Optimizing Operations with Different Conveyor Pulley Types
Understanding the various conveyor pulley types are crucial for optimizing conveyor systems. The drive pulley plays a vital role in propelling the conveyor belt. Positioned at the discharge end, the drive pulley is connected to a motor that provides the necessary force to move the belt and the materials on it. Efficient drive pulleys ensure smooth and reliable operation, minimizing slippage and energy loss. Using high-quality drive pulleys can significantly enhance the performance of the conveyor system, reduce maintenance costs, and extend the lifespan of the conveyor belt. By selecting the appropriate conveyor pulley types, businesses can improve productivity and ensure continuous, efficient material handling.
Optimizing Conveyor Pulley Types with the Right Pulleys
In the intricate world of conveyor systems, the selection and use of the appropriate pulleys can significantly influence the efficiency, performance, and longevity of the entire system. Understanding the different conveyor pulley types and their specific applications is crucial for optimizing conveyor operations. This section delves into best practices for selecting and using conveyor pulleys and explores how the right pulley selection can enhance conveyor performance and longevity.
Best Practices for Selecting and Using Conveyor Pulleys
Selecting the right conveyor pulley types is fundamental to ensuring efficient and reliable conveyor system operation. Here are some best practices for choosing and using conveyor pulleys:
Identify the Application Requirements: The first step in selecting the right pulley is to understand the specific requirements of the application. This includes considering the type of materials being transported, the operational environment, load capacities, and the speed of the conveyor system. For instance, a conveyor system in a mining operation will have different demands compared to one in a food processing plant.
Consider the Pulley Function: Different conveyor pulley types serve various functions within a conveyor system. Common types include drive pulleys, tail pulleys, snub pulleys, bend pulleys, and take-up pulleys. Each type has its role, such as driving the belt, redirecting belt paths, or maintaining tension. Selecting the right type for the specific function is crucial for optimal performance.
Material Selection: The material of the pulley must be chosen based on the operating conditions. For heavy-duty applications, pulleys made of robust materials like steel or cast iron are preferable. For environments that require corrosion resistance, such as food processing or chemical industries, stainless steel or coated pulleys may be more appropriate. The pulley material should also be compatible with the type of belt used in the conveyor system.
Pulley Diameter and Face Width: The diameter of the pulley affects the bending stress on the belt and the grip between the belt and the pulley. Larger diameters are generally better for reducing belt stress and increasing belt life. The face width of the pulley should be selected to ensure it accommodates the full width of the belt with some clearance on each side to prevent belt slippage and misalignment.
Lagging Considerations: Lagging, or the covering on the pulley surface, enhances the friction between the pulley and the belt, reducing slippage. Rubber lagging is common for general applications, while ceramic lagging provides higher friction and is used in high-tension applications. Selecting the appropriate lagging material based on the specific requirements can significantly improve the conveyor’s performance.
Alignment and Installation: Proper alignment and installation of the pulleys are critical for preventing belt misalignment and reducing wear. Ensure that the pulleys are installed squarely and that the shafts are parallel. Misalignment can cause uneven wear on the belt and pulleys, leading to premature failure and increased maintenance costs.
Enhancing Conveyor Performance and Longevity with Appropriate Pulley Selection
Choosing the right conveyor pulley types and ensuring their proper use can lead to significant enhancements in conveyor performance and longevity. Here’s how the appropriate pulley selection contributes to these improvements:
Reduced Belt Slippage: The correct selection and installation of drive pulleys, with appropriate lagging, ensure that there is sufficient friction between the belt and the pulley. This reduces belt slippage, which can cause inefficiencies, increased wear, and potential damage to the belt and other components.
Improved Belt Tracking: The use of snub pulleys and take-up pulleys helps maintain proper belt tension and alignment. This is essential for keeping the belt centered on the pulleys and preventing tracking issues that can lead to edge wear and belt damage. Proper belt tracking ensures smooth and reliable operation, reducing downtime and maintenance requirements.
