Comprehensive Guide to Belt Conveyor Roller Types
Belt conveyor roller types are essential components in the operation and efficiency of belt conveyor systems. These rollers support and guide the conveyor belt, ensuring smooth and reliable movement of materials across various distances. The significance of these rollers cannot be overstated, as they play a crucial role in reducing friction, preventing belt wear, and maintaining overall conveyor performance. This guide will delve into the different types of belt conveyor rollers, highlighting their unique features and applications. Understanding the diverse belt conveyor roller types is vital for selecting the right components to enhance productivity and efficiency in various industrial sectors.
What are Belt Conveyor Roller Types
Definition and Basic Function of Belt Conveyor Rollers
Belt conveyor roller types are essential components in conveyor systems, serving a critical role in the smooth and efficient movement of materials. A belt conveyor roller is a cylindrical component that facilitates the movement of the conveyor belt and its load. These rollers are strategically placed along the conveyor frame to support the belt, reduce friction, and guide the belt through its motion.
The primary function of belt conveyor rollers is to minimize the resistance that occurs when the conveyor belt moves, thus enhancing the system’s overall efficiency. By providing support and stability to the conveyor belt, these rollers ensure that the belt remains aligned and operates smoothly, even under heavy loads and continuous use. This reduction in friction not only improves the operational efficiency of the conveyor system but also extends the lifespan of the belt itself, reducing maintenance costs and downtime.
The Distinction Between Rollers and Idlers in Conveyor Systems
In the context of conveyor systems, it is crucial to understand the distinction between rollers and idlers, as they are often used interchangeably but serve different purposes. While all idlers are rollers, not all rollers are idlers.
Rollers
Rollers in conveyor systems are the primary components that support and guide the conveyor belt. They come in various types and are designed to handle different load capacities and environmental conditions. Rollers are responsible for reducing the drag that the belt encounters as it moves, thereby increasing the efficiency and reliability of the conveyor system. They are typically used in the carrying section of the conveyor where the belt is loaded with materials.
Idlers
Idlers, on the other hand, refer specifically to the rollers that are designed to support the unloaded portion of the conveyor belt. They are usually placed on the return side of the conveyor belt to provide support and maintain tension in the belt. Idlers help in maintaining the alignment of the belt and ensuring that it runs smoothly without sagging or misalignment. There are different types of idlers, including return idlers, training idlers, and impact idlers, each serving a specific function in the conveyor system.
Types of Belt Conveyor Rollers
Understanding the various conveyor belt roller types is essential for selecting the right components for specific applications. Each type of roller is designed to meet different operational needs and environmental conditions. The following are some common types of belt conveyor rollers:
Standard Belt Conveyor Rollers
Standard belt conveyor rollers are the most commonly used rollers in conveyor systems. They are designed to provide support to the conveyor belt and its load in a wide range of applications. These rollers are typically made from durable materials such as steel or aluminum and are available in various sizes to accommodate different conveyor belt widths and load capacities. Standard rollers are suitable for most general-purpose conveyor systems and are known for their reliability and cost-effectiveness.
Heavy Duty Belt Conveyor Rollers
Heavy duty belt conveyor rollers are designed for applications that involve the transportation of heavy loads or materials with high impact forces. These rollers are constructed from robust materials and feature reinforced designs to withstand the rigors of demanding operational environments. Heavy duty rollers are commonly used in industries such as mining, construction, and manufacturing, where conveyor systems are required to handle large volumes of material efficiently.
Idler Rollers
Idler rollers are specifically designed to support the return side of the conveyor belt. They are available in different configurations, including flat return idlers, v-return idlers, and garland idlers. Each type of idler roller is designed to maintain belt alignment and prevent sagging, ensuring smooth and efficient belt operation. Idler rollers are essential for maintaining the tension and tracking of the conveyor belt, which helps in prolonging the lifespan of the belt and reducing maintenance costs.
