Conveyor Belt EP 800 4: Mining and Stone Handing
The conveyor belt EP 800 4 is renowned for its high tensile strength and durability, making it ideal for heavy-duty applications such as mining and stone handling. This belt features a robust construction with four plies of polyester and nylon fabric, providing exceptional resistance to impact and abrasion. Compared to the EP 400/3 conveyor belt, the conveyor belt EP 800 4 offers superior strength and longevity, making it suitable for medium to long-distance transportation of heavy loads. Its low elongation properties ensure stability and efficiency in demanding environments, reducing maintenance needs and enhancing operational reliability.
Conveyor Belt EP 800 4
Material Composition and Construction
The conveyor belt EP 800 4 is renowned for its robust construction and superior performance in various industrial applications. This particular type of conveyor belt is designed to handle heavy loads and operate in demanding environments, making it an essential component in industries such as mining, manufacturing, and material handling. The key to its durability and efficiency lies in its material composition and construction, specifically the use of polyester and nylon in its fabric carcass.
Fabric Carcass: Polyester and Nylon
The core of the conveyor belt EP 800 4 is its fabric carcass, which is constructed from a blend of polyester (EP) and nylon. This combination of materials provides an excellent balance of strength, flexibility, and resistance to wear and tear.
Polyester (EP): Polyester fibers are used in the warp (longitudinal) direction of the fabric. Polyester is chosen for its high tensile strength, excellent dimensional stability, and resistance to stretching. These properties are crucial for maintaining the integrity of the conveyor belt under heavy loads and high tension. Polyester’s resistance to moisture and chemicals further enhances the belt’s durability, making it suitable for harsh industrial environments.
Nylon: Nylon fibers are used in the weft (transverse) direction. Nylon is known for its exceptional elasticity and impact resistance. This flexibility allows the conveyor belt to absorb shocks and vibrations, reducing the risk of damage and prolonging the belt’s lifespan. Additionally, nylon’s resistance to abrasion ensures that the belt can withstand the constant friction and wear encountered during operation.
Construction of the EP 800 4 Conveyor Belt
The construction of the conveyor belt EP 800 4 involves layering these polyester and nylon materials to create a multi-ply structure. The “800” in its name refers to the belt’s tensile strength, which is 800 N/mm, indicating its capacity to handle heavy loads. The “4” denotes the number of fabric plies, which contribute to the belt’s overall strength and durability.
Multi-Ply Structure: The multi-ply structure of the EP 800 4 conveyor belt consists of four layers of fabric, each bonded together with a rubber compound. This design enhances the belt’s tensile strength and resistance to punctures and tears. The use of multiple plies also distributes the load evenly across the belt, reducing the stress on individual fibers and extending the belt’s service life.
Rubber Compounds: The layers of polyester and nylon fabric are bonded with high-quality rubber compounds that provide additional protection and flexibility. These rubber layers act as a cushion, absorbing impacts and reducing the risk of damage from sharp or abrasive materials. The rubber also enhances the belt’s grip, ensuring that materials are securely transported without slipping.
Performance Advantages
The material composition and construction of the conveyor belt EP 800 4 offer several performance advantages, making it ideal for demanding industrial applications.
High Tensile Strength: The combination of polyester and nylon provides exceptional tensile strength, allowing the belt to handle heavy loads without stretching or breaking. This strength is particularly important in mining and material handling applications, where the conveyor belt must transport large quantities of materials over long distances.
Durability and Longevity: The use of high-quality materials and multi-ply construction ensures that the EP 800 4 conveyor belt is highly durable and resistant to wear and tear. The belt’s ability to withstand harsh conditions, including exposure to moisture, chemicals, and extreme temperatures, contributes to its long service life and reduces the need for frequent replacements.
Flexibility and Impact Resistance: The nylon fibers in the weft direction provide excellent flexibility and impact resistance, allowing the belt to absorb shocks and vibrations without sustaining damage. This flexibility is crucial for applications involving the transportation of heavy or abrasive materials, as it minimizes the risk of punctures and tears.
Chemical and Moisture Resistance: The polyester fibers in the warp direction offer superior resistance to moisture and chemicals, ensuring that the belt maintains its structural integrity even in challenging environments. This resistance is essential for industries such as mining and manufacturing, where the belt may be exposed to corrosive substances.
Applications of Conveyor Belt EP 800 4
The conveyor belt EP 800 4 is widely used in various industries due to its robust construction and reliable performance. Some of the key applications include:
Mining: In the mining industry, the EP 800 4 conveyor belt is used to transport bulk materials such as coal, ore, and gravel. Its high tensile strength and durability make it ideal for handling heavy loads and abrasive materials commonly found in mining operations.
Manufacturing: The belt is also used in manufacturing facilities to move raw materials, components, and finished products along production lines. Its flexibility and impact resistance are beneficial in environments where the belt must navigate through complex systems and handle varying loads.
Material Handling: In material handling applications, the EP 800 4 conveyor belt is used to transport goods and materials in warehouses, distribution centers, and ports. Its ability to withstand heavy loads and resist wear ensures efficient and reliable material movement.
Agriculture: The belt is used in agricultural settings to transport crops, feed, and other agricultural products. Its resistance to moisture and chemicals makes it suitable for outdoor use and exposure to various environmental conditions.