Minimized Wear and Tear: Selecting pulleys with the correct diameter and face width minimizes the bending stress on the belt, reducing fatigue and extending the belt’s life. Additionally, using pulleys made from durable materials appropriate for the operating environment minimizes wear on both the pulleys and the belt, leading to longer component life and reduced maintenance costs.
Enhanced Load Capacity: Properly selected and installed pulleys ensure that the conveyor system can handle the required load capacity without excessive strain on the belt and other components. This is particularly important in high-load applications where the system needs to operate efficiently and reliably under significant stress.
Increased Operational Efficiency: The right combination of conveyor pulley types ensures that the system operates smoothly and efficiently. This includes minimizing power loss due to slippage, ensuring consistent belt speed, and reducing the risk of unexpected failures. Efficient operation translates to higher productivity and lower operational costs.
Safety Improvements: Proper pulley selection and installation also enhance the safety of the conveyor system. Reduced slippage, better alignment, and minimized wear all contribute to a safer working environment by reducing the likelihood of belt breakages and component failures that could lead to accidents.
Adaptability to Environmental Conditions: The selection of pulley materials and coatings that are resistant to specific environmental conditions, such as moisture, chemicals, or extreme temperatures, ensures that the conveyor system can operate reliably in challenging environments. This adaptability reduces the risk of corrosion and other environmental damage, further extending the lifespan of the conveyor system.
What is Conveyor Pulley Types
In the realm of material handling, conveyor systems play an indispensable role, and pulleys are vital components that determine their efficiency and reliability. Understanding the different conveyor pulley types and their specific functions can help in optimizing the design and performance of these systems. This section focuses on the function of the snub pulley in belt conveyors, providing a detailed explanation of its roles and the advantages of integrating snub pulleys in conveyor systems.
Function of Snub Pulley in Belt Conveyor
Detailed Explanation of Snub Pulley Functions
A snub pulley is an essential component in a belt conveyor system, strategically positioned to enhance the performance and efficiency of the conveyor. The primary function of a snub pulley is to increase the wrap angle of the conveyor belt around the drive pulley, thereby improving traction and reducing slippage. Here is a detailed explanation of the various functions performed by snub pulleys:
1. Increasing Wrap Angle:
The wrap angle is the degree of contact between the conveyor belt and the drive pulley. By increasing this angle, the snub pulley enhances the grip of the belt on the drive pulley, which is crucial for effective power transmission. The increased contact surface ensures that the drive pulley can exert sufficient force on the belt, preventing slippage and maintaining consistent belt movement.
2. Enhancing Belt Tension:
Proper belt tension is vital for the efficient operation of a conveyor system. Snub pulleys help in maintaining the desired tension by positioning the belt in a way that maximizes contact with the drive pulley. This tension prevents sagging, reduces wear on the belt and other components, and ensures that the belt remains aligned and runs smoothly.
3. Improving Belt Tracking:
Belt tracking refers to the alignment of the conveyor belt as it moves along the pulleys. Misalignment can lead to operational issues such as spillage, increased wear, and potential damage to the conveyor system. Snub pulleys aid in guiding the belt and keeping it centered on the pulleys. By adjusting the position and angle of the snub pulley, operators can fine-tune the tracking, ensuring optimal alignment and reducing the risk of disruptions.
4. Reducing Belt Slippage:
Slippage occurs when the frictional forces between the conveyor belt and the drive pulley are insufficient to move the belt effectively. This can result in inefficient material handling and increased wear on the belt. By increasing the wrap angle, the snub pulley enhances the grip of the belt on the drive pulley, significantly reducing the likelihood of slippage. This improved traction ensures that the conveyor system operates efficiently, with minimal downtime and maintenance requirements.
5. Supporting Load Distribution:
The snub pulley also plays a role in distributing the load more evenly across the conveyor belt. This balanced load distribution reduces strain on specific sections of the belt and prevents localized wear, enhancing the overall durability and performance of the conveyor system.
