Advantages of Consistent 2 Ply Conveyor Belt Thickness
The importance of 2 ply conveyor belt thickness in industrial applications cannot be overstated. Conveyor belts are crucial for transporting materials efficiently and safely across various sectors. The thickness of a conveyor belt plays a significant role in its durability, strength, and overall performance. A 2 ply conveyor belt consists of two layers of material, which provide added strength and resistance to wear and tear compared to single-ply belts. This makes 2 ply conveyor belts ideal for heavy-duty applications where a robust and reliable solution is essential. Understanding the specific thickness requirements helps in selecting the right conveyor belt for specific industrial needs.
Materials Used in 2 Ply Conveyor Belt Thickness
Detailed Description of the Materials Commonly Used in 2 Ply Conveyor Belts
The 2 ply conveyor belt thickness is a crucial factor in determining the belt’s strength, durability, and suitability for various applications. The materials used in the construction of these belts play a significant role in achieving the desired thickness and performance characteristics. The primary materials used in 2 ply conveyor belts include:
- Polyester (EP):
Polyester is one of the most common materials used in conveyor belts due to its excellent strength-to-weight ratio. Polyester fabrics provide high tensile strength and resistance to stretching, making them ideal for applications where dimensional stability is essential. The use of polyester in 2 ply conveyor belts ensures that the belts maintain their shape and structural integrity even under heavy loads. - Nylon (NN):
Nylon is another popular material used in conveyor belts, known for its flexibility and high impact resistance. Nylon fabrics are often used in combination with polyester to create belts that can withstand dynamic loads and repeated flexing. The inclusion of nylon in 2 ply conveyor belts enhances their durability and ability to absorb shock, making them suitable for demanding applications. - Cotton:
Cotton is used in some conveyor belts for its natural properties, including good adhesion to rubber and excellent flexibility. While not as strong as polyester or nylon, cotton can be an effective material for light to medium-duty applications where flexibility and cost-effectiveness are important considerations. - Rubber:
The rubber used in conveyor belts serves as both the bonding agent and the protective outer layer. Various types of rubber, such as natural rubber, neoprene, and nitrile, are used depending on the specific application requirements. Rubber provides essential properties such as abrasion resistance, weather resistance, and the ability to handle different temperature ranges. It also helps in achieving the desired thickness and cushioning effect for the belt.
Benefits of These Materials in Ensuring Optimal Thickness
The combination of these materials in the construction of 2 ply conveyor belts offers several benefits that contribute to achieving and maintaining the optimal thickness:
- Strength and Durability:
The use of polyester and nylon fabrics provides high tensile strength and resistance to stretching and tearing. This ensures that the belt can handle heavy loads without compromising its thickness or structural integrity. - Flexibility:
Nylon and cotton fabrics enhance the flexibility of the belt, allowing it to bend and flex without cracking or delaminating. This flexibility is crucial for applications that involve intricate conveyor systems with curves and bends. - Abrasion and Impact Resistance:
The rubber layers in the belt provide excellent abrasion and impact resistance, protecting the inner fabric layers from wear and tear. This prolongs the life of the belt and maintains its thickness over time. - Weather and Chemical Resistance:
Depending on the type of rubber used, the conveyor belt can offer resistance to various environmental factors such as extreme temperatures, moisture, and chemicals. This ensures that the belt maintains its performance and thickness even in harsh conditions. - Cost-Effectiveness:
The combination of materials used in 2 ply conveyor belts provides a cost-effective solution for many industrial applications. Polyester and nylon offer high performance at a reasonable cost, while cotton provides a budget-friendly option for less demanding uses.
