Challenges with the Largest Conveyor Belt in the World
The largest conveyor belt in the world is a marvel of engineering, stretching over vast distances to transport materials efficiently across challenging terrains. This enormous conveyor system plays a critical role in various industries, including mining and manufacturing, where it moves large quantities of materials with ease. The significance of the largest conveyor belt in the world lies in its ability to enhance operational efficiency, reduce transportation costs, and minimize environmental impact. Its applications are diverse, ranging from carrying minerals in mines to transporting goods in industrial settings, showcasing the versatility and importance of this engineering feat.
Top 10 Largest Conveyor Belt in the World
The world’s largest conveyor belts are engineering marvels designed to transport vast quantities of materials over long distances. These belts play a crucial role in various industries, particularly mining, where they move raw materials from extraction points to processing facilities. Below is a detailed list and description of the top 10 largest conveyor belts globally, including their lengths, locations, and primary uses.
1. Bou Craa, Western Sahara
- Length: Approximately 98 kilometers (61 miles)
- Location: Bou Craa, Western Sahara
- Primary Use: Phosphate transportation
- Description: The Bou Craa conveyor belt is considered the longest conveyor belt system in the world. It is used to transport phosphate from the Bou Craa mine in Western Sahara to the coastal city of El-Aaiun, where the phosphate is processed and shipped. The belt’s massive length and capacity highlight the efficiency of using conveyor systems for large-scale material transportation.
2. Boddington Bauxite Mine, Australia
- Length: Approximately 31 kilometers (19 miles)
- Location: Boddington, Western Australia
- Primary Use: Bauxite transportation
- Description: This conveyor belt is used to transport bauxite from the Boddington Bauxite Mine to the alumina refinery. The system’s design ensures the continuous and efficient flow of bauxite, playing a critical role in the production of alumina.
3. Curragh, Australia
- Length: Approximately 20 kilometers (12.4 miles)
- Location: Central Queensland, Australia
- Primary Use: Coal transportation
- Description: The Curragh conveyor belt system transports coal from the Curragh coal mine to the nearby processing plant. This belt system is notable for its capacity and efficiency, supporting one of Australia’s major coal mines.
4. MRC Cable Belt, Chile
- Length: Approximately 31 kilometers (19 miles)
- Location: Los Pelambres, Chile
- Primary Use: Copper ore transportation
- Description: The MRC Cable Belt system at the Los Pelambres copper mine in Chile is one of the longest single-belt conveyor systems. It transports copper ore from the mine to the processing plant, significantly improving the efficiency and cost-effectiveness of the mining operation.
5. Shanxi Datong, China
- Length: Approximately 30 kilometers (18.6 miles)
- Location: Shanxi Province, China
- Primary Use: Coal transportation
- Description: This conveyor system is used in one of China’s largest coal mining operations. It efficiently moves coal from the mining site to the processing facilities, demonstrating the importance of conveyor systems in large-scale coal mining.
6. Raghunathpur, India
- Length: Approximately 20 kilometers (12.4 miles)
- Location: West Bengal, India
- Primary Use: Coal transportation
- Description: The Raghunathpur conveyor belt transports coal from the mining site to the thermal power plant. It is an essential component of India’s energy infrastructure, ensuring a steady supply of coal for power generation.
7. Sichuan, China
- Length: Approximately 25 kilometers (15.5 miles)
- Location: Sichuan Province, China
- Primary Use: Limestone transportation
- Description: This conveyor system is used to transport limestone from the quarry to the cement plant. The efficient movement of raw materials supports the large-scale production of cement in the region.
8. Hanson, UK
- Length: Approximately 18 kilometers (11.2 miles)
- Location: Peak District, UK
- Primary Use: Limestone transportation
- Description: The Hanson conveyor belt is used in the Peak District limestone quarries. It transports limestone to various processing facilities, highlighting the role of conveyor systems in the UK’s mining industry.
9. Foskor, South Africa
- Length: Approximately 26 kilometers (16 miles)
- Location: Phalaborwa, South Africa
- Primary Use: Phosphate transportation
- Description: The Foskor conveyor system transports phosphate from the Phalaborwa mine to the processing plant. This system is crucial for the efficient production and export of phosphate products.