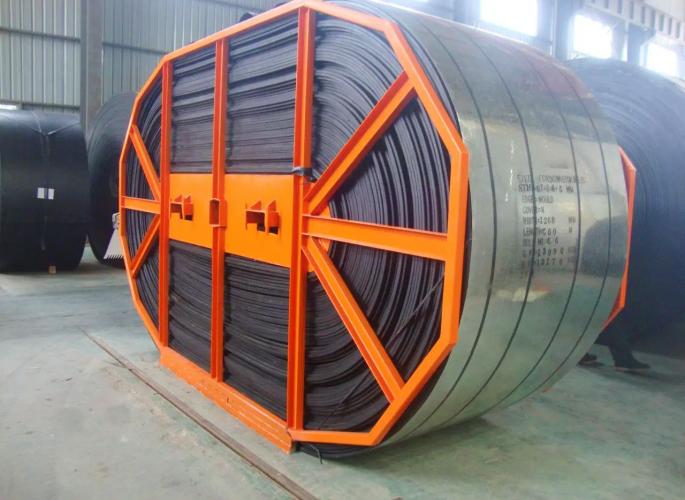
Conveyor Belt EP 800 4 Features and Specifications
Conveyor belt ep 800 4 ply with excellent tensile strength is designed for heavy-duty applications such as mining and stone quarries. Here’s an overview of its features and specifications:
Features:
- Strength and Durability: EP (Polyester/Nylon) belts offer excellent tensile strength and resistance to impact, making them suitable for carrying heavy loads.
- 4 Ply Construction: The 4-ply design provides added strength and flexibility. This construction means the belt has four layers of reinforcing fabric, which adds to its durability and load-bearing capacity.
- Abrasion Resistance: The outer cover of the belt is typically made from a rubber compound that resists wear and tear from sharp and abrasive materials like rocks and minerals.
- Heat Resistance: Suitable for environments where high temperatures are present, such as around conveyor belt drives or in hot climates.
- Oil and Chemical Resistance: Resistant to oils and chemicals that could potentially damage the belt, ensuring longer service life in challenging conditions.
- High Troughability: The belt can form a deep trough, allowing it to carry more material over longer distances efficiently.
Specifications:
- Belt Type: EP 800
- Ply: 4
- Tensile Strength: 800 N/mm per ply
- Thickness: Varies depending on manufacturer and specific application needs, but typically ranges from 15mm to 20mm.
- Width: Available in various widths, typically ranging from 500mm to 2200mm.
- Cover Grade: Grades vary depending on the specific requirements, such as abrasion-resistant, heat-resistant, oil-resistant, etc.
- Temperature Range: Can usually operate in temperatures ranging from -20°C to +100°C, depending on the specific belt design.
Production Process for Conveyor Belt EP 800 4
The production process for a conveyor belt EP 800 4 ply involves several key steps to ensure the final product meets the required specifications and performance standards. Here’s an overview of the typical production process:
Raw Material Preparation
- Polyester and Nylon Fabric: The reinforcing fabric is prepared, usually a combination of polyester (warp) and nylon (weft) to provide the necessary tensile strength and flexibility.
- Rubber Compounds: Different rubber compounds are prepared for the inner and outer layers of the belt. These compounds are mixed with various additives to enhance properties like abrasion resistance, heat resistance, and flexibility.
Calendering
- Fabric Coating: The polyester/nylon fabric is passed through a calendering machine where it is coated with a rubber compound. This process impregnates the fabric with rubber, providing adhesion between the layers.
- Rubber Sheets: Rubber sheets for the top and bottom covers are produced by passing the rubber compound through calendering rollers, creating uniform sheets of the required thickness.
Layering and Building
- Layer Formation: The conveyor belt is built up layer by layer. For an EP 800 4 ply belt, this involves stacking four layers of coated fabric on top of each other.
- Rubber Cover Application: The top and bottom rubber covers are applied to the layered fabric structure. These covers provide protection against wear and environmental factors.
Curing and Vulcanization
- Pressing: The layered belt is placed into a vulcanizing press, which applies heat and pressure to cure the rubber. This process bonds the layers together and solidifies the rubber, giving the belt its final shape and properties.
- Cooling: After vulcanization, the belt is cooled to room temperature, allowing it to solidify and stabilize.
Finishing
- Trimming: The edges of the belt are trimmed to ensure uniform width and remove any excess material.
- Inspection: The finished belt undergoes thorough inspection for any defects, such as air bubbles, incomplete bonding, or surface irregularities.
- Surface Treatment: Depending on the application, the belt may receive additional surface treatments, such as adding a patterned texture to improve grip.
Testing and Quality Control
- Tensile Strength Test: The belt is tested for tensile strength to ensure it meets the EP 800 specification of 800 N/mm per ply.
- Abrasion Resistance Test: The outer cover is tested for resistance to wear and tear.
- Heat Resistance Test: If the belt is designed for high-temperature applications, it is tested for heat resistance.
- Chemical Resistance Test: The belt is tested for resistance to oils, chemicals, and other substances it may encounter in its working environment.
Packaging and Shipping
- Coiling: The finished belt is coiled into rolls for easy handling and transportation.
- Labeling: Each roll is labeled with information about its specifications, such as type, dimensions, and intended use.
