Custom Conveyor Belt Drives for Aggregate Production
In the realm of aggregate production, conveyor belt drives play a pivotal role in ensuring efficiency and productivity. These systems are essential for transporting materials quickly and effectively, reducing manual labor and operational costs. This blog post explores the various aspects of conveyor belt drives for aggregate production, detailing the types of systems available, their benefits, and key considerations for selection and use. From portable aggregate conveyors to radial stacker conveyors, we will discuss how these systems enhance the efficiency of aggregate production processes. Understanding the importance and functionality of conveyor belt drives for aggregate production is crucial for optimizing operations and maximizing output.
Portable Aggregate Conveyor Belt Drives for Aggregate Production
Overview
Portable aggregate conveyor belt drives for aggregate production are crucial for flexible and mobile material handling solutions. These systems provide the ability to transport materials over short or long distances, adapting to various project sites. Whether in construction, mining, or other industries, the need for efficient, reliable, and easy-to-move conveyor systems is paramount. Portable conveyor belt drives for aggregate production can be quickly set up and taken down, making them ideal for temporary or remote locations where traditional, permanent conveyor systems are impractical.
Benefits
Mobility
Portable aggregate conveyor belt drives for aggregate production offer unparalleled mobility, allowing them to be easily moved to different locations as needed. This flexibility is essential for operations that frequently change sites or need to adjust their setup to accommodate different stages of production. For instance, a construction company working on multiple sites can use portable conveyor belt drives for aggregate production to quickly set up material handling systems at each new location without significant downtime or additional infrastructure.
Versatility
The versatility of portable conveyor belt drives for aggregate production is another major advantage. These systems are suitable for various types of aggregates, from sand and gravel to larger rocks and minerals. Companies like Superior Industries offer portable conveyor solutions that can handle a wide range of materials, ensuring that businesses can use a single type of system for multiple applications, reducing the need for multiple specialized conveyors.
Efficiency
Efficiency is a key benefit of portable aggregate conveyor belt drives for aggregate production. Quick setup and takedown processes significantly reduce downtime, allowing operations to start sooner and maintain productivity even when moving between sites. For example, the portable conveyors from West River Conveyors are designed for rapid deployment and can be operational within a few hours, compared to the days or weeks required for permanent systems. This efficiency translates to cost savings and increased operational speed.
Applications
Construction Sites

At construction sites, portable aggregate conveyor belt drives for aggregate production are invaluable. They streamline the process of transporting raw materials like sand, gravel, and concrete from storage areas to where they are needed on-site. This not only speeds up construction activities but also reduces the physical strain on workers, improving safety and efficiency. Portable conveyor systems from companies like Terex can be seen in large-scale projects, including highway construction and urban development, where mobility and adaptability are crucial.
Temporary Project Setups
For temporary project setups, the use of portable aggregate conveyor belt drives for aggregate production is essential. Projects such as short-term mining operations, site remediation, or disaster response efforts benefit greatly from the flexibility and speed of these systems. For example, during the cleanup after natural disasters, portable conveyors can quickly move debris and aggregate materials, facilitating faster recovery efforts.
Remote Locations
In remote locations with limited infrastructure, portable aggregate conveyor belt drives for aggregate production are often the only viable solution for material handling. These systems can be transported to remote mining sites or off-the-grid construction areas where permanent conveyor installations are not feasible. Companies like McCloskey International provide robust, portable conveyor solutions that can be deployed in the most challenging environments, ensuring continuous production and material flow despite the lack of permanent infrastructure.
Portable aggregate conveyor belt drives for aggregate production are a vital tool in various industries, providing the mobility, versatility, and efficiency needed to handle diverse material handling challenges. With the ability to quickly adapt to different sites and project requirements, these systems play a critical role in maintaining productivity and operational flexibility.
Aggregate Conveyor for Sale: Finding the Right Conveyor Belt Drives for Aggregate Production
Key Considerations
When looking to purchase aggregate conveyor belt drives for aggregate production, several factors must be considered to ensure optimal performance and longevity. The right system can significantly enhance efficiency, reduce costs, and improve overall productivity. Key considerations include the system’s durability, capacity, and customization options.
Features to Look For
Durability
Durability is paramount when selecting conveyor belt drives for aggregate production. The systems must withstand the rigors of transporting heavy, abrasive materials over extended periods. For instance, West River Conveyors offers conveyor systems designed with high-quality materials and robust construction, ensuring they can handle the toughest conditions. These systems often feature reinforced belts and heavy-duty rollers, which can significantly extend their lifespan and reduce maintenance costs.
Capacity
The capacity of conveyor belt drives for aggregate production is another critical feature. It’s essential to choose a system capable of transporting the required volume of materials efficiently. Superior Industries, a leading manufacturer in the industry, provides conveyors with varying capacities to suit different production needs. Their systems can handle anything from small-scale operations to large, industrial-scale aggregate production, ensuring that businesses can find a solution that matches their specific requirements.
