How to Change A Conveyor Belt and Troubleshoot
This guide aims to provide a detailed, step-by-step process on how to change a conveyor belt, addressing common questions, necessary tools, and best practices. Proper conveyor belt replacement is crucial for maintaining efficiency, reducing downtime, and ensuring the longevity of the conveyor system. Whether you’re searching for how to change a conveyor belt or need answers about replacement services near you, this guide covers it all. From essential tools and preparation to professional tips and troubleshooting, learn how to change a conveyor belt effectively to keep your operations running smoothly and efficiently.
How to Change a Conveyor Belt:Tools and Materials Needed
Safety Equipment
- Safety gloves
- Safety goggles
- Hard hat
- Ear protection (if necessary)
- Lockout/tagout kit
Hand Tools
- Wrench set (metric and imperial)
- Screwdrivers (flathead and Phillips)
- Allen keys/hex keys
- Pliers (needle-nose and standard)
- Utility knife or belt cutter
- Hammer and mallet
- Adjustable wrench
Measuring and Marking Tools
- Measuring tape
- Chalk or marking tool
- Square ruler or straight edge
Belt Installation Tools
- Belt tensioner
- Belt clamps or vice grips
- Splicing kit (if the belt needs to be joined)
- Vulcanizing press (for hot splicing, if applicable)
- Belt skiver (if needed for preparation)
Lubricants and Cleaning Supplies
- Degreaser or cleaning solvent
- Rags or cleaning cloths
- Lubricating oil or spray
- Brushes (wire and soft-bristle)
Replacement Parts
- New conveyor belt (ensure it matches the required specifications)
- Replacement bolts, nuts, and washers (if any are damaged or worn)
Miscellaneous
- Flashlight or portable work light
- Extension cords (if needed)
- Toolbox or tool bag for organization
By having these tools and materials on hand, you will be well-prepared to change the conveyor belt efficiently and safely.
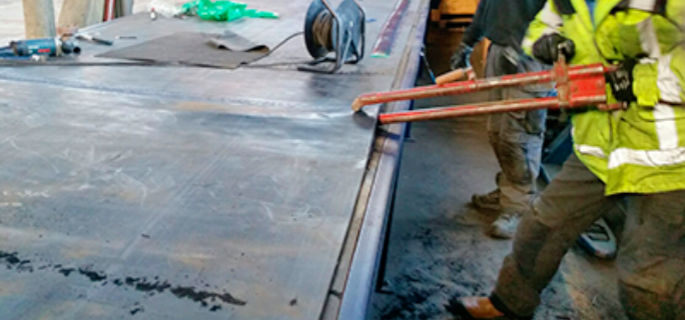
How to Change a Conveyor Belt:Step by Step
- Safety First
- Turn off and disconnect the power supply to the conveyor system.
- Lockout/tagout the conveyor to prevent accidental start-up.
- Wear appropriate personal protective equipment (PPE) such as gloves and safety goggles.
- Release Tension
- Locate the tensioning mechanism (usually a tensioning pulley or screw).
- Use the wrench set to loosen the tension, making it easier to remove the old belt.
- Ensure all tension is released to prevent injury when removing the belt.
- Remove the Old Belt
- Carefully slide the old belt off the conveyor system. This may require unbolting or unclipping certain parts of the conveyor.
- Inspect the conveyor system for any damage or wear that might need repair before installing the new belt.
- Clean the Conveyor System
- Use cleaning supplies to remove any dirt, debris, or residue from the conveyor system.
- Ensure the conveyor rollers, pulleys, and frame are clean and in good condition.
- Measure and Prepare the New Belt
- Measure the new conveyor belt to ensure it matches the required length and width.
- If necessary, cut the belt to the appropriate size using a sharp utility knife or belt cutter.
- Mark the belt where it will be joined if it requires splicing.
- Install the New Belt
- Position the new belt on the conveyor system, ensuring it is aligned properly with the rollers and pulleys.
- If the belt requires splicing, follow the manufacturer’s instructions to join the ends securely.
- Tension the Belt
- Use the belt tensioner to apply the appropriate amount of tension to the new belt.
- Ensure the belt is tight enough to operate smoothly without slipping but not so tight that it causes excessive wear on the components.
- Check Alignment
- Check the alignment of the belt to ensure it runs straight on the conveyor.
- Adjust the tracking if necessary by modifying the position of the rollers or using tracking screws.
- Test the Conveyor
- Reconnect the power supply and start the conveyor system.
- Observe the belt operation to ensure it runs smoothly and without issues.
- Listen for any unusual noises and check for proper tracking.
- Final Adjustments
- Make any necessary adjustments to the tension and alignment based on the test run.
- Re-tighten any bolts or screws that were loosened during the process.
- Document the Maintenance
- Record the maintenance work in your log, noting the date, the replacement belt used, and any adjustments made.
By following these steps, you can ensure that your conveyor belt is replaced safely and effectively, minimizing downtime and maintaining productivity.
