Optimizing Operations: The Value of Shuttle Conveyor Systems
A shuttle conveyor system is a versatile and efficient material handling solution used in various industries. These systems are designed to facilitate horizontal transport of materials, making them essential in sectors like manufacturing, mining, and agriculture. The shuttle conveyor system’s ability to move materials efficiently across different points enhances productivity and operational efficiency. Key features include mobility, flexibility, and the capability to handle bulk materials, while benefits range from reduced labor costs to improved safety. Understanding the shuttle conveyor system’s role and advantages is crucial for optimizing industrial processes and achieving higher efficiency in material handling operations.
What is a Shuttle Conveyor System?
Definition and Basic Operation
A shuttle conveyor system is a specialized type of conveyor belt system designed for the efficient horizontal movement of materials within an industrial setting. Unlike fixed conveyors, shuttle conveyors are mounted on trolleys, allowing them to traverse back and forth along a predetermined path. This movement enables the system to transport materials to multiple discharge points, enhancing operational flexibility and efficiency.
The basic operation of shuttle conveyors involves a belt that is stretched across two or more pulleys, forming a closed loop. This belt is powered by a drive pulley, which is usually motorized, creating the necessary friction to move the belt and the materials on it. The shuttle conveyor system is equipped with a reversible belt, allowing it to change direction and transport materials to both ends of the conveyor path. This reversibility is a key feature that distinguishes shuttle conveyors from traditional fixed conveyors.
Differences from Traditional Belt Conveyors
Shuttle conveyors differ significantly from traditional belt conveyors in several ways. Traditional belt conveyors are typically fixed in one location and move materials along a single, linear path. In contrast, a shuttle conveyor system is designed for horizontal movement along a track, which provides greater flexibility in material handling. This mobility allows shuttle conveyors to service multiple discharge points, making them ideal for applications where materials need to be distributed to different locations.
Another major difference is the reversible belt feature of the shuttle conveyor system. Traditional conveyors generally move materials in one direction only. However, the shuttle conveyor’s ability to reverse the belt direction means it can efficiently handle materials coming from or going to multiple directions, thus optimizing the workflow and reducing the need for multiple fixed conveyor systems.
Importance of Horizontal Transport in Material Handling
Horizontal transport is a critical aspect of material handling in many industries, and the shuttle conveyor system excels in this domain. In sectors such as manufacturing, mining, and agriculture, the ability to move materials horizontally is essential for several reasons:
- Space Optimization: Horizontal transport systems like shuttle conveyors make better use of available space. They can navigate around obstacles and transport materials across large areas without the need for extensive vertical movement, which can be more complex and costly.
- Efficiency and Productivity: By enabling the movement of materials to multiple discharge points, shuttle conveyors enhance the efficiency of material handling processes. This flexibility reduces the time and effort required to transport materials manually or with less efficient systems.
- Reduced Labor Costs: The automation capabilities of shuttle conveyor systems mean that fewer human resources are needed to oversee and manage material transport. This reduction in labor requirements leads to cost savings and allows personnel to focus on more value-added tasks.
- Improved Safety: Shuttle conveyor systems can be equipped with various safety features, such as emergency stop systems and sensors, to protect workers and prevent accidents. Automated horizontal transport reduces the need for manual handling, thus minimizing the risk of injuries.
- Versatility: The shuttle conveyor system is highly versatile and can be customized to meet specific operational requirements. Whether handling bulk materials, pallets, or smaller items, the system can be adjusted in terms of belt speed, direction, and discharge points to suit different applications.
Applications in Various Industries
Shuttle conveyor systems find applications in a wide range of industries due to their versatility and efficiency:
- Manufacturing: In manufacturing plants, shuttle conveyors are used to transport raw materials, components, and finished products between different stages of production. This ensures a smooth flow of materials and minimizes downtime.
- Mining: Shuttle conveyor systems are essential in mining operations for the horizontal movement of ores and other bulk materials. They help in distributing materials to processing plants, storage bins, or directly to transport vehicles.
- Agriculture: In agricultural settings, shuttle conveyors facilitate the movement of grains, seeds, and other agricultural products. This is particularly useful during harvesting and storage processes.
- Warehousing: Shuttle conveyors are used in warehouses to move products between different storage areas and loading docks. Their ability to service multiple discharge points is particularly beneficial in large-scale warehousing operations.
