Garland Belt Conveyor Idler Roller: Improving Performance
Idler rollers are essential components in the performance and longevity of belt conveyors, providing crucial support and reducing friction for smooth material transport. Garland belt conveyor idler roller provide stable support for heavy-duty conveyor belts, preventing spillage and ensuring efficient material transport.The garland belt conveyor idler roller is specifically designed to handle heavy materials at high speeds, making it ideal for demanding industrial applications. Unlike standard idler rollers, garland idlers offer enhanced flexibility and durability, allowing them to perform efficiently in adverse conditions. Their unique design helps in reducing the impact on the conveyor belt, minimizing wear and tear, and ensuring continuous operation even with irregular loads. This introduction highlights the significant role of garland belt conveyor idler rollers in optimizing conveyor systems and maintaining operational efficiency.
What are Garland Belt Conveyor Idler Rollers?
Garland belt conveyor idler rollers are specialized components used in belt conveyor systems, designed to support and guide the conveyor belt while reducing friction and wear. These idler rollers are distinct from standard idler rollers in several key ways, offering unique advantages that enhance the performance and durability of conveyor systems.
Garland belt conveyor idler rollers consist of multiple rollers linked together in a configuration that allows them to flex and adapt to varying loads and conveyor belt movements. This flexible design provides superior support and reduces the risk of belt misalignment, ensuring smooth and efficient operation. Garland idlers are particularly effective in handling heavy materials at high speeds, making them ideal for industries such as mining, construction, and bulk material handling.
The primary function of garland belt conveyor idler rollers is to minimize the friction between the conveyor belt and the rollers, thereby reducing wear and tear on the belt and extending its lifespan. By distributing the load more evenly across multiple rollers, garland idlers help to maintain the belt’s alignment and prevent damage caused by heavy or irregular loads. This flexibility also allows garland idlers to absorb impacts and vibrations, further protecting the conveyor system and enhancing its overall efficiency.
Types of Garland Belt Conveyor Idler Roller
There are several types of garland belt conveyor idler rollers, each designed to perform specific functions within a conveyor system. Understanding the differences between these types can help in selecting the right garland idlers for various applications.
Upper Garland Idlers
Upper garland idlers are installed on the carrying side of the conveyor belt, where they support the belt and the load it carries. These idlers are crucial in maintaining the belt’s alignment and stability, especially when transporting heavy or bulky materials. Upper garland idlers are designed to accommodate the weight and movement of the load, ensuring that the belt remains centered and operates smoothly.
Upper garland idlers are typically used in applications where the conveyor belt needs to handle heavy loads at high speeds. Their flexible design allows them to adapt to changes in load distribution and belt movement, preventing misalignment and reducing the risk of belt damage. This adaptability makes upper garland idlers an essential component in maintaining the efficiency and reliability of the conveyor system.

Return Garland Idlers
Return garland idlers are installed on the return side of the conveyor belt, where they support the empty belt as it returns to the loading point. These idlers play a critical role in guiding the belt and preventing sagging or misalignment, which can lead to operational inefficiencies and increased wear on the belt.
Return garland idlers are designed to provide consistent support for the empty belt, ensuring that it remains taut and properly aligned. This support helps to reduce the risk of belt damage and extends the lifespan of the conveyor system. By maintaining the belt’s alignment and preventing sagging, return garland idlers contribute to the overall efficiency and reliability of the conveyor operation.
- Specifically designed for the return side of the conveyor belt.
- Helps in guiding the empty belt back to the loading point.
- Available in two, three, or five-roll configurations.

Garland Idlers for Load Points
Garland idlers for load points are specifically designed to handle the impact and weight of materials being loaded onto the conveyor belt. These idlers are typically installed at the loading points of the conveyor system, where the belt is subjected to significant forces from falling materials.
Garland idlers for load points are engineered to absorb the impact of heavy loads, reducing the stress on the conveyor belt and minimizing the risk of damage. Their flexible design allows them to adapt to changes in load distribution and belt movement, ensuring that the belt remains properly aligned and operates smoothly. This adaptability makes garland idlers for load points an essential component in maintaining the efficiency and reliability of the conveyor system, especially in applications where the belt is subjected to heavy impacts and irregular loads.

