Selecting Conveyor Belt Material Used
Conveyor belts are essential components in numerous industries, facilitating the efficient transport of materials across various stages of production. The selection of the appropriate conveyor belt material used is crucial for ensuring operational efficiency and longevity. Different materials offer unique properties, making them suitable for specific applications and environmental conditions. This article provides a comprehensive overview of the conveyor belt material used in diverse industrial settings, highlighting the importance of choosing the right material. We will cover a range of materials commonly used in conveyor belts, including rubber, metal, and reinforced fabrics, and discuss their respective advantages and ideal applications.
5 Conveyor Belt Material Used
Conveyor belts are essential in various industries, and their materials vary based on the application and requirements. Here are five commonly used conveyor belt materials:
- Rubber: Rubber is a versatile and durable material used for general-purpose conveyor belts. It is flexible, resistant to abrasion, and suitable for carrying heavy and sharp materials.
- PVC (Polyvinyl Chloride): PVC conveyor belts are lightweight, cost-effective, and resistant to chemicals and oils. They are commonly used in the food industry due to their easy-to-clean surface and non-toxic properties.
- PU (Polyurethane): PU conveyor belts are known for their excellent wear resistance, flexibility, and resistance to oil and grease. They are often used in the food, pharmaceutical, and packaging industries.
- Metal: Metal conveyor belts, such as stainless steel, are robust and can withstand high temperatures and heavy loads. They are used in applications requiring a strong and durable conveyor system, such as in baking, freezing, and heat treating processes.
- Fabric: Fabric conveyor belts, typically made from materials like polyester, nylon, or cotton, provide flexibility and strength. They are used in a wide range of applications, including mining, agriculture, and logistics.
Each material has its advantages and is selected based on the specific needs of the application, such as load capacity, environmental conditions, and the type of materials being transported.
What is the Best Conveyor Belt Material Used
The “best” conveyor belt material depends on the specific application and requirements. However, some materials stand out for their versatility, durability, and suitability across various industries. Here are a few key factors to consider when determining the best conveyor belt material for a particular application:
- Application Requirements: Different industries and applications have unique needs. For instance, food processing requires materials that are easy to clean and non-toxic, while heavy industrial applications need materials that can withstand high loads and abrasive materials.
- Environmental Conditions: The working environment, including temperature, humidity, and exposure to chemicals, impacts the choice of conveyor belt material. For example, metal belts are suitable for high-temperature environments, while rubber belts perform well in outdoor and abrasive conditions.
- Load Capacity and Durability: The material’s ability to handle the load without excessive wear and tear is crucial. Heavy-duty applications might require more robust materials like metal or reinforced rubber.
- Cost and Maintenance: The initial cost, maintenance requirements, and overall lifespan of the conveyor belt material also play a significant role in determining the best material.
Commonly Considered “Best” Materials for Various Applications:
- Rubber: Often considered the best for general-purpose applications due to its flexibility, durability, and resistance to abrasion. It’s widely used in industries like mining, quarrying, and bulk material handling.
- PU (Polyurethane): Preferred in the food, pharmaceutical, and packaging industries for its excellent wear resistance, flexibility, and resistance to oils and grease. It’s considered one of the best materials for applications requiring hygiene and easy cleaning.
- Metal (Stainless Steel): Ideal for high-temperature applications and environments requiring robust durability, such as in baking, freezing, and heavy-duty industrial processes. It’s often the best choice where strength and resistance to heat are paramount.
- PVC (Polyvinyl Chloride): Commonly used in light to medium-duty applications, especially in the food and packaging industries. It’s considered one of the best materials for its cost-effectiveness and chemical resistance.
There isn’t a single “best” conveyor belt material universally; the choice depends on specific application needs, environmental conditions, load requirements, and cost considerations. Assessing these factors will help determine the most suitable material for a given conveyor system.
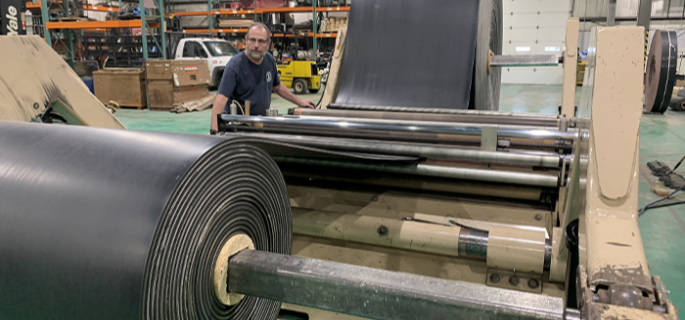
Heavy Duty Conveyor Belt Materials: Conveyor Belt Material Used in Tough Environments
Conveyor belts are integral to many industries, from manufacturing to mining, where they must withstand harsh conditions and heavy loads. Selecting the right material used for conveyor belt in heavy-duty applications is essential to ensure durability, efficiency, and safety. This section delves into the specific materials suited for these demanding environments and their unique properties.