A shuttle conveyor system is an advanced material handling solution designed for horizontal transport within various industrial settings. Its key features, such as reversible belts and trolley-mounted mobility, distinguish it from traditional belt conveyors and provide significant advantages in terms of efficiency, flexibility, and safety. By optimizing space use, reducing labor costs, and enhancing productivity, shuttle conveyor systems play a crucial role in modern material handling processes across multiple industries.
Features of Shuttle Conveyor Systems
Mobility and Flexibility
One of the defining features of a shuttle conveyor system is its exceptional mobility and flexibility. Unlike traditional conveyor systems that are fixed in one location, shuttle conveyor systems are mounted on trolleys, allowing for horizontal movement along a predetermined track. This mobility is crucial for industries where materials need to be distributed to multiple discharge points efficiently.
The shuttle conveyor system can move back and forth along the track, transporting materials to various locations within a facility. This horizontal movement capability reduces the need for multiple fixed conveyor systems, streamlining operations and saving space. The system can be integrated into existing workflows with minimal disruption, enhancing overall operational efficiency.
Additionally, shuttle conveyor systems offer the capability for both automated and manual operation. Automated systems can be programmed to follow specific routes and schedules, ensuring consistent and reliable material transport. This automation reduces the need for human intervention, lowering labor costs and minimizing the risk of human error. However, the system can also be manually operated when necessary, providing flexibility for operators to control the movement and discharge of materials based on real-time needs.
Reversible Belt Design
A significant advantage of the shuttle conveyor system is its reversible belt design. Unlike traditional conveyors that move materials in a single direction, the shuttle conveyor system features a belt that can change direction, allowing for the transportation of materials to both ends of the conveyor path. This reversibility is achieved through the use of specialized drive mechanisms that control the belt’s direction of movement.
The reversible belt design offers several benefits. Firstly, it enhances the flexibility of material handling operations by enabling the system to serve multiple discharge points along its track. This is particularly useful in applications where materials need to be evenly distributed across different locations, such as filling multiple storage bins, hoppers, or silos.
Secondly, the ability to reverse the belt direction optimizes workflow by reducing the time and effort required to transport materials to different areas within a facility. This not only improves efficiency but also helps in managing inventory and material distribution more effectively. For example, in a manufacturing setting, raw materials can be delivered to various production lines, and finished products can be transported to different packaging or storage areas using the same shuttle conveyor system.
High-Quality Construction and Durability
The shuttle conveyor system is renowned for its high-quality construction and durability. To ensure long-term reliability and performance, these systems are built using high-grade materials and components. The structural frame is typically made from welded steel, providing a robust and stable foundation for the conveyor system. This steel frame is designed to withstand the rigors of continuous operation and heavy loads, ensuring durability and longevity.
High-quality motors and gear reducers are used to power the shuttle conveyor system, delivering the necessary torque and speed for efficient material transport. These components are selected for their reliability and performance, ensuring smooth and consistent operation. Industrial-grade trough idlers and high-grade steel pulley shafts further enhance the system’s durability, reducing wear and tear on the belt and other components.
The construction of the shuttle conveyor system also includes several features designed to enhance its durability and reduce maintenance requirements. For example, the drive drum is often rubberized to increase friction and improve belt traction, while the return drum is equipped with robust bearings and a fixed shaft connected to manual tensioning devices. These features help maintain optimal belt tension and alignment, reducing the risk of belt slippage or misalignment.
Moreover, the shuttle conveyor system can be equipped with various damping elements and shock absorbers in the loading zone. These components help absorb impact forces and reduce vibrations, protecting the conveyor system and extending its lifespan. The use of self-lubricating rollers with PCS seals also minimizes maintenance requirements by ensuring smooth and reliable operation with minimal friction and wear.
The high-quality construction and durability of the shuttle conveyor system make it a reliable and cost-effective solution for material handling. By utilizing high-grade materials and components, and incorporating features designed to enhance performance and reduce maintenance, the shuttle conveyor system provides long-term reliability and efficiency in various industrial applications.
Technical Specifications of Shuttle Conveyor System
The technical specifications of a shuttle conveyor system are meticulously designed to ensure optimal performance, durability, and efficiency. Understanding these specifications is crucial for selecting the right system for your material handling needs. Here, we delve into the key technical aspects of shuttle conveyor systems, focusing on drum diameters, roller specifications, damping elements, belt quality, and cleaning systems.
