Coal Conveyor in Thermal Power Plant Handing Systems
The coal conveyor in thermal power plant is a critical component that ensures the efficient transportation and handling of coal. These conveyors are designed to move large quantities of coal from storage areas to the boilers, facilitating a smooth and continuous supply. The importance of a coal conveyor in thermal power plant lies in its ability to minimize manual labor, reduce operational costs, and enhance overall plant efficiency. By automating the coal handling process, these conveyors play a vital role in maintaining the consistent performance and reliability of the power generation system. Their robust construction and design are essential for handling the heavy, abrasive nature of coal, ensuring durability and longevity.
What is Coal Conveyor in Thermal Power Plant
The coal conveyor in thermal power plant systems is crucial for transporting coal from storage areas to the boilers, ensuring a consistent and reliable fuel supply.Coal conveyor in thermal power plant efficiently transport large quantities, reducing costs and supporting seamless operations in thermal power plants. Different types of coal conveyors are used to meet various operational requirements, each with unique features and benefits.
Types of Coal Conveyors
Coal conveyors come in several types, each designed to handle specific transportation needs within a thermal power plant. The primary types include belt conveyors, screw conveyors, and flight conveyors. Understanding the distinct advantages and applications of each can help optimize the coal handling process.
Belt Conveyors
Belt conveyors are among the most commonly used systems for long-distance coal transport in thermal power plants. They consist of an endless loop of carrying medium—the conveyor belt—that rotates around rollers. Belt conveyors are ideal for moving large quantities of coal efficiently over long distances.
Features of Belt Conveyors
- High Capacity:
Belt conveyors can transport large volumes of coal, making them suitable for power plants that require substantial fuel supplies. Their high capacity ensures a steady flow of coal to the boilers. - Long-Distance Transport:
These conveyors are designed to cover long distances, often spanning several kilometers. They provide a cost-effective solution for moving coal from remote storage areas to the plant. - Continuous Operation:
Belt conveyors operate continuously, reducing the need for frequent start-stop cycles. This continuous operation enhances efficiency and reduces wear and tear on the system. - Flexibility:
Belt conveyors can be customized to fit various layouts and elevations. They can navigate curves and inclines, allowing for flexible installation in different plant configurations.
Benefits of Belt Conveyors
- Efficiency: Belt conveyors offer high efficiency in coal transport, reducing operational costs and energy consumption.
- Reliability: The robust design and continuous operation minimize the risk of downtime, ensuring a reliable coal supply to the plant.
- Safety: Modern belt conveyors are equipped with safety features such as emergency stop buttons and anti-slip surfaces, enhancing worker safety.
Screw Conveyors
Screw conveyors are compact and efficient systems used for short-distance coal transport within thermal power plants. They consist of a helical screw blade that rotates inside a tube, moving coal along the conveyor.
Features of Screw Conveyors
- Compact Design:
Screw conveyors have a compact design, making them ideal for areas with limited space. Their small footprint allows for installation in tight spaces within the plant. - Efficient Material Handling:
The rotating screw mechanism ensures efficient material handling, moving coal quickly and evenly through the conveyor. - Enclosed System:
Screw conveyors are enclosed, preventing spillage and reducing dust generation. This feature is particularly important for maintaining cleanliness and minimizing environmental impact. - Versatility:
These conveyors can handle a variety of materials and are suitable for both horizontal and inclined installations. They can be used to transport coal to different levels within the plant.
Benefits of Screw Conveyors
- Space-Saving: The compact design of screw conveyors makes them suitable for installations where space is a constraint.
- Clean Operation: The enclosed system minimizes spillage and dust, contributing to a cleaner working environment.
- Cost-Effective: Screw conveyors are relatively inexpensive to install and maintain, offering a cost-effective solution for short-distance coal transport.
Flight Conveyors
Flight conveyors, also known as drag chain conveyors, are used for moving coal through multiple storage bins and hoppers within a thermal power plant. They consist of a series of flights or paddles attached to a chain that drags coal along a trough.
