Common Belt Conveyor Problems Solutions
Conveyor belts play a critical role in industrial settings, ensuring the efficient movement of materials across various stages of production. Despite their importance, conveyor belts are prone to problems that can disrupt operations and lead to costly downtime. Common belt conveyor problems include misalignment, belt slippage, and material spillage, which are often caused by improper installation, lack of maintenance, and wear and tear over time. This blog aims to provide comprehensive solutions to these conveyor belt problems through a detailed, downloadable PDF guide. By understanding and addressing these issues, you can maintain the efficiency and reliability of your conveyor systems, ultimately saving time and resources.
Common Belt Conveyor Problems
Belt conveyors are widely used in various industries, including mining, due to their efficiency and reliability in transporting materials. However, they can encounter several common problems that can affect their performance and lead to downtime. Common belt conveyor problems including belt mistracking、slippage、wear and tear、misalignment、tension issues ,stalling…Here are some of the most common belt conveyor problems:
Belt Mistracking
- Description: The conveyor belt deviates from its intended path, causing it to run off-center.
- Causes: Misalignment of conveyor components, uneven loading, or improper belt tension.
- Solutions: Regular inspection and maintenance, proper alignment of pulleys and idlers, and installing tracking devices.
Belt Slippage
- Description: The belt slips on the drive pulley, reducing its ability to move materials effectively.
- Causes: Insufficient tension, worn drive pulley, or contamination (e.g., oil or water) on the belt.
- Solutions: Adjusting belt tension, replacing or reconditioning the drive pulley, and ensuring the belt is clean and dry.
Belt Wear and Tear
- Description: Physical damage to the belt, such as fraying, cracking, or tearing.
- Causes: Abrasive materials, improper loading, or sharp objects on the belt.
- Solutions: Using higher quality, more durable belts, ensuring proper loading techniques, and removing debris from the belt.
Material Spillage
- Description: Material falling off the sides of the conveyor belt.
- Causes: Overloading, belt misalignment, or inadequate skirting and sealing.
- Solutions: Reducing load sizes, ensuring proper belt alignment, and installing or improving skirting and sealing systems.
Belt Misalignment
- Description: Misalignment of the belt can cause damage to the belt and conveyor structure.
- Causes: Poor installation, structural issues, or irregular maintenance.
- Solutions: Regular inspections, proper installation techniques, and structural adjustments as needed.
Belt Conveyor Belt Tension Issues
- Description: Incorrect belt tension can lead to various problems, including mistracking and slippage.
- Causes: Improper installation, lack of maintenance, or environmental factors.
- Solutions: Regularly checking and adjusting belt tension, using automatic tensioning systems.
Pulley Problems
- Description: Issues with pulleys, such as misalignment, wear, or damage.
- Causes: Poor installation, lack of maintenance, or material build-up.
- Solutions: Regular inspection and maintenance, proper pulley alignment, and cleaning pulleys regularly.
Idler and Roller Issues
- Description: Problems with idlers and rollers, such as seizing, misalignment, or wear.
- Causes: Lack of lubrication, improper installation, or heavy loads.
- Solutions: Regular lubrication, ensuring proper installation, and replacing worn components.
Conveyor Belt Stalling
- Description: The conveyor belt stops moving, which can halt the entire production line.
- Causes: Overloading, motor issues, or drive system problems.
- Solutions: Avoiding overloading, regular maintenance of motors and drive systems, and using appropriate drive components.
Noise and Vibration
- Description: Excessive noise and vibration from the conveyor system.
- Causes: Misalignment, worn components, or improper installation.
- Solutions: Regular inspections, replacing worn parts, and ensuring proper installation and alignment.
By understanding and addressing these common belt conveyor problems, operators can enhance the reliability and efficiency of their conveyor systems, reducing downtime and maintenance costs.
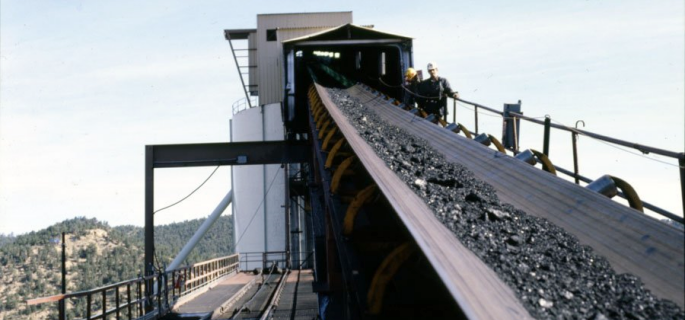
Types of Conveyor Belt Damage
Conveyor belts are essential components in industrial settings, providing a reliable method for transporting materials from one point to another. However, these systems are not immune to issues, and understanding belt conveyor problems is crucial for maintaining operational efficiency and minimizing downtime.
