Conveyor Drum Pulley: Types and Sizes
In conveyor systems, the conveyor drum pulley plays a crucial role by providing the driving force to move the conveyor belt. Conveyor drum pulley are the heart of any conveying system, ensuring maximum operational life and cost-efficiency. Located at both the head and tail ends of the conveyor, these pulleys are essential for the smooth operation and efficiency of the material handling process. Selecting the right conveyor drum pulley is vital for ensuring the optimal performance of the system. An appropriately chosen pulley not only enhances the efficiency of material transportation but also extends the lifespan of the conveyor belt. Understanding the various types and features of conveyor drum pulleys can help in making informed decisions for specific applications, leading to more efficient and reliable conveyor operations.
What are Conveyor Drum Pulleys
Conveyor drum pulleys are fundamental components in conveyor systems, contributing significantly to their efficiency and reliability. Understanding the different types and sizes of these pulleys, along with their applications, is essential for optimizing conveyor operations.
Types of Conveyor Drum Pulleys
Conveyor drum pulleys come in various types, each designed for specific functions within the conveyor system. The two primary types are head pulleys and tail pulleys.
Conveyor drum pulleys come in various types, each designed for specific applications and environments. Here are the most common types of conveyor drum pulleys:
1. Drive Pulley
- Description: This pulley is powered and drives the conveyor belt. It is typically located at the head of the conveyor.
- Features: It often has a rubber or ceramic lagging to increase friction between the pulley and the belt.
2. Head Pulley
The head pulley is a critical component located at the discharge end of the conveyor system. It is responsible for driving the conveyor belt and moving the material along the system. The head pulley is typically larger in diameter compared to other pulleys and is powered by an external motor. This pulley provides the necessary force to keep the belt in motion, ensuring continuous material flow. The head pulley’s efficiency and performance directly impact the overall productivity of the conveyor system.
3. Tail Pulley
The tail pulley is situated at the loading end of the conveyor system. Unlike the head pulley, the tail pulley does not drive the belt but plays a crucial role in maintaining belt tension and redirecting the belt back to the head pulley. Proper tensioning is essential to prevent slippage and ensure the smooth operation of the conveyor belt. The tail pulley’s function is vital for reducing wear and tear on the belt and other components, thereby extending the lifespan of the conveyor system.
- Description: Located at the opposite end of the conveyor from the drive pulley, the tail pulley helps in belt tension and tracking.
- Features: It is usually an idler pulley, meaning it is not powered and rotates freely.
4. Snub Pulley
- Description: Positioned close to the drive pulley, the snub pulley increases the belt’s contact with the drive pulley to improve traction and prevent slipping.
- Features: It is used to change the direction of the belt, increasing the wrap angle around the drive pulley.
5. Take-Up Pulley
- Description: This pulley is mounted on a tensioning device to maintain the correct belt tension. It can be adjusted to compensate for belt stretch and wear.
- Features: Typically found in conveyor systems where there is a need for belt length adjustment.
6. Bend Pulley
- Description: Used to change the direction of the belt in the conveyor system. It is often found in applications where the conveyor path needs to be redirected.
- Features: It may or may not be driven and can also help in increasing the wrap angle on the drive pulley.
7. Wing Pulley
- Description: Also known as self-cleaning pulleys, wing pulleys have a series of fins or wings that allow material to pass through the pulley, preventing build-up and reducing wear.
- Features: Often used in applications where material build-up on the belt is a concern, such as in bulk material handling.
- Description: A pulley with a layer of material (rubber, ceramic, etc.) applied to its surface to increase grip and reduce slippage.
- Features: Lagging improves traction, reduces belt wear, and can help to extend the life of the conveyor system.
9. Spiral Pulley
- Description: Designed with a spiral groove pattern on its surface, this pulley is used to improve belt tracking and reduce material build-up.
- Features: The spiral design helps to center the belt on the pulley and can also enhance self-cleaning properties.
10. Dead Shaft Pulley
- Description: A pulley with a stationary shaft around which the pulley rotates. The shaft is fixed to the conveyor frame, while the pulley itself is free to rotate.
- Features: Often used in applications requiring precise pulley alignment and stability.
11. Live Shaft Pulley
- Description: Unlike the dead shaft pulley, the live shaft pulley has a rotating shaft that moves with the pulley.
- Features: Typically used in more heavy-duty applications where robust power transmission is needed.
These different types of pulleys are selected based on the specific needs of the conveyor system, such as the type of material being transported, the environment in which the conveyor operates, and the desired speed and load capacity.