Manufacturing Process of 2 Ply Conveyor Belt Thickness
Step-by-Step Explanation of the Manufacturing Process
The manufacturing process of a 2 ply conveyor belt involves several stages to ensure the correct thickness, strength, and durability of the final product. Here is a detailed step-by-step explanation of the process:
- Material Selection and Preparation:
The first step involves selecting the appropriate materials for the belt, such as polyester, nylon, cotton fabrics, and rubber compounds. These materials are then prepared by cutting them into the required sizes and shapes. - Calendering:
Calendering is the process of bonding the fabric layers with rubber. The prepared fabric layers are passed through large rollers (calenders) where they are coated with a layer of rubber on both sides. This process ensures that the fabric layers are thoroughly impregnated with rubber, providing strength and flexibility. - Ply Assembly:
Once the fabric layers are coated with rubber, they are assembled to form the 2 ply structure. The rubber-coated fabric layers are placed one on top of the other, ensuring proper alignment and bonding. This assembly process is critical for achieving the desired 2 ply conveyor belt thickness. - Vulcanization:
The assembled belt is then subjected to a process called vulcanization, where it is heated under pressure. Vulcanization causes the rubber to cure and bond with the fabric layers, resulting in a strong, durable belt. This process also ensures that the belt achieves the required thickness and mechanical properties. - Cooling and Trimming:
After vulcanization, the belt is cooled to room temperature. Once cooled, the belt is trimmed to remove any excess material and ensure uniform thickness throughout its length and width. - Inspection and Quality Control:
The final stage involves inspecting the belt for any defects or inconsistencies. The belt’s thickness is measured and tested to ensure it meets the specified standards. Quality control checks also include testing for tensile strength, flexibility, and abrasion resistance.
How Thickness is Achieved and Maintained During Production
Achieving and maintaining the desired thickness of a 2 ply conveyor belt during production involves several key factors:
- Precision Calendering:
The calendering process is critical for controlling the thickness of the rubber layers. Precise control of the roller settings and the amount of rubber applied ensures that the fabric layers are uniformly coated. - Accurate Ply Assembly:
Proper alignment and bonding of the fabric layers during ply assembly are essential for achieving the correct thickness. Any misalignment can result in variations in thickness and affect the belt’s performance. - Controlled Vulcanization:
The vulcanization process must be carefully controlled to ensure consistent curing of the rubber. This involves maintaining the correct temperature, pressure, and curing time to achieve the desired thickness and mechanical properties. - Quality Control Measures:
Regular quality control checks throughout the production process help to identify and correct any deviations in thickness. This includes measuring the thickness at multiple points along the belt and performing mechanical tests to ensure compliance with specifications.
Applications of 2 Ply Conveyor Belt Thickness
Various Industrial Applications Where 2 Ply Conveyor Belts are Utilized
The 2 ply conveyor belt thickness makes it suitable for a wide range of industrial applications. Some of the key industries and applications include:
- Manufacturing:
In manufacturing plants, 2 ply conveyor belts are used to transport raw materials, semi-finished products, and finished goods along production lines. The belts’ strength and durability make them ideal for handling heavy loads and continuous operation, ensuring efficient production processes. - Mining and Quarrying:
The mining and quarrying industries require conveyor belts that can withstand harsh conditions and heavy loads. The 2 ply conveyor belt thickness provides the necessary strength and resistance to abrasion, making it suitable for transporting minerals, ores, and rocks from extraction sites to processing facilities. - Agriculture:
In agricultural settings, these belts are used for conveying grains, seeds, and other agricultural products. The belts’ durability and flexibility allow them to handle bulk quantities efficiently, reducing manual labor and improving productivity during harvest and processing. - Food Processing:
Food processing plants use 2 ply conveyor belts to move products through various stages of production, including sorting, washing, cooking, and packaging. The belts are designed to meet hygiene standards and can be easily cleaned, ensuring safe and sanitary handling of food products. - Construction:
In the construction industry, conveyor belts are used to transport materials such as sand, gravel, and concrete. The 2 ply conveyor belt thickness provides the necessary strength to handle these heavy materials, ensuring efficient material handling on construction sites.
