Conveyor Belt Cleaners:Belt Scraper
A belt scraper is a device used to clean material from conveyor belts, ensuring efficient and safe operation in various industries like mining, manufacturing, and food processing. Belt scrapers play a vital role in preventing material buildup, which can cause belt damage and operational inefficiencies.Belt scrapers are essential for maintaining conveyor efficiency and safety. By removing residual material, they prevent belt misalignment and reduce the risk of accidents. Additionally, belt scrapers help lower maintenance costs and extend the lifespan of conveyor belts, making them a critical component in industrial operations.
Types of Conveyor Belt Scrapers
Conveyor belt scrapers are essential components in maintaining the cleanliness and efficiency of conveyor systems across various industries. They come in different types, each designed to perform specific functions and to handle distinct operational challenges. Understanding these types and their applications can help in selecting the right scraper for your system’s needs.
Primary Conveyor Belt Scrapers
Primary conveyor belt scrapers are positioned at the discharge point of the conveyor, directly after the head pulley. They serve as the first line of defense against bulk material carryback, which refers to the residue that sticks to the belt after it discharges its load.
Role and Placement
Primary conveyor belt scrapers are crucial for aggressively removing large chunks of material right as they leave the head pulley. By doing so, they prevent excessive build-up on the belt, which can lead to several operational issues including misalignment and increased wear on the belt and other conveyor components. This type of scraper is typically mounted perpendicular to the belt surface, ensuring maximum contact and scraping efficiency.
Design and Functionality
Primary scrapers often feature heavy-duty blades made from durable materials such as polyurethane or tungsten carbide. These materials are chosen for their resilience and ability to withstand the harsh conditions of mining, quarrying, and other demanding environments. The robust construction of primary conveyor belt scrapers allows them to effectively handle high volumes of material and the rigorous demands of heavy-duty applications. For example, a heavy-duty belt scraper might be used in a mining operation to scrape off abrasive ores and rocks from the conveyor belt.
Primary conveyor belt scrapers are essential for ensuring that large debris is removed immediately, preventing the potential for carryback and reducing maintenance needs. This makes them an indispensable part of any high-capacity conveyor system where bulk material handling is critical.

Secondary Conveyor Belt Scrapers
Secondary conveyor belt scrapers are installed further along the conveyor line, usually after the material has passed the primary scrapers. Their purpose is to remove any residual material that the primary scrapers might have missed.
Positioning and Purpose
These scrapers are typically positioned just before the return rollers or idlers, catching finer particles and smaller residues that cling to the belt. By ensuring a thorough cleaning of the belt surface, secondary scrapers help in maintaining optimal belt hygiene and preventing any potential issues downstream.
Design and Integration
Secondary scrapers generally have lighter, less aggressive blades compared to primary scrapers. They are designed to complement the action of primary scrapers by targeting leftover fines and sticky materials. Many secondary scrapers, like the Flexco Belt scraper, are engineered for easy integration into existing conveyor systems, providing an additional layer of cleaning without significant modifications to the setup. The flexibility and adjustability of these scrapers make them suitable for a variety of operational conditions and belt speeds.
Secondary belt scrapers cleaner play a vital role in the final cleaning process, ensuring that all traces of material are removed. This minimizes the risk of belt wear and improves overall system efficiency, making them a valuable addition to any conveyor setup.

Specialized Scrapers
Beyond the primary and secondary categories, there are specialized scrapers designed to meet unique operational requirements. These scrapers are tailored for specific conditions and challenges, providing targeted solutions where standard scrapers might fall short.
Tertiary and High-Temperature Scrapers
Tertiary scrapers, for instance, are used in systems that require an additional cleaning stage to ensure maximum belt cleanliness. They are particularly useful in applications where even the smallest amounts of carryback can cause significant problems.
High-temperature scrapers are designed to operate in environments where the belt and materials are subjected to extreme heat. These scrapers are made from materials that can withstand high temperatures without degrading, ensuring continuous and effective cleaning under challenging conditions.
Abrasive and Chemical-Resistant Scrapers
In environments where the conveyor belt is exposed to abrasive materials or harsh chemicals, specialized scrapers with enhanced durability and resistance are necessary. These scrapers are constructed from materials that can endure the wear and tear of abrasive substances or the corrosive effects of chemicals, extending the lifespan of both the scraper and the conveyor belt.
The variety of specialized scraper belt options available allows for tailored solutions that meet the exact demands of different operational environments. From handling extreme temperatures to managing abrasive materials, specialized scrapers ensure that every aspect of belt cleaning is covered.
