The Longest Conveyor Belt in North America: An Overview
Conveyor belts are essential for efficient material transportation in various industries, from mining to manufacturing. They streamline processes, reduce labor costs, and enhance productivity. The longest conveyor belt in North America is a testament to engineering excellence, significantly impacting the material handling industry. This impressive system spans several miles, efficiently transporting materials across vast distances. Located in Oklahoma, the longest conveyor belt in North America is primarily used in the mining industry, showcasing the technological advancements and innovative solutions in conveyor belt design. Understanding the significance of the longest conveyor belt in North America highlights its role in boosting industrial efficiency and sustainability.
Longest Conveyor Belt in North America
Atlas Conveyor: Leading the Way
When discussing the longest conveyor belt in North America, the conversation inevitably turns to the pioneering efforts of Atlas Conveyor. This company has become a leader in conveyor belt technology, known for its innovative solutions and large-scale projects that set industry standards. The Atlas Conveyor’s projects, including the renowned Dune Express, showcase the company’s role in revolutionizing material transportation across vast distances, enhancing efficiency, and promoting sustainability.
Description of Atlas Conveyor and Its Role in Conveyor Belt Technology
Atlas Conveyor has established itself as a key player in the development and deployment of advanced conveyor belt systems. Specializing in the design, construction, and maintenance of long-distance conveyor belts, the company leverages cutting-edge technology to address the complex challenges of material transport. Atlas Conveyor’s expertise extends across various industries, including mining, oil and gas, and agriculture, where efficient material handling is critical.
The company’s approach is characterized by a commitment to innovation and sustainability. By integrating state-of-the-art materials and automation technologies, Atlas Conveyor creates systems that are not only efficient but also environmentally friendly. Their projects often involve the use of renewable energy sources, such as solar and wind power, to reduce the carbon footprint of their operations.
Key Projects and Innovations Spearheaded by Atlas Conveyor
Atlas Conveyor’s portfolio of projects includes some of the most ambitious and technologically advanced conveyor belt systems in the world. One of the standout projects is the Dune Express, which holds the title of the longest conveyor belt in North America. Spanning 42 miles across the rugged terrain of Texas and New Mexico, this conveyor belt is a testament to the company’s engineering prowess and innovative spirit.
The Dune Express is designed to transport sand used in hydraulic fracturing (fracking) operations. Before its construction, the transportation of sand relied heavily on trucks, which not only incurred high costs but also contributed significantly to greenhouse gas emissions and road congestion. The Dune Express addresses these issues by providing a continuous, efficient, and eco-friendly means of transporting sand from the mines to processing facilities.
The fully electric operation of the Dune Express is one of its most notable features. By utilizing electric motors powered by renewable energy sources, the conveyor belt eliminates the need for diesel-powered trucks, drastically reducing emissions and the environmental impact. This project exemplifies Atlas Conveyor’s commitment to sustainability and their ability to integrate green technologies into large-scale industrial applications.
Another key project by Atlas Conveyor is the Copper Mountain Conveyor in Arizona. This system is designed to transport copper ore from the mine to the processing plant, covering a distance of 25 miles. The Copper Mountain Conveyor incorporates advanced automation and control systems that ensure optimal performance and reliability. Sensors and real-time monitoring technologies allow for continuous tracking of the belt’s condition, enabling proactive maintenance and reducing the risk of downtime.
The use of high-strength, lightweight materials in the construction of the Copper Mountain Conveyor demonstrates Atlas Conveyor’s commitment to innovation. These materials enhance the durability and efficiency of the system, reducing energy consumption and operational costs. This project not only improves the efficiency of copper mining operations but also sets a benchmark for future conveyor belt installations.
Technological Innovations
Atlas Conveyor’s success is driven by their emphasis on technological advancements. The company invests heavily in research and development to stay at the forefront of conveyor belt technology. Some of the key innovations include the integration of Internet of Things (IoT) devices and artificial intelligence (AI) into their systems.
