Guide to Conveyor Pulley Lagging Types: Which One to Choose
Pulley lagging is a protective and functional material applied to the surface of conveyor pulleys. Its main purpose is to enhance the friction between the pulley and the conveyor belt, preventing slippage. This is crucial for maintaining the efficiency and longevity of conveyor systems.Understanding different conveyor pulley lagging types are essential for selecting the right solution for specific operational needs. Pulley lagging serves several key functions: it shields the pulley shell from wear, boosts the friction to ensure effective belt movement, and can aid in water dispersion to prevent belt slippage in wet conditions. Each type of lagging offers unique benefits and is suited for particular environments and applications.
Conveyor Pulley Lagging Types
Conveyor pulley lagging types are an essential component in enhancing the performance and longevity of conveyor systems. Lagging is applied to the surface of conveyor pulleys to improve friction, reduce slippage, and protect the pulley from wear. This section will provide a detailed comparison of different conveyor pulley lagging types, focusing on rubber lagging variants: plain rubber lagging, diamond grooved rubber lagging, and chevron rubber lagging.
Comparison of Rubber Lagging Types
Rubber lagging is one of the most commonly used materials for conveyor pulley lagging due to its flexibility, cost-effectiveness, and ease of installation. Each type of rubber lagging offers distinct advantages depending on the application requirements and operating conditions.
Plain Rubber Lagging
Overview:
Plain rubber lagging is characterized by a smooth rubber surface applied to the pulley. This type of lagging is primarily used on non-drive pulleys where the main goal is to minimize wear and extend the life of the pulley.
Applications:
Plain rubber lagging is ideal for non-drive pulleys such as tail pulleys and bend pulleys. These pulleys do not require high friction but need protection from wear caused by continuous contact with the conveyor belt.
Advantages:
- Cost-Effective: Plain rubber lagging is generally less expensive compared to other lagging types, making it a cost-effective solution for non-drive pulleys.
- Ease of Installation: The smooth surface of plain rubber lagging simplifies the installation process, reducing downtime.
- Wear Protection: By providing a protective layer, plain rubber lagging helps to extend the life of the pulley by minimizing wear and abrasion.
Disadvantages:
- Limited Friction: Since plain rubber lagging does not offer enhanced friction, it is not suitable for drive pulleys where high traction is required.
Diamond Grooved Rubber Lagging
Overview:
Diamond grooved rubber lagging features a pattern of diamond-shaped grooves on the rubber surface. This design enhances the flexibility and water-shedding capabilities of the lagging, making it ideal for drive pulleys that require higher friction.
Applications:
Diamond grooved rubber lagging is commonly used on drive pulleys where improved traction is essential. The diamond grooves provide additional grip, which helps to reduce slippage and enhance the efficiency of the conveyor system.
Advantages:
- Enhanced Friction: The diamond-shaped grooves increase the surface area in contact with the conveyor belt, providing better grip and reducing slippage.
- Water Shedding: The grooves help to channel water away from the pulley surface, maintaining friction even in wet conditions.
- Flexibility: The pattern allows the rubber to flex more effectively, accommodating minor misalignments and reducing the risk of belt damage.
Disadvantages:
- Higher Cost: Diamond grooved rubber lagging is typically more expensive than plain rubber lagging due to the additional processing required to create the grooves.
- Complex Installation: The grooved pattern can make installation more complex and time-consuming compared to plain rubber lagging.
Chevron Rubber Lagging
Overview:
Chevron rubber lagging features a chevron or herringbone pattern on the rubber surface. This pattern is specifically designed to provide excellent traction in wet conditions, making it suitable for applications where water or other liquids are present.
Applications:
Chevron rubber lagging is ideal for drive pulleys in environments where wet conditions are common, such as mining, aggregate processing, and other outdoor applications. The chevron pattern helps to maintain traction and prevent slippage, ensuring reliable conveyor operation.
Advantages:
- Superior Traction: The chevron pattern provides enhanced grip, particularly in wet conditions, reducing slippage and improving conveyor efficiency.
- Effective Water Channeling: The design channels water away from the pulley surface, maintaining friction and preventing hydroplaning.