Drive Rollers
Drive rollers, also known as drive pulleys, are critical components in conveyor systems that provide the necessary power to move the conveyor belt. These rollers are connected to a motor and transmit torque to the belt, enabling it to move forward. Drive rollers are typically made from high-strength materials and are designed to handle the torque and rotational forces required for conveyor operation. They play a vital role in the overall performance and efficiency of the conveyor system.
Specialized Rollers for Specific Applications
In addition to the standard and heavy duty rollers, there are specialized belt conveyor roller types designed for unique applications. These rollers are customized to meet specific operational requirements and environmental conditions. For example, rollers used in food processing industries are made from materials that are resistant to corrosion and contamination. Similarly, rollers used in high-temperature environments are constructed from heat-resistant materials to ensure reliable performance. Specialized rollers are designed to enhance the efficiency and longevity of conveyor systems in specialized applications.
Understanding the various types of roller in conveyor belt is crucial for selecting the right components to optimize the performance and efficiency of conveyor systems. Each type of roller serves a specific function and is designed to meet different operational needs and environmental conditions. By choosing the appropriate rollers, businesses can enhance the reliability and longevity of their conveyor systems, reducing maintenance costs and improving overall productivity.
Types of Belt Conveyor Roller Types
Various Belt Conveyor Roller Types Utilized in Different Applications
Belt conveyor roller types are essential components in the efficient functioning of conveyor systems across various industries. These rollers come in different designs and are tailored to meet specific operational requirements. Understanding the diverse types of belt conveyor rollers is crucial for selecting the appropriate roller for your conveyor system, ensuring optimal performance, longevity, and cost-effectiveness. This section provides a detailed overview of the different types of conveyor belt rollers and their specific applications.
Standard Belt Conveyor Rollers
Standard belt conveyor rollers are the most commonly used rollers in conveyor systems. They are designed to provide support and stability to the conveyor belt, facilitating the smooth movement of materials. These rollers are typically made from materials such as steel or aluminum and are available in various sizes to accommodate different conveyor belt widths and load capacities.
Description and Application of Standard Rollers:
- Steel Rollers: Durable and suitable for general-purpose applications, ideal for transporting bulk materials in industries like mining and agriculture.
- Plastic Rollers: Lightweight and corrosion-resistant, used in food processing and packaging industries.
- Aluminum Rollers: Lightweight yet strong, often used in conveyor systems where weight reduction is crucial, such as in automotive manufacturing.
- Rubber-Covered Rollers: Provide additional grip and are used in applications where the conveyor belt needs extra traction, such as in recycling plants.
- Stainless Steel Rollers: Corrosion-resistant and hygienic, commonly used in pharmaceutical and food processing industries.
Heavy Duty Belt Conveyor Rollers
Heavy duty belt conveyor rollers are designed to handle large volumes and heavy loads, making them ideal for demanding industrial environments. These rollers are constructed from robust materials and feature reinforced designs to withstand high impact and stress.
Insight into the Design and Application of Heavy Duty Rollers:
- High-Load Steel Rollers: Built to support extremely heavy loads, used in industries like mining and construction.
- Impact Rollers: Designed with shock-absorbing materials to handle the impact of falling materials, commonly used in quarry and aggregate operations.
- High-Temperature Rollers: Made from heat-resistant materials for use in environments with high temperatures, such as in steel mills.
- Chemical-Resistant Rollers: Constructed from materials that resist chemical corrosion, used in chemical processing plants.
- Extra-Wide Rollers: Designed for wide conveyor belts carrying bulky materials, used in the lumber and paper industries.
Idler Rollers
Idler rollers are specifically designed to support the return side of the conveyor belt, maintaining tension and alignment. These rollers come in various configurations to address specific needs in conveyor systems.
Differentiation of Idler Roller Types:
- Flat Return Idlers: Used to support the unloaded return side of the belt, ensuring smooth and efficient operation.
- V-Return Idlers: Feature a v-shaped configuration to enhance belt tracking and stability.
- Garland Idlers: Consist of multiple rollers connected in a chain-like formation, used to support belts in curved sections of the conveyor.
- Self-Aligning Idlers: Automatically adjust to correct belt misalignment, improving belt tracking and reducing wear.