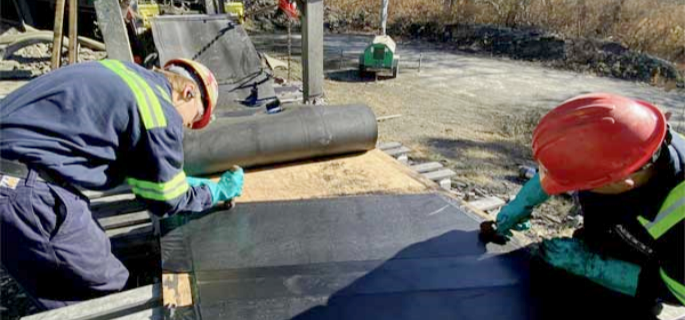
How To Troubleshoot a New Conveyor Belt
Troubleshooting a new conveyor belt involves identifying and resolving any issues that may arise during its initial operation. Here is a step-by-step guide to help you troubleshoot a new conveyor belt:
1. Visual Inspection
- Check for Alignment: Ensure the belt is properly aligned with the conveyor frame and rollers.
- Inspect for Damage: Look for any signs of damage or defects on the belt surface.
- Verify Installation: Confirm that all components, such as rollers and pulleys, are correctly installed and secured.
2. Check Tension
- Proper Tension: Ensure the belt is neither too tight nor too loose. Use a tension gauge if available.
- Adjust Tension: If the belt is too tight, it may cause excessive wear or breakage. If too loose, it may slip. Adjust the tension accordingly.
3. Test Run
- Initial Start-Up: Run the conveyor belt at a slow speed initially to observe its operation.
- Listen for Unusual Noises: Any unusual sounds may indicate misalignment, improper tension, or other mechanical issues.
4. Tracking Issues
- Check Tracking: Ensure the belt runs straight and does not drift to one side.
- Adjust Rollers/Pulleys: Adjust the position of the rollers or pulleys to correct any tracking issues.
- Clean Components: Dirt or debris on the rollers can cause tracking problems. Clean the rollers and other components.
5. Belt Slippage
- Inspect Drive Pulley: Ensure the drive pulley is clean and free of any residue.
- Check Tension: Verify that the belt tension is correct. Adjust if necessary.
- Belt Material: Ensure the belt material is suitable for the conveyed material and conditions.
6. Check for Obstructions
- Clear Pathway: Ensure there are no obstructions on the conveyor that might impede belt movement.
- Remove Debris: Clear any debris or foreign objects that might have fallen onto the conveyor.
7. Monitor Load
- Check Load Capacity: Ensure the belt is not overloaded beyond its capacity.
- Even Distribution: Verify that the load is evenly distributed across the belt.
8. Inspect Belt Joints/Splices
- Check Splices: Ensure any belt joints or splices are properly executed and secure.
- Look for Weak Points: Inspect splices for signs of wear or separation.
9. Lubrication
- Lubricate Bearings: Ensure that all bearings and moving parts are adequately lubricated.
- Avoid Belt Contamination: Be cautious not to contaminate the belt with lubricants.
10. Temperature and Environmental Conditions
- Check for Extreme Conditions: Ensure the conveyor belt is suitable for the operating temperature and environmental conditions.
- Adjust if Necessary: Make adjustments or provide protective measures if the belt is exposed to extreme temperatures or harsh environments.
11. Documentation and Maintenance Records
- Keep Records: Document any issues and the steps taken to resolve them.
- Schedule Regular Maintenance: Plan regular inspections and maintenance to prevent future problems.
By following these troubleshooting steps, you can identify and resolve issues with your new conveyor belt, ensuring its smooth and efficient operation.
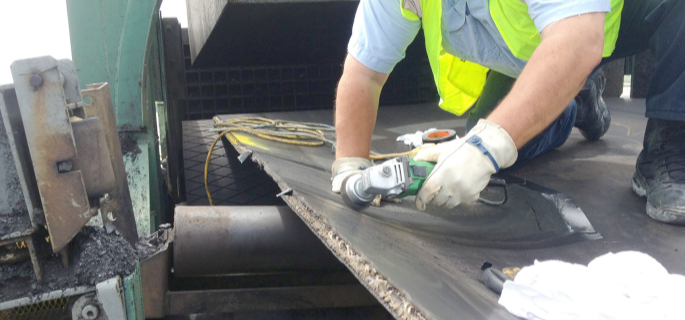
How to Change a Conveyor Belt: Proper Storage Techniques When Not in Use
Proper storage of conveyor belts when they are not in use is crucial to maintaining their condition and extending their lifespan. Here are some techniques and best practices for storing conveyor belts:
1. Clean the Belt
- Remove Debris: Clean off any dirt, dust, or material residues from the belt surface.
- Dry the Belt: Ensure the belt is completely dry before storage to prevent mold and mildew.
2. Choose the Right Location
- Dry Environment: Store belts in a dry, cool environment to prevent moisture damage.
- Avoid Direct Sunlight: Keep belts away from direct sunlight and UV rays, which can degrade the material.
- Temperature Control: Ideal storage temperatures range between 50°F (10°C) and 70°F (21°C). Avoid extreme temperatures.
3. Proper Positioning
- Horizontal Storage: Store belts flat in a horizontal position to avoid warping or bending.
- Avoid Hanging: Do not hang belts as this can cause distortion and stretching.
- Use Pallets or Shelves: Place belts on pallets or shelves to keep them off the ground and away from contaminants.