Importance of Thickness in These Applications
The thickness of 2 ply conveyor belts is crucial for their performance and suitability in various industrial applications. Here are some reasons why thickness is important:
- Load Capacity:
The thickness of the belt determines its ability to handle different load capacities. Thicker belts can support heavier loads without stretching or tearing, making them ideal for demanding applications. - Durability:
Thicker belts have more material to withstand wear and tear, extending their lifespan. This is particularly important in industries such as mining and construction, where the belts are exposed to abrasive materials and harsh conditions. - Flexibility:
While thicker belts provide added strength, they must also maintain flexibility to navigate curves and bends in conveyor systems. The right balance of thickness and flexibility ensures smooth and efficient operation. - Resistance to Abrasion and Impact:
Thicker belts offer better resistance to abrasion and impact, protecting the inner fabric layers from damage. This is essential in applications where the belts are subjected to frequent loading and unloading of heavy or abrasive materials. - Maintenance and Downtime:
Belts with the appropriate thickness require less frequent maintenance and are less prone to failures. This reduces downtime and maintenance costs, improving overall productivity and efficiency.
The 2 ply conveyor belt thickness is a critical factor in determining the belt’s performance, durability, and suitability for various industrial applications. The materials used in the construction of these belts, such as polyester, nylon, cotton, and rubber, provide the necessary strength, flexibility, and resistance to wear and tear. The manufacturing process, including calendering, ply assembly, and vulcanization, ensures that the belts achieve the desired thickness and mechanical properties.
Understanding the importance of thickness in different applications helps in selecting the right conveyor belt for specific needs. Whether in manufacturing, mining, agriculture, food processing, or construction, 2 ply conveyor belts offer a reliable and efficient solution for material handling, enhancing productivity and reducing operational costs. Proper maintenance and quality control during production further ensure that these belts perform optimally and have a long service life.
Advantages of Consistent 2 Ply Conveyor Belt Thickness
Benefits of Maintaining a Consistent Thickness in Conveyor Belts
Maintaining a consistent 2 ply conveyor belt thickness offers numerous advantages, crucial for optimal operation in industrial settings. A uniform thickness ensures that the conveyor belt operates smoothly, reducing the likelihood of disruptions that could halt production. Here are some key benefits of maintaining consistent thickness:
- Enhanced Durability and Longevity: A conveyor belt with consistent thickness experiences less wear and tear, as the load is evenly distributed across its surface. This uniformity prevents areas of excessive stress, thereby extending the belt’s lifespan and reducing the need for frequent replacements.
- Improved Load Distribution: When the thickness of the conveyor belt is uniform, the load is evenly distributed across its entire width. This balance minimizes the risk of slippage and ensures that the belt can handle the maximum load capacity effectively.
- Reduced Maintenance Costs: Consistent 2 ply conveyor belt thickness reduces the frequency of maintenance interventions. By minimizing the chances of uneven wear and mechanical failures, businesses can save on maintenance costs and allocate resources more efficiently.
- Increased Efficiency and Productivity: A conveyor belt operating at consistent thickness enhances the overall efficiency of the conveyor system. The smooth operation without interruptions ensures continuous production, leading to higher productivity and better throughput.
- Enhanced Safety: A uniform conveyor belt thickness reduces the risk of belt failure, which can lead to accidents and injuries. By maintaining consistent thickness, workplaces can ensure a safer environment for their employees.
- Optimized Energy Consumption: Conveyor belts with consistent thickness require less energy to operate smoothly. The even distribution of load reduces the strain on the conveyor motor, leading to optimized energy consumption and cost savings on energy bills.
- Better Material Handling: Consistent thickness ensures that the conveyor belt can handle a variety of materials efficiently. Whether it’s transporting heavy loads or delicate items, the uniform surface supports better material handling and reduces the chances of product damage.