Customization
Customization options are vital for tailoring conveyor belt drives for aggregate production to fit specific project needs. Custom designs can include specific belt types, drive systems, and configurations to handle unique material characteristics or operational environments. Companies like KWS Manufacturing offer extensive customization options, allowing businesses to design conveyor systems that meet their exact specifications. This level of customization ensures that the conveyor system integrates seamlessly into existing operations, optimizing workflow and efficiency.
Leading Suppliers
Overview of Top Manufacturers
When purchasing conveyor belt drives for aggregate production, it’s essential to consider offerings from top manufacturers known for their quality and reliability. Companies like Superior Industries, West River Conveyors, and KWS Manufacturing are leaders in the field, providing a wide range of conveyor solutions.
Comparison of Features, Prices, and Warranties
Superior Industries is renowned for its innovative conveyor systems that offer high capacity and robust durability. Their products are competitively priced and come with extensive warranties, ensuring long-term reliability and customer satisfaction. West River Conveyors is another top supplier, known for their custom solutions and high-quality materials, which are ideal for heavy-duty applications. They offer detailed customization options and competitive pricing. KWS Manufacturing specializes in custom conveyor solutions tailored to meet specific industry needs, providing detailed engineering support and robust warranties to back their products.
Examples and Real-World Applications
Superior Industries recently provided conveyor systems for a large-scale aggregate production facility in Texas. Their high-capacity systems enabled the facility to significantly increase its production rate while reducing operational costs. The durability of the systems has led to a reduction in downtime and maintenance requirements, resulting in improved overall efficiency.
West River Conveyors customized a conveyor belt drive system for a mining operation in Nevada, ensuring it could handle the abrasive materials and harsh conditions typical of the industry. The tailored solution included reinforced belts and heavy-duty rollers, which have performed exceptionally well, enhancing the mine’s productivity and reducing maintenance needs.
KWS Manufacturing worked with a construction company in California to design a conveyor system for a complex project that required transporting various types of aggregates over challenging terrain. The custom-designed system included specialized belt types and drive configurations that optimized the material handling process, significantly improving the project’s efficiency and timeline.
Choosing the right conveyor belt drives for aggregate production involves considering factors like durability, capacity, and customization. By evaluating offerings from leading suppliers and understanding the specific needs of your operation, you can select a system that enhances productivity and operational efficiency. With solutions from top manufacturers like Superior Industries, West River Conveyors, and KWS Manufacturing, you can ensure your aggregate production processes are streamlined and effective.
Aggregate Conveyor Rental: Cost-Effective Conveyor Belt Drives for Aggregate Production
Advantages of Renting

Renting aggregate conveyor belt drives for aggregate production can be a highly cost-effective solution, especially for short-term projects or trial periods before committing to a purchase. Renting provides flexibility, allowing companies to access high-quality equipment without the significant upfront investment required for purchase. This is particularly beneficial for projects with limited durations or for companies looking to test the effectiveness of a specific conveyor system before making a long-term commitment.
- Flexibility
Renting conveyor belt drives for aggregate production offers significant flexibility. Companies can choose rental periods that match their project timelines, whether it’s a few weeks or several months. For example, during a large-scale construction project in New York, a construction firm rented conveyor systems from Sunbelt Rentals for a six-month period. This allowed them to complete the project efficiently without the burden of purchasing and maintaining the equipment long-term. - Cost Savings
Cost savings are another major advantage of renting. Renting conveyor belt drives for aggregate production eliminates the need for a large initial investment, freeing up capital for other critical areas of the project. Additionally, rental agreements often include maintenance and support services, reducing the overall cost and hassle of keeping the equipment in optimal working condition. For instance, Herc Rentals provides comprehensive maintenance services as part of their rental agreements, ensuring that the equipment remains in top condition and minimizing downtime. - Access to Latest Technology
Renting also allows companies to access the latest technology without the commitment of a purchase. This is particularly important in an industry where technological advancements can significantly impact efficiency and productivity. By renting, companies can ensure they are using the most advanced and efficient conveyor belt drives for aggregate production available on the market. United Rentals, for instance, offers state-of-the-art conveyor systems that incorporate the latest advancements in material handling technology, providing renters with high-performance equipment that boosts productivity.
Rental Considerations
Rental Duration
When considering rental options for conveyor belt drives for aggregate production, it’s essential to think about the rental duration. Flexible rental terms are crucial to align with project timelines, ensuring that equipment is available for the entire duration of the project. Companies should seek rental providers like BlueLine Rental, which offer flexible terms that can be tailored to the specific needs of each project, whether short-term or long-term.