Conveyor Drum Pulley Sizes
Conveyor drum pulleys come in various sizes, each suited for different applications. The size of the pulley affects the conveyor system’s performance, including the belt speed, load capacity, and overall efficiency. Here, we discuss the importance of selecting the right size and provide a summary of common sizes and their applications.
How to Select the Right Conveyor Drum Pulley Size
Selecting the appropriate conveyor drum pulley size is crucial for ensuring optimal performance and efficiency. Here are key considerations when choosing the right size:
- Load Capacity: Determine the maximum load the conveyor system will carry. Larger pulleys are typically required for higher load capacities to provide the necessary strength and support.
- Belt Width: Match the pulley diameter with the width of the conveyor belt. Proper alignment ensures smooth operation and prevents belt slippage.
- Belt Speed: Consider the desired belt speed. Larger pulleys can help maintain higher speeds without causing excessive wear on the belt.
- Application Type: Identify the specific application requirements. For example, mining and bulk material handling may require larger and more robust pulleys to withstand harsh conditions.
- Space Constraints: Evaluate the available space within the conveyor system. Ensure the selected pulley size fits within the system’s design parameters.
- Material Type: Consider the type of material being transported. Heavier and abrasive materials may necessitate larger, more durable pulleys.
Understanding the various types and sizes of conveyor drum pulleys is essential for selecting the right components for your conveyor system. The head pulley drives the conveyor belt and is crucial for system efficiency, while the tail pulley maintains belt tension and alignment. Choosing the appropriate pulley size depends on factors such as load capacity, belt width, belt speed, application type, space constraints, and material type. By carefully considering these factors, you can ensure the optimal performance and longevity of your conveyor system, leading to more efficient and reliable material handling operations.

Features of Conveyor Drum Pulleys
Conveyor drum pulleys are integral components of conveyor systems, offering various features that enhance their performance and reliability. Understanding these features, including technical drawings and the role of drive pulleys, is essential for optimizing conveyor system operations.
Advantages of Conveyor Drum Pulleys
Conveyor drum pulleys offer several advantages in conveyor systems, making them a critical component in various industries. Here are some of the key advantages:
These advantages make conveyor drum pulleys an essential component for ensuring the efficiency, reliability, and safety of conveyor systems across a wide range of industries.
Drum Pulley Drawing
Technical drawings of drum pulleys are detailed schematics that provide precise measurements, materials, and specifications necessary for manufacturing and installation. These drawings are crucial for ensuring that the pulleys meet the required standards and function correctly within the conveyor system.
Explanation of Drum Pulley Technical Drawings
- Dimensional Details: Technical drawings include exact dimensions of the drum pulley, such as diameter, width, and shaft size. These details ensure the pulley fits perfectly within the conveyor system and operates efficiently.
- Material Specifications: The drawings specify the materials used in the construction of the drum pulley, such as steel or aluminum. This information is essential for selecting the right material based on the application’s requirements, such as load capacity and environmental conditions.
- Tolerances: Drawings indicate the permissible variations in dimensions and angles, ensuring precision in manufacturing. Tolerances are critical for maintaining the pulley’s structural integrity and performance.
- Assembly Instructions: Detailed instructions on how to assemble the pulley with other components, including bolts, bearings, and shafts, are included. Proper assembly is vital for the pulley’s smooth operation and longevity.
- Safety Standards: Technical drawings incorporate safety standards and guidelines, ensuring the pulley’s design complies with industry regulations. Adhering to safety standards helps prevent accidents and equipment failures.
Importance of Accurate Drawings in Manufacturing and Installation Processes
Accurate technical drawings are indispensable in the manufacturing and installation processes for several reasons:
- Precision Manufacturing: Accurate drawings ensure that the drum pulleys are manufactured to exact specifications, reducing the risk of defects and improving performance.
- Efficient Installation: Detailed drawings facilitate easy and precise installation, minimizing downtime and ensuring that the conveyor system operates smoothly from the start.
- Cost-Effectiveness: By providing clear specifications, accurate drawings help avoid costly errors and rework, saving time and resources in the long run.
- Quality Assurance: Drawings serve as a reference for quality control, ensuring that each pulley meets the required standards before it is installed.
- Maintenance and Repairs: Technical drawings are useful for maintenance and repairs, providing a clear guide for replacing worn or damaged components.