Selecting the right type of conveyor scraper belt is crucial for maintaining the efficiency and longevity of conveyor systems. Whether it’s the robust primary scrapers tackling bulk material or the finer secondary scrapers handling residual particles, each type plays a vital role in ensuring clean and safe conveyor operations. Additionally, specialized scrapers offer solutions for unique challenges, further enhancing the versatility and effectiveness of belt cleaning systems.
Belt Scraper Product Specifications
Blade Material
- Polyurethane: Durable, flexible, and resistant to abrasion.
- Tungsten Carbide: Highly resistant to wear and impact, suitable for heavy-duty applications.
- Stainless Steel: Corrosion-resistant and ideal for food processing and chemical applications.
Blade Dimensions
- Width: Typically ranges from 100mm to 300mm, depending on the conveyor belt width.
- Thickness: Varies between 10mm and 25mm to suit different operational demands.
Mounting System
- Adjustable Tensioners: Allows for precise pressure adjustments to ensure effective scraping.
- Spring-Loaded: Provides consistent blade pressure against the belt, accommodating belt movement and wear.
Operating Temperature Range
- Standard: -20°C to +80°C, suitable for most industrial applications.
- High Temperature: Up to +200°C for use in high-heat environments such as cement plants and foundries.
Conveyor Belt Width Compatibility
- Available for belt widths from 300mm to 3000mm.
Blade Hardness
- Polyurethane: Shore A hardness between 85 and 95.
- Tungsten Carbide: Hardness typically above 1500 HV (Vickers hardness).
Installation
- Easy to Install: Can be mounted on existing conveyor systems with minimal modifications.
- Modular Design: Allows for quick replacement of worn parts without dismantling the entire scraper assembly.
Additional Features
- Self-Cleaning: Some models feature a self-cleaning mechanism to prevent clogging and buildup.
- Multi-Blade Options: For enhanced cleaning efficiency, particularly in handling sticky or wet materials.
These specifications ensure that belt scrapers are designed to meet various industrial requirements, providing efficient and reliable performance for maintaining conveyor belt cleanliness and operational efficiency.

Features of Conveyor Belt Scraper Blades
Conveyor belt scraper blades are critical components in the effective cleaning and maintenance of conveyor systems. The right scraper blade can significantly enhance the efficiency and lifespan of the conveyor belt. This section delves into the essential features of conveyor belt scraper blades, including their material composition, durability, design, and efficiency.
Material and Durability
The material composition of conveyor belt scraper blades plays a pivotal role in their performance and longevity. The choice of material directly impacts how well the blades can handle different types of materials and environmental conditions. Here are some common materials used for scraper blades and their respective advantages:
Polyurethane Blades
Polyurethane is a versatile and widely used material for conveyor belt scraper blades. Known for its excellent abrasion resistance and flexibility, polyurethane blades are ideal for applications involving softer or moderately abrasive materials. They provide a good balance between durability and gentleness on the belt, making them suitable for industries like food processing and packaging where both efficiency and product safety are paramount.
Carbide Blades
Tungsten carbide blades are renowned for their exceptional hardness and wear resistance. These blades are particularly suited for heavy-duty applications in mining and quarrying, where they must scrape off tough, abrasive materials like ores and stones. The high durability of carbide blades translates to longer service life and reduced frequency of replacements, making them a cost-effective option for handling rigorous and high-impact cleaning tasks.
Stainless Steel Blades
Stainless steel blades offer superior strength and corrosion resistance, making them suitable for environments with harsh chemicals or wet conditions. These blades are often used in industrial settings where the conveyor system may be exposed to corrosive agents or where hygiene is a critical factor, such as in pharmaceutical or chemical processing plants. The robust nature of stainless steel blades ensures they can withstand both mechanical wear and corrosive environments effectively.
The material of conveyor belt scraper blades is crucial in determining their durability and effectiveness. Whether using polyurethane for softer applications, carbide for abrasive conditions, or stainless steel for corrosive environments, selecting the right blade material ensures optimal performance and longevity in diverse operational settings.
Design and Efficiency
The design of conveyor scraper belt blades significantly influences their cleaning efficiency and overall effectiveness. Various design elements can enhance the performance of scraper blades, ensuring they meet the specific needs of different conveyor systems.
Blade Shape and Angle
The shape and angle of the scraper blade are vital in maximizing contact with the conveyor belt surface and effectively removing material. Blades may be straight, curved, or segmented, each designed to tackle specific cleaning challenges. For example, curved blades can better conform to the belt’s surface, providing consistent pressure and more thorough cleaning, while segmented blades allow for flexibility and better handling of uneven surfaces.