- Durability: Chevron rubber lagging is typically made from high-quality rubber compounds that offer excellent wear resistance and longevity.
Disadvantages:
- Cost: Similar to diamond grooved rubber lagging, chevron rubber lagging can be more expensive due to the specialized pattern and manufacturing process.
- Installation Complexity: The chevron pattern may require more precise alignment during installation to ensure optimal performance, potentially increasing installation time and costs.
What is Conveyor Pulley Lagging Types
Conveyor pulley lagging is a crucial aspect of conveyor system performance, enhancing friction, reducing slippage, and extending the lifespan of both the pulley and the conveyor belt. Different types of lagging materials are used depending on the specific requirements of the application. This article provides a detailed overview of various conveyor pulley lagging types, with a focus on ceramic pulley lagging, its durability, common types, cost vs. service life, applications, installation, and key considerations.
Ceramic Pulley Lagging
Durability
Ceramic pulley lagging is renowned for its exceptional durability and abrasion resistance. Unlike traditional rubber lagging, ceramic lagging is designed to withstand the harshest operating conditions, including heavy loads, high speeds, and abrasive materials. The ceramic tiles used in this type of lagging offer superior hardness and toughness, which significantly reduces wear and tear on both the pulley and the conveyor belt. This makes ceramic lagging an ideal choice for industries that demand long-lasting and reliable conveyor systems.
Common Types
Ceramic pulley lagging comes in two main types: smooth ceramic lagging and dimple ceramic lagging. Each type offers unique benefits in terms of friction and belt tracking.
- Smooth Ceramic Lagging: Smooth ceramic lagging provides a balance between grip and minimizing belt wear. It is less abrasive than dimple ceramic lagging and is suitable for non-drive pulleys. This type of lagging ensures the belt runs smoothly and steadily, reducing the risk of premature belt damage while maintaining adequate friction to prevent slippage.
- Dimple Ceramic Lagging: Dimple ceramic lagging features a textured surface with dimples or protrusions that enhance grip and friction. This type of lagging is ideal for drive pulleys, where high traction is required to move the belt effectively. The dimples increase the contact area between the pulley and the belt, improving belt tracking and reducing slippage, even under wet or oily conditions.
Cost vs. Service Life
While ceramic pulley lagging tends to have a higher upfront cost compared to rubber lagging, its extended service life and reduced wear offer significant long-term savings. The initial investment in ceramic lagging is offset by the lower maintenance costs and fewer replacements needed over time. The superior durability and abrasion resistance of ceramic lagging mean that conveyor systems can operate more efficiently and with less downtime, ultimately leading to increased productivity and lower total cost of ownership.
Application
Ceramic lagging is most beneficial in applications where enhanced grip and friction are critical. It is particularly advantageous for drive pulleys, which require a strong and reliable grip to move the conveyor belt. Industries such as mining, quarrying, and heavy material handling often use ceramic lagging to handle the demanding conditions of these environments. The enhanced friction provided by ceramic lagging ensures efficient material transport, even in challenging conditions such as wet, muddy, or oily environments.
Installation
Ceramic pulley lagging can be installed in several ways, depending on the specific requirements of the application:
- Rubber-Backed Strips/Sheets: Ceramic lagging is often available as rubber-backed strips or sheets that can be bonded to the pulley surface. This method provides flexibility and ease of installation, allowing for quick and effective application.
- Directly Bonded Tiles: Ceramic tiles can also be directly bonded to the pulley surface, offering a more permanent and robust solution. This method ensures that the tiles remain securely in place, even under high-stress conditions, providing consistent performance over time.
Considerations
While ceramic pulley lagging offers numerous benefits, there are some considerations to keep in mind:
- Potential Fragility: Ceramic tiles, despite their hardness and durability, can be fragile and may crack or chip if not handled properly during installation or if subjected to extreme impacts. It is essential to ensure proper handling and installation techniques to prevent damage.
- Proper Conveyor Design and Lagging Selection: Choosing the right type of lagging for a specific application is crucial. Factors such as the type of materials being conveyed, the operating environment, and the specific requirements of the conveyor system must be considered. Proper conveyor design and lagging selection will ensure optimal performance and longevity.