Drum Diameter and Types
A shuttle conveyor system features two primary types of drums: the drive drum and the return drum. The drum diameter is a critical specification that affects the system’s performance and durability.
- Drive Drum: The drive drum is responsible for powering the conveyor belt. It is typically rubberized to enhance friction between the belt and the drum, ensuring smooth operation and reducing slippage. The rubberized surface also helps extend the life of the belt by minimizing wear. The drive drum is equipped with heavy-duty foot-mounted bearings, which provide robust support and stability during operation. The diameter of the drive drum can be up to 400mm, making it suitable for handling substantial loads.
- Return Drum: The return drum guides the belt back to the drive drum, completing the loop. It is designed with robust bearings and a fixed shaft connected to manual tensioning devices. These features ensure the belt remains properly aligned and tensioned, preventing issues such as belt sagging or misalignment. The return drum’s construction is equally important for maintaining the system’s overall reliability and efficiency.
Roller Specifications
Rollers play a vital role in the operation of a shuttle conveyor system. They support the belt and help maintain smooth and efficient movement.
- Diameter: The rollers used in shuttle conveyor systems typically have a diameter of up to 133mm. This size provides the necessary support for the belt and the materials being transported, ensuring stability and reducing the risk of belt deformation.
- Self-Lubricating Properties: To minimize maintenance requirements and enhance longevity, the rollers are designed with self-lubricating properties. They are often equipped with PCS (Permanent Contact Seal) seals, which help keep dust and debris out, reducing wear and tear. The self-lubricating nature of these rollers ensures they operate smoothly with minimal friction, contributing to the overall efficiency of the shuttle conveyor system.
Damping Elements and Shock Absorbers
In the loading zone of a shuttle conveyor system, damping elements and shock absorbers are crucial for protecting the system from impact forces.
- Damping Elements: These components are strategically placed in the loading zone to absorb the initial impact of materials being loaded onto the conveyor. They help prevent damage to the belt and other components, ensuring the system remains in good condition even under heavy usage.
- Shock Absorbers: Shock absorbers further enhance the system’s ability to handle impacts. They reduce vibrations and mitigate the effects of sudden loads, protecting the structural integrity of the conveyor system. This protection is essential for maintaining the long-term reliability and performance of the shuttle conveyor system.
Rubber Belt Quality Variations
The quality of the rubber belt used in a shuttle conveyor system is critical, as it directly impacts the system’s durability and suitability for different materials.
- Material-Specific Belts: Depending on the materials being handled, the quality and composition of the rubber belt can vary. For instance, belts used for abrasive materials might be reinforced with additional layers to withstand wear, while belts used for food-grade applications might be made from materials that meet hygiene standards.
- Customization Options: Shuttle conveyor systems often offer customization options for the rubber belt, allowing users to select the most appropriate belt type for their specific needs. This flexibility ensures the system can handle a wide range of materials efficiently and safely.
Belt Cleaning Systems
Effective belt cleaning is essential for maintaining the performance and longevity of a shuttle conveyor system. Several cleaning mechanisms are incorporated to ensure the belt remains free of debris and build-up.
- Primary and Secondary Tension Belt Cleaners: These cleaners are positioned at strategic points along the belt to remove any residual material. Primary cleaners are typically located at the head pulley, while secondary cleaners are placed further along the belt. Together, they ensure thorough cleaning and prevent material build-up that could affect the belt’s operation.
- Plough Scrapers: Positioned on the return belt, plough scrapers are designed to remove any material that may have adhered to the belt during its operation. These scrapers are essential for maintaining the cleanliness of the belt and preventing any potential issues caused by accumulated debris.
The technical specifications of a shuttle conveyor system are carefully engineered to ensure efficient, reliable, and durable operation. From the drum diameters and roller specifications to the damping elements, belt quality, and cleaning systems, each aspect plays a crucial role in the overall performance of the system. By understanding these specifications, users can select the most suitable shuttle conveyor system for their material handling needs, ensuring optimal productivity and longevity.