10. Yadong Cement, China
- Length: Approximately 22 kilometers (13.7 miles)
- Location: Lhasa, Tibet, China
- Primary Use: Limestone transportation
- Description: This conveyor belt is used to transport limestone from the quarry to the Yadong Cement plant. It is an integral part of the cement production process in Tibet, ensuring a continuous supply of raw materials.
Exploring the Second Largest Conveyor Belt in the World
The second largest conveyor belt in the world, located in Boddington, Western Australia, is a testament to the engineering prowess and industrial capability required to support large-scale mining operations. This section will provide an in-depth look at this impressive conveyor belt, highlighting its features, location, and operational details.
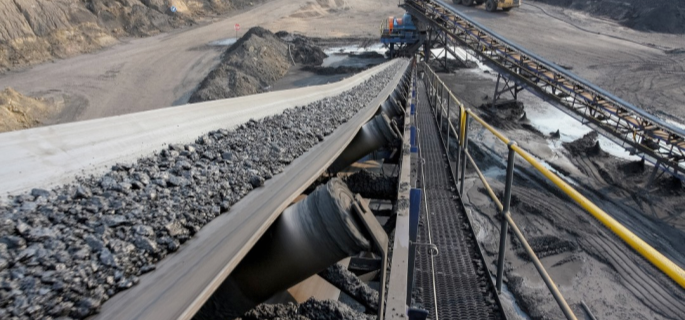
Location and Purpose
The Boddington conveyor belt is situated in Western Australia, primarily serving the Boddington Bauxite Mine. This region is known for its rich bauxite deposits, which are essential for producing alumina and aluminum. The conveyor belt’s primary purpose is to transport bauxite from the mining site to the alumina refinery, facilitating the efficient and continuous movement of materials.
Key Features
1. Length and Capacity
- The Boddington conveyor belt spans approximately 31 kilometers (19 miles), making it the second longest conveyor belt in the world. Its substantial length allows it to cover the distance between the mine and the refinery seamlessly.
- The belt is designed to handle a high capacity of bauxite, ensuring that the transportation process meets the demands of the mining operation. The belt’s robust construction and efficient design enable it to move large quantities of bauxite quickly and reliably.
2. Engineering and Construction
- The construction of the Boddington conveyor belt involved significant engineering efforts. The belt is made from durable materials that can withstand the harsh conditions of mining operations, including exposure to heavy loads, abrasive materials, and varying weather conditions.
- The belt’s support structure is designed to provide stability and durability, ensuring smooth and efficient operation. Advanced engineering techniques were used to optimize the belt’s performance and minimize maintenance requirements.
3. Environmental Considerations
- Environmental sustainability is a key consideration in the design and operation of the Boddington conveyor belt. The system is designed to minimize environmental impact by reducing the need for truck transportation, which lowers greenhouse gas emissions and reduces road traffic.
- The belt’s design also includes measures to prevent spillage and dust generation, further minimizing its environmental footprint. These features contribute to the overall sustainability of the mining operation.
Operational Details
1. Integration with Mining Operations
- The Boddington conveyor belt is seamlessly integrated into the mining operations, forming a critical link between the extraction site and the processing facilities. The belt’s efficient operation ensures that bauxite is transported continuously, supporting the refinery’s production schedule.
- The conveyor system is monitored and controlled using advanced automation and monitoring technologies. These systems ensure optimal performance, detect potential issues early, and allow for timely maintenance and adjustments.
2. Maintenance and Upkeep
- Regular maintenance is essential to keep the Boddington conveyor belt operating efficiently. Maintenance activities include inspecting the belt for wear and tear, ensuring the support structure is intact, and lubricating moving parts.
- The use of predictive maintenance technologies helps identify potential problems before they cause significant disruptions. This proactive approach to maintenance reduces downtime and extends the lifespan of the conveyor belt.
3. Economic Impact
- The Boddington conveyor belt significantly contributes to the economic viability of the Boddington Bauxite Mine. By providing a reliable and efficient transportation system, the belt helps reduce operational costs and improve productivity.
- The conveyor system also supports local employment and contributes to the economic development of the region. Its operation provides jobs and generates revenue, benefiting the local community.