Other Types of Conveyor Pulley Lagging
While ceramic lagging is a popular choice for its durability and performance, other types of lagging materials are also commonly used in various applications. These include rubber lagging, diamond-pattern lagging, and polyurethane lagging.
Rubber Lagging
Rubber lagging is one of the most widely used materials for conveyor pulley lagging. It offers a good balance of cost, durability, and performance. Rubber lagging provides sufficient friction to prevent belt slippage and is available in various hardness levels to suit different applications. It is also relatively easy to install and replace, making it a cost-effective choice for many industries.
Diamond-Pattern Lagging
Diamond-pattern lagging features a unique diamond-shaped texture that enhances grip and improves belt tracking. This type of lagging is particularly effective in applications where moisture or debris can cause belt slippage. The diamond pattern channels water and debris away from the contact surface, ensuring a clean and efficient operation. It is commonly used in wet or muddy environments, such as in aggregate and mining applications.
Polyurethane Lagging
Polyurethane lagging offers excellent resistance to abrasion and chemical exposure, making it suitable for harsh industrial environments. It provides a high level of grip and durability, ensuring reliable performance even under extreme conditions. Polyurethane lagging is often used in applications involving abrasive materials, such as sand, gravel, and chemicals. Its flexibility and resilience make it an ideal choice for high-stress applications where traditional rubber lagging may not perform as well.
The Types of Conveyor Pulley Lagging
Conveyor pulley lagging is an essential aspect of conveyor systems, providing the necessary grip and protection to ensure efficient operation and longevity. This section will focus on the different types of lagging available, with a detailed comparison of ceramic lagging types, including dimple ceramic lagging and smooth ceramic lagging.
Comparison of Ceramic Lagging Types
Ceramic lagging is renowned for its durability and ability to significantly increase friction between the conveyor belt and pulley. This type of lagging is particularly beneficial in harsh environments where high levels of abrasion and heavy loads are common. The primary types of ceramic lagging include dimple ceramic lagging and smooth ceramic lagging, each offering distinct advantages and considerations.
Dimple Ceramic Lagging
Overview:
Dimple ceramic lagging features a surface covered with small, raised dimples. These dimples enhance the friction between the pulley and the conveyor belt, making it an excellent choice for applications where slippage is a major concern.
Applications:
Dimple ceramic lagging is ideal for drive pulleys in high-torque applications. It is commonly used in industries such as mining, where the conveyor systems are subjected to heavy loads and abrasive materials.
Advantages:
- Increased Friction: The raised dimples on the surface of the ceramic lagging significantly increase the contact area between the belt and the pulley, providing superior grip and reducing the risk of slippage. This increased friction is particularly beneficial in maintaining the efficiency and reliability of conveyor systems under heavy loads.
- Enhanced Performance in Wet Conditions: Dimple ceramic lagging performs well in wet or muddy environments. The dimples help to shed water and other materials, maintaining high friction levels and preventing slippage even when the pulley surface is wet.
Disadvantages:
- Potential for Belt Damage: While the increased friction provided by dimple ceramic lagging is advantageous in preventing slippage, it can also lead to increased wear on the conveyor belt. In cases where slippage does occur, the abrasive nature of the ceramic dimples can cause significant damage to the belt surface.
- Higher Initial Cost: Dimple ceramic lagging is typically more expensive than other types of lagging due to the advanced materials and manufacturing processes involved. However, the long-term benefits in terms of reduced maintenance and extended pulley life can offset this initial investment.
Smooth Ceramic Lagging
Overview:
Smooth ceramic lagging offers a flat, ceramic surface without the raised dimples found in dimple ceramic lagging. This type of lagging balances the high durability of ceramic materials with reduced wear on the conveyor belt, providing a compromise between rubber and dimple ceramic lagging.
Applications:
Smooth ceramic lagging is suitable for a variety of applications, including both drive and non-drive pulleys. It is particularly useful in environments where abrasion resistance is important, but the risk of belt damage from high friction is a concern.
Advantages:
- Balanced Friction and Belt Wear: Smooth ceramic lagging provides a good level of friction while minimizing wear on the conveyor belt. This balance makes it a versatile option for many conveyor systems, offering both durability and reduced maintenance needs.