Adjustable and Self-Adjusting Blades
Adjustable scraper blades allow for manual tuning of the blade’s position and pressure against the belt. This adjustability is crucial for maintaining optimal cleaning efficiency as the blade wears down or as the belt’s conditions change. In contrast, self-adjusting blades automatically adapt to the wear and tear of both the blade and the belt, ensuring consistent cleaning performance without frequent manual intervention. These self-adjusting systems are particularly beneficial in minimizing maintenance and downtime, enhancing the overall productivity of the conveyor system.
The design features of belt scrapers, including the shape, angle, and adjustability of the blades, are critical in achieving efficient and thorough cleaning. Adjustable and self-adjusting blades, in particular, offer significant advantages in maintaining optimal performance and reducing the need for constant manual adjustments.
Performance Enhancing Features
Temperature and Chemical Resistance
Some conveyor belt scraper blades are specifically designed to withstand extreme temperatures and exposure to chemicals. High-temperature blades are essential in industries where the conveyor belt carries hot materials, such as in steel production or foundries. Similarly, chemical-resistant blades are crucial in environments where the belt and blades are exposed to harsh chemicals, ensuring the scrapers maintain their structural integrity and cleaning efficiency.
Modular and Replaceable Components
Many modern scraper blades come with modular and replaceable components, allowing for easy and cost-effective maintenance. Modular designs enable users to replace only the worn parts rather than the entire scraper assembly, saving both time and money. This feature is particularly advantageous in high-wear applications where parts need frequent replacement.
Performance-enhancing features such as temperature and chemical resistance, along with modular and replaceable components, further optimize the functionality and longevity of belt scrapers. These innovations make scraper blades more adaptable and efficient in a wide range of industrial applications.
The features of conveyor belt scraper blades, from their material composition and durability to their design and performance-enhancing characteristics, are integral to their effectiveness in maintaining clean and efficient conveyor systems. Understanding these features helps in selecting the appropriate scraper blades that align with the specific operational needs and conditions of different industries. With the right combination of material, design, and performance features, conveyor belt scraper blades can significantly enhance the productivity and safety of conveyor operations.
Benefits of Using Belt Scrapers
Utilizing a belt scraper in conveyor systems brings a multitude of benefits, ranging from enhanced performance and cost efficiency to improved safety and environmental impact. Belt scrapers are integral components in various industries, including mining, manufacturing, and food processing, where maintaining clean and efficient conveyor systems is crucial. This section explores the significant advantages of incorporating belt scrapers into your conveyor operations.
Improved Conveyor System Performance
One of the primary benefits of using a belt scraper is the substantial improvement in conveyor system performance. Belt scrapers play a vital role in ensuring that conveyor belts remain clean and free from debris, which directly impacts the efficiency and effectiveness of the conveyor system.
Enhanced System Efficiency
Belt scrapers maintain the cleanliness of the conveyor belt by continuously removing bulk material carryback. This cleaning process prevents the buildup of materials on the belt surface, which can cause slippage, misalignment, and increased friction. By keeping the belt clean, scrapers ensure that the conveyor operates at optimal speed and efficiency, facilitating a smooth and uninterrupted flow of materials.
Reduction in Operational Downtime
Operational downtime is a significant concern for industries reliant on conveyor systems. Frequent stoppages for cleaning and maintenance can severely disrupt production schedules and reduce overall productivity. By employing belt scrapers, businesses can minimize these interruptions. Belt scrapers reduce the need for manual cleaning and frequent belt adjustments, allowing the conveyor to run continuously and reliably. This reduction in downtime translates to higher throughput and increased operational efficiency.
Minimized Belt Wear and Tear
Conveyor belts are subject to significant wear and tear due to constant contact with transported materials. The accumulation of abrasive materials on the belt surface can accelerate this wear, leading to premature belt damage and failure. Heavy duty belt scrapers are designed to effectively remove these abrasive materials, thereby protecting the belt and extending its service life. By reducing wear and tear, belt scrapers help maintain the integrity of the conveyor system and prevent costly unplanned replacements.
Cost Savings
Investing in belt scrapers can lead to substantial cost savings for businesses. These savings are realized through reduced cleanup expenses, lower maintenance costs, and extended lifespan of conveyor components.
Reduced Cleanup Costs
One of the most immediate cost benefits of using a belt scraper is the reduction in cleanup expenses. Without scrapers, material carryback can accumulate under and around the conveyor system, requiring frequent and labor-intensive cleanup efforts. By effectively removing carryback, belt scrapers minimize the amount of spilled material, reducing the need for extensive cleanup operations. This reduction in cleanup not only lowers labor costs but also minimizes the use of cleaning supplies and equipment.