World’s Largest Border-Crossing Conveyor Belt
The world’s largest single-belt conveyor that crosses international borders is located between India and Bangladesh. This impressive conveyor belt, constructed in 2004, spans approximately 11 miles (17 kilometers) in total length. Specifically, over 4 miles of the belt are in the Indian state of Meghalaya, and more than 6 miles are in Bangladesh. The primary purpose of this conveyor belt is to transport limestone and shale from a quarry in India to a cement factory in Bangladesh.
Comprehensive understanding
1.Construction and Purpose
The conveyor was built to facilitate the efficient and continuous transport of raw materials, namely limestone and shale, from an Indian quarry to a cement factory in Bangladesh. This setup allows for the transportation of approximately 960 tonnes of material every hour, ensuring a steady supply for the cement production process.
2.Design and Elevation
To prevent flooding during the monsoon season, the entire conveyor system has been elevated about five meters above the ground on a specially designed frame structure. This elevation is crucial for maintaining uninterrupted operation during heavy rains and ensuring the longevity of the conveyor system.
3.Operational Features
The belt is equipped with special rollers that can move both horizontally and vertically, adapting to the terrain and ensuring smooth operation throughout its length. These rollers help in maintaining the alignment and functionality of the belt over varying landscapes.
4.Maintenance and Collaboration
Maintenance of the conveyor system is conducted via overhead trolleys that travel above the belt. Both India and Bangladesh have their own trolleys and maintenance teams responsible for their respective sections of the conveyor. This bi-national cooperation ensures that the entire system remains in good working condition.
5.Economic and Environmental Impact
The conveyor belt not only boosts the efficiency of transporting raw materials but also reduces the need for road transport, thereby lowering carbon emissions and road congestion. This environmentally friendly solution exemplifies the benefits of modern engineering in cross-border industrial projects.
Replacing conveyor belt
Replacing the world’s longest trans-border conveyor belt, which runs between India and Bangladesh, is a complex and meticulous process. This conveyor, stretching approximately 11 miles (17 kilometers) and transporting limestone and shale from an Indian quarry to a Bangladeshi cement factory, requires careful planning and execution for its replacement.
1.Preliminary Assessment and Planning
- Inspection: Conduct a thorough inspection of the existing conveyor system to identify the specific components that need replacement.
- Engineering Design: Develop a detailed engineering plan that outlines the new conveyor belt’s specifications, materials, and structural requirements. This includes assessing the terrain and environmental conditions.
- Budget and Timeline: Establish a budget and timeline for the replacement project, including procurement of materials, labor costs, and expected downtime.
2.Procurement of Materials
- Sourcing: Source high-quality materials for the new conveyor belt, including the belt itself, rollers, support structures, and any necessary electronic components for automation and monitoring.
- Customization: Ensure that the materials are customized to meet the specific needs of the terrain and the operational requirements, such as the ability to withstand monsoon floods.
3.Preparation and Dismantling
- Temporary Shutdown: Plan for a temporary shutdown of the conveyor system to minimize disruption to the cement factory’s operations. Coordinate this with both Indian and Bangladeshi authorities and stakeholders.
- Dismantling: Carefully dismantle the existing conveyor belt and associated components. This includes removing the old belt, rollers, and support structures while ensuring safety protocols are strictly followed.
4.Installation of the New Conveyor Belt
- Foundation and Support: Install new support structures and foundation frames elevated about five meters to prevent flooding during the monsoon season.
- Belt and Rollers: Install the new conveyor belt and rollers, ensuring they are properly aligned and tensioned. Special rollers that can move both horizontally and vertically should be fitted to adapt to the varying terrain.
- Safety Features: Implement safety features, such as emergency stop mechanisms, guard rails, and maintenance access points, to ensure safe operation and easy maintenance.
5.Testing and Commissioning
- Initial Testing: Conduct initial tests to ensure the new conveyor belt operates smoothly and efficiently. This includes running the belt empty and then with a load to check for any alignment or operational issues.
- Calibration: Calibrate the belt’s speed, tension, and alignment to optimize performance and ensure it can handle the 960 tonnes per hour capacity.