Advantages of Integrating Snub Pulleys in Conveyor Systems
Integrating snub pulleys into conveyor systems offers numerous advantages that contribute to improved efficiency, reliability, and longevity of the equipment. Here are some of the key benefits:
1. Enhanced Conveyor Efficiency:
With improved traction and reduced slippage, snub pulleys enable more efficient power transmission from the drive pulley to the conveyor belt. This efficiency translates into smoother and more reliable belt movement, ensuring that materials are transported consistently and without interruptions. Enhanced efficiency can lead to increased throughput and higher productivity.
2. Extended Component Lifespan:
By preventing slippage and ensuring proper belt tension, snub pulleys reduce the wear and tear on the conveyor belt and other components. This reduction in wear extends the lifespan of the belt, pulleys, and bearings, leading to lower maintenance costs and less frequent replacement of parts. The extended lifespan of components results in significant cost savings over the long term.
3. Improved Material Handling:
Consistent belt movement is crucial for effective material handling. Uneven belt speed or direction changes caused by slippage can lead to material spillage, blockages, or uneven distribution of materials on the belt. Snub pulleys ensure that the belt moves smoothly and predictably, improving the reliability of the conveyor system. This reliability is essential in industries where precise material handling is critical, such as food processing, pharmaceuticals, and automotive manufacturing.
4. Increased Safety:
A well-functioning conveyor system is also a safer system. Belt slippage and misalignment can create hazardous conditions, including the risk of material spillage, equipment damage, and worker injuries. By improving belt traction and ensuring smooth operation, snub pulleys help mitigate these risks, contributing to a safer working environment. Enhanced safety not only protects workers but also reduces the likelihood of costly accidents and downtime.
5. Greater Flexibility in Conveyor Design:
The use of snub pulleys provides greater flexibility in conveyor system design. By adjusting the position and angle of the snub pulley, operators can fine-tune the wrap angle and tension of the conveyor belt. This flexibility allows for customization of the conveyor system to meet specific operational requirements and constraints. It also enables the system to adapt to changes in load conditions, material types, and other variables, ensuring consistent performance across a range of applications.
6. Optimized Load Distribution:
Snub pulleys help distribute the load more evenly across the conveyor belt, reducing the strain on specific sections and preventing localized wear. This balanced load distribution enhances the overall durability and performance of the conveyor system, ensuring consistent material handling and minimizing the risk of belt failure.
7. Cost-Effective Solution:
The integration of snub pulleys into conveyor systems is a cost-effective solution for improving efficiency and reducing maintenance costs. The initial investment in snub pulleys is offset by the long-term savings achieved through extended component lifespan, reduced downtime, and lower maintenance requirements. This cost-effectiveness makes snub pulleys an attractive option for various industries looking to optimize their material handling operations.
8. Versatility Across Industries:
Snub pulleys are versatile components that can be used in a wide range of conveyor systems and applications. Whether in mining, manufacturing, packaging, or distribution, snub pulleys can be adapted to meet the specific needs of different industries. Their ability to enhance belt traction, improve tracking, and maintain proper tension makes them valuable assets in diverse operational environments.
Key of Conveyor Pulley Types and Their Roles
About the key components of conveyor pulleys and how they contribute to the overall functionality is essential for optimizing conveyor system performance. Conveyor pulleys play a pivotal role in the operation of conveyor belts, ensuring smooth movement and efficient material handling. This section will delve into the essential components of conveyor pulleys and explain how each part contributes to their functionality.
Essential Components of Conveyor Pulleys
When discussing conveyor pulley types, it is crucial to understand the specific parts that make up these essential components. Here are the primary parts of conveyor pulleys:
1. Pulley Shell (Drum)
The pulley shell, or drum, is the cylindrical outer surface of the pulley. It is typically made from steel or other durable materials capable of withstanding the operational stresses of conveyor systems. The shell’s primary function is to provide a smooth surface for the conveyor belt to contact, ensuring even tension and reducing the risk of slippage.
2. Shaft
The shaft is the central part of the pulley that provides structural support and transfers rotational force from the drive system to the pulley shell. Made from high-strength materials, the shaft must be able to handle significant mechanical loads and rotational forces. The ends of the shaft are often machined to fit bearings and couplings, which are crucial for the pulley’s movement and alignment.