What are Heavy Duty Applications
Heavy-duty applications refer to environments where conveyor belts are subjected to high stress, abrasion, and impact. Industries such as mining, construction, and bulk material handling often require robust conveyor belt material used to handle extreme conditions. These applications demand materials that can endure heavy loads, resist wear and tear, and maintain performance over extended periods. Understanding the properties of different materials helps in choosing the right conveyor belt material used for these tough environments, ensuring operational efficiency and reducing downtime.
Materials Suited for Heavy Duty Use
Several materials are specifically designed to meet the challenges of heavy-duty applications. The primary materials used include rubber, metal, and reinforced fabrics. Each of these materials offers unique benefits and is suited for different aspects of heavy-duty conveyor belt use.
Rubber
Rubber is one of the most common materials used in heavy-duty conveyor belts. Its flexibility, durability, and resistance to abrasion make it ideal for demanding applications. The conveyor belt material used in rubber belts is typically a blend of natural and synthetic rubber, providing a balance of strength and flexibility. Rubber belts are particularly useful in environments where they encounter sharp objects, heavy impacts, and constant wear. They also offer excellent resistance to chemicals and oils, making them suitable for various industrial applications.
Metal
Metal conveyor belts are known for their exceptional strength and durability. The conveyor belt material used in metal belts can vary from stainless steel to carbon steel, each offering distinct advantages. Stainless steel belts provide superior resistance to corrosion and high temperatures, making them suitable for applications involving extreme heat or harsh chemical exposure. Carbon steel belts, on the other hand, offer high tensile strength and are often used in heavy load applications where structural integrity is crucial. Metal belts are also used in food processing, automotive, and electronics industries due to their hygienic properties and ease of cleaning.
Reinforced Fabrics
Reinforced fabric conveyor belts combine the flexibility of fabric with the strength of additional materials such as steel or aramid fibers. The conveyor belt material used in these belts typically includes layers of woven fabrics, coated with rubber or PVC for added durability. These belts are designed to handle high tension and impact, making them suitable for heavy-duty applications. The reinforcement provided by materials like Kevlar or steel cords enhances the belt’s resistance to stretching and tearing, ensuring a longer lifespan and reliable performance under heavy loads.
Properties That Make Them Ideal
The ideal properties of conveyor belt material used in heavy-duty applications include high tensile strength, abrasion resistance, impact resistance, and flexibility. Each material offers a combination of these properties, making them suitable for different types of heavy-duty use.
High Tensile Strength: This property is crucial for handling heavy loads without stretching or breaking. Materials like metal and reinforced fabrics are particularly known for their high tensile strength, ensuring they can support significant weight over long distances.
Abrasion Resistance: Heavy-duty applications often involve continuous friction and wear. Rubber and reinforced fabrics are excellent choices for their ability to withstand abrasion and reduce wear and tear over time.
Impact Resistance: In environments where conveyor belts are subject to heavy impacts from falling materials, the conveyor belt material used must absorb shocks without damage. Rubber belts excel in impact resistance, making them ideal for such conditions.
Flexibility: Flexibility is important for conveyor belts to move smoothly over rollers and pulleys. Rubber and certain reinforced fabrics offer the necessary flexibility while maintaining their structural integrity.
Chemical and Heat Resistance: For applications involving exposure to chemicals or high temperatures, materials like stainless steel and certain rubber compounds are preferred. These materials resist degradation and maintain performance under harsh conditions.
Choosing the right conveyor belt material used in heavy-duty applications involves understanding the specific demands of the environment and selecting materials that offer the necessary properties for durability and efficiency. Rubber, metal, and reinforced fabrics each provide unique advantages, ensuring reliable performance in the most challenging industrial settings.
Choosing the Right Conveyor Belt Material Used
Selecting the right conveyor belt material used in various industrial applications is crucial for ensuring efficiency, durability, and cost-effectiveness. The choice of material impacts the belt’s performance and longevity, as well as its suitability for specific operational conditions. This section explores the key factors influencing material choice and provides a guide to selecting the right conveyor belt material used for different applications.
Factors Influencing Material Choice
Several factors must be considered when selecting the appropriate conveyor belt material used in any given application. These factors include the type of application, environmental conditions, and load weight. Each factor plays a significant role in determining the most suitable material for the conveyor belt.
Application Type
The type of application significantly influences the selection of conveyor belt material used.
- Mining and Quarrying: In these applications, belts are exposed to heavy loads, sharp objects, and abrasive materials. Rubber belts, especially those reinforced with steel cords, are ideal due to their durability and resistance to wear and tear.
- Food Processing: Hygiene is a top priority in food processing. Stainless steel and food-grade rubber belts are preferred for their cleanliness, ease of sanitation, and resistance to oils and chemicals.
- Logistics and Warehousing: For sorting and transporting packages, belts made of PVC or lightweight rubber are suitable. These materials offer flexibility and sufficient strength for handling various packages.