4. Roll or Coil Storage
- Roll Properly: If storing belts in a rolled or coiled position, ensure they are rolled evenly and not too tightly to avoid creases or bends.
- Stand Vertically: If possible, store rolled belts standing on their edges to prevent flattening.
5. Protection from Contaminants
- Cover Belts: Use protective covers or tarps to shield belts from dust, dirt, and other contaminants.
- Avoid Chemicals: Store belts away from chemicals, solvents, oils, and other substances that could cause damage.
6. Label and Record
- Label Belts: Clearly label stored belts with information such as size, type, and date of storage.
- Inventory Records: Maintain an inventory record to track storage times and conditions, ensuring that older belts are used first.
7. Regular Inspections
- Periodic Checks: Conduct regular inspections to ensure belts remain in good condition during storage.
- Look for Damage: Check for signs of damage, such as cracks, tears, or deformities, and address any issues promptly.
8. Handling with Care
- Use Appropriate Tools: Use proper tools and equipment when moving or handling stored belts to avoid damage.
- Avoid Dropping: Handle belts carefully to prevent dropping or mishandling, which can cause structural damage.
9. Special Considerations
- Avoid Overlapping: If storing multiple belts, avoid stacking them directly on top of each other. Use separators if necessary.
- Controlled Access: Limit access to the storage area to trained personnel to reduce the risk of accidental damage.
By following these proper storage techniques, you can ensure that your conveyor belts remain in optimal condition, ready for use when needed, and maintain their longevity.
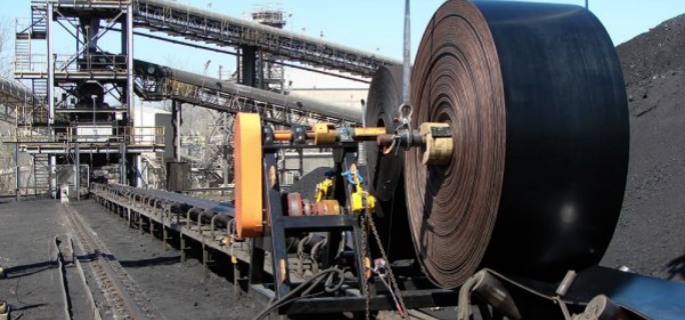
How to Change a Conveyor Belt: Conveyor Belt Replacement Near Me
Finding Local Services
How to locate conveyor belt replacement services
When searching for how to change conveyor belt services near you, it is essential to find reliable providers who can ensure a smooth and efficient replacement process. Start by conducting an online search using keywords like “conveyor belt replacement services near me” or “industrial conveyor belt repair.” Websites like Yelp, Angie’s List, and Google Reviews can provide valuable insights into local companies.
Additionally, industry-specific forums and networks can offer recommendations for reputable service providers. For instance, you can check with professional organizations like the Conveyor Equipment Manufacturers Association (CEMA) for a list of certified companies in your area. Networking with other businesses in your industry may also yield useful referrals.
Criteria for selecting a service provider
Selecting the right service provider is crucial for ensuring a successful conveyor belt replacement. Consider the following factors when evaluating potential providers:
- Experience: Look for companies with a proven track record in conveyor belt replacement. Providers like Fluent Conveyors have extensive experience in handling various types of conveyor systems and can offer expert advice tailored to your needs.
- Reviews and Testimonials: Customer reviews and testimonials can provide insights into the quality of service a company offers. Positive feedback from previous clients is a good indicator of reliability and professionalism.
- Certifications: Ensure that the service provider holds relevant certifications and complies with industry standards. Certifications from organizations like CEMA or the International Organization for Standardization (ISO) demonstrate a commitment to quality and safety.
- Response Time: In industries where downtime can be costly, a provider’s ability to respond quickly to service requests is critical. Companies like Conveyor Solutions Inc. pride themselves on rapid response times and efficient service delivery.
- Cost: While cost should not be the sole determining factor, it is essential to get detailed quotes and compare prices from multiple providers. Ensure that the quoted price includes all necessary services, such as inspection, removal, installation, and post-installation checks.
DIY vs. Professional Replacement
Advantages of professional replacement
Hiring professionals to handle how to change conveyor belt offers several advantages:
- Expertise: Professional technicians have the knowledge and experience to replace conveyor belts efficiently and correctly. This reduces the risk of errors that could lead to operational issues.
- Safety: Trained professionals follow stringent safety protocols to prevent accidents during the replacement process. This is particularly important in industrial settings where heavy machinery is involved.
- Efficiency: Professionals can complete the replacement process faster than an in-house team with limited experience, minimizing downtime and keeping production on schedule.
- Warranty: Many professional services offer warranties on their work, providing peace of mind and protection against potential future issues.
When to consider DIY replacement
While professional replacement is often the best option, there are scenarios where DIY replacement may be appropriate:
- Simple Repairs: For minor repairs, such as fixing a small tear or replacing a section of the belt, in-house maintenance teams can handle the task using a conveyor belt repair kit.
- Cost-Saving: Small businesses with limited budgets might opt for DIY replacement to save on service fees. However, it is crucial to ensure that the team has the necessary skills and tools to perform the replacement safely and effectively.