3. End Discs
End discs, also known as end plates, are located on either end of the pulley shell and are welded or otherwise fixed to the shell. These discs provide additional structural support to the pulley shell and help maintain its cylindrical shape. They also serve as mounting points for the pulley shaft and bearings.
4. Bearings
Bearings are critical components that support the conveyor roller shaft and allow it to rotate smoothly with minimal friction. Bearings are typically housed within the end discs and are essential for reducing wear and tear on the shaft and other pulley components. They also help maintain the alignment of the pulley within the conveyor system.
5. Hub and Bushing
The hub and bushing are components that connect the pulley to the shaft. The hub is part of the end disc, while the bushing is a removable component that fits inside the hub and clamps onto the shaft. This arrangement allows for easy installation and removal of the pulley, facilitating maintenance and replacements.
6. Lagging
Lagging is a covering applied to the outer surface of the pulley shell to increase friction between the pulley and the conveyor belt. Lagging materials can include rubber, ceramic, or other composites, depending on the application requirements. The purpose of lagging is to prevent belt slippage, especially in high-tension or high-load scenarios.
7. Keyways and Keys
Keyways are slots machined into the pulley shaft and hub that accommodate keys, which are metal pieces that lock the hub to the shaft. This prevents relative motion between the shaft and the pulley, ensuring that rotational force is effectively transferred from the drive system to the pulley.
How Each Part Contributes to Pulley Functionality
Each part of a conveyor pulley plays a specific role in ensuring the smooth operation and efficiency of conveyor systems. Here’s how these components contribute to pulley functionality:
Pulley Shell (Drum)
The shell provides the primary surface area for the conveyor belt to grip. Its smooth, cylindrical shape ensures even distribution of tension across the belt, reducing the risk of belt misalignment and wear. The durability of the shell material also helps it withstand the constant contact and pressure exerted by the belt and the materials being conveyed.
Shaft
The shaft acts as the backbone of the pulley, supporting the weight and forces applied to the pulley. It must be robust enough to handle the torque from the drive system and the tension from the conveyor belt. The precision machining of the shaft ends allows for proper alignment and smooth rotation, which are critical for the overall efficiency of the conveyor system.
End Discs
End discs maintain the structural integrity of the pulley shell, ensuring it retains its shape under load. They provide secure mounting points for the shaft and bearings, which are essential for the stable and reliable operation of the pulley. By supporting the shell, the end discs help prevent deformation and ensure consistent performance.
Bearings
Bearings reduce friction between the rotating shaft and the stationary parts of the conveyor system, allowing the pulley to rotate smoothly. This smooth rotation is crucial for minimizing wear on the shaft and other components, reducing maintenance requirements, and extending the life of the pulley and the conveyor system as a whole.
Hub and Bushing
The hub and bushing system allows for secure attachment of the pulley to the shaft while also enabling easy removal and replacement. This design simplifies maintenance and ensures that the pulley can be quickly and efficiently serviced, minimizing downtime and operational disruptions.
Lagging
Lagging increases the friction between the pulley and the conveyor belt, preventing slippage and ensuring efficient power transmission. The choice of lagging material can be tailored to specific operational conditions, such as high-tension applications or environments with abrasive materials. This customization helps optimize the performance and lifespan of the pulley and the conveyor belt.
Keyways and Keys
Keyways and keys ensure that the hub and shaft rotate together, allowing the drive system to transmit rotational force to the pulley effectively. This secure connection is vital for maintaining the synchronization of the pulley with the rest of the conveyor system, preventing slippage and ensuring consistent belt movement.
Types of Idlers in Conveyor Pulley Types
When discussing types of conveyor pulley, it is essential to also consider the different types of idlers in belt conveyor systems. Idlers are critical components that support the conveyor belt and facilitate its movement along the system. This section explores the various idler types and their roles, as well as the impact of idlers on conveyor efficiency and belt life.