Conveyor belt damage can take various forms, each of which can severely impact the performance and lifespan of the belt.
- Cuts and Gouges: These are usually caused by sharp or heavy objects falling onto the belt, creating deep incisions that weaken the belt structure.
- Abrasions: Continuous friction between the belt and other surfaces or materials can wear down the belt’s surface, leading to thinning and eventual breakage.
- Punctures: Pointed objects can penetrate the belt, causing holes that may expand under stress, leading to further damage.
- Edge Damage: Misalignment of the belt or improper tracking can cause the belt edges to fray or wear unevenly, affecting the belt’s integrity.
- Delamination: Over time, the layers of the belt can start to separate due to constant flexing and stress, leading to a breakdown in the belt’s structure.
Several factors contribute to the wear, tear, and overall damage of conveyor belts. Here are five critical factors:
- Material Characteristics: Hard, abrasive, or heavy materials can accelerate the wear and tear on conveyor belts, reducing their lifespan.
- Operational Environment: Harsh conditions, such as extreme temperatures, humidity, or exposure to chemicals, can degrade belt materials more quickly.
- Loading Practices: Overloading the conveyor belt or uneven distribution of materials can cause excessive stress and wear on specific areas of the belt.
- Maintenance Practices: Lack of regular maintenance, such as cleaning and inspection, can allow minor issues to develop into significant problems.
- Belt Quality: Low-quality or improperly specified belts may not withstand the operational demands, leading to premature failure.
Causes of Conveyor Belt Failure
Understanding the causes of belt conveyor problems is essential for preventing failures. Here are the main causes that lead to conveyor belt failure:
- Misalignment: When the conveyor belt is not correctly aligned, it can cause uneven wear, edge damage, and increased tension, leading to belt failure.
- Slippage: Belt slippage occurs when the drive pulley fails to grip the belt effectively, often due to insufficient tension or contamination on the belt or pulleys.
- Blockages: Foreign objects or material build-up on the conveyor system can obstruct the belt’s movement, causing strain and potential damage.
- Tension Issues: Incorrect tensioning, whether too tight or too loose, can lead to belt slippage, excessive wear, or even breakage.
- Poor Installation: Incorrect installation procedures, such as improper splicing or inadequate pulley alignment, can cause immediate or long-term belt issues.
Identifying early signs of belt degradation and failure is vital for timely intervention and prevention. Here are some indicators to watch for:
- Visible Damage: Regular inspections can reveal visible signs of damage, such as cuts, abrasions, or punctures, that need immediate attention.
- Abnormal Noises: Unusual sounds, such as squeaking or grinding, can indicate misalignment, slippage, or other underlying issues.
- Irregular Movement: If the belt moves unevenly or jerks, it could be a sign of misalignment or tension problems.
- Material Spillage: Excessive spillage along the conveyor path can signal belt misalignment, damage, or blockages.
- Heat Build-up: Overheating of the belt or pulleys can indicate excessive friction or slippage, leading to potential failure.
Understanding and addressing these belt conveyor problems through regular maintenance, proper installation, and timely interventions can significantly enhance the reliability and efficiency of your conveyor systems. For a comprehensive guide on diagnosing and solving these issues, download our detailed PDF guide, which offers in-depth insights and practical solutions.
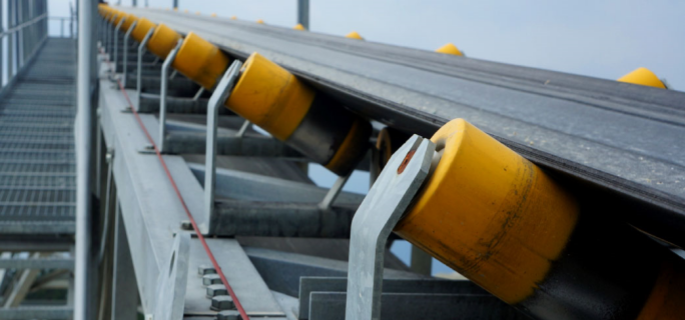
Belt Conveyor Problems Diagnosis
Diagnosing belt conveyor problems is essential for maintaining efficient operations and preventing costly downtime. By understanding the common issues that arise in both used and industrial belt conveyors, you can take proactive steps to address them and ensure your conveyor systems operate smoothly.