Two-Roll Garland Idler:
- Consists of two idler rollers linked together.
- Suitable for light to medium load capacities.
- Commonly used in short to medium-length conveyors.
Three-Roll Garland Idler:
- Features three idler rollers connected in a triangular arrangement.
- Provides better support and stability for the conveyor belt.
- Ideal for medium to heavy load capacities.
Five-Roll Garland Idler:
- Includes five idler rollers linked together, offering enhanced support.
- Used for very heavy load capacities and long conveyor belts.
- Ensures uniform distribution of load and minimizes belt sag.
Offset Garland Idler:
- The idler rollers are arranged in an offset pattern.
- Provides additional stability and reduces belt sway.
- Commonly used in high-speed conveyor systems.
Self-Aligning Garland Idler:
- Equipped with a mechanism to automatically align the conveyor belt.
- Prevents belt misalignment and reduces maintenance needs.
- Suitable for long conveyors with varying loads.

Impact Garland Idler:
- Designed with reinforced rollers to absorb impact at loading points.
- Protects the conveyor belt from damage due to heavy or sharp materials.
- Often used in mining and quarrying applications.
Transition Garland Idler:
- Used in the transition zone where the conveyor belt changes inclination.
- Helps in maintaining the belt profile and reducing belt stress.
- Available in various roll configurations depending on the application.
V-Return Garland Idler:
- The rollers are arranged in a V-shape to support the return side of the belt.
- Enhances belt tracking and stability.
- Suitable for conveyors with large belt widths.
Garland belt conveyor idler rollers are essential components in modern conveyor systems, offering superior support and flexibility compared to standard idler rollers. Their ability to adapt to varying loads and belt movements makes them ideal for demanding industrial applications, ensuring the smooth and efficient operation of the conveyor system. By understanding the different types of garland idlers and their specific functions, businesses can select the right components to optimize their conveyor operations and extend the lifespan of their equipment.
The Advantages of Using Garland Belt Conveyor Idler Roller
Garland belt conveyor idler rollers offer a range of advantages that significantly enhance the performance and durability of conveyor systems. These advantages stem from their unique design and ability to adapt to various operational demands, making them an invaluable component in many industrial applications.
Adaptability to Heavy Loads and Large Lump Sizes
One of the most significant advantages of garland belt conveyor idler rollers is their adaptability to heavy loads and large lump sizes. Traditional idler rollers may struggle to handle the stress and wear caused by transporting massive, bulky materials. In contrast, garland idlers are designed with a flexible, linked configuration that distributes the load across multiple rollers. This distribution reduces the stress on individual rollers and the conveyor belt itself, preventing premature wear and tear.
The ability to adapt to heavy loads ensures that the conveyor system operates efficiently, even under demanding conditions. This adaptability is particularly beneficial in industries such as mining, construction, and bulk material handling, where conveyors regularly transport large, heavy materials. By accommodating these challenging loads, garland belt conveyor idler rollers help maintain the system’s longevity and reliability.
Enhanced Mobility for Irregular Loads
Another key advantage of garland belt conveyor idler rollers is their enhanced mobility for irregular loads. In many industrial applications, the materials being transported are not uniform in size or shape. Irregular loads can cause alignment issues and operational inefficiencies with standard idler rollers. However, the flexible design of garland idlers allows them to adapt to these variations, ensuring smooth and stable transportation of materials.
This enhanced mobility is achieved through the garland idlers’ ability to pivot and adjust to the changing contours of the conveyor belt and the load it carries. This flexibility minimizes the risk of belt misalignment and reduces the likelihood of material spillage or blockages. As a result, garland belt conveyor idler rollers contribute to more efficient and reliable conveyor operations, even when handling unpredictable loads.
Impact Reduction for Material Handling and Protection of the Conveyor Belt
Garland belt conveyor idler rollers are also highly effective at reducing the impact forces associated with material handling. When heavy or bulky materials are loaded onto the conveyor belt, they can create significant impact forces that strain the belt and the supporting idlers. These impact forces can lead to belt damage, increased maintenance requirements, and operational downtime.