Different Idler Types and Their Roles
Idlers are categorized based on their specific functions and the locations where they are used in the conveyor system. Here are the primary types of idlers and their respective roles:
1. Carrying Idlers
Carrying idlers are positioned on the carrying side of the conveyor belt and support the weight of the material being transported. They are typically spaced at regular intervals along the length of the conveyor and ensure that the belt remains flat and stable. Carrying idlers are essential for maintaining the belt’s alignment and preventing sagging, which can lead to material spillage and belt damage.
2. Return Idlers
Return idlers are located on the return side of the conveyor belt and support the empty belt on its return journey to the tail pulley. These idlers help to keep the belt aligned and prevent it from dragging on the conveyor structure. Return idlers are crucial for minimizing belt wear and ensuring smooth operation.
3. Impact Idlers
Impact idlers are installed at loading points where the material is deposited onto the conveyor belt. They are designed with shock-absorbing materials such as rubber rings to cushion the impact of falling material and protect the belt from damage. Impact idlers play a vital role in extending the life of the conveyor belt by reducing the risk of punctures, tears, and other forms of damage caused by heavy or sharp materials.
4. Transition Idlers
Transition idlers are used at points where the conveyor belt transitions from a flat profile to a trough or vice versa. These idlers are positioned at the head and tail ends of the conveyor and help to gradually change the belt’s shape, minimizing stress and preventing damage. Transition idlers are important for maintaining belt integrity and ensuring smooth transitions between different sections of the conveyor.
5. Self-aligning Idlers
Self-aligning idlers are designed to correct any misalignment of the conveyor belt automatically. They are equipped with pivoting mechanisms that allow them to adjust their angle based on the belt’s movement. Self-aligning idlers are typically used in the carrying and return sections of the conveyor to maintain proper belt alignment and prevent tracking issues that can lead to uneven wear and operational inefficiencies.
6. Training Idlers
Training idlers are similar to self-aligning idlers but are manually adjustable. Operators can adjust the angle of training idlers to guide the belt back to its correct path. Training idlers are used to correct persistent alignment issues and ensure the belt runs true along the conveyor system.
Impact of Idlers on Conveyor Efficiency and Belt Life
The selection and maintenance of idlers have a significant impact on the overall efficiency and lifespan of a conveyor system. Here are some of the ways idlers influence conveyor performance:
1. Enhanced Belt Support and Stability
Properly selected and maintained idlers provide consistent support to the conveyor belt, ensuring it remains flat and stable. This stability is crucial for preventing material spillage and maintaining efficient material flow. By reducing the risk of belt sagging and misalignment, idlers help to improve the overall efficiency of the conveyor system.
2. Reduced Belt Wear and Tear
Impact idlers play a critical role in protecting the conveyor belt from damage at loading points. By absorbing the shock of falling materials, these idlers prevent punctures, tears, and other forms of damage that can shorten the belt’s lifespan. Additionally, carrying and return idlers support the belt evenly, reducing localized wear and extending the belt’s life.
3. Improved Material Handling Efficiency
Idlers contribute to smooth and efficient material handling by maintaining the proper alignment and tension of the conveyor belt. Self-aligning and training idlers ensure that the belt runs true along the system, preventing tracking issues that can disrupt operations and cause delays. Efficient material handling reduces downtime and increases productivity.
4. Minimized Maintenance Requirements
Well-maintained idlers reduce the frequency and severity of maintenance issues in conveyor systems. By preventing belt misalignment, wear, and damage, idlers minimize the need for repairs and replacements. This reduction in maintenance requirements leads to lower operational costs and increased system reliability.
5. Increased Conveyor System Longevity
The overall longevity of a conveyor system is heavily influenced by the condition and performance of its idlers. Properly functioning idlers reduce stress and wear on the conveyor belt and other components, extending the system’s operational life. Investing in high-quality idlers and performing regular maintenance can significantly enhance the durability and longevity of the entire conveyor system.
6. Enhanced Safety
Idlers contribute to the safety of conveyor operations by maintaining the stability and alignment of the conveyor belt. Misaligned belts can cause material spillage, leading to hazardous conditions in the work environment. By ensuring proper belt tracking and support, idlers help to create a safer working environment for personnel.