Features of Flight Conveyors
- Robust Construction:
Flight conveyors are built with heavy-duty materials, ensuring durability and long service life. Their robust construction can withstand the abrasive nature of coal. - Multiple Discharge Points:
These conveyors can have multiple discharge points, allowing coal to be delivered to various storage bins and hoppers. This feature is useful for distributing coal to different areas of the plant. - Horizontal and Inclined Transport:
Flight conveyors can transport coal both horizontally and at an incline, providing flexibility in plant layout and design. - Low Maintenance:
The simple design and rugged construction of flight conveyors result in low maintenance requirements, reducing downtime and maintenance costs.
Benefits of Flight Conveyors
- Versatile Transport: Flight conveyors are versatile and can handle various transport directions and elevations within the plant.
- Efficient Distribution: Multiple discharge points enable efficient distribution of coal to different storage areas.
- Durability: The heavy-duty construction ensures a long service life, even in demanding coal handling environments.
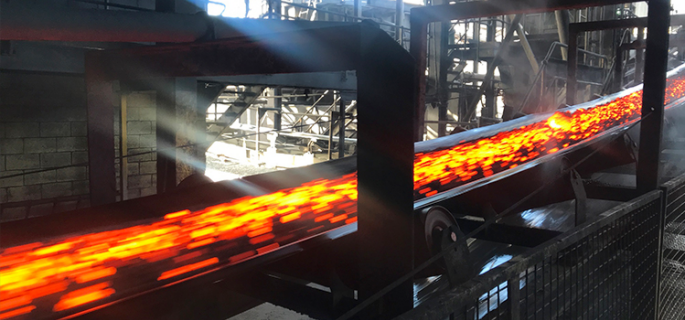
What is The Thermal Power Plant Conveyor System?
A thermal power plant conveyor system is an essential part of the power generation process, designed to transport materials such as coal, ash, and other fuel sources efficiently and reliably within the plant. Here’s a detailed overview:
Components of the Conveyor System
Belt Conveyors:
- Function: Transport coal from storage to the furnace or boiler.
- Features: Typically made of durable materials to handle heavy loads and resist wear.
Bucket Elevators:
- Function: Vertically lift coal and ash to higher levels.
- Features: Efficiently move materials between different sections of the plant.
Screw Conveyors:
- Function: Move ash and other by-products to disposal areas.
- Features: Enclosed design to prevent dust and material spillage.
Roller Conveyors:
- Function: Assist in material handling and processing within the plant.
- Features: Use rollers to facilitate the movement of heavy materials.
Vibrating Conveyors:
- Function: Move fine particles and ash.
- Features: Use vibration to move materials smoothly.
Functions of the Conveyor System
Coal Handling:
- Transporting Coal: Moves coal from unloading areas (trucks, trains) to storage silos or directly to the boiler feed.
- Crushing and Screening: Conveyor systems integrate with crushers and screens to ensure coal is of the required size for combustion.
Ash Handling:
- Removing Ash: Transports ash from the furnace to storage silos or disposal units.
- Cooling Ash: Some conveyors have integrated cooling mechanisms to handle hot ash.
Fuel Feeding:
- Continuous Supply: Ensures a steady supply of fuel to the furnace or boiler, maintaining efficient combustion and power generation.
Benefits of a Conveyor System in Thermal Power Plants
- Efficiency: Automated and continuous transport of materials enhances overall plant efficiency and reduces manual labor.
- Safety: Enclosed systems reduce dust, spillage, and exposure to hazardous materials, improving plant safety.
- Cost-Effective: Reduces operational costs by minimizing the need for manual material handling and improving throughput.
- Reliability: Durable materials and robust design ensure long-term reliability and minimal downtime.
In summary, a thermal power plant conveyor system is a crucial infrastructure that supports the continuous and efficient operation of the power plant by handling the transportation and processing of coal and ash.