Garland idlers mitigate these impact forces through their linked roller design, which distributes the impact across multiple points. This distribution reduces the stress on any single roller and protects the conveyor belt from excessive wear and damage. By cushioning the impact, garland belt conveyor idler rollers enhance the overall durability of the conveyor system and minimize the need for frequent repairs or replacements.
Durability and Reliability
- Garland Idler Rollers are designed to withstand harsh environmental conditions and heavy loads.
- Made from high-quality materials, ensuring long service life and minimal maintenance.
Flexibility
- The garland design allows for better alignment and adaptability to the conveyor structure.
- Can handle varying degrees of load and belt tension, providing smooth operation.
Reduced Maintenance
- The robust construction reduces the frequency of maintenance and replacements.
- Sealed bearings and other protective features minimize wear and tear.
Enhanced Performance
- Improves the efficiency and speed of material transport on conveyor belts.
- Reduces energy consumption due to smoother operation and less friction.
Safety
- Designed to reduce the risk of belt misalignment and potential spillage.
- Enhances the overall safety of conveyor operations, particularly in hazardous environments.
The Role of Return Garland Idlers in Facilitating Belt Guide and Enhancing Conveyor Efficiency
Return garland idlers play a crucial role in facilitating the belt guide and enhancing conveyor efficiency. Positioned on the return side of the conveyor belt, these idlers support the empty belt as it returns to the loading point. Their primary function is to maintain the belt’s alignment and prevent sagging, which can lead to operational inefficiencies and increased wear.
Return garland idlers achieve this by providing consistent support and guiding the belt along its path. Their flexible design allows them to adapt to changes in the belt’s tension and movement, ensuring that the belt remains properly aligned. This alignment is essential for preventing belt misalignment and minimizing the risk of damage.
By facilitating the belt guide, return garland idlers help maintain the overall efficiency and reliability of the conveyor system. Proper belt alignment reduces friction and wear, extending the lifespan of both the belt and the idlers. Additionally, it ensures that the conveyor operates smoothly and efficiently, reducing the likelihood of operational disruptions and downtime.
The advantages of using garland belt conveyor idler rollers are numerous and significant. Their adaptability to heavy loads and large lump sizes, enhanced mobility for irregular loads, impact reduction capabilities, and the crucial role of return garland idlers in maintaining belt alignment all contribute to the superior performance and longevity of conveyor systems. These benefits make garland belt conveyor idler rollers an essential component in optimizing the efficiency and reliability of industrial conveyor operations.
Applications of Garland Belt Conveyor Idler Roller
Mining Industry
- Used extensively in underground and open-pit mining operations.
- Suitable for conveying bulk materials such as coal, ore, and aggregates.
Material Handling
- Employed in facilities that handle bulk materials, including ports, steel plants, and power stations.
- Ideal for transporting materials over long distances.
Construction Industry
- Used in the transportation of construction materials such as sand, gravel, and cement.
- Effective for moving materials in both small and large-scale construction projects.
Cement Plants
- Integral to the conveyor systems in cement manufacturing plants.
- Helps in the efficient movement of raw materials, clinker, and finished cement products.
Agriculture
- Utilized in agricultural settings for transporting grains, seeds, and other agricultural products.
- Enhances the efficiency of material handling in farms and grain storage facilities.
Examples of Garland Belt Conveyor Idler Roller Types
- Three-Roll Garland Idlers
- Consists of three rollers linked together, providing a stable and balanced support system.
- Commonly used in medium to heavy-duty applications.
- Five-Roll Garland Idlers
- Includes five rollers, offering even more support and stability.
- Suitable for very heavy loads and long conveyor systems.
Garland Belt Conveyor Idler Roller Specifications and Selection
Understanding the specifications and selection criteria for garland belt conveyor idler rollers is essential for optimizing conveyor performance and ensuring the longevity of your conveyor system. This section provides a detailed overview of the key features and technical specifications of garland idlers, along with a guide on selecting the right type for various conveyor operations and materials.
Key Features and Technical Specifications of Garland Idlers
Garland belt conveyor idler rollers are designed with several key features that enhance their performance and durability. These features include the number of rolls, the arrangement of the rollers, and the materials used in their construction.