- Training Idlers: Help to maintain proper belt alignment and prevent the belt from wandering off track.
Drive Rollers
Drive rollers, also known as drive pulleys, are integral to conveyor systems as they provide the necessary power to move the conveyor belt. These rollers are connected to a motor, which transmits torque to the belt, enabling it to move.
Exploration of Drive Roller Mechanisms:
Feature | Drive Rollers | Idler Rollers |
---|---|---|
Function | Transmit power to move the belt | Support and guide the belt |
Material | High-strength materials | Various materials depending on application |
Design | Reinforced to handle torque | Standard designs for support |
Placement | Head or tail of the conveyor | Throughout the conveyor frame |
Maintenance | Requires regular checks and lubrication | Minimal maintenance needed |
Specialized Rollers for Specific Applications
Specialized belt conveyor roller types are designed to meet unique operational needs and environmental conditions. These rollers incorporate innovative technologies to enhance efficiency and performance in specific applications.
Introduction to Customized Rollers:
- Anti-Static Rollers: Designed to dissipate static electricity, used in industries handling sensitive electronic components.
- Magnetic Rollers: Incorporate magnetic properties to attract and separate ferrous materials, used in recycling and material handling.
- Grooved Rollers: Feature grooves for guiding belts with raised edges, ensuring precise belt tracking.
- Tapered Rollers: Used in curved sections of conveyors to maintain belt alignment and smooth movement.
- Water-Resistant Rollers: Made from materials resistant to water and moisture, used in marine and outdoor applications.
Understanding the various belt conveyor roller types and their applications is crucial for selecting the right rollers to enhance the efficiency, reliability, and longevity of your conveyor system. By choosing the appropriate rollers for specific needs, businesses can optimize their conveyor operations and achieve better performance outcomes.
Selecting the Right Belt Conveyor Roller Types
Key Considerations When Choosing Rollers for Your Conveyor System
Selecting the appropriate belt conveyor roller types for your system is a critical decision that affects the efficiency, longevity, and performance of the entire conveyor operation. The right choice depends on various factors including material, size, weight of the load, operational environment, and specific application needs. Each of these factors plays a significant role in determining the most suitable rollers for your conveyor system.
Material
The material of the belt conveyor roller types is one of the primary considerations. The choice of material affects the roller’s durability, weight, and suitability for specific environments.
- Steel: Ideal for heavy-duty applications due to its strength and durability. Commonly used in mining and construction industries.
- Stainless Steel: Offers corrosion resistance and is suitable for food processing, pharmaceutical, and chemical industries.
- Plastic: Lightweight and corrosion-resistant, often used in packaging and light-duty conveyor systems.
- Rubber-Covered: Provides additional grip and cushioning, making it ideal for handling delicate or slippery materials.
- Aluminum: Lightweight and resistant to corrosion, suitable for environments where weight is a concern, such as in aerospace or automotive industries.
Size
The size of the rollers, including diameter and length, must be appropriate for the conveyor belt and the loads it will carry. Incorrect sizing can lead to inefficiencies and increased wear and tear.
- Small Diameter Rollers: Suitable for light-duty applications where space is limited and belt speed is relatively low.
- Medium Diameter Rollers: Versatile and used in a variety of applications, balancing strength and flexibility.
- Large Diameter Rollers: Designed for heavy-duty applications, capable of supporting large loads and high belt speeds.
- Custom Length Rollers: Tailored to fit specific conveyor belt widths, ensuring proper support and alignment.
- Tapered Rollers: Used in curved conveyor sections to maintain belt alignment and smooth transitions.
Weight of the Load
The weight of the load being conveyed is a crucial factor in selecting the right belt conveyor roller types. Rollers must be capable of supporting the weight without deforming or failing.
- Lightweight Rollers: Used for small packages and lightweight materials, typically in packaging and e-commerce.
- Medium Load Rollers: Suitable for general manufacturing and assembly lines, handling moderate weights.