Impact on Efficiency and Productivity
The impact of maintaining a consistent 2 ply conveyor belt thickness on efficiency and productivity is profound. A consistent thickness ensures that the conveyor belt performs reliably, without unexpected breakdowns or interruptions. This reliability is crucial for maintaining high levels of productivity and meeting production targets. Here’s how consistent thickness influences efficiency and productivity:
- Minimized Downtime: Downtime can be costly for any production facility. By ensuring a consistent thickness, the chances of belt failure are significantly reduced, leading to fewer interruptions and more continuous operation. This minimizes downtime and keeps production schedules on track.
- Smooth Operation: A conveyor belt with consistent thickness operates smoothly, reducing friction and mechanical resistance. This smooth operation means that the belt can move materials more efficiently, leading to faster processing times and increased output.
- Improved Accuracy: For industries that rely on precise material handling, such as packaging or assembly lines, consistent thickness ensures that the conveyor belt moves materials accurately. This precision helps in maintaining the quality of the end product and reduces the likelihood of errors.
- Higher Throughput: Consistent thickness allows the conveyor system to handle higher volumes of material without the risk of jams or breakdowns. This higher throughput is essential for industries with high production demands, enabling them to meet their targets more effectively.
- Better Resource Utilization: With fewer interruptions and breakdowns, resources such as labor, machinery, and time are utilized more efficiently. Employees can focus on productive tasks rather than troubleshooting conveyor issues, leading to better overall resource management.
- Consistency in Product Quality: Maintaining consistent thickness ensures that the conveyor belt operates reliably, which in turn helps in maintaining consistent product quality. Variations in conveyor belt performance can lead to inconsistencies in product handling, affecting the final product quality.
- Cost Savings: Reduced maintenance costs, optimized energy consumption, and fewer production interruptions lead to significant cost savings. These savings can be reinvested in other areas of the business, enhancing overall profitability.
Factors Affecting 2 Ply Conveyor Belt Thickness
Common Factors That Can Influence the Thickness of a 2 Ply Conveyor Belt
Several factors can influence the thickness of a 2 ply conveyor belt, affecting its performance and longevity. Understanding these factors is crucial for managing and maintaining the desired thickness. Here are the common factors:
- Manufacturing Variations: Differences in the manufacturing process can lead to variations in belt thickness. Ensuring that belts are produced with stringent quality control measures can help maintain consistent thickness.
- Material Quality: The quality of the materials used in the construction of the conveyor belt plays a significant role in its thickness. High-quality materials are less likely to wear unevenly, maintaining consistent thickness over time.
- Operating Conditions: Harsh operating conditions, such as extreme temperatures, abrasive materials, and high levels of moisture, can cause uneven wear and affect the thickness of the conveyor belt. Proper selection of belts designed to withstand specific conditions is essential.
- Load Distribution: Uneven load distribution can lead to localized wear, causing variations in belt thickness. Ensuring that the load is evenly distributed across the belt can help maintain uniform thickness.
- Maintenance Practices: Regular maintenance practices, such as cleaning and inspections, play a crucial role in preserving belt thickness. Neglecting these practices can lead to buildup of debris and uneven wear.
- Belt Tension: Incorrect tensioning of the conveyor belt can cause uneven stretching and wear, leading to variations in thickness. Proper tensioning is necessary to maintain consistent belt thickness.
- Environmental Factors: Exposure to chemicals, UV light, and other environmental factors can degrade the belt material, affecting its thickness. Selecting belts with appropriate resistance properties can mitigate these effects.
How to Manage and Control These Factors
Effectively managing and controlling the factors that influence 2 ply conveyor belt thickness is essential for maintaining optimal performance. Here are some strategies:
- Implementing Quality Control: Ensure that conveyor belts are manufactured under strict quality control standards. Regularly inspect new belts for consistency in thickness before installation.
- Using High-Quality Materials: Invest in conveyor belts made from high-quality materials that are designed to resist wear and tear. This investment can pay off in the long run by reducing maintenance costs and extending belt life.