Lower Maintenance Costs
Conveyor systems require regular maintenance to ensure they operate efficiently and safely. However, the buildup of materials on the belt can increase the frequency and complexity of maintenance tasks. By keeping the belt clean, scrapers help reduce the wear on conveyor components such as rollers, idlers, and pulleys. This reduction in component wear translates to fewer maintenance interventions and lower overall maintenance costs. Additionally, the extended lifespan of these components reduces the need for frequent replacements, further contributing to cost savings.
Extended Conveyor Lifespan
Belt scrapers contribute to the longevity of the entire conveyor system. By preventing material buildup and reducing wear on the belt and other components, scrapers help extend the operational life of the conveyor. This extension means that businesses can delay costly capital expenditures on new conveyor systems, instead maximizing the return on their existing investments.
Safety and Environmental Impact
Belt scrapers also play a crucial role in enhancing workplace safety and minimizing environmental impact. These benefits are particularly important in industries where dust, spills, and other hazards pose significant risks.
Minimized Dust and Spills
The accumulation of materials on conveyor belts can lead to dust and spillage, both of which pose safety hazards. Dust can create respiratory problems for workers and increase the risk of explosions in certain environments, while spills can create slippery surfaces and trip hazards. Scraper belts efficiently remove material from the belt, reducing the amount of dust and preventing spills. This reduction in dust and spills helps maintain a safer work environment and complies with regulatory safety standards.
Improved Workplace Safety
Safety is a top priority in any industrial setting, and belt scrapers contribute significantly to maintaining a safe workplace. By preventing material buildup and reducing the potential for accidents related to spills and belt misalignment, scrapers help protect workers from injuries. Heavy duty belt scrapers, in particular, are designed to handle challenging conditions and ensure that even in demanding environments, the conveyor system operates safely and effectively.
Reduced Environmental Impact
Environmental sustainability is an increasing concern for many industries. By keeping conveyor belts clean, scrapers help minimize waste and reduce the environmental footprint of conveyor operations. Less material spillage means fewer resources are required for cleanup, and there is less risk of contaminating the surrounding environment. Efficient belt scrapers also contribute to the overall energy efficiency of the conveyor system, further supporting environmental conservation efforts.
The benefits of using a belt scraper extend beyond simple cleanliness. From enhancing conveyor system performance and achieving significant cost savings to improving workplace safety and reducing environmental impact, belt scrapers are essential tools for maintaining efficient and sustainable conveyor operations. By investing in the right belt scrapers, businesses can optimize their conveyor systems, safeguard their workers, and support their long-term operational goals.

How Do Belt Scrapers Work?
Belt scrapers, also known as belt cleaners, are devices used to remove material from conveyor belts. Here’s an overview of how they work:
Installation Position
- Primary Scraper: Positioned at the head pulley, where the belt changes direction and material is most likely to stick.
- Secondary Scraper: Placed further along the belt, usually under the belt where additional cleaning is required.
Scraping Mechanism
- Blade Contact: The scraper blade makes direct contact with the conveyor belt, positioned at an angle to effectively remove material.
- Pressure Adjustment: The tensioning system ensures that the blade maintains consistent pressure against the belt to scrape off material without damaging the belt.
Material Removal
- Carryback Removal: As the conveyor belt moves, material adhering to the belt surface (carryback) is scraped off by the blade.
- Debris Collection: The removed material is directed away from the belt and collected in a chute or bin, preventing buildup on the return side of the belt.
Types of Blades
- Polyurethane Blades: Flexible and durable, suitable for light to moderate applications.
- Tungsten Carbide Blades: Extremely hard and wear-resistant, ideal for heavy-duty and abrasive applications.
Tensioning Systems
- Spring-Loaded: Uses springs to maintain constant pressure of the blade against the belt, accommodating changes in belt thickness and wear.
- Mechanical Tensioners: Allows manual adjustment of blade pressure to ensure optimal contact with the belt.
Cleaning Efficiency
- Primary Cleaners: Remove the bulk of the material right at the head pulley.
- Secondary Cleaners: Provide additional cleaning to remove residual material missed by the primary cleaner.
Belt scrapers are essential for maintaining the efficiency and longevity of conveyor belt systems. By effectively removing material carryback, they ensure the conveyor operates smoothly, with minimal downtime and maintenance. Their design, incorporating adjustable tensioning systems and durable blades, allows them to adapt to various operational conditions and belt types.
