Choosing the Best Drive Drum for Belt Conveyor
The drive drum for belt conveyor is a critical component in conveyor systems, ensuring the efficient movement of materials across various industries. As the primary mechanism that transfers power from the motor to the conveyor belt, the drive drum for belt conveyor plays a pivotal role in maintaining smooth operations. Understanding its function and significance is essential for selecting the right drive drum for belt conveyor, as it directly impacts the system’s performance and longevity. By choosing an appropriate drive drum, businesses can enhance their conveyor operations, reduce maintenance costs, and improve overall productivity. In this blog, we will delve into the intricacies of the drive drum for belt conveyor, exploring its components, types, and benefits.
What is the Drive Drum for Belt Conveyor
Definition and Function
A drive drum for belt conveyor is a cylindrical component that plays a pivotal role in the belt conveyor system. It is primarily responsible for driving the conveyor belt, facilitating the smooth and efficient movement of materials across various industries. The drive drum for belt conveyor is typically positioned at the head of the conveyor, where it connects to the motor through a gearbox. This connection is crucial as it transmits the necessary torque from the motor to the conveyor belt, enabling the belt to move.
The drive drum for belt conveyor is designed to ensure the continuous and reliable operation of the conveyor system. Its primary function is to provide the mechanical force required to move the conveyor belt, which in turn transports materials from one point to another. For instance, in mining operations, the drive drum is essential for moving bulk materials such as coal or ore over long distances. Similarly, in manufacturing plants, it helps in the smooth transportation of products along the production line.
Components and Materials
The drive drum for belt conveyor is composed of several critical components, each made from materials chosen for their specific properties and performance characteristics. These components include the shell, shaft, and lagging.
Shell: The shell of the drive drum for belt conveyor is typically made from high-strength steel. This choice of material ensures durability and the ability to withstand the high stresses and loads encountered during operation. The shell is cylindrical and forms the main body of the drive drum.
Shaft: The shaft is another vital component, usually constructed from high-grade steel such as Q235 or Q345. It serves as the central axis around which the shell rotates. The shaft is designed to handle significant torsional forces and is often supported by bearings at either end to ensure smooth rotation.
Lagging: The outer surface of the drive drum is often covered with a layer of lagging material, such as rubber or ceramic. This lagging enhances the friction between the drum and the conveyor belt, improving traction and reducing slippage. For example, in wet or oily environments, rubber lagging provides the necessary grip to maintain efficient conveyor operation.
Real-World Applications and Examples
In real-world applications, the drive drum for belt conveyor is used extensively across various industries. Companies like Rulmeca and Flexco are well-known manufacturers of high-quality drive drums. Rulmeca’s motorized pulleys, for example, integrate the motor and gearbox within the drum itself, offering a compact and efficient solution for driving belt conveyors. These motorized pulleys are used in applications ranging from mining and quarrying to food processing and packaging.
Flexco, another industry leader, provides drive drums that are designed to meet the specific needs of different conveyor systems. Their products are known for their durability and reliability, ensuring minimal downtime and reduced maintenance costs for conveyor operators.
In mining operations, the drive drum for belt conveyor is essential for moving large quantities of materials over long distances. For instance, a mining company might use a drive drum with a diameter of 1000 mm and a length of 2000 mm to transport ore from the extraction site to the processing plant. Such drive drums are designed to handle the heavy loads and harsh conditions typical of mining environments.
Importance of Material Selection
The materials used in the construction of the drive drum for belt conveyor significantly impact its performance and longevity. High-strength steel is commonly used for the shell and shaft due to its ability to withstand heavy loads and resist wear and tear. Rubber and ceramic lagging materials are chosen for their ability to provide excellent grip and reduce slippage, ensuring the efficient operation of the conveyor system.
The selection of materials also depends on the specific requirements of the application. For example, in food processing environments, stainless steel might be used for the shell to ensure hygiene and prevent contamination. Similarly, in high-temperature applications, heat-resistant materials are chosen to withstand the extreme conditions.
The drive drum for belt conveyor is a critical component that ensures the smooth and efficient operation of conveyor systems across various industries. By understanding its definition, function, components, and materials, businesses can make informed decisions when selecting and maintaining drive drums for their conveyor systems, thereby enhancing productivity and reducing operational costs.
What Are the Drive Drum for Belt Conveyor Systems
Types of Conveyor Drum Pulleys
The drive drum for belt conveyor systems is a critical component, but it is only one type of pulley used in these systems. There are several types of conveyor drum pulleys, each serving specific functions to ensure the efficient operation of the conveyor.
Drive Pulleys vs. Tail Pulleys
The drive drum for belt conveyor, also known as the drive pulley, is responsible for driving the conveyor belt and is usually located at the head of the conveyor system. It connects to the motor and transmits power to move the belt. Drive pulleys are typically larger in diameter and are designed to handle the high torque required to move heavy loads. For example, in mining operations, the drive pulley must be robust enough to move tons of material over long distances.
In contrast, the tail pulley, located at the opposite end of the conveyor system, serves as an idler to redirect the belt back to the drive pulley. Tail pulleys are generally smaller and do not require the same structural strength as drive pulleys. They help maintain tension and alignment of the belt, ensuring smooth operation.