Additional Components of Shuttle Conveyor System
In a shuttle conveyor system, the additional components are crucial for enhancing its functionality, safety, and durability. These components ensure that the system operates smoothly, protects the conveyed materials, and meets the specific needs of different industries. Here, we provide a detailed overview of the key additional components that can be integrated into a shuttle conveyor system.
Inlet Chute with Rubber Seals and Wear Plates
The inlet chute is a vital component of the shuttle conveyor system, responsible for directing materials onto the conveyor belt efficiently and safely.
- Rubber Seals: Rubber seals are incorporated into the inlet chute to prevent spillage and reduce dust generation. These seals ensure that the materials enter the conveyor belt in a controlled manner, minimizing waste and maintaining a clean working environment.
- Wear Plates: Wear plates, often made from Hardox or other high-durability materials, are installed in the inlet chute to protect it from abrasion and impact caused by the materials being loaded. These plates extend the lifespan of the chute by resisting wear and tear, especially when handling abrasive or heavy materials.
Optional Equipment
To customize the shuttle conveyor system for specific operational needs, various optional equipment can be added. These components enhance the system’s versatility, safety, and ease of maintenance.
- Rails: Rails are essential for guiding the movement of the shuttle conveyor. They provide a stable and precise path for the conveyor to travel along, ensuring accurate placement of materials and reliable operation.
- Walkways and Service Platforms: These additions facilitate easy access for maintenance and inspection. Walkways and service platforms are designed to be robust and safe, allowing personnel to perform necessary tasks without disrupting the conveyor’s operation.
- Covers: Covers are used to protect the conveyor belt and materials from environmental factors such as rain, dust, and debris. They help maintain the quality of the conveyed materials and extend the lifespan of the conveyor components by shielding them from harsh conditions.
- Emergency Stop Systems: Safety is paramount in any conveyor system. Emergency stop systems allow operators to quickly halt the conveyor in case of an emergency, preventing accidents and damage. These systems are strategically placed for easy access.
- Speed Sensors: Speed sensors monitor the conveyor belt’s speed to ensure it operates within the desired range. They help in maintaining optimal performance and can trigger alarms or automatic shutdowns if the belt speed deviates from set parameters.
- Alignment Switches: Alignment switches detect any misalignment of the conveyor belt and send alerts to the control system. Proper belt alignment is crucial for preventing wear and tear and ensuring smooth operation. These switches help maintain the belt’s correct position, reducing downtime and maintenance costs.
Dust Enclosures for Environmental Protection and Weatherproofing
Dust enclosures are critical for maintaining a clean and safe working environment. They encapsulate the conveyor system to contain dust and prevent it from spreading.
- Environmental Protection: Dust enclosures help protect the surrounding environment from the dust generated by the conveyed materials. This is particularly important in industries where dust can pose health hazards or contaminate products.
- Weatherproofing: Enclosures also shield the conveyor system from adverse weather conditions such as rain, snow, and wind. This protection ensures that the system operates reliably regardless of the external environment, reducing the risk of weather-related interruptions.
Main Parts Treatment: Sandblasting, Priming, and Painting
The treatment of the main parts of a shuttle conveyor system is essential for ensuring their durability and resistance to corrosion.
- Sandblasting: Sandblasting is the process of cleaning and preparing the surface of the conveyor components by blasting them with abrasive materials. This process removes any rust, old paint, and surface contaminants, providing a clean and smooth surface for further treatment.
- Priming: After sandblasting, a primer is applied to the components. Priming is crucial as it provides a base layer that enhances the adhesion of the final paint coat. It also adds an extra layer of protection against corrosion and wear.
- Painting: The final step involves painting the primed components. The paint not only improves the aesthetic appearance of the conveyor system but also provides a protective coating that resists corrosion, wear, and environmental damage. The paint used is typically of industrial-grade quality, designed to withstand harsh operating conditions.
The additional components of a shuttle conveyor system significantly contribute to its overall performance, safety, and durability. From the inlet chute with rubber seals and wear plates to the optional equipment like rails, walkways, covers, emergency stop systems, speed sensors, and alignment switches, each component plays a vital role in customizing and optimizing the conveyor system for specific industrial needs. Dust enclosures provide environmental protection and weatherproofing, while the thorough treatment of main parts through sandblasting, priming, and painting ensures long-term reliability and resistance to corrosion. Together, these components make the shuttle conveyor system a versatile and robust solution for various material handling applications.