Roll Numbers and Arrangements
Garland idlers are typically available in various configurations, with the number of rolls ranging from three to five. The specific configuration depends on the requirements of the conveyor system and the nature of the materials being transported. The most common configurations include:
- 3-Roll Garland Idlers: These idlers consist of three rollers linked together in a triangular arrangement. They provide excellent support and flexibility for standard conveyor operations.
- 4-Roll Garland Idlers: With four rollers, these idlers offer enhanced support and stability for heavier loads and larger lump sizes.
- 5-Roll Garland Idlers: The five-roll configuration provides maximum support and flexibility, making it ideal for handling extremely heavy loads and high-impact applications.
The rollers used in garland idlers are typically made from high-quality materials such as steel or composite materials, ensuring durability and resistance to wear. Steel idler rollers are known for their strength and durability, making them suitable for heavy-duty applications. Composite rollers, on the other hand, offer the advantage of being lighter and more corrosion-resistant, which can be beneficial in certain environments.
Sealing and Lubrication
To ensure smooth operation and minimize maintenance requirements, garland belt conveyor idler rollers are equipped with advanced sealing and lubrication systems. Sealed bearings protect the rollers from dust and contaminants, reducing the risk of premature wear and extending the lifespan of the idlers. Additionally, many garland idlers feature self-lubricating bearings, which help maintain optimal performance and reduce the need for frequent lubrication.
Guide on Selecting the Right Garland Idler Type
Selecting the right garland belt conveyor idler roller type is crucial for optimizing conveyor performance and ensuring the efficient transport of materials. The selection process involves considering several factors, including the type of materials being conveyed, the operational environment, and the specific requirements of the conveyor system.
Material Type and Load Characteristics
The type of materials being transported and their load characteristics play a significant role in determining the appropriate garland idler type. For instance:
- Heavy and Bulky Materials: For applications involving the transport of heavy and bulky materials, a 4-roll or 5-roll garland idler configuration is recommended. These configurations provide enhanced support and stability, reducing the risk of belt misalignment and wear.
- Irregular Loads: If the conveyor system frequently handles irregular loads, such as varying sizes and shapes of materials, garland idlers with flexible configurations (e.g., 4-roll or 5-roll) are ideal. Their adaptability ensures smooth and stable transport, minimizing the risk of material spillage or blockages.
- Light to Medium Loads: For lighter to medium loads, a 3-roll garland idler configuration may be sufficient. These idlers offer excellent support and flexibility for standard conveyor operations.
Operational Environment
The operational environment also influences the selection of garland belt conveyor idler rollers. Factors such as temperature, humidity, and exposure to corrosive substances should be considered:
- Harsh Environments: In environments with extreme temperatures, high humidity, or exposure to corrosive substances, composite rollers may be more suitable due to their corrosion resistance and lightweight properties.
- Standard Environments: For standard operational environments, steel rollers are typically preferred due to their strength and durability.
Conveyor System Requirements
The specific requirements of the conveyor system, including speed, incline, and load distribution, also impact the selection of garland idlers:
- High-Speed Conveyors: For high-speed conveyor systems, it is essential to choose garland idlers with advanced sealing and lubrication systems to ensure smooth operation and reduce maintenance requirements.
- Inclined Conveyors: In inclined conveyor systems, selecting garland idlers that provide sufficient support and stability is crucial to prevent belt slippage and ensure efficient material transport.
Conveyor Specifications
- Belt Width: Ensure the idler matches the width of your conveyor belt.
- Load Capacity: Determine the maximum load the conveyor will handle and choose idlers that can support this weight.
- Speed: High-speed conveyors may require idlers with specific design features to handle the increased wear and tear.
Application Requirements
- Distance and Incline: Long-distance or inclined conveyors may need idlers with additional support and stability.
- Vibration and Impact: Applications with high vibration or impact loads may require reinforced idlers.
Understanding the specifications and selection criteria for garland belt conveyor idler rollers is vital for optimizing conveyor performance and ensuring the longevity of the system. By considering factors such as material type, operational environment, and conveyor system requirements, you can select the right garland idler type to meet your specific needs. With their advanced design and durable construction, garland belt conveyor idler rollers offer a reliable and efficient solution for a wide range of industrial applications.