- Automotive Manufacturing: In automotive plants, belts must withstand exposure to oils, greases, and heavy parts. Rubber and reinforced fabric belts are often used for their durability and resistance to chemicals.
- Agriculture: Conveying agricultural products requires belts that are resistant to moisture and abrasion. Fabric-reinforced rubber belts are commonly used due to their durability and ability to handle different agricultural materials.
Environmental Conditions
The operating environment plays a critical role in selecting the conveyor belt material used.
- High Temperatures: Applications involving high temperatures, such as metal processing, require heat-resistant belts. Stainless steel and heat-resistant rubber belts are suitable for these conditions.
- Cold Environments: In cold storage or outdoor operations in winter, belts must remain flexible at low temperatures. Belts made of cold-resistant rubber or PVC are ideal.
- Chemical Exposure: Industries that involve exposure to harsh chemicals, such as chemical manufacturing, need belts that resist chemical corrosion. Stainless steel and chemically resistant rubber belts are preferred.
- Wet and Humid Conditions: For applications in wet or humid environments, such as wastewater treatment, belts must resist water and corrosion. Waterproof rubber and stainless steel belts are commonly used.
- Dusty Environments: In environments with a lot of dust, such as cement plants, belts must resist abrasion and clogging. Reinforced rubber belts are suitable due to their durability and resistance to dust abrasion.
Load Weight
The weight of the load being transported is a crucial factor in selecting the conveyor belt material used.
- Light Loads: For light loads, such as small packages in e-commerce, lightweight PVC or fabric belts are adequate.
- Medium Loads: For medium loads, such as boxes in warehousing, rubber belts with moderate reinforcement are suitable.
- Heavy Loads: For heavy loads, such as bulk materials in mining, reinforced rubber belts with steel cords are necessary to handle the weight.
- Extra Heavy Loads: For extremely heavy loads, such as large automotive parts, metal belts provide the necessary strength and durability.
- Variable Loads: For applications with varying load weights, such as mixed production lines, versatile rubber belts with adjustable tensioning systems are ideal.
Guide to Selecting the Right Material
Selecting the right conveyor belt material used involves a systematic approach considering the factors discussed above. Here is a step-by-step guide to help in making the right choice:
- Assess the Application Requirements: Identify the specific needs of your application, including the type of materials being transported and the operational environment.
- Evaluate Environmental Conditions: Consider the environmental factors such as temperature, humidity, and exposure to chemicals that the belt will be subjected to.
- Determine Load Weight: Calculate the maximum load weight that the belt will need to support to ensure it can handle the required capacity.
- Compare Material Properties: Review the properties of different materials, such as tensile strength, abrasion resistance, flexibility, and chemical resistance, to match them with your requirements.
- Consult with Manufacturers: Engage with conveyor belt manufacturers and suppliers to get expert advice and recommendations based on your specific needs.
- Test and Validate: Before full-scale implementation, test the selected belt material in your operational environment to ensure it meets all performance criteria.
By carefully considering these factors and following this guide, you can select the most suitable conveyor belt material used for your specific application, ensuring optimal performance and longevity.
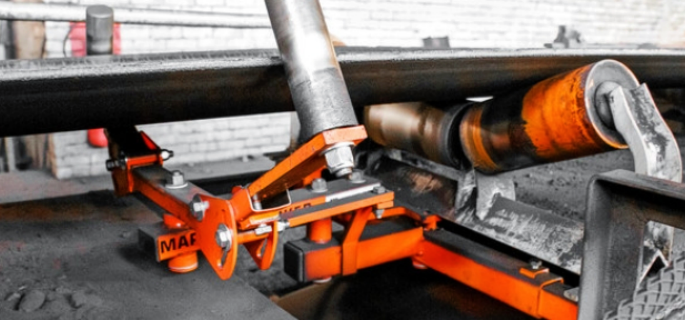
Sourcing Used Conveyor Belt Materials
Sourcing used conveyor belt materials offers a sustainable and cost-effective solution for many industries. The conveyor belt material used in recycling can provide significant benefits, reduce waste, and offer a second life to materials that might otherwise be discarded. This section explores the advantages of using recycled materials, provides guidance on finding high-quality used conveyor belts, and offers tips for assessing the quality of these materials.
Advantages of Using Recycled Materials
Using recycled conveyor belt material used in various applications can offer numerous benefits.
- Cost Savings: Recycled conveyor belts are often significantly cheaper than new ones. This cost reduction can be especially beneficial for businesses with tight budgets or those looking to reduce operational expenses without compromising on quality.
- Environmental Impact: By repurposing used conveyor belts, companies can reduce their environmental footprint. Recycling helps divert waste from landfills and reduces the demand for new raw materials, thus conserving natural resources and lowering greenhouse gas emissions.