Maintenance
Maintenance is another critical consideration. Ensuring that the rental agreement includes maintenance and support services can prevent costly downtime and keep the project on track. Providers like Sunbelt Rentals offer comprehensive maintenance packages as part of their rental agreements, ensuring that any issues are promptly addressed, and equipment remains operational throughout the rental period.
Upgrades
Access to the latest upgrades is an important benefit of renting conveyor belt drives for aggregate production. Rental agreements often allow for equipment upgrades, ensuring that companies can take advantage of the latest technological advancements without additional costs. For example, Herc Rentals frequently updates their inventory with the latest models, providing renters with access to cutting-edge technology and improved performance features.
Popular Rental Options
Several companies specialize in renting conveyor belt drives for aggregate production, each offering a variety of rental packages and pricing options.
- Sunbelt Rentals
Sunbelt Rentals is a leading provider of equipment rental services, including conveyor systems. They offer a wide range of conveyor belt drives for aggregate production, with flexible rental terms and comprehensive maintenance packages. Sunbelt’s rental options are ideal for both short-term projects and longer-term needs, providing reliable and efficient equipment. - Herc Rentals
Herc Rentals offers state-of-the-art conveyor systems that incorporate the latest technology. Their rental packages include maintenance and support services, ensuring that the equipment remains in optimal condition throughout the rental period. Herc Rentals is known for its customer service and high-quality equipment, making them a top choice for many companies. - BlueLine Rental
BlueLine Rental provides flexible rental terms and a variety of conveyor systems suitable for aggregate production. Their rental agreements can be tailored to fit the specific needs of each project, and they offer comprehensive maintenance services to ensure minimal downtime. BlueLine Rental is a reliable provider with a strong reputation for quality and flexibility.
Renting aggregate conveyor belt drives for aggregate production is a practical and cost-effective solution for many companies. It offers flexibility, cost savings, and access to the latest technology, ensuring efficient and productive operations. By considering factors such as rental duration, maintenance, and available upgrades, companies can choose the best rental option to meet their specific needs and maximize their operational efficiency.
Aggregate Conveyor Belt: Essential Components of Conveyor Belt Drives for Aggregate Production
Belt Types
Different types of conveyor belts are integral components of conveyor belt drives for aggregate production, each suited for specific applications based on the materials they handle and the operational environment. Understanding the various belt types helps in selecting the right belt for efficient and reliable aggregate handling.
- Rubber Belts
Rubber belts are among the most commonly used in conveyor belt drives for aggregate production. They are known for their durability and flexibility, making them ideal for transporting abrasive materials like sand, gravel, and crushed stone. For example, companies like Fenner Dunlop manufacture high-quality rubber conveyor belts designed to withstand heavy loads and harsh conditions typical in aggregate production. These belts can operate in temperatures ranging from -20°C to +50°C, ensuring performance stability across various environments. - Metal Belts
Metal belts are preferred in scenarios where heat resistance belt and strength are critical. These belts are often used in high-temperature environments or where sharp and heavy materials are conveyed. Metal belts, such as those produced by Wire Belt Company, offer excellent resistance to wear and corrosion, making them suitable for applications involving hot aggregate or slag. Their robust construction ensures they can handle the rigors of demanding production processes, extending the operational lifespan of conveyor belt drives for aggregate production. - Fabric Belts
Fabric belts, typically made from materials like polyester, nylon, or cotton, are lightweight and easy to handle. They are used in conveyor belt drives for aggregate production where lighter, non-abrasive materials are transported. These belts are often employed in applications where weight reduction and ease of maintenance are important. For instance, Intralox offers fabric belts designed for efficiency in light aggregate handling, providing a balance between strength and flexibility.
Material Composition

The material composition of conveyor belts is crucial in determining their suitability for different aggregate production environments. Each material type offers distinct advantages tailored to specific operational needs.
- Rubber Belts
Rubber belts provide excellent abrasion resistance and flexibility, which are essential for handling rough and uneven aggregate materials. The rubber composition allows these belts to absorb impacts and resist cuts, ensuring longevity and reducing maintenance costs. Their flexibility also allows for easy installation and adaptation to varying conveyor system configurations. - Metal Belts
Metal belts, made from stainless steel or other durable metals, offer superior strength and heat resistance. These belts can withstand high temperatures and heavy loads, making them ideal for extreme conditions found in some aggregate production environments. The metal composition also ensures minimal elongation, maintaining consistent performance over time. - Fabric Belts
Fabric belts are composed of multiple layers of woven materials, providing a balance between strength and flexibility. The lightweight nature of these belts makes them easy to install and maintain. Additionally, fabric belts can be coated with materials like PVC or polyurethane to enhance their durability and resistance to specific environmental factors.
Maintenance Tips
Proper maintenance of conveyor belts is essential to ensure the efficiency and longevity of conveyor belt drives for aggregate production. Regular maintenance practices can prevent unexpected downtimes and extend the lifespan of the belts.
