Having a comprehensive catalogue of conveyor belt drive pulleys ensures that the right pulley is available for any specific application. This variety is crucial for meeting the diverse needs of different industries. For example, a mining operation may require heavy-duty drive head pulleys with ceramic lagging, while a food processing plant might need self-cleaning pulleys to handle sticky materials.
Facilitates Quick Replacement and Maintenance
A well-rounded pulley catalogue facilitates quick replacement and maintenance. When a pulley needs to be replaced, having a variety of options readily available can significantly reduce downtime. Companies like Metso Outotec offer a wide range of conveyor belt drive pulleys that are designed for easy installation and replacement, ensuring minimal disruption to operations.
Enhances Overall System Efficiency
A diverse selection of conveyor belt drive pulleys enhances overall system efficiency by ensuring that each pulley is optimized for its specific role within the conveyor system. For instance, using the correct drive head pulley can improve belt traction and reduce slippage, leading to smoother and more efficient operations. Additionally, specialized pulleys such as self-cleaning or take-up pulleys can address specific challenges within the system, further enhancing performance and reliability.
Having a comprehensive and well-rounded drive pulley conveyor belt catalogue is essential for ensuring the availability of the right pulley for specific applications, facilitating quick replacement and maintenance, and enhancing overall system efficiency. With a variety of pulleys designed for different functions and environments, industries can optimize their conveyor systems for maximum productivity and reliability.
Conveyor Belt Drive Pulley Diameter Calculation
Importance of Correct Diameter
The diameter of a conveyor belt drive pulley is critical to the performance of the entire conveyor system. Selecting the correct diameter influences belt tension, power consumption, and overall operational efficiency.
Influence on Belt Tension and System Performance
A properly sized conveyor belt drive pulley ensures optimal belt tension, which is vital for the smooth and efficient operation of the conveyor system. If the pulley diameter is too small, it can cause excessive tension, leading to premature wear and tear on the belt and other components. Conversely, if the diameter is too large, it may result in insufficient tension, causing slippage and inefficient material handling.
For example, in a mining operation where heavy loads are transported, using a conveyor belt drive pulley with the correct diameter ensures that the belt remains taut and moves materials efficiently. A drive pulley that is too small might cause the belt to stretch or break under the heavy load, while a pulley that is too large might not grip the belt effectively, leading to slippage and reduced operational efficiency.
Impact on Power Consumption and Operational Efficiency
The diameter of the drive pulley conveyor belt also affects power consumption. A correctly sized pulley minimizes the power required to drive the belt, as it reduces friction and slippage. This leads to lower energy costs and enhances the operational efficiency of the conveyor system.
For instance, in a manufacturing facility, using a belt conveyor drive pulley with an optimized diameter can lead to significant energy savings. If the pulley diameter is correctly calculated, the motor driving the pulley operates more efficiently, consuming less power and reducing operational costs. Companies like Fenner Dunlop and Continental offer a range of conveyor belt drive pulleys designed to optimize power consumption and improve overall system efficiency.
Calculation Methods
Determining the appropriate diameter for a belt conveyor drive pulley involves several calculation methods and considerations.
Basic Formulae and Principles
The basic formula for calculating the diameter of a belt conveyor drive pulley involves the belt speed, the desired pulley RPM, and the load requirements. The general formula is:
[ \text{Pulley Diameter (D)} = \frac{Belt Speed (V)}{\pi \times \text{Pulley RPM (N)}} ]
Where:
- ( V ) is the belt speed in meters per second (m/s)
- ( N ) is the pulley rotational speed in revolutions per minute (RPM)
Factors to Consider
Several factors must be taken into account when determining the appropriate pulley diameter:
- Belt Speed: The speed at which the conveyor belt moves is a crucial factor. Higher belt speeds require larger pulley diameters to maintain efficiency and reduce wear.
- Load Requirements: The weight and type of material being transported influence the pulley diameter. Heavier loads necessitate larger diameters to ensure adequate grip and tension.
- Pulley Lagging: The type and thickness of lagging on the pulley surface can affect the required diameter. Lagging enhances the friction between the belt and pulley, improving grip and reducing slippage.
Practical Examples
Applying these principles to practical scenarios helps illustrate the importance of correctly calculating the belt conveyor drive pulley diameter.
Step-by-Step Calculation for Common Industrial Applications
Consider a conveyor system in a logistics warehouse that requires a belt speed of 2 m/s and a pulley RPM of 60. Using the formula:
[ \text{Pulley Diameter (D)} = \frac{2 \text{ m/s}}{\pi \times 60} \approx 0.0106 \text{ m} \approx 10.6 \text{ cm} ]
This calculation shows that a pulley diameter of approximately 10.6 cm is required for the specified belt speed and RPM. Adjustments may be necessary based on load requirements and lagging.
Tools and Software for Accurate Diameter Calculations
Several tools and software applications can aid in accurately calculating the conveyor belt drive pulley diameter. Software like FlexSim and Sidewinder Conveyor Design Software provide advanced calculations, taking into account various factors such as load, belt speed, and environmental conditions. These tools help engineers and technicians design efficient conveyor systems by ensuring that all parameters are optimized for maximum performance.
