Belt Conveyor System Details Information
Belt conveyor system details reveal how these mechanisms are integral to modern industry, facilitating the swift and efficient transportation of goods across various sectors.Belt conveyor system details:consists of two or more pulleys with an endless loop of carrying medium—the conveyor belt— around them. This overview introduces the foundational elements of belt conveyor systems, highlighting their importance in automating processes and reducing labor costs in industrial applications. By understanding the essential belt conveyor system details, businesses can enhance operational efficiency and adapt to the high demands of production and distribution. This post will delve into the critical components, working mechanisms, and strategic considerations involved in choosing and implementing the right conveyor system for specific industrial needs.
Exploring Belt Conveyor System Details
Definition and Functionality
Belt conveyor systems are a cornerstone of the modern industry, designed for the continuous transportation of goods and materials across varying distances. These systems consist of two or more pulleys, with a continuous loop of carrying medium—the conveyor belt—that rotates around them. One or more of the pulleys are powered, moving the belt and the material on the belt forward. The powered pulleys are known as drive pulleys while the unpowered ones are called idlers.
The essential function of belt conveyor system details lies in their ability to move products efficiently and reliably across production lines, warehouses, and even from one facility to another. This seamless transportation is crucial not only for industries such as mining, agriculture, and manufacturing but also in retail and airport baggage handling. The versatility of conveyor systems allows them to be customized with various belt materials tailored to different environmental conditions and material handling needs, making them indispensable in sectors where quick and effective movement of goods is critical.
Historical Background
The history of conveyor belts is a fascinating journey that mirrors the evolution of industrial technology. The first primitive conveyor belts appeared in the late 18th century, with the basic concepts used primarily in the agricultural and mining industries to move bulk materials. These early belts were typically made of leather or canvas driven by pulleys and were manually operated.
However, the industrial revolution catalyzed significant advancements in conveyor technology. The introduction of steam power in the 19th century, and later, electrical power, transformed conveyor belts from simple manual systems to complex mechanized systems. In 1901, the Swedish engineering company Sandvik invented the first steel conveyor belt, which was more durable and capable of handling heavier loads than its predecessors.
Further innovation occurred in the 20th century with the development of synthetic materials, such as rubbers and polymers, which provided more strength, flexibility, and resistance to environmental factors. These materials revolutionized belt conveyor system details by enabling the design of belts that could be used in diverse environments and for a broader range of applications. Today, modern conveyor belts are highly engineered systems designed with sophisticated materials and capabilities, including sensors and automated controls, that optimize efficiency and safety.
The journey from those early designs to today’s advanced systems highlights the ingenuity and continual progress within the engineering and manufacturing fields. Belt conveyor systems have evolved from basic mechanical components to intricate systems that are integral in various industries around the world. This evolution reflects broader industrial innovations and challenges, emphasizing the continuous need for efficiency and productivity improvements in all sectors of the economy.
As industries continue to demand faster, more efficient, and safer transportation methods for goods and materials, the role of belt conveyor systems is likely to grow. Innovations in materials science and automation technology may lead to the next generation of conveyor systems, which will be even more reliable, efficient, and tailored to specific industrial needs. Understanding these belt conveyor plant details is crucial for anyone involved in the design, operation, or maintenance of these systems, as they provide the critical link in a chain of operations that must run smoothly for optimal production and distribution efficiency.

Belt Conveyor System Details: Components and Functions
A belt conveyor system is an essential mechanism in material handling, used to transport goods and materials over short or long distances. Here’s a detailed look at its components and their functions:
1. Belt
- Function: The main surface that carries the materials.
- Details: Made from materials like rubber, fabric, or metal, chosen based on the type of material being transported and the environment of the conveyor system.
2. Pulleys
- Drive Pulley
- Function: Provides the driving force to move the belt.
- Details: Connected to the motor; located at the head of the conveyor.
- Idler Pulley
- Function: Guides and maintains belt tension.
- Details: Positioned at the tail or along the conveyor to support the belt and reduce slack.
3. Motor
- Function: Powers the drive pulley.
- Details: Can be electric, hydraulic, or pneumatic, depending on the system’s power requirements.
4. Gearbox
- Function: Adjusts the speed and torque from the motor to the belt.
- Details: Ensures the belt runs at the correct speed and power.
