Efficient Conveyor Head and Tail Pulley Functions
About the importance of conveyor head and tail pulleys is essential for the efficient operation of any conveyor system. The conveyor head and tail pulleys play a crucial role in driving and supporting the conveyor belt. The head pulley, located at the discharge end, is responsible for moving the belt forward, while the tail pulley, at the loading end, provides tension and alignment. Proper maintenance and alignment of the conveyor head and tail pulleys ensure smooth operation and prevent downtime. An overview of conveyor head and tail systems highlights their significance in material handling, emphasizing the need for high-quality components and regular inspection.
Conveyor Head and Tail Pulley Functions
About the dynamics of conveyor belt systems is essential for optimizing performance and ensuring reliability in various industrial applications. Key components such as the conveyor head and tail pulleys play a pivotal role in the overall function of the conveyor system. This section delves into the interaction between these critical components and the conveyor belt, as well as the importance of maintaining belt tension and alignment.
Interaction Between Head Pulley, Tail Pulley, and Conveyor Belt
The conveyor head and tail pulleys are integral parts of the conveyor system, each serving distinct yet complementary functions. The head pulley, located at the discharge end of the conveyor, drives the belt and ensures that the material is conveyed effectively to the next stage of processing or packaging. Conversely, the tail pulley, situated at the feed end, helps guide the belt and maintains the necessary tension for smooth operation.
The interaction between the head pulley, tail pulley, and conveyor belt is a complex yet vital aspect of conveyor belt dynamics. The head pulley is typically powered by an electric motor, which imparts motion to the belt. This motion enables the belt to transport materials from the tail pulley, through the conveyor system, to the head pulley. The tail pulley, while not powered, provides a counterpoint that helps maintain the tension required for the belt to function correctly.
Several factors influence the interaction between these components, including the type of material being conveyed, the speed of the belt, and the load on the system. For instance, heavy or abrasive materials require more robust pulleys and belts to withstand the increased wear and tear. Additionally, the speed at which the belt moves can affect the efficiency of material transport and the overall energy consumption of the system.
Maintaining Belt Tension and Alignment for Optimal Performance
Maintaining proper belt tension and alignment is crucial for the optimal performance of conveyor systems. Incorrect tension can lead to a variety of issues, including slippage, excessive wear, and even system failure. Similarly, misalignment can cause uneven wear on the belt and pulleys, leading to increased maintenance costs and downtime.
Belt Tension: The tension of the conveyor belt must be carefully regulated to ensure that it remains in contact with the pulleys and operates efficiently. Too much tension can cause the belt to stretch and wear prematurely, while too little tension can lead to slippage and loss of efficiency. The conveyor head and tail pulleys work together to maintain the appropriate tension. The head pulley, by driving the belt, ensures that the tension is distributed evenly along the length of the conveyor. The tail pulley, equipped with adjustable mechanisms, allows operators to fine-tune the tension to match the specific requirements of the material being conveyed and the operational conditions.
Belt Alignment: Proper alignment of the conveyor belt is essential to prevent uneven wear and ensure smooth operation. Misalignment can occur due to a variety of factors, including improper installation, wear and tear, and operational stresses. The conveyor head and tail pulleys must be precisely aligned to guide the belt along the intended path. Misalignment can cause the belt to drift to one side, leading to uneven wear on the belt edges and increased stress on the pulleys.
To maintain alignment, regular inspections and adjustments are necessary. These inspections should include checking the position of the pulleys, the condition of the belt, and the alignment of the entire conveyor structure. Advanced systems, such as laser alignment tools, can provide precise measurements and help operators make the necessary adjustments quickly and accurately.
Dynamic Adjustments: Modern conveyor systems often incorporate automated mechanisms to adjust belt tension and alignment dynamically. These systems use sensors to monitor the position and condition of the belt in real-time, making automatic adjustments to maintain optimal tension and alignment. Such technologies not only improve the efficiency of the conveyor system but also reduce the need for manual interventions, thereby lowering maintenance costs and minimizing downtime.