Regular Inspections
Conducting regular inspections for wear and tear is crucial. Look for signs of abrasion, cuts, or punctures that could compromise the belt’s integrity. For instance, an aggregate production facility using Fenner Dunlop belts might schedule weekly inspections to identify and address any issues promptly.
Proper Tensioning
Maintaining proper tension in the conveyor belt is vital to prevent slippage and ensure smooth operation. Over-tensioning can lead to excessive wear, while under-tensioning can cause the belt to slip and reduce efficiency. Companies like Continental provide guidelines and tools for accurate belt tensioning, helping maintain optimal performance.
Cleaning and Lubrication
Keeping the conveyor belt clean and well-lubricated reduces friction and prevents material buildup that could cause belt misalignment. Regular cleaning schedules and the use of appropriate lubricants can significantly extend the belt’s operational life. For example, using a belt cleaner from Martin Engineering can help remove debris and reduce the risk of damage.
Aggregate conveyor belts are essential components of conveyor belt drives for aggregate production. By understanding the different belt types, material compositions, and maintenance practices, businesses can ensure efficient and reliable material handling operations. With the right belts and proper maintenance, conveyor belt drives for aggregate production can achieve optimal performance, reducing downtime and operational costs.
Conveyor Belt Drive Motor: Powering Conveyor Belt Drives for Aggregate Production
Types of Drive Motors
Conveyor belt drives for aggregate production rely heavily on the choice of drive motor to ensure efficient and consistent operation. Various types of drive motors are used, each with unique characteristics suited to different operational requirements and conditions.
- Electric Motors
Electric motors are among the most commonly used in powering conveyor belt drives for aggregate production. They are known for their efficiency and reliability, making them ideal for continuous use in demanding environments. For instance, companies like Baldor Electric Company offer a wide range of electric motors specifically designed for industrial applications, including those in aggregate production. These motors can handle significant loads and provide consistent power, ensuring that conveyor systems operate smoothly and without interruption. - Hydraulic Motors
Hydraulic motors are another option, particularly useful in heavy-duty applications where high torque is required. These motors convert hydraulic pressure into mechanical energy, providing the power needed to move large quantities of aggregate materials. Bosch Rexroth is a leading manufacturer of hydraulic motors, offering models that are designed to withstand the harsh conditions often found in aggregate production environments. Hydraulic motors are especially beneficial in mobile and portable conveyor systems, where their compact size and high power output can be fully utilized. - Variable Frequency Drives (VFDs)
Variable Frequency Drives (VFDs) are advanced motor controllers that adjust the speed and torque of electric motors. VFDs are highly beneficial in conveyor belt drives for aggregate production because they allow for precise control over conveyor speeds, optimizing performance and reducing energy consumption. Companies like Siemens provide VFD solutions that integrate seamlessly with conveyor systems, offering enhanced control and flexibility. By using VFDs, operators can adjust conveyor speeds to match the specific needs of the production process, improving efficiency and reducing wear and tear on the equipment.
Motor Selection
Choosing the right drive motor for conveyor belt drives for aggregate production involves considering several factors to ensure the motor meets the specific needs of the operation.
Electric Motors
Electric motors are often selected for their efficiency and reliability. They are suitable for applications where continuous, consistent power is required. For example, a large-scale aggregate production facility using electric motors from ABB can benefit from reduced energy costs and minimal maintenance requirements, thanks to the motors’ high efficiency and robust construction. ABB’s electric motors are designed to handle the heavy loads and constant operation typical in aggregate production, making them a reliable choice for many facilities.
Hydraulic Motors
Hydraulic motors are chosen for their ability to provide high torque, which is essential in applications involving heavy materials and demanding operational conditions. A mining operation using hydraulic motors from Parker Hannifin can achieve the necessary power to move large volumes of aggregate efficiently. These motors are designed to operate in the harshest environments, providing the durability and power required for continuous, heavy-duty use.
Variable Frequency Drives (VFDs)
VFDs are selected for their ability to offer precise control over motor speeds, enhancing the efficiency and flexibility of conveyor belt drives for aggregate production. An aggregate production plant utilizing VFDs from Schneider Electric can fine-tune conveyor speeds to match varying production demands, reducing energy consumption and improving overall process efficiency. Schneider Electric’s VFDs are engineered to integrate with existing conveyor systems, providing a seamless solution for optimizing motor performance.
Installation and Maintenance
Proper installation and maintenance of drive motors are crucial to ensure the optimal performance and longevity of conveyor belt drives for aggregate production.
Guidelines for Proper Installation
Ensuring proper installation involves following manufacturer guidelines and best practices to avoid common issues that could affect motor performance. For example, aligning the motor correctly with the conveyor belt is essential to prevent undue wear and tear. Using conveyor roller mounting brackets and alignment tools provided by manufacturers like SEW-EURODRIVE can help achieve precise installation. Additionally, ensuring that electrical connections are secure and that the motor is adequately ventilated will contribute to reliable operation.