- Availability of Tools: If your facility is equipped with the required tools and your staff has received proper training, DIY replacement can be a feasible option. Companies like Flexco offer detailed guides and training resources to support DIY efforts.
Steps for On-Site Replacement
Preparation
Proper preparation is key to a successful conveyor belt replacement. Begin by gathering all necessary tools and parts, including the new belt, belt cutter, splicing kit, tensioning tools, and safety gear. Ensure that the work area is clean and free of obstructions.
Next, conduct a thorough inspection of the conveyor system to identify any additional issues that may need to be addressed during the replacement process. This includes checking for worn-out rollers, misaligned pulleys, and other potential problems.
Execution
Follow these steps for the actual replacement process:
- Deactivating the System: Safely shut down the conveyor system and follow lockout-tagout (LOTO) procedures to prevent accidental startup.
- Removing the Old Belt: Unlace or cut the old belt and carefully remove it from the system. Dispose of the old belt according to your facility’s waste management protocols.
- Installing the New Belt: Position the new belt on the conveyor, ensuring it is properly aligned. Use the splicing kit to join the ends of the belt securely.
- Tensioning the Belt: Adjust the tensioning devices to ensure the belt is tight enough to avoid slippage but not so tight that it causes excessive wear on the components.
Final Checks
After installing and tensioning the new belt, conduct a series of final checks to ensure everything is in order:
- Alignment: Verify that the belt is correctly aligned with the pulleys and rollers to prevent tracking issues.
- Tension: Double-check the tension to ensure it is within the recommended range for the specific belt type and application.
- Test Run: Perform a test run of the conveyor system with a light load to confirm that the belt operates smoothly and without issues.
Regular maintenance and prompt replacement of worn components are essential for maintaining the efficiency and longevity of your conveyor system. By following this comprehensive guide on how to change conveyor belt, you can ensure minimal downtime and optimal performance for your industrial operations.
How to Change a Conveyor Belt: Conveyor Belt Interview Questions
Key Interview Questions
Common Technical Questions
When interviewing for a position that involves knowing how to change conveyor belt, employers often focus on technical questions to assess your understanding of conveyor systems, maintenance, and troubleshooting. Here are some common technical questions you might encounter:
- Can you describe the steps involved in how to change a conveyor belt?
- This question evaluates your familiarity with the replacement process, including preparation, removal of the old belt, installation of the new belt, tensioning, and alignment.
- What are the most common issues you have faced when changing a conveyor belt, and how did you resolve them?
- Interviewers look for specific examples that demonstrate your problem-solving skills and ability to troubleshoot common issues like misalignment, improper tension, and material jams.
- What tools and equipment are essential for changing a conveyor belt?
- Your answer should include a detailed list of tools such as belt cutters, splicing kits, tensioning devices, and safety gear, explaining their importance in the replacement process.
- How do you ensure the proper tension and alignment of a conveyor belt after installation?
- This question tests your knowledge of post-installation checks and adjustments necessary to ensure efficient belt operation and prevent premature wear.
Behavioral Questions
In addition to technical skills, employers are interested in your behavioral competencies, such as problem-solving, teamwork, and handling emergency situations. Here are some behavioral questions you might face:
- Describe a time when you had to solve a complex problem related to conveyor belt maintenance.Provide a specific example, detailing the problem, the steps you took to resolve it, and the outcome. This showcases your analytical and problem-solving abilities.
- How do you prioritize tasks when multiple conveyor systems need maintenance at the same time?
- Discuss your approach to prioritizing tasks based on factors like urgency, impact on production, and safety considerations.
- Can you give an example of how you worked as part of a team to complete a conveyor belt replacement?
- Highlight your teamwork skills, including communication, collaboration, and coordination with other team members to achieve a common goal.
- How do you handle emergency situations, such as a conveyor belt malfunction during peak production hours?
- Explain your approach to quickly diagnosing the problem, implementing immediate fixes, and ensuring minimal disruption to operations.
Preparing for the Interview
Researching the Company
Before attending an interview, it is crucial to research the company thoroughly. Understanding the specific conveyor systems they use will help you tailor your responses and demonstrate your relevance to the role. For instance, if you are interviewing with a company like FedEx, knowing that they use high-speed sortation systems will allow you to discuss your experience with similar systems and the particular challenges they present.
Practice Scenarios
Preparing for practical scenarios can significantly boost your confidence and performance during the interview. Conduct mock interviews with a colleague or mentor, focusing on both technical and behavioral questions. Additionally, consider practical problem-solving exercises related to how to change a conveyor belt, such as diagnosing a belt misalignment issue or selecting the appropriate splicing method for different belt materials.
Tips for Success
Presenting Relevant Experience
During the interview, make sure to highlight your past work experience with conveyor systems. Discuss specific projects or tasks where you successfully changed conveyor belts, mentioning the types of belts and systems you worked on. For example, you might say, “At ABC Manufacturing, I led a team in changing over 50 conveyor belts annually, including both flat and modular belts, ensuring minimal downtime and maximum efficiency.”
Demonstrating Knowledge
Employers are looking for candidates who can demonstrate a deep understanding of the techniques and tools used in conveyor belt replacement. Discuss specific methods you have used, such as vulcanizing or mechanical splicing, and explain why you chose those methods for particular situations. Mentioning industry-standard tools and brands, like Flexco’s Alligator splicing system, can add credibility to your responses.