Application of Belt Scraper
Belt scrapers are essential components in conveyor belt systems, particularly in industries where bulk material handling is prevalent. Here’s an overview of their applications:
- Mining and Quarrying: Belt scrapers remove debris, reducing wear and tear on belts and minimizing downtime.
- Agriculture: Used in grain handling systems to keep belts clean and prevent contamination.
- Food Processing: Ensures hygiene by cleaning belts of food residues, preventing cross-contamination.
- Recycling Plants: Keeps belts free of residual materials, enhancing efficiency and reducing maintenance.
- Cement and Construction: Prevents material buildup on belts, ensuring smooth and uninterrupted operation.
- Chemical Industry: Removes corrosive materials from belts, protecting the equipment and maintaining safety.
Key Benefits:
- Efficiency: Maintains optimal belt performance by removing carryback material.
- Cost-Effectiveness: Reduces maintenance costs and prolongs the lifespan of the conveyor belt.
- Safety: Minimizes the risk of material spillage and related hazards.
Belt scrapers are vital for maintaining clean and efficient conveyor belt systems across various industries, contributing to operational efficiency and safety.
Choosing the Right Belt Scraper for Your Needs
Selecting the appropriate belt scraper for your conveyor system is a crucial decision that can significantly impact the efficiency, maintenance, and longevity of your operations. With various options available, understanding the factors that influence scraper choice and ensuring compatibility with your existing system are essential steps in optimizing your conveyor’s performance. This section delves into the key considerations for selecting the right belt scraper, as well as the importance of customization and compatibility.
Considerations for Selection
When choosing a belt scraper, several factors must be taken into account to ensure optimal performance and longevity. The right selection can minimize maintenance costs, reduce material buildup, and enhance the overall efficiency of your conveyor system.
Material Type and Application
The type of material being transported plays a significant role in determining the most suitable belt scraper. Different materials have varying properties, such as abrasiveness, moisture content, and stickiness, which can affect the scraper’s performance and durability.
- Abrasive Materials: For highly abrasive materials, such as ores and minerals in mining operations, scrapers made from durable materials like tungsten carbide or hardened steel are preferred. These materials resist wear and provide a longer service life under harsh conditions.
- Moist or Sticky Materials: For materials that tend to adhere to the belt, such as wet or sticky substances found in food processing, polyurethane or rubber scrapers are ideal. These materials provide a balance between flexibility and effectiveness in removing material without damaging the belt.
- General Use: For general applications where the materials are neither too abrasive nor too sticky, a medium-grade scraper made from a combination of materials can be effective. Polyurethane is often used due to its durability and moderate cost.
Selecting the appropriate material for your scraper blade is crucial to maintaining the efficiency and longevity of your conveyor system.
Conveyor Speed and Load
The speed and load of the conveyor also impact the choice of belt scraper. High-speed conveyors, commonly found in bulk handling and mining industries, require scrapers that can withstand the increased wear and tear. Conversely, low-speed conveyors, typical in food processing or packaging lines, may benefit from more flexible scraper materials.
- High-Speed Conveyors: For belts operating at high speeds, durable and robust scrapers, such as those made from tungsten carbide or steel, are necessary to handle the increased impact and wear. These scrapers are designed to maintain consistent contact with the belt surface at higher velocities.
- Low-Speed Conveyors: For slower-moving belts, softer and more flexible scrapers, such as those made from rubber or polyurethane, can effectively clean the belt without causing excessive wear. These scrapers can adapt to the belt’s surface and maintain efficiency at lower speeds.
Properly matching the scraper to the conveyor speed and load ensures efficient cleaning and prolongs the life of both the scraper and the conveyor belt.
Environmental Conditions
The operating environment of the conveyor system is another critical factor in scraper selection. Environmental conditions, such as temperature, humidity, and exposure to chemicals, can affect the scraper’s performance and durability.
- Temperature: In high-temperature environments, such as those found in smelting or kiln operations, scrapers must be able to withstand extreme heat without degrading. Materials like high-temperature-resistant metals or ceramics are ideal for these conditions.
- Humidity and Moisture: In environments with high humidity or where the belt is exposed to water, such as in washing or cooling processes, scrapers made from corrosion-resistant materials like stainless steel or certain polymers are preferred. These materials resist rust and maintain performance in wet conditions.
- Chemical Exposure: For conveyors exposed to harsh chemicals, such as in chemical processing or waste treatment, scrapers must be made from materials that can resist corrosion and chemical degradation. Specially treated metals or chemically resistant polymers are suitable for these environments.