Routine Maintenance Practices
Routine maintenance is key to preventing motor failures and ensuring consistent performance. Regular inspections should be conducted to check for signs of wear, overheating, or unusual vibrations. Lubricating moving parts, cleaning the motor to prevent dust and debris buildup, and checking electrical connections are all critical maintenance tasks. Implementing a maintenance schedule, as recommended by motor manufacturers such as Nidec Motor Corporation, can help identify potential issues before they lead to significant problems, thus minimizing downtime and maintenance costs.
Conveyor belt drive motors are integral to the operation of conveyor belt drives for aggregate production. By selecting the appropriate type of motor, ensuring proper installation, and maintaining the equipment regularly, companies can enhance the efficiency and reliability of their aggregate production processes. Whether using electric motors, hydraulic motors, or VFDs, understanding the specific needs and operational conditions is crucial for optimal motor performance and longevity.
Aggregate Conveyor Manufacturers: Leaders in Conveyor Belt Drives for Aggregate Production
Top Manufacturers
In the realm of conveyor belt drives for aggregate production, several manufacturers stand out due to their innovative solutions, robust products, and exceptional customer service. These companies have established themselves as leaders by consistently providing high-quality equipment that meets the demanding needs of aggregate production environments. Understanding the strengths of these top manufacturers can help businesses make informed decisions when selecting conveyor systems.
Company Profiles
GRAM Conveyor
GRAM Conveyor is a distinguished manufacturer renowned for its high-quality conveyor belt drives tailored specifically for aggregate production. Their products are engineered to meet the unique requirements of each project, ensuring robust performance and efficiency. GRAM’s expertise extends to a wide range of conveyor systems, including the ‘GRAM Nylon Series,’ which is designed for heavy-duty applications with lightweight, corrosion-resistant materials. With a focus on innovation and durability, GRAM Conveyor has established itself as a trusted name in the industry, providing reliable solutions that enhance operational efficiency in aggregate production.
West River Conveyors
West River Conveyors is renowned for its custom solutions and robust conveyor systems designed specifically for aggregate production. They offer a range of conveyor belt drives tailored to meet the unique requirements of each project. With over 40 years of experience, West River Conveyors has a deep understanding of the challenges faced by the industry and provides systems that enhance efficiency and reliability. For instance, their custom-engineered overland conveyors are used in mining operations across the United States, ensuring seamless material transport over long distances.
Superior Industries
Superior Industries is a leading manufacturer that offers a wide array of aggregate handling equipment, including conveyor belt drives for aggregate production. Their product line includes portable and stationary conveyors, stackers, and transfer systems designed to handle various types of aggregate materials. Superior Industries’ equipment is known for its durability and performance, making it a preferred choice for large-scale aggregate producers. An example of their impact can be seen in a quarry in Texas, where Superior’s TeleStacker® Conveyor increased the stockpiling capacity by 30%, optimizing the site’s operational efficiency.
KWS Manufacturing
KWS Manufacturing specializes in heavy-duty conveyor systems, providing reliable and efficient solutions for the most demanding aggregate production environments. Their conveyor belt drives are designed to handle heavy loads and abrasive materials, ensuring long-lasting performance. KWS Manufacturing’s expertise in screw conveyors and bucket elevators allows them to offer comprehensive material handling solutions. A notable project involved the installation of a high-capacity screw conveyor system in a cement plant, significantly improving the facility’s material handling efficiency and reducing maintenance costs.
Product Highlights
Innovative Designs and Technologies
The leading manufacturers of conveyor belt drives for aggregate production continuously innovate to improve their product offerings. West River Conveyors, for example, incorporates advanced control systems and automated features into their conveyors, enhancing operational efficiency and safety. Superior Industries leverages cutting-edge technology to develop telescoping conveyors that provide precise control over material placement, reducing waste and improving stockpile management. KWS Manufacturing focuses on designing robust systems with enhanced wear resistance, ensuring their conveyors can withstand the harshest operating conditions.
Customer Support and Service Offerings
Excellent customer support and comprehensive service offerings are critical components of the value provided by top manufacturers. West River Conveyors offers extensive after-sales support, including installation services, maintenance training, and parts replacement programs. Superior Industries provides technical support and on-site training to ensure customers get the most out of their equipment. KWS Manufacturing’s service team works closely with clients to design and implement customized solutions, offering ongoing support to optimize system performance and longevity.
Real-World Examples
West River Conveyors
In a recent project, West River Conveyors supplied a custom overland belt conveyor system to a mining operation in Nevada. The system, designed to transport aggregate over rugged terrain, improved the site’s material handling efficiency by 25%. The conveyor’s durable construction and advanced control systems minimized downtime and maintenance costs, demonstrating the company’s commitment to quality and innovation in conveyor belt drives for aggregate production.