- Packaging: The coiled belts are packaged securely to protect them during transit.
This production process ensures that the EP 800 4 ply conveyor belt meets the high standards required for demanding applications in mining, stone quarries, and other heavy-duty industries.
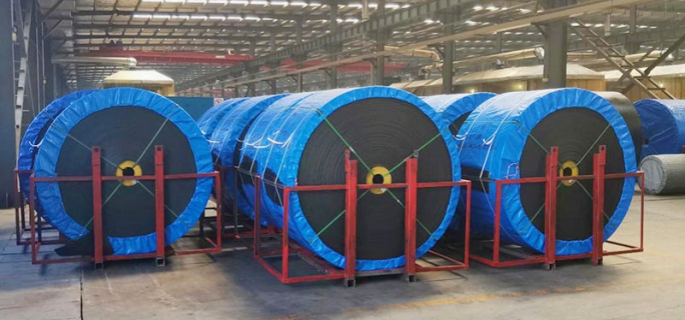
Applications of Conveyor Belt EP 800 4in Mining and Heavy Industries
The conveyor belt EP 800 4 is a robust and highly durable piece of equipment designed to meet the demanding needs of mining, stone handling, and other heavy industries. This specific type of conveyor belt is engineered to withstand tough working conditions and handle substantial loads, making it an essential component in these sectors. In this section, we will delve into the primary applications of the conveyor belt EP 800 4 in these industries, highlighting its capabilities and advantages.
Mining Industry
The mining industry is one of the most demanding environments where conveyor belts are utilized. The conveyor belt EP 800 4 is specifically designed to meet the rigorous requirements of this sector, providing reliable and efficient transportation of mined materials.
Durability and Strength:
In mining operations, conveyor belts must endure extreme conditions, including abrasion, impact, and heavy loads. The conveyor belt EP 800 4 is constructed with multiple layers of polyester (EP) fabric and reinforced with a durable rubber cover, giving it exceptional tensile strength and resistance to wear and tear. This makes it ideal for transporting heavy ores, rocks, and minerals over long distances without the risk of damage or failure.
High Load Capacity:
The high load capacity of the conveyor belt EP 800 4 allows it to move large quantities of material efficiently. In mining operations, where the volume of material can be vast, this conveyor belt ensures continuous and smooth transportation, minimizing downtime and maximizing productivity. Its ability to handle heavy loads without stretching or deforming is crucial for maintaining operational efficiency.
Adaptability to Harsh Conditions:
Mining environments often involve harsh and variable conditions, such as extreme temperatures, moisture, and chemical exposure. The conveyor belt EP 800 4 is designed to withstand these challenges, with materials that are resistant to oil, heat, and chemical degradation. This adaptability ensures that the belt performs consistently and reliably, even in the most challenging mining environments.
Stone Handling
Stone handling is another industry where the conveyor belt EP 800 4 demonstrates its exceptional capabilities. The handling of heavy and abrasive stones requires a conveyor belt that can manage the stress and impact without compromising performance.
Impact Resistance:
The conveyor belt EP 800 4 is engineered to absorb and dissipate the energy from heavy impacts, which are common in stone handling operations. This impact resistance prevents damage to the belt and extends its service life, reducing the need for frequent replacements and maintenance. It ensures that the belt can handle the continuous loading and unloading of stones without sustaining significant wear.
Abrasion Resistance:
Stone handling involves the constant abrasion of the conveyor belt surface by sharp and rough materials. The conveyor belt EP 800 4 features a rubber cover that is highly resistant to abrasion, protecting the underlying fabric and maintaining the belt’s integrity. This resistance to wear ensures that the belt remains functional and efficient over extended periods of use.
Heavy Load Handling:
The capacity to handle heavy loads is critical in stone handling, where large and dense stones must be transported efficiently. The conveyor belt EP 800 4 is designed to support substantial weights without sagging or tearing, ensuring smooth and reliable operation. This capability enhances the overall productivity of stone handling operations by enabling the continuous and rapid movement of materials.
Heavy Industries
Beyond mining and stone handling, the conveyor belt EP 800 4 is also widely used in various other heavy industries, including steel production, cement manufacturing, and bulk material handling. Its design and construction make it suitable for a range of demanding applications.
Steel Production:
In steel production, conveyor belts are used to transport raw materials, such as iron ore, coal, and limestone, as well as finished products like steel sheets and bars. The conveyor belt EP 800 4 is ideal for these tasks due to its high tensile strength and durability. It can handle the heavy and abrasive nature of these materials while maintaining consistent performance, ensuring that production processes run smoothly and efficiently.
Cement Manufacturing:
Cement manufacturing involves the handling of raw materials, such as limestone, clay, and gypsum, as well as the transportation of finished cement products. The conveyor belt EP 800 4 is well-suited for this industry due to its ability to withstand the harsh conditions and heavy loads associated with cement production. Its resistance to abrasion and impact ensures that it can handle the rigorous demands of this industry without compromising on performance.
Bulk Material Handling:
In bulk material handling, conveyor belts are used to transport large volumes of materials, such as grains, fertilizers, and chemicals. The conveyor belt EP 800 4 is designed to manage these tasks efficiently, with a high load capacity and resistance to various environmental factors. Its versatility makes it an excellent choice for a wide range of bulk material handling applications, providing reliable and efficient transportation solutions.