- Durability: Like dimple ceramic lagging, smooth ceramic lagging is highly resistant to wear and abrasion. This durability ensures a long operational life, reducing the frequency of pulley replacements and associated downtime.
- Lower Risk of Belt Damage: The flat surface of smooth ceramic lagging reduces the risk of damaging the conveyor belt compared to dimple ceramic lagging. This feature is particularly beneficial in applications where the belt is subjected to frequent starts and stops, which can increase the likelihood of slippage.
Disadvantages:
- Lower Friction Compared to Dimple Lagging: While smooth ceramic lagging provides good friction, it does not offer the same level of grip as dimple ceramic lagging. In high-torque applications where maximum friction is required, dimple ceramic lagging may be a better choice.
- Higher Cost than Rubber Lagging: Although smoother ceramic lagging is more affordable than dimple ceramic lagging, it is still more expensive than traditional rubber lagging. The decision to use smooth ceramic lagging should be based on a cost-benefit analysis, considering the specific needs and conditions of the application.
How about Conveyor Pulley Lagging Types
Selecting the appropriate conveyor pulley lagging types is crucial for optimizing the performance and longevity of conveyor systems. Different types of lagging provide unique benefits and are suitable for various applications, from enhancing friction to protecting the pulley and belt from wear. In this section, we will explore some other lagging options beyond the commonly used rubber and ceramic types, focusing on polyurethane/plastic lagging and the implications of using no lagging at all.
Other Lagging Options
Polyurethane/Plastic Lagging
Polyurethane or plastic lagging is a versatile option for conveyor pulleys, known for its excellent durability and adaptability. Here are some key points about polyurethane/plastic lagging:
- Benefits: Polyurethane lagging is highly resistant to abrasion and chemical exposure, making it ideal for harsh industrial environments. It offers a long service life and can withstand extreme conditions better than traditional rubber lagging. Additionally, polyurethane lagging provides a high level of grip and flexibility, ensuring reliable performance even under heavy loads and high-speed operations.
- Versatility: This type of lagging is suitable for a wide range of applications, including those involving abrasive materials like sand, gravel, and chemicals. Its resilience and ability to handle diverse operational demands make it a popular choice in various industries, from mining to food processing.
- Cost and Replacement Challenges: Despite its benefits, polyurethane lagging can be more expensive than other lagging materials. The higher initial cost might be a consideration for some operations, although the extended service life often offsets this expense. Additionally, replacing polyurethane lagging can be more challenging due to its toughness, requiring specialized tools and expertise.
In summary, polyurethane/plastic lagging offers significant advantages in terms of durability and performance, making it an excellent choice for demanding applications. However, the higher costs and potential replacement challenges should be carefully weighed against the operational benefits.
No Lagging
Some conveyor systems may operate without any lagging on the pulleys. This option, while the simplest and least expensive initially, comes with several drawbacks:
- Lowest Friction Option: Operating with no lagging means that there is minimal friction between the pulley and the conveyor belt. While this can reduce energy consumption in certain applications, it is generally not recommended for systems where maintaining traction is crucial.
- Lack of Protection: Without lagging, the pulley shell is exposed to direct contact with the conveyor belt and the materials being transported. This lack of protection leads to increased wear and tear on the pulley shell, resulting in early replacement and higher maintenance costs. The conveyor belt itself is also more susceptible to damage, reducing its service life.
- Operational Issues: The absence of lagging can lead to significant operational challenges, such as belt slippage, misalignment, and reduced efficiency. These issues can cause frequent downtime and disrupt production, ultimately impacting the overall productivity of the system.
While opting for no lagging might seem like a cost-saving measure initially, the long-term implications often outweigh the benefits. The increased wear and operational issues can lead to higher maintenance costs and reduced system reliability.
The Key of Conveyor Pulley Lagging Types
Choosing the right lagging for your conveyor pulley is crucial to ensure efficient operation, reduce maintenance, and extend the life of both the pulley and the conveyor belt. In this section, we will discuss key factors to consider when selecting the appropriate conveyor pulley lagging types, including operating conditions, abrasion levels, pulley types, and the impact of belt speed and tension.