- Availability and Variety: Used conveyor belts are available in a wide range of materials and specifications. This variety allows businesses to find belts that match their specific needs without the long lead times associated with ordering new custom belts.
- Proven Durability: Many used conveyor belts have already demonstrated their durability and performance in demanding applications. This track record can provide reassurance about the belt’s ability to handle similar conditions in a new setting.
- Customization Potential: Recycled conveyor belts can often be cut, spliced, and customized to fit specific requirements. This flexibility makes them suitable for a variety of applications, from industrial use to creative repurposing projects.
How to Find High-Quality Used Conveyor Belt Material Near You
Finding high-quality used conveyor belt material used in various applications requires knowing where to look and what to consider.
- Industrial Suppliers and Dealers: Many industrial suppliers and dealers specialize in used equipment, including conveyor belts. These suppliers often have a wide selection of materials and can provide detailed information about the condition and history of the belts.
- Online Marketplaces: Websites such as eBay, Craigslist, and specialized industrial auction sites frequently list used conveyor belts for sale. These platforms can be a good source for finding belts at competitive prices.
- Recycling Centers: Some recycling centers and scrap yards collect used conveyor belts as part of their operations. These centers can be an excellent resource for finding belts that have been retired from service but are still in good condition.
- Direct from Industries: Contacting companies that use conveyor belts extensively, such as mining or manufacturing firms, can yield opportunities to purchase used belts directly. These businesses often replace belts on a regular schedule and may be willing to sell their old belts at a reduced price.
- Networking and Referrals: Industry networks and trade associations can be valuable sources of information and referrals. Networking with other professionals in your field can help you locate suppliers and learn about available used conveyor belts.
Tips for Assessing the Quality of Used Materials
When sourcing used conveyor belt material used in your operations, it’s crucial to assess the quality to ensure it meets your requirements.
- Visual Inspection: Conduct a thorough visual inspection of the belt. Look for signs of excessive wear, such as cracks, fraying, or thinning areas. Ensure that the belt’s edges are intact and not excessively worn.
- Surface Condition: Examine the belt’s surface for any signs of damage, such as gouges, cuts, or punctures. Minor surface imperfections may be acceptable, but extensive damage can compromise the belt’s performance.
- Flexibility and Rigidity: Check the flexibility and rigidity of the belt. A good quality used belt should retain its flexibility without being too stiff or brittle. Excessive rigidity can indicate material fatigue or exposure to harsh conditions.
- Tensile Strength: Assess the belt’s tensile strength by checking for any weak spots or areas that have been excessively stretched. Ensure that the belt can handle the intended load without deforming or breaking.
- Documentation and History: Whenever possible, obtain documentation or information about the belt’s history, including its previous use, maintenance records, and any repairs. This information can provide insights into the belt’s remaining lifespan and suitability for your application.
By considering these factors and following these tips, you can effectively source high-quality used conveyor belt material used in your operations, ensuring that you get the most value and performance from your investment.
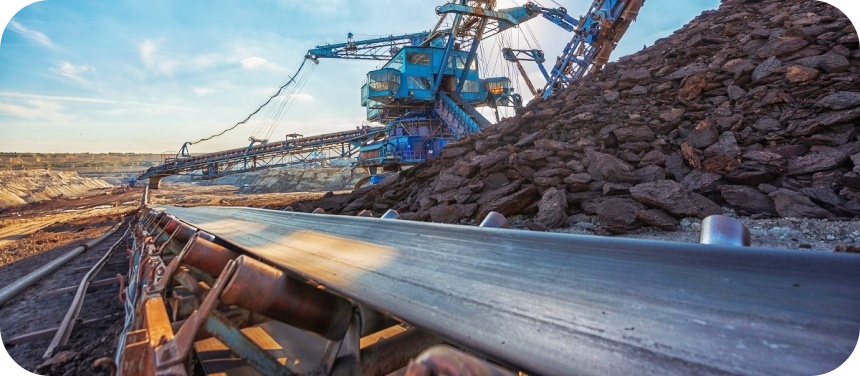
Conveyor Belt Material Properties
Understanding the properties of conveyor belt material used in various applications is crucial for selecting the right belt for specific industrial needs. This section provides an overview of commonly used materials and a comparative analysis of their properties, helping you make informed decisions about the best material for your conveyor belt.
Overview of Commonly Used Materials
Different materials are used to manufacture conveyor belts, each offering unique properties that make them suitable for various applications. Here are the most commonly used materials:
Thermoplastics
Thermoplastics are widely used in conveyor belts due to their versatility, durability, and ease of fabrication. Common types of thermoplastics include PVC (polyvinyl chloride), PU (polyurethane), and PE (polyethylene). These materials are ideal for applications requiring lightweight, flexible, and chemical-resistant belts. Thermoplastic belts are often used in food processing, packaging, and pharmaceutical industries because they are easy to clean and maintain.