- Optimizing Operating Conditions: Select conveyor belts that are specifically designed to withstand the operating conditions of your facility. For example, choose belts with high heat resistance for high-temperature environments or belts with chemical resistance for corrosive conditions.
- Ensuring Even Load Distribution: Design conveyor systems to distribute loads evenly across the belt. This can involve using appropriately sized belts, adjusting the positioning of materials, and ensuring that load weights are balanced.
- Regular Maintenance and Inspections: Establish a routine maintenance schedule that includes regular inspections of the conveyor belt for signs of wear and thickness variations. Promptly address any issues that are identified to prevent further deterioration.
- Proper Belt Tensioning: Regularly check and adjust the tension of the conveyor belt to ensure it is within the manufacturer’s recommended range. Use tensioning devices and follow best practices for tensioning to prevent uneven wear.
- Environmental Protection: Protect conveyor belts from harmful environmental factors by implementing protective measures such as shielding from UV light, using covers to protect from chemicals, and maintaining a clean operating environment.
- Training and Awareness: Train employees on the importance of maintaining consistent belt thickness and the factors that can affect it. Raise awareness about proper handling and maintenance practices to ensure everyone is contributing to the longevity of the conveyor belt.
Maintenance of 2 Ply Conveyor Belt Thickness
Best Practices for Maintaining the Thickness of a 2 Ply Conveyor Belt
Proper maintenance is key to ensuring that the 2 ply conveyor belt thickness remains consistent over its operational life. Here are some best practices for maintaining the thickness of a 2 ply conveyor belt:
- Regular Cleaning: Keep the conveyor belt clean to prevent buildup of debris and materials that can cause uneven wear. Use appropriate cleaning methods and materials to ensure the belt remains in good condition.
- Scheduled Inspections: Conduct regular inspections to check for signs of wear, damage, or variations in thickness. Use measuring tools to accurately assess the thickness of the belt at various points.
- Lubrication: Ensure that the conveyor system is properly lubricated to reduce friction and wear on the belt. Use the correct type of lubricant recommended by the belt manufacturer.
- Alignment Checks: Regularly check the alignment of the conveyor belt to ensure it is running true. Misalignment can cause uneven wear and affect the belt’s thickness.
- Tension Monitoring: Continuously monitor and adjust the tension of the conveyor belt to ensure it is within the recommended range. Use automatic tensioning devices if available to maintain consistent tension.
- Wear Strip Replacement: Replace wear strips and other components that come into direct contact with the belt as needed. These components can wear down over time and affect the belt’s thickness.
- Protective Measures: Implement protective measures such as using belt scrapers and cleaners to remove materials that can cause abrasion. Use covers or guards to protect the belt from external elements.
- Record Keeping: Maintain detailed records of maintenance activities, including inspections, repairs, and adjustments. This documentation can help identify patterns and predict when maintenance is needed.
Tips for Regular Inspection and Maintenance Routines
Regular inspection and maintenance routines are essential for preserving the 2 ply conveyor belt thickness. Here are some tips to help establish effective routines:
- Develop a Maintenance Schedule: Create a detailed maintenance schedule that outlines when inspections and maintenance activities should be performed. Stick to this schedule to ensure consistency.
- Use a Checklist: Develop a comprehensive checklist that covers all aspects of the conveyor belt and system. This checklist should include items such as cleaning, lubrication, alignment, and tension checks.
- Involve Trained Personnel: Ensure that maintenance tasks are performed by trained personnel who understand the importance of maintaining consistent belt thickness. Provide ongoing training to keep them updated on best practices.
- Utilize Technology: Leverage technology such as automated monitoring systems and sensors to continuously track the condition of the conveyor belt. These systems can provide real-time data and alerts for maintenance needs.
- Visual Inspections: Conduct regular visual inspections to identify obvious signs of wear or damage. Look for uneven wear patterns, cracks, and areas where the belt thickness may be compromised.