For example, Sidewinder Conveyor Design Software allows users to input specific parameters such as belt speed, load weight, and pulley lagging to automatically calculate the optimal pulley diameter. This software is widely used in industries such as mining, manufacturing, and logistics, where precise calculations are essential for efficient operations.
The correct calculation of the conveyor belt drive pulley diameter is crucial for maintaining optimal belt tension, reducing power consumption, and enhancing overall system efficiency. By understanding the influence of pulley diameter on system performance and utilizing accurate calculation methods and tools, industries can ensure that their conveyor systems operate at peak efficiency, minimizing downtime and operational costs.
Leading Conveyor Belt Drive Pulley Manufacturers
Top Manufacturers
The conveyor belt drive pulley market features several top manufacturers known for their high-quality products and innovative solutions. Understanding the key players in this industry helps businesses make informed decisions when selecting conveyor belt drive pulleys for their operations.
Overview of Leading Manufacturers in the Conveyor Pulley Industry
- Fenner Dunlop: Known for their robust and durable conveyor belt drive pulleys, Fenner Dunlop offers a wide range of pulleys designed to meet the needs of various industries, including mining, manufacturing, and logistics. Their products are renowned for their reliability and long service life.
- Martin Engineering: Martin Engineering provides a comprehensive selection of conveyor belt drive pulleys, focusing on innovative designs that enhance operational efficiency. Their pulleys often feature advanced lagging materials and precision engineering to reduce maintenance needs and improve performance.
- Continental: As a global leader in conveyor belt technology, Continental produces conveyor belt drive pulleys that integrate seamlessly with their conveyor systems. Their emphasis on quality and innovation ensures that their pulleys offer excellent performance and durability in demanding environments.
- Rulmeca: Specializing in rollers and components for conveyor systems, Rulmeca offers high-quality conveyor belt drive pulleys that are designed for heavy-duty applications. Their products are known for their precision engineering and ability to handle high loads.
Comparison of Product Offerings, Quality, and Innovations
- Product Offerings: Fenner Dunlop offers a broad range of standard and custom-designed pulleys, catering to various industry requirements. Martin Engineering focuses on providing innovative solutions, such as self-cleaning pulleys and advanced lagging materials. Continental integrates their pulleys with their extensive conveyor belt product line, ensuring compatibility and efficiency. Rulmeca provides heavy-duty pulleys that are ideal for industrial and mining applications.
- Quality: All four manufacturers maintain high standards of quality, but they differentiate themselves through specific strengths. Fenner Dunlop is known for their robust designs and long-lasting products. Martin Engineering excels in innovation, constantly improving their designs to reduce maintenance and enhance performance. Continental’s products are synonymous with reliability and integration, while Rulmeca’s pulleys are recognized for their durability and precision.
- Innovations: Martin Engineering leads the way in innovation with features like their unique self-cleaning pulley designs, which help reduce downtime and maintenance costs. Continental focuses on integrating advanced materials and technology to enhance the efficiency of their conveyor systems. Rulmeca continues to innovate in the heavy-duty sector, improving the load-bearing capabilities and lifespan of their pulleys.
Selection Criteria
When choosing a manufacturer for belt conveyor drive pulleys, several factors need to be considered to ensure the best fit for your specific needs.
Factors to Consider When Choosing a Manufacturer: Reputation, Product Range, Customer Support, and Customization Capabilities
- Reputation: A manufacturer’s reputation is a crucial indicator of their reliability and the quality of their products. Companies like Fenner Dunlop and Continental have built strong reputations over decades, making them trusted choices in the industry.
- Product Range: The breadth of a manufacturer’s product range is essential to meet diverse operational requirements. Martin Engineering and Fenner Dunlop offer extensive catalogues, ensuring that customers can find the right pulley for any application.
- Customer Support: Effective customer support is vital for addressing issues promptly and ensuring smooth operations. Manufacturers like Rulmeca and Martin Engineering provide excellent customer service, offering technical support and maintenance services to minimize downtime.
- Customization Capabilities: The ability to customize pulleys to specific requirements can be a significant advantage. Continental and Fenner Dunlop excel in providing customized solutions, tailoring their products to meet unique operational challenges and specifications.
Market Trends
The conveyor belt drive pulley industry is continuously evolving, with new trends and advancements shaping the market. Staying abreast of these trends can help businesses adopt the latest technologies and materials for enhanced efficiency and sustainability.
Recent Advancements and Trends in Conveyor Pulley Manufacturing
- Sustainability and Eco-Friendly Materials: There is a growing emphasis on sustainability in the manufacturing of conveyor belt drive pulleys. Companies like Continental are leading the charge by incorporating eco-friendly materials and sustainable manufacturing practices into their production processes. This trend not only reduces the environmental impact but also appeals to companies looking to improve their sustainability credentials.
- Advanced Lagging Materials: Innovations in lagging materials have significantly improved the performance of belt conveyor drive pulleys. Martin Engineering, for instance, uses advanced rubber and ceramic lagging that enhances grip, reduces slippage, and extends the life of both the pulley and the conveyor belt.