- Safety Checks: Perform comprehensive safety checks to ensure all safety mechanisms are functional and that the system complies with international safety standards.
6.Ongoing Maintenance and Monitoring
- Maintenance Schedule: Establish a regular maintenance schedule to keep the conveyor belt in optimal condition. This includes routine inspections, lubrication of moving parts, and replacement of worn components.
- Monitoring Systems: Install advanced monitoring systems to continuously track the belt’s performance, detect potential issues early, and ensure efficient operation. This may include sensors for belt speed, load weight, and alignment.
7.Training and Handover
- Training: Provide training for the maintenance teams from both India and Bangladesh on the new system’s operation and maintenance procedures.
- Handover: Officially hand over the new conveyor system to the operational teams, ensuring they are fully equipped and informed about its functionalities and maintenance requirements.
Largest Conveyor Belt in the World: The Phosphorus Conveyor Problem
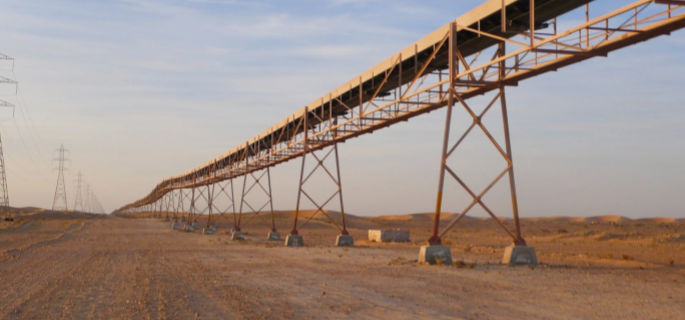
The phosphorus conveyor problem is a significant issue that affects conveyor belt operations in various industries, particularly those involved in mining and material processing. This section will analyze the phosphorus conveyor problem, its implications for conveyor belt operations, and potential solutions to address the issue.
The phosphorus conveyor problem arises when phosphorus-containing materials are transported using conveyor belts. Phosphorus is a reactive element that can cause several issues when it comes into contact with conveyor belts and related equipment. The problem is particularly prevalent in industries such as phosphate mining and fertilizer production, where phosphorus is a key component of the transported materials.
Implications for Conveyor Belt Operations
1. Material Build-Up
- One of the primary issues caused by the phosphorus conveyor problem is the build-up of phosphorus-containing materials on the conveyor belt and associated equipment. This build-up can lead to reduced efficiency, increased wear and tear, and potential blockages.
- The accumulation of phosphorus materials can also affect the belt’s tracking and alignment, leading to operational disruptions and increased maintenance requirements.
2. Corrosion and Damage
- Phosphorus is highly reactive and can cause corrosion and damage to the conveyor belt and its components. The chemical reaction between phosphorus and the materials used in the belt’s construction can weaken the belt, reducing its lifespan and reliability.
- Corrosion can also affect the belt’s support structure, rollers, and other mechanical components, leading to increased maintenance costs and potential safety hazards.
3. Safety Concerns
- The phosphorus conveyor problem poses several safety concerns for workers and equipment. The reactive nature of phosphorus can create hazardous conditions, including the risk of fire and explosions.
- Ensuring the safety of workers requires implementing stringent safety protocols and using protective equipment to mitigate the risks associated with handling phosphorus-containing materials.
Potential Solutions
1. Material Handling Improvements
- Improving material handling practices can help mitigate the phosphorus conveyor problem. This includes using specialized equipment and techniques to minimize the build-up of phosphorus materials on the conveyor belt.
- Regular cleaning and maintenance of the belt and associated equipment can prevent the accumulation of materials and reduce the risk of blockages and operational disruptions.
2. Corrosion-Resistant Materials
- Using corrosion-resistant materials in the construction of conveyor belts and related equipment can help address the issues caused by phosphorus. Materials such as stainless steel, coated metals, and specialized polymers can withstand the corrosive effects of phosphorus, extending the lifespan and reliability of the belt.
- Implementing protective coatings and treatments on the belt and its components can also provide an additional layer of defense against corrosion.