Drive Pulley for Conveyor Belt
Drive pulleys play a crucial role in transmitting motion power to conveyor belts, ensuring the efficient movement of materials along the conveyor system.
Role of Drive Pulleys in Transmitting Motion Power to Conveyor Belts
- Power Transmission: Drive pulleys transfer power from the motor to the conveyor belt, propelling it forward. This power transmission is essential for the continuous movement of materials.
- Speed Regulation: Drive pulleys help regulate the speed of the conveyor belt, ensuring that materials are transported at the desired pace. This regulation is crucial for maintaining consistent production rates.
- Load Handling: Drive pulleys are designed to handle varying load capacities, providing the necessary force to move heavy materials efficiently.
- Direction Control: Drive pulleys can control the direction of the conveyor belt, enabling flexible material handling processes. This control is vital for complex conveyor system layouts.
- Energy Efficiency: High-quality drive pulleys are designed to operate with minimal energy consumption, reducing operational costs and enhancing overall system efficiency.
Comparison Between Drive Pulleys and Non-Drive Pulleys in Conveyor Systems
Understanding the features of conveyor pulley drums, including their technical drawings and the role of drive pulleys, is essential for optimizing conveyor system performance. Accurate technical drawings ensure precision in manufacturing and installation, while drive pulleys play a vital role in transmitting power and regulating belt movement. By comprehending these aspects, you can enhance the efficiency and reliability of your conveyor system, leading to more effective material handling operations.
Conveyor Drum Pulley:Drum & Wing Pulleys
Conveyor drum pulleys come in different types, with the most common being drum pulleys and wing pulleys. Each type serves specific functions in a conveyor system. Here’s a closer look at both:
Drum Pulleys
Description:
- Drum pulleys are the most common type of conveyor pulley. They are typically cylindrical in shape and used to transmit the drive force from the motor to the conveyor belt.
Applications:
- Drum pulleys are widely used in bulk material handling applications, such as mining, quarrying, and aggregate processing.
Key Features:
- Cylindrical Shape: Provides even contact with the conveyor belt, ensuring smooth operation.
- Lagging Options: Drum pulleys can be equipped with rubber or ceramic lagging to increase friction and reduce slippage.
- Versatility: They can be used as drive pulleys, tail pulleys, or snub pulleys, depending on the conveyor system’s design.
Advantages:
- Smooth Operation: Their cylindrical design allows for a consistent driving surface, reducing belt wear.
- Customization: Drum pulleys can be customized in diameter, length, and lagging material to suit specific applications.
- Durability: Made from materials like steel, drum pulleys are designed to withstand heavy loads and harsh conditions.
Wing Pulleys
Description:
- Wing pulleys are a variation of drum pulleys with a series of wings or fins extending from the center to the edges. These wings are designed to shed material that could build up on the pulley or the belt.
Applications:
- Wing pulleys are commonly used in environments where material build-up on the pulley could be a problem, such as in wet or sticky conditions, or where there’s a lot of debris, like in recycling or agricultural applications.
Key Features:
- Winged Design: The fins or wings on the pulley create gaps that allow material to escape, preventing build-up.
- Self-Cleaning: The open design of the pulley reduces maintenance by minimizing material build-up.
- Material Handling: Ideal for applications where the conveyor system handles sticky, wet, or abrasive materials.
Advantages:
- Self-Cleaning: Wing pulleys are designed to clean themselves by allowing material to escape, reducing the risk of belt slippage and maintaining efficient operation.
- Reduced Wear: The self-cleaning action helps to prevent the accumulation of material, which can lead to wear and tear on both the belt and the pulley.
- Versatility: Wing pulleys can be used in both drive and tail positions, though they are most commonly used in tail positions where material build-up is a concern.
Comparison of Drum & Wing Pulleys
Choosing Between Drum and Wing Pulleys
- Drum Pulleys are ideal for general conveyor applications where material build-up is not a significant concern and where smooth, continuous contact with the belt is needed.
- Wing Pulleys are better suited for environments where material build-up could cause operational issues, such as in wet, sticky, or abrasive environments. Their self-cleaning design helps keep the conveyor running smoothly with less maintenance.
By understanding the differences between these two types of pulleys, you can select the right one to optimize the performance and efficiency of your conveyor system.
Selecting the Right Conveyor Drum Pulley
Choosing the right conveyor drum pulley is crucial for ensuring the efficiency and longevity of your conveyor system. Proper selection involves understanding when a pulley needs replacement and selecting a reliable manufacturer.