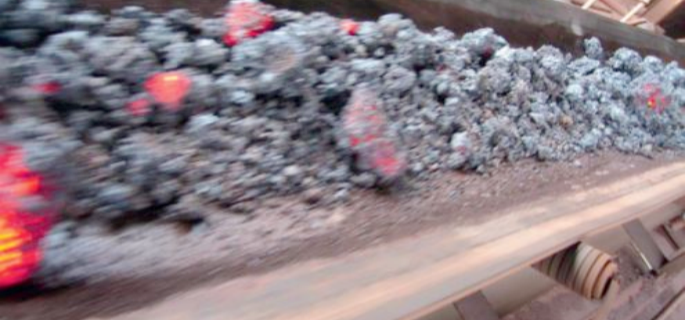
Coal Conveyor in Thermal Power Plant Specifications
A coal conveyor in a thermal power plant is a critical component responsible for transporting coal from storage areas to the power generation units. The efficiency and reliability of these conveyor systems directly impact the overall performance of the power plant. Below, we will delve into the specifications of coal conveyor belts used in thermal power plants, focusing on material, width, strength requirements, and the importance of durability and resistance to wear and tear.
Coal Conveyor Belt Specifications
Material Requirements
The material of the coal conveyor belt is crucial for ensuring the system’s longevity and efficiency. In thermal power plants, conveyor belts must withstand harsh conditions, including exposure to abrasive coal, high temperatures, and varying environmental factors. Typically, these belts are made from rubber compounds reinforced with materials like steel or polyester.
Rubber is chosen for its flexibility and resistance to impact and abrasion. High-quality rubber ensures that the belt can handle the rough texture of coal without significant wear and tear. Additionally, rubber’s resistance to high temperatures is essential, as the environment within a thermal power plant can be quite demanding.
Steel or polyester reinforcements are embedded within the rubber to enhance the belt’s strength and durability. Steel-cord belts are particularly favored in high-capacity conveyors due to their excellent tensile strength and resistance to elongation. On the other hand, polyester belts offer good flexibility and are less prone to damage from repeated bending.
Width Requirements
The width of a coal conveyor belt in a thermal power plant is determined by the volume of coal that needs to be transported. Wider belts are capable of handling larger quantities of coal, which is essential for meeting the high demands of power generation.
Standard widths for coal conveyor belts range from 500 mm to 2400 mm. The choice of width depends on factors such as the capacity of the conveyor system, the size of the coal particles, and the design of the power plant. For instance, a thermal power plant with a higher energy output requirement will need wider belts to transport a larger volume of coal efficiently.
Strength Requirements
The strength of a coal conveyor belt is another critical specification. These belts must be robust enough to carry heavy loads of coal over long distances without breaking or stretching excessively. The strength of a conveyor belt is usually specified in terms of its tensile strength, which is measured in newtons per millimeter of belt width (N/mm).
For coal conveyors in thermal power plants, belts typically need a tensile strength ranging from 500 N/mm to 2000 N/mm, depending on the load and distance requirements. Higher tensile strength belts are essential for applications where the conveyor must operate continuously under heavy loads, as they offer better resistance to stretching and can handle more weight without failure.
Importance of Durability and Resistance to Wear and Tear
Durability and resistance to wear and tear are paramount for coal conveyor belts in thermal power plants. The continuous movement of abrasive coal can quickly degrade the quality of a conveyor belt if it is not designed to withstand such conditions. Therefore, selecting a belt with high durability and wear resistance is essential to ensure uninterrupted operations and minimize maintenance costs.
Durable conveyor belts reduce the frequency of replacements and repairs, leading to lower operational costs and increased efficiency. These belts are typically designed with specialized rubber compounds that offer enhanced resistance to abrasion, cuts, and gouges. Additionally, they are treated to withstand the thermal stresses encountered in power plants, ensuring they maintain their integrity over extended periods.
The wear resistance of a conveyor belt is also influenced by its thickness and the quality of the rubber used. Thicker belts provide better resistance to wear, but they also require more power to drive, which must be considered in the overall system design. High-quality rubber compounds that incorporate additives such as carbon black or anti-oxidants can significantly enhance the belt’s wear resistance.