3. Advanced Monitoring and Control Systems
- Advanced monitoring and control systems can help detect and address issues related to the phosphorus conveyor problem early. These systems can monitor the condition of the belt, track material build-up, and identify potential corrosion and damage.
- Automated control systems can adjust the operation of the conveyor belt to prevent excessive material accumulation and ensure optimal performance. Predictive maintenance technologies can also be used to schedule maintenance activities proactively, reducing downtime and improving efficiency.
4. Safety Protocols and Training
- Implementing stringent safety protocols and providing training for workers is essential to mitigate the safety risks associated with the phosphorus conveyor problem. This includes using protective equipment, following safe handling practices, and conducting regular safety audits.
- Emergency response plans should be in place to address potential incidents, such as fires or explosions, ensuring the safety of workers and minimizing the impact on operations.
5. Research and Development
- Ongoing research and development efforts are crucial to finding innovative solutions to the phosphorus conveyor problem. This includes developing new materials and technologies that can withstand the challenges posed by phosphorus-containing materials.
- Collaboration between industry experts, researchers, and equipment manufacturers can lead to the development of more effective and efficient conveyor systems that address the phosphorus conveyor problem.
The phosphorus conveyor problem is a significant challenge for industries that transport phosphorus-containing materials. The issues of material build-up, corrosion, and safety concerns can impact the efficiency, reliability, and safety of conveyor belt operations. However, through improved material handling practices, the use of corrosion-resistant materials, advanced monitoring and control systems, stringent safety protocols, and ongoing research and development, it is possible to mitigate the impact of the phosphorus conveyor problem and ensure the smooth and safe operation of conveyor systems.
By addressing the phosphorus conveyor problem, industries can improve the efficiency and reliability of their conveyor belt operations, reduce maintenance costs, and enhance the safety of their workers. This proactive approach to managing the challenges posed by phosphorus can lead to more sustainable and effective material transportation solutions, supporting the continued growth and success of the industries involved.
Largest Conveyor Belt in the World: Overview of the Largest Phosphate Mine in the World
Phosphates are a crucial component in global agriculture, providing essential nutrients that support the growth of crops. Among the numerous phosphate mines worldwide, the Bou Craa phosphate mine in Western Sahara stands out as the largest phosphate mine in the world. This section provides a comprehensive overview of this significant mining operation, detailing its history, production capacity, and economic impact.

History of the Bou Craa Phosphate Mine
The Bou Craa phosphate mine, located in the Western Sahara region, has a rich history dating back to its discovery in 1947. The initial exploration and discovery of phosphate deposits in the area were driven by the growing global demand for fertilizers. The Spanish government, which controlled the region at the time, established the Bou Craa mine in the early 1960s. The mine quickly became a cornerstone of the region’s economy due to its vast phosphate reserves.
The Bou Craa mine’s development faced several challenges, including geopolitical tensions and the harsh desert environment. Despite these obstacles, the mine began full-scale production in 1972. The Western Sahara conflict, which erupted in the mid-1970s, posed significant threats to the mine’s operations. However, Morocco’s annexation of Western Sahara in 1975 allowed for the continued exploitation of the phosphate reserves.
Production Capacity of the Bou Craa Phosphate Mine
The Bou Craa mine is renowned for its impressive production capacity, making it the largest phosphate mine in the world. The mine boasts an annual production rate of approximately 3 million metric tons of phosphate rock. This high output is facilitated by the mine’s extensive infrastructure, including the world’s longest conveyor belt system, which stretches over 100 kilometers to transport the phosphate rock to the coast for export.
The phosphate extracted from Bou Craa is of high quality, with a high concentration of phosphoric acid, making it highly sought after in the global market. The mine’s production is crucial for Morocco, which is the world’s third-largest producer of phosphates, contributing significantly to the country’s economy.
Economic Impact of the Bou Craa Phosphate Mine
The Bou Craa phosphate mine plays a pivotal role in the economy of both Western Sahara and Morocco. The revenues generated from the mine are substantial, providing critical financial resources for the Moroccan government. These funds are used to support various sectors, including infrastructure development, healthcare, and education, thereby improving the quality of life for the local population.