Garland Belt Conveyor Idler Roller Parts and Accessories
To ensure the optimal performance and longevity of garland belt conveyor idler rollers, it is crucial to understand the various parts and accessories that support their function. This section provides a detailed look at these components and offers advice on maintaining an inventory of essential parts for quick repairs and replacements.
Detailed Look at Parts and Accessories Specific to Garland Idler Rollers
Garland belt conveyor idler rollers consist of several key parts and accessories that contribute to their effective operation. Understanding these components can help in identifying issues and performing maintenance or replacements when necessary.
1. Rollers
The rollers are the primary components of garland idlers, responsible for supporting the conveyor belt and reducing friction. They come in various materials, including steel and composite materials, each suited to different operational environments. Steel rollers are known for their durability and strength, while composite rollers offer lighter weight and corrosion resistance.
2. Bearings
Bearings are critical to the smooth operation of garland belt conveyor idler rollers. They reduce friction between the rollers and the shaft, ensuring that the rollers rotate smoothly. Bearings can be sealed or shielded to protect against dust and contaminants, extending their lifespan. Regular inspection and lubrication of bearings are essential for maintaining their performance.
3. Seals
Seals protect the internal components of the idler rollers from dust, moisture, and other contaminants. Effective sealing is crucial to prevent premature wear and damage to the bearings. There are various types of seals, including labyrinth seals and contact seals, each designed to provide different levels of protection.
4. Shafts
The shaft is the central axis around which the garland belt conveyor idler rollers rotate. It must be robust and precisely machined to ensure the proper alignment and function of the rollers. Shafts are typically made from high-strength materials to withstand the loads and stresses of conveyor operations.
5. Brackets and Mounting Hardware
Brackets and mounting hardware are used to secure the garland idler rollers to the conveyor frame. These components must be strong and properly aligned to maintain the stability and performance of the idler rollers. Proper installation and regular inspection of brackets and mounting hardware are essential to prevent misalignment and ensure reliable operation.
6. Lubrication Systems
Lubrication systems are critical for maintaining the smooth operation of garland belt conveyor idler rollers. These systems ensure that bearings and other moving parts are adequately lubricated, reducing friction and wear. Lubrication systems can be manual or automatic, with automatic systems providing consistent lubrication and reducing maintenance efforts.
7. Impact Bars and Frames
Impact bars and frames are used in load zones to absorb the impact of materials being loaded onto the conveyor belt. They help protect the garland idler rollers and the conveyor belt from damage caused by heavy or sharp materials. Impact bars are typically made from high-density polyethylene or rubber, providing a cushioning effect.
Advice on Maintaining an Inventory of Essential Parts for Quick Repairs and Replacements
Maintaining an inventory of essential parts for garland belt conveyor idler rollers is vital for minimizing downtime and ensuring continuous operation.
1. Identify Critical Components
Identify the critical components of your garland belt conveyor idler rollers that are most likely to require replacement or maintenance. These typically include rollers, bearings, seals, shafts, and lubrication systems.
2. Stock Spare Parts
Keep a stock of spare parts for the critical components identified. Having these parts readily available can significantly reduce the time required for repairs and replacements, minimizing downtime and maintaining productivity.
3. Monitor Inventory Levels
Regularly monitor inventory levels to ensure that you have an adequate supply of spare parts. Implement an inventory management system to track usage and reorder parts before they run out. This proactive approach helps prevent delays in repairs and replacements.
4. Supplier Relationships
Develop strong relationships with reliable suppliers to ensure quick and consistent access to spare parts. Establishing good communication and agreements with suppliers can help in obtaining parts promptly, especially during emergencies.
5. Maintenance Schedule
Implement a regular maintenance schedule for your garland belt conveyor idler rollers. Routine maintenance helps identify worn or damaged parts early, allowing for timely replacements. This practice not only extends the lifespan of the rollers but also reduces the likelihood of unexpected breakdowns.
6. Training and Documentation
Ensure that maintenance personnel are well-trained in the repair and replacement of garland belt conveyor idler rollers. Provide detailed documentation and manuals to guide them through the process. Proper training and documentation help maintain high standards of maintenance and repair work.
7. Emergency Preparedness
Prepare for emergencies by having a contingency plan in place. This plan should include procedures for quick identification and replacement of faulty parts, as well as contact information for suppliers and service providers.