How about Coal Conveyor in Thermal Power Plant
The coal conveyor in thermal power plant systems plays a crucial role in transporting coal from storage areas to the boilers, ensuring a steady and efficient fuel supply. Among these systems, the transportation of pulverised coal is particularly important due to its influence on the plant’s efficiency and performance. Here, we delve into the methods of transferring pulverised coal, the role and efficiency of pneumatic conveyors, and comparisons with other conveyor types used in thermal power plants.
Pulverised Coal Transportation
In thermal power plants, coal is often pulverised into a fine powder to enhance combustion efficiency and improve heat generation. The transportation of this pulverised coal requires specialized conveyor systems that can handle the fine, dusty material effectively and reliably.
Methods of Transferring Pulverised Coal in Thermal Power Plants
There are several methods for transferring pulverised coal within thermal power plants. These methods ensure that the fine coal particles are delivered to the boilers efficiently and with minimal loss.
Pneumatic Conveying Systems
- Overview: Pneumatic conveying systems use air pressure or vacuum to transport pulverised coal through pipelines. This method is highly efficient and can move coal over long distances within the plant.
- Advantages: Pneumatic systems are enclosed, reducing the risk of coal dust escaping into the environment. They also allow for flexible routing and can transport coal both horizontally and vertically.
Mechanical Conveying Systems
- Belt Conveyors: Although more commonly used for transporting lump coal, belt conveyors can be adapted for pulverised coal with appropriate modifications to contain the fine material and prevent dust emissions.
- Screw Conveyors: Screw conveyors use a rotating helical screw to move pulverised coal through a tube. They are effective for short-distance transport and can handle inclined or vertical movements.
- Bucket Elevators: These conveyors use buckets attached to a belt or chain to lift pulverised coal vertically. They are often used to transfer coal to higher elevations within the plant.
Dense Phase Conveying Systems
- Overview: Dense phase conveying systems transport pulverised coal at high pressure but low velocity, reducing wear and tear on the pipelines and minimizing the risk of dust explosions.
- Advantages: These systems are energy-efficient and can handle abrasive materials like pulverised coal with reduced degradation of the conveying equipment.
Explanation of Pneumatic Conveyors and Their Efficiency
Pneumatic conveyors are among the most efficient and effective methods for transporting pulverised coal in thermal power plants. These systems use either positive or negative air pressure to move the coal through a network of pipelines.
Positive Pressure Systems:
- Mechanism: In positive pressure systems, air is blown into the pipelines, creating a flow that carries the pulverised coal to its destination.
- Applications: These systems are typically used for long-distance horizontal transport and can handle large volumes of coal.
Vacuum Systems:
- Mechanism: Vacuum systems use negative pressure to suck the pulverised coal through the pipelines. This method is effective for shorter distances and vertical transport.
- Applications: Vacuum systems are often used for feeding coal directly into boilers or for transporting coal from storage silos to processing units.
Efficiency:
- High Throughput: Pneumatic conveyors can move large quantities of pulverised coal quickly and efficiently, ensuring a steady supply to the boilers.
- Dust Control: The enclosed nature of pneumatic systems minimizes coal dust emissions, improving plant cleanliness and reducing health risks.
- Flexibility: These systems can be easily adapted to various plant layouts and can navigate complex routes with minimal disruption to existing infrastructure.
Comparisons with Other Conveyor Types for Pulverised Coal
While pneumatic conveyors are highly efficient for transporting pulverised coal, other conveyor types also play a role in thermal power plants. Here’s a comparison of pneumatic conveyors with belt conveyors and screw conveyors.
Belt Conveyors:
- Advantages: Belt conveyors are suitable for long-distance transport of lump coal and can be modified for pulverised coal with dust containment measures.
- Disadvantages: They are less efficient for fine materials due to the risk of spillage and dust emissions. Additionally, belt conveyors require regular maintenance to prevent wear and tear from the abrasive coal particles.