Applications of Shuttle Conveyor Systems
Filling Bulk Material to Storage Bins, Hoppers, or Silos
The shuttle conveyor system is highly effective for filling bulk materials into storage bins, hoppers, or silos. This system is designed to move back and forth on a track, allowing it to distribute materials evenly across the length of the storage unit. This ensures that the space within the bin, hopper, or silo is used efficiently, preventing the formation of material piles and reducing the need for manual intervention. The shuttle conveyor system’s precision and automation capabilities significantly enhance productivity, especially in industries where bulk material handling is critical, such as agriculture, mining, and manufacturing. By ensuring an even distribution of materials, the system also helps maintain the quality and integrity of the stored products.
Industrial Applications
Power Plants
In power plants, the shuttle conveyor system plays a vital role in handling coal and other bulk materials required for energy production. These systems are used to transport coal from storage areas to the furnace or boiler room, ensuring a continuous supply of fuel. The shuttle conveyor system’s ability to handle large volumes of material efficiently makes it indispensable in maintaining the steady operation of power plants. Additionally, its automated controls and safety features help minimize the risk of accidents and ensure compliance with industry regulations.
Pulp and Paper Mills
The pulp and paper industry relies heavily on the shuttle conveyor system for transporting raw materials such as wood chips, pulp, and recycled paper. These systems are used to move materials between different stages of the production process, from initial processing to final packaging. The shuttle conveyor system’s versatility and capacity to handle various types of materials make it an essential component in pulp and paper mills. By streamlining the material handling process, these systems help reduce production costs and improve overall efficiency.
Granular Product Warehousing
In granular product warehousing, the shuttle conveyor system is used to transport products such as grains, seeds, and other small particulate materials. These systems can be programmed to distribute materials evenly across multiple storage bins, ensuring optimal use of warehouse space. The shuttle conveyor system’s precision and reliability are crucial in maintaining the quality of stored products and minimizing waste. By automating the material handling process, these systems also reduce labor costs and improve warehouse safety.
Frac Sand Processing
Frac sand processing facilities use the shuttle conveyor system to transport sand from storage areas to processing equipment. These systems are designed to handle the abrasive nature of frac sand, ensuring smooth and efficient operation. The shuttle conveyor system’s ability to move materials precisely and efficiently helps optimize the processing workflow, resulting in higher productivity and lower operational costs. Additionally, the system’s durability and low maintenance requirements make it a cost-effective solution for frac sand processing.
Specialized Uses
SMT Shuttle Conveyors for Electronic Manufacturing
In the electronics manufacturing industry, Surface Mount Technology (SMT) shuttle conveyors are specialized types of shuttle conveyors used for handling electronic components and assemblies. These systems are designed to transport delicate and high-precision items between different stages of the production process, such as from the pick-and-place machine to the reflow oven. The shuttle conveyor system’s precision and gentle handling capabilities are essential in preventing damage to sensitive electronic components. Additionally, these systems can be integrated with other automated equipment to create a seamless and efficient manufacturing workflow. By reducing manual handling and increasing production speed, SMT shuttle conveyors help electronics manufacturers improve product quality and reduce production costs.
The shuttle conveyor system is a versatile and efficient solution for a wide range of applications, from filling bulk materials into storage units to handling specialized tasks in industrial and manufacturing settings. Its ability to automate and optimize material handling processes makes it an invaluable asset across various industries, contributing to increased productivity, reduced costs, and improved safety.
Benefits of Shuttle Conveyor Systems
The shuttle conveyor system offers a multitude of advantages that make it an indispensable solution in various industries. From enhanced flexibility to cost efficiency, the benefits of incorporating a shuttle conveyor system into your material handling operations are significant and far-reaching. This section delves into the key benefits that make shuttle conveyors a preferred choice for many businesses.
Enhanced Flexibility in Material Handling
One of the primary benefits of a shuttle conveyor system is its exceptional flexibility. Unlike traditional fixed conveyors, shuttle conveyors are mounted on trolleys, allowing them to move horizontally along a predefined path. This mobility enables the system to distribute materials to multiple locations with precision and ease.
- Versatile Movement: The shuttle conveyor system can be programmed to move back and forth along its track, delivering materials to specific points as required. This versatility is particularly beneficial in processes that involve feeding multiple bins, silos, or hoppers from a single conveyor line.