5. Frame
- Function: Provides structural support to the conveyor system.
- Details: Typically made of steel or aluminum; holds all components in place.
6. Rollers
- Carrying Rollers
- Function: Support the belt and the load being transported.
- Details: Placed along the length of the conveyor to keep the belt flat and stable.
- Return Rollers
- Function: Support the belt on its return journey to the drive pulley.
- Details: Positioned underneath the belt to minimize friction and wear.
7. Tensioning Device
- Function: Maintains the correct tension in the belt.
- Details: Can be a screw take-up, gravity take-up, or hydraulic take-up system; prevents belt slippage and ensures smooth operation.
8. Belt Cleaner
- Function: Removes residual material from the belt.
- Details: Positioned at the discharge point to keep the belt clean and prevent material build-up.
9. Hopper
- Function: Feeds materials onto the belt.
- Details: Funnels materials evenly onto the belt; can be adjusted for different material types and loads.
10. Discharge Chute
- Function: Guides materials off the belt.
- Details: Controls the direction and flow of discharged materials; can be designed to suit different discharge requirements.
11. Guarding and Safety Devices
- Function: Ensure the safe operation of the conveyor system.
- Details: Includes emergency stop switches, guards to cover moving parts, and sensors to detect malfunctions or overloads.
Each of these components works together to create a functional and efficient belt conveyor system, tailored to the specific needs of the material being transported and the operating environment.

Belt Conveyor System Details: Working Mechanism
Working Mechanism
Understanding the working mechanism of belt conveyor systems is crucial for optimizing their efficiency and functionality. This section breaks down the basic working principle and the various energy sources that can power these systems, providing a comprehensive look into how these complex assemblies operate seamlessly in countless industrial applications.
A belt conveyor system operates on a simple yet effective mechanism that involves several key steps and components working in unison to transport materials efficiently from one point to another.
1. Loading the Material
The process begins with the material being loaded onto the conveyor belt. This can be achieved through various means, such as manually, using a hopper, or with the help of auxiliary equipment like feeders and chutes. The hopper or feeding device ensures that the material is evenly distributed onto the belt to avoid overload and ensure smooth transportation.
2. Motor and Drive Pulley Operation
Once the material is loaded, the motor is activated. The motor is connected to the drive pulley via a gearbox. The gearbox adjusts the motor’s speed and torque to match the operational requirements of the conveyor. The drive pulley, powered by the motor, generates the necessary force to move the belt.
3. Belt Movement
As the drive pulley rotates, it moves the conveyor belt along with it. The belt, supported by a series of carrying rollers, travels along the conveyor frame. These rollers are spaced at intervals along the conveyor to support the belt and the load it carries, ensuring minimal sagging and maximum efficiency.
4. Material Transportation
The moving belt carries the material along the designated path. The belt’s surface can be smooth or textured, depending on the type of material being transported. The belt’s speed can be adjusted to control the rate of material flow, ensuring that it meets the specific needs of the operation.
5. Idler Pulleys and Return Rollers
As the belt moves, it passes over idler pulleys positioned at intervals along the conveyor. These pulleys help guide and maintain the tension of the belt. Return rollers, located on the underside of the conveyor, support the belt as it returns to the drive pulley. These rollers minimize friction and wear, ensuring a smooth and efficient return path for the belt.
6. Tensioning Device
To maintain optimal belt tension, a tensioning device is used. This device can be a screw take-up, gravity take-up, or hydraulic take-up system. Proper tension is crucial to prevent belt slippage and ensure the belt remains aligned with the pulleys and rollers.
7. Discharge of Material
At the end of the conveyor path, the material is discharged. This can be facilitated by a discharge chute, which guides the material off the belt in a controlled manner. The design of the discharge chute can be adjusted to suit the specific needs of the material and the next stage of the process.
8. Belt Cleaning
To ensure the belt remains clean and free of residual material, a belt cleaner is installed at the discharge point. This cleaner removes any material that might stick to the belt, preventing build-up and maintaining the efficiency of the system.
9. Safety and Control
Throughout the operation, safety devices and control systems are in place to monitor and regulate the conveyor’s performance. Emergency stop switches allow operators to halt the conveyor in case of an emergency, while sensors detect malfunctions or overloads, alerting operators to potential issues.