The Role of Conveyor Head and Tail in System Efficiency
The efficiency of a conveyor system is directly linked to the performance of the conveyor head and tail pulleys. These components must be designed and maintained to handle the specific requirements of the application. For instance, in high-capacity systems, the head pulley must be capable of delivering sufficient power to move large volumes of material without slipping or overheating. Similarly, the tail pulley must be robust enough to support the tension required for such operations.
Material Handling: Different materials have varying impacts on conveyor head and tail components. Abrasive materials, for example, can cause significant wear on the pulleys and belt, necessitating the use of high-durability materials and coatings. Smooth, low-friction materials, on the other hand, require less tension and may benefit from different pulley designs to maximize efficiency.
Environmental Conditions: The operating environment also affects the performance of the conveyor head and tail. In dusty or wet conditions, the pulleys and belt may require additional protection or specialized designs to prevent clogging, slippage, and corrosion. Regular maintenance and the use of appropriate materials can mitigate these challenges and extend the lifespan of the conveyor system.
Load Distribution: Effective load distribution is another critical factor in maintaining system efficiency. The conveyor head and tail pulleys must work together to distribute the load evenly across the belt. Uneven load distribution can cause sections of the belt to wear more quickly, leading to premature failure and increased maintenance costs.
What is Conveyor Head and Tail
In the world of conveyor systems, the conveyor head and tail are two critical components that ensure the smooth and efficient operation of material handling processes. Understanding the significance and functionality of these elements is essential for optimizing conveyor performance and reliability.
Conveyor Tail End
The tail end of a conveyor system is where the material loading process begins. It plays a pivotal role in determining the overall efficiency and effectiveness of the conveyor system. A well-designed conveyor tail end ensures that materials are loaded smoothly and evenly onto the conveyor belt, preventing spillage, reducing wear and tear, and maintaining a consistent flow of materials.
Importance of Tail End in Material Loading
The tail end of a conveyor is the starting point for material transport. It is responsible for receiving bulk materials from hoppers, feeders, or other loading devices and ensuring they are deposited onto the conveyor belt in a controlled manner. The efficiency of this process is crucial for several reasons:
- Preventing Spillage: Proper loading at the tail end minimizes the risk of material spillage, which can lead to waste, safety hazards, and additional cleanup costs. Ensuring materials are loaded centrally and at the correct speed reduces the chances of spillage and ensures a cleaner and safer working environment.
- Reducing Belt Wear: Uneven loading can cause excessive wear on the conveyor belt, leading to premature failure and increased maintenance costs. By ensuring that materials are loaded evenly and smoothly, the tail end helps to extend the lifespan of the belt and other conveyor components.
- Maintaining Flow Consistency: Consistent material flow is essential for optimizing the efficiency of the conveyor system. The tail end’s design and functionality ensure that materials are fed onto the conveyor belt at a steady rate, preventing bottlenecks and maintaining a continuous flow of materials through the system.
- Improving Safety: A well-designed conveyor tail end reduces the risk of accidents and injuries by minimizing spillage and ensuring that materials are loaded safely and efficiently. This is particularly important in mining and other heavy industries where the handling of bulk materials poses significant safety risks.
Features of a Well-Designed Conveyor Tail End
A well-designed conveyor tail end incorporates several key features that enhance its functionality and efficiency. These features ensure that materials are loaded smoothly, evenly, and safely onto the conveyor belt.
- Loading Chutes and Hoppers: Loading chutes and hoppers are essential components of the tail end, guiding materials onto the conveyor belt. They are designed to ensure that materials are deposited centrally and at the correct speed, minimizing spillage and reducing belt wear. High-quality chutes and hoppers are made from durable materials that can withstand the abrasive nature of bulk materials.
- Adjustable Skirts and Seals: Skirts and seals are used to contain materials and prevent spillage at the loading point. Adjustable skirts and seals ensure a tight seal between the conveyor belt and the loading chute, accommodating different material sizes and flow rates. This flexibility is crucial for maintaining an efficient loading process and minimizing material loss.
- Impact Beds and Rollers: Impact beds and rollers are installed at the tail end to absorb the impact of falling materials and protect the conveyor belt from damage. These components are designed to distribute the load evenly and reduce the stress on the belt, extending its lifespan and reducing maintenance costs. High-quality impact beds and rollers are made from robust materials that can withstand heavy impacts and abrasive conditions.