IoT devices enable comprehensive monitoring and data collection along the length of the conveyor belt. These devices provide real-time information on various parameters, such as belt speed, tension, and temperature. AI algorithms analyze this data to predict maintenance needs and optimize performance. By leveraging these technologies, Atlas Conveyor can ensure that their systems operate smoothly and efficiently, minimizing downtime and maximizing productivity.
The company is also exploring the use of smart materials that can self-heal or adapt to changing environmental conditions. These materials have the potential to further enhance the durability and longevity of conveyor belts, reducing the frequency and cost of maintenance. Atlas Conveyor’s focus on cutting-edge materials science highlights their commitment to continuous improvement and innovation.
Environmental and Economic Impact
The environmental benefits of Atlas Conveyor’s projects are significant. By replacing traditional transportation methods with electric conveyor belts, the company helps reduce greenhouse gas emissions and lower the environmental footprint of industrial operations. The use of renewable energy sources further amplifies these benefits, contributing to broader efforts to combat climate change.
Economically, the efficiency gains achieved through Atlas Conveyor’s systems translate to substantial cost savings for their clients. Reduced transportation costs, lower maintenance expenses, and increased productivity all contribute to higher profit margins. These savings can be reinvested into other areas of the business, driving further growth and development.
Future Prospects
Looking to the future, Atlas Conveyor continues to push the boundaries of what is possible in conveyor belt technology. The company is exploring new applications for their systems, including in emerging industries such as renewable energy and advanced manufacturing. By expanding their portfolio and leveraging their expertise, Atlas Conveyor aims to remain at the forefront of the industry.
Future projects are likely to incorporate even more advanced technologies, such as autonomous maintenance robots and enhanced AI-driven control systems. These innovations will further improve the efficiency, reliability, and sustainability of conveyor belt operations. As industries worldwide seek to reduce their environmental impact and improve operational efficiency, the demand for Atlas Conveyor’s solutions is expected to grow.
What is The Longest Conveyor Belt in North America
The Longest Conveyor Belt in Oklahoma
The longest conveyor belt in North America is a remarkable feat of engineering located in the state of Oklahoma. This conveyor belt system, which stretches across a considerable distance, plays a crucial role in various industrial operations, demonstrating the technological advancements and efficiency of modern conveyor systems. In this section, we will explore the detailed aspects of the longest conveyor belt in Oklahoma, including its length, purpose, and the industries it serves.
Detailed Exploration of the Conveyor Belt in Oklahoma
The longest conveyor belt in North America, found in Oklahoma, extends over an impressive distance, making it a key infrastructure component in the region. This conveyor belt is part of the extensive network that supports the mining and transportation of materials, particularly in the coal and aggregate industries. The belt is designed to handle the rigorous demands of transporting heavy and abrasive materials over long distances, ensuring efficient and continuous operation.
Length and Structure:
The conveyor belt in Oklahoma spans approximately 10 miles (16 kilometers), making it one of the longest in North America. Its construction incorporates advanced materials and engineering techniques to ensure durability and reliability. The belt is made from high-strength rubber and reinforced with steel cables to withstand the weight and abrasiveness of the transported materials. The structure is supported by a series of rollers and pulleys, which help to maintain the belt’s alignment and reduce wear.
Purpose of the Conveyor Belt
The primary purpose of the longest conveyor belt in North America is to facilitate the efficient transport of coal and aggregates from mining sites to processing plants and distribution centers. This conveyor belt system significantly reduces the need for traditional transportation methods such as trucks and trains, which can be costly and environmentally taxing.
Efficiency and Cost-Effectiveness:
By using a conveyor belt system, companies can achieve greater efficiency in their operations. The continuous movement of materials ensures a steady supply to processing facilities, minimizing downtime and enhancing productivity. Additionally, the conveyor belt system reduces transportation costs by eliminating the need for fuel, maintenance, and labor associated with truck and train transport. This cost-effectiveness translates to lower operational expenses and higher profitability for the industries that utilize the belt.