By understanding and managing these components and steps, a belt conveyor system can effectively and efficiently transport materials, making it a vital tool in various industries such as mining, manufacturing, and logistics.
Basic Working Principle
Belt conveyors operate on a relatively simple principle: a belt made from various materials is set in motion by pulleys that rotate. The process begins with the belt being looped around the drive pulley (or pulleys) that are connected to a motor. As the motor activates, the rotational movement is transferred from the motor to the drive pulley. The friction between the pulley and the belt propels the belt forward, carrying any material placed upon it from the loading point to the unloading point.
The system typically includes at least one or more idler pulleys which are not powered but serve to guide and support the belt as it travels. These pulleys help maintain the belt’s tension and alignment. The entire system is supported by a frame that holds all the components in their proper positions, ensuring that the belt has a smooth path to follow.
For the conveyor to operate efficiently, the belt’s surface, material, and tension must be correctly selected and maintained. The belt’s movement can be controlled in terms of speed and direction, depending on the needs of the application. This controlled movement is what allows conveyor belts to be such an integral part of production lines and material handling systems.
The basic working principle of a belt conveyor system is straightforward and involves several key components working together to transport materials efficiently. Here is an outline of the fundamental working principle:
1. Material Loading
Materials are loaded onto the conveyor belt through a loading area, such as a hopper, chute, or directly onto the belt from another process. This initial step ensures that materials are placed uniformly onto the belt to avoid overloading and ensure smooth transport.
2. Motor and Drive Pulley Activation
A motor powers the system by driving the drive pulley. The drive pulley, connected to the motor, initiates the movement of the belt. The motor can be electric, hydraulic, or pneumatic, depending on the system requirements. The gearbox, connected to the motor, adjusts the motor’s speed and torque to match the operational needs of the conveyor.
3. Belt Movement
The drive pulley rotates, pulling the belt along with it. The belt, typically made from rubber, fabric, or metal, moves over a series of carrying rollers. These rollers support the belt and the load, ensuring that the belt stays flat and stable during transport.
4. Material Transport
As the belt moves, it carries the loaded materials along the designated path. The continuous movement of the belt ensures a steady flow of materials from the loading point to the discharge point. The speed of the belt can be adjusted to control the rate at which materials are transported.
5. Idler Pulleys and Return Rollers
Idler pulleys are strategically placed along the conveyor to guide and maintain the tension of the belt. Return rollers, located on the underside of the conveyor, support the belt as it returns to the drive pulley, reducing friction and wear.
6. Tensioning Device
A tensioning device maintains the appropriate tension in the belt, preventing slippage and ensuring efficient operation. This can be a screw take-up, gravity take-up, or hydraulic take-up system, which adjusts to compensate for any changes in belt length due to stretching or wear.
7. Material Discharge
At the end of the conveyor path, the materials are discharged from the belt. This can be facilitated by a discharge chute, which directs the materials to the next stage of the process or into a storage area. The design of the discharge area ensures a controlled and efficient transfer of materials.
8. Belt Cleaning
To keep the belt clean and prevent material build-up, a belt cleaner is positioned at the discharge point. This device removes any residual material from the belt, ensuring it remains clean and operationally efficient.
9. Safety and Control Systems
Safety devices, such as emergency stop switches, are integrated into the system to allow for immediate shutdown in case of an emergency. Sensors monitor the system’s performance, detecting any malfunctions or overloads and alerting operators to potential issues.

Energy Sources
The operation of belt conveyor systems can be powered by various energy sources, which influence their application and efficiency. The most common sources include:
- Motor-driven: This is the most prevalent source of power for conveyor belts, especially in industrial applications. Electric motors are used to drive the drive pulley, effectively moving the conveyor belt. Depending on the system, the motor might be connected directly to the pulley or through a gearbox that reduces speed and increases torque.
- Gravity: Some conveyor systems are designed to utilize gravity, especially for downward transportation. These systems are usually positioned at a slight decline, and the weight of the materials being transported is enough to move the belt as it goes over the rollers. Gravity conveyors are simple and cost-effective but are limited by the necessity of having a downward path.
- Manual: In smaller or less automated settings, some conveyor belts can be manually operated. These are less common and are typically found in applications where motorized belts are not feasible or necessary. Manual belts require human effort to move goods along the conveyor, which can be labor-intensive and inefficient for larger operations.