- Belt Cleaners: Belt cleaners are essential for maintaining a clean and efficient conveyor system. They are installed at the tail end to remove any residual material from the belt, preventing buildup and reducing the risk of spillage. Effective belt cleaners ensure that the conveyor operates smoothly and efficiently, minimizing downtime and maintenance requirements.
- Tail Pulley: The tail pulley is a critical component of the tail end, providing the necessary tension to the conveyor belt and ensuring its smooth operation. The design and construction of the tail pulley are crucial for maintaining the alignment and tension of the belt, preventing slippage and ensuring a consistent material flow. High-quality tail pulleys are designed to withstand the harsh conditions of industrial environments, providing reliable performance and longevity.
- Dust Suppression Systems: In industries where dust generation is a concern, dust suppression systems are essential for maintaining a safe and clean working environment. These systems are installed at the tail end to capture and control dust, preventing it from spreading and reducing the risk of respiratory issues for workers. Effective dust suppression systems improve air quality and enhance the overall safety of the conveyor system.
Conveyor Head End
While the tail end focuses on the efficient loading of materials, the head end of the conveyor system is responsible for the discharge of materials. The head end ensures that materials are transferred smoothly from the conveyor belt to the next stage of the process, whether it be another conveyor, a storage bin, or a processing unit. The design and functionality of the head end are critical for maintaining the efficiency and reliability of the conveyor system.
The head pulley, drive system, and discharge chute are key components of the head end, each playing a crucial role in the efficient transfer of materials. The head pulley provides the necessary drive force to move the conveyor belt, while the discharge chute ensures that materials are deposited accurately and efficiently.
How about Conveyor Head and Tail Pulley
The efficiency and functionality of conveyor systems heavily rely on the key components, particularly the conveyor head and tail pulleys. These elements are crucial in driving and guiding the conveyor belt, ensuring smooth and efficient operation. This section will delve into the mechanism of the head pulley in driving the conveyor belt and the advantages of using a head pulley in conveyor systems.
Mechanism of Head Pulley in Driving the Conveyor Belt
The head pulley is a critical component located at the discharge end of the conveyor system. Its primary function is to drive the conveyor belt, propelling materials towards the intended destination. The head pulley is typically powered by an electric motor, which provides the necessary torque to rotate the pulley and, consequently, move the belt.
The interaction between the head pulley and the conveyor belt is a complex process involving friction, tension, and alignment. When the electric motor turns the head pulley, friction between the pulley surface and the conveyor belt causes the belt to move. This movement is facilitated by the tension in the belt, which is maintained by the tail pulley at the opposite end of the conveyor. The tail pulley helps to keep the belt taut, ensuring it remains in contact with the head pulley and moves consistently.
The surface of the head pulley is often coated with materials that enhance friction, such as rubber or ceramic. This coating increases the grip between the pulley and the belt, reducing the likelihood of slippage and ensuring efficient power transfer. Additionally, the head pulley is designed to accommodate the belt’s load, which can vary significantly depending on the materials being transported. For instance, in mining applications, the head pulley must be robust enough to handle the weight and abrasiveness of the extracted materials.
Advantages of Using a Head Pulley in Conveyor Systems
Using a head pulley in conveyor systems offers several advantages, contributing to the overall efficiency and reliability of material handling operations. Here are some of the key benefits:
Efficient Power Transmission: The primary advantage of a head pulley is its ability to transmit power efficiently from the motor to the conveyor belt. The direct contact and enhanced friction between the pulley and the belt ensure that the energy from the motor is effectively used to move the belt and the transported materials. This efficiency reduces energy consumption and operational costs.
Improved Belt Traction: The design and surface coating of the head pulley improve the traction between the pulley and the belt. This enhanced traction minimizes the risk of slippage, which can cause disruptions in the material handling process. By maintaining consistent belt movement, the head pulley helps to ensure a steady flow of materials, enhancing productivity.