Snub Pulleys and Take-Up Pulleys for Belt Tensioning
Snub pulleys are used to increase the angle of wrap around the drive drum for belt conveyor. This increased wrap angle provides greater traction, reducing the risk of belt slippage. By positioning snub pulleys strategically, conveyor designers can enhance the efficiency of the drive system without requiring additional power.
Take-up pulleys, on the other hand, are used to maintain proper tension on the conveyor belt. They are typically adjustable and are located near the drive drum for belt conveyor or at the tail end. Proper tensioning is crucial to prevent belt sag, reduce wear and tear, and ensure the longevity of the conveyor system. For example, in a large manufacturing plant, a take-up pulley system might be used to automatically adjust belt tension as loads vary throughout the day.
Material and Construction
The construction of a drive drum for belt conveyor involves using high-quality materials and advanced manufacturing techniques to ensure durability and optimal performance.
Materials Used in Manufacturing Conveyor Drum Pulleys
The drive drum for belt conveyor is typically constructed from high-strength steel, which provides the necessary durability and resistance to wear and tear. The outer surface of the drum is often covered with a layer of lagging material, such as rubber or ceramic, to enhance traction and reduce slippage. For instance, rubber lagging is commonly used in environments where the belt may come into contact with moisture or oils, as it offers excellent grip and resistance to slippage.
Ceramic lagging, on the other hand, is used in applications where higher levels of wear resistance are required. This type of lagging is particularly beneficial in harsh environments such as mining or aggregate processing, where the conveyor system is exposed to abrasive materials.
Construction Techniques for Durability and Performance
Manufacturing a drive drum for belt conveyor involves several critical steps to ensure it can withstand the demanding conditions of industrial applications. The drum shell is usually made from rolled steel plates, which are welded together to form a cylindrical shape. This shell is then precision-machined to ensure a perfect balance, which is crucial for smooth operation at high speeds.
The shaft of the drive drum is typically made from high-strength steel, such as Q235 or Q345, and is designed to handle significant torsional forces. The shaft is connected to the shell using locking elements, which provide a secure and durable connection. Bearings are used to support the shaft and allow it to rotate smoothly, minimizing friction and wear.
Companies like Rulmeca and Flexco employ advanced construction techniques to enhance the performance and durability of their drive drums for belt conveyors. For example, Rulmeca uses finite element analysis (FEA) during the design process to identify and address potential stress points, ensuring their products can withstand the toughest conditions. Flexco, on the other hand, focuses on precision manufacturing and quality control to produce drive drums that meet the highest industry standards.
In practical applications, a drive drum for belt conveyor in a large quarry operation might be designed to handle loads of up to 500 tons per hour, with a diameter of 1000 mm and a length of 2500 mm. Such a drum would be constructed with heavy-duty steel and ceramic lagging to ensure it can operate reliably under continuous use.
The selection and construction of the drive drum for belt conveyor are crucial to the efficient and reliable operation of conveyor systems. By understanding the types of pulleys, materials, and construction techniques involved, businesses can make informed decisions that enhance the performance and longevity of their conveyor systems.
Conveyor Belt Drum: Key Component of the Drive System
Integration with the Conveyor Belt
The drive drum for belt conveyor is an integral component that works in conjunction with the conveyor belt to facilitate the smooth and efficient movement of materials. It is positioned at the head of the conveyor system, where it connects to the motor, transmitting the necessary power to drive the belt. The drive drum for belt conveyor not only provides the mechanical force needed to move the belt but also ensures that the belt maintains proper tension and alignment throughout its operation.
The seamless integration of the drive drum with the conveyor belt is crucial for maintaining the efficiency of the entire system. Proper alignment of the drive drum for belt conveyor is essential to prevent the belt from drifting off course, which can lead to operational inefficiencies and increased wear and tear on the belt and drum. Misalignment can cause the belt to rub against the conveyor structure, leading to fraying and potential belt failure. For example, in a packaging plant, if the drive drum is not aligned correctly, it can cause the conveyor belt to slip or run off track, resulting in downtime and reduced productivity.
Proper alignment involves ensuring that the drive drum for belt conveyor is parallel to the tail pulley and that the belt tension is evenly distributed across its width. This alignment helps in maintaining consistent contact between the belt and the drive drum, enhancing traction and reducing slippage. Companies like Rulmeca provide detailed guidelines and tools for aligning drive drums to ensure optimal performance. By following these guidelines, conveyor operators can minimize the risk of belt misalignment and prolong the lifespan of both the belt and the drive drum.
Maintenance and Replacement
Regular maintenance of the drive drum for belt conveyor is vital to ensure its longevity and reliable performance. Maintenance involves routine inspections, lubrication of moving parts, and timely repairs to address any wear and tear. By implementing a proactive maintenance schedule, businesses can prevent costly downtime and extend the lifespan of their conveyor systems.
Tips for Maintaining Conveyor Belt Drums
- Regular Inspections: Conduct regular visual inspections of the drive drum for belt conveyor to check for signs of wear, such as cracks, dents, or unusual noises during operation. Inspect the lagging material for signs of wear and replace it if necessary.
- Lubrication: Ensure that the bearings and other moving parts of the drive drum are properly lubricated. Lubrication reduces friction, preventing overheating and extending the life of the drum and bearings.
- Tension Adjustment: Regularly check and adjust the tension of the conveyor belt to ensure it is within the recommended range. Proper tensioning prevents slippage and reduces stress on the drive drum and belt.