Conveyor Pulley Types
Snub Pulley Function in Conveyor Systems
In the intricate world of conveyor systems, understanding the roles of different pulley types is essential for optimizing performance and efficiency. Among the various conveyor pulley types, the snub pulley holds a critical position. This section delves into the specific functions of snub pulleys, focusing on how they increase belt wrap and improve traction, and their importance in high-tension applications.
How Snub Pulleys Increase Belt Wrap and Improve Traction
The primary function of a snub pulley is to increase the wrap angle of the conveyor belt around the drive pulley. The wrap angle is the portion of the drive pulley circumference that is in contact with the conveyor belt. By increasing this angle, the snub pulley enhances the belt’s grip on the drive pulley, which is crucial for effective power transmission and reducing slippage.
Increasing Wrap Angle:
A snub pulley is strategically positioned close to the drive pulley. Its placement allows the conveyor belt to be redirected in a way that increases the wrap angle around the drive pulley. For instance, if the belt initially wraps 180 degrees around the drive pulley, the addition of a snub pulley can increase this wrap to 210 degrees or more. This increased contact surface provides greater friction between the belt and the pulley, enhancing the grip.
Improving Traction:
Enhanced belt traction is a direct result of the increased wrap angle. With more of the belt’s surface area in contact with the drive pulley, the force exerted by the drive pulley is distributed over a larger area. This distribution reduces the risk of belt slippage, ensuring that the belt moves smoothly and consistently. Improved traction is particularly important in applications where precise material handling is required, such as in manufacturing or packaging processes.
Benefits of Increased Belt Wrap:
- Reduced Slippage: By increasing the contact area between the belt and the drive pulley, snub pulleys significantly reduce slippage. This is crucial for maintaining consistent belt speed and preventing disruptions in material flow.
- Enhanced Power Transmission: More efficient power transmission from the drive motor to the conveyor belt ensures that the system operates smoothly and efficiently. This leads to better performance and productivity.
- Prolonged Belt Life: Reduced slippage and improved traction mean less wear and tear on the belt. This extends the belt’s lifespan and reduces the frequency of replacements, leading to cost savings.
Importance of Snub Pulleys in High-Tension Applications
Snub pulleys play an indispensable role in high-tension applications where the demands on the conveyor system are particularly rigorous. High-tension applications typically involve heavy loads, long conveyor lengths, or steep inclines, all of which require robust solutions to maintain system integrity and performance.
Enhancing Belt Tension:
In high-tension applications, maintaining proper belt tension is critical. Snub pulleys help achieve the necessary tension by increasing the wrap angle, which in turn enhances the frictional grip of the belt on the drive pulley. Proper tension ensures that the belt remains taut and aligned, preventing sagging and misalignment that could lead to operational issues.
Supporting Load Distribution:
High-tension conveyor systems often deal with substantial loads that can place significant strain on the belt and pulleys. Snub pulleys help distribute these loads more evenly across the belt, reducing localized stress and wear. This balanced load distribution is essential for preventing belt failure and ensuring consistent material handling.
Improving System Reliability:
The reliability of a conveyor system is paramount in high-tension applications. Snub pulleys contribute to this reliability by minimizing the risk of belt slippage and ensuring smooth, continuous operation. Reduced slippage means fewer interruptions and less downtime, which is crucial for maintaining productivity in demanding environments.
Reducing Maintenance Costs:
In high-tension applications, the wear and tear on conveyor components can be significant. Snub pulleys help mitigate this wear by improving belt traction and reducing slippage, which in turn lowers the overall maintenance requirements. The extended lifespan of the belt and pulleys translates to lower maintenance costs and less frequent replacements.
Ensuring Safety:
Safety is a critical concern in any conveyor system, but it is especially important in high-tension applications where the risks are greater. Snub pulleys enhance safety by ensuring that the belt remains properly tensioned and aligned, reducing the likelihood of accidents caused by belt failure or misalignment. This not only protects the equipment but also safeguards the personnel working with or around the conveyor system.