Metal: Stainless and Carbon Steel
Metal conveyor belts, particularly those made from stainless steel and carbon steel, are known for their exceptional strength, durability, and resistance to high temperatures. Stainless steel belts are corrosion-resistant and suitable for applications involving harsh chemicals or extreme heat, such as food processing, automotive, and electronics manufacturing. Carbon steel belts offer high tensile strength and are commonly used in heavy-duty applications like mining and bulk material handling, where the conveyor belt material used must withstand significant wear and tear.
Rubber: Vulcanized and Non-Vulcanized
Rubber is a popular material for conveyor belts due to its excellent durability, flexibility, and resistance to abrasion. Vulcanized rubber belts undergo a curing process that enhances their strength and elasticity, making them suitable for heavy-duty applications such as mining, quarrying, and construction. Non-vulcanized rubber belts are softer and more flexible, ideal for lighter applications where flexibility and impact resistance are essential.
Fabric: Nylon, Polyester, Kevlar
Fabric conveyor belts are reinforced with materials like nylon, polyester, and Kevlar to enhance their strength and durability. Nylon belts are known for their high tensile strength and resistance to abrasion, making them suitable for heavy-duty applications. Polyester belts offer excellent resistance to moisture and chemicals, making them ideal for environments with harsh conditions. Kevlar-reinforced belts provide superior strength and durability, often used in demanding applications where the conveyor belt material used must withstand extreme stress and high impact.
Leather: The Classic Choice
Leather conveyor belts, while less common today, are still used in specific applications due to their unique properties. Leather belts offer excellent flexibility, durability, and resistance to wear. They are often used in industries requiring gentle handling of materials, such as the textile and woodworking industries. Leather belts are also preferred in applications where a non-conductive and non-magnetic material is necessary.
Comparative Analysis of Material Properties
Understanding the comparative properties of different conveyor belt materials is essential for selecting the best option for your application. Here is a comparative analysis of the key properties of commonly used conveyor belt materials:
Tensile Strength
- Thermoplastics: Moderate tensile strength, suitable for light to medium-duty applications.
- Metal: High tensile strength, ideal for heavy-duty applications and high load capacities.
- Rubber: High tensile strength, particularly in vulcanized rubber, making it suitable for heavy-duty applications.
- Fabric: High tensile strength, especially in Kevlar-reinforced belts, suitable for high-stress environments.
- Leather: Moderate tensile strength, adequate for specific applications requiring flexibility and durability.
Abrasion Resistance
- Thermoplastics: Moderate abrasion resistance, suitable for environments with minimal abrasive materials.
- Metal: Excellent abrasion resistance, ideal for applications involving sharp or abrasive materials.
- Rubber: High abrasion resistance, making it suitable for environments with significant wear and tear.
- Fabric: High abrasion resistance, especially in nylon and polyester belts, suitable for heavy-duty applications.
- Leather: Moderate abrasion resistance, suitable for applications with gentle material handling.
Flexibility
- Thermoplastics: High flexibility, ideal for applications requiring lightweight and adaptable belts.
- Metal: Low flexibility, suitable for applications requiring rigid and durable belts.
- Rubber: High flexibility, particularly in non-vulcanized rubber, making it suitable for applications requiring adaptable belts.
- Fabric: High flexibility, especially in nylon and polyester belts, suitable for various applications.
- Leather: High flexibility, making it ideal for applications requiring gentle handling and adaptability.
Chemical and Heat Resistance
- Thermoplastics: Moderate chemical resistance, high heat resistance in specific types like PU.
- Metal: Excellent chemical and heat resistance, particularly in stainless steel belts, suitable for harsh environments.
- Rubber: High chemical resistance, particularly in specific rubber compounds, suitable for various applications.
- Fabric: Moderate chemical and heat resistance, suitable for environments with moderate exposure to harsh conditions.
- Leather: Low chemical and heat resistance, suitable for specific applications requiring non-conductive and non-magnetic properties.
Selecting the right conveyor belt material used involves understanding the specific properties and advantages of each material. Thermoplastics, metals, rubber, fabrics, and leather each offer unique benefits, making them suitable for different industrial applications. By considering the tensile strength, abrasion resistance, flexibility, and chemical and heat resistance of each material, you can choose the most suitable conveyor belt material used for your specific needs, ensuring optimal performance and durability in your operations.
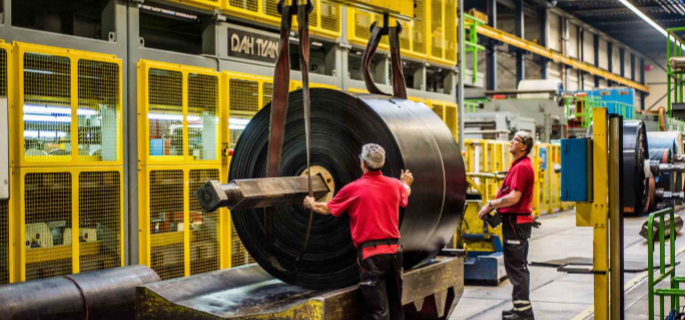
The Versatile Conveyor Belt Material Used Across Industries
Rubber is one of the most versatile materials used in the production of conveyor belts. Its unique properties make it suitable for a wide range of applications, from light-duty tasks to the most demanding heavy-duty operations. This section explores the versatility of rubber conveyor belts, the different types of rubber used, and the specific applications and advantages of rubber belts.