Assessing and addressing these environmental factors help in selecting a belt scraper that will perform reliably and durably in your specific operational conditions.
Customization and Compatibility
Ensuring that the belt scraper you choose fits seamlessly with your existing conveyor system is essential for optimal performance. Customization options and compatibility considerations are vital aspects to explore when selecting a scraper.
Customizable Options
Many manufacturers offer customizable belt scrapers to meet the specific needs of different conveyor systems and operational requirements. Customization can include:
- Blade Size and Shape: Adjusting the size and shape of the scraper blade to match the width and contour of the conveyor belt ensures comprehensive cleaning coverage and prevents material buildup along the edges.
- Mounting and Installation: Customizable mounting options allow the scraper to be installed at the optimal angle and position for maximum efficiency. This flexibility is crucial for adapting to various conveyor configurations and discharge points.
- Material and Hardness: Selecting the right material and hardness level for the scraper blade based on the transported material and operating conditions can significantly enhance the scraper’s effectiveness and lifespan.
By opting for customizable belt scrapers, you can tailor the scraper to your specific conveyor system, maximizing its cleaning efficiency and durability.
Ensuring Compatibility
Compatibility with existing conveyor components is crucial to avoid operational disruptions and ensure seamless integration of the belt scraper. Key compatibility considerations include:
- Conveyor Belt Type: The scraper must be compatible with the type of conveyor belt in use, including its material, thickness, and surface texture. For instance, scrapers used on rubber belts may differ from those used on metal or fabric belts.
- Conveyor Components: The scraper should not interfere with other conveyor components, such as rollers, idlers, or skirting systems. Ensuring that the scraper’s installation and operation do not cause conflicts or damage to these components is essential for maintaining overall system integrity.
- Operational Requirements: The scraper must align with the operational requirements of the conveyor system, such as load capacity, speed, and direction of travel. It should also be compatible with any existing cleaning or maintenance protocols in place.
Carefully evaluating these compatibility factors helps in selecting a belt scraper that integrates smoothly with your conveyor system and enhances its performance without causing disruptions or requiring significant modifications.
Choosing the right belt scraper for your needs involves a thorough assessment of various factors, including material type, conveyor speed, environmental conditions, and system compatibility. By understanding these considerations and exploring customizable options, you can select a belt scraper that not only meets your operational requirements but also enhances the efficiency, safety, and longevity of your conveyor system. Investing in the right belt scraper ultimately leads to improved productivity, reduced maintenance costs, and a safer working environment.
Installation and Maintenance Tips
Proper installation and regular maintenance are crucial to ensuring the optimal performance and longevity of belt scrapers. Whether you’re dealing with a primary or secondary belt scraper, following best practices during installation and adhering to a routine maintenance schedule can significantly enhance the efficiency of your conveyor system. This section provides detailed guidelines for both installation and maintenance, helping you get the most out of your belt scrapers.
Proper Installation Practices
Correct installation of belt scrapers is essential to achieving effective cleaning performance and preventing unnecessary wear on both the scraper and the conveyor belt. Here are some key practices to follow:
Follow Manufacturer Instructions
Every belt scraper comes with specific installation instructions provided by the manufacturer. Adhering to these guidelines is crucial to ensure that the scraper is positioned and adjusted correctly. This includes setting the scraper at the appropriate angle and pressure against the belt, which is vital for optimal material removal and minimizing damage to the belt surface.
- Primary Scrapers: Typically installed at the head pulley where the conveyor belt discharges, primary scrapers act as the first line of defense against bulk material carryback. Ensure that the primary belt scraper is mounted securely and adjusted to maintain consistent contact with the belt without exerting excessive pressure, which could lead to premature wear.
- Secondary Scrapers: Positioned further along the conveyor line, secondary scrapers are designed to remove residual material left by the primary scraper. Installation of secondary belt scrapers should focus on achieving precise alignment and pressure settings to maximize their cleaning effectiveness without affecting the belt’s integrity.
Following the manufacturer’s instructions not only ensures proper installation but also helps in maintaining the warranty and operational safety standards.
Positioning and Alignment
Accurate positioning and alignment of belt scrapers are crucial for their efficient operation. Improper alignment can lead to inadequate cleaning, increased wear on the scraper and belt, and potential damage to the conveyor system.
- Mounting Position: The scraper should be installed at the correct location relative to the belt’s surface and its travel path. For primary scrapers, this is typically at the point where the belt wraps around the head pulley. Secondary scrapers should be positioned to follow the belt’s contour and ensure full contact with the belt surface.