Understanding the various parts and accessories specific to garland belt conveyor idler rollers is essential for maintaining their performance and longevity. By keeping an inventory of essential spare parts and implementing effective maintenance practices, businesses can ensure the reliable operation of their conveyor systems. Regular monitoring, proper training, and strong supplier relationships are key to minimizing downtime and maximizing productivity in industrial applications involving garland belt conveyor idler rollers.
Installation and Replacement of Garland Belt Conveyor Idler Roller
Proper installation and replacement of garland belt conveyor idler rollers are crucial for maintaining the efficiency and longevity of conveyor systems. This section provides a detailed step-by-step guide on how to replace garland idlers, along with maintenance tips to ensure their durability and optimal performance.
Step-by-Step Guide on Replacing Garland Belt Conveyor Idler Rollers
Step 1: Safety Precautions
Before beginning the replacement process, ensure all safety protocols are in place. Turn off and lock out the conveyor system to prevent accidental start-up. Wear appropriate personal protective equipment (PPE), including gloves, safety glasses, and protective clothing.
Step 2: Inspect the Conveyor System
Examine the conveyor system to identify the specific garland belt conveyor idler roller that needs replacement. Check for signs of wear, misalignment, or damage to the rollers and the conveyor belt.
Step 3: Remove the Old Idler Roller
Carefully remove the damaged or worn garland idler roller. Depending on the configuration, this may involve loosening bolts or clamps that secure the idler in place. Use appropriate tools to avoid damaging the conveyor structure or adjacent components.
Step 4: Prepare the New Idler Roller
Prepare the new garland belt conveyor idler roller for installation. Ensure it matches the specifications and configuration of the old roller. Check that the new idler is clean and free from defects.
Step 5: Install the New Idler Roller
Position the new garland idler roller in place. Secure it using bolts or clamps, ensuring it is properly aligned with the conveyor belt. Tighten all fasteners to the recommended torque specifications.
Step 6: Test the Installation
After installing the new idler roller, test the conveyor system to ensure proper operation. Run the conveyor at a slow speed to check for alignment issues, unusual noises, or vibrations. Make any necessary adjustments to ensure smooth operation.
Step 7: Resume Normal Operation
Once the new garland belt conveyor idler roller is installed and tested, resume normal conveyor operation. Monitor the system closely for the first few hours to ensure everything is functioning correctly.
Tips for Maintenance and Ensuring the Longevity of Garland Idlers
Maintaining garland belt conveyor idler rollers is essential for their long-term performance and reliability.
1. Regular Inspections
Conduct regular inspections of the garland belt conveyor idler rollers and the entire conveyor system. Look for signs of wear, misalignment, or damage. Early detection of issues can prevent more significant problems and reduce downtime.
2. Lubrication
Ensure that garland idlers are properly lubricated. Use the recommended lubricant for the specific type of idler roller. Proper lubrication reduces friction, minimizes wear, and extends the lifespan of the rollers.
3. Alignment Checks
Regularly check the alignment of the garland idlers and the conveyor belt. Misalignment can cause excessive wear on both the rollers and the belt. Use alignment tools and adjust the idlers as needed to maintain proper alignment.
4. Load Distribution
Monitor the load distribution on the conveyor system. Uneven loads can cause excessive stress on certain garland idlers, leading to premature wear. Ensure that materials are evenly distributed across the conveyor belt.
5. Replace Worn Components
Promptly replace any worn or damaged garland belt conveyor idler rollers. Delaying replacement can lead to more significant issues, including belt damage and system inefficiencies. Keep an inventory of essential spare parts to minimize downtime.
The proper installation and replacement of garland belt conveyor idler rollers are vital for maintaining the efficiency and longevity of conveyor systems. Following a systematic approach to replacement and adhering to maintenance best practices can significantly enhance the performance and durability of garland idlers. Regular inspections, proper lubrication, alignment checks, load distribution monitoring, and timely replacement of worn components are key to ensuring the optimal operation of your conveyor system. By investing in the maintenance and care of garland belt conveyor idler rollers, businesses can achieve reliable and efficient material handling, minimizing downtime and maximizing productivity.