Superior Industries
At a sand and gravel operation in Colorado, Superior Industries installed a series of portable conveyors and stackers. These systems significantly increased the site’s production capacity, allowing for more efficient material processing and reduced operational costs. The reliability and flexibility of Superior’s equipment have made a substantial impact on the site’s profitability and operational efficiency.
KWS Manufacturing
KWS Manufacturing recently completed a project for a concrete production facility in California. The facility required a robust material handling system to manage the high-volume, abrasive materials used in concrete production. KWS provided a custom-designed screw conveyor system that improved material flow and reduced maintenance downtime by 40%, highlighting their expertise in creating durable and efficient conveyor belt drives for aggregate production.
The top manufacturers in the field of conveyor belt drives for aggregate production, such as West River Conveyors, Superior Industries, and KWS Manufacturing, provide high-quality, innovative solutions tailored to meet the specific needs of the aggregate industry. Their products and services enhance operational efficiency, reliability, and productivity, making them invaluable partners for businesses involved in aggregate production.
Radial Stacker Conveyor: Enhancing Efficiency in Conveyor Belt Drives for Aggregate Production
Functionality
Radial stacker conveyors play a critical role in enhancing the efficiency of conveyor belt drives for aggregate production. These systems are designed to create large piles of aggregate materials efficiently, facilitating better organization and storage on-site. By utilizing a pivoting mechanism, radial stackers can move in a circular arc, distributing material evenly and forming conical stockpiles. This functionality is crucial for optimizing storage space and ensuring the smooth flow of materials in aggregate production facilities.
Benefits
Increased Storage
Radial stacker conveyors significantly increase storage capacity without the need for extensive groundwork or additional infrastructure. By creating high and dense stockpiles, these systems maximize the use of available space. For example, a radial stacker from Superior Industries was implemented at a large quarry in California, enabling the facility to increase its storage capacity by 30%. This improvement allowed for more efficient material handling and reduced the need for frequent transportation of aggregates to off-site storage locations.
Flexibility
The flexibility of radial stacker conveyors in conveyor belt drives for aggregate production is a notable advantage. These conveyors feature adjustable heights and angles, allowing for precise material placement. This adaptability ensures that aggregates are evenly distributed, minimizing material segregation and optimizing the quality of the stockpiles. Companies like McCloskey International provide radial stackers with advanced control systems that enable operators to adjust settings easily, ensuring optimal performance for various material types and production needs.
Mobility
Mobility is another key benefit of radial stacker conveyors. These systems can be easily moved and repositioned as needed, providing unparalleled versatility for dynamic production environments. For instance, a construction company in Texas used a portable radial stacker from Terex to manage materials across multiple project sites. The ability to quickly relocate the conveyor system reduced setup times and improved overall project efficiency, highlighting the importance of mobility in conveyor belt drives for aggregate production.
Use Cases
Mining Operations
In mining operations, radial stacker conveyors are essential for efficiently handling extracted materials. They enable the creation of large, organized stockpiles, facilitating easier access and transport of aggregates to processing plants. A mining site in Nevada implemented a radial stacker from West River Conveyors, enhancing its material handling capabilities and reducing operational costs by minimizing the need for additional handling equipment.
Aggregate Production Facilities
Aggregate production facilities benefit significantly from the use of radial stacker conveyors. These systems streamline the process of stockpiling various aggregate materials, ensuring that production flows smoothly and efficiently. For example, a facility in Ohio incorporated a radial stacker from Superior Industries, which allowed for continuous production without interruptions caused by storage limitations. This implementation resulted in a 25% increase in production efficiency.
Construction Sites
Construction sites often require flexible and efficient material handling solutions. Radial stacker conveyors provide the mobility and adaptability needed to manage aggregates on-site effectively. A large-scale infrastructure project in Florida utilized a McCloskey radial stacker, enabling the efficient movement and storage of materials such as sand, gravel, and crushed stone. This use of advanced conveyor belt drives for aggregate production helped streamline operations and maintain project timelines.
Radial stacker conveyors are vital components in enhancing the efficiency of conveyor belt drives for aggregate production. Their ability to increase storage capacity, provide flexibility in material placement, and offer mobility makes them indispensable for various applications in mining, aggregate production facilities, and construction sites. By incorporating these advanced systems, businesses can optimize their material handling processes, reduce operational costs, and improve overall productivity.
Stacking Conveyors: Integral to Conveyor Belt Drives for Aggregate Production
Role in Aggregate Production

Stacking conveyors are essential components of conveyor belt drives for aggregate production. These systems play a crucial role in organizing and managing aggregate materials on-site, facilitating efficient stockpiling and material handling. Stacking conveyors are designed to transport and stack bulk materials, creating organized piles that optimize storage space and improve accessibility. Their importance in aggregate production cannot be overstated, as they contribute significantly to the overall efficiency and productivity of operations.