- Customizable Paths: The system can be customized to follow various paths and configurations, adapting to the unique layout and requirements of different facilities. Whether you need straight-line movement or complex paths with multiple stops, the shuttle conveyor system can be tailored to meet these needs.
- Automated Operation: Shuttle conveyor systems can be integrated with automation controls, allowing for precise and programmable operation. This automation reduces the need for manual intervention, ensuring consistent and accurate material distribution.
Reduced Need for Multiple Fixed Conveyors
Another significant advantage of the shuttle conveyor system is the reduction in the need for multiple fixed conveyors. In traditional setups, each destination point often requires its dedicated conveyor line, leading to a complex and space-consuming arrangement. Shuttle conveyors streamline this process.
- Space Efficiency: By replacing multiple fixed conveyors with a single shuttle system, you can free up valuable floor space. This space efficiency is crucial in facilities where floor area is at a premium or where you need to optimize the layout for better workflow.
- Cost Savings: Installing and maintaining multiple fixed conveyors can be expensive. A shuttle conveyor system consolidates these needs into one versatile solution, reducing installation costs, maintenance requirements, and overall investment.
- Simplified Maintenance: Maintaining a single shuttle conveyor system is simpler and more cost-effective than managing several fixed conveyors. With fewer components to service and repair, maintenance becomes less time-consuming and more manageable.
Improved Efficiency and Reduced Labor Costs
The shuttle conveyor system enhances operational efficiency and reduces labor costs, making it a cost-effective solution for many industries.
- Higher Throughput: Shuttle conveyors are designed to handle high volumes of materials efficiently. Their ability to move continuously and distribute materials accurately increases the overall throughput of your operations, leading to improved productivity.
- Reduced Manual Handling: With the automated movement and precise control offered by shuttle conveyors, the need for manual material handling is significantly reduced. This not only lowers labor costs but also minimizes the risk of workplace injuries associated with manual lifting and transporting of heavy materials.
- Consistent Performance: Shuttle conveyor systems deliver consistent and reliable performance. Automated control systems ensure that materials are conveyed and distributed with high accuracy, reducing the chances of errors and material waste.
Additional Benefits
Beyond the core advantages mentioned, shuttle conveyor systems also offer several other benefits that contribute to their popularity in various industries.
- Scalability: Shuttle conveyor systems can be easily scaled to accommodate growing production needs. Whether you need to extend the track length, add more destination points, or increase the conveyor’s load capacity, these systems are highly adaptable.
- Durability: Built with high-quality materials and robust construction, shuttle conveyors are designed for long-term reliability and durability. This durability ensures that the system can withstand the demanding conditions of industrial environments.
- Environmental Benefits: By optimizing material handling and reducing the need for multiple conveyors, shuttle systems can also contribute to environmental sustainability. They help minimize energy consumption and reduce the overall carbon footprint of your operations.
The shuttle conveyor system stands out as a highly flexible, efficient, and cost-effective solution for material handling. Its ability to replace multiple fixed conveyors, improve operational efficiency, and reduce labor costs makes it an attractive option for various industries, including manufacturing, mining, and agriculture. The scalability, durability, and environmental benefits further enhance its value, making the shuttle conveyor system a smart investment for businesses looking to optimize their material handling processes.
Choosing the Right Shuttle Conveyor System
Selecting the appropriate shuttle conveyor system for your facility is a critical decision that requires careful consideration of various factors. From material handling capacity to customization options, several key aspects need to be evaluated to ensure that the chosen system meets your operational requirements and budget constraints.
Factors to Consider
- Material Handling Capacity: The first step in choosing a shuttle conveyor system is determining the material handling capacity required for your operations. Consider the volume and type of materials that need to be transported, as well as the frequency and speed of conveyance.
- Specific Industry Requirements: Different industries have unique material handling needs. Ensure that the shuttle conveyor system you choose is designed to meet the specific requirements of your industry. Factors such as environmental conditions, safety standards, and regulatory compliance should be taken into account.
- Budget and Cost Considerations: Budget is a crucial factor in selecting a shuttle conveyor system. Determine the total cost of ownership, including installation, maintenance, and operational costs, to ensure that the system is cost-effective over its lifespan.
- Operational Flexibility: Consider the flexibility of the shuttle conveyor system in terms of its ability to adapt to changing operational needs. A system that can be easily reconfigured or expanded is preferable for future scalability.