Each of these energy sources has its advantages and constraints, and the choice of which to use depends largely on the specific needs of the application, including the desired speed, load capacity, and operational environment. Motor-driven systems offer the greatest flexibility and control, making them suitable for most industrial applications. Gravity systems, while limited, provide a cost-effective solution for certain logistical operations. Manual systems are less common but may be used in specialty applications where simplicity and cost are more critical than efficiency.
Understanding these belt conveyor system details not only aids in selecting the right system for an application but also enhances the ability to troubleshoot, maintain, and optimize the conveyor for prolonged service life and better reliability. This detailed examination of the working mechanism and energy sources of conveyor systems underscores the importance of thoughtful design and configuration in meeting the demanding conditions of modern industrial environments.
Types of Belt Conveyor System
Belt conveyor systems come in various types, each designed to suit different applications and industries. Here are some of the most common types of belt conveyor systems:
1. Flat Belt Conveyor
- Description: The most basic type of belt conveyor, featuring a flat belt that runs over flat surfaces or rollers.
- Applications: Ideal for transporting light to medium-weight items in industries such as packaging, manufacturing, and logistics.
- Advantages: Simple design, cost-effective, and easy to maintain.
2. Cleated Belt Conveyor
- Description: Similar to flat belt conveyors but with cleats (raised dividers) attached to the belt.
- Applications: Used for transporting bulk materials and items on inclined or vertical paths, such as in agriculture and mining.
- Advantages: Prevents material from slipping back, allowing for steeper inclines.
3. Modular Belt Conveyor
- Description: Uses interlocking plastic or metal modules instead of a continuous belt.
- Applications: Commonly used in food processing, pharmaceuticals, and automotive industries.
- Advantages: Highly flexible, easy to clean, and can be designed to follow complex paths, including curves.
4. Curved Belt Conveyor
- Description: Designed to navigate corners and changes in direction within a conveyor system.
- Applications: Used in industries where space is limited and conveyors need to fit around obstacles or follow non-linear paths.
- Advantages: Efficiently utilizes space and integrates seamlessly into existing layouts.
5. Incline/Decline Belt Conveyor
- Description: Features an adjustable angle to transport materials up or down between different levels.
- Applications: Used in warehouses, distribution centers, and manufacturing plants to move products to different heights.
- Advantages: Reduces the need for manual lifting, increasing efficiency and safety.
6. Trough Belt Conveyor
- Description: The belt is designed to form a trough shape, which helps contain loose materials.
- Applications: Ideal for transporting bulk materials like grains, coal, sand, and gravel.
- Advantages: High capacity, suitable for long-distance transport of bulk materials.
7. Roller Bed Belt Conveyor
- Description: The belt is supported by rollers rather than a flat surface.
- Applications: Suitable for handling heavier loads and for applications where belt friction needs to be minimized.
- Advantages: Reduces friction, making it easier to transport heavy items over long distances.
8. Sanitary and Washdown Conveyors
- Description: Designed for environments requiring frequent cleaning and hygiene, such as food processing and pharmaceuticals.
- Applications: Used in industries with strict sanitary requirements.
- Advantages: Made from corrosion-resistant materials and designed for easy cleaning.
9. Heavy-Duty Belt Conveyor
- Description: Built to handle extremely heavy and bulky materials.
- Applications: Used in mining, construction, and other heavy industries.
- Advantages: Robust construction, capable of handling large loads and harsh conditions.
10. Portable Belt Conveyor
- Description: Lightweight, mobile conveyors that can be easily moved and adjusted.
- Applications: Used in construction sites, warehouses, and agricultural fields for temporary conveying needs.
- Advantages: Highly versatile, easy to transport and set up.
Each type of belt conveyor system is tailored to specific applications and operational requirements, offering distinct advantages depending on the material, environment, and logistical needs. Understanding the different types of belt conveyors can help in selecting the right system for a particular industry or application.
Choosing the Right Belt Conveyor System
Selecting the right conveyor system is pivotal for ensuring efficiency, reducing downtime, and optimizing the workflow within various industrial environments. This section discusses the critical considerations needed when choosing the ideal conveyor system, focusing on the materials and products being handled, as well as the specific environmental and spatial challenges that might influence system design and functionality.