By thoroughly preparing for both the technical and behavioral aspects of the interview and effectively demonstrating your experience and knowledge, you can confidently answer questions related to how to change a conveyor belt and showcase your suitability for the role.
How to Change a Conveyor Belt: Conveyor Belt Quiz
Understanding the Basics
Purpose of the quiz
A conveyor belt quiz is designed to assess your knowledge and understanding of conveyor belt systems and the procedures for replacing them. This type of quiz is essential for anyone involved in maintenance and operational roles, ensuring they are well-versed in how to change a conveyor belt efficiently and safely. Companies like Flexco and Sparks Belting often use quizzes as part of their training programs to ensure that their employees can handle various aspects of conveyor belt maintenance.
Sample questions
To prepare for a conveyor belt quiz, it’s useful to familiarize yourself with typical questions you might encounter. These questions often cover the following areas:
- Types of Conveyor Belts:
- What are the differences between flat belts, modular belts, and cleated belts?
- When would you use a wire mesh belt over a traditional rubber belt?
- Common Issues:
- What are the most frequent causes of conveyor belt misalignment?
- How do you identify and troubleshoot issues related to belt slippage?
- Replacement Steps:
- Describe the step-by-step process for how to change a conveyor belt.
- What tools are necessary for properly splicing a conveyor belt?
Sample Question: “What is the primary reason for adjusting the tension on a conveyor belt after installation?” This question tests your understanding of the critical maintenance steps involved in ensuring the longevity and efficiency of the conveyor system.
Preparing for the Quiz
Study materials
Effective preparation for a quiz on how to change a conveyor belt involves using a variety of study materials. Manuals and online tutorials are excellent resources. For example, Flexco offers detailed guides and instructional videos on their website, covering everything from belt selection to installation techniques. Additionally, industry publications such as “Bulk Solids Handling” provide in-depth articles on conveyor belt maintenance and best practices.
- Manuals: These are often provided by conveyor belt manufacturers and include detailed instructions on installation and maintenance procedures. Reading these manuals helps you understand the specific requirements and recommendations for different belt types.
- Online Tutorials: Websites like YouTube and professional training platforms offer videos demonstrating how to change a conveyor belt. These visual aids can be particularly helpful in grasping complex techniques and procedures.
Practice quizzes
To enhance your readiness, taking practice quizzes can be very beneficial. Online platforms such as Quizlet and industry-specific training sites offer mock tests that simulate the actual quiz environment. These practice quizzes cover a range of topics, including belt types, troubleshooting methods, and replacement steps.
- Online Platforms: Websites like Quizlet allow you to create and take custom quizzes based on the study materials. These platforms provide a convenient way to test your knowledge and identify areas where you need further review.
- Mock Tests: Some industry training programs include mock tests as part of their curriculum. These tests are designed to mimic the format and content of actual quizzes, helping you become familiar with the types of questions you will face.
Benefits of Taking the Quiz
Knowledge assessment
Taking a quiz on how to change a conveyor belt provides a clear assessment of your knowledge and skills. It helps identify areas of strength and improvement, ensuring that you are well-prepared for practical applications. For instance, if you perform well on questions related to belt tensioning but struggle with splicing techniques, you know where to focus your additional studies and practice.
- Self-Assessment: Quizzes provide immediate feedback on your understanding of the material. This allows you to gauge your proficiency and identify any gaps in your knowledge.
- Focused Improvement: By highlighting specific areas where you need improvement, quizzes help you tailor your study efforts more effectively. For example, if you consistently miss questions about belt types, you can dedicate more time to reviewing that topic.
Certification
Many organizations offer certification programs for conveyor belt maintenance. Successfully passing a quiz or series of quizzes is often a requirement for obtaining these certifications. Certification not only validates your skills but also enhances your credibility and career prospects. For example, the Conveyor Equipment Manufacturers Association (CEMA) offers certification programs that are recognized throughout the industry.
- Professional Recognition: Earning a certification demonstrates your expertise and commitment to professional development. This can lead to greater job opportunities and career advancement.
- Increased Credibility: Certified professionals are often preferred by employers because they have proven their ability to perform critical maintenance tasks. This can give you a competitive edge in the job market.
By taking a comprehensive quiz on how to change a conveyor belt, you can ensure that you are fully prepared to handle this essential maintenance task effectively and safely. Regularly testing your knowledge through quizzes and practical exercises helps you stay updated on best practices and enhances your proficiency in maintaining conveyor systems.
How to Change a Conveyor Belt: Conveyor Belt Repair Kit
Importance of a Repair Kit
Why a repair kit is essential
A conveyor belt repair kit is an indispensable tool for anyone responsible for maintaining conveyor systems. Knowing how to change a conveyor belt is crucial, but having a repair kit on hand allows for quick fixes and emergency repairs, significantly reducing downtime and extending the life of the belt. For instance, during peak operational hours at a facility like Walmart’s distribution centers, a damaged conveyor belt can halt the entire process, leading to delays and increased costs. Having a repair kit ensures that minor damages can be swiftly addressed, keeping the system running smoothly.