In addition to its direct economic contributions, the Bou Craa mine also supports numerous ancillary industries, such as transportation and manufacturing. The employment opportunities created by the mine are significant, providing jobs for thousands of individuals in the region. The mine’s operations also foster economic growth by attracting investments and facilitating trade with other countries.
Uses of the Phosphate Mine
1.Fertilizer Production
Phosphate ore is primarily used to produce phosphate fertilizers, which enhance soil fertility and increase crop yields.
2.Animal Feed
Phosphates from ore are used as additives in animal feed to provide essential phosphorus, promoting growth and bone health in livestock.
3.Industrial Chemicals
Phosphate ore is processed into chemicals like phosphoric acid, which are used in manufacturing detergents, cleaners, and other industrial products.
4.Water Treatment
Phosphates are utilized in water treatment processes to remove contaminants and purify water, making it safer for consumption and use.
5.Aluminum Smelting
Phosphate ore can be used as a flux in aluminum smelting to assist in the extraction of aluminum from its ore.
6.Glass Manufacturing
Phosphates are used in the production of certain types of glass, including specialty glasses, to improve their quality and durability.
7.Metallurgy
Phosphates are used in the metallurgy industry as a flux in the production of steel and other metals to remove impurities and improve the quality of the metal.
8.Fireproofing Agents
Phosphates are used in fireproofing materials and coatings to enhance their fire resistance.
9.Ceramics
Phosphates are incorporated into ceramic materials to improve their properties, such as strength and thermal resistance.
10.Food Industry
Phosphates are used as food additives in the food industry to regulate acidity, improve texture, and act as preservatives in various food products.
Largest Conveyor Belt in the World: Inside the Bou Craa Phosphate Mine
To truly understand the significance of the Bou Craa phosphate mine, it is essential to delve into its inner workings, examining its operational processes, technological advancements, and its overall contribution to the global phosphate industry.
Operational Processes at Bou Craa
The mining process at Bou Craa begins with the extraction of phosphate rock from open-pit mines. Advanced mining equipment, including draglines and excavators, are used to remove the overburden and access the phosphate-bearing strata. Once the phosphate rock is exposed, it is blasted and transported to processing facilities.
The processing of the extracted phosphate involves several stages, including crushing, screening, and washing. These processes are designed to increase the phosphate content and remove impurities. The processed phosphate rock is then transported via the largest conveyor belt in the world to the port of El Aaiún, where it is loaded onto ships for export.
Technological Advancements at Bou Craa
The Bou Craa phosphate mine is a testament to the advancements in mining technology. The mine utilizes state-of-the-art equipment and techniques to enhance efficiency and productivity. One of the most notable technological features is the extensive conveyor belt system, which significantly reduces the cost and environmental impact of transporting phosphate rock over long distances.
In addition to the conveyor belt system, the mine employs advanced monitoring and control systems to optimize operations. These systems include remote sensing technology, automated drilling equipment, and advanced data analytics, all of which contribute to improved resource management and operational efficiency.
Contribution to the Global Phosphate Industry
The Bou Craa phosphate mine holds a significant position in the global phosphate industry. The high-quality phosphate produced at Bou Craa is in high demand, particularly in the agricultural sector, where it is used to manufacture fertilizers. The mine’s output helps to meet the growing global demand for phosphates, ensuring a stable supply of this essential resource.
Furthermore, the Bou Craa mine’s operations have a broader impact on the global phosphate market. The mine’s production levels and pricing strategies influence global phosphate prices, affecting both producers and consumers worldwide. The stability and reliability of Bou Craa’s phosphate supply are critical for maintaining balance in the global market.
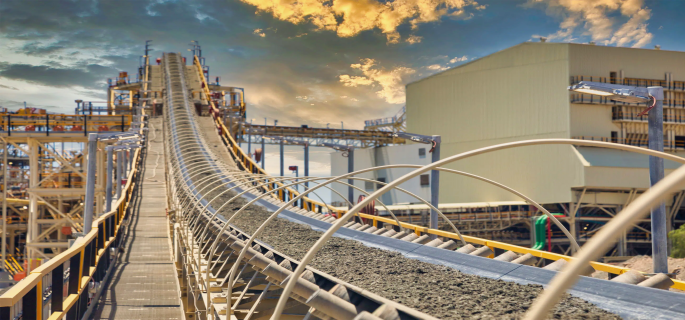
Largest Conveyor Belt in the World: The Significance of Western Sahara Phosphate Reserves
The phosphate reserves in Western Sahara are among the largest in the world, and their significance extends beyond the region, impacting global phosphate supply and the geopolitical landscape.