Used Belt Conveyor Problems
Used belt conveyors, while cost-effective, often come with their own set of problems that can impact performance and longevity. Here are some common issues that arise in used belt conveyors:
- Wear and Tear: Used conveyors often exhibit signs of wear and tear, such as surface abrasions, cuts, and punctures. These damages can compromise the belt’s structural integrity and lead to failure if not addressed promptly.
- Misalignment: Over time, the alignment of the conveyor belt can shift, causing the belt to track improperly. This misalignment can result in uneven wear, increased friction, and potential damage to the belt edges.
- Stretched Belts: Prolonged use can cause the belt to stretch, leading to slippage and reduced tension. This stretching affects the belt’s ability to carry loads efficiently and can cause operational issues.
- Belt Splice Deterioration: The splices in a used conveyor belt can deteriorate over time, especially if not properly maintained. Weak or damaged splices can lead to belt breakage and significant downtime.
- Contamination: Used belts are often contaminated with debris, oils, and other substances that can affect performance. Contaminants can cause the belt to slip, wear faster, and even damage the conveyor components.
To assess the condition of a used conveyor belt effectively, consider the following tips:
- Visual Inspection: Conduct a thorough visual inspection to identify any visible signs of damage, such as cuts, abrasions, or frayed edges.
- Check Alignment: Ensure the belt is properly aligned by inspecting the tracking and adjusting as necessary to prevent uneven wear and potential damage.
- Test Tension: Verify that the belt maintains the correct tension. If the belt is too loose or too tight, adjust the tension to ensure optimal performance.
- Inspect Splices: Examine the belt splices for any signs of wear or deterioration. Ensure that all splices are secure and properly aligned to prevent breakage.
- Clean and Lubricate: Clean the belt thoroughly to remove any contaminants and apply appropriate lubrication to reduce friction and wear.
Industrial Belt Conveyor Problems
Industrial applications of conveyor belts present unique challenges that can lead to specific problems. Understanding these challenges is crucial for effective problem diagnosis and maintenance. Here are some common issues faced in industrial belt conveyor systems:
- Heavy Load Handling: Industrial conveyors often handle heavy loads, which can exert significant stress on the belt and other components. Over time, this stress can lead to belt stretching, misalignment, and potential failure.
- High Operating Speeds: Industrial conveyor systems frequently operate at high speeds to maintain production efficiency. High speeds can increase the risk of belt slippage, misalignment, and wear.
- Harsh Environments: Many industrial settings involve harsh environmental conditions, such as extreme temperatures, humidity, and exposure to chemicals. These conditions can degrade belt materials and affect performance.
- Continuous Operation: Industrial conveyors often run continuously for extended periods, leading to increased wear and tear. Continuous operation requires regular maintenance to prevent unexpected breakdowns.
- Complex Configurations: Industrial conveyor systems can have complex configurations, including multiple belts, pulleys, and drive systems. These configurations can complicate troubleshooting and maintenance efforts.
Analyzing scenarios leading to belt malfunctions in an industrial context involves understanding the interplay of various factors:
- Load Distribution: Uneven load distribution can cause certain sections of the belt to experience excessive stress, leading to premature wear and potential failure.
- Component Wear: Continuous operation can cause wear on conveyor components, such as pulleys, idlers, and rollers. Worn components can affect belt alignment and performance.
- Thermal Expansion: In environments with significant temperature fluctuations, thermal expansion and contraction of the belt can cause misalignment and tension issues.
- Contamination: Industrial settings often involve exposure to dust, debris, and other contaminants. These contaminants can accumulate on the belt and components, causing friction, wear, and potential malfunctions.
- Maintenance Practices: Inadequate or irregular maintenance can exacerbate existing problems and lead to more severe issues over time. Regular inspections, cleaning, and lubrication are essential to maintaining conveyor performance.
By addressing these belt conveyor problems through thorough diagnosis and proactive maintenance, you can enhance the reliability and efficiency of your industrial conveyor systems. For a detailed guide on troubleshooting and maintaining conveyor belts, download our comprehensive PDF guide, which offers in-depth insights and practical solutions.