- Angle of Contact: The scraper blade should be set at an angle that allows it to effectively scrape material off the belt without gouging or damaging it. The optimal angle usually falls between 15 to 30 degrees relative to the belt’s surface, but this can vary depending on the type of scraper and conveyor system.
- Pressure Adjustment: The pressure exerted by the scraper on the belt should be sufficient to remove material without causing excessive wear. Adjustable tensioning mechanisms are often used to fine-tune this pressure, allowing for adjustments as the scraper or belt wears over time.
Proper positioning and alignment of belt scrapers enhance their cleaning efficiency and prolong the lifespan of both the scraper and the conveyor belt.
Routine Maintenance
Regular maintenance of belt scrapers is essential to keep them functioning effectively and to extend their operational life. Here are some key maintenance practices:
Regular Inspections
Conducting routine inspections helps identify wear and potential issues before they lead to system failures or significant downtime.
- Visual Checks: Perform regular visual inspections of the scraper blades, mounts, and adjustment mechanisms. Look for signs of wear, damage, or misalignment that could affect performance. Pay particular attention to the edges of the scraper blades, as these are often the first areas to show wear.
- Operational Testing: Run the conveyor system and observe the scrapers in action. Check for any irregularities in their movement or contact with the belt. Ensure that the scrapers are removing material effectively without leaving streaks or patches of residue.
Regular inspections allow for early detection of issues and timely maintenance interventions, reducing the risk of costly repairs or replacements.
Blade Replacement and Adjustment
Scraper blades will wear out over time and need periodic replacement to maintain cleaning efficiency. Additionally, regular adjustments are necessary to compensate for wear and to ensure consistent performance.
- Replacing Blades: Monitor the condition of the scraper blades and replace them when they become worn or damaged. Depending on the type of material being transported and the operating conditions, blades may need to be replaced more or less frequently. Keep spare blades on hand to minimize downtime during replacements.
- Adjusting Tension: As scraper blades wear, the tension or pressure applied to the belt may need adjustment to maintain optimal contact. Use the tensioning mechanism to fine-tune the pressure and angle of the scraper blade as needed. Ensure that adjustments are made evenly across the width of the belt to avoid uneven wear or cleaning performance.
Regular blade replacement and adjustment are key to maintaining the effectiveness and longevity of belt scrapers.
Cleaning and Lubrication
Keeping belt scrapers clean and well-lubricated is essential for smooth operation and preventing premature wear.
- Cleaning: Remove any accumulated material from the scraper blades and mounting hardware. This prevents buildup that could interfere with the scraper’s function or cause damage to conveyor belt. Use appropriate cleaning tools and solutions to avoid damaging the scraper or the belt.
- Lubrication: If the scraper system includes moving parts or tensioning mechanisms, ensure they are properly lubricated according to the manufacturer’s recommendations. Proper lubrication reduces friction and wear, extending the life of the scraper components.
Regular cleaning and lubrication help maintain the efficiency and reliability of belt scrapers.
Proper installation and routine maintenance of belt scrapers are crucial for maximizing their performance and lifespan. By following manufacturer instructions, ensuring accurate positioning and alignment, and adhering to regular maintenance practices, you can significantly enhance the efficiency and durability of your conveyor system. Investing time and effort into these practices not only improves operational performance but also leads to long-term cost savings and safer working conditions.
Notable Belt Scraper Products and Brands
Belt scrapers are essential components of conveyor systems, and several brands offer high-quality products designed to meet various industry needs. Here, we highlight some notable belt scraper products and brands that have made significant contributions to the market.
Flexco Belt Scrapers
Flexco stands out as a leading manufacturer of conveyor belt maintenance tools, including a range of belt scrapers. Their scrapers are designed to improve conveyor efficiency and reduce maintenance costs. Some popular Flexco belt scraper products include:
- Flexco® EZP1 Rockline® Precleaner: This primary belt scraper features a rugged, abrasion-resistant polyurethane blade for effective cleaning and long service life. It is suitable for use in heavy-duty applications, such as mining and aggregate operations.
- Flexco® EZS2 Rockline® Secondary Cleaner: Designed to remove residual material from the belt after the primary scraper, the EZS2 Rockline® Secondary Cleaner offers efficient cleaning performance and easy maintenance.
- Flexco® EZP1 Tungsten Carbide Precleaner: For extremely abrasive materials, the EZP1 Tungsten Carbide Precleaner provides superior wear resistance and extended blade life. It is ideal for challenging applications where standard polyurethane blades may wear quickly.
Flexco belt scrapers are known for their durability, reliability, and ease of maintenance, making them a popular choice among conveyor operators worldwide.