Durability and Reliability: Head pulleys are built to withstand the demanding conditions of various industrial environments. Whether in mining, manufacturing, or logistics, these pulleys are designed to handle heavy loads, abrasive materials, and continuous operation. Their robust construction and reliable performance reduce the need for frequent maintenance and replacements, contributing to lower operational costs and increased uptime.
Ease of Maintenance: While head pulleys are durable, they are also designed for ease of maintenance. Regular inspections and maintenance are essential to ensure the longevity and optimal performance of the conveyor system. Head pulleys can be easily accessed and serviced, allowing for quick identification and resolution of potential issues. This ease of maintenance helps to minimize downtime and keep the conveyor system running smoothly.
Versatility: Head pulleys are versatile components that can be used in various types of conveyor systems, including belt conveyors, roller conveyors, and chain conveyors. Their adaptability makes them suitable for a wide range of applications, from transporting raw materials in mining operations to moving packaged goods in a warehouse. This versatility makes head pulleys an integral part of many conveyor systems.
Enhanced Safety: The use of a head pulley in conveyor systems can also enhance safety. By ensuring consistent belt movement and reducing the risk of slippage, head pulleys help to create a safer working environment. Additionally, modern head pulleys are often equipped with safety features such as guards and emergency stop mechanisms, further enhancing the safety of the conveyor system.
The Keys of Conveyor Head and Tail
In any conveyor system, the conveyor head and tail are crucial components that determine the efficiency and reliability of material handling processes. The proper functioning of both ends is essential to ensure smooth and continuous operation.
Tail Pulley Function
The tail pulley is a vital part of the conveyor tail end, serving several essential functions that contribute to the overall performance of the conveyor system.
How Tail Pulley Ensures Proper Belt Alignment
The tail pulley plays a critical role in maintaining the alignment of the conveyor belt. Proper belt alignment is crucial for preventing operational issues such as belt slippage, uneven wear, and material spillage. The tail pulley helps keep the belt centered on the conveyor frame by providing a stable, aligned surface for the belt to track on.
The alignment process involves the use of adjustable bearings or bushings that allow for precise positioning of the tail pulley. By adjusting these components, maintenance personnel can ensure that the pulley is perfectly aligned with the conveyor frame, which in turn keeps the belt running straight. Regular inspections and adjustments of the tail pulley are necessary to maintain proper alignment, especially in systems that handle heavy loads or operate in harsh conditions.
Moreover, the tail pulley’s design often includes crowned surfaces or specially designed lagging that helps guide the belt and maintain its alignment. These features ensure that the belt remains centered even under varying load conditions, reducing the risk of operational disruptions and extending the lifespan of the conveyor belt.
The Role of Tail Pulley in Tensioning the Conveyor Belt
In addition to ensuring proper alignment, the tail pulley is also instrumental in maintaining the correct tension in the conveyor belt. Proper tension is essential for the efficient operation of the conveyor system, as it prevents the belt from slipping on the drive pulley and ensures that the belt can carry the load effectively.
The tail pulley works in conjunction with the take-up unit to maintain the required tension. The take-up unit, which can be either manual or automatic, applies a consistent force to the tail pulley, ensuring that the belt remains taut. This setup compensates for any elongation or stretching that occurs over time, keeping the belt at the optimal tension.
Maintaining the correct tension is crucial for several reasons. Firstly, it prevents belt slippage, which can lead to material spillage, reduced efficiency, and increased wear on the belt and pulleys. Secondly, proper tension helps distribute the load evenly across the belt, reducing localized stress and wear. This not only extends the life of the belt but also minimizes the risk of breakdowns and costly repairs.
Additionally, the tail pulley and take-up unit help absorb any shock loads or impacts that occur during operation. This shock absorption capability is particularly important in heavy-duty applications where the conveyor system may experience sudden changes in load or impacts from large, heavy materials.
The Types of Conveyor Head and Tail Functions
The efficient operation of conveyor systems is heavily dependent on the roles played by the head end and tail end of conveyor pulleys. These components are integral to the smooth functioning of the conveyor belt, ensuring that materials are transported effectively and reliably. This section will explore the primary functions of the head pulley and the essential functions of the tail pulley within a conveyor system.