Screw Conveyors:
- Advantages: Screw conveyors are effective for short-distance transport and can handle inclined or vertical movements. They are relatively simple and cost-effective.
- Disadvantages: They have a limited capacity and are not suitable for long-distance transport. The rotating screw can also cause degradation of the pulverised coal.
Pneumatic Conveyors:
- Advantages: Pneumatic systems offer high efficiency, enclosed transport, and flexibility in routing. They are ideal for long-distance and vertical transport of pulverised coal.
- Disadvantages: Initial installation costs can be high, and the systems require a reliable air supply. However, the benefits in terms of efficiency and dust control often outweigh these drawbacks.
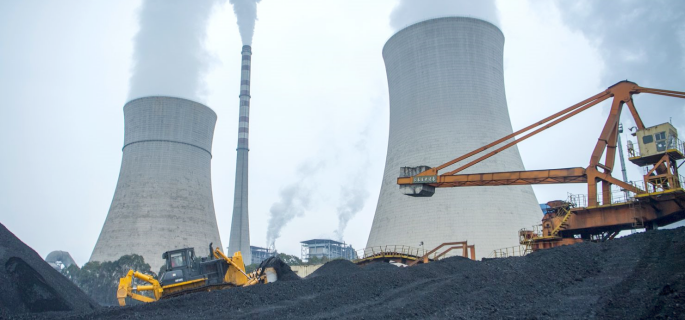
The Key of Coal Conveyor in Thermal Power Plant
A coal conveyor in a thermal power plant is an essential component that ensures the steady supply of coal to the boilers, which is crucial for the continuous production of electricity. Among the various types of conveyors used, the skip hoist conveyor plays a significant role, especially in handling the vertical transportation of coal. This section will provide a detailed description of skip hoist conveyors, their functions, advantages, and applications in thermal power plants and other industries.
Skip Hoist Conveyor
Description and Function
Skip hoist conveyors are designed to transport bulk materials, such as coal, vertically from one level to another. These conveyors are particularly effective in situations where space is limited and a steep incline is required. The skip hoist conveyor consists of a hopper or skip, a lifting mechanism, and a guiding structure that ensures the precise movement of the skip.
The primary function of the skip hoist conveyor in coal handling is to lift the coal from a lower storage area to a higher level, such as a processing unit or a boiler feed point. The skip is filled with coal at the lower level, and the lifting mechanism, usually driven by motors, hoists the skip along a guided path to the designated discharge point. Once the skip reaches the top, it discharges the coal, which is then transported to the next stage of the process.
Advantages of Using Skip Hoist Conveyors for Vertical Transportation
There are several advantages of using skip hoist conveyors for vertical transportation of coal in thermal power plants:
- Space Efficiency: Skip hoist conveyors are ideal for installations where space is constrained. Their vertical design allows for efficient use of space, making them suitable for power plants with limited horizontal room.
- High Lifting Capacity: These conveyors can handle significant loads, making them suitable for transporting large quantities of coal. The robust construction and powerful lifting mechanism ensure reliable operation even under heavy loads.
- Flexibility in Design: Skip hoist conveyors can be customized to fit specific requirements, including varying heights and load capacities. This flexibility makes them adaptable to different plant layouts and operational needs.
- Reduced Maintenance: The design of skip hoist conveyors minimizes wear and tear, leading to lower maintenance requirements. The guided structure ensures smooth operation, reducing the likelihood of mechanical failures.
- Safety: Skip hoist conveyors are equipped with safety features such as emergency brakes and limit switches to prevent accidents. The enclosed design of the skip also reduces the risk of coal spillage and dust generation, enhancing the overall safety of the plant.
Applications in Thermal Power Plants and Other Industries
Skip hoist conveyors are widely used in thermal power plants for the vertical transportation of coal. In these plants, they are typically employed to move coal from ground-level storage facilities to elevated processing units or directly to the boilers. The ability to efficiently transport coal vertically makes skip hoist conveyors an integral part of the coal handling system in thermal power plants.