- Integration with Smart Technologies: The integration of smart technologies and IoT (Internet of Things) is becoming more prevalent in conveyor systems. Manufacturers like Fenner Dunlop are incorporating sensors and monitoring systems into their pulleys, allowing for real-time performance tracking and predictive maintenance. This technology helps prevent unexpected failures and optimize the maintenance schedule, ensuring continuous and efficient operation.
- Customization and Modularity: The demand for customized and modular conveyor systems is increasing. Companies like Rulmeca are focusing on providing highly customizable pulley designs that can be easily integrated into existing systems. This flexibility allows businesses to adapt their conveyor systems to changing operational needs without extensive overhauls.
Understanding these trends and advancements in conveyor belt drive pulley manufacturing can help businesses make informed decisions and adopt the latest technologies for improved performance and sustainability. With a focus on innovation, quality, and customer support, top manufacturers like Fenner Dunlop, Martin Engineering, Continental, and Rulmeca continue to lead the industry, providing reliable and efficient solutions for material handling.
Comprehensive Guide to Conveyor Belt Drive Pulley Types
Main Types of Conveyor Belt Drive Pulleys
Understanding the main types of conveyor belt drive pulleys is essential for selecting the right pulley for specific applications. Each type has unique characteristics that make it suitable for different operational needs and environments.
Head Drive Pulleys
Head drive pulleys are located at the discharge end of the conveyor system and are crucial for driving the conveyor belt. These pulleys are typically larger in diameter and feature a variety of surface coatings to enhance grip and reduce slippage.
- Applications: Head drive pulleys are used in industries such as mining, manufacturing, and logistics. They are ideal for applications requiring high torque and efficient material handling.
- Examples: Flexco and Fenner Dunlop manufacture head drive pulleys with advanced rubber or ceramic lagging to improve traction and durability. These pulleys are designed to handle heavy loads and harsh operating conditions.
- Advantages: Enhanced traction, reduced slippage, and increased efficiency in driving the conveyor belt.
Tail Drive Pulleys
Tail drive pulleys are positioned at the loading end of the conveyor system. They help maintain belt tension and alignment, ensuring smooth operation and preventing belt sagging.
- Applications: Tail drive pulleys are widely used in industries such as food processing, packaging, and material handling. They are essential for maintaining proper belt tension and preventing belt misalignment.
- Examples: Companies like Kinder Australia offer tail drive pulleys with a winged design that aids in self-cleaning and reduces material build-up, ensuring minimal maintenance.
- Advantages: Improved belt alignment, reduced maintenance requirements, and enhanced system reliability.
Snub and Bend Pulleys
Snub pulleys and bend pulleys are used to change the direction of the conveyor belt and increase the wrap angle around the drive pulley, enhancing the drive force.
- Applications: These pulleys are commonly used in complex conveyor systems with multiple directional changes, such as those found in mining and bulk material handling.
- Examples: Rulmeca produces snub and bend pulleys designed for high tension and heavy-duty applications. Their pulleys are built to withstand high loads and harsh conditions.
- Advantages: Increased belt wrap angle, enhanced drive force, and improved belt tension control.
Take-Up Pulleys
Take-up pulleys are essential for maintaining the proper tension in the conveyor belt, ensuring smooth and efficient operation.
- Applications: Take-up pulleys are used in various industries, including logistics, mining, and manufacturing. They are particularly important in systems where the belt length changes due to thermal expansion or load variations.
- Examples: Dodge offers take-up pulleys that are easy to adjust and maintain, making them ideal for dynamic operational environments.
- Advantages: Maintained belt tension, prevention of sagging and slippage, and reduced maintenance costs.
Specialized Conveyor Belt Drive Pulleys
Specialized belt conveyor drive pulleys are designed to meet specific operational requirements and handle unique challenges.
Self-Cleaning Pulleys
Self-cleaning pulleys feature spiral or wing designs that prevent material build-up on the belt, ensuring continuous and smooth operation.
- Applications: These pulleys are ideal for industries handling sticky or abrasive materials, such as cement, sugar processing, and waste management.
- Examples: PPI’s self-cleaning pulleys have a wing design that effectively dislodges material, reducing downtime for cleaning and maintenance.
- Advantages: Reduced material build-up, decreased maintenance downtime, and extended pulley lifespan.
Motorized Pulleys
Motorized pulleys, also known as drum motors, integrate the motor inside the pulley shell, providing a compact and efficient drive solution.
- Applications: Motorized pulleys are used in food processing, packaging, and airport baggage handling systems where space and hygiene are critical.
- Examples: Interroll offers motorized pulleys with varying power and speed options, designed for efficient and hygienic operations.
- Advantages: Space-saving design, increased efficiency, and enhanced hygiene due to enclosed motor.
Spiral and Wing Pulleys
Spiral pulleys and wing pulleys are designed for specific material handling challenges. Spiral pulleys feature a self-cleaning design, while wing pulleys have angled fins to prevent material build-up.
- Applications: These pulleys are used in industries such as agriculture, mining, and recycling where handling bulk materials efficiently is crucial.