Choosing the Right Pulley Lagging
Selecting the appropriate lagging for a conveyor pulley involves evaluating several factors to match the lagging type with the specific needs of the operation. This detailed consideration helps optimize the performance and longevity of the conveyor system.
Operating Conditions
Factors to Consider:
Operating conditions play a significant role in determining the best type of lagging for a conveyor pulley. Key environmental factors include:
- Wet Conditions: In wet environments, lagging with excellent water-shedding capabilities, such as dimple ceramic lagging or chevron rubber lagging, is essential. These types of lagging help maintain high friction levels and prevent slippage.
- Dry Conditions: In dry environments, smooth ceramic lagging or plain rubber lagging may be sufficient. These types provide the necessary grip and wear resistance without the need for additional water-shedding features.
- Abrasive Conditions: For abrasive conditions, where materials such as coal, minerals, or aggregates are being conveyed, lagging with high abrasion resistance, like ceramic lagging, is preferred. This ensures longevity and reduces maintenance needs.
Specific Operational Needs:
Operational requirements, such as the frequency of starts and stops, load variations, and temperature extremes, also influence the choice of lagging. For instance, high-torque applications benefit from lagging types that offer superior grip and durability, such as dimple ceramic lagging.
Abrasion Level
Impact of Conveyed Material:
The type and abrasiveness of the material being conveyed significantly affect the choice of lagging. Materials that are highly abrasive, such as sand, gravel, and ores, necessitate lagging with exceptional wear resistance.
- High Abrasion Materials: Ceramic lagging, both dimpled and smooth, is ideal for handling abrasive materials. Its high resistance to wear ensures that the lagging and pulley have a long operational life, even in harsh conditions.
- Low Abrasion Materials: For less abrasive materials, such as packaged goods or lighter aggregates, rubber lagging types, including plain and diamond grooved rubber lagging, may suffice. These materials still offer adequate protection and friction without the need for the enhanced durability of ceramics.
Pulley Type
Drive Pulleys:
Drive pulleys require lagging that maximizes friction and minimizes slippage to ensure efficient power transmission. Therefore, lagging types such as dimple ceramic lagging or diamond grooved rubber lagging are ideal for drive pulleys. These types provide the necessary grip to maintain consistent belt movement and operational efficiency.
Non-Drive Pulleys:
Non-drive pulleys, such as tail and bend pulleys, do not transmit power but need to manage belt tension and alignment. For these pulleys, plain rubber lagging or smooth ceramic lagging is typically sufficient. These types of lagging protect the pulley surface from wear and ensure smooth belt travel without requiring the enhanced friction needed by drive pulleys.
Belt Speed and Tension
Impact on Lagging Selection:
Belt speed and tension are critical factors that influence the choice of conveyor pulley lagging types. High-speed and high-tension belts exert significant force on the pulley, necessitating robust lagging materials.
- High-Speed Belts: For conveyor systems with high-speed belts, lagging with superior wear resistance and consistent friction is essential. Ceramic lagging, especially smooth ceramic lagging, is well-suited for high-speed applications due to its durability and ability to maintain grip.
- High-Tension Belts: High-tension belts require lagging that can withstand the increased forces without deforming or wearing prematurely. Dimple ceramic lagging is ideal in such scenarios because its enhanced grip and robustness handle high tension effectively.
Considerations:
- Wear and Tear: High speeds and tensions increase wear and tear on the lagging and pulley. Selecting a lagging material with high abrasion resistance, such as ceramic, ensures longevity and reduces maintenance frequency.
- Heat Generation: High-speed operations can generate heat, affecting the lagging material. Ceramic lagging is advantageous in these conditions due to its heat-resistant properties.
FAQS about Conveyor Pulley Lagging Types
Ceramic lagging is a type of pulley lagging that incorporates ceramic tiles embedded in a rubber matrix. This combination provides a highly durable and wear-resistant surface that significantly enhances the grip and traction between the conveyor belt and the pulley. Ceramic lagging is especially beneficial in environments where the pulley is subjected to high levels of abrasion, impact, or slippage.
The ceramic tiles are often arranged in a pattern that maximizes surface contact and improves the belt’s traction on the pulley. This type of lagging is known for its superior wear resistance compared to traditional rubber lagging, making it ideal for harsh conditions found in industries like mining, cement, and aggregate processing.