- Heavy Load Rollers: Designed for bulk materials and heavy industrial loads, such as in mining and quarrying.
- Impact Rollers: Built to absorb shock and protect the conveyor system from heavy, falling loads.
- High Load Capacity Rollers: Used in applications requiring the movement of very heavy items, such as automotive components or large construction materials.
Operational Environment
The operational environment significantly impacts the choice of belt conveyor roller types. Factors such as temperature, humidity, and exposure to chemicals dictate the material and design of the rollers.
- High-Temperature Environments: Require heat-resistant rollers, often made from specialized alloys or coated with heat-resistant materials.
- Cold Environments: Need rollers that can operate efficiently at low temperatures, typically made from materials that resist brittleness.
- Wet Environments: Use water-resistant rollers, such as those made from stainless steel or plastic, to prevent corrosion.
- Dusty or Dirty Environments: Require rollers with sealed bearings and smooth surfaces to minimize maintenance and prevent buildup.
- Chemical Exposure: Demand rollers made from chemically resistant materials, such as certain plastics or coated metals, to avoid degradation.
Specific Application Needs
Different applications have unique requirements that influence the choice of belt conveyor roller types. Understanding these specific needs ensures that the rollers selected provide optimal performance. Five examples based on application needs are:
- Food Processing: Requires hygienic, easy-to-clean rollers, often made from stainless steel or food-grade plastic.
- Pharmaceuticals: Needs rollers that meet strict cleanliness and safety standards, typically stainless steel with smooth finishes.
- Recycling: Utilizes heavy-duty, impact-resistant rollers to handle various materials and withstand harsh conditions.
- Aerospace: Demands lightweight yet strong rollers to handle delicate components without adding excessive weight to the system.
- Automotive: Requires robust rollers capable of handling heavy components and high-throughput operations.
Selecting the right belt conveyor roller types is a multifaceted process that involves careful consideration of material, size, load weight, operational environment, and specific application needs. By understanding these factors and evaluating the unique requirements of your conveyor system, you can choose the most suitable rollers to enhance efficiency, reduce maintenance costs, and extend the lifespan of your conveyor system. Each roller type has its own set of advantages tailored to different applications, ensuring that there is a perfect match for every conveyor requirement.
Maintenance and Replacement of Belt Conveyor Roller Types
Tips on Maintaining Belt Conveyor Rollers for Prolonged Service Life
Proper maintenance of belt conveyor roller types is crucial to ensure their longevity and efficient operation. Regular maintenance helps prevent unexpected breakdowns, reduces downtime, and extends the service life of the rollers.
- Regular Inspection:
Routine inspections are vital to detect early signs of wear and tear on belt conveyor roller types. Inspect rollers for signs of corrosion, abnormal noise, misalignment, and physical damage. Early detection allows for timely intervention and prevents minor issues from escalating into major problems. - Lubrication:
Keeping the rollers well-lubricated is essential for smooth operation and reducing friction. Use the recommended lubricant for the specific type of roller and follow the manufacturer’s guidelines for lubrication frequency. Over-lubrication or using the wrong lubricant can cause damage, so it’s crucial to adhere to proper lubrication practices. - Cleaning:
Regular cleaning of belt conveyor roller types helps in removing dirt, debris, and any material buildup that can cause operational inefficiencies. Use appropriate cleaning methods and solutions to avoid damaging the rollers. In industries where hygiene is critical, such as food processing, ensure that cleaning agents are suitable and safe for use. - Alignment Checks:
Misaligned rollers can cause uneven wear on the conveyor belt and reduce the efficiency of the conveyor system. Regularly check the alignment of the rollers and adjust as necessary. Proper alignment ensures that the belt runs smoothly and evenly, reducing the risk of damage to both the belt and the rollers. - Bearing Maintenance:
The bearings in belt conveyor roller types are critical components that need regular attention. Check for signs of wear, noise, or excessive vibration. Replace worn or damaged bearings promptly to avoid further damage to the rollers. Well-maintained bearings help in smooth roller operation and extend the overall lifespan of the rollers.