- Examples: Martin Engineering’s wing pulleys are designed to handle large lump, sharp, and sticky materials, providing robust performance in abrasive and dirty environments.
- Advantages: Effective self-cleaning, reduced maintenance, and improved material handling efficiency.
Applications and Advantages of Conveyor Belt Drive Pulley Types
Different types of conveyor belt drive pulleys are used across various industries, each offering unique benefits and addressing specific operational challenges.
How Different Pulley Types Are Used in Various Industries
- Mining: In mining, head drive pulleys with ceramic lagging are used to handle heavy loads and abrasive materials, ensuring durability and efficient material transport.
- Food Processing: Motorized pulleys are preferred in food processing due to their compact design and hygiene benefits, facilitating efficient and clean operations.
- Packaging: Take-up pulleys are essential in packaging systems to maintain belt tension and prevent slippage, ensuring smooth and reliable material handling.
Benefits and Limitations of Each Pulley Type
- Head Drive Pulleys: Benefit from increased traction and reduced slippage, but may require more maintenance due to their larger size and exposure to heavy loads.
- Tail Drive Pulleys: Offer improved belt alignment and reduced maintenance, but may not be suitable for applications requiring high torque.
- Snub and Bend Pulleys: Enhance drive force and belt tension control, but their installation can be complex in systems with multiple directional changes.
- Take-Up Pulleys: Ensure maintained belt tension and reduce sagging, but may require regular adjustments in dynamic environments.
- Self-Cleaning Pulleys: Provide effective self-cleaning and reduced downtime, but may have higher initial costs due to specialized designs.
- Motorized Pulleys: Offer space-saving and hygienic benefits, but may be limited in power compared to traditional drive pulleys.
- Spiral and Wing Pulleys: Excel in handling bulk materials and reducing maintenance, but may not be suitable for all conveyor system designs.
Understanding the various types of conveyor belt drive pulleys and their specific applications and advantages helps in selecting the right pulley for your needs. Whether you are dealing with heavy loads, requiring hygienic operations, or managing bulk materials, there is a conveyor belt drive pulley designed to meet your requirements and enhance your system’s efficiency.
Understanding Conveyor Belt Drive Pulley Dimensions
Standard Dimensions
Standard dimensions for belt conveyor drive pulleys are essential for ensuring compatibility and efficiency in conveyor systems. These dimensions are typically determined based on industry standards and the specific requirements of the conveyor system.
Common Dimensions for Various Pulley Types
Conveyor belt drive pulleys come in various standard sizes, which are designed to meet the most common operational needs. The dimensions include the diameter, face width, and shaft size of the pulley. For example, typical diameters for drive pulleys range from 200 mm to 1250 mm, with face widths from 200 mm to 2500 mm. The shaft size varies depending on the load and application, usually ranging from 30 mm to 300 mm.
The Significance of Standardization in Pulley Dimensions
Standardization in pulley dimensions plays a critical role in ensuring that pulleys can be easily replaced or upgraded without requiring significant modifications to the conveyor system. This standardization facilitates interoperability between different systems and manufacturers. For instance, companies like Dodge and Fenner Dunlop adhere to standard dimensions to ensure their pulleys can be used interchangeably in various conveyor systems.
Standardized dimensions also contribute to reducing downtime during maintenance and repairs. When a conveyor belt drive pulley needs to be replaced, having standardized dimensions allows for quick and easy installation, minimizing disruption to operations. Furthermore, standardized pulleys ensure that the belt tension and alignment remain consistent, maintaining the efficiency and longevity of the conveyor system.
Custom Dimensions
While standard dimensions cover a wide range of applications, there are situations where custom dimensions are necessary to meet specific operational requirements.
When and Why Custom Dimensions Are Required
Custom dimensions are often required for specialized conveyor systems that operate under unique conditions or handle specific materials. For example, in industries such as mining or heavy manufacturing, where conveyor systems may need to handle extremely heavy loads or abrasive materials, custom pulleys with larger diameters and reinforced structures may be necessary.
Custom dimensions are also important for conveyor systems with space constraints or non-standard configurations. In such cases, pulleys may need to be designed with specific face widths or shaft sizes to fit within the available space while maintaining optimal performance.
Process of Determining and Manufacturing Custom Pulleys
Determining the appropriate custom dimensions for a conveyor belt drive pulley involves a thorough analysis of the operational requirements and constraints. This process typically includes:
- Load Analysis: Evaluating the weight and type of materials being conveyed to determine the required strength and durability of the pulley.
- Space Constraints: Assessing the available space within the conveyor system to ensure the pulley fits without causing interference or operational issues.
- Belt Speed and Tension: Calculating the belt speed and tension requirements to determine the appropriate diameter and face width of the pulley.
Once the custom dimensions are determined, the manufacturing process begins. Companies like Martin Engineering and Rulmeca specialize in producing custom conveyor belt drive pulleys tailored to specific requirements. The manufacturing process involves precision engineering and high-quality materials to ensure the pulleys meet the operational demands.
Impact on System Design
The dimensions of a conveyor belt drive pulley significantly affect the overall design and functionality of the conveyor system. Properly sized pulleys ensure efficient operation, while incorrect dimensions can lead to various operational issues.