- Alignment Checks: Periodically check the alignment of the drive drum to ensure it is parallel to the tail pulley and that the belt is running straight. Misalignment can cause uneven wear and potential damage to the belt and drum.
Signs That Indicate the Need for Replacement
Despite regular maintenance, there will come a time when the drive drum for belt conveyor needs to be replaced. Recognizing the signs of a failing drive drum can help prevent unexpected breakdowns and maintain operational efficiency.
- Excessive Wear: If the lagging material on the drive drum shows excessive wear or peeling, it may be time to replace the drum. Worn lagging reduces traction and can lead to belt slippage.
- Cracks or Damage: Visible cracks or dents on the drum shell indicate structural damage that can compromise the drum’s integrity. In such cases, replacement is necessary to avoid further damage to the conveyor system.
- Unusual Noises: Unusual noises such as grinding or squeaking during operation can indicate bearing failure or misalignment. If lubrication and alignment checks do not resolve the issue, replacing the drive drum may be necessary.
- Decreased Performance: A noticeable decrease in conveyor performance, such as reduced speed or frequent belt slippage, can signal that the drive drum is no longer functioning efficiently. Replacement can restore optimal performance.
Real-world examples underscore the importance of timely maintenance and replacement. For instance, a large-scale distribution center utilizing conveyor systems from Flexco reported a significant reduction in downtime after implementing a rigorous maintenance schedule for their drive drums. By regularly inspecting and maintaining their equipment, they were able to identify and replace worn drive drums before they failed, ensuring continuous and efficient operations.
The drive drum for belt conveyor is a key component that ensures the efficient operation of conveyor systems. Proper integration, alignment, and maintenance are essential to maximize the lifespan and performance of the drive drum. By understanding the importance of these factors and implementing regular maintenance practices, businesses can enhance the reliability and efficiency of their conveyor systems.
Drive Drum for Belt Conveyor: Power and Efficiency
Power Transmission
The drive drum for belt conveyor is the primary component responsible for transmitting power from the motor to the conveyor belt. It is crucial to understand how this transmission occurs and the factors that influence its effectiveness. The drive drum for belt conveyor connects to the motor via a gearbox, which amplifies the torque produced by the motor. This torque is essential for moving the conveyor belt, especially when transporting heavy loads over long distances.
The power transmission process begins with the motor generating rotational force, which is then transferred to the drive drum through the gearbox. The drive drum for belt conveyor, typically located at the head of the conveyor system, rotates and moves the belt. This movement propels the materials placed on the belt, allowing for efficient material handling.
Torque and power ratings are critical aspects of the power transmission process. The torque rating of the drive drum for belt conveyor must be sufficient to handle the load and overcome any resistance encountered during operation. Insufficient torque can lead to belt slippage, reduced efficiency, and potential damage to the conveyor system. For instance, a drive drum with a torque rating of 1000 Nm (Newton-meters) would be suitable for medium to heavy-duty applications, ensuring smooth and reliable belt movement.
Power ratings, measured in horsepower (HP) or kilowatts (kW), indicate the amount of power the drive drum can handle. Higher power ratings are necessary for conveyors transporting heavy or bulk materials. For example, a conveyor system in a mining operation might require a drive drum with a power rating of 50 HP to move large quantities of ore. Companies like ABB and Siemens provide motors and gearboxes specifically designed to meet the power and torque requirements of drive drums for belt conveyors, ensuring optimal performance and longevity.
Efficiency Considerations
Efficiency is a critical consideration when selecting and operating a drive drum for belt conveyor. Several factors can affect the efficiency of the drive drum, including the design of the drum, the type of lagging used, and the overall maintenance of the conveyor system.
One of the primary factors affecting efficiency is the design of the drive drum for belt conveyor. Modern drive drums are engineered to minimize energy loss and maximize power transmission. For instance, drive drums with a spiral or wing design can reduce the buildup of material on the drum surface, improving traction and reducing energy consumption. Additionally, using high-quality bearings and precision machining can enhance the efficiency of the drive drum by reducing friction and ensuring smooth operation.
The type of lagging used on the drive drum for belt conveyor also plays a significant role in efficiency. Rubber and ceramic lagging are commonly used to improve traction and reduce slippage. Rubber lagging provides a good balance between cost and performance, while ceramic lagging offers superior wear resistance and longevity, particularly in harsh environments. For example, Flexco’s ceramic lagging products have been shown to increase the efficiency of drive drums by up to 20%, reducing energy consumption and extending the life of the conveyor system.
Proper maintenance is essential to maintain the efficiency of the drive drum for belt conveyor. Regular inspections and timely repairs can prevent minor issues from escalating into major problems. Lubricating bearings, checking alignment, and adjusting belt tension are all crucial maintenance tasks that can enhance the efficiency of the drive drum. In a large manufacturing facility, implementing a preventative maintenance program can reduce downtime and improve overall operational efficiency.
Energy-saving technologies and practices can further enhance the efficiency of the drive drum for belt conveyor. Variable frequency drives (VFDs) are one such technology that allows for precise control of motor speed and torque, optimizing the performance of the drive drum. By adjusting the motor speed to match the load requirements, VFDs can significantly reduce energy consumption and operating costs. Companies like Danfoss and Schneider Electric offer VFD solutions specifically designed for conveyor systems, enabling operators to achieve higher efficiency and lower energy costs.