Guidelines on Identifying When to Replace Rollers and How to Choose the Right Replacement
Knowing when to replace belt conveyor roller types is crucial to maintaining the efficiency and reliability of your conveyor system. Here are some guidelines to help you identify the right time for conveyor roller replacement and how to choose the appropriate replacement rollers:
- Signs of Wear and Damage:
Regular inspections will reveal signs of wear and damage. Look for flat spots, cracks, dents, or any deformation on the rollers. Excessive wear on the surface of the rollers can lead to poor belt tracking and increased friction. Replace rollers showing significant wear or damage to maintain optimal conveyor performance. - Unusual Noises:
Abnormal noises during conveyor operation, such as grinding or squeaking, can indicate issues with the rollers. These noises often point to problems like worn bearings, misalignment, or insufficient lubrication. If lubricating or realigning the rollers doesn’t resolve the issue, it may be time to replace them. - Increased Vibration:
Excessive vibration is another sign that the rollers may need replacement. Vibration can result from worn bearings, misalignment, or roller imbalance. Continuous vibration can lead to further damage to the conveyor system, so it’s essential to address the issue promptly by replacing the problematic rollers. - Belt Tracking Issues:
Poor belt tracking, where the conveyor belt moves off-center, can be caused by worn or misaligned rollers. If tracking issues persist despite adjustments, inspect the rollers for wear or damage. Replacing the affected rollers can restore proper belt alignment and improve system efficiency. - Performance Degradation:
A noticeable decrease in the performance of the conveyor system, such as reduced speed or increased energy consumption, can be attributed to worn or damaged rollers. Monitoring the performance of your conveyor system and identifying any decline can help determine when to replace the rollers.
Choosing the Right Replacement Rollers
When selecting replacement rollers for your conveyor system, consider the following factors to ensure compatibility and optimal performance:
- Material Compatibility:
Choose rollers made from materials suitable for your specific application. For example, stainless steel rollers are ideal for corrosive environments, while rubber-covered rollers provide extra grip for handling slippery materials. - Correct Size:
Ensure the replacement rollers match the size specifications of the original rollers, including diameter and length. Incorrectly sized rollers can cause operational issues and reduce the efficiency of the conveyor system. - Load Capacity:
Select rollers that can support the weight of the materials being conveyed. Overloading the rollers can lead to premature wear and failure. Ensure the load capacity of the replacement rollers matches or exceeds that of the original rollers. - Operational Environment:
Consider the environmental conditions in which the rollers will operate. Choose rollers designed to withstand the specific conditions, such as high temperatures, humidity, or exposure to chemicals. - Manufacturer Recommendations:
Follow the manufacturer’s guidelines and recommendations for selecting replacement rollers. Using recommended rollers ensures compatibility with your conveyor system and helps maintain warranty coverage.
By adhering to these maintenance tips and guidelines for replacement, you can ensure the longevity and efficient operation of your belt conveyor roller types, ultimately enhancing the productivity and reliability of your conveyor system.
Where to Find Belt Conveyor Roller Types
Advice on Sourcing Quality Conveyor Belt Rollers, Including New and Used Options
Finding the right types of roller in conveyor belt is essential for maintaining the efficiency and reliability of your conveyor system. Whether you are looking for new or used rollers, sourcing from reputable suppliers ensures you get high-quality products that meet your operational needs.