Other Leading Brands
In addition to Flexco, several other brands offer quality belt scrapers that cater to various industries and conveyor types. Some notable brands include:
- Martin Engineering: Known for their innovative conveyor belt cleaning solutions, Martin Engineering offers a wide range of belt scrapers designed for different applications. Their products are known for their durability and cleaning efficiency.
- ASGCO: ASGCO is another reputable brand that manufactures belt scrapers and other conveyor components. Their products are designed to improve conveyor performance and reduce maintenance costs.
- Richwood: Richwood offers a range of belt cleaning solutions, including belt scrapers, for bulk material handling applications. Their products are known for their high quality and reliability.
- Rema Tip Top: Rema Tip Top is a global provider of conveyor maintenance solutions, including belt scrapers. Their products are designed to optimize conveyor performance and minimize downtime.
When choosing a belt scraper, it’s essential to consider factors such as the application, conveyor type, and material being transported. Comparing products from different manufacturers can help you find the best solution for your specific needs.
FAQs about Belt Scraper
A belt scraper is a device commonly used in conveyor systems to remove materials that have adhered to the belt surface during transport. These devices are crucial for the maintenance and efficiency of conveyor belts, preventing excessive buildup that can lead to belt misalignment, decreased operational efficiency, and increased wear and tear. Belt scrapers are positioned at strategic points along the conveyor system, often at the head pulley where the material discharge occurs or at the tail pulley where the belt turns back after discharging material. The design and implementation of belt scrapers must consider the type of material being conveyed, the environment of operation, and the specific requirements of the conveyor system to ensure effective cleaning and minimal impact on the belt’s integrity.
Conveyor belts are cleaned using several techniques and tools designed to keep the belt surface free from material buildup and to maintain operational efficiency. The primary method involves the use of belt scrapers, which come in contact with the belt to strip away stuck materials. Primary scrapers are installed at the discharge point to remove the bulk of the material, followed by secondary scrapers that remove finer particles further along the belt. Supplementary cleaning methods include rotating brushes, water sprays, or air knives to handle particularly challenging materials or applications. Consistent maintenance and cleaning are essential for conveyor belt longevity, preventing potential hazards and ensuring a clean return path for the belt.
A belt cleaner is a system or component designed to clean conveyor belts in an automated fashion. Primarily, belt cleaners serve to remove the carryback—the material that sticks to the belt after the cargo has been discharged. They are a vital part of the conveyor system, enhancing both the efficiency and safety of material transport. Belt cleaners can be categorized based on their placement and function: primary belt cleaners are mounted on the head pulley, removing the large majority of material, while secondary belt cleaners clear away any residual materials left by primary cleaners. Some systems also include tertiary cleaners, which provide additional cleaning when necessary. Regular use of belt cleaners extends the life of conveyor belts and reduces the risks associated with material spillage.
Conveyor scrapers, or belt cleaners, are made from a variety of materials, each chosen for its specific properties to match the needs of different applications. Common materials include:
Polyurethane: With good wear resistance and the ability to work with various types of belts, polyurethane scrapers provide a durable cleaning solution that minimizes potential damage to the belt.
Rubber: Rubber scrapers are flexible and provide efficient cleaning for belts with irregular surfaces or for operations handling wet or sticky materials.
Carbide-tipped and Metal Blades: These are used for their hardness and ability to handle tough, abrasive materials that might be resistant to softer materials.
Ceramic: Known for its exceptional durability and resistance to wear, ceramic scrapers are suited for harsh conditions and high-speed conveyor systems.
Each material offers specific benefits and is selected based on factors like the type of conveyor belt, the materials being conveyed, and the conditions of the operating environment. The objective is to achieve the most effective cleaning without compromising the conveyor belt’s integrity or lifespan.
Last Updated on June 28, 2024 by Jordan Smith
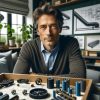
Jordan Smith, a seasoned professional with over 20 years of experience in the conveyor system industry. Jordan’s expertise lies in providing comprehensive solutions for conveyor rollers, belts, and accessories, catering to a wide range of industrial needs. From initial design and configuration to installation and meticulous troubleshooting, Jordan is adept at handling all aspects of conveyor system management. Whether you’re looking to upgrade your production line with efficient conveyor belts, require custom conveyor rollers for specific operations, or need expert advice on selecting the right conveyor accessories for your facility, Jordan is your reliable consultant. For any inquiries or assistance with conveyor system optimization, Jordan is available to share his wealth of knowledge and experience. Feel free to reach out at any time for professional guidance on all matters related to conveyor rollers, belts, and accessories.