How Pulley Dimensions Affect the Overall Conveyor System Layout and Functionality
Belt Tension and Alignment
The diameter and face width of the pulley play crucial roles in maintaining the correct belt tension and alignment. A pulley with an appropriate diameter ensures that the belt remains taut, reducing the risk of slippage and misalignment. Incorrect pulley dimensions can cause excessive belt tension, leading to increased wear and tear or insufficient tension, resulting in slippage and inefficient operation.
Load Distribution
Properly dimensioned pulleys distribute the load evenly across the conveyor belt, preventing excessive wear on specific sections of the belt. For instance, a pulley with an adequately sized face width ensures that the load is evenly distributed, reducing the risk of belt damage and extending the lifespan of both the belt and the pulley.
Space Utilization
Custom dimensions allow for optimal space utilization within the conveyor system. In facilities with limited space, pulleys with specific dimensions can be designed to fit within the available area without compromising performance. This flexibility is particularly important in complex conveyor layouts where space constraints are a significant consideration.
Operational Efficiency
Overall, correctly sized pulleys enhance the operational efficiency of the conveyor system. By ensuring proper belt tension, alignment, and load distribution, the system operates smoothly and efficiently, reducing downtime and maintenance costs. For example, in an automotive manufacturing plant, using custom-dimensioned pulleys that fit precisely within the conveyor system’s design can lead to significant improvements in production efficiency and reduced maintenance intervals.
Understanding the importance of conveyor belt drive pulley dimensions and their impact on system design is crucial for optimizing conveyor performance. Whether using standard dimensions for ease of replacement and maintenance or custom dimensions for specialized applications, selecting the right pulley dimensions ensures the conveyor system operates efficiently and reliably. Companies like Dodge, Fenner Dunlop, Martin Engineering, and Rulmeca provide both standard and custom solutions to meet the diverse needs of various industries, ensuring that each conveyor system can achieve its full potential.
Conveyor Belt Drive Pulley Head and Tail Pulleys
Roles and Functions
Understanding the roles and functions of conveyor belt drive pulley head and tail pulleys is essential for optimizing the performance and efficiency of a conveyor system.
Detailed Explanation of Head and Tail Pulleys in a Conveyor System
Head pulleys are located at the discharge end of the conveyor system and play a critical role in driving the conveyor belt. They are typically larger in diameter compared to other pulleys and are equipped with various types of lagging to enhance grip and reduce slippage. The primary function of the head pulley is to transmit power from the motor to the belt, ensuring that the belt moves continuously and smoothly.
Tail pulleys, on the other hand, are positioned at the loading end of the conveyor system. Their main function is to help maintain the tension in the conveyor belt, ensuring that it remains taut and properly aligned. Tail pulleys also guide the belt back into the system after it has discharged the carried material. They are generally smaller in diameter compared to head pulleys and can feature wing or slatted designs to assist in cleaning the belt and preventing material build-up.
Differences Between Head and Tail Pulleys in Terms of Design and Operation
Head pulleys are designed to handle the higher loads and stresses associated with driving the conveyor belt. They often feature robust construction and advanced lagging materials such as ceramic or rubber to improve traction and durability. For example, head pulleys manufactured by Flexco are designed to provide maximum grip and reduce wear, ensuring reliable performance even under heavy-duty conditions.
Tail pulleys, while also crucial, are primarily focused on maintaining belt tension and alignment. Their design often includes features that aid in self-cleaning and reducing maintenance needs. Kinder Australia’s tail pulleys, for instance, have a unique wing design that helps dislodge material from the belt, reducing the risk of build-up and ensuring smooth operation.
Design Considerations
Designing effective conveyor belt drive pulley head and tail pulleys requires careful consideration of several factors to ensure optimal performance and longevity.
Key Factors in Designing Effective Head and Tail Pulleys
- Material Selection
- The materials used in the construction of head and tail pulleys significantly impact their performance and durability. For head pulleys, materials like high-strength steel are commonly used to withstand the high forces exerted by the motor and the belt. Additionally, the lagging material, which can be rubber, ceramic, or a combination of both, is selected based on the operational environment and the type of materials being transported. For tail pulleys, the materials should provide adequate strength while also offering self-cleaning properties if required.
- Lagging Options
- Lagging on head pulleys enhances grip and reduces slippage, which is crucial for efficient belt operation. Different types of lagging, such as plain rubber, diamond-patterned rubber, or ceramic lagging, offer various benefits. For example, ceramic lagging, used by companies like Continental, provides excellent abrasion resistance and extended service life, making it suitable for high-load and high-speed applications.
- Mounting Configurations
- The mounting configuration of head and tail pulleys affects their installation and maintenance. Head pulleys typically require a more robust mounting system to handle the higher forces involved in driving the belt. Tail pulleys, while generally easier to install, must be mounted in a way that allows for easy adjustment to maintain proper belt tension. Adjustable mounts and tensioning systems are often used to facilitate this process.
Maintenance Tips
Proper maintenance of conveyor belt drive pulley head and tail pulleys is crucial for ensuring their longevity and reliable performance.