Primary Functions of Head Pulley in a Conveyor System
The head pulley is a critical component located at the discharge end of the conveyor system. Its primary function is to drive the conveyor belt, enabling the continuous movement of materials from one point to another. The head pulley is typically powered by an electric motor, which imparts the necessary torque to rotate the pulley and, consequently, move the belt.
Driving the Conveyor Belt: The main role of the head pulley is to drive the conveyor belt. When the motor turns the head pulley, friction between the pulley surface and the belt causes the belt to move. This friction is essential for the efficient transfer of power from the motor to the belt, ensuring that the belt moves smoothly and consistently. The surface of the head pulley is often covered with materials that enhance friction, such as rubber or ceramic, to prevent slippage and improve efficiency.
Material Discharge: Another crucial function of the head pulley is to facilitate the discharge of materials from the conveyor system. As the belt reaches the head pulley, it changes direction, allowing the materials to be released and collected for further processing or transport. The design and positioning of the head pulley are critical to ensure that materials are discharged accurately and efficiently, minimizing spillage and maximizing throughput.
Tension and Alignment: The head pulley also plays a significant role in maintaining the tension and alignment of the conveyor belt. Proper tension is essential to prevent slippage and ensure that the belt remains in contact with the pulleys. The head pulley helps to distribute tension evenly across the belt, while alignment ensures that the belt moves along the intended path without drifting to the sides. Misalignment can cause uneven wear and reduce the lifespan of the belt and pulleys, making regular maintenance and adjustments necessary.
Essential Functions of Tail Pulley in a Conveyor System
The tail pulley, located at the feed end of the conveyor system, complements the functions of the head pulley by maintaining the necessary tension and alignment for the smooth operation of the belt. While it is not driven by a motor, the tail pulley is equally important in ensuring the efficient performance of the conveyor system.
Guiding the Conveyor Belt: One of the primary functions of the tail pulley is to guide the conveyor belt. By maintaining the belt’s tension and alignment, the tail pulley ensures that the belt follows a straight path and remains in contact with the head pulley. This guidance is crucial for the smooth operation of the conveyor system, preventing issues such as belt drift and uneven wear.
Adjusting Belt Tension: The tail pulley is typically equipped with adjustable mechanisms that allow operators to fine-tune the tension of the conveyor belt. Proper tension is vital to ensure that the belt remains taut and does not sag or slip. Too much tension can cause excessive wear and reduce the belt’s lifespan, while too little tension can lead to slippage and inefficiency. The tail pulley’s adjustable features enable precise control over belt tension, optimizing performance and minimizing maintenance requirements.
Supporting Load Distribution: The tail pulley also plays a role in supporting the distribution of the load on the conveyor belt. By maintaining proper tension and alignment, the tail pulley helps to ensure that the load is evenly distributed across the belt. This even distribution is essential for preventing excessive wear on specific sections of the belt and pulleys, reducing the risk of damage and extending the lifespan of the conveyor system.
Facilitating Maintenance: Regular maintenance is crucial for the optimal performance and longevity of conveyor systems. The tail pulley, with its adjustable features and accessible design, facilitates easy maintenance and adjustments. Operators can quickly and accurately adjust the tension and alignment of the belt, ensuring that the system operates efficiently and reducing the risk of unexpected downtime.
Supporting Conveyor Length Adjustments: In some conveyor systems, the tail pulley can also be used to adjust the overall length of the conveyor belt. This is particularly useful in applications where the length of the conveyor system needs to be modified to accommodate changes in the layout or operational requirements. By adjusting the position of the tail pulley, operators can increase or decrease the length of the conveyor belt, providing flexibility and adaptability to the system.
The Choose of Conveyor Head and Tail
About the components of a conveyor system is essential for optimizing its performance and reliability. Among these components, the conveyor head and tail pulleys play critical roles. This section will delve into the definition and role of these pulleys, and highlight the key differences between them.
Conveyor Head and Tail Pulley
Definition and Role of Conveyor Head and Tail Pulleys
The head and tail pulleys are integral parts of a conveyor system, ensuring the continuous and efficient movement of materials.