Conveyor Drum Pulley Replacement
Knowing when to replace a drum pulley conveyor is essential to maintain the smooth operation of your conveyor system.
- Excessive Wear and Tear: If the pulley surface shows significant wear, it can lead to belt slippage and reduced efficiency.
- Cracks or Fractures: Visible cracks or fractures in the pulley body can compromise its structural integrity, posing a safety risk.
- Unusual Noises: Unusual sounds such as grinding or squealing can indicate internal damage or misalignment.
- Vibration: Excessive vibration during operation suggests imbalance or wear in the pulley bearings.
- Belt Misalignment: Persistent belt misalignment issues, despite proper tensioning, can be a sign of pulley wear or damage.
Step-by-Step Guide on Replacing a Conveyor Drum Pulley
Replacing a conveyor drum pulley involves several steps to ensure a smooth and efficient process:
- Shut Down the Conveyor System: Ensure the conveyor system is completely powered off and locked out to prevent accidental operation during replacement.
- Remove the Belt: Loosen the belt tension and remove the conveyor belt from the pulley to access the drum pulley.
- Disconnect the Pulley: Detach the pulley from its mounting by removing the securing bolts or clamps. Ensure all connections are carefully handled to prevent damage.
- Inspect and Clean: Before installing the new pulley, inspect the surrounding components for wear or damage and clean the area to ensure a proper fit.
- Install the New Pulley: Position the new pulley in place, aligning it correctly with the conveyor system. Secure it using the appropriate bolts or clamps.
- Reassemble and Tension the Belt: Reinstall the conveyor belt and adjust the tension according to the manufacturer’s specifications to ensure proper alignment and operation.
- Test the System: Power on the conveyor system and run it at a low speed to check for proper installation and operation. Make any necessary adjustments to ensure smooth performance.
How to Choose the Right Conveyor Drum Pulley
Choosing the right conveyor drum pulley is crucial for the efficiency, reliability, and longevity of your conveyor system. Here are the key factors to consider when selecting the appropriate pulley:
Steps to Choose the Right Pulley
- Assess Your Needs: Start by analyzing the material handling requirements, including load, speed, and environment.
- Consult Specifications: Match the pulley specifications (diameter, material, lagging) to the conveyor belt and application.
- Consider the System Layout: Ensure the pulley fits within the conveyor system’s design, including space constraints and alignment needs.
- Evaluate Long-Term Costs: Factor in the potential maintenance costs and lifespan of the pulley versus the initial purchase price.
- Seek Expert Advice: If unsure, consult with a conveyor system specialist to ensure the selected pulley meets all operational requirements.
By carefully considering these factors, you can choose a conveyor drum pulley that optimizes the performance and efficiency of your conveyor system, minimizing downtime and extending the life of your equipment.
Choosing Manufacturers
Selecting a reliable manufacturer for your conveyor drum pulley is crucial for ensuring the quality and durability of the component.
- Reputation and Experience: Look for manufacturers with a proven track record and extensive experience in producing conveyor drum pulleys. Positive reviews and case studies can indicate reliability.
- Quality Standards: Ensure the manufacturer adheres to industry quality standards and certifications, such as ISO 9001, to guarantee high-quality production processes.
- Customization Options: A good manufacturer should offer customization options to tailor the drum pulleys to your specific requirements, including size, material, and design features.
- Technical Support: Reliable manufacturers provide comprehensive technical support and after-sales services, including installation guidance and troubleshooting assistance.
- Material and Construction: Consider the materials and construction methods used by the manufacturer. High-quality materials and robust construction ensure the pulley’s durability and performance.
How Quality Manufacturing Impacts the Efficiency and Longevity of Drum Pulleys
Quality manufacturing plays a critical role in the efficiency and longevity of drum pulley conveyors. Here’s how:
- Durability: High-quality materials and precise manufacturing processes result in durable pulleys that withstand wear and tear, reducing the frequency of replacements and downtime.
- Performance: Well-manufactured pulleys ensure smooth and efficient belt movement, minimizing the risk of slippage and misalignment.
- Safety: Quality construction reduces the likelihood of pulley failure, enhancing the safety of the conveyor system and preventing accidents.
- Cost-Effectiveness: Investing in high-quality pulleys can lead to long-term cost savings by reducing maintenance costs and extending the lifespan of the conveyor system.
- Energy Efficiency: Efficiently manufactured pulleys reduce energy consumption by minimizing friction and improving the overall performance of the conveyor system.