Importance of Western Sahara Phosphate Reserves
Western Sahara’s phosphate reserves are of immense importance due to their size and quality. The region is estimated to hold over 1.7 billion metric tons of phosphate rock, making it one of the largest phosphate reserves globally. The high concentration of phosphoric acid in the rock further enhances its value, making it a critical resource for the production of fertilizers and other phosphate-based products.
The exploitation of these reserves is vital for meeting the global demand for phosphates. As the world’s population continues to grow, the need for agricultural products increases, driving the demand for fertilizers. Western Sahara’s phosphate reserves play a crucial role in ensuring a stable and sufficient supply of phosphates to support global agriculture.
Impact on Global Phosphate Supply
The phosphate reserves in Western Sahara have a significant impact on the global phosphate supply. The region’s production capabilities contribute substantially to the overall availability of phosphates, helping to stabilize prices and ensure a consistent supply. The Bou Craa mine, as the largest phosphate mine in the world, is a key player in this dynamic, with its production directly influencing global market conditions.
The strategic location of Western Sahara also enhances its significance. The proximity to major shipping routes allows for efficient export of phosphate rock to various international markets. This logistical advantage further strengthens Western Sahara’s role in the global phosphate industry, making it a crucial hub for the distribution of phosphate resources.
Geopolitical Implications
The phosphate reserves in Western Sahara are not only economically significant but also have profound geopolitical implications. The region’s status as a disputed territory adds a layer of complexity to the exploitation and management of its phosphate resources. The ongoing conflict between Morocco and the Polisario Front, a Sahrawi rebel national liberation movement, has led to international debates and controversies over the control and use of these resources.
Morocco’s control over the Bou Craa mine and the broader phosphate reserves has been a point of contention, with various international organizations and countries expressing differing views on the legitimacy of Morocco’s claims. The revenues generated from phosphate mining in Western Sahara are critical for Morocco, providing substantial financial resources that support its national economy.
The geopolitical significance of Western Sahara’s phosphate reserves extends beyond the immediate region, influencing global diplomatic relations and economic policies. The management and exploitation of these resources are closely watched by the international community, with implications for trade, investment, and regional stability.
Environmental and Social Considerations
The exploitation of phosphate reserves in Western Sahara also raises important environmental and social considerations. The mining operations, including those at the Bou Craa mine, have significant environmental impacts, including habitat disruption, water usage, and potential pollution. Efforts to mitigate these impacts are crucial for sustainable mining practices.
Socially, the phosphate mining industry in Western Sahara affects local communities, providing employment opportunities and contributing to economic development. However, it also brings challenges, such as displacement and social unrest. Balancing the economic benefits of phosphate mining with environmental and social responsibilities is essential for the long-term sustainability of the industry.
Future Prospects
Looking ahead, the future prospects for Western Sahara’s phosphate reserves remain promising. Advances in mining technology and resource management are expected to enhance the efficiency and sustainability of phosphate extraction. Additionally, the global demand for phosphates is likely to continue growing, driven by agricultural needs and the development of new phosphate-based products.
The resolution of geopolitical tensions in the region could further unlock the potential of Western Sahara’s phosphate reserves. A stable and peaceful environment would facilitate increased investment, improved infrastructure, and greater international cooperation, all of which would contribute to the optimal utilization of these valuable resources.
The phosphate reserves in Western Sahara, and particularly the operations at the Bou Craa mine, are of immense significance to the global phosphate industry. The largest conveyor belt in the world, part of this extensive mining operation, symbolizes the scale and importance of the phosphate resources in this region. The economic, geopolitical, and environmental dimensions of these reserves highlight their critical role in supporting global agriculture and economic development. As the world continues to rely on phosphates for food production and other uses, the strategic importance of Western Sahara’s phosphate reserves will remain a focal point of attention and investment.