Repair kits are essential because they provide all the necessary tools and materials in one convenient package. This means that maintenance teams can respond immediately to issues without wasting time gathering supplies. Quick fixes not only save time but also prevent small problems from escalating into major breakdowns. Additionally, regularly using a repair kit to address wear and tear can significantly extend the lifespan of conveyor belts, providing cost savings over time.
Components of a Repair Kit
Common tools and materials
A comprehensive conveyor belt repair kit typically includes a variety of tools and materials designed to handle different types of damage. Key components often found in these kits include:
- Fasteners: These are used to reattach sections of a torn belt. Types of fasteners might include metal clips or plastic rivets, depending on the belt material.
- Patches: Patches are essential for covering holes and small tears. They are usually made from the same material as the conveyor belt to ensure compatibility.
- Adhesives: Specialized adhesives are used to bond patches to the belt securely. They must be durable and able to withstand the operational stresses of the conveyor system.
- Cutting Tools: A belt cutter is necessary for trimming damaged sections and cutting patches to size.
- Splicing Tools: These tools help join the ends of the belt together. They may include splicing clamps, presses, and guides.
- Tensioning Devices: These are used to ensure the repaired belt is properly tensioned to avoid slippage and misalignment.
For example, a repair kit from Flexco might include their patented Alligator Staple Fasteners, which provide a strong and durable hold for most belt types. These kits are designed to be user-friendly, allowing maintenance personnel to quickly and effectively perform repairs.
How to Use a Repair Kit
Step-by-step guide
Using a conveyor belt repair kit requires a systematic approach to ensure effective and long-lasting repairs. Here’s a step-by-step guide on how to change a conveyor belt using a repair kit:
- Identifying Damage: First, inspect the belt to determine the extent and type of damage. Look for tears, holes, and worn-out sections.
- Preparing the Belt: Clean the damaged area thoroughly to remove dirt, debris, and any loose material. This ensures better adhesion and a stronger repair.
- Applying Repairs: Depending on the damage, choose the appropriate tools from the kit. For small tears, use patches and adhesives. For larger rips, employ splicing techniques using fasteners and splicing tools.
- Ensuring Durability: After applying the repair, allow sufficient time for adhesives to cure, ensuring the repair is strong and durable. Use tensioning devices to adjust the belt tension appropriately.
Tips for effective repairs
- Clean the Belt Thoroughly: Ensuring the repair area is free from contaminants will result in a stronger bond.
- Follow Manufacturer Instructions: Use the repair kit components as instructed by the manufacturer to achieve the best results.
- Test the Repair: After the repair is complete, run the conveyor system under light load to test the integrity of the repair before resuming full operations.
Choosing the Right Repair Kit
Factors to consider
When selecting a conveyor belt repair kit, it’s important to consider several factors to ensure compatibility and effectiveness:
- Belt Type: Different belts require different repair materials. Ensure the kit is suitable for the specific type of belt used in your system, whether it’s rubber, PVC, or metal mesh.
- Material Compatibility: The repair kit components should be compatible with the belt material to provide a strong and durable repair. For instance, adhesives should be able to bond effectively with the belt material.
- Quality of the Repair Kit: High-quality kits, such as those from Flexco or Sparks Belting, are designed to provide reliable repairs that can withstand operational stresses. Look for kits with good reviews and those recommended by industry professionals.
For example, a high-quality repair kit from Sparks Belting includes robust metal fasteners and durable adhesive that are compatible with a variety of belt materials. This ensures that repairs are not only quick but also long-lasting, maintaining the efficiency and reliability of the conveyor system.
By understanding how to change a conveyor belt and utilizing a comprehensive repair kit, maintenance teams can effectively manage and extend the life of their conveyor systems, ensuring minimal disruption and optimal performance in their operations.
How to Change a Conveyor Belt: Which of the Following is Not of Importance When a Conveyor is Designed
Design Considerations
Critical factors
When designing a conveyor system, several critical factors must be considered to ensure the system operates efficiently and reliably. Understanding these factors is also essential for knowing how to change a conveyor belt properly.
- Load Capacity: One of the most important considerations is the load capacity of the conveyor system. This includes understanding the maximum weight the belt will carry and the distribution of this weight. Overloading a conveyor belt can lead to premature wear and potential failure, making it crucial to design for the heaviest expected loads. For instance, a logistics company like FedEx must ensure their conveyor belts can handle the heavy packages processed daily without failure.
- Belt Material: The material of the conveyor belt must be chosen based on the specific application. Different materials are suited for different tasks, such as rubber belts for heavy-duty industrial applications or food-grade belts for sanitary environments. For example, in a meat processing plant, a stainless steel mesh belt might be used because it is easy to clean and resistant to bacteria.
- Environmental Conditions: The environment in which the conveyor operates also plays a significant role in design. Factors such as temperature, humidity, and exposure to chemicals can affect the belt’s performance and lifespan. For example, a conveyor belt used in a freezer warehouse must be designed to remain flexible and functional at sub-zero temperatures.
Non-critical factors
While critical factors ensure the functionality and durability of the conveyor system, non-critical factors generally pertain to aesthetics and features that do not impact performance.
- Aesthetic Appearance: The appearance of the conveyor system, while sometimes important for customer-facing applications, is generally not critical for performance. Industrial environments prioritize functionality over looks.