Beyond thermal power plants, skip hoist conveyors find applications in various other industries:
- Mining: In the mining industry, skip hoist conveyors are used to lift ore and other materials from underground mines to the surface. Their robust construction and high lifting capacity make them ideal for mining operations.
- Cement Plants: Skip hoist conveyors are used in cement plants to transport raw materials such as limestone and clay to the processing units. Their vertical design is particularly useful in the multi-level layout of cement plants.
- Chemical Plants: In chemical plants, skip hoist conveyors are used to handle bulk materials and chemicals, facilitating vertical transportation within the plant.
- Food Processing: In the food processing industry, skip hoist conveyors are used to transport ingredients and products vertically, ensuring efficient material handling and processing.
Advantages of Using Coal Conveyors in Thermal Power Plants
A coal conveyor in thermal power plant is an integral part of the coal handling system, responsible for transporting coal from storage areas to the boilers where it is burned to generate electricity. This essential component ensures a steady and reliable supply of coal, enabling the power plant to operate efficiently. In this section, we will explore the advantages of using coal conveyors in power plants, focusing on increased efficiency and reliability in coal handling, reduction in manual labor and operational costs, and enhanced safety and environmental benefits.
Increased Efficiency and Reliability in Coal Handling
One of the primary advantages of using a coal conveyor in a thermal power plant is the significant increase in efficiency and reliability in coal handling. Coal conveyors are designed to transport large volumes of coal quickly and efficiently, reducing the time required to move coal from storage areas to the boilers.
- Continuous Operation: Coal conveyors can operate continuously, ensuring a constant supply of coal to the boilers. This continuous operation is crucial for maintaining a steady power output and avoiding interruptions in electricity generation.
- Automated Systems: Modern coal conveyors are equipped with automated control systems that optimize the flow of coal and ensure smooth operation. These systems can adjust the speed and load of the conveyor based on real-time demand, enhancing overall efficiency.
- Reduced Handling Time: By automating the coal transportation process, conveyors significantly reduce the time and effort required to handle coal. This reduction in handling time translates to faster turnaround times and improved productivity for the power plant.
- Minimal Downtime: Coal conveyors are designed to be robust and reliable, with minimal maintenance requirements. This reliability ensures that the coal handling system operates with minimal downtime, further enhancing the efficiency of the power plant.
Reduction in Manual Labor and Operational Costs
Another significant advantage of using coal conveyors in thermal power plants is the reduction in manual labor and operational costs. Manual handling of coal is labor-intensive and time-consuming, often requiring a large workforce and resulting in higher operational costs.
- Labor Savings: By automating the coal handling process, conveyors drastically reduce the need for manual labor. This reduction in labor requirements not only lowers operational costs but also allows the workforce to be allocated to other critical tasks within the power plant.
- Operational Cost Reduction: Automated coal conveyors reduce the need for equipment and resources associated with manual coal handling, such as loaders, trucks, and cranes. This reduction in equipment usage leads to significant cost savings in terms of fuel, maintenance, and operational expenses.
- Efficiency Gains: The increased efficiency and speed of coal conveyors result in lower operational costs. By minimizing handling time and optimizing coal flow, conveyors help reduce the overall cost of coal transportation within the power plant.
- Improved Resource Allocation: With coal conveyors handling the bulk of coal transportation, the power plant can allocate its resources more effectively. This improved resource allocation leads to better overall management and operation of the power plant.
Enhanced Safety and Environmental Benefits
The use of coal conveyors in thermal power plants also brings about enhanced safety and environmental benefits. Handling coal manually can pose significant safety risks to workers, while the environmental impact of coal transportation must also be considered.
- Worker Safety: Coal conveyors reduce the need for manual coal handling, which can be hazardous for workers. By minimizing direct contact with coal and reducing the physical strain associated with manual handling, conveyors help improve worker safety and reduce the risk of accidents and injuries.