Features
Adjustable Lengths
One of the standout features of stacking conveyors used in conveyor belt drives for aggregate production is their adjustable lengths. These conveyors can be extended or shortened to fit specific project needs, offering unparalleled flexibility. For example, a construction company in Utah uses Telestack’s TS 842 radial telescopic conveyor, which can extend up to 42 meters, allowing for high-capacity stockpiling. This adjustability ensures that the conveyor can be tailored to different site layouts and material volumes, maximizing operational efficiency.
Durability
Durability is a critical feature of stacking conveyors in aggregate production. These conveyors are built to withstand harsh conditions and heavy loads, ensuring long-term reliability and minimal downtime. Companies like Masaba Inc. manufacture stacking conveyors with heavy-duty steel frames and components designed to handle the rigors of aggregate production. Their conveyors are equipped with reinforced belts and robust rollers, capable of supporting large volumes of materials without compromising performance.
Automation
Automation options in stacking conveyors enhance the efficiency of conveyor belt drives for aggregate production. Automated stacking and retrieval systems reduce the need for manual intervention, improving safety and productivity. For instance, Superior Industries offers the Telestacker® Conveyor, which features automated stockpile management systems. These systems use sensors and control software to adjust the conveyor’s position and height automatically, optimizing material distribution and minimizing the risk of human error.
Benefits
Space Optimization
Stacking conveyors are instrumental in optimizing space utilization on aggregate production sites. By creating tall, dense piles of materials, these conveyors make the most of available storage areas, reducing the footprint required for stockpiling. A quarry in Arizona implemented a stacking conveyor system from Edge Innovate, which allowed them to increase their storage capacity by 40% without expanding their site. This efficient use of space is crucial for operations with limited land availability or those looking to minimize their environmental impact.
Labor Reduction
Reducing manual labor is another significant benefit of stacking conveyors in conveyor belt drives for aggregate production. Automated and mechanized stacking processes decrease the need for manual handling, lowering labor costs and reducing the risk of injuries. A mining operation in Colorado reported a 25% reduction in labor costs after deploying a series of stacking conveyors from McCloskey International. The conveyors streamlined the material handling process, enabling the workforce to focus on other critical tasks.
Improved Workflow
Stacking conveyors improve workflow by streamlining material handling processes. These conveyors ensure a continuous flow of materials from extraction to stockpiling, minimizing interruptions and bottlenecks. For example, a sand and gravel production facility in Texas integrated a Terex MPS stacking conveyor into their operation, resulting in a 30% increase in processing efficiency. The conveyor system facilitated a smoother transition of materials through different stages of production, enhancing overall productivity.
Stacking conveyors are integral to the efficiency and effectiveness of conveyor belt drives for aggregate production. Their adjustable lengths, durability, and automation capabilities make them versatile tools for managing and organizing bulk materials. By optimizing space, reducing labor requirements, and improving workflow, stacking conveyors contribute significantly to the success of aggregate production operations. Companies that invest in high-quality stacking conveyors can expect enhanced productivity, reduced operational costs, and improved site management.
FAQa about Conveyor Belt Drives For Aggregate Production
An aggregate conveyor is a type of machinery used in the construction and mining industries to transport bulk materials such as sand, gravel, crushed stone, and other aggregate materials. These conveyors are essential for efficient material handling in aggregate production, ensuring that large volumes of material are moved quickly and safely. The conveyor belts are usually made from durable materials designed to withstand the heavy loads and abrasive nature of the aggregate. Aggregate conveyors come in various configurations, including fixed, portable, radial stacking, and overland conveyors, to meet the specific needs of different production sites. In the context of conveyor belt drives for aggregate production, these systems are often equipped with powerful drive mechanisms to ensure continuous operation under challenging conditions. By automating the transportation of aggregates, these conveyors help to reduce labor costs, increase production efficiency, and minimize downtime, making them a crucial component in modern aggregate production facilities.
In conveyor systems, especially those used in aggregate production, the most commonly used gear drives are helical, bevel, and worm gear drives. Helical gear drives are favored for their efficiency and quiet operation, making them suitable for high-speed applications. Bevel gear drives, with their ability to handle high torque and provide precise control, are often used in heavy-duty applications where the direction of the shaft needs to change. Worm gear drives, known for their compact design and high torque output, are used in applications requiring significant speed reduction and where space constraints are a concern. In conveyor belt drives for aggregate production, selecting the appropriate gear drive is crucial for optimizing performance and ensuring reliability. These gear drives are typically paired with electric motors to provide the necessary power for moving heavy loads of aggregate materials. The choice of gear drive depends on factors such as the conveyor’s speed, load capacity, and operational environment.