The Versatility of Rubber Conveyor Belts
Rubber conveyor belts are renowned for their flexibility, durability, and adaptability to various industrial environments.
- Mining and Quarrying: Rubber conveyor belts are extensively used in mining and quarrying operations. They can handle abrasive materials such as ores, rocks, and minerals, providing excellent resistance to wear and tear. The robustness of rubber belts ensures they can withstand the harsh conditions found in these environments.
- Agriculture: In the agricultural sector, rubber conveyor belts are used to transport crops, grains, and other agricultural products. Their flexibility and ability to handle a variety of materials make them ideal for moving both lightweight and bulk products efficiently.
- Food Processing: Rubber belts are often used in food processing plants due to their non-toxic and easy-to-clean properties. They can handle different food items, from raw ingredients to packaged goods, ensuring hygiene and safety standards are maintained.
- Manufacturing: In manufacturing industries, rubber conveyor belts are used to transport parts and products along assembly lines. Their durability and resistance to chemicals and oils make them suitable for handling various manufacturing processes.
- Recycling: Rubber belts are also used in recycling plants to sort and transport recyclable materials. Their strength and resistance to punctures and cuts make them ideal for handling a wide range of materials, including metals, plastics, and paper.
Types of Rubber Used
Rubber conveyor belts are made from various types of rubber, each offering distinct advantages for specific applications. The main types of rubber used include:
- Natural Rubber: Known for its excellent tensile strength and flexibility, natural rubber is often used in applications requiring a high degree of elasticity and durability. It is suitable for handling light to medium loads in relatively clean environments.
- Synthetic Rubber: Synthetic rubbers, such as SBR (Styrene-Butadiene Rubber), NBR (Nitrile Butadiene Rubber), and EPDM (Ethylene Propylene Diene Monomer), offer enhanced properties like oil and heat resistance. These rubbers are used in more demanding applications where exposure to chemicals, oils, or extreme temperatures is common.
- Vulcanized Rubber: Vulcanization is a process that involves heating natural or synthetic rubber with sulfur to improve its strength and elasticity. Vulcanized rubber belts are highly durable and resistant to abrasion, making them suitable for heavy-duty applications.
- Non-Vulcanized Rubber: Non-vulcanized rubber belts are softer and more flexible than their vulcanized counterparts. They are used in applications requiring gentle handling of materials, such as in food processing or packaging industries.
Rubber Belt Applications and Advantages
Rubber conveyor belts offer numerous advantages and are used in various applications across industries. Here are five examples highlighting the specific applications and benefits of rubber belts:
- Material Handling in Warehouses: Rubber conveyor belts are used in warehouses for transporting packages, boxes, and pallets. Their flexibility and ability to handle diverse loads make them ideal for efficient material handling and logistics operations.
- Automotive Industry: In the automotive industry, rubber belts are used to transport car parts and assemblies along production lines. The belts’ resistance to oils, greases, and chemicals ensures they can withstand the rigors of automotive manufacturing processes.
- Construction and Demolition: Rubber conveyor belts are used in construction and demolition sites to transport debris, rubble, and other materials. Their durability and resistance to impact and abrasion make them suitable for these harsh environments.
- Airport Baggage Handling: Airports use rubber conveyor belts in their baggage handling systems. The belts’ flexibility and strength allow them to efficiently move luggage through complex conveyor systems, ensuring smooth and reliable operation.
- Bulk Material Handling: In industries like cement, steel, and power generation, rubber belts are used to transport bulk materials such as coal, cement, and aggregates. Their robustness and ability to handle heavy loads ensure efficient and continuous operation.
Rubber conveyor belts are a versatile and reliable choice for various industrial applications. The unique properties of rubber, such as flexibility, durability, and resistance to abrasion, make it an ideal material for conveyor belts used in a wide range of environments. By understanding the different types of rubber used and the specific applications and advantages of rubber belts, industries can select the most suitable conveyor belt material used to meet their operational needs and enhance efficiency and productivity.
Finding the Right Conveyor Belt Material Used for Your Needs
Purchasing used conveyor belt material can be a cost-effective and sustainable option for many businesses. This guide explores the reasons for opting for used materials, where to find them, and essential inspection tips before making a purchase.
Why Opt for Used Material?
Opting for used conveyor belt material used in various applications offers several advantages:
- Cost Savings: Used conveyor belts are generally much cheaper than new ones. This can significantly reduce capital expenditure, especially for businesses with tight budgets or those looking to expand operations without substantial financial outlay.