Real-world examples demonstrate the impact of these efficiency considerations. For instance, a food processing plant that implemented VFDs and high-quality ceramic lagging on their drive drums reported a 15% reduction in energy consumption and a 25% increase in conveyor system lifespan. These improvements not only reduced operational costs but also enhanced the reliability and productivity of the plant.
The drive drum for belt conveyor is a vital component that ensures the efficient operation of conveyor systems. Understanding the power transmission process, the importance of torque and power ratings, and the factors affecting efficiency can help businesses optimize their conveyor systems. By implementing energy-saving technologies and maintaining regular maintenance schedules, companies can enhance the performance and longevity of their drive drums, leading to improved operational efficiency and reduced costs.
Motorized Pulley Conveyor: An Integrated Solution with Drive Drum for Belt Conveyor
Advantages of Motorized Pulleys
Motorized pulleys, often referred to as drive drum for belt conveyor systems, offer a range of benefits that make them an attractive option for many industrial applications. These integrated solutions encapsulate the motor, gearbox, and bearings within the drum, streamlining the conveyor system design and offering several key advantages.
Compact Design and Space-Saving Benefits
One of the most significant advantages of motorized pulleys is their compact design. By integrating the motor and gearbox inside the drum, motorized pulleys eliminate the need for external drive components. This compactness allows for more efficient use of space within a facility. For example, in a warehouse or distribution center where space is at a premium, motorized pulleys enable the installation of more conveyor lines within the same footprint. This efficiency can lead to higher throughput and better utilization of available space.
Enhanced Safety and Reduced Maintenance Needs
Safety is another critical advantage of using motorized pulleys as a drive drum for belt conveyor systems. Traditional conveyor drive systems often have exposed moving parts, which can pose safety hazards to workers. Motorized pulleys, with their enclosed design, significantly reduce the risk of accidents and injuries. By housing all moving components within the drum, motorized pulleys prevent direct contact, thereby enhancing workplace safety.
Maintenance requirements are also considerably lower with motorized pulleys. The sealed design protects internal components from dust, dirt, and moisture, which are common causes of wear and failure in traditional drive systems. This protection leads to longer service intervals and reduces the overall maintenance burden. For instance, companies like Rulmeca have reported that their motorized pulleys require up to 50% less maintenance compared to conventional drive systems, resulting in lower operational costs and increased uptime.
Applications and Use Cases
Motorized pulleys, serving as the drive drum for belt conveyor systems, are versatile and can be used in various industries and applications. Their compact and efficient design makes them suitable for environments where space, safety, and reliability are paramount.
Examples of Industries and Scenarios Where Motorized Pulleys Are Ideal
- Food Processing Industry: In food processing plants, hygiene and cleanliness are crucial. Motorized pulleys, with their enclosed and easy-to-clean design, meet stringent sanitary standards. Companies like Van der Graaf offer motorized pulleys with stainless steel construction, ideal for food processing applications where regular washdowns are required.
- Mining and Quarrying: In these harsh environments, durability and reliability are critical. Motorized pulleys are designed to withstand extreme conditions, such as heavy loads, abrasive materials, and continuous operation. For example, in a coal mine, a motorized pulley can handle the transportation of large volumes of coal with minimal maintenance and high reliability.
- Logistics and Distribution: Space optimization and efficiency are essential in warehouses and distribution centers. The compact design of motorized pulleys allows for the installation of more conveyor lines, improving the flow of goods and increasing throughput. Amazon’s distribution centers, for instance, use motorized pulleys to maximize efficiency and maintain high standards of safety.
Comparison with Traditional Drive Systems
When comparing motorized pulleys with traditional drive systems, several differences highlight the advantages of using motorized pulleys as the drive drum for belt conveyor systems. Traditional systems often consist of a motor, gearbox, and external drive components that require substantial space and frequent maintenance. These systems are also prone to alignment issues and increased wear due to exposure to environmental factors.
Motorized pulleys, on the other hand, offer a more streamlined and efficient solution. By integrating all drive components within the drum, motorized pulleys eliminate alignment issues and reduce wear. The enclosed design also protects the internal components from dust, dirt, and moisture, significantly extending their lifespan and reducing the need for frequent maintenance.
In terms of energy efficiency, motorized pulleys are typically more efficient than traditional drive systems. The direct drive mechanism reduces energy losses associated with belt slippage and misalignment. For instance, Danfoss’ motorized pulleys are designed to operate with up to 96% mechanical efficiency, translating to lower energy consumption and reduced operational costs.
Motorized pulleys, as an integrated drive drum for belt conveyor systems, offer numerous advantages over traditional drive systems. Their compact design, enhanced safety features, reduced maintenance needs, and higher efficiency make them ideal for a wide range of industrial applications. By choosing motorized pulleys, businesses can optimize their conveyor operations, improve safety, and achieve significant cost savings.
Drive Drum for Belt Conveyor: Leading the Charge with the Head Pulley
Function of the Head Pulley
The head pulley, often referred to as the drive drum for belt conveyor systems, plays a crucial role in driving the conveyor belt. Positioned at the front end of the conveyor, the head pulley is responsible for generating the necessary force to move the belt and the materials it carries. This primary function makes the head pulley the driving force behind the conveyor system’s efficiency and productivity.