- Specialized Manufacturers:
Directly sourcing from specialized manufacturers of belt conveyor rollers is often the best way to ensure you get high-quality, durable rollers. These manufacturers have expertise in producing rollers tailored to specific applications and operational requirements. They offer a range of products, including standard, heavy-duty, and specialized rollers, ensuring that you find the exact type needed for your conveyor system. - Industrial Suppliers:
Industrial suppliers and distributors often carry a wide variety of belt conveyor roller types from multiple manufacturers. They provide a convenient one-stop-shop for various industrial components, including rollers. Suppliers such as Grainger, MSC Industrial Supply, and Motion Industries have extensive catalogs and can provide technical support to help you select the right rollers. - Online Marketplaces:
Online marketplaces like Amazon, eBay, and Alibaba offer both new and used conveyor rollers. These platforms allow you to compare prices, read customer reviews, and select from a wide range of options. While buying online, it’s crucial to verify the seller’s reputation and the quality of the products through reviews and ratings. - Auction Sites and Surplus Equipment Dealers:
For cost-effective options, consider purchasing used rollers from auction sites like Bid on Equipment or surplus equipment dealers. These sources often have lightly used or surplus rollers at a fraction of the cost of new ones. Ensure to inspect the rollers for wear and damage before purchase to ensure they are in good working condition. - Local Dealers and Distributors:
Local dealers and distributors can provide personalized service and quicker delivery times. They often have established relationships with reputable manufacturers and can offer expert advice on selecting the right belt conveyor roller types. Visiting a local dealer allows you to physically inspect the rollers before purchase, ensuring they meet your quality standards.
The Importance of Partnering with Reputable Suppliers
Partnering with reputable suppliers for the purchase and maintenance of belt conveyor roller types is crucial for several reasons:
- Quality Assurance:
Reputable suppliers are committed to providing high-quality products that meet industry standards. They source their rollers from trusted manufacturers known for their quality and durability. This ensures that the rollers you purchase are reliable and capable of withstanding the demands of your conveyor system. - Technical Expertise:
Working with reputable suppliers gives you access to technical expertise and support. They can assist you in selecting the right types of conveyor belt rollers for your specific application, considering factors such as load capacity, material, and environmental conditions. Their expertise helps in making informed decisions that enhance the performance and longevity of your conveyor system. - After-Sales Support:
Reputable suppliers offer after-sales support, including installation assistance, maintenance services, and troubleshooting. This support is invaluable in ensuring that your conveyor rollers operate efficiently and any issues are promptly addressed. After-sales support also includes warranty services, giving you peace of mind and protection against manufacturing defects. - Customization Options:
Established suppliers often provide customization options to meet unique operational needs. Whether you require specialized rollers for high-temperature environments or custom sizes for specific conveyor designs, reputable suppliers can tailor their products to match your requirements. This customization ensures optimal performance and efficiency in your conveyor operations. - Long-Term Partnerships:
Building a long-term partnership with a reputable supplier fosters trust and reliability. Over time, the supplier becomes familiar with your operational needs and can anticipate and address future requirements. This relationship ensures a consistent supply of quality roller conveyor belt types and contributes to the overall efficiency and productivity of your conveyor system.
Sourcing high-quality belt conveyor roller types involves exploring various options, from specialized manufacturers and industrial suppliers to online marketplaces and local dealers. Each sourcing avenue offers unique advantages, and choosing the right one depends on your specific needs and preferences. Partnering with reputable suppliers is critical for ensuring quality, accessing technical expertise, receiving after-sales support, and obtaining customized solutions. By prioritizing these factors, you can enhance the performance, reliability, and longevity of your conveyor system, ultimately contributing to the success of your operations.
FAQs About Belt Conveyor Roller Types
Conveyor rollers come in various types, each designed to fulfill specific roles within a conveyor system. The primary types include:
Standard Rollers: These are the most commonly used rollers, suitable for general-purpose applications across various industries. They are made from durable materials such as steel or aluminum and come in different sizes.
Heavy Duty Rollers: Designed for applications involving heavy loads or high impact forces. These rollers are robust and can withstand the rigors of demanding environments like mining or construction.
Idler Rollers: These rollers support the belt on the return side and help maintain proper tension and alignment. They come in various configurations, including flat return, v-return, and self-aligning idlers.
Drive Rollers: Connected to a motor, these rollers transmit power to the conveyor belt, enabling movement. They are essential for the operation of powered conveyor systems.
Specialized Rollers: Customized for unique applications, such as anti-static rollers for electronics handling, grooved rollers for guiding belts with raised edges, and water-resistant rollers for outdoor or marine environments.
Understanding these types helps in selecting the right rollers for specific applications, ensuring efficiency and longevity of the conveyor system.