How to Prevent Belt Conveyor Problems
Preventing belt conveyor problems requires a combination of regular maintenance, proper installation, and operational best practices. Here are some detailed strategies to prevent common belt conveyor issues:
1. Regular Inspections and Maintenance
- Routine Inspections: Conduct regular visual and operational inspections of the conveyor system to identify wear, misalignment, or other potential issues early.
- Scheduled Maintenance: Establish a maintenance schedule for checking and servicing all components, including belts, pulleys, idlers, and rollers.
- Lubrication: Ensure all moving parts, such as bearings and rollers, are properly lubricated to reduce friction and wear.
2. Proper Installation
- Alignment: Ensure that all conveyor components are correctly aligned during installation. Misalignment can cause mistracking and increased wear.
- Tensioning: Properly tension the conveyor belt to avoid slippage and ensure smooth operation. Use automatic tensioning devices if possible.
- Quality Materials: Use high-quality belts and components that are appropriate for the specific application and material being transported.
3. Operational Best Practices
- Load Management: Avoid overloading the conveyor system. Ensure the load is evenly distributed to prevent belt slippage and excessive wear.
- Speed Control: Operate the conveyor at the recommended speed to avoid excessive stress on the belt and components.
- Material Handling: Ensure that materials are loaded onto the belt in a way that minimizes impact and avoids spillage. Use chutes and skirts to guide materials onto the belt.
4. Belt Tracking and Alignment
- Tracking Devices: Install belt tracking devices to keep the belt centered on the pulleys. Regularly check and adjust these devices as needed.
- Adjustable Idlers: Use adjustable idlers to help maintain proper belt alignment. Regularly inspect and adjust them to prevent mistracking.
5. Environmental Control
- Clean Environment: Keep the conveyor system and surrounding area clean. Remove debris and spilled material that can cause belt wear or obstruct moving parts.
- Dust Control: Implement dust control measures, such as dust suppression systems or enclosures, to reduce abrasive wear on the belt and components.
6. Skirting and Sealing
- Proper Skirting: Install and maintain proper skirting along the sides of the conveyor to prevent material spillage and reduce belt wear.
- Sealing Systems: Use sealing systems at transfer points to contain materials and prevent spillage.
7. Regular Component Checks
- Idlers and Rollers: Regularly inspect idlers and rollers for wear and proper operation. Replace any damaged or worn components promptly.
- Pulleys: Check pulleys for alignment and wear. Ensure they are properly maintained and replace them as necessary.
8. Training and Safety
- Employee Training: Provide training for all employees who operate or maintain the conveyor system. Ensure they understand the importance of proper operation and maintenance procedures.
- Safety Protocols: Implement and enforce safety protocols to prevent accidents and injuries. This includes proper lockout/tagout procedures during maintenance.
9. Monitoring Systems
- Condition Monitoring: Use condition monitoring systems to track the performance and health of the conveyor system. Sensors can detect issues such as temperature changes, misalignment, and abnormal vibrations.
- Predictive Maintenance: Implement predictive maintenance strategies using data from monitoring systems to address potential problems before they cause downtime.
10. Documentation and Records
- Maintenance Records: Keep detailed records of all maintenance activities, inspections, and repairs. This helps track the system’s history and identify recurring issues.
- Operational Logs: Maintain logs of conveyor operation, including load levels, speeds, and any incidents. This information can help diagnose problems and improve operational practices.
By following these strategies, operators can significantly reduce the likelihood of belt conveyor problems, ensuring a more efficient, reliable, and long-lasting conveyor system.
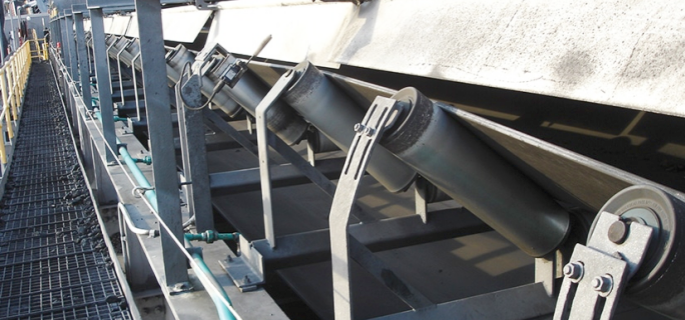
Troubleshooting Belt Conveyor Problems
Effective troubleshooting of belt conveyor problems is crucial for maintaining efficient operations and minimizing downtime. This section provides a detailed guide on diagnosing and resolving common issues, as well as highlights the availability of a comprehensive PDF resource for in-depth insights and solutions.