Ceramic lagging helps to extend the service life of the conveyor system by protecting the pulley from excessive wear and tear, reducing maintenance costs, and improving the overall efficiency and reliability of the conveyor system. It is particularly effective in applications where the conveyed materials are abrasive or where the conveyor system operates in challenging environmental conditions.
The herringbone lagging pattern is a type of rubber lagging that features a V-shaped or chevron pattern arranged in a herringbone design. This pattern is specifically designed to enhance the grip and traction between the conveyor belt and the pulley. The herringbone design channels water, dirt, and debris away from the belt, reducing slippage and ensuring consistent belt performance even in wet or dirty conditions.
This type of lagging is particularly effective in applications where the belt is exposed to moisture, heavy dust, or other contaminants. The herringbone pattern helps to improve the overall efficiency and reliability of the conveyor system by maintaining better contact between the belt and the pulley, reducing downtime, and extending the life of both the belt and the pulley. It is commonly used in industries such as mining, quarrying, and bulk material handling, where robust and reliable performance is essential.
Conveyor systems use various types of pulleys, each serving a distinct function. The main types include:
Drive Pulley: This is the primary pulley that drives the conveyor belt. It is powered by a motor and is responsible for moving the belt and the materials on it. The drive pulley is typically located at the discharge end of the conveyor.
Tail Pulley: Located at the opposite end of the drive pulley, the tail pulley provides tension and direction to the conveyor belt. It helps to keep the belt aligned and taut.
Snub Pulley: Positioned close to the drive pulley, the snub pulley increases the wrap angle of the belt around the drive pulley, enhancing traction and reducing slippage.
Take-Up Pulley: This pulley is used to maintain proper belt tension. It is adjustable and helps to compensate for belt stretch and wear over time.
Bend Pulley: Used to change the direction of the belt, bend pulleys are typically found in areas where the belt needs to navigate turns or changes in elevation.
Return Pulley: Also known as a return idler, this pulley supports the return side of the belt and helps to maintain its alignment.
Each type of pulley plays a critical role in the efficient operation and longevity of a conveyor system, ensuring smooth and consistent movement of materials.
Rubber lagging comes in various types, each designed to meet specific operational requirements and conditions. The main types include:
Plain Rubber Lagging: This is the most basic type, featuring a smooth rubber surface. It is suitable for general-purpose applications where slippage is minimal and grip requirements are moderate.
Diamond Rubber Lagging: Also known as rhomboid lagging, this type has a diamond-shaped pattern on the surface. It enhances grip and is ideal for conditions where there is moderate to high slippage.
Chevron Rubber Lagging: Featuring a chevron pattern, this lagging type offers excellent traction and is particularly effective in applications with high slippage and wet conditions. It helps to channel water and debris away from the belt.
Ceramic-Embedded Rubber Lagging: This combines rubber with ceramic tiles embedded in the surface. It provides superior abrasion resistance and is suitable for extremely harsh conditions, such as mining operations.
Plain Textured Rubber Lagging: Similar to plain rubber lagging but with a textured surface, it provides better grip without the complex patterns of diamond or chevron lagging.
Each type of rubber lagging is chosen based on specific operational needs, such as the level of slippage, environmental conditions, and the nature of the materials being conveyed.
Last Updated on June 12, 2024 by Jordan Smith
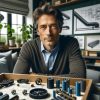
Jordan Smith, a seasoned professional with over 20 years of experience in the conveyor system industry. Jordan’s expertise lies in providing comprehensive solutions for conveyor rollers, belts, and accessories, catering to a wide range of industrial needs. From initial design and configuration to installation and meticulous troubleshooting, Jordan is adept at handling all aspects of conveyor system management. Whether you’re looking to upgrade your production line with efficient conveyor belts, require custom conveyor rollers for specific operations, or need expert advice on selecting the right conveyor accessories for your facility, Jordan is your reliable consultant. For any inquiries or assistance with conveyor system optimization, Jordan is available to share his wealth of knowledge and experience. Feel free to reach out at any time for professional guidance on all matters related to conveyor rollers, belts, and accessories.