- Non-functional Features: Features that do not contribute to the operational efficiency or safety of the conveyor system, such as decorative elements, are considered non-critical.
Common Mistakes in Conveyor Design
Overlooking key aspects
Designing a conveyor system involves many considerations, and overlooking key aspects can lead to significant problems down the line. Understanding these pitfalls is vital for those who know how to change a conveyor belt, as proper design can prevent many common issues.
- Neglecting Maintenance Access: One common mistake is failing to design the conveyor system with adequate access for maintenance. If maintenance personnel cannot easily reach and service the conveyor belt, it can lead to increased downtime and more complicated repair procedures. For example, if a belt needs to be replaced and the area is cramped and difficult to access, the process can take much longer and increase the risk of further damage.
- Improper Belt Selection: Choosing the wrong type of belt for the application is another frequent error. Each type of belt has specific properties suited for different tasks. For instance, using a belt designed for light loads in a heavy-duty application will result in frequent breakdowns and higher maintenance costs.
Impact of poor design
Poor design choices can have a significant impact on the efficiency and cost-effectiveness of a conveyor system.
- Increased Downtime: Systems not designed with maintenance in mind can result in longer periods of downtime during repairs or replacements. For example, if a belt requires frequent tension adjustments due to poor initial alignment, operations can be consistently interrupted.
- Higher Maintenance Costs: Poorly designed systems often incur higher maintenance costs due to more frequent repairs and part replacements. For example, using low-quality materials might save money upfront but will lead to higher costs in the long run due to more frequent failures and replacements.
Best Practices in Conveyor Design
Ensuring efficiency and longevity
Applying best practices in conveyor design can significantly enhance the efficiency and longevity of the system, directly impacting how to change a conveyor belt effectively.
- Prioritizing Functionality, Safety, and Ease of Maintenance: Ensuring that the conveyor system is functional and safe is paramount. This includes selecting appropriate materials, designing for load capacity, and providing easy access for maintenance. For instance, a well-designed system by a company like Siemens incorporates user-friendly features that allow for quick and safe belt changes.
- Regular Reviews and Updates: Continuously reviewing and updating the design based on operational feedback ensures the system remains efficient and effective. This proactive approach can help identify potential issues before they become major problems. For example, regularly scheduled inspections can reveal wear and tear on belts, prompting timely replacements and adjustments.
By incorporating these best practices, designers can create conveyor systems that are easier to maintain, reducing the frequency and complexity of how to change a conveyor belt, ultimately ensuring smoother and more reliable operations.
How to Change a Conveyor Belt: Comprehensive Questions and Answers PDF
Understanding the Basics
What is a conveyor belt?
A conveyor belt is a continuous loop of material that rotates around two or more pulleys, functioning as an essential component in material handling systems. Conveyor belts are used across various industries, including manufacturing, mining, logistics, and food processing, to transport goods and materials efficiently. For example, in Amazon’s fulfillment centers, conveyor belts streamline the sorting and shipping of millions of packages daily, showcasing their pivotal role in industrial operations.
Why do conveyor belts need to be changed?
Conveyor belts need to be replaced due to several common factors:
- Wear and Tear: Over time, constant usage leads to natural degradation of the belt material, reducing its efficiency and reliability.
- Damage: Sharp or heavy objects can cause tears, punctures, or other forms of damage that compromise the belt’s integrity.
- Upgrading Systems: Technological advancements and changes in operational requirements may necessitate the installation of newer, more efficient conveyor belts. For instance, a mining company like Rio Tinto might upgrade to more durable belts to handle increased loads and harsh conditions.
Common Questions and Answers
What tools are needed to change a conveyor belt?
Changing a conveyor belt requires specific tools and equipment to ensure a smooth and efficient replacement process. Essential tools include:
- Belt Cutter: Used to cut the old belt to remove it and trim the new belt to the required length.
- Splicing Kit: Contains materials and tools for joining the ends of the new belt, such as adhesive, fasteners, and clamps.
- Tensioning Tools: Devices like a belt tension gauge ensure the belt is correctly tensioned to prevent slippage and misalignment.
- Lacing Tool: Used to secure the belt ends together with metal or plastic lacing.
- Safety Gear: Gloves, safety glasses, and other protective equipment to ensure worker safety during the replacement process.
How long does it take to change a conveyor belt?
The time required to change a conveyor belt can vary based on several factors:
- Belt Length and Type: Longer and more complex belts, such as those used in mining operations by companies like BHP Billiton, take more time to replace.
- Accessibility: Easier access to the conveyor system can significantly reduce the replacement time.
- Experience and Skill Level: Experienced technicians can complete the task more quickly and efficiently. On average, changing a standard conveyor belt in a factory setting can take anywhere from 4 to 8 hours, including preparation and safety checks.
Detailed PDF Guide
Availability of PDF guides
For those looking to delve deeper into how to change a conveyor belt, comprehensive PDF guides are available from various manufacturers and industry experts. Companies like Flexco and Sparks Belting offer detailed guides that can be downloaded from their websites. These guides typically include step-by-step instructions, diagrams, and troubleshooting tips.