Conveyor Troubleshooting PDF
For those facing belt conveyor problems, a comprehensive troubleshooting guide in PDF format is an invaluable resource. This guide offers detailed instructions on diagnosing and resolving various issues that can arise in conveyor systems.
- Identify the Problem: The first step in troubleshooting is to accurately identify the issue. This involves a thorough inspection of the conveyor system to look for visible signs of damage or malfunction, such as misalignment, wear, and tear, or unusual noises.
- Check Alignment: Misalignment is a common problem that can cause uneven wear and potential damage to the belt. Ensure that the belt is properly aligned with the pulleys and idlers. Adjust the tracking if necessary to prevent the belt from running off-center.
- Inspect for Wear and Damage: Regularly check the belt for signs of wear, cuts, abrasions, or punctures. Look for any deterioration in the belt splices and repair or replace damaged sections promptly to prevent further issues.
- Verify Tension: Proper tension is critical for the smooth operation of the conveyor belt. Check the tension to ensure it is neither too tight nor too loose. Adjust as needed to maintain the correct tension and prevent slippage or excessive wear.
- Examine Components: Inspect all conveyor components, including pulleys, rollers, and idlers, for signs of wear or damage. Replace any worn or damaged parts to ensure the system operates efficiently.
- Clean and Lubricate: Regular cleaning and lubrication of the conveyor belt and components can prevent many common issues. Remove any debris, dirt, or contaminants that could cause friction or wear. Apply appropriate lubricants to moving parts to reduce friction and wear.
By following these steps, you can effectively diagnose and resolve common belt conveyor problems, ensuring the continued efficiency and reliability of your conveyor system.
Belt Conveyor Problems PDF
To further aid in troubleshooting and maintaining conveyor systems, we offer a downloadable PDF resource that provides extensive insights into belt conveyor problems and solutions. This guide is designed to be a comprehensive reference for anyone responsible for the operation and maintenance of conveyor systems.
The Belt Conveyor Problems PDF includes detailed information on:
- Common Issues: An overview of the most frequently encountered belt conveyor problems, including misalignment, slippage, wear and tear, and contamination. Each issue is explained in detail, with descriptions of how they occur and their impact on the system.
- Diagnosis Tips: Practical advice on how to diagnose specific problems. This section includes checklists and visual aids to help identify issues quickly and accurately.
- Maintenance Tips: Guidelines for regular maintenance practices that can prevent problems from occurring. This includes tips on cleaning, lubrication, and routine inspections to keep the conveyor system in optimal condition.
- Repair and Replacement: Step-by-step instructions for repairing or replacing damaged components. This section covers everything from fixing minor issues to performing major repairs, with clear, easy-to-follow procedures.
- Preventive Measures: Strategies for preventing common problems before they arise. This includes advice on proper installation, regular maintenance, and the use of high-quality materials and components.
By downloading the Belt Conveyor Problems PDF, you gain access to a wealth of knowledge that can help you maintain your conveyor system more effectively. This guide is an essential tool for anyone involved in the operation, maintenance, or troubleshooting of belt conveyors.
Belt Conveyor Problems Maintenance and Solutions
Effective maintenance and timely solutions are critical to addressing belt conveyor problems and ensuring the longevity and efficiency of your conveyor system. This section focuses on the importance of preventive maintenance and outlines practical solutions to common issues, with a downloadable PDF guide offering detailed insights and expert advice.
Conveyor Belt Maintenance PDF
Preventive maintenance is a proactive approach to managing belt conveyor problems, designed to identify and address potential issues before they escalate into significant failures. Our comprehensive Conveyor Belt Maintenance PDF guide promotes a series of best practices aimed at keeping your conveyor system in optimal condition.
Promote Preventive Maintenance Practices
- Regular Inspections: Conduct thorough and regular inspections of the conveyor belt and its components. Look for signs of wear, misalignment, and other issues that could lead to operational failures. Detailed checklists in the PDF guide help ensure nothing is overlooked.