Troubleshooting Common Issues with Garland Belt Conveyor Idler Roller
Garland belt conveyor idler rollers are essential components in conveyor systems, but like any mechanical part, they can encounter issues that affect performance. This section outlines common problems faced with garland idlers and provides troubleshooting tips to address these issues effectively. Additionally, it emphasizes the importance of regular inspection and maintenance to prevent and resolve problems.
Common Issues Faced with Garland Idlers and How to Troubleshoot Them
1. Misalignment
Issue: Misalignment of the garland belt conveyor idler roller can cause uneven wear on the rollers and the conveyor belt, leading to inefficiencies and potential damage.
Troubleshooting:
- Inspection: Regularly check the alignment of the idler rollers and the conveyor belt. Use alignment tools to ensure that the rollers are correctly positioned.
- Adjustment: Adjust the position of the idler rollers to ensure they are parallel to the conveyor belt. Tighten any loose bolts or clamps that may have caused the misalignment.
- Prevention: Install alignment devices or guides to maintain the proper alignment of the conveyor belt and idlers.
2. Excessive Noise and Vibration
Issue: Excessive noise and vibration from the garland belt conveyor idler roller can indicate issues such as misalignment, worn bearings, or inadequate lubrication.
Troubleshooting:
- Inspection: Identify the source of the noise and vibration. Check for loose or worn components, misaligned rollers, and insufficient lubrication.
- Lubrication: Ensure that the idler rollers are properly lubricated. Use the recommended lubricant and follow the manufacturer’s guidelines for lubrication intervals.
- Replacement: Replace worn or damaged bearings and other components that contribute to excessive noise and vibration.
3. Roller Wear and Damage
Issue: Wear and damage to the garland belt conveyor idler roller can lead to reduced performance and increased maintenance costs.
Troubleshooting:
- Inspection: Regularly inspect the rollers for signs of wear, such as flat spots, cracks, or excessive wear patterns.
- Replacement: Replace damaged or excessively worn rollers promptly to prevent further damage to the conveyor belt and system.
- Material Choice: Consider using rollers made from materials better suited to the operational environment, such as corrosion-resistant or wear-resistant materials.
4. Belt Slippage
Issue: Belt slippage occurs when the conveyor belt does not maintain proper tension and slips over the idler rollers, causing operational inefficiencies and potential damage.
Troubleshooting:
- Tension Adjustment: Check and adjust the tension of the conveyor belt to ensure it is within the recommended range. Use tensioning devices to maintain consistent tension.
- Alignment: Ensure that the garland belt conveyor idler rollers are properly aligned to prevent slippage.
- Surface Condition: Check the surface condition of the rollers and the belt. Clean any debris or buildup that may cause slippage.
5. Material Buildup
Issue: Material buildup on the garland belt conveyor idler roller can lead to uneven wear, increased friction, and reduced efficiency.
Troubleshooting:
- Cleaning: Regularly clean the idler rollers and the conveyor belt to remove any accumulated material. Use appropriate cleaning tools and techniques to avoid damaging the components.
- Scrapers and Brushes: Install scrapers and brushes on the conveyor system to continuously clean the belt and rollers during operation.
- Material Handling: Evaluate the material being transported and consider changes to handling procedures or material properties to reduce buildup.
Importance of Regular Inspection and Maintenance
Regular inspection and maintenance are critical to preventing and addressing common issues with garland belt conveyor idler rollers.
1. Early Detection of Issues
Regular inspections allow for the early detection of potential problems, such as misalignment, wear, and damage. Identifying issues early helps prevent more significant problems and reduces the risk of unexpected downtime.
2. Prolonging Equipment Life
Consistent maintenance practices, such as proper lubrication and timely replacement of worn components, help prolong the life of garland belt conveyor idler rollers. This reduces the frequency of replacements and lowers overall maintenance costs.
3. Improving Operational Efficiency
Well-maintained idler rollers ensure smooth and efficient conveyor operation. This improves material handling efficiency, reduces energy consumption, and enhances overall productivity.
4. Enhancing Safety
Regular maintenance helps ensure that all components are in good working condition, reducing the risk of accidents and injuries caused by equipment failure. Maintaining a safe working environment is essential for the well-being of employees.