The head pulley in a drive drum for belt conveyor system is connected to a motor via a gearbox. This setup allows the head pulley to convert the motor’s rotational energy into linear motion, propelling the conveyor belt forward. This conversion of energy is essential for maintaining a consistent and controlled movement of the belt, which is critical for the precise handling of materials.
The differences between head pulleys and other types of pulleys in a conveyor system are significant. While the head pulley drives the belt, other pulleys such as the tail pulley and snub pulley serve different functions. The tail pulley, located at the opposite end of the conveyor, acts as an idler, helping to redirect the belt back towards the head pulley. Snub pulleys are used to increase the belt’s wrap angle around the head pulley, improving traction and reducing slippage.
For example, in a large mining operation, the head pulley (drive drum) might be designed to handle heavy loads of mined material. The tail pulley ensures that the belt returns smoothly, while snub pulleys are strategically placed to maximize the contact area between the belt and the drive drum for belt conveyor, enhancing grip and efficiency.
Design and Specifications
The design and specifications of the head pulley, or drive drum for belt conveyor, are critical to its performance and longevity. Several factors, including diameter, face width, and material selection, influence the design of the head pulley.
Common Design Specifications for Head Pulleys
Head pulleys come in various sizes and configurations, depending on the specific requirements of the conveyor system. Common design specifications include:
- Diameter: The diameter of the head pulley affects the amount of torque it can generate. Larger diameters provide greater torque, which is essential for moving heavier loads. For instance, a head pulley with a diameter of 1000 mm might be used in a heavy-duty mining conveyor, while smaller diameters are suitable for light to medium-duty applications.
- Face Width: The face width of the head pulley should match the width of the conveyor belt to ensure uniform distribution of the load and prevent belt slippage. A wider face width can accommodate wider belts, which are used in high-capacity applications.
- Lagging: The outer surface of the head pulley is often covered with lagging material, such as rubber or ceramic. Lagging improves the friction between the pulley and the belt, enhancing traction and reducing slippage. Rubber lagging is commonly used for general applications, while ceramic lagging is preferred in high-wear environments due to its superior durability.
Material Choices and Their Impact on Performance
The materials used in the construction of the head pulley significantly impact its performance, durability, and maintenance requirements. High-strength steel is the most common material for head pulleys, offering excellent durability and resistance to deformation under heavy loads. Stainless steel is also used in environments where corrosion resistance is critical, such as in food processing or chemical industries.
For example, in a coal mine, a head pulley made from high-strength steel with ceramic lagging might be used to handle the abrasive nature of coal and the harsh operating conditions. In contrast, a stainless steel head pulley with rubber lagging might be used in a food processing plant to ensure hygiene and ease of cleaning.
Companies like Rulmeca and Dodge offer a range of head pulleys designed to meet various industry standards and specifications. Rulmeca’s head pulleys, for instance, are known for their robust construction and ability to handle high-tension applications. Dodge offers head pulleys with advanced lagging options, enhancing the grip and reducing maintenance needs.
In practical applications, a well-designed head pulley can significantly improve the efficiency and reliability of a conveyor system. For example, a logistics company might install head pulleys with advanced rubber lagging in their distribution centers to handle the high throughput of packages and reduce downtime due to maintenance.
The head pulley, or drive drum for belt conveyor, is a vital component that drives the conveyor belt and ensures the efficient movement of materials. Understanding its function, design, and material choices is crucial for optimizing conveyor system performance. By selecting the right head pulley for their specific needs, businesses can enhance productivity, reduce maintenance costs, and improve overall operational efficiency.
Drive Drum for Belt Conveyor: Getting the Measurements Right
Importance of Accurate Dimensions
The drive drum for belt conveyor is a crucial component that requires precise measurements to ensure optimal performance and efficiency. Accurate dimensions of the drive drum affect the overall functionality and longevity of the conveyor system. Understanding how these dimensions impact performance is essential for selecting and maintaining the right drive drum for specific applications.
How Dimensions Affect Conveyor Performance
The dimensions of the drive drum for belt conveyor significantly influence the belt’s tension, alignment, and speed. Incorrect dimensions can lead to a range of operational issues, including belt slippage, misalignment, and increased wear and tear. For example, a drive drum with an inadequate diameter might not provide sufficient torque, causing the belt to slip and reducing the efficiency of material transport.
Key measurements such as diameter, face width, and shaft size are critical in designing an effective drive drum for belt conveyor. These measurements determine the drum’s capacity to handle different loads and operating conditions. In a manufacturing plant, for instance, a drive drum with a larger diameter and appropriate face width can ensure smooth operation and minimize downtime.
Key Measurements to Consider
- Diameter: The diameter of the drive drum for belt conveyor is one of the most important measurements. A larger diameter provides greater torque and can handle heavier loads. For example, a drive drum with a diameter of 800 mm is suitable for heavy-duty applications, while smaller diameters may be used for lighter loads. Companies like Flexco design drive drums with various diameters to meet specific operational requirements.
- Face Width: The face width should match the width of the conveyor belt to ensure even load distribution and prevent belt slippage. A wider face width is beneficial for high-capacity systems where the belt needs to support substantial material volumes. For instance, a conveyor belt in a mining operation might require a drive drum with a face width of 1500 mm to handle the large quantities of ore being transported.