- Cleaning and Lubrication: Maintaining a clean conveyor belt and lubricating moving parts reduce friction and wear, preventing premature belt degradation. The guide provides step-by-step instructions on the proper cleaning methods and lubrication schedules.
- Tension Adjustment: Proper belt tension is crucial for efficient operation. The PDF guide offers detailed procedures for checking and adjusting belt tension to prevent slippage and reduce wear.
- Component Replacement: Timely replacement of worn or damaged components is vital. The guide outlines how to identify and replace critical parts such as rollers, pulleys, and splices, ensuring the system runs smoothly.
- Training and Documentation: Educating your maintenance team on best practices and keeping detailed maintenance logs can prevent many belt conveyor problems. The guide includes training modules and templates for documentation.
Benefits of Regular Maintenance
Regular maintenance offers numerous benefits, including:
- Extended Lifespan: Proper care and timely repairs extend the lifespan of the conveyor belt, reducing the need for costly replacements.
- Reduced Downtime: Preventive maintenance minimizes unexpected breakdowns, ensuring continuous operation and higher productivity.
- Improved Safety: Regular inspections and maintenance enhance the safety of the conveyor system, preventing accidents caused by belt failures.
- Cost Savings: By addressing minor issues before they become major problems, maintenance reduces repair costs and increases the return on investment.
- Optimal Performance: Well-maintained conveyor systems operate more efficiently, handling materials smoothly and consistently.
Solutions to Conveyor Belt Problems
Addressing belt conveyor problems promptly and effectively requires a combination of practical solutions and expert support. Our PDF guide highlights several readily available solutions to common conveyor belt issues and emphasizes the importance of expert assistance in mitigating these problems.
Readily Available Solutions
- Realignment Tools: Misalignment is a frequent problem that can cause significant damage. Tools like laser alignment systems can help ensure precise alignment of the belt and pulleys.
- Belt Repair Kits: For minor cuts and abrasions, belt repair kits offer quick fixes that can be applied on-site, preventing further damage and extending the belt’s life.
- Tensioners: Automatic belt tensioners help maintain the correct tension, reducing the risk of slippage and wear.
- Cleaning Systems: Belt cleaning systems, including scrapers and brushes, can be installed to keep the belt surface free from debris and build-up.
- Monitoring Systems: Conveyor monitoring systems can detect early signs of wear and potential failures, allowing for proactive maintenance.
Expert Support in Mitigating and Solving Issues
- Consultation Services: Expert consultants can assess your conveyor system, identify potential problems, and recommend tailored solutions to address specific issues.
- Maintenance Training: Providing your maintenance team with training from industry experts ensures they are equipped with the knowledge and skills to maintain the conveyor system effectively.
- Custom Solutions: Experts can design and implement custom solutions, such as specialized belt materials or configurations, to address unique operational challenges.
- Regular Audits: Periodic audits by professionals can uncover hidden problems and ensure that maintenance practices are up to standard.
- Emergency Support: Having access to emergency support services ensures that any sudden belt conveyor problems are resolved quickly, minimizing downtime and operational disruption.
By leveraging the preventive maintenance practices and solutions outlined in our PDF guide, you can significantly reduce belt conveyor problems and enhance the reliability and efficiency of your conveyor system. Download the guide for detailed maintenance tips and expert solutions to keep your operations running smoothly.
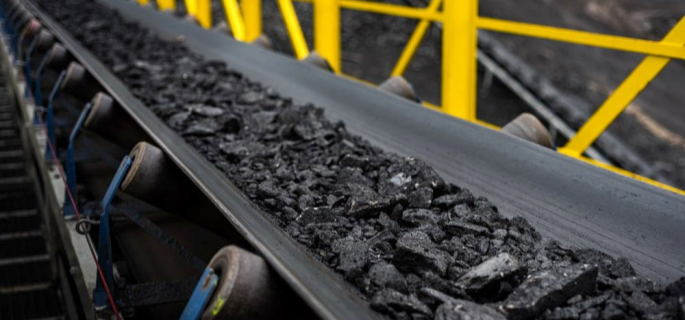
FAQs About Belt Conveyor Problems
Belt conveyors can encounter a variety of issues that affect their performance and efficiency. Common problems include misalignment, where the belt veers off its intended path, leading to edge damage and increased wear. Belt slippage occurs when there isn’t enough tension or friction between the belt and the pulleys, causing the belt to slip and lose efficiency. Wear and tear, such as cuts, abrasions, and punctures, are inevitable over time and can lead to serious damage if not addressed promptly. Material spillage is another issue where transported materials fall off the belt, leading to product loss and potential safety hazards. Other problems include belt breakage due to weak splices, contamination from dirt and debris, and excessive noise from worn components. Regular maintenance and timely interventions are essential to prevent these problems and ensure the smooth operation of belt conveyors.