Best Practices for Maintaining Head and Tail Pulleys
- Regular Inspections
- Conducting regular inspections of head and tail pulleys helps identify signs of wear and potential issues before they become serious problems. Inspect the lagging for signs of wear or damage, check the alignment and tension of the belt, and ensure that all mounting hardware is secure.
- Lubrication and Cleaning
- Proper lubrication of the pulley bearings is essential for smooth operation and to prevent premature wear. Use the recommended type of lubricant and follow the manufacturer’s guidelines for lubrication intervals. Cleaning the pulleys, especially tail pulleys with self-cleaning designs, helps prevent material build-up and ensures efficient operation.
Common Issues and Troubleshooting Methods
- Belt Slippage
- Belt slippage is a common issue with head pulleys, often caused by inadequate lagging or improper tension. Ensuring that the lagging is in good condition and the belt is correctly tensioned can help prevent slippage. If slippage persists, consider upgrading to a higher-grip lagging material.
- Misalignment
- Misalignment of the belt can cause excessive wear on both the belt and the pulleys. Regularly check and adjust the alignment of the head and tail pulleys to ensure the belt runs smoothly. Using alignment tools and regularly inspecting the belt path can help maintain proper alignment.
- Bearing Wear
- Bearing wear in both head and tail pulleys can lead to operational issues and downtime. Regularly inspect the bearings for signs of wear or damage and replace them as needed. Proper lubrication and avoiding overloading the conveyor system can extend the life of the bearings.
Effective maintenance practices, combined with a thorough understanding of the design and functions of conveyor belt drive pulley head and tail pulleys, can significantly enhance the performance and reliability of a conveyor system. By addressing common issues and ensuring proper installation and maintenance, companies can achieve optimal operational efficiency and reduce downtime, leading to increased productivity and cost savings.
Comprehensive Guide to Conveyor Belt Drive Pulley Specification
Technical Specifications
When selecting a conveyor belt drive pulley, understanding the key technical specifications is crucial for ensuring optimal performance and longevity. These specifications include the diameter, face width, shaft size, and lagging type.
Key Technical Parameters to Consider: Diameter, Face Width, Shaft Size, and Lagging Type
- Diameter
- The diameter of a conveyor belt drive pulley is one of the most critical parameters. It directly affects the belt tension, speed, and overall efficiency of the conveyor system. Standard diameters typically range from 200 mm to 1250 mm, but custom sizes can be designed for specific applications. For example, in heavy-duty mining operations, larger diameters (up to 1600 mm) are often required to handle high loads and reduce the risk of belt slippage.
- Face Width
- The face width of the pulley must match the width of the conveyor belt to ensure even distribution of load and prevent belt misalignment. Common face widths range from 300 mm to 2500 mm. For instance, a logistics company like DHL might use pulleys with a face width of 1500 mm for their sorting belts, ensuring smooth and efficient material handling across wide belts.
- Shaft Size
- The shaft size determines the pulley’s ability to withstand the operational loads. It is influenced by the pulley diameter, face width, and the type of materials being conveyed. Standard shaft sizes range from 30 mm to 300 mm. In automotive manufacturing, where high torque is required, larger shafts are preferred to ensure durability and reliability.
- Lagging Type
- Lagging enhances the friction between the belt and the pulley, reducing slippage and increasing the pulley’s grip. Types of lagging include plain rubber, diamond-patterned rubber, and ceramic. For example, Continental’s ceramic lagging provides superior abrasion resistance and is ideal for high-speed applications where belt slippage can significantly impact performance.
How Specifications Influence Pulley Performance and Longevity
Properly specified conveyor belt drive pulleys ensure efficient power transmission, reduced maintenance costs, and extended service life. For instance, selecting the correct diameter and lagging type can minimize wear and tear on the belt, preventing premature failures. Similarly, matching the face width and shaft size to the operational requirements ensures that the pulley can handle the load without deformation, maintaining alignment and reducing operational interruptions.
Specification Sheets
Detailed specification sheets are essential for the successful installation and maintenance of conveyor belt drive pulleys. They provide all necessary technical details and guidelines for proper use.
Importance of Detailed Specification Sheets for Installation and Maintenance
Specification sheets offer comprehensive information about the conveyor belt drive pulley, including its dimensions, materials, load capacities, and installation instructions. These sheets are crucial for engineers and maintenance teams to ensure that the pulley is installed correctly and operates within its designed parameters.
For example, Fenner Dunlop provides detailed specification sheets that include the exact measurements, material composition, and recommended maintenance practices for their pulleys. This information helps prevent common issues such as misalignment and excessive wear, ensuring the pulley operates efficiently over its lifespan.
How to Read and Interpret Specification Sheets
Understanding how to read and interpret specification sheets is vital for selecting and maintaining the right pulley. Key sections typically include:
- Dimensions: Provides the diameter, face width, and shaft size.
- Materials: Details the construction materials for the pulley and lagging.
- Load Capacity: Specifies the maximum load the pulley can handle.
- Installation Guidelines: Offers step-by-step instructions for proper installation.
- Maintenance Recommendations: Lists regular maintenance tasks to ensure longevity and performance.