- Shaft Size: The size of the shaft affects the stability and alignment of the drive drum for belt conveyor. A larger shaft provides better support and reduces the risk of misalignment under heavy loads. Precision in shaft size is crucial for maintaining the balance and smooth rotation of the drive drum, ensuring efficient operation.
Customization Options
Customization of drive drum dimensions is often necessary to meet the unique requirements of different conveyor systems. Tailoring the dimensions of the drive drum for belt conveyor can provide significant operational benefits, including improved performance, reduced maintenance, and longer lifespan.
Availability of Custom-Sized Pulleys
Manufacturers like Rulmeca and Martin Engineering offer custom-sized drive drums to cater to specific industry needs. Customization options include variations in diameter, face width, and shaft size, allowing for a perfect fit in any conveyor system. These custom-sized pulleys are designed to meet specific operational parameters, ensuring optimal performance.
For example, Rulmeca provides drive drums tailored to the dimensions required by customers in the mining industry. These custom drums are designed to handle the extreme conditions and heavy loads typical of mining operations. Similarly, Martin Engineering offers bespoke solutions for material handling systems in sectors like agriculture and logistics, where precise dimensions are critical for efficient operation.
Benefits of Tailored Pulley Dimensions for Specific Applications
Tailoring the dimensions of the drive drum for belt conveyor to specific applications offers several benefits. Custom-sized drive drums can enhance the efficiency and reliability of the conveyor system, reducing downtime and maintenance costs. For instance, a custom-designed drive drum with an optimized diameter and face width can improve belt traction and minimize slippage, leading to smoother operation and less wear on the belt.
In the food processing industry, custom-sized drive drums can be designed to meet stringent hygiene standards. Stainless steel drive drums with specific dimensions ensure that the conveyor system operates efficiently while complying with food safety regulations. This customization can lead to better product quality and increased production efficiency.
Accurate dimensions are also essential for applications involving high-speed conveyors. Custom drive drums designed to precise specifications can handle the increased stress and wear associated with high-speed operations. For example, in a packaging plant where conveyors run at high speeds, a drive drum with the correct dimensions can ensure reliable performance and minimize the risk of breakdowns.
Accurate dimensions of the drive drum for belt conveyor are crucial for the efficient and reliable operation of conveyor systems. By considering key measurements such as diameter, face width, and shaft size, and opting for customized solutions, businesses can enhance the performance and longevity of their conveyors. Tailored drive drums provide significant operational benefits, making them a valuable investment for industries that rely on conveyor systems for material handling.
Choosing the Right Supplier for Drive Drum for Belt Conveyor
Criteria for Selection
Selecting the right manufacturer for a drive drum for belt conveyor is crucial for ensuring the efficiency, durability, and overall performance of your conveyor system. Here are the key factors to consider when choosing a supplier:
Key Factors to Consider When Selecting a Manufacturer
- Quality and Reliability: The quality of the drive drum for belt conveyor is paramount. Look for manufacturers that use high-quality materials and advanced manufacturing processes to produce reliable and durable drive drums. For instance, steel with high tensile strength is essential for withstanding the stresses and loads typical in heavy-duty applications.
- Experience and Expertise: Manufacturers with extensive experience and expertise in producing drive drums for belt conveyors are more likely to deliver superior products. Experienced manufacturers understand the nuances of different industries and can provide solutions tailored to specific needs. Companies like Rulmeca and Flexco have decades of experience in the conveyor industry and are known for their high-quality products.
- Customization Capabilities: Depending on your specific requirements, you might need a custom-sized drive drum for belt conveyor. Manufacturers that offer customization options can provide drive drums with precise dimensions and specifications that meet your operational needs. For example, Martin Engineering offers bespoke drive drum solutions designed to fit unique conveyor systems.
- Customer Support and Service: Excellent customer support is critical for addressing any issues that arise during installation and operation. Choose manufacturers that offer robust customer service, including technical support, maintenance services, and prompt response times. Companies like Dodge provide comprehensive customer support and technical assistance to ensure smooth operations.
- Lead Times and Delivery: Timely delivery of drive drums is crucial to avoid disruptions in your operations. Manufacturers with efficient production processes and reliable supply chains can ensure that you receive your drive drums when you need them. Quick lead times are particularly important in industries with high demands and tight schedules.
Importance of Quality Certifications and Industry Standards
Quality certifications and adherence to industry standards are indicators of a manufacturer’s commitment to producing high-quality drive drums for belt conveyors. Certifications such as ISO 9001:2015 demonstrate that a manufacturer follows stringent quality management practices. Additionally, compliance with industry standards like CEMA (Conveyor Equipment Manufacturers Association) ensures that the drive drums meet specific performance and safety criteria.
For example, a manufacturer certified with ISO 9001:2015 has established quality management systems that consistently provide products meeting customer and regulatory requirements. Similarly, drive drums that comply with CEMA standards are designed to ensure safe and reliable conveyor operations.
Top Manufacturers
Several leading manufacturers specialize in producing high-quality drive drums for belt conveyors. Here is an overview of some of the top manufacturers in the industry:
Rulmeca
Rulmeca is a global leader in the production of rollers, motorized pulleys, and other components for conveyor systems. With a strong focus on innovation and quality, Rulmeca’s drive drums are designed to meet the rigorous demands of various industries, including mining, logistics, and food processing. Rulmeca’s motorized pulleys integrate the motor and gearbox within the drum, offering a compact and efficient solution for driving conveyor belts.