Troubleshooting a conveyor belt involves a systematic approach to identify and resolve issues. Start by conducting a thorough visual inspection to detect any visible signs of damage, such as cuts, abrasions, or misalignment. Check the alignment of the belt to ensure it runs centrally over the pulleys and idlers. Misalignment can cause uneven wear and potential damage. Verify the belt tension to make sure it is neither too tight nor too loose, adjusting as necessary to prevent slippage or excessive wear. Inspect the splices for any signs of deterioration or weakness, and repair or replace them if needed. Clean the belt and remove any debris that might be causing friction or contamination. Lubricate moving parts to reduce friction and wear. Listen for unusual noises that might indicate issues with the belt or components. If problems persist, consult the manufacturer’s troubleshooting guide or seek expert assistance to diagnose and fix more complex issues.
Conveyors can experience several failure modes that disrupt their operation. Misalignment is a common failure mode where the belt moves off its intended path, causing wear and potential damage. Belt slippage occurs when the belt loses traction with the drive pulley, often due to improper tension or contamination. Component failure, such as broken or worn-out pulleys, idlers, or rollers, can lead to system breakdowns. Belt breakage can happen due to weak splices or excessive wear, resulting in significant downtime and repair costs. Overloading the conveyor can cause excessive strain on the belt and components, leading to premature failure. Material build-up and blockages can obstruct the belt’s movement, causing stress and potential damage. Regular maintenance, proper installation, and timely interventions are crucial to prevent these failure modes and ensure the reliable operation of conveyors.
Belt tracking problems occur when the conveyor belt does not run straight along the conveyor system, causing it to veer off its intended path. This misalignment can lead to a range of issues, including edge damage, uneven wear, and potential belt failure. Several factors can contribute to belt tracking problems, such as improper installation, misaligned pulleys or rollers, and uneven loading. The consequences of poor belt tracking include increased friction, which accelerates wear and tear, and the risk of the belt slipping off the track entirely, leading to significant downtime and maintenance costs. To address belt tracking problems, it is essential to regularly inspect and adjust the alignment of the belt and components. Ensuring that the belt is properly tensioned and that the pulleys and rollers are correctly aligned can help maintain optimal tracking. In some cases, installing tracking devices or guides can also help keep the belt on course, reducing the risk of misalignment and associated problems.
A conveyor belt might not move due to several reasons:
Power Issues: The motor or power supply could be malfunctioning or disconnected.
Mechanical Failures: Components like bearings, rollers, or the drive pulley might be damaged or seized.
Belt Tension: The belt might be too loose, causing it to slip and not move effectively.
Obstructions: Debris or materials could be obstructing the belt’s path.
Control System Failures: Issues with the control system or sensors could prevent the belt from starting.
Emergency Stops: An emergency stop button might have been engaged, halting the system.
The two major causes of belt slippage are:
Insufficient Belt Tension: If the belt is not tensioned properly, it can slip on the drive pulley, leading to a lack of movement.
Drive Pulley Issues: Wear and tear on the drive pulley, such as a worn surface or contamination with substances like oil or water, can reduce friction and cause the belt to slip.
Last Updated on July 31, 2024 by Jordan Smith
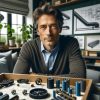
Jordan Smith, a seasoned professional with over 20 years of experience in the conveyor system industry. Jordan’s expertise lies in providing comprehensive solutions for conveyor rollers, belts, and accessories, catering to a wide range of industrial needs. From initial design and configuration to installation and meticulous troubleshooting, Jordan is adept at handling all aspects of conveyor system management. Whether you’re looking to upgrade your production line with efficient conveyor belts, require custom conveyor rollers for specific operations, or need expert advice on selecting the right conveyor accessories for your facility, Jordan is your reliable consultant. For any inquiries or assistance with conveyor system optimization, Jordan is available to share his wealth of knowledge and experience. Feel free to reach out at any time for professional guidance on all matters related to conveyor rollers, belts, and accessories.