By carefully reviewing these sections, engineers can ensure they select a pulley that meets their operational needs and follow best practices for installation and maintenance.
Customization Options
While standard pulleys cover a wide range of applications, there are situations where custom specifications are necessary to meet unique operational requirements.
Available Customization Options to Meet Specific Operational Requirements
Customization options for conveyor belt drive pulleys include modifications to the diameter, face width, shaft size, and lagging type. Custom pulleys can also be designed with specific mounting configurations and materials to suit specialized applications.
For instance, in the food processing industry, where hygiene and corrosion resistance are critical, companies like Interroll offer custom stainless steel pulleys with food-grade lagging materials. These customized pulleys ensure compliance with health and safety standards while providing reliable performance in a demanding environment.
Benefits of Tailored Pulley Specifications for Optimized Performance
Customizing conveyor belt drive pulleys offers several benefits, including:
- Enhanced Performance: Tailoring the dimensions and materials to the specific operational conditions ensures optimal performance and efficiency.
- Reduced Maintenance: Custom pulleys designed for specific loads and environments require less frequent maintenance, reducing downtime and operational costs.
- Increased Longevity: By addressing the unique stresses and demands of the application, custom pulleys are less prone to premature wear and failure, extending their service life.
For example, a mining operation might require custom pulleys with reinforced shafts and ceramic lagging to handle the abrasive nature of the materials and the high loads involved. These customizations help maintain the reliability and efficiency of the conveyor system, minimizing disruptions and maintenance needs.
Understanding and specifying the correct dimensions and materials for conveyor belt drive pulleys is crucial for ensuring the efficiency, reliability, and longevity of conveyor systems. By leveraging detailed specification sheets and considering customization options, businesses can optimize their conveyor operations and achieve significant improvements in performance and cost-effectiveness.
Comprehensive Guide to Conveyor Belt Drive Pulley Tail Pulley
Function and Importance
The tail pulley in a conveyor belt drive pulley system plays a vital role in maintaining the efficiency and reliability of the entire conveyor operation.
The Role of the Tail Pulley in the Conveyor System
The tail pulley is located at the loading end of the conveyor system and serves several critical functions. Primarily, it helps to maintain the proper tension in the conveyor belt, ensuring that the belt remains taut and runs smoothly over the pulleys. This tension is crucial for preventing slippage and maintaining the alignment of the belt, which in turn ensures efficient material handling and reduces wear on the belt and other components.
Additionally, the tail pulley assists in guiding the belt back into the return side of the conveyor after it has discharged the material. This guidance is essential for maintaining the continuous loop of the belt and preventing any disruptions in the material handling process.
How It Contributes to Belt Tension and Alignment
Maintaining proper belt tension is essential for the efficient operation of a conveyor system. The tail pulley contributes to this by providing a stable point for the belt to be tensioned against. By ensuring that the belt is properly tensioned, the tail pulley helps prevent issues such as belt slippage, misalignment, and uneven wear.
For example, in a large-scale mining operation, a tail pulley from a company like Fenner Dunlop, designed to handle heavy loads, can maintain the necessary tension to ensure that the conveyor belt operates smoothly even under the stress of transporting large quantities of material. This proper tension helps in keeping the belt aligned, reducing the risk of downtime due to belt tracking issues.
Design Features
Designing an efficient conveyor belt drive pulley tail pulley involves considering several key features that ensure optimal performance and durability.
Essential Design Features for Efficient Tail Pulleys
- Robust Construction
- Tail pulleys must be built to withstand the forces exerted by the conveyor belt and the materials being transported. This requires the use of high-strength materials such as steel or alloy, which provide the necessary durability and resistance to wear and tear.
- Lagging
- The surface of the tail pulley is often lagged with materials such as rubber or ceramic to enhance grip and reduce slippage. Rubber lagging, for instance, is commonly used to increase friction between the belt and the pulley, ensuring better traction. Ceramic lagging, offered by manufacturers like Continental, provides superior abrasion resistance, making it ideal for applications involving abrasive materials.
- Self-Cleaning Features
- To minimize maintenance and prevent material build-up, many tail pulleys are designed with self-cleaning features. These can include wing or spiral designs that help dislodge material from the pulley surface as it rotates. Kinder Australia, for example, offers tail pulleys with a wing design that effectively prevents material accumulation and reduces the need for frequent cleaning.
Differences Between Standard and Specialized Tail Pulleys
Standard tail pulleys are designed for general use and are suitable for most conveyor applications. They provide the necessary tension and alignment support but may lack the specialized features required for certain industries or environments.
Specialized tail pulleys, on the other hand, are tailored for specific applications. For instance, in the food processing industry, stainless steel tail pulleys with food-grade lagging are used to meet hygiene standards and resist corrosion. In heavy-duty mining operations, tail pulleys with reinforced structures and advanced lagging materials are used to handle the extreme conditions and high loads.
Installation and Maintenance
Proper installation and maintenance of conveyor belt drive pulley tail pulleys are crucial for ensuring their longevity and reliable performance.