Flexco
Flexco is renowned for its high-quality conveyor belt maintenance solutions, including drive drums for belt conveyors. Flexco’s products are designed to enhance belt performance and extend the lifespan of conveyor systems. Their drive drums are manufactured using advanced materials and precision engineering to ensure optimal performance and durability. Flexco also offers extensive customer support and technical services to help customers maintain their conveyor systems efficiently.
Martin Engineering
Martin Engineering provides innovative solutions for bulk material handling, including custom-sized drive drums for belt conveyors. Martin’s drive drums are known for their robust construction and ability to handle heavy loads in challenging environments. The company offers a range of customization options to meet specific operational requirements, making them a preferred choice for industries such as mining and aggregate processing.
Dodge
Dodge, a brand of ABB, is a leading manufacturer of mechanical power transmission products, including drive drums for belt conveyors. Dodge’s drive drums are designed for durability and performance, with features like precision machining and high-quality lagging materials. Dodge also provides comprehensive customer support and technical assistance, ensuring that customers receive the best possible service and solutions.
Siemens
Siemens is a global technology powerhouse known for its advanced drive systems, including drive drums for belt conveyors. Siemens’ drive drums are engineered for efficiency and reliability, utilizing cutting-edge technology to optimize conveyor operations. With a strong focus on innovation, Siemens continues to develop new solutions that enhance the performance and efficiency of conveyor systems.
Choosing the right supplier for your drive drum for belt conveyor is essential for ensuring the reliability and efficiency of your conveyor system. By considering factors such as quality, experience, customization capabilities, and customer support, and by selecting manufacturers with relevant certifications and industry standards, you can make an informed decision that will benefit your operations in the long term.
Drive Drum for Belt Conveyor: A Case Study on Rulmeca Motorized Pulley
Introduction to Rulmeca
Rulmeca is a renowned global leader in the production of rollers, motorized pulleys, and other components for conveyor systems. With over 50 years of experience in the industry, Rulmeca has established a solid reputation for innovation, quality, and reliability. The company’s motorized pulleys, often referred to as drive drum for belt conveyor systems, have revolutionized the way conveyors are powered, providing a compact and efficient solution that integrates the motor, gearbox, and bearings within the drum itself.
Founded in 1962 in Bergamo, Italy, Rulmeca quickly became a key player in the conveyor component market. The company expanded its operations globally, establishing manufacturing plants and sales offices in Europe, Asia, and the Americas. Today, Rulmeca is known for its commitment to excellence, producing high-quality products that meet the stringent demands of various industries, including mining, logistics, food processing, and bulk material handling.
Features of Rulmeca Motorized Pulleys
Rulmeca’s motorized pulleys, designed as the drive drum for belt conveyor systems, offer several unique features and benefits that set them apart from traditional conveyor drive systems.
Compact and Efficient Design
The primary advantage of Rulmeca’s motorized pulleys is their compact design. By integrating all drive components within the drum, these motorized pulleys eliminate the need for external motors, gearboxes, and bearings. This design not only saves space but also simplifies the conveyor system, reducing the number of components that need to be maintained. For example, a distribution center using Rulmeca motorized pulleys can achieve a more streamlined conveyor layout, allowing for increased throughput and better space utilization.
Enhanced Safety and Reliability
Safety is a critical concern in any industrial setting, and Rulmeca’s motorized pulleys address this by enclosing all moving parts within the drum. This design reduces the risk of accidents and injuries caused by exposed components. Additionally, the sealed construction protects the internal components from dust, dirt, and moisture, enhancing the reliability and longevity of the drive drum for belt conveyor systems. In a case study involving a large cement plant, the use of Rulmeca motorized pulleys resulted in a significant reduction in maintenance-related downtime and improved overall safety.
High Efficiency and Performance
Rulmeca motorized pulleys are engineered for high efficiency and performance. The direct drive mechanism minimizes energy losses, ensuring that more power is transmitted to the conveyor belt. This efficiency translates to lower energy consumption and reduced operating costs. For instance, a mining operation that switched to Rulmeca motorized pulleys reported a 15% decrease in energy usage and a corresponding reduction in energy costs.
Customization and Versatility
Rulmeca offers a wide range of motorized pulleys with various diameters, power ratings, and lagging options to suit different applications. This versatility allows customers to choose the right drive drum for belt conveyor systems based on their specific needs. In the food processing industry, for example, Rulmeca provides stainless steel motorized pulleys with food-grade lagging to meet hygiene and safety standards. In the logistics sector, companies can opt for pulleys with higher power ratings and specialized lagging materials to handle heavy loads and high-speed operations.
Case Study: Successful Implementation
A notable case study involves a large logistics company that implemented Rulmeca motorized pulleys in its distribution centers. The company faced challenges with space constraints and frequent maintenance issues with its traditional conveyor drive systems. By replacing these systems with Rulmeca motorized pulleys, the company achieved a 20% increase in available floor space, reduced maintenance costs by 30%, and improved overall system reliability. This successful implementation highlights the benefits and efficiency of using Rulmeca motorized pulleys as the drive drum for belt conveyor systems.
Customer Support and Services
Rulmeca’s commitment to customer satisfaction extends beyond product quality to comprehensive support and services. The company offers a range of services to ensure that customers receive the best possible experience with their drive drum for belt conveyor systems.