Industries Served by the Conveyor Belt
The longest conveyor belt in North America serves several key industries in Oklahoma and beyond. The primary industries that benefit from this conveyor belt system include the coal mining industry and the aggregate industry.
Coal Mining Industry:
Oklahoma is home to several coal mining operations, and the conveyor belt plays a vital role in transporting coal from the mines to processing plants. Coal is a critical energy resource used in power generation and various industrial applications. The conveyor belt system ensures that coal is transported efficiently and safely, maintaining a consistent supply to meet energy demands.
Aggregate Industry:
The aggregate industry, which includes the extraction and processing of materials such as sand, gravel, and crushed stone, also relies heavily on the conveyor belt system. These materials are essential for construction projects, including the building of roads, bridges, and infrastructure. The conveyor belt in Oklahoma enables the swift and efficient movement of aggregates from quarries to processing plants, ensuring that construction projects have a reliable supply of materials.
Technological Advancements
The design and operation of the longest conveyor belt in North America incorporate several technological advancements that enhance its performance and reliability. These innovations address various challenges associated with long-distance material transport.
Advanced Materials:
The use of high-strength rubber and steel-reinforced cables ensures that the conveyor belt can handle the heavy loads and abrasive nature of the transported materials. These materials are selected for their durability and resistance to wear, reducing the frequency of maintenance and replacements.
Automation and Monitoring:
The conveyor belt system is equipped with automated monitoring and control systems that track its performance in real-time. Sensors placed along the belt monitor parameters such as tension, alignment, and speed. This data is analyzed to predict maintenance needs and prevent potential issues, ensuring continuous operation and minimizing downtime.
Environmental Considerations:
Environmental sustainability is a critical aspect of the conveyor belt’s design. By reducing the reliance on traditional transportation methods, the conveyor belt system helps to lower greenhouse gas emissions and decrease the environmental impact of mining and material transport. Additionally, dust suppression systems are implemented to minimize airborne particles, protecting air quality and the health of workers and nearby communities.
Maintenance Practices
Effective maintenance practices are essential for the longevity and reliability of the longest conveyor belt in North America. These practices include regular inspections, predictive maintenance, and preventive measures.
Regular Inspections:
Routine inspections are conducted to identify and address any signs of wear, damage, or misalignment. Inspectors check the condition of the belt, rollers, pulleys, and other components to ensure they are functioning correctly.
Predictive Maintenance:
Predictive maintenance involves using data from sensors and monitoring systems to predict when maintenance should be performed. This proactive approach allows for timely interventions before minor issues escalate into major problems, reducing downtime and extending the belt’s operational lifespan.
Preventive Measures:
Scheduled maintenance tasks, such as lubricating moving parts, tightening fittings, and replacing worn components, are performed regularly to prevent unexpected breakdowns. These preventive measures help maintain the efficiency and reliability of the conveyor belt system.
How about Longest Conveyor Belt in North America
Comparison with the Bou Craa Conveyor Belt
When discussing the longest conveyor belt in North America, it’s essential to compare it with another colossal engineering feat: the Bou Craa conveyor belt in Western Sahara. Both conveyor belts are remarkable in their design, purpose, and impact, but they serve different industries and face unique challenges. This comparison provides insights into their lengths, purposes, and significance in their respective regions.
Overview of the Bou Craa Conveyor Belt
The Bou Craa conveyor belt is one of the longest conveyor systems in the world, stretching approximately 98 kilometers (61 miles) across the harsh desert landscape of Western Sahara. This conveyor belt is integral to the operations of the Bou Craa phosphate mines, managed by the Moroccan state-owned company OCP. Its primary function is to transport phosphate rock from the mines to the port of El Aaiún, where it is then shipped globally.
Phosphate from Bou Craa is a critical component in the production of fertilizers, making it a vital resource for global agriculture. The conveyor belt’s construction is designed to withstand extreme desert conditions, including high temperatures, strong winds, and abrasive sand. Despite these challenges, it operates efficiently, demonstrating the robustness and reliability of the system.