- Environmental Benefits: Reusing conveyor belts reduces waste and the demand for new raw materials, contributing to environmental conservation. It helps in minimizing the ecological footprint of your operations by promoting recycling and sustainable practices.
- Immediate Availability: Used conveyor belts are often available immediately, unlike new belts that might require lead time for manufacturing and delivery. This immediate availability can be crucial for businesses needing quick replacements to minimize downtime.
- Proven Durability: Many used conveyor belts have already been tested in real-world conditions, proving their durability and performance. This track record can provide assurance about the belt’s ability to handle similar conditions in a new application.
- Customizability: Used belts can often be cut and customized to fit specific requirements. This flexibility makes them suitable for a variety of applications, from industrial to creative repurposing projects.
Where to Find Conveyor Belt Material for Sale Near Me
Finding high-quality used conveyor belt material used in various settings involves exploring several sources:
- Industrial Suppliers and Dealers: Many suppliers specialize in used industrial equipment, including conveyor belts. These suppliers can offer a wide selection of materials and detailed information about the belts’ condition and history.
- Online Marketplaces: Websites like eBay, Craigslist, and specialized industrial auction sites frequently list used conveyor belts for sale. These platforms can be a good source for finding belts at competitive prices and from a variety of sellers.
- Recycling Centers: Some recycling centers and scrap yards collect used conveyor belts as part of their operations. These centers can be an excellent resource for finding belts that have been retired from service but are still in good condition.
- Direct from Industries: Contacting companies that extensively use conveyor belts, such as mining or manufacturing firms, can yield opportunities to purchase used belts directly. These businesses often replace belts on a regular schedule and may be willing to sell their old belts at a reduced price.
- Networking and Referrals: Industry networks and trade associations can be valuable sources of information and referrals. Networking with other professionals in your field can help you locate suppliers and learn about available used conveyor belts.
Inspection Tips Before Purchase
When sourcing used conveyor belt material used in your operations, it is crucial to thoroughly inspect the belts to ensure they meet your requirements.
- Visual Inspection: Conduct a thorough visual inspection of the belt. Look for signs of excessive wear, such as cracks, fraying, or thinning areas. Ensure that the belt’s edges are intact and not excessively worn. This initial inspection can help identify any obvious issues that might affect performance.
- Surface Condition: Examine the belt’s surface for any signs of damage, such as gouges, cuts, or punctures. While minor surface imperfections may be acceptable, extensive damage can compromise the belt’s performance. Check for uniformity in thickness and texture across the belt.
- Flexibility and Rigidity: Check the flexibility and rigidity of the belt. A good quality used belt should retain its flexibility without being too stiff or brittle. Excessive rigidity can indicate material fatigue or exposure to harsh conditions. Flex the belt along its length to ensure it bends smoothly without cracking.
- Tensile Strength: Assess the belt’s tensile strength by checking for any weak spots or areas that have been excessively stretched. Ensure that the belt can handle the intended load without deforming or breaking. You might perform a small load test to see how the belt reacts under stress.
- Documentation and History: Whenever possible, obtain documentation or information about the belt’s history, including its previous use, maintenance records, and any repairs. This information can provide insights into the belt’s remaining lifespan and suitability for your application. Knowing the belt’s history can help predict its future performance and potential issues.
By considering these factors and following these tips, you can effectively source high-quality used conveyor belt material used in your operations. This approach ensures that you get the most value and performance from your investment, making the most of the benefits offered by recycled materials.
Improve efficiency with our reliable conveyor belt products.
FAQs About Conveyor Belt Material Used
Metals commonly used in conveyor belts include stainless steel and carbon steel. Stainless steel is widely preferred for its excellent resistance to corrosion and ability to withstand high temperatures. It is ideal for applications in food processing, pharmaceuticals, and chemical industries, where hygiene and durability are critical. Carbon steel, on the other hand, is known for its high tensile strength and is typically used in heavy-duty applications such as mining, construction, and bulk material handling. Both types of steel provide robust structural support and can handle significant wear and tear, ensuring long-lasting performance in demanding industrial environments.
The best material for a conveyor system depends on the specific requirements of the application. For general-purpose applications, rubber is often considered the best material due to its durability, flexibility, and resistance to abrasion. In environments where hygiene is paramount, such as food processing or pharmaceuticals, stainless steel or food-grade plastic is preferred for its ease of cleaning and resistance to contaminants. For high-temperature applications, materials like stainless steel or heat-resistant synthetic rubbers are ideal. Ultimately, the best material is determined by factors such as load weight, environmental conditions, and specific industry standards, ensuring optimal performance and longevity of the conveyor system.
Conveyor belts are manufactured from a variety of materials, each chosen for its specific properties suited to different applications. Common materials include:
Rubber: Widely used for its flexibility, durability, and resistance to abrasion. Both natural and synthetic rubbers are utilized, with vulcanized rubber offering enhanced strength and elasticity.