Technical Support and Consultation
Rulmeca provides expert technical support to help customers select the right motorized pulleys for their specific applications. The company’s engineers work closely with clients to understand their needs and recommend the most suitable solutions. This personalized approach ensures that customers get the maximum benefit from their conveyor systems.
Installation and Maintenance Services
To further support their customers, Rulmeca offers installation and maintenance services. These services include on-site installation assistance, routine maintenance checks, and troubleshooting support. By providing these services, Rulmeca helps customers maintain the efficiency and reliability of their drive drum for belt conveyor systems, reducing downtime and operational costs.
Training and Resources
Rulmeca also offers training programs and resources to help customers and their staff understand the operation and maintenance of motorized pulleys. These programs cover best practices for installation, routine maintenance, and troubleshooting, ensuring that customers can maintain their conveyor systems effectively.
Customer Satisfaction and Reliability
Rulmeca’s focus on customer satisfaction and product reliability has earned the company a strong reputation in the industry. The company’s commitment to quality, innovation, and comprehensive support ensures that customers receive durable and efficient drive drum for belt conveyor systems. This dedication to excellence is reflected in the positive feedback and long-term relationships Rulmeca has built with its clients.
Rulmeca motorized pulleys, designed as the drive drum for belt conveyor systems, offer a compact, efficient, and reliable solution for powering conveyor belts. With a strong emphasis on safety, performance, and customer support, Rulmeca continues to lead the industry, providing innovative solutions that meet the diverse needs of its global customer base.
FAQa about Drive Drum For Belt Conveyor
A drum in a conveyor, specifically known as a drive drum for belt conveyor, is a cylindrical component that plays a crucial role in the conveyor system’s operation. The drum, also referred to as a pulley, is mounted at the ends of the conveyor and helps in supporting and moving the conveyor belt. In a typical belt conveyor system, there are at least two drums – a drive drum, which provides the driving force, and an idler drum, which supports the belt without driving it. The drive drum is connected to a motor that powers the conveyor, causing the belt to move. This movement facilitates the transportation of materials from one point to another, enhancing efficiency and productivity in various industries such as mining, manufacturing, and logistics. The drum’s surface can be smooth or coated with rubber to improve grip and reduce slippage, ensuring the belt moves consistently and reliably.
A drive motor drum, often referred to as a drive drum for belt conveyor, is an integral component of the conveyor system that combines the functions of a drum and a motor. This configuration simplifies the design and operation of the conveyor by integrating the motor directly into the drum itself. The drive motor drum is responsible for generating the rotational force needed to move the conveyor belt. It eliminates the need for external motor mounts and additional drive components, leading to a more compact and efficient system. These drums are designed to provide consistent and reliable power transmission, ensuring smooth and uninterrupted operation of the conveyor. The integration of the motor within the drum also reduces maintenance requirements and enhances the system’s overall reliability. Drive motor drums are commonly used in various industries where space constraints and efficiency are critical considerations, offering a streamlined solution for material handling applications.
The drive system of a belt conveyor, incorporating the drive drum for belt conveyor, is the mechanism that provides the necessary force to move the conveyor belt and transport materials. This system typically consists of several key components: the drive drum, motor, gearbox, coupling, and support structure. The motor, often electric, generates the power that is transmitted through the gearbox, which adjusts the speed and torque to suitable levels for the conveyor. This power is then transferred to the drive drum, which, in turn, moves the belt. The drive drum is critical as it ensures the belt runs smoothly and maintains proper tension. In some systems, multiple drive drums may be used to handle heavier loads or to distribute the driving force more evenly. The efficiency of the drive system directly impacts the conveyor’s performance, influencing factors like speed, load capacity, and energy consumption. Properly designed drive systems are essential for the reliable and efficient operation of belt conveyors in various industrial applications.
A drive pulley on a conveyor belt, often referred to as a drive drum for belt conveyor, is a vital component that drives the belt, enabling the transportation of materials along the conveyor path. The drive pulley is connected to a motor and transmits the rotational force generated by the motor to the conveyor belt. This action causes the belt to move, facilitating the continuous flow of materials. Drive pulleys are typically located at the discharge end of the conveyor, although they can also be positioned at the feed end or both ends in some configurations. The surface of the drive pulley is usually coated with rubber or another high-friction material to enhance grip and prevent belt slippage, ensuring efficient power transfer. Properly designed and maintained drive pulleys are crucial for the smooth and reliable operation of conveyor systems, playing a key role in industries such as mining, manufacturing, and logistics, where efficient material handling is essential.
Last Updated on July 10, 2024 by Jordan Smith
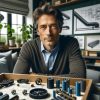
Jordan Smith, a seasoned professional with over 20 years of experience in the conveyor system industry. Jordan’s expertise lies in providing comprehensive solutions for conveyor rollers, belts, and accessories, catering to a wide range of industrial needs. From initial design and configuration to installation and meticulous troubleshooting, Jordan is adept at handling all aspects of conveyor system management. Whether you’re looking to upgrade your production line with efficient conveyor belts, require custom conveyor rollers for specific operations, or need expert advice on selecting the right conveyor accessories for your facility, Jordan is your reliable consultant. For any inquiries or assistance with conveyor system optimization, Jordan is available to share his wealth of knowledge and experience. Feel free to reach out at any time for professional guidance on all matters related to conveyor rollers, belts, and accessories.