Comparison of Length
In terms of length, the Bou Craa conveyor belt surpasses the longest conveyor belt in North America, the Dune Express. While the Bou Craa belt stretches 98 kilometers, the Dune Express covers 42 miles (approximately 68 kilometers). Although shorter, the Dune Express is still a significant engineering achievement, designed to meet the specific needs of the fracking industry in the Permian Basin.
The disparity in length highlights the different scales of operation and geographic challenges faced by each conveyor belt. The Bou Craa belt’s extensive length is necessary to connect the remote mining site with the coastal port, while the Dune Express is optimized for transporting sand across the rugged terrain between Texas and New Mexico.
Purpose and Industrial Significance
The primary purpose of the Bou Craa conveyor belt is to facilitate the efficient transport of phosphate rock. This mineral is crucial for producing fertilizers that support global food production. The belt’s continuous operation ensures a steady supply of phosphate to international markets, reinforcing its importance in the global agricultural supply chain.
In contrast, the longest conveyor belt in North America, the Dune Express, serves the oil and gas industry by transporting sand used in hydraulic fracturing. This process, commonly known as fracking, requires large quantities of sand to extract oil and gas from shale formations. The Dune Express streamlines this process by providing a reliable and cost-effective method of transporting sand from mines to processing facilities.
The significance of the Dune Express lies in its ability to reduce the environmental and economic costs associated with truck transportation. By eliminating the need for numerous truck trips, the conveyor belt reduces fuel consumption, emissions, and road wear, offering a more sustainable solution for the fracking industry.
Environmental Impact
Both conveyor belts offer environmental benefits by reducing reliance on traditional transportation methods. The Bou Craa conveyor belt minimizes the need for trucks and rail transport, which would otherwise contribute to higher greenhouse gas emissions and environmental degradation. By efficiently moving phosphate across the desert, the conveyor belt reduces its environmental footprint and supports more sustainable mining practices.
Similarly, the Dune Express, as the longest conveyor belt in North America, helps mitigate the environmental impact of sand transportation for fracking. Its fully electric operation, powered by renewable energy sources, further enhances its environmental credentials. By lowering emissions and reducing traffic on local roads, the Dune Express contributes to cleaner air and a reduced carbon footprint in the Permian Basin.
Economic Contributions
Economically, both conveyor belts play pivotal roles in their respective industries. The Bou Craa conveyor belt ensures the economic viability of the phosphate mines by lowering transportation costs and improving operational efficiency. This efficiency translates to higher profitability and supports the livelihoods of workers in the region.
The Dune Express also provides significant economic benefits by reducing transportation costs and increasing efficiency for the fracking industry. The cost savings from using the conveyor belt instead of trucks can be reinvested in other areas, such as technological upgrades and environmental initiatives. Additionally, the conveyor belt’s construction and maintenance create job opportunities, boosting the local economy.
The Keys of Longest Conveyor Belt in North America
Longest Conveyor Belt in the World
The longest conveyor belt in the world is an engineering marvel that stands as a testament to modern technology’s ability to solve logistical challenges in mining and material transportation. Spanning over 61 miles (98 kilometers), this conveyor belt system is located in Western Sahara and serves a critical purpose in the global supply chain. By examining the world’s longest conveyor belt and comparing it with the longest conveyor belt in North America, we can appreciate their respective lengths, purposes, and significances.
Examination of the World’s Longest Conveyor Belt
The world’s longest conveyor belt is situated in Western Sahara, specifically designed to transport phosphate rock from the Bou Craa mines to the port city of El Marsa. This belt plays a vital role in the mining and transportation of phosphate, a key ingredient in agricultural fertilizers. Its extensive length and continuous operation make it a cornerstone of the global phosphate industry.
Location and Purpose:
The Bou Craa conveyor belt begins at the phosphate mines in Bou Craa, a region rich in phosphate deposits. The belt transports the mined phosphate rock across the arid desert landscape to the port city of El Marsa. Here, the phosphate is loaded onto ships and exported to various parts of the world. This efficient transportation system ensures a steady supply of phosphate to meet global agricultural demands.