Advantages of Conveyor Belt EP 800 4
The conveyor belt EP 800 4 offers several advantages that make it a preferred choice in mining, stone handling, and other heavy industries:
Enhanced Durability:
The multiple layers of polyester fabric and reinforced rubber cover provide exceptional durability, ensuring a long service life even under harsh conditions.
High Load Capacity:
The belt’s ability to handle heavy loads without stretching or deforming ensures consistent performance and high productivity.
Resistance to Abrasion and Impact:
The robust construction of the belt protects it from wear and damage, reducing maintenance costs and downtime.
Adaptability to Harsh Environments:
The belt’s resistance to oil, heat, and chemical exposure allows it to perform reliably in a variety of challenging conditions.
Cost-Effective:
The long service life and low maintenance requirements of the conveyor belt EP 800 4 make it a cost-effective solution for heavy-duty applications.
The Keys of Conveyor Belt EP 800 4
Maintenance and Durability
The conveyor belt EP 800 4 is a high-performance belt designed to withstand the rigors of heavy-duty industrial applications. Its durability and reliable performance make it an essential component in sectors such as mining, manufacturing, and material handling. However, to maximize its lifespan and maintain its efficiency, proper maintenance practices are crucial. This section will delve into the maintenance requirements and durability aspects of the EP 800 4 conveyor belt, providing valuable tips for ensuring its longevity in demanding environments.
Durability of the Conveyor Belt EP 800 4
The durability of the conveyor belt EP 800 4 is one of its most defining features. Constructed with a robust fabric carcass made from polyester (EP) and nylon, this belt is designed to handle high tensile loads and resist wear and tear. The polyester fibers provide excellent dimensional stability and resistance to stretching, while the nylon fibers offer superior flexibility and impact resistance. These materials work together to create a belt that can endure heavy loads, abrasive materials, and harsh environmental conditions.
The multi-ply structure of the EP 800 4 adds to its durability. With four layers of fabric, each bonded with high-quality rubber compounds, the belt can distribute loads evenly and resist punctures and tears. The rubber compounds also enhance the belt’s grip and protect it from external damage, further contributing to its longevity.
Maintenance Requirements
To ensure the conveyor belt EP 800 4 operates at peak performance and achieves its maximum lifespan, regular maintenance is essential. Here are some key maintenance practices:
Routine Inspections: Regular inspections are crucial for identifying signs of wear and tear early. Inspect the belt for any fraying edges, cracks, or surface damage. Also, check for any unusual noises or vibrations during operation, as these could indicate underlying issues.
Proper Tensioning: Maintaining the correct belt tension is vital for its performance and longevity. Over-tensioning can cause excessive wear on the belt and the conveyor components, while under-tensioning can lead to slippage and misalignment. Use the manufacturer’s guidelines to ensure the belt is tensioned correctly.
Alignment Checks: Misalignment can cause uneven wear and damage to the belt. Regularly check the alignment of the conveyor belt EP 800 4 and adjust it as necessary to ensure it runs smoothly and evenly on the pulleys and rollers.
Cleaning: Keeping the belt clean is essential to prevent the buildup of dirt, debris, and material residues that can cause abrasion and damage. Use appropriate cleaning methods, such as brushing or washing with water, to keep the belt surface clean.
Lubrication: Lubricate the moving parts of the conveyor system, such as bearings and rollers, to reduce friction and wear. Ensure that the lubricant does not come into contact with the belt surface, as it can degrade the rubber compounds.
Regular Maintenance Schedule: Establish a regular maintenance schedule that includes all the above practices. Regular maintenance helps prevent unexpected breakdowns and extends the belt’s lifespan.
Tips for Extending Lifespan
In addition to regular maintenance, here are some tips to further extend the lifespan of the conveyor belt EP 800 4:
Avoid Overloading: Ensure that the load on the conveyor belt does not exceed its specified capacity. Overloading can cause excessive strain and lead to premature wear and damage.
Use Belt Covers: In environments with abrasive materials or harsh conditions, consider using belt covers to protect the belt surface from damage. Covers can also help reduce material spillage and improve overall efficiency.
Monitor Temperature and Environment: Extreme temperatures and harsh environmental conditions can affect the belt’s performance. Monitor the operating environment and take necessary measures, such as ventilation or cooling, to maintain optimal conditions.
Implement Predictive Maintenance: Use advanced monitoring technologies to implement predictive maintenance. Sensors and data analytics can help identify potential issues before they become critical, allowing for timely interventions and reducing the risk of unexpected failures.
Ensuring Reliable Performance
The reliable performance of the conveyor belt EP 800 4 in demanding environments is crucial for uninterrupted operations. Here are some strategies to ensure its reliability:
Training and Supervision: Ensure that all personnel involved in operating and maintaining the conveyor belt are adequately trained. Proper training helps in identifying issues early and performing maintenance tasks correctly.
Emergency Protocols: Establish clear protocols for handling emergencies, such as belt failures or malfunctions. Quick response and efficient handling of issues can minimize downtime and prevent further damage.
Regular Upgrades: Keep abreast of technological advancements and consider regular upgrades to the conveyor system. Upgrades can enhance performance, efficiency, and reliability.