Variable Frequency Drives (VFDs) play a critical role in conveyor belt drives for aggregate production. A VFD controls the speed and torque of the electric motors driving the conveyor belts, allowing for precise adjustment of the conveyor’s speed to match the production requirements. This capability is essential in aggregate production, where material flow rates can vary significantly. By using VFDs, operators can optimize the conveyor speed to enhance efficiency, reduce energy consumption, and minimize wear and tear on the equipment. Additionally, VFDs provide smooth start-up and shutdown of conveyor belts, reducing the mechanical stress on the system and preventing potential damage. This smooth operation is particularly important in handling heavy and abrasive aggregate materials. VFDs also enable better control of the material flow, improving the overall production process and reducing the risk of blockages or spillage. In summary, the use of VFDs in conveyor belt drives for aggregate production enhances operational flexibility, efficiency, and longevity of the equipment.
In aggregate production, conveyor belts are driven using various mechanisms to ensure the efficient transportation of materials. The primary drive system involves electric motors connected to gear drives, which provide the necessary torque and speed to move the belts. These motors can be directly coupled to the drive pulley or connected via gearboxes that adjust the speed and torque output to suit the conveyor’s operational requirements. Helical, bevel, and worm gear drives are commonly used in these systems due to their efficiency and ability to handle high loads. Additionally, Variable Frequency Drives (VFDs) are often employed to control the motor speed and torque, allowing for precise adjustment based on the material flow and production demands. In some cases, hydraulic drives may be used, particularly in portable or mobile conveyor systems, providing flexibility and ease of movement. The drive systems are designed to handle the heavy loads and abrasive nature of aggregate materials, ensuring continuous and reliable operation. Proper maintenance of the drive components is essential to prevent downtime and extend the lifespan of the conveyor belts in aggregate production.
The drive system for a conveyor belt consists of several components that work together to move the belt and transport materials. The primary components of a conveyor belt drive system include the drive pulley, motor, gearbox, and coupling.
Drive Pulley: The drive pulley is a cylindrical drum that transmits power to the conveyor belt, causing it to move. It is typically located at one end of the conveyor system and is connected to the motor.
Motor: The motor provides the necessary power to turn the drive pulley. Motors can vary in size and type, depending on the requirements of the conveyor system.
Gearbox: The gearbox is used to reduce the speed of the motor to a suitable level for driving the conveyor belt. It increases the torque, enabling the belt to move heavier loads.
Coupling: The coupling connects the motor and gearbox to the drive pulley, ensuring smooth power transmission and reducing the impact of misalignment between the components.
This drive system is essential for ensuring efficient and reliable operation of the conveyor belt, enabling it to handle various materials in different industrial applications.
A Variable Frequency Drive (VFD) is used in conveyor belt systems to control the speed and torque of the motor driving the belt. VFDs offer several advantages in conveyor belt operations:
Speed Control: VFDs allow for precise control of the conveyor belt speed. This is particularly useful in applications where different speeds are required for different materials or processes. Operators can adjust the speed to match production requirements, optimizing efficiency and throughput.
Energy Efficiency: By controlling the motor speed, VFDs can reduce energy consumption. Running the motor at lower speeds when full power is not required can lead to significant energy savings and lower operating costs.
Soft Start and Stop: VFDs enable smooth acceleration and deceleration of the conveyor belt, reducing mechanical stress on the system. This helps prevent sudden jerks and mechanical wear, extending the lifespan of the belt and associated components.
Torque Control: VFDs provide precise torque control, ensuring the conveyor belt can handle varying loads without slipping or stalling. This is crucial for maintaining consistent material flow and preventing damage to the belt or drive system.
Enhanced Control and Monitoring: Modern VFDs come with advanced control and monitoring features, allowing operators to track performance metrics, detect faults, and implement automated responses to changing conditions.
Overall, the use of VFDs in conveyor belt systems enhances operational efficiency, reduces energy consumption, and improves the reliability and longevity of the equipment.
Last Updated on June 20, 2024 by Jordan Smith
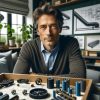
Jordan Smith, a seasoned professional with over 20 years of experience in the conveyor system industry. Jordan’s expertise lies in providing comprehensive solutions for conveyor rollers, belts, and accessories, catering to a wide range of industrial needs. From initial design and configuration to installation and meticulous troubleshooting, Jordan is adept at handling all aspects of conveyor system management. Whether you’re looking to upgrade your production line with efficient conveyor belts, require custom conveyor rollers for specific operations, or need expert advice on selecting the right conveyor accessories for your facility, Jordan is your reliable consultant. For any inquiries or assistance with conveyor system optimization, Jordan is available to share his wealth of knowledge and experience. Feel free to reach out at any time for professional guidance on all matters related to conveyor rollers, belts, and accessories.