Engineering Feat:
Constructed with durability and efficiency in mind, the Bou Craa conveyor belt is made from high-strength materials capable of withstanding the harsh desert conditions. It incorporates advanced technologies such as automated monitoring systems and dust suppression measures, which enhance its operational reliability and minimize environmental impact.
Comparison with the Longest Conveyor Belt in North America
While the Bou Craa conveyor belt holds the record for the longest conveyor belt in the world, the longest conveyor belt in North America, located in Oklahoma, also showcases significant technological achievements. Comparing these two systems provides insights into their lengths, purposes, and overall significance.
Length:
The Bou Craa conveyor belt is unparalleled in length, stretching over 61 miles. In contrast, the longest conveyor belt in North America, located at the Barrick Goldstrike mine in Nevada, extends approximately 10 miles (16 kilometers). Although shorter, the North American conveyor belt is still a substantial engineering accomplishment, designed to meet the specific needs of the mining industry.
Purpose:
The primary purpose of the Bou Craa conveyor belt is to transport phosphate rock, a critical resource for global agriculture. The efficient movement of phosphate from the mines to the port ensures a consistent supply for fertilizer production, supporting food production worldwide.
In North America, the longest conveyor belt serves a different purpose. It is integral to the mining operations at the Barrick Goldstrike mine, facilitating the transport of gold ore from the Cortez Hills Mine to processing facilities. This conveyor belt is crucial for maintaining the efficiency and productivity of one of the largest gold mines in the United States.
Significance:
The global significance of the Bou Craa conveyor belt cannot be overstated. It is a vital component of the international phosphate supply chain, directly impacting agricultural productivity and food security. The belt’s ability to transport vast quantities of phosphate rock over long distances underscores its importance in the global economy.
Similarly, the longest conveyor belt in North America holds significant economic value. By streamlining the transport of gold ore, it enhances the operational efficiency of the Barrick Goldstrike mine, contributing to the United States’ gold production. The belt reduces transportation costs, minimizes environmental impact, and supports the local and national economy through job creation and revenue generation.
Technological and Environmental Considerations
Both the Bou Craa conveyor belt and the longest conveyor belt in North America incorporate advanced technologies to address operational and environmental challenges.
Technological Innovations:
The Bou Craa conveyor belt features state-of-the-art monitoring systems that track its performance in real-time. Sensors along the belt measure parameters such as tension, alignment, and wear, allowing for predictive maintenance and minimizing downtime. These innovations ensure the continuous and efficient operation of the belt in a harsh desert environment.
The North American conveyor belt at the Barrick Goldstrike mine similarly utilizes advanced technologies. Automated systems monitor the belt’s condition, enabling timely maintenance and reducing the risk of operational disruptions. The belt’s design also includes energy-efficient motors and components, which lower energy consumption and operational costs.
Environmental Impact:
Environmental sustainability is a key consideration for both conveyor belt systems. The Bou Craa conveyor belt incorporates dust suppression measures to minimize airborne particles, protecting the health of workers and local communities. Its design also aims to reduce habitat disruption and preserve the desert ecosystem.
In North America, the conveyor belt system at the Barrick Goldstrike mine implements similar environmental measures. Dust control systems and environmental monitoring technologies help mitigate the impact of mining operations. The belt’s continuous operation reduces the need for truck transport, lowering greenhouse gas emissions and minimizing the environmental footprint.
The Types of Longest Conveyor Belt in North America
Impact of Atlas Sand
When discussing the longest conveyor belt in North America, the significant contributions of Atlas Sand cannot be overlooked. Atlas Sand has played a pivotal role in advancing the conveyor belt industry, particularly through their innovative projects and commitment to enhancing efficiency and sustainability. Their efforts have not only transformed material transportation in the fracking industry but have also set new standards for environmental responsibility.