- Environmental Protection: Coal conveyors are designed to minimize coal spillage and dust generation during transportation. This design helps reduce the environmental impact of coal handling, protecting the surrounding environment from contamination and pollution.
- Dust Control: Modern coal conveyors are equipped with dust control systems that capture and contain coal dust during transportation. These systems help maintain air quality within the power plant and surrounding areas, reducing the risk of respiratory issues for workers and nearby residents.
- Efficient Use of Resources: By optimizing coal transportation, conveyors reduce the amount of energy required to move coal within the power plant. This efficient use of resources contributes to the overall sustainability of the power plant, reducing its carbon footprint and environmental impact.
Applications of Coal Conveyor in Thermal Power Plant
Coal conveyors are essential in thermal power plants for the efficient transportation of coal from storage facilities to the power plant’s boilers. Here are some key applications of coal conveyors in thermal power plants:
Coal Handling Plant (CHP):
- Receiving and Unloading: Coal conveyors transport coal from the unloading area (where coal is brought in by trucks, trains, or ships) to the storage yard or directly to the coal handling plant.
- Stacking and Reclaiming: Coal conveyors are used to stack the coal in the storage yard and later reclaim it for use. Stackers and reclaimers work in tandem with conveyors to manage the coal stockpiles.
Crusher House:
- Coal Crushing: Conveyors transport coal to the crusher house, where it is crushed into smaller, manageable pieces suitable for the boiler’s feed system.
Coal Bunkers and Silos:
- Feeding Coal to Bunkers: Conveyors transport crushed coal from the crusher house to the coal bunkers or silos, where it is stored before being fed into the boiler.
- Controlled Feeding: Conveyors equipped with feeders provide a controlled feed of coal to the bunkers, ensuring a consistent and reliable supply to the boilers.
Boiler Feeding:
- Feeding Pulverizers: Conveyors feed coal from the bunkers or silos into pulverizers, which grind the coal into a fine powder for efficient combustion in the boilers.
- Direct Boiler Feed: In some plants, conveyors may directly feed the pulverized coal into the boiler.
Fly Ash and Bottom Ash Handling:
- Ash Removal: After combustion, conveyors are used to remove fly ash and bottom ash from the boiler area. This ash is then transported to disposal areas or for further processing.
Environmental Controls:
- Dust Suppression: Conveyors equipped with dust suppression systems help minimize coal dust generation and dispersion, reducing environmental pollution and improving plant safety.
Maintenance and Monitoring:
- Inspection and Maintenance: Coal conveyors in thermal power plants are equipped with systems for monitoring and maintaining conveyor belts, ensuring continuous operation and minimizing downtime.
Safety Systems:
- Fire Detection and Suppression: Conveyors are integrated with fire detection and suppression systems to quickly address any potential fire hazards associated with coal handling.
By ensuring the efficient and reliable transport of coal, these conveyors play a critical role in maintaining the continuous operation and energy production of thermal power plants.
FAQS about Coal Conveyor in Thermal Power Plant
A coal conveyor is a mechanical system used to transport coal from one location to another. In power plants and other industrial settings, coal conveyors are essential for moving large quantities of coal efficiently and safely. These conveyors typically consist of belts, rollers, and other components that help guide and move the coal along a designated path. Coal conveyors help streamline operations, reduce the need for manual labor, and ensure a consistent supply of coal to the power plant or processing facility. They are designed to handle the heavy, abrasive nature of coal and often include features to prevent spillage and dust generation.
In power plants, several types of coal conveyors are used to ensure the efficient movement of coal from storage to the combustion units. The main types include:
Belt Conveyors: These are the most common type and consist of a continuous belt that carries coal from one end to the other. Belt conveyors are suitable for long-distance transport and can handle large volumes of coal.
Chain Conveyors: These conveyors use chains to move the coal and are particularly useful in transporting coal over short distances or in tight spaces.
Screw Conveyors: These conveyors use a rotating screw mechanism to move coal. They are ideal for precise control of coal flow but are typically used for short distances.