FAQs about Largest Conveyor Belt in the World
The world’s biggest conveyor belt is located in the Western Sahara, running from the Bou Craa phosphate mines to the coast at El-Aaiun. This impressive conveyor belt system stretches over 100 kilometers (about 62 miles) and is used to transport phosphate rocks from the mining area to the coast for shipment. The conveyor belt is a crucial component of the mining operation, significantly reducing the need for truck transportation and making the process more efficient and environmentally friendly.
Several companies dominate the conveyor belt industry due to their innovation, quality, and comprehensive service offerings. Some of the biggest conveyor belt companies include:
Gram Conveyor – Renowned for its cutting-edge conveyor technology and exceptional service.With a strong focus on innovation and quality, Gram Conveyor is committed to providing customized solutions , ensuring efficiency and durability in every project they undertake.
Fenner Dunlop – Known for producing high-quality conveyor belts for mining and industrial applications.
ContiTech AG – A subsidiary of Continental AG, ContiTech offers a wide range of conveyor belt products and services.
Bridgestone Corporation – A leading manufacturer of conveyor belts, particularly known for their high durability and performance.
Phoenix Conveyor Belt Systems – Part of the Continental AG group, Phoenix specializes in developing advanced conveyor belt systems.
Bando Chemical Industries, Ltd. – Provides a variety of conveyor belts for different industrial needs, including automotive and manufacturing sectors. These companies are recognized for their innovative technologies, extensive product ranges, and commitment to quality and customer service.
The strongest conveyor belt in the world is the ST10000, produced by ContiTech AG. This conveyor belt is specifically designed for high-stress applications and can withstand extreme conditions. It is made of steel cords and offers an ultimate tensile strength of 10,000 N/mm (Newtons per millimeter). This exceptional strength allows the ST10000 to carry heavy loads over long distances, making it ideal for demanding industries such as mining, where reliability and durability are paramount.
The world’s longest single flight conveyor is located at the Impumelelo coal mine in South Africa. This conveyor belt spans an incredible distance of 27 kilometers (about 16.8 miles) in a single, continuous flight. Designed by Sandvik Mining and Construction, this conveyor belt system is a testament to modern engineering, capable of transporting coal from the mining site to the processing plant efficiently. The single flight design minimizes transfer points, reducing maintenance needs and increasing operational efficiency. This conveyor belt represents a significant achievement in conveyor technology, showcasing the capability to move large quantities of material over vast distances with minimal interruption.
The world’s longest conveyor belt is located in Western Sahara. This conveyor belt stretches 61 miles (about 98 kilometers) from the phosphate mines of Bou Craa to the port city of Marsa near El-Aaiun. This impressive system transports phosphate rock, a critical component in agricultural fertilizers, from the mining site to the coast for export.
The longest conveyor belt in Texas is found at the North American Limestone Corporation (NALC) in Marble Falls. This overland conveyor system is used to transport crushed limestone from the quarry to the processing plant, covering a distance of several miles. This efficient system helps reduce the need for truck transportation, lowering operational costs and environmental impact.
In heavy industry, a “human conveyor belt” is commonly referred to as a “manual conveyor system” or “human-assisted conveyor system.” This term describes a system where human operators are involved in the handling and movement of materials along a conveyor line, often working in conjunction with automated conveyor belts.
Last Updated on August 16, 2024 by Jordan Smith
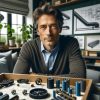
Jordan Smith, a seasoned professional with over 20 years of experience in the conveyor system industry. Jordan’s expertise lies in providing comprehensive solutions for conveyor rollers, belts, and accessories, catering to a wide range of industrial needs. From initial design and configuration to installation and meticulous troubleshooting, Jordan is adept at handling all aspects of conveyor system management. Whether you’re looking to upgrade your production line with efficient conveyor belts, require custom conveyor rollers for specific operations, or need expert advice on selecting the right conveyor accessories for your facility, Jordan is your reliable consultant. For any inquiries or assistance with conveyor system optimization, Jordan is available to share his wealth of knowledge and experience. Feel free to reach out at any time for professional guidance on all matters related to conveyor rollers, belts, and accessories.