Key Considerations During the Installation of Tail Pulleys
- Alignment
- Ensuring that the tail pulley is properly aligned with the rest of the conveyor system is critical. Misalignment can cause excessive wear on the belt and pulley, leading to premature failure. Using precision alignment tools and following the manufacturer’s guidelines can help achieve the correct alignment.
- Tensioning
- The belt must be correctly tensioned against the tail pulley to prevent slippage and ensure smooth operation. This involves adjusting the take-up mechanisms and regularly checking the tension to ensure it remains within the recommended range.
- Mounting
- The mounting of the tail pulley should be secure and stable to withstand the operational forces. Using robust mounting brackets and ensuring that all fasteners are tightened to the specified torque settings can help prevent movement and maintain the stability of the pulley.
Routine Maintenance Practices to Ensure Longevity and Performance
- Regular Inspections
- Conducting regular inspections of the tail pulley is essential for identifying signs of wear or damage. This includes checking the lagging for wear, inspecting the bearings for signs of failure, and ensuring that the pulley remains properly aligned and tensioned.
- Lubrication
- Proper lubrication of the pulley bearings is crucial for smooth operation and to prevent overheating and wear. Following the manufacturer’s recommendations for lubrication intervals and using the specified lubricant can help maintain the performance of the bearings.
- Cleaning
- For tail pulleys with self-cleaning features, it is still important to periodically check and clean the pulley to ensure that the self-cleaning mechanisms are functioning correctly. Removing any accumulated material helps prevent excessive wear and ensures the pulley operates efficiently.
Replacement of Worn Components
Over time, components such as the lagging and bearings may wear out and require replacement. Regularly monitoring these components and replacing them as needed can prevent unexpected failures and reduce downtime.
By understanding the function, design features, and maintenance requirements of conveyor belt drive pulley tail pulleys, businesses can ensure that their conveyor systems operate efficiently and reliably. Companies like Fenner Dunlop, Continental, and Kinder Australia provide high-quality tail pulleys designed to meet the demands of various industries, ensuring optimal performance and longevity. Proper installation and routine maintenance are key to maximizing the lifespan and efficiency of these critical conveyor components.
Need a price estimate? Contact us through this inquiry form.
FAQs about Conveyor Belt Drive Pulley
A drive pulley on a conveyor belt is a critical component that provides the driving force to move the belt. It is typically located at the end of the conveyor system and is powered by a motor. The drive pulley is connected to the motor through a shaft and transfers the motor’s rotational energy to the belt, enabling it to transport materials from one point to another. The drive pulley is designed with a high-friction surface to grip the belt effectively, ensuring efficient power transmission and minimal slippage. Proper maintenance of the drive pulley is essential to ensure the longevity and reliability of the conveyor system.
The terms “drive pulley” and “head pulley” are often used interchangeably but have distinct meanings in the context of conveyor systems. A drive pulley is specifically responsible for driving the conveyor belt, typically powered by a motor. It imparts the necessary force to move the belt. On the other hand, a head pulley is located at the discharge end of the conveyor system and can also be a drive pulley. However, not all head pulleys are drive pulleys. The primary function of a head pulley is to guide and redirect the belt as it completes its loop. When the head pulley also serves as the drive pulley, it both guides the belt and powers its movement.
A drive belt pulley is a wheel-like component that is used in conjunction with a belt to transmit power in mechanical systems, including conveyor systems. The drive belt pulley is connected to a motor or another power source and transfers rotational energy to the belt, which in turn drives other components in the system. In the context of a conveyor belt, the drive belt pulley is essential for moving the conveyor belt and ensuring the efficient transport of materials. The design of the drive belt pulley includes grooves or a textured surface to enhance grip and reduce slippage, ensuring smooth operation and consistent performance.
The drive mechanism of a belt conveyor is the system responsible for moving the conveyor belt and the materials on it. This mechanism typically includes a motor, drive pulley, and sometimes additional components like a gearbox or coupling. The motor provides the necessary power to turn the drive pulley, which in turn moves the conveyor belt. The drive pulley is connected to the motor through a shaft, and its surface is designed to grip the belt securely. In some conveyor systems, there may also be an idler pulley that helps guide the belt and maintain tension. The efficiency and reliability of the drive mechanism are crucial for the smooth operation of the conveyor system, ensuring that materials are transported efficiently and without interruption.
Last Updated on July 31, 2024 by Jordan Smith
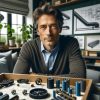
Jordan Smith, a seasoned professional with over 20 years of experience in the conveyor system industry. Jordan’s expertise lies in providing comprehensive solutions for conveyor rollers, belts, and accessories, catering to a wide range of industrial needs. From initial design and configuration to installation and meticulous troubleshooting, Jordan is adept at handling all aspects of conveyor system management. Whether you’re looking to upgrade your production line with efficient conveyor belts, require custom conveyor rollers for specific operations, or need expert advice on selecting the right conveyor accessories for your facility, Jordan is your reliable consultant. For any inquiries or assistance with conveyor system optimization, Jordan is available to share his wealth of knowledge and experience. Feel free to reach out at any time for professional guidance on all matters related to conveyor rollers, belts, and accessories.