Insight into Atlas Sand and Its Influence on the Conveyor Belt Industry
Atlas Sand is a leading provider of frac sand, which is essential for hydraulic fracturing operations in the oil and gas industry. The company’s operations are primarily based in the Permian Basin, where the demand for high-quality frac sand is immense. To meet this demand efficiently and sustainably, Atlas Sand has been at the forefront of integrating advanced conveyor belt systems into their operations.
The influence of Atlas Sand on the conveyor belt industry is profound. By leveraging cutting-edge technology and sustainable practices, the company has significantly improved the transportation of sand, which is a critical component in fracking. Their commitment to innovation has led to the development of more efficient, reliable, and environmentally friendly conveyor belt systems, setting a benchmark for the industry.
Specific Projects or Achievements of Atlas Sand
One of the most notable projects spearheaded by Atlas Sand is the Dune Express, recognized as the longest conveyor belt in North America. This 42-mile conveyor system is a testament to the company’s dedication to efficiency and sustainability. The Dune Express was designed to address the logistical challenges of transporting sand over long distances, reducing reliance on truck transportation, and minimizing environmental impact.
Enhancing Conveyor Belt Efficiency
The Dune Express has revolutionized the way frac sand is transported in the Permian Basin. Traditional methods of using trucks for sand transportation are not only costly but also environmentally detrimental due to high fuel consumption and emissions. The Dune Express offers a more efficient solution by continuously transporting large quantities of sand directly from the mines to the processing facilities.
The efficiency of this conveyor belt system is further enhanced by the integration of advanced automation and control technologies. Real-time monitoring systems track various parameters such as belt speed, tension, and temperature, ensuring optimal performance and early detection of potential issues. This proactive approach to maintenance reduces downtime and enhances the overall reliability of the system.
Promoting Sustainability
Atlas Sand’s commitment to sustainability is evident in the design and operation of the Dune Express. The conveyor belt is fully electric, powered by renewable energy sources such as solar and wind power. This shift to clean energy significantly reduces the carbon footprint of the sand transportation process, aligning with broader environmental goals to combat climate change.
In addition to using renewable energy, the Dune Express minimizes land disturbance and habitat destruction by following the natural contours of the landscape. This careful planning and design help preserve the local ecosystem while still meeting the operational needs of the fracking industry.
Economic Impact
The economic impact of Atlas Sand’s innovative projects is substantial. By reducing transportation costs through the use of conveyor belts, the company enhances the profitability of its operations. The savings generated can be reinvested into further technological advancements and sustainability initiatives, driving continuous improvement and growth.
Moreover, the construction and maintenance of the Dune Express have created job opportunities in the region, boosting the local economy. The project supports not only the direct workforce involved in its operation but also ancillary industries that provide goods and services to the mining and fracking sectors.
Industry Leadership
Atlas Sand’s achievements with the Dune Express have positioned the company as a leader in the conveyor belt industry. Their approach to integrating sustainability with operational efficiency serves as a model for other companies in the sector. By demonstrating that economic success can go hand-in-hand with environmental responsibility, Atlas Sand has set a precedent for future developments in the industry.
Longest Conveyor Belt in North America
Economic and Environmental Benefits
The longest conveyor belt in North America is a testament to the advancements in industrial transportation systems, reflecting significant economic and environmental benefits. This conveyor belt, located at the Barrick Goldstrike mine in Nevada, is integral to the efficient movement of materials and contributes to various industries’ sustainability and profitability. By analyzing its economic advantages and environmental benefits, we can better appreciate the vital role long conveyor belts play in modern industrial operations.
Economic Advantages
The implementation of long conveyor belts, such as the longest conveyor belt in North America, provides substantial economic advantages for mining operations and related industries.
Cost Efficiency:
One of the primary economic benefits of using long conveyor belts is cost efficiency. Traditional transportation methods, such as trucks and trains, involve substantial expenses related to fuel, maintenance, and labor. Conveyor belts, on the other hand, offer a continuous and automated means of transport, significantly reducing operational costs. The initial investment in a conveyor belt system is often offset by the long-term savings in transportation expenses, making it a financially sound choice for large-scale operations.