Optimizing Performance in Varied Conditions:
High-tension applications often involve variable operating conditions, such as changes in load, speed, and environmental factors. Snub pulleys provide the flexibility needed to adapt to these conditions. By allowing adjustments to the wrap angle and belt tension, snub pulleys help maintain optimal performance across a range of scenarios.
Enhancing Efficiency and Productivity:
The cumulative effect of increased belt wrap, improved traction, and enhanced tension control is greater overall efficiency and productivity. Snub pulleys enable conveyor systems to handle higher loads and operate at faster speeds without compromising performance. This increased efficiency can lead to significant gains in productivity, making snub pulleys a valuable investment for high-tension applications.
FAQS about Conveyor Pulley Types
The return pulley of a belt conveyor is a crucial component located on the return side of the conveyor belt, guiding the belt back to the head pulley after it has discharged its load. This pulley helps to maintain proper tension and alignment of the conveyor belt, ensuring smooth and efficient operation. The return pulley also aids in reducing belt wear and tear by providing support and maintaining the belt’s shape during its return journey. Proper functioning of the return pulley is essential for minimizing maintenance costs and extending the lifespan of the conveyor system, as it ensures that the belt remains correctly positioned and tensioned throughout its cycle.
There are various types of conveyors used in different industries, but the three most common types are:
Belt Conveyors: These use a continuous belt made of various materials to transport items from one point to another. They are widely used in industries like manufacturing, packaging, and mining due to their ability to handle a variety of materials efficiently.
Roller Conveyors: Consist of a series of rollers, either powered or gravity-driven, that move items along a flat or inclined surface. Roller conveyors are ideal for transporting heavy or bulky items and are commonly used in warehouses and distribution centers.
Chain Conveyors: Utilize chains to move products along a production line. They are suitable for heavy-duty applications, such as automotive and heavy manufacturing, where the materials being transported are large or heavy.
These conveyors are chosen based on the specific needs of the industry, material type, and operational requirements.
A pulley on a conveyor is a mechanical device that changes the direction of the conveyor belt, provides tension, and drives the belt forward. Pulleys are essential components in conveyor systems, enabling the belt to move materials from one point to another efficiently. The primary types of pulleys include head pulleys, which drive the belt, tail pulleys, which provide tension and alignment, and snub pulleys, which increase the wrap angle around the drive pulley for better traction. Pulleys can be made of various materials, including steel and rubber, to withstand different operational demands. They play a critical role in ensuring the smooth operation, stability, and longevity of conveyor systems.
Conveyor systems utilize several types of pulleys, each serving specific functions to ensure smooth and efficient operation. The main types of pulleys in a conveyor system include:
Head Pulley: Located at the discharge end, it drives the conveyor belt and is typically larger in diameter to provide better traction.
Tail Pulley: Positioned at the loading end, it helps maintain belt tension and alignment.
Snub Pulley: Increases the wrap angle of the belt around the drive pulley, improving traction and reducing slippage.
Bend Pulley: Used to change the direction of the belt within the conveyor system.
Take-Up Pulley: Ensures proper tension of the conveyor belt by adjusting its position.
Drive Pulley: Powers the conveyor belt, usually the head pulley, driven by a motor.
These pulleys work together to ensure the efficient movement of materials along the conveyor belt, each playing a specific role in the system’s functionality.
Last Updated on August 15, 2024 by Jordan Smith
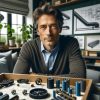
Jordan Smith, a seasoned professional with over 20 years of experience in the conveyor system industry. Jordan’s expertise lies in providing comprehensive solutions for conveyor rollers, belts, and accessories, catering to a wide range of industrial needs. From initial design and configuration to installation and meticulous troubleshooting, Jordan is adept at handling all aspects of conveyor system management. Whether you’re looking to upgrade your production line with efficient conveyor belts, require custom conveyor rollers for specific operations, or need expert advice on selecting the right conveyor accessories for your facility, Jordan is your reliable consultant. For any inquiries or assistance with conveyor system optimization, Jordan is available to share his wealth of knowledge and experience. Feel free to reach out at any time for professional guidance on all matters related to conveyor rollers, belts, and accessories.