Material and Product Considerations
When selecting a conveyor belt system, the characteristics of the materials and products that will be transported are among the most crucial factors to consider. These characteristics can significantly affect the choice of conveyor type, belt material, and system design:
- Type of Material: The nature of the materials—whether they are bulky, heavy, fine-grained, sticky, or hot—affects the type of conveyor belt needed. For example, materials that are hot or have high abrasiveness might require specialized conveyor belts that are heat-resistant and designed to reduce wear and tear.
- Weight of Material: The weight of the products being transported directly influences the design of the conveyor system. Heavier loads require stronger belts with higher load capacities and more robust construction to prevent breakdowns and maintain efficiency.
- Moisture Content: Materials with high moisture content can affect the integrity of certain conveyor belt materials and may require the use of stainless steel components and water-resistant belts to prevent corrosion and slippage.
- Abrasive Characteristics: Materials that are highly abrasive can wear down belt materials quickly. For these types of materials, belts with reinforced fabrics or top-coatings that resist cuts and gouges are preferable to extend the lifespan of the conveyor system.
Understanding these material and product considerations is critical in the selection process, as they ensure the chosen belt conveyor system details are tailored to handle the specific demands of the materials, thereby optimizing both operational efficiency and longevity.
Environmental and Spatial Considerations
The environmental conditions and physical space of the facility where the conveyor system will be installed play a significant role in determining the most suitable conveyor design:
- Environmental Factors: Temperature, humidity, and exposure to chemicals are all environmental factors that can affect conveyor operation. Systems used in cold environments may require materials that maintain flexibility at low temperatures, while those used in wet or corrosive environments might need corrosion-resistant materials like stainless steel or specially coated components.
- Spatial Limitations: The available space within a facility can greatly influence the type and configuration of conveyor systems that can be installed. In facilities with limited space, curved conveyors, vertical conveyors, or even overhead systems may be necessary to maximize the use of available space. Each option comes with its own set of belt conveyor system details that must be considered, such as turning radius for curved conveyors or load capacity for vertical systems.
- Facility Layout: The layout of the plant will determine the path that the conveyor system will follow. Complex layouts may require conveyors with flexible pathing options, such as modular belt conveyors that can easily be configured to navigate around obstacles and through tight spaces.
Considering these environmental and spatial aspects during the conveyor selection process is crucial to ensure that the system not only fits within the operational parameters but also operates efficiently under the specific conditions of the site. By thoroughly evaluating these belt conveyor system or belt conveyor details, businesses can make informed decisions that result in optimal conveyor solutions tailored to their unique industrial needs, ensuring both high performance and cost-effectiveness in their material handling operations.
FAQs about Belt Conveyor System Details
Conveyor belts are engineered systems designed to move materials or objects from one location to another efficiently. The technical specifications of conveyor belts can vary widely depending on their intended use, but common parameters include material, width, thickness, tensile strength, and operating speed. Materials used for conveyor belts might range from rubber and PVC (polyvinyl chloride) to more specialized materials like Kevlar or stainless steel, depending on the demands of the application such as heat resistance or load capacity. Additionally, conveyor belts can be either flat or textured, with the latter helping to increase grip on transported items. Belt length and width are determined based on the load and the distance that needs to be covered by the conveyor system.
A conveyor belt system operates on the principle of two or more pulleys, with a continuous loop of material – the conveyor belt – that rotates around them. One of the pulleys is usually powered, moving the belt and the material on the belt forward. The powered pulley is called the drive pulley while the unpowered one is known as the idler pulley. This system is commonly used in various industries including manufacturing, agriculture, and packaging, for transporting goods over short or long distances. Additional components like motors, belts, and control systems are configured to meet specific handling requirements, ensuring that materials are moved efficiently from one stage of production or processing to another.
The conveyor belt system comprises several key components that work together to transport materials efficiently. These include:
Belt: This is the flexible element of the conveyor that moves the materials.
Pulleys: Typically, there are at least two pulleys in a conveyor belt system – a drive pulley, which is powered and moves the belt, and an idler pulley, which is unpowered.
Motors: These provide the necessary power to the drive pulley.
Rollers: These support the conveyor belt and are spaced throughout the length of the system to ensure that the belt remains in alignment and doesn’t sag.