Increased Productivity:
Long conveyor belts enhance productivity by ensuring a constant and reliable flow of materials. In mining operations, this means that ore can be continuously transported from the extraction site to the processing facilities without the interruptions associated with vehicle-based transport. The steady supply of materials minimizes downtime and maximizes throughput, leading to higher output levels. For the Barrick Goldstrike mine, this results in more efficient gold production and increased profitability.
Reduced Labor Costs:
Automated conveyor belt systems reduce the need for manual labor in material transportation. By decreasing the reliance on truck drivers and loaders, companies can allocate human resources to more critical tasks, improving overall operational efficiency. This reduction in labor costs contributes to the economic viability of using long conveyor belts in extensive industrial operations.
Enhanced Operational Efficiency:
The integration of advanced technologies, such as sensors and automated monitoring systems, further enhances the operational efficiency of long conveyor belts. These systems provide real-time data on the condition and performance of the conveyor belt, allowing for predictive maintenance and minimizing the risk of unexpected breakdowns. The ability to address potential issues proactively ensures that the conveyor belt operates at peak efficiency, reducing maintenance costs and extending the system’s lifespan.
Environmental Benefits
Beyond the economic advantages, the longest conveyor belt in North America offers significant environmental benefits, aligning with the growing emphasis on sustainability in industrial operations.
Reduced Emissions:
One of the most notable environmental benefits of using long conveyor belts is the reduction in greenhouse gas emissions. Traditional transportation methods, such as trucks and trains, rely heavily on fossil fuels, contributing to air pollution and carbon emissions. Conveyor belts, powered by electricity, produce significantly fewer emissions. This shift to electric-powered transport helps mining operations lower their carbon footprint and comply with environmental regulations aimed at reducing industrial emissions.
Decreased Traffic Congestion:
The use of conveyor belts for material transportation also helps decrease traffic congestion around mining and industrial sites. By reducing the number of trucks and heavy vehicles on the roads, conveyor belts alleviate traffic, leading to lower emissions and improved road safety. This reduction in vehicle traffic is particularly beneficial in regions where mining operations are located near residential areas, as it contributes to better air quality and a quieter environment.
Minimized Land Disturbance:
Conveyor belts require a relatively narrow footprint compared to the extensive road networks needed for truck transport. This reduced land disturbance is crucial in preserving natural habitats and minimizing the impact on local ecosystems. The longest conveyor belt in North America, designed with environmental considerations in mind, helps to protect the surrounding landscape by limiting habitat disruption and soil erosion.
Energy Efficiency:
Long conveyor belts are designed to be energy-efficient, utilizing technologies such as variable speed drives and regenerative braking systems. These features optimize energy use by adjusting the belt’s speed according to the load and recovering energy during braking. The implementation of renewable energy sources, such as solar panels, to power the conveyor belts further enhances their environmental benefits. These renewable energy solutions reduce reliance on fossil fuels and promote the use of clean energy in industrial operations.
Dust Suppression:
Dust generation is a significant environmental concern in mining and material transportation. Conveyor belts equipped with dust suppression systems help to mitigate this issue by minimizing the amount of airborne particles released during the transport of materials. These systems improve air quality, protecting the health of workers and nearby communities. The longest conveyor belt in North America incorporates advanced dust control measures, ensuring that its operation has minimal impact on the environment.
Case Study: Barrick Goldstrike Mine
The Barrick Goldstrike mine’s conveyor belt system exemplifies the economic and environmental benefits of long conveyor belts. By replacing truck-based transport with a 10-mile conveyor belt, the mine has achieved significant cost savings and operational efficiencies. The reduction in greenhouse gas emissions and traffic congestion highlights the environmental advantages of using conveyor belts in large-scale mining operations.
Economic Impact:
The cost savings from reduced fuel consumption, lower maintenance costs, and decreased labor expenses contribute to the mine’s economic success. The continuous transport of gold ore ensures that processing facilities operate at maximum capacity, increasing overall productivity and profitability.