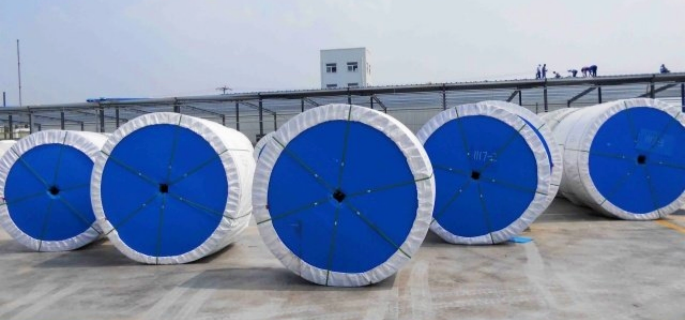
Comparing EP Conveyor Belts: EP 400/3 vs. EP 800 4
When selecting a conveyor belt for industrial applications, it’s essential to choose one that meets the specific demands of the operation. Among the various options available, the conveyor belt EP 800 4 and the EP 400/3 are two popular choices, each offering unique strengths and suitability for different use cases. This comparative analysis will help outline their respective strengths and ideal applications, assisting readers in making an informed decision.
Conveyor Belt EP 400/3
The EP 400/3 conveyor belt is a widely used option in industries that require a reliable yet economical solution for material handling. This belt is constructed with three plies of polyester fabric, providing a balanced combination of strength, flexibility, and affordability.
Strengths:
- Cost-Effective:
The EP 400/3 is known for its cost-efficiency. It offers good performance at a lower price point, making it an ideal choice for businesses looking to optimize their budget without compromising on quality. - Flexibility:
With three plies of polyester fabric, the EP 400/3 provides excellent flexibility. This characteristic makes it suitable for applications requiring a conveyor belt that can navigate tight bends and small pulley diameters. - Moderate Strength:
The tensile strength of the EP 400/3 is suitable for handling moderate loads. It is designed to carry lighter to medium-weight materials efficiently, making it ideal for various standard industrial applications.
Ideal Use Cases:
- Light to Medium Duty Applications:
The EP 400/3 is perfect for industries that handle light to medium-duty tasks. This includes food processing, packaging, and small-scale material handling operations. - Agricultural Sector:
Due to its flexibility and cost-effectiveness, the EP 400/3 is commonly used in the agricultural sector for transporting grains, seeds, and other agricultural products. - General Manufacturing:
In manufacturing settings where moderate strength and flexibility are required, the EP 400/3 serves well, particularly in environments with tight conveyor layouts.
Conveyor Belt EP 800 4
The conveyor belt EP 800 4 is designed for heavy-duty applications, where high tensile strength and durability are paramount. Constructed with four plies of polyester fabric, this belt offers superior load-bearing capacity and resistance to harsh working conditions.
Strengths:
- High Tensile Strength:
The EP 800 4 boasts a tensile strength of 800 N/mm, making it highly suitable for carrying heavy loads. This high strength ensures that the belt can handle substantial weight without stretching or breaking. - Durability:
With four plies of polyester fabric and a robust rubber cover, the EP 800 4 is built to withstand harsh conditions, including abrasion, impact, and extreme temperatures. This durability reduces maintenance costs and extends the belt’s operational life. - Resistance to Wear and Tear:
The sturdy construction of the EP 800 4 provides excellent resistance to wear and tear, making it ideal for environments where the belt is subjected to constant heavy use and abrasive materials.
Ideal Use Cases:
- Mining Industry:
The conveyor belt EP 800 4 is a top choice for the mining industry. Its high tensile strength and durability make it perfect for transporting heavy ores, rocks, and minerals over long distances. - Heavy Industrial Applications:
Industries such as steel production, cement manufacturing, and bulk material handling benefit significantly from the EP 800 4. Its ability to carry heavy loads and resist harsh conditions ensures efficient and reliable operation. - Stone Handling:
In the stone handling industry, where materials are heavy and abrasive, the EP 800 4 excels. Its impact resistance and durability protect it from damage, ensuring continuous and effective material transport.
Comparative Analysis
When comparing the EP 400/3 and conveyor belt EP 800 4, several key differences and considerations emerge.
Load Capacity:
- The EP 400/3 is suitable for light to medium loads, making it ideal for less demanding applications.
- The EP 800 4, with its high tensile strength, is designed to handle heavy loads, making it suitable for more demanding industries like mining and heavy manufacturing.
Durability:
- The EP 400/3 offers good durability for standard applications but may not withstand extremely harsh conditions as well as the EP 800 4.
- The EP 800 4 is built to endure severe conditions, including high abrasion, impact, and temperature variations, providing superior longevity and reliability.
Flexibility:
- The EP 400/3 is more flexible, making it suitable for systems with tight bends and small pulleys.
- The EP 800 4 is less flexible but offers greater strength and durability, which is more critical for heavy-duty applications.
Cost:
- The EP 400/3 is more cost-effective, making it an attractive option for businesses with budget constraints or for applications where extreme durability is not required.
- The EP 800 4 is a higher investment due to its advanced construction and capabilities but offers long-term savings through reduced maintenance and longer service life.