- Space Constraints: Evaluate the available space in your facility and choose a shuttle conveyor system that fits within the available footprint. Consider vertical clearance, aisle width, and layout constraints when selecting the system.
- Automation Compatibility: If you plan to automate your material handling processes, ensure that the shuttle conveyor system is compatible with automation technologies such as sensors, controllers, and software.
- Energy Efficiency: Look for energy-efficient features in the shuttle conveyor system, such as variable speed drives and energy-efficient motors, to reduce operational costs and environmental impact.
Customization Options
- Tailoring Designs to Specific Operational Needs: Many shuttle conveyor systems offer customization options to meet specific operational requirements. This may include adjusting the conveyor length, width, and height to fit the available space or incorporating specialized features for handling unique materials.
- Availability of Specialized Components and Features: Consider the availability of specialized components and features that can enhance the performance and efficiency of the shuttle conveyor system. This may include advanced control systems, specialized belts, or safety features tailored to your industry requirements.
Choosing the right shuttle conveyor system requires a thorough assessment of your material handling needs, budget constraints, and operational requirements. By carefully considering these factors and exploring customization options, you can select a system that not only meets your current needs but also provides flexibility for future growth and efficiency.
Case Studies and Examples
Brief Descriptions of Successful Implementations
Amazon
Amazon, the global e-commerce giant, implemented a shuttle conveyor system in one of their largest fulfillment centers to improve their order processing capabilities. Prior to this implementation, Amazon faced challenges with handling the massive volume of orders efficiently. The shuttle conveyor system was integrated into their automated warehouse system, allowing for quick and precise movement of products between different storage and packing areas. This upgrade resulted in a 30% increase in order processing speed, significantly reducing delivery times and enhancing overall customer satisfaction.
Tesla
Tesla, the renowned electric vehicle manufacturer, incorporated a shuttle conveyor system in their Gigafactory to streamline the movement of components across various production stages. Before the implementation, Tesla experienced delays due to manual handling and transportation of parts, which impacted their production timelines. By integrating the shuttle conveyor system, Tesla was able to automate the transportation of heavy and bulky components, ensuring a continuous flow of materials and reducing production bottlenecks. This led to a 25% increase in production efficiency and allowed Tesla to meet their ambitious manufacturing targets.
Coca-Cola
Coca-Cola, a leading beverage company, utilized a shuttle conveyor system in their bottling plant to enhance their material handling process. The system was installed to transport bottles from the production line to the packaging area, ensuring a smooth and efficient operation. Prior to this, Coca-Cola faced issues with breakage and inefficiencies due to manual handling. The shuttle conveyor system’s precise and automated movement significantly reduced bottle breakage and improved the overall efficiency of the packaging process, resulting in a 20% increase in productivity.
Highlighting the Impact on Efficiency and Productivity
DHL
DHL, a global logistics company, implemented a shuttle conveyor system in their central distribution hub to address inefficiencies in their sorting process. The system allowed for automated sorting of packages based on their destination, reducing the need for manual intervention. As a result, DHL experienced a significant improvement in sorting accuracy and speed, leading to a 40% increase in throughput. This enhancement not only improved operational efficiency but also reduced the cost associated with manual labor and sorting errors.
Walmart
Walmart, one of the largest retail chains, adopted a shuttle conveyor system in their regional distribution centers to optimize the movement of goods. The system facilitated the efficient transportation of products from inbound trucks to storage areas and then to outbound trucks for delivery to stores. This automation reduced the reliance on forklifts and manual labor, resulting in a 35% reduction in handling time and a substantial decrease in operational costs. Walmart’s ability to restock stores faster improved their inventory management and customer satisfaction.
Intel
Intel, a leader in semiconductor manufacturing, integrated a shuttle conveyor system in their chip production facility to enhance the handling of delicate components. The system provided a precise and controlled environment for moving semiconductor wafers between different processing stations. This automation reduced the risk of damage and contamination, leading to a 15% increase in yield rates. Intel’s implementation of the shuttle conveyor system also improved the overall speed and efficiency of their manufacturing process, allowing them to meet the high demand for their products.