Conveyor Head Pulley:
The head pulley, also known as the drive pulley, is typically located at the discharge end of the conveyor. Its primary function is to drive the belt, propelling it forward and enabling the transportation of materials along the conveyor. The head pulley is connected to a motor, which provides the necessary rotational force to move the belt. This pulley is often larger in diameter compared to the tail pulley to accommodate the drive system and ensure adequate grip on the belt.
The head pulley is essential for the overall operation of the conveyor system. It determines the speed and direction of the belt, directly influencing the efficiency of material handling. Additionally, the head pulley can be equipped with lagging—a covering that enhances friction between the belt and the pulley. This lagging is crucial for preventing slippage, especially in conditions where the belt may be wet or coated with material residues.
Conveyor Tail Pulley:
The tail pulley is located at the loading end of the conveyor. Unlike the head pulley, the tail pulley is not driven but serves as a return point for the belt. Its main functions include maintaining proper tension in the belt and ensuring it is aligned correctly as it travels back from the head pulley to the tail end.
The tail pulley plays a crucial role in the smooth operation of the conveyor system. By providing a stable and aligned return path for the belt, it helps prevent misalignment issues that could lead to belt damage or spillage of materials. The tail pulley is often equipped with adjustable bearings, allowing for precise alignment and tension adjustments. These adjustments are vital for maintaining optimal belt tension, which is essential for preventing slippage and ensuring efficient material transport.
Key Differences Between Head and Tail Pulleys
While both the head and tail pulleys are essential for the operation of a conveyor system, they have distinct roles and characteristics. Understanding these differences is crucial for proper maintenance and optimization of the conveyor system.
1. Location and Function:
- The head pulley is located at the discharge end of the conveyor and is responsible for driving the belt. It is connected to a motor and determines the speed and direction of the belt.
- The tail pulley is located at the loading end of the conveyor and serves as a return point for the belt. It helps maintain proper tension and alignment of the belt.
2. Drive Mechanism:
- The head pulley is a drive pulley, meaning it is powered by a motor to move the belt. It is responsible for providing the necessary force to transport materials along the conveyor.
- The tail pulley is an idler pulley, meaning it is not driven but freely rotates to guide the belt back to the loading end.
3. Size and Design:
- Head pulleys are typically larger in diameter than tail pulleys to accommodate the drive system and ensure adequate grip on the belt. They may also be equipped with lagging to enhance friction.
- Tail pulleys are generally smaller in diameter and are designed for free rotation. They are often equipped with adjustable bearings for precise alignment and tension adjustments.
4. Role in Belt Tension and Alignment:
- The head pulley’s role in belt tension is indirect, primarily influencing it through the drive mechanism. Proper tension is crucial for preventing belt slippage and ensuring efficient material transport.
- The tail pulley plays a direct role in maintaining belt tension and alignment. It ensures the belt is aligned correctly as it returns from the head pulley and allows for adjustments to maintain optimal tension.
5. Maintenance and Adjustments:
- Maintenance of the head pulley primarily involves ensuring the drive system is functioning correctly and that the lagging is in good condition. Regular inspections are necessary to prevent slippage and ensure efficient material transport.
- Maintenance of the tail pulley focuses on alignment and tension adjustments. Regular inspections and adjustments are necessary to prevent misalignment issues and ensure the belt operates smoothly.
6. Impact on Conveyor Performance:
- The head pulley has a significant impact on the overall performance of the conveyor system. It determines the speed and efficiency of material transport, making it a critical component for optimizing productivity.
- The tail pulley, while less directly involved in material transport, plays a crucial role in ensuring the smooth operation of the conveyor system. Proper alignment and tension maintained by the tail pulley are essential for preventing operational issues and extending the lifespan of the belt.
The Importance of Maintenance and Optimization
Both the head and tail pulleys are essential for the efficient operation of a conveyor system. Proper maintenance and optimization of these components are crucial for ensuring the system operates smoothly and efficiently.
Maintenance of Head Pulleys:
- Regular inspections should be conducted to ensure the drive system is functioning correctly. Any signs of wear or damage to the motor, bearings, or lagging should be addressed promptly.
- The head pulley should be checked for proper alignment and tension. Misalignment or improper tension can lead to belt slippage, reducing the efficiency of material transport and increasing wear on the belt and pulley.