How about Conveyor Belt EP 800 4
Global Standards and Quality Assurance
The conveyor belt EP 800 4 is a high-performance belt designed to meet the rigorous demands of various industrial applications. Ensuring its safety, reliability, and performance requires adherence to stringent global standards and robust quality assurance practices. These standards not only guarantee the belt’s durability and efficiency but also ensure that it operates safely in demanding environments. This section explores the global standards for conveyor belt manufacturing and quality assurance, emphasizing the importance of compliance to maintain the highest levels of operational integrity.
Importance of Global Standards
Global standards for conveyor belts, including the EP 800 4, are established by various international organizations to ensure products meet specific performance, safety, and quality criteria. Adhering to these standards is crucial for several reasons:
Safety: Conveyor belts often operate in hazardous environments where safety is paramount. Global standards ensure that belts are manufactured to withstand specific stresses and conditions, reducing the risk of accidents and injuries.
Reliability: Standards ensure that conveyor belts are reliable and perform consistently under specified conditions. This reliability is essential for minimizing downtime and maintaining continuous operations in industries such as mining and manufacturing.
Performance: Adherence to standards guarantees that conveyor belts meet the performance requirements needed for their intended applications. This includes factors like load-bearing capacity, abrasion resistance, and flexibility.
Interchangeability: Standardization allows for the interchangeability of conveyor belt components and systems across different manufacturers and regions. This is important for global operations and maintenance.
Regulatory Compliance: Many countries have regulations that require conveyor belts to meet specific standards. Compliance with these standards is necessary to avoid legal issues and ensure market access.
Key Global Standards for Conveyor Belts
Several international organizations develop and maintain standards for conveyor belts. Some of the key standards relevant to the conveyor belt EP 800 4 include:
ISO 14890: The International Organization for Standardization (ISO) provides guidelines for rubber and plastic conveyor belts. ISO 14890 specifies the requirements for belts used in general-purpose applications, including the EP 800 4. This standard covers dimensions, mechanical properties, and performance criteria.
DIN 22102: The Deutsches Institut für Normung (DIN) standard 22102 applies to textile conveyor belts used in heavy-duty applications. It outlines specifications for tensile strength, elongation, and cover thickness, ensuring that belts like the EP 800 4 meet the necessary durability and performance requirements.
EN 12882: The European standard EN 12882 specifies safety requirements for conveyor belts used in hazardous environments. It covers fire safety, static electricity, and other safety aspects, ensuring that belts are safe for use in potentially explosive atmospheres.
CEMA: The Conveyor Equipment Manufacturers Association (CEMA) sets standards for the design, manufacturing, and application of conveyor equipment, including belts. CEMA standards ensure that conveyor belts are designed for optimal performance and safety.
Quality Assurance Practices
Adhering to global standards is only part of ensuring the quality and reliability of the conveyor belt EP 800 4. Comprehensive quality assurance practices are also essential. These practices involve systematic procedures and protocols that ensure every belt manufactured meets the required standards and specifications.
Material Testing: Quality assurance begins with the selection and testing of raw materials. For the EP 800 4 conveyor belt, the polyester and nylon fibers used in the fabric carcass must undergo rigorous testing to ensure they meet the specified tensile strength, flexibility, and resistance properties.
Manufacturing Process Control: During manufacturing, strict process controls are implemented to maintain consistency and quality. This includes precise control of temperature, pressure, and timing during the vulcanization process, which bonds the fabric plies and rubber layers together.
Inspection and Testing: Finished conveyor belts are subjected to thorough inspection and testing. This includes visual inspections for defects and imperfections, as well as mechanical tests to verify tensile strength, elongation, and other performance characteristics. For the EP 800 4, tests also ensure that the belt meets the specified N/mm tensile strength.
Performance Testing: In addition to standard mechanical tests, performance testing under simulated operational conditions is conducted. This ensures that the conveyor belt can perform reliably in the environments it is designed for, such as high-load, high-abrasion settings.
Certification and Documentation: Quality assurance also involves proper certification and documentation. Manufacturers provide detailed reports and certificates of compliance that confirm the conveyor belt meets all relevant standards and specifications. This documentation is crucial for end-users and regulatory compliance.
Continuous Improvement: Quality assurance is an ongoing process. Manufacturers like those producing the EP 800 4 conveyor belt continually monitor performance data and feedback to identify areas for improvement. This proactive approach ensures that the conveyor belt remains at the cutting edge of performance and reliability.
Ensuring Safety, Reliability, and Performance
The conveyor belt EP 800 4 exemplifies the importance of adhering to global standards and rigorous quality assurance practices. These measures ensure that the belt performs safely and reliably in demanding environments, providing several benefits:
Extended Lifespan: High-quality materials and manufacturing processes extend the lifespan of the conveyor belt, reducing the frequency and cost of replacements.
Operational Efficiency: Reliable performance minimizes downtime, enhancing the overall efficiency of industrial operations.
Safety: Compliance with safety standards protects workers and equipment, reducing the risk of accidents and associated costs.
Cost-Effectiveness: Long-lasting, reliable conveyor belts lower total ownership costs through reduced maintenance and operational disruptions.
Future Trends in Conveyor Belt Technology
As industries continue to evolve and demands for efficiency, durability, and sustainability increase, the technology behind conveyor belts, including the conveyor belt EP 800 4, is also advancing. Future trends and innovations in conveyor belt technology promise to enhance their capabilities and broaden their applications across various industries. This section explores potential advancements and how they might impact the future use of EP conveyor belts.