- Thickness Measurements: Use calipers or other measuring tools to take precise measurements of the belt thickness at regular intervals. Record these measurements to track changes over time.
- Preventive Maintenance: Focus on preventive maintenance rather than reactive maintenance. Address potential issues before they become major problems to avoid unexpected downtime and costly repairs.
- Collaborate with Manufacturers: Work closely with conveyor belt manufacturers to understand the specific maintenance requirements for the 2 ply conveyor belt. Follow their recommendations and guidelines to ensure optimal performance.
By following these best practices and tips, you can effectively maintain the 2 ply conveyor belt thickness, ensuring reliable operation, reduced maintenance costs, and extended belt life. This proactive approach to maintenance will contribute to the overall efficiency and productivity of your conveyor system, providing significant benefits to your industrial operations.
FAQs about 2 Ply Conveyor Belt Thickness
A 2 ply conveyor belt typically has a thickness ranging from 5mm to 8mm. The exact thickness can vary depending on the materials used in its construction and the specific requirements of its application. The term “2 ply” indicates that the belt is made up of two layers of fabric, usually polyester or nylon, which are bonded together with layers of rubber. This multi-layered construction provides the belt with enhanced strength and durability, making it suitable for a variety of industrial applications. The thickness of the belt contributes to its ability to handle different load capacities and resist wear and tear.
The thickness of a conveyor belt can vary significantly based on its type and intended use. Standard conveyor belts typically range in thickness from 3mm to 20mm. Thinner belts, around 3mm to 5mm, are often used in lighter applications such as packaging or food processing. Medium thickness belts, around 6mm to 12mm, are used in more demanding applications like manufacturing and logistics. Thicker belts, up to 20mm, are designed for heavy-duty applications such as mining and quarrying, where they need to transport large quantities of materials and endure harsh operating conditions. The thickness of a conveyor belt is crucial as it affects its strength, flexibility, and overall performance.
A 3 ply conveyor belt typically has a thickness ranging from 7mm to 10mm. The “3 ply” designation means that the belt consists of three layers of fabric, usually made from materials like polyester or nylon, bonded together with rubber. This multi-layered construction enhances the belt’s strength, durability, and ability to handle heavier loads compared to 2 ply belts. The added thickness of a 3 ply belt makes it suitable for more demanding industrial applications where higher tensile strength and resistance to abrasion are required. Industries such as mining, construction, and manufacturing often use 3 ply belts to ensure reliable and efficient material handling.
The standard size of a conveyor belt can vary widely depending on the application and industry requirements. Conveyor belts come in various widths, lengths, and thicknesses to accommodate different types of materials and operating conditions. Common standard widths include 300mm, 500mm, 800mm, 1000mm, and 1200mm. The length of a conveyor belt can range from a few meters to several kilometers, depending on the layout of the conveyor system and the distance materials need to be transported. Thickness, as mentioned earlier, can range from 3mm to 20mm. When selecting a conveyor belt, it’s important to consider factors such as the type of material being transported, the operating environment, and the specific requirements of the conveyor system to determine the most suitable size.
Last Updated on June 12, 2024 by Jordan Smith
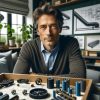
Jordan Smith, a seasoned professional with over 20 years of experience in the conveyor system industry. Jordan’s expertise lies in providing comprehensive solutions for conveyor rollers, belts, and accessories, catering to a wide range of industrial needs. From initial design and configuration to installation and meticulous troubleshooting, Jordan is adept at handling all aspects of conveyor system management. Whether you’re looking to upgrade your production line with efficient conveyor belts, require custom conveyor rollers for specific operations, or need expert advice on selecting the right conveyor accessories for your facility, Jordan is your reliable consultant. For any inquiries or assistance with conveyor system optimization, Jordan is available to share his wealth of knowledge and experience. Feel free to reach out at any time for professional guidance on all matters related to conveyor rollers, belts, and accessories.