Thermoplastics: Materials such as PVC (polyvinyl chloride), PU (polyurethane), and PE (polyethylene) are popular for their versatility, lightweight, and chemical resistance. They are often used in food processing and packaging industries.
Metals: Stainless steel and carbon steel are used for their strength, durability, and resistance to extreme conditions. These metals are ideal for heavy-duty and high-temperature applications.
Fabrics: Nylon, polyester, and Kevlar are commonly used as reinforcement layers in belts to provide additional strength and durability. These materials offer excellent tensile strength and resistance to stretching and tearing.
Leather: Occasionally used for specific applications requiring flexibility and durability, such as in the textile and woodworking industries.
Food grade conveyor belts are made from materials that meet stringent health and safety standards to ensure hygiene and prevent contamination. Common materials include:
Food-Grade Plastic: Materials such as polyurethane (PU) and polyethylene (PE) are widely used due to their non-toxic nature, ease of cleaning, and resistance to chemicals. These plastics are ideal for handling various food products, from raw ingredients to packaged goods.
Stainless Steel: Often used in food processing environments where high temperatures and rigorous cleaning processes are involved. Stainless steel is corrosion-resistant and easy to sanitize, making it suitable for applications requiring high hygiene standards.
Food-Grade Rubber: Certain types of rubber, such as those compliant with FDA regulations, are used for their flexibility and durability. These rubbers are designed to withstand the harsh conditions of food processing, including exposure to oils and fats.
These materials ensure that food grade conveyor belts are safe for use in environments where food products are processed, packaged, and transported, maintaining the highest standards of hygiene and safety.
The surface of a conveyor belt can be made from various materials depending on its intended use. Common surface materials include:
Rubber: Durable and flexible, suitable for carrying heavy and abrasive materials.
PVC (Polyvinyl Chloride): Smooth, easy to clean, and often used in food processing.
PU (Polyurethane): Wear-resistant, oil and grease resistant, and ideal for food and pharmaceutical applications.
Fabric: Often reinforced with materials like polyester or nylon to provide additional strength and flexibility.
The material of a conveyor belt shaft is typically:
Steel: Commonly used due to its high strength and durability. Stainless steel is often used in environments where corrosion resistance is important.
Aluminum: Used in applications where weight is a concern and less strength is required.
Composite Materials: Sometimes used for specific applications that require unique properties such as high strength-to-weight ratios.
A conveyor belt is made of various materials based on its application. Common materials include:
Rubber: Provides flexibility and durability for general-purpose use.
PVC (Polyvinyl Chloride): Lightweight and resistant to chemicals, often used in the food industry.
PU (Polyurethane): Known for its wear resistance and flexibility, used in food and pharmaceutical applications.
Metal (Stainless Steel): Used in high-temperature or heavy-duty applications.
Fabric: Reinforced with materials like polyester, nylon, or cotton for additional strength.
Grade M24 refers to a high-quality grade of rubber conveyor belt used primarily in industries requiring a durable and wear-resistant material. The “M” signifies the grade’s resistance to cutting, gouging, and abrasion, while “24” indicates the tensile strength (24 MPa, MegaPascals). This grade is commonly used in mining, quarrying, and heavy-duty material handling.
There are several types of conveyor belts, including:
Flat Belt Conveyors: The most common type, used for general material handling.
Modular Belt Conveyors: Made of interlocking plastic pieces, ideal for easy cleaning and maintenance.
Cleated Belt Conveyors: Feature vertical cleats to help transport loose or granular materials.
Inclined/Declined Belt Conveyors: Designed to move materials up or down a slope.
Curved Belt Conveyors: Allow for changes in direction while maintaining the flow of materials.
Roller Bed Conveyors: Use rollers placed beneath the belt to reduce friction and support heavier loads.
The material widely used in making belt drives is rubber, often reinforced with materials like fabric (e.g., polyester, nylon) to provide additional strength and flexibility. Rubber is preferred due to its durability, flexibility, and ability to grip pulleys effectively, making it suitable for transmitting power efficiently in various mechanical systems.
Last Updated on August 16, 2024 by Jordan Smith
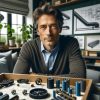
Jordan Smith, a seasoned professional with over 20 years of experience in the conveyor system industry. Jordan’s expertise lies in providing comprehensive solutions for conveyor rollers, belts, and accessories, catering to a wide range of industrial needs. From initial design and configuration to installation and meticulous troubleshooting, Jordan is adept at handling all aspects of conveyor system management. Whether you’re looking to upgrade your production line with efficient conveyor belts, require custom conveyor rollers for specific operations, or need expert advice on selecting the right conveyor accessories for your facility, Jordan is your reliable consultant. For any inquiries or assistance with conveyor system optimization, Jordan is available to share his wealth of knowledge and experience. Feel free to reach out at any time for professional guidance on all matters related to conveyor rollers, belts, and accessories.