Benefits of a comprehensive PDF guide
Having access to a detailed PDF guide offers numerous benefits:
- Step-by-Step Instructions: Clear, sequential instructions make the replacement process straightforward, even for those less experienced.
- Illustrations and Diagrams: Visual aids help in understanding the complex steps involved in changing a conveyor belt.
- Troubleshooting Tips: Guides often include solutions to common problems encountered during belt replacement, helping to avoid delays and additional costs.
For example, Flexco’s guide on how to change conveyor belt includes detailed illustrations of splicing techniques and tensioning methods, which can be invaluable for ensuring a successful installation. The guide also provides information on the tools required and safety precautions, making it a comprehensive resource for maintenance teams.
Using these resources effectively can greatly enhance the efficiency and safety of conveyor belt replacements, ensuring minimal disruption to operations and extending the lifespan of the equipment.
FAQs about How To Change A Conveyor Belt
Replacing a conveyor belt involves several key steps to ensure a smooth and efficient process. First, shut down the conveyor system and disconnect the power supply to ensure safety. Next, remove any necessary conveyor covers or guards. Loosen the tension on the old belt by adjusting the tensioners. Carefully remove the old belt, taking note of its orientation and positioning. Clean the conveyor frame and rollers to remove any debris. Install the new conveyor belt by positioning it correctly and securing it around the pulleys. Gradually tighten the tensioners, ensuring the belt is properly aligned. Finally, test the conveyor system to ensure the new belt operates smoothly and make any necessary adjustments. Proper maintenance and regular inspections can extend the life of your conveyor belt and minimize downtime.
The time required to replace a conveyor belt can vary depending on the size and complexity of the conveyor system, as well as the experience of the maintenance team. On average, replacing a conveyor belt can take anywhere from a few hours to an entire shift. Simple conveyor systems with accessible components may be completed in under four hours, while more complex systems with intricate configurations may require up to eight hours or more. Preparation, such as having the new belt ready and ensuring all necessary tools and safety equipment are on hand, can significantly reduce downtime. Regular maintenance and prompt attention to minor issues can also help streamline the replacement process.
Installing a conveyor belt involves several crucial steps. First, ensure the conveyor system is powered off and locked out to prevent accidental startup. Clean the conveyor frame and rollers to remove any debris or buildup. Position the new conveyor belt at one end of the conveyor system, making sure it is oriented correctly. Secure the belt around the drive and tail pulleys, then gradually feed it through the system. Tighten the tensioners evenly to ensure the belt is properly aligned. Once the belt is in place, perform a test run to check for proper tracking and tension. Make any necessary adjustments to ensure smooth operation. Regular inspections and maintenance will help extend the life of the conveyor belt and ensure optimal performance.
Fixing a broken conveyor belt requires prompt action to minimize downtime. First, identify the location and cause of the damage. For minor tears or punctures, use a belt repair kit to patch the damaged area. This typically involves cleaning the damaged section, applying a suitable adhesive, and securing the patch with a vulcanizing process or mechanical fasteners. For more extensive damage, you may need to replace the damaged section of the belt or splice in a new piece. Ensure the belt is properly aligned and tensioned before restarting the conveyor system. Regular inspections and preventative maintenance can help identify potential issues before they lead to significant damage, reducing the need for emergency repairs.
The best way to cut a conveyor belt is to use a sharp utility knife or a specialized belt cutter. Mark the cutting line clearly, ensuring it is straight and even. Use a straight edge to guide the knife, applying steady pressure and making multiple passes if necessary. For thicker belts, a saw with a fine-tooth blade or an electric belt cutter can be used. Always wear safety gloves and goggles to protect yourself during the cutting process.
The replacement frequency for conveyor belts depends on several factors, including the type of material conveyed, operating conditions, maintenance practices, and the belt’s quality. Generally, conveyor belts should be inspected regularly, and minor issues should be addressed promptly. On average, a conveyor belt might need to be replaced every three to five years. However, high-wear applications may require more frequent replacements, while well-maintained belts in less demanding conditions can last longer.
Old conveyor belts can be repurposed or recycled in various ways. They can be used as mats for industrial flooring, truck bed liners, or anti-slip surfaces. They can also be cut into smaller pieces for agricultural uses, such as protecting crops or creating pathways. Some belts can be transformed into rubber mulch for playgrounds or landscaping. Additionally, many recycling centers accept old conveyor belts to reclaim and repurpose the rubber and other materials.
Last Updated on August 5, 2024 by Jordan Smith
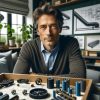
Jordan Smith, a seasoned professional with over 20 years of experience in the conveyor system industry. Jordan’s expertise lies in providing comprehensive solutions for conveyor rollers, belts, and accessories, catering to a wide range of industrial needs. From initial design and configuration to installation and meticulous troubleshooting, Jordan is adept at handling all aspects of conveyor system management. Whether you’re looking to upgrade your production line with efficient conveyor belts, require custom conveyor rollers for specific operations, or need expert advice on selecting the right conveyor accessories for your facility, Jordan is your reliable consultant. For any inquiries or assistance with conveyor system optimization, Jordan is available to share his wealth of knowledge and experience. Feel free to reach out at any time for professional guidance on all matters related to conveyor rollers, belts, and accessories.