Procter & Gamble
Procter & Gamble (P&G), a multinational consumer goods company, implemented a shuttle conveyor system in their packaging facility to streamline the movement of products from the production line to the packaging area. The system’s automated handling reduced the need for manual labor, resulting in a 25% increase in packaging speed and efficiency. This improvement enabled P&G to meet the growing demand for their products while reducing labor costs and minimizing the risk of product damage during handling.
The shuttle conveyor system has proven to be a valuable asset across various industries, enhancing efficiency, productivity, and operational cost-effectiveness. These case studies demonstrate the significant impact of implementing shuttle conveyor systems, showcasing how they can transform material handling processes and drive business success.
FAQs about Shuttle Conveyor System
A shuttle conveyor is an innovative type of conveyor system designed for versatile and efficient material handling. Unlike traditional conveyor belts that move in a fixed direction, shuttle conveyors are equipped with a mechanism that allows the conveyor to move along a track, back and forth. This functionality makes them incredibly useful for operations requiring the distribution of materials to multiple locations or across different points along a production line. Shuttle conveyors are commonly found in industries like mining, agriculture, and manufacturing, where they are used to transport bulk materials, including grains, minerals, and other commodities, between various processing stages. The key advantage of a shuttle conveyor is its ability to maximize space efficiency by eliminating the need for multiple conveyor systems, thereby streamlining operations and reducing overall costs.
Conveyors are essential components in the material handling industry, facilitating the efficient transport of goods across facilities. There are several types of conveyor systems, but three common types are:
Belt Conveyors: These are the most widespread type of conveyor system. A belt conveyor consists of a continuous belt made from a variety of materials, including fabric, rubber, or plastic, that moves over a series of pulleys. They are used for transporting light to heavy materials over short to long distances and can be designed to handle different shapes, sizes, and weights of materials.
Roller Conveyors: These systems make use of rollers mounted in frames to convey products. Roller conveyors are particularly well-suited for moving items that have a rigid bottom surface. They can be powered or unpowered (gravity roller conveyors) and are often used in warehousing and logistics for the efficient movement of boxes, pallets, and trays.
Chain Conveyors: Chain conveyors use chains or a series of chains to move products along the conveyor pathway. These are particularly useful for heavy or bulky materials that require a strong, durable method to be transported. Chain conveyors can also be designed for specific applications, such as carrying high-heat items or for use in wet environments.
The cost of a shuttle conveyor system can vary widely depending on several factors, including its size, material capacity, design complexity, and the specific requirements of the operation it serves. Generally, the initial investment can range from tens of thousands to several hundred thousand dollars. For custom-engineered systems, designed to handle unique or challenging material handling needs, the costs can be significantly higher. It’s also important to consider ongoing operating and maintenance costs, which can impact the total cost of ownership over the conveyor’s lifespan. To get an accurate estimate, it’s advisable to consult with conveyor system manufacturers who can provide detailed quotations based on the specific needs and parameters of your operation.
A conveyor system works by providing a continuous, efficient, and automated means of transporting goods and materials from one point to another within a facility. At its core, a conveyor uses a belt, chain, rollers, or a combination of these components to move items along its length. In powered conveyor systems, an electric motor drives the movement, either by moving the conveyor belt, rotating the rollers, or propelling the chains that, in turn, move the items placed on them. The operation can be controlled manually or automated through computerized systems, allowing for the precise control of speed, direction, and destination of the conveyed materials. Conveyor systems are instrumental in optimizing workflow, enhancing productivity, and reducing labor costs in industries ranging from manufacturing and warehousing to retail and food processing.
Last Updated on June 6, 2024 by Jordan Smith
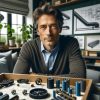
Jordan Smith, a seasoned professional with over 20 years of experience in the conveyor system industry. Jordan’s expertise lies in providing comprehensive solutions for conveyor rollers, belts, and accessories, catering to a wide range of industrial needs. From initial design and configuration to installation and meticulous troubleshooting, Jordan is adept at handling all aspects of conveyor system management. Whether you’re looking to upgrade your production line with efficient conveyor belts, require custom conveyor rollers for specific operations, or need expert advice on selecting the right conveyor accessories for your facility, Jordan is your reliable consultant. For any inquiries or assistance with conveyor system optimization, Jordan is available to share his wealth of knowledge and experience. Feel free to reach out at any time for professional guidance on all matters related to conveyor rollers, belts, and accessories.