Pneumatic Conveyors: These use air pressure to transport coal through pipelines. Pneumatic systems are efficient and can move coal vertically or horizontally, but they are more expensive and complex than other types.
Bucket Elevators: These are used to lift coal vertically from a lower to a higher level and are particularly useful in handling large amounts of coal.
Each type of conveyor has its advantages and is selected based on the specific needs of the power plant, including the distance coal needs to be moved, the layout of the facility, and the volume of coal handled.
Coal is a primary fuel used in thermal power plants to generate electricity. The process begins with coal being transported to the power plant, where it is stored in large coal yards or silos. From there, coal is conveyed to the boiler house where it is pulverized into a fine powder. This powdered coal is then mixed with air and blown into the furnace of the boiler. Inside the furnace, the coal-air mixture is ignited, producing a high-temperature flame. The heat generated from the burning coal converts water in the boiler’s tubes into steam. This high-pressure steam is directed to a turbine, which spins and drives a generator to produce electricity. The steam is then cooled and condensed back into water, which is returned to the boiler to start the process again. This cyclical process continues, providing a reliable source of electricity.
The coal handling process in a thermal power plant is crucial for ensuring the efficient and reliable operation of the plant. The main steps involved are:
Unloading: Coal is delivered to the power plant by rail, truck, or barge. It is then unloaded using various equipment such as rotary dumpers or grab buckets.
Transportation: After unloading, coal is transported to the storage yard using conveyors. This transport system includes several types of conveyors, such as belt conveyors, screw conveyors, and bucket elevators, designed to move coal efficiently to different parts of the plant.
Storage: Coal is stored in coal yards or silos to ensure a steady supply. Storage systems must prevent coal degradation and spontaneous combustion.
Crushing: Before being fed into the boiler, large chunks of coal are crushed into smaller pieces using crushers to ensure efficient combustion.
Screening: The crushed coal is screened to remove impurities and oversized particles that could damage the boiler and other equipment.
Pulverizing: The screened coal is then pulverized into a fine powder in pulverizers or mills. Pulverization increases the surface area of the coal, enhancing its combustion efficiency.
Feeding: The pulverized coal is transported to the boiler using feeders and air conveyors. The precise control of coal flow ensures consistent combustion and efficient power generation.
Combustion: In the boiler, the pulverized coal is mixed with air and ignited to produce heat. This heat converts water into steam, which drives the turbines to generate electricity.
Each step in the coal handling process is designed to maximize efficiency, minimize losses, and ensure the reliable operation of the thermal power plant.
A coal conveyance system in a thermal power station transports coal from storage to the boilers. It begins at the unloading area, where coal is delivered by trucks, trains, or ships and transferred to conveyors. These conveyors move the coal to a crusher house, where it is crushed into smaller pieces. The crushed coal is then transported to bunkers or silos via conveyors. From there, controlled feeders ensure a steady flow of coal to the pulverizers, which grind it into a fine powder for efficient combustion. The powdered coal is then fed into the boilers for energy production. Throughout the process, conveyors are equipped with dust suppression, fire detection, and suppression systems to maintain safety and environmental compliance. The system also includes maintenance and monitoring equipment to ensure continuous operation.
Last Updated on August 14, 2024 by Jordan Smith
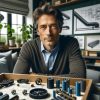
Jordan Smith, a seasoned professional with over 20 years of experience in the conveyor system industry. Jordan’s expertise lies in providing comprehensive solutions for conveyor rollers, belts, and accessories, catering to a wide range of industrial needs. From initial design and configuration to installation and meticulous troubleshooting, Jordan is adept at handling all aspects of conveyor system management. Whether you’re looking to upgrade your production line with efficient conveyor belts, require custom conveyor rollers for specific operations, or need expert advice on selecting the right conveyor accessories for your facility, Jordan is your reliable consultant. For any inquiries or assistance with conveyor system optimization, Jordan is available to share his wealth of knowledge and experience. Feel free to reach out at any time for professional guidance on all matters related to conveyor rollers, belts, and accessories.