Maintenance of Tail Pulleys:
- Regular inspections should be conducted to ensure the tail pulley is aligned correctly and that the bearings are in good condition. Misalignment can lead to belt damage and material spillage.
- The tension of the belt should be checked regularly and adjusted as necessary. Proper tension is crucial for preventing slippage and ensuring the belt operates smoothly.
Optimization of Conveyor Systems:
- Optimization of the conveyor system involves ensuring that both the head and tail pulleys are functioning correctly and that the belt is properly tensioned and aligned. This can be achieved through regular inspections, maintenance, and adjustments.
- Upgrading components such as motors, bearings, and lagging can also improve the efficiency and reliability of the conveyor system. Investing in high-quality components can reduce maintenance costs and increase the lifespan of the system.
FAQS about Conveyor Head And Tail
The head end and tail end of a conveyor refer to the two primary ends of the conveyor system. The head end is the part of the conveyor where the material is discharged. This end is typically equipped with a drive motor that powers the conveyor belt. The head end is crucial because it controls the movement of the belt and is usually where the material is deposited onto another conveyor or into a chute. The tail end, on the other hand, is the starting point of the conveyor system where the material is loaded onto the belt. It is generally equipped with a pulley that helps in guiding the belt into its proper alignment and tension. Understanding these two ends is essential for efficient operation and maintenance of conveyor systems.
The tail of a conveyor, also known as the tail end, is the part of the conveyor system where the material is loaded onto the belt. This end is critical as it begins the transportation process of materials along the conveyor. The tail typically features a tail pulley, which helps in guiding and maintaining the alignment of the conveyor belt. Proper alignment and tension at the tail end are vital to prevent belt slippage and ensure smooth operation. The tail of a conveyor often includes features such as loading hoppers or chutes that facilitate the easy loading of materials. Regular maintenance and inspection of the tail end can help prevent operational issues and extend the lifespan of the conveyor system.
The difference between a head drive and a tail drive on a conveyor lies in the location and function of the drive mechanism that powers the conveyor belt. A head drive is located at the discharge end (head end) of the conveyor. It pulls the belt and moves it forward, making it the most common drive arrangement in conveyor systems. The head drive is typically used for applications that require precise control over the belt speed and direction. On the other hand, a tail drive is situated at the loading end (tail end) of the conveyor. It pushes the belt rather than pulling it. Tail drives are less common and are usually used in situations where the conveyor layout or material flow direction necessitates such a configuration. Both drive types are essential for different operational needs and can be selected based on the specific requirements of the conveyor system.
Head rollers and tail rollers are essential components of a conveyor system, serving different purposes. The head roller, located at the head end of the conveyor, is the roller over which the belt passes and where the drive mechanism is typically attached. This roller is responsible for the forward movement of the conveyor belt and is crucial for the discharge of materials. The tail roller, positioned at the tail end of the conveyor, serves to guide and align the conveyor belt as it returns to the loading point. It ensures that the belt remains in the correct position and tension, preventing misalignment and slippage. Both rollers are integral to the smooth operation of a conveyor system, ensuring that the belt moves efficiently and materials are transported without interruption. Regular maintenance of both the head and tail rollers is essential to prevent operational issues and prolong the life of the conveyor system.
Last Updated on June 12, 2024 by Jordan Smith
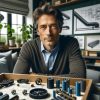
Jordan Smith, a seasoned professional with over 20 years of experience in the conveyor system industry. Jordan’s expertise lies in providing comprehensive solutions for conveyor rollers, belts, and accessories, catering to a wide range of industrial needs. From initial design and configuration to installation and meticulous troubleshooting, Jordan is adept at handling all aspects of conveyor system management. Whether you’re looking to upgrade your production line with efficient conveyor belts, require custom conveyor rollers for specific operations, or need expert advice on selecting the right conveyor accessories for your facility, Jordan is your reliable consultant. For any inquiries or assistance with conveyor system optimization, Jordan is available to share his wealth of knowledge and experience. Feel free to reach out at any time for professional guidance on all matters related to conveyor rollers, belts, and accessories.