Smart Conveyor Belts
One of the most significant trends in conveyor belt technology is the integration of smart features. Smart conveyor belts incorporate sensors and Internet of Things (IoT) technology to provide real-time monitoring and data collection. This innovation is particularly relevant for the conveyor belt EP 800 4, which is used in demanding environments where downtime can be costly.
Real-Time Monitoring:
Smart sensors embedded in the conveyor belt can monitor various parameters such as tension, temperature, speed, and wear. These sensors collect data continuously, which can be analyzed to predict maintenance needs and prevent unexpected failures. For the conveyor belt EP 800 4, real-time monitoring ensures that it operates at peak efficiency, reducing maintenance costs and extending its lifespan.
Predictive Maintenance:
With predictive maintenance, the data collected from smart sensors is analyzed using advanced algorithms to forecast when maintenance should be performed. This approach minimizes downtime and maximizes productivity, as maintenance can be scheduled proactively rather than reactively. In industries like mining and heavy manufacturing, where the conveyor belt EP 800 4 is widely used, predictive maintenance can significantly enhance operational efficiency.
Advanced Materials
The development of new materials is set to revolutionize conveyor belt technology. The conveyor belt EP 800 4 already benefits from advanced polyester (EP) fabric and reinforced rubber, but future materials could offer even greater performance enhancements.
High-Performance Polymers:
Future conveyor belts may incorporate high-performance polymers that provide superior strength, flexibility, and resistance to extreme conditions. These materials could further enhance the durability and load-bearing capacity of the conveyor belt EP 800 4, making it even more suitable for harsh industrial environments.
Self-Healing Materials:
Innovations in materials science are also leading to the development of self-healing materials. These materials can automatically repair small cuts and abrasions, reducing the need for frequent maintenance and extending the belt’s service life. Implementing self-healing materials in the conveyor belt EP 800 4 could offer significant cost savings and improve reliability.
Energy Efficiency
As sustainability becomes a more critical focus for industries worldwide, enhancing the energy efficiency of conveyor belts is a major trend. The conveyor belt EP 800 4 is already designed to be robust and durable, but future advancements could make it even more energy-efficient.
Energy-Efficient Motors:
Integrating energy-efficient motors and drive systems can reduce the overall power consumption of conveyor belts. These advanced motors can operate at optimal efficiency, adjusting speed and torque based on the load, which can result in substantial energy savings. For the conveyor belt EP 800 4, energy-efficient motors would help lower operational costs and reduce its environmental footprint.
Renewable Energy Integration:
The future of conveyor belt technology may also include the integration of renewable energy sources. Solar panels and wind turbines could be used to power conveyor systems, reducing reliance on fossil fuels and minimizing carbon emissions. The conveyor belt EP 800 4 could benefit from such innovations, making it a more sustainable choice for industries committed to reducing their environmental impact.
Automation and Robotics
Automation and robotics are transforming industrial operations, and conveyor belts are no exception. The conveyor belt EP 800 4 could see significant enhancements through increased automation and the use of robotics.
Automated Control Systems:
Automated control systems can manage the operation of conveyor belts more precisely, adjusting speed, tension, and other parameters to optimize performance. These systems can respond to real-time data and environmental conditions, ensuring that the conveyor belt EP 800 4 operates efficiently and safely.
Robotic Inspection and Maintenance:
Robotics can also play a role in the inspection and maintenance of conveyor belts. Drones and robotic arms equipped with cameras and sensors can inspect the conveyor belt EP 800 4 for signs of wear or damage, performing maintenance tasks without the need for human intervention. This technology can reduce downtime and improve safety by minimizing the need for workers to perform hazardous maintenance activities.
Customization and Modular Design
The demand for customized and modular conveyor belt systems is growing as industries seek solutions tailored to their specific needs. The conveyor belt EP 800 4 could be adapted to meet these demands through advancements in customization and modular design.
Tailored Solutions:
Future conveyor belts may be designed to meet the exact requirements of different industries, offering customized solutions that optimize performance for specific applications. For the conveyor belt EP 800 4, this could mean enhancements that improve its suitability for particular materials or operating conditions.
Modular Components:
Modular design allows for the quick assembly and disassembly of conveyor belt systems. This flexibility is particularly valuable in industries where operational needs may change frequently. The conveyor belt EP 800 4 could benefit from modular components that make it easier to reconfigure and adapt to different tasks, enhancing its versatility and usability.
Environmental Sustainability
Sustainability is an increasingly important consideration for all industrial operations. Future trends in conveyor belt technology will likely focus on reducing environmental impact and promoting sustainable practices.
Recyclable Materials:
Using recyclable materials in the construction of conveyor belts can significantly reduce waste and promote sustainability. The conveyor belt EP 800 4 could incorporate materials that are easier to recycle at the end of their life cycle, contributing to a circular economy.
Eco-Friendly Manufacturing Processes:
Advancements in manufacturing processes could also make the production of conveyor belts more environmentally friendly. Techniques that reduce energy consumption, minimize waste, and use sustainable materials will be crucial in developing future conveyor belts. The conveyor belt EP 800 4 could be produced using such eco-friendly processes, further enhancing its appeal to environmentally conscious industries.