5. Reducing Downtime
Preventive maintenance minimizes the likelihood of unexpected equipment failures, reducing downtime and ensuring continuous operation. This is particularly important in industries where conveyor systems are critical to production processes.
Troubleshooting common issues with garland belt conveyor idler rollers involves regular inspections, proper maintenance, and timely addressing of problems such as misalignment, noise, wear, belt slippage, and material buildup. By prioritizing these practices, businesses can ensure the efficient and reliable operation of their conveyor systems, extending the lifespan of their equipment and enhancing overall productivity. Regular maintenance not only prevents issues but also contributes to a safer and more efficient working environment.
FAQs About Garland Belt Conveyor Idler Roller
Conveyor idler rollers come in various sizes to accommodate different conveyor belt widths and operational requirements. The diameter of these rollers typically ranges from 4 inches to 8 inches, but can be customized to suit specific needs. Lengthwise, they are designed to fit the width of the conveyor belt, which can vary significantly depending on the application, from narrow belts used in material handling to wide belts used in mining and heavy industry. The selection of the appropriate roller size depends on factors such as the load capacity, speed of the conveyor, and the type of materials being transported. For precise sizing, it is recommended to consult with conveyor system manufacturers or suppliers who can provide rollers tailored to specific operational conditions.
Idlers and rollers are both essential components of conveyor systems, but they serve different purposes. An idler refers to the complete assembly that includes the roller, the frame, and sometimes additional components like bearings and seals. Idlers are designed to support the conveyor belt and the material being transported, ensuring smooth and efficient movement. Rollers, on the other hand, are the cylindrical components that rotate around a fixed axis within the idler assembly. They are the parts that come into direct contact with the conveyor belt, reducing friction and wear. Essentially, all idlers contain rollers, but not all rollers are part of an idler assembly. Understanding this distinction is important for selecting and maintaining conveyor system components effectively.
There are several types of idler roller conveyors, each designed for specific applications and operational conditions. The main types include:
Carrying Idlers: These support the loaded belt and are positioned on the carrying side of the conveyor. They come in various configurations such as flat, trough, and garland, each suited for different material types and conveyor designs.
Return Idlers: Located on the return side of the conveyor, these idlers support the empty belt as it returns to the loading point. They can be flat or V-shaped to maintain belt alignment.
Impact Idlers: Positioned at loading points, impact idlers are designed to absorb the impact of heavy, falling materials. They feature rollers with shock-absorbing materials like rubber or polyurethane.
Transition Idlers: Used at points where the conveyor belt changes direction or angle, transition idlers help in maintaining belt alignment and reducing stress.
Understanding the various types of idler roller conveyors is crucial for designing an efficient and reliable conveyor system tailored to specific material handling needs.
The primary function of idler rollers in a conveyor system is to support and guide the conveyor belt, ensuring smooth and efficient transportation of materials. Idler rollers reduce friction between the belt and the conveyor structure, which minimizes wear and tear on the belt and extends its lifespan. They also help maintain belt alignment, preventing misalignment issues that can cause operational inefficiencies and damage. Additionally, idler rollers play a crucial role in absorbing impacts and vibrations, especially in areas where heavy or bulky materials are loaded onto the conveyor. By distributing the load evenly and providing stable support, idler rollers contribute to the overall stability and efficiency of the conveyor system, ensuring continuous and reliable operation.
Last Updated on August 14, 2024 by Jordan Smith
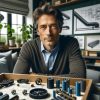
Jordan Smith, a seasoned professional with over 20 years of experience in the conveyor system industry. Jordan’s expertise lies in providing comprehensive solutions for conveyor rollers, belts, and accessories, catering to a wide range of industrial needs. From initial design and configuration to installation and meticulous troubleshooting, Jordan is adept at handling all aspects of conveyor system management. Whether you’re looking to upgrade your production line with efficient conveyor belts, require custom conveyor rollers for specific operations, or need expert advice on selecting the right conveyor accessories for your facility, Jordan is your reliable consultant. For any inquiries or assistance with conveyor system optimization, Jordan is available to share his wealth of knowledge and experience. Feel free to reach out at any time for professional guidance on all matters related to conveyor rollers, belts, and accessories.