Idler rollers are critical components in conveyor systems, supporting the unloaded side of the belt and maintaining alignment. The different types of idler rollers include:
Flat Return Idlers: These provide support to the belt on the return side, ensuring smooth and stable operation.
V-Return Idlers: Featuring a v-shaped configuration, these idlers enhance belt tracking and stability, preventing the belt from shifting off-center.
Garland Idlers: Consisting of multiple rollers connected in a chain-like formation, these idlers are used to support belts in curved sections, providing flexibility and reducing belt stress.
Self-Aligning Idlers: These idlers automatically adjust to correct belt misalignment, helping to maintain proper tracking and reduce wear on the belt.
Impact Idlers: Designed to absorb shock and protect the belt from heavy impact loads, these idlers are typically placed at loading points to cushion the belt from falling material.
Each type of idler roller serves a specific purpose, and selecting the right type is essential for maintaining the efficiency and reliability of the conveyor system.
Belt conveyors come in various types, each designed to meet specific operational needs. The main types of belt conveyors include:
Flat Belt Conveyors: These are the most common type, featuring a flat belt running on flat rollers or a slider bed. They are used for transporting light to medium-weight materials in industries like manufacturing, packaging, and distribution.
Incline/Decline Belt Conveyors: Designed to move materials between different elevations. These conveyors have belts with cleats or textured surfaces to prevent materials from slipping as they move uphill or downhill.
Cleated Belt Conveyors: Equipped with vertical cleats, these conveyors are ideal for transporting loose or bulk materials without spillage. They are commonly used in agriculture, food processing, and mining.
Curved Belt Conveyors: These conveyors navigate around curves and corners, optimizing space utilization in facilities. They are used in industries where floor space is limited or conveyor paths need to change direction.
Modular Belt Conveyors: Featuring interlocking plastic segments, these conveyors offer flexibility and easy maintenance. They are used in industries requiring frequent cleaning and quick belt changes, such as food processing and pharmaceuticals.
Each type of belt conveyor is designed for specific tasks, and selecting the right one depends on the nature of the material being transported and the operational environment.
Drive rollers and driven rollers play different roles in conveyor systems, contributing to the movement and control of the conveyor belt. The key differences between them include:
Function:
Drive Roller: This roller is connected to a motor and is responsible for transmitting power to the conveyor belt, causing it to move. It plays a crucial role in the overall operation of powered conveyor systems.
Driven Roller: Also known as an idler roller, this roller is not powered. Instead, it is turned by the friction of the moving belt. Driven rollers provide support and help guide the belt but do not contribute to its propulsion.
Placement:
Drive Roller: Typically located at the head or tail of the conveyor, where it can efficiently transmit power to the belt.
Driven Roller: Positioned throughout the conveyor frame to support the belt and maintain alignment, particularly on the return side.
Construction:
Drive Roller: Constructed with materials and designs to handle the torque and rotational forces required to move the belt. It often includes features such as reinforced shafts and high-strength bearings.
Driven Roller: Generally simpler in construction, designed primarily for support rather than power transmission.
Understanding these differences is essential for designing and maintaining an efficient conveyor system, ensuring that each component fulfills its specific role effectively.
Last Updated on July 25, 2024 by Jordan Smith
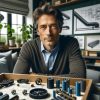
Jordan Smith, a seasoned professional with over 20 years of experience in the conveyor system industry. Jordan’s expertise lies in providing comprehensive solutions for conveyor rollers, belts, and accessories, catering to a wide range of industrial needs. From initial design and configuration to installation and meticulous troubleshooting, Jordan is adept at handling all aspects of conveyor system management. Whether you’re looking to upgrade your production line with efficient conveyor belts, require custom conveyor rollers for specific operations, or need expert advice on selecting the right conveyor accessories for your facility, Jordan is your reliable consultant. For any inquiries or assistance with conveyor system optimization, Jordan is available to share his wealth of knowledge and experience. Feel free to reach out at any time for professional guidance on all matters related to conveyor rollers, belts, and accessories.