FAQS about Conveyor Belt Ep 800 4
A conveyor belt EP 800 4 is a specific type of conveyor belt that is designed for heavy-duty industrial applications. The “EP” in the designation stands for “Polyester/Polyamide” (also known as Nylon), indicating the materials used in the belt’s fabric carcass. The number “800” refers to the tensile strength of the belt in Newtons per millimeter (N/mm) of belt width, meaning this belt has a tensile strength of 800 N/mm. The “4” indicates the number of plies or layers of fabric in the belt. This multi-ply construction provides the belt with added strength and durability, making it suitable for transporting heavy materials such as minerals, coal, and aggregates over long distances. The EP 800 4 belt is known for its high performance, resistance to wear and tear, and ability to maintain integrity under high stress.
In conveyor belt terminology, “EP” stands for “Polyester/Polyamide” (also known as Nylon). These letters refer to the materials used in the belt’s fabric carcass. Polyester is used in the warp (lengthwise) direction of the belt, providing excellent resistance to elongation and ensuring dimensional stability. Polyamide (Nylon) is used in the weft (crosswise) direction, offering superior flexibility and resistance to impact and abrasion. The combination of these materials results in a conveyor belt that is both strong and flexible, capable of handling heavy loads and harsh working conditions. EP conveyor belts are widely used in various industries, including mining, construction, and manufacturing, due to their durability, high tensile strength, and resistance to chemicals and moisture.
The strength of an EP (Polyester/Polyamide) conveyor belt is typically measured in terms of its tensile strength, which is expressed in Newtons per millimeter (N/mm) of belt width. This measurement indicates the maximum force that the belt can withstand before breaking. For example, an EP 800 conveyor belt has a tensile strength of 800 N/mm, meaning it can endure a force of 800 Newtons per millimeter of its width. The strength of EP belts varies depending on their specific construction and the number of plies they contain. Higher tensile strength belts, such as EP 1000 or EP 1600, are used in more demanding applications where heavy materials need to be transported over long distances or in harsh environments. The robust construction of EP belts ensures they can handle significant stress and provide reliable performance in industrial settings.
The elongation of an EP (Polyester/Polyamide) conveyor belt refers to the extent to which the belt can stretch under load before reaching its breaking point. This characteristic is crucial for ensuring the belt’s stability and performance during operation. Typically, the elongation at break for EP belts is around 10% to 20%, meaning the belt can stretch up to 20% of its original length before breaking. However, the working elongation, or the elongation that occurs during normal operation under load, is much lower, usually around 1.5% to 2%. This low working elongation is essential for maintaining belt tension and preventing excessive sagging or slack, which could lead to operational issues. The combination of polyester and polyamide in the EP belt’s fabric carcass provides a balanced blend of strength and flexibility, ensuring the belt can withstand the stresses of heavy-duty industrial applications without significant elongation.
What is M grade in conveyor belt?
M grade in conveyor belts refers to a specific type of belt with high abrasion resistance. It is designed to withstand wear and tear from abrasive materials, making it ideal for applications in industries like mining, quarrying, and construction where the belt is exposed to rough and abrasive materials.
Rubber Conveyor Belts: These are the most common and are used for a wide range of applications, including heavy-duty industrial processes.
Metal Conveyor Belts: Made of metal, these belts are used for high-temperature applications or where strong and durable belts are required.
Plastic Conveyor Belts: These are lightweight and used in food processing, packaging, and other industries where hygiene is critical.
Grade M in conveyor belts indicates that the belt has high resistance to abrasion. This means it can handle heavy and abrasive materials without significant wear, making it suitable for tough environments like mining and quarrying.
Belt rating refers to the strength and durability of a conveyor belt, usually expressed in terms of its tensile strength. This is measured in Newtons per millimeter (N/mm) and indicates the maximum stress the belt can withstand. For example, an EP 800 belt has a tensile strength of 800 N/mm.
EP Belt (Polyester/Nylon): Made of polyester in the warp and nylon in the weft. It offers excellent strength, low elongation, and good resistance to moisture.
NN Belt (Nylon/Nylon): Made entirely of nylon fabric. These belts have high tensile strength, excellent flexibility, and good resistance to impact and abrasion.
The thickness of a 4 ply conveyor belt typically ranges from 15mm to 20mm. The exact thickness depends on the specific requirements of the application, including the type of materials being transported and the operating conditions.
Last Updated on August 5, 2024 by Jordan Smith
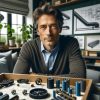
Jordan Smith, a seasoned professional with over 20 years of experience in the conveyor system industry. Jordan’s expertise lies in providing comprehensive solutions for conveyor rollers, belts, and accessories, catering to a wide range of industrial needs. From initial design and configuration to installation and meticulous troubleshooting, Jordan is adept at handling all aspects of conveyor system management. Whether you’re looking to upgrade your production line with efficient conveyor belts, require custom conveyor rollers for specific operations, or need expert advice on selecting the right conveyor accessories for your facility, Jordan is your reliable consultant. For any inquiries or assistance with conveyor system optimization, Jordan is available to share his wealth of knowledge and experience. Feel free to reach out at any time for professional guidance on all matters related to conveyor rollers, belts, and accessories.