Frame: This provides the structure that supports the pulleys, rollers, belt, and the material being conveyed. Each component must be precisely engineered and maintained to ensure efficient and reliable operation of the conveyor belt system.
The basic working principle of a belt conveyor system is relatively straightforward and involves the movement of a looped belt along a predefined path. The system typically consists of a belt that is wrapped around two or more pulleys. When at least one pulley is powered, usually by an electric motor, the friction between the belt and the pulley causes the belt to move. This movement transports the material placed on the belt from one point to another. The belt’s motion can be controlled in terms of speed and direction to suit specific tasks within a production process. Additionally, the efficiency and effectiveness of a conveyor belt system depend on proper loading, regular maintenance, and the suitability of the belt material for the specific task.
Flat Belt Conveyor: The most common type, featuring a flat, continuous belt made from materials such as rubber, fabric, or plastic. It is used for general material handling and light-to-medium duty applications.
Cleated Belt Conveyor: Similar to flat belts but with cleats attached to the belt surface. The cleats help to prevent materials from slipping, making them suitable for inclined or vertical transport.
Modular Belt Conveyor: Made of interlocking plastic or metal modules. These belts are highly flexible, durable, and easy to clean, making them ideal for food processing and other industries requiring hygiene and complex routing.
A conveyor belt structure typically consists of several layers:
Cover Layer: The outer layer, made from materials like rubber or PVC, which protects the belt from wear and tear and provides grip.
Carcass: The middle layer, providing strength and support. It can be made from various materials, including fabric, steel cords, or other synthetic materials.
Bottom Cover: The underside layer, which can also be made of rubber or PVC, providing additional protection and grip on the pulleys.
Conveyor belts are measured in several ways:
Length: The total distance from end to end of the belt. This can be measured by running a tape measure along the length of the belt.
Width: The distance across the belt from one edge to the other. This is typically measured with a ruler or measuring tape.
Thickness: The distance between the top and bottom surfaces of the belt, which can be measured using a caliper.
To calculate the load on a belt conveyor, you need to consider several factors:
Material Load (Q): The mass of the material being transported per unit length of the conveyor belt, often measured in kilograms per meter (kg/m).
Belt Speed (v): The speed at which the conveyor belt moves, measured in meters per second (m/s).
Total Load (L): This can be calculated using the formula: L=Q×v
L = Q \times vL=Q×v Where L
LL is the load in kilograms per second (kg/s).
The anatomy of a belt conveyor includes:
Belt: The continuous loop that carries the material.
Pulleys: The drive pulley provides the driving force, and the idler pulleys guide and support the belt.
Motor: Powers the drive pulley.
Gearbox: Adjusts the speed and torque from the motor to the belt.
Frame: Provides structural support to the conveyor system.
Rollers: Support the belt and the load, reducing friction.
Tensioning Device: Maintains proper belt tension.
Belt Cleaner: Removes material from the belt to prevent build-up.
Hopper: Feeds material onto the belt.
Discharge Chute: Guides material off the belt.
Guarding and Safety Devices: Ensure safe operation by covering moving parts and providing emergency stops.
The most common conveyor belt system is the Flat Belt Conveyor. It is widely used across various industries due to its simplicity, versatility, and cost-effectiveness. This system is suitable for a range of applications, from packaging and assembly lines to warehouses and distribution centers, making it the go-to choice for general material handling tasks.
Last Updated on July 31, 2024 by Jordan Smith
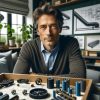
Jordan Smith, a seasoned professional with over 20 years of experience in the conveyor system industry. Jordan’s expertise lies in providing comprehensive solutions for conveyor rollers, belts, and accessories, catering to a wide range of industrial needs. From initial design and configuration to installation and meticulous troubleshooting, Jordan is adept at handling all aspects of conveyor system management. Whether you’re looking to upgrade your production line with efficient conveyor belts, require custom conveyor rollers for specific operations, or need expert advice on selecting the right conveyor accessories for your facility, Jordan is your reliable consultant. For any inquiries or assistance with conveyor system optimization, Jordan is available to share his wealth of knowledge and experience. Feel free to reach out at any time for professional guidance on all matters related to conveyor rollers, belts, and accessories.