Selecting the right conveyor drum pulley involves recognizing the signs of wear, understanding the replacement process, and choosing a reputable manufacturer. By focusing on these aspects, you can ensure the optimal performance and longevity of your conveyor system, leading to more efficient and reliable material handling operations.

FAQs About Conveyor Drum Pulley
A drum pulley is a cylindrical component used in conveyor systems to drive and support the conveyor belt. These pulleys are typically made from high-strength materials like steel or aluminum to withstand the mechanical stresses involved in conveying materials. Drum pulleys can be found at both the head (driving) end and the tail (non-driving) end of a conveyor system. The primary function of a drum pulley is to transmit the rotational power from the motor to the conveyor belt, facilitating the movement of materials along the conveyor. They are crucial for maintaining the belt’s tension and alignment, ensuring smooth and efficient operation.
A pulley on a conveyor is a mechanical device used to guide and drive the conveyor belt. Pulleys come in various forms, such as drum pulleys, wing pulleys, and spiral pulleys, each serving different purposes within the conveyor system. The main roles of these pulleys include transmitting power to the belt, maintaining proper tension, and redirecting the belt as needed. Pulleys are essential for the continuous and efficient movement of materials along the conveyor. Proper selection and maintenance of conveyor pulleys are vital for ensuring the system’s longevity and performance.
The primary difference between a head pulley and a tail pulley lies in their location and function within the conveyor system. The head pulley is located at the discharge end of the conveyor and is responsible for driving the conveyor belt. It is powered by a motor, providing the necessary force to move the belt and transport materials along the conveyor. In contrast, the tail pulley is situated at the loading end of the conveyor. Its main function is to redirect the belt back towards the head pulley and maintain proper tension. While the head pulley propels the belt, the tail pulley ensures the belt’s smooth return, preventing slippage and ensuring consistent belt alignment.
A conveyor drum, often referred to as a drum pulley, is a key component of a conveyor system. It is a cylindrical device that helps drive the conveyor belt and support its movement. Conveyor drums are typically placed at the head and tail ends of the conveyor, playing a critical role in the system’s operation. At the head end, the conveyor drum is connected to a motor that drives the belt, facilitating the transportation of materials. At the tail end, the conveyor drum helps in maintaining the belt tension and guides it back towards the head drum. The design and construction of conveyor drums are crucial for ensuring the efficiency, reliability, and longevity of the conveyor system.
Pulleys for conveyor belt drives are essential components that provide the necessary traction to move the belt. The primary types of pulleys used include the drive pulley, which is connected to a motor and drives the belt, and the tail pulley, which is located at the opposite end to provide tension and alignment. Additional types like snub pulleys and take-up pulleys help improve belt traction and maintain proper tension. Drive pulleys are often equipped with lagging (rubber or ceramic) to increase friction and reduce slippage. These pulleys are critical in various industries, such as mining, manufacturing, and logistics, ensuring the smooth and efficient operation of conveyor systems by transferring the motor’s power to move materials along the belt.
A pulley works on a conveyor belt by transmitting mechanical power and motion to move the belt. The drive pulley, which is powered by a motor, rotates, creating friction between the pulley surface and the conveyor belt. This frictional force propels the belt forward, carrying materials along its surface. Idler pulleys, like the tail and snub pulleys, do not drive the belt but help guide it, maintain tension, and increase the belt’s wrap angle around the drive pulley, improving traction and preventing slippage. The tension and alignment are managed by the take-up pulley, ensuring that the belt runs smoothly without sagging or misalignment. Together, these pulleys enable the conveyor system to transport materials efficiently across various distances and elevations.
Last Updated on August 9, 2024 by Jordan Smith
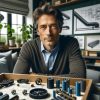
Jordan Smith, a seasoned professional with over 20 years of experience in the conveyor system industry. Jordan’s expertise lies in providing comprehensive solutions for conveyor rollers, belts, and accessories, catering to a wide range of industrial needs. From initial design and configuration to installation and meticulous troubleshooting, Jordan is adept at handling all aspects of conveyor system management. Whether you’re looking to upgrade your production line with efficient conveyor belts, require custom conveyor rollers for specific operations, or need expert advice on selecting the right conveyor accessories for your facility, Jordan is your reliable consultant. For any inquiries or assistance with conveyor system optimization, Jordan is available to share his wealth of knowledge and experience. Feel free to reach out at any time for professional guidance on all matters related to conveyor rollers, belts, and accessories.