Environmental Impact:
Environmentally, the conveyor belt system at the Barrick Goldstrike mine has led to lower emissions and reduced land disturbance. The use of dust suppression systems and energy-efficient technologies further underscores the mine’s commitment to sustainable practices. These measures not only benefit the environment but also enhance the mine’s reputation as a responsible and forward-thinking operation.
FAQS about Longest Conveyor Belt in North America
The longest conveyor belt in the world is located in the Western Sahara and stretches an impressive 61 miles (98 kilometers) from the Bou Craa phosphate mines to the coastal port of El Marsa. This conveyor belt system was constructed in the early 1980s to efficiently transport large quantities of phosphate rock from the mine to the port. Capable of moving up to 2,000 tons of phosphate rock per hour, it plays a critical role in the global phosphate supply chain. The belt’s considerable length and capacity highlight the significant engineering challenges and innovative solutions required to transport materials over such vast distances. Additionally, the conveyor belt is notable for being visible from space, with the white dust from the phosphate rock standing out against the desert landscape.
The world’s largest conveyor belt is located in the Western Sahara, stretching from the Bou Craa phosphate mines to the coastal port near Laayoune. This 61-mile (98-kilometer) conveyor belt system is pivotal for transporting phosphate rock, a key ingredient in agricultural fertilizers, from the mines to the port for shipping worldwide. The Bou Craa conveyor belt’s substantial size and capacity make it a cornerstone of the region’s economic activity, significantly contributing to Morocco’s phosphate production. The system’s extensive scale and ability to transport large quantities of material efficiently highlight its importance in industrial operations and global trade. The visibility of this massive conveyor belt from space underscores its impressive scale and engineering marvel.
Conveyor belts come in various lengths, depending on their specific applications and industrial needs. The length of a conveyor belt can range from a few feet to several miles. For example, the world’s longest conveyor belt in the Western Sahara measures 61 miles (98 kilometers), used primarily to transport phosphate rock from mines to ports. In contrast, typical conveyor belts used in manufacturing or warehousing might be only a few hundred feet long. The length of a conveyor belt is determined by the distance materials need to be transported, the terrain, and the specific requirements of the industry. Advances in conveyor technology continue to push the boundaries of conveyor belt lengths, enhancing their efficiency and operational capabilities in various sectors.
The longest single flight conveyor is located in Western Australia, running from the Mount Saddleback mine to the Worsley refinery near Collie. This conveyor belt system measures 31 kilometers (19.3 miles) for its longest single flight and spans a total length of 51 kilometers (31.6 miles). Built in 1983, it is used to transport bauxite ore, a primary source of aluminum, efficiently across a significant distance. The conveyor operates at a speed of 26 kilometers per hour (16 miles per hour) and can move approximately 2,700 tonnes (about 5.95 million pounds) of bauxite ore every hour. The system’s design includes traversing through 22 tunnels and over 10 bridges, demonstrating the complex engineering required to maintain such a long and continuous transport operation. This system showcases the advancements in conveyor technology and the ability to handle extensive and demanding industrial transportation needs.
Last Updated on October 18, 2024 by Jordan Smith
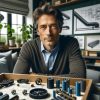
Jordan Smith, a seasoned professional with over 20 years of experience in the conveyor system industry. Jordan’s expertise lies in providing comprehensive solutions for conveyor rollers, belts, and accessories, catering to a wide range of industrial needs. From initial design and configuration to installation and meticulous troubleshooting, Jordan is adept at handling all aspects of conveyor system management. Whether you’re looking to upgrade your production line with efficient conveyor belts, require custom conveyor rollers for specific operations, or need expert advice on selecting the right conveyor accessories for your facility, Jordan is your reliable consultant. For any inquiries or assistance with conveyor system optimization, Jordan is available to share his wealth of knowledge and experience. Feel free to reach out at any time for professional guidance on all matters related to conveyor rollers, belts, and accessories.