Choosing the Right Belt Scale for Your Conveyor System
A belt scale is an essential device used in conveyor systems to measure the flow rate of bulk materials. Belt scales are crucial for industries such as mining, agriculture, and manufacturing, where precise material handling is vital for operational efficiency and profitability. By providing accurate measurements of the material on the conveyor belt, a belt scale helps in maintaining control over the production process, ensuring consistency and quality in the final output. The real-time data provided by belt scales is invaluable for inventory management, reducing material wastage, and optimizing the overall production process. This leads to increased productivity, reduced downtime, and lower maintenance costs, making belt scales a critical component in modern industrial applications.
Flexco Lacing Systems of Belt Scale
Flexco is renowned for its innovative and reliable conveyor belt solutions, including its high-quality lacing systems. These systems are designed to provide secure, efficient, and durable splicing for conveyor belts, ensuring seamless operation and minimal downtime. This section provides an overview of Flexco lacing systems, highlighting their key features and benefits.
Overview of Flexco Lacing
Flexco lacing systems are engineered to join conveyor belt ends to create a continuous loop, allowing for smooth and efficient material transport. These systems are essential in various industries, including mining, manufacturing, food processing, and logistics, where conveyor belts play a critical role in daily operations. The lacing systems are available in multiple designs and materials to suit different belt types and application requirements.
Flexco offers a range of lacing systems, each tailored to specific operational needs. Some of the most popular Flexco lacing solutions include the Alligator® Lacing System, the Clipper® Lacing System, and the Rivet Hinged Fastening System. Each of these systems is designed to provide a reliable and long-lasting splice, ensuring the conveyor belt performs optimally under various conditions.
Key Features and Benefits
Flexco lacing systems boast numerous features and benefits that make them a preferred choice for many industries. Here’s a detailed look at what sets these systems apart:
Ease of Installation: One of the standout features of Flexco lacing systems is their ease of installation. The systems are designed for quick and straightforward application, reducing downtime and minimizing operational disruptions. Tools and instructions provided by Flexco ensure that even users with limited technical expertise can achieve a secure and reliable splice. This ease of installation is particularly beneficial in emergency repair situations where time is of the essence.
Durability and Strength: Flexco lacing systems are built to withstand the demanding conditions of various industrial environments. The materials used in these lacing systems, such as stainless steel and high-strength plastic, are chosen for their durability and resistance to wear and tear. This durability ensures that the lacing system maintains its integrity over time, providing a long-lasting splice that reduces the frequency of maintenance and replacements.
Versatility: Flexco lacing systems are highly versatile, making them suitable for a wide range of conveyor belt types and applications. Whether dealing with lightweight belts in the food industry or heavy-duty belts in mining operations, Flexco has a lacing system that fits the bill. This versatility allows companies to standardize their splicing solutions across different conveyor systems, simplifying maintenance and inventory management.
Enhanced Performance: The design of Flexco lacing systems ensures optimal belt performance. By providing a smooth and seamless splice, these systems help maintain the belt’s alignment and tension, reducing the risk of slippage and misalignment. This enhanced performance translates to improved conveyor efficiency, higher productivity, and reduced energy consumption.
Improved Safety: Safety is a critical consideration in any industrial operation. Flexco lacing systems are designed with safety in mind, featuring rounded edges and secure fastening mechanisms that reduce the risk of injury during installation and maintenance. Additionally, the reliable splices provided by these systems minimize the likelihood of belt failures and accidents, contributing to a safer working environment.
Cost-Effectiveness: While the initial investment in high-quality lacing systems may be higher, the long-term benefits far outweigh the costs. Flexco lacing systems help reduce maintenance expenses, minimize downtime, and extend the life of conveyor belts. These cost savings, combined with the systems’ durability and performance, make Flexco lacing a cost-effective solution for businesses looking to optimize their conveyor operations.
Environmental Resistance: Flexco lacing systems are designed to perform reliably in a variety of environmental conditions. Whether exposed to moisture, chemicals, extreme temperatures, or abrasive materials, these systems maintain their strength and integrity. This environmental resistance ensures that the lacing systems can be used in diverse settings without compromising performance.
Alligator® Lacing System: The Alligator® Lacing System is one of Flexco’s most popular solutions, known for its simplicity and effectiveness. It uses a single tool to install a continuous row of fasteners across the belt end, creating a strong, flexible splice. This system is ideal for applications requiring frequent belt adjustments or replacements, such as in agricultural or package handling industries.
Clipper® Lacing System: The Clipper® Lacing System is another highly regarded Flexco solution, featuring a low-profile design that minimizes noise and wear on conveyor components. This system uses individual staples to create a strong, smooth splice that can easily navigate smaller pulleys and belt scrapers. The Clipper® system is particularly well-suited for food processing and other light to medium-duty applications.
Rivet Hinged Fastening System: For heavy-duty applications, the Rivet Hinged Fastening System offers unparalleled strength and durability. This system uses self-setting rivets that penetrate the belt and the fastener plate, creating a secure and permanent splice. The rivet hinged system is ideal for use in mining, quarrying, and other demanding industries where belts are subject to heavy loads and harsh conditions.
What is Belt Scale
Belt Lacing Joints
In the world of conveyor systems, maintaining the integrity and efficiency of the belt is paramount. One of the critical components in ensuring a conveyor belt’s reliability and performance is the belt lacing joint. This section provides an in-depth explanation of belt lacing joints and discusses their importance in conveyor systems.
Explanation of Belt Lacing Joints
Belt lacing joints are mechanical fasteners used to join the ends of a conveyor belt to form a continuous loop. These joints are essential for both endless belts, which are installed as a continuous loop, and for belts that require frequent removal for maintenance or repair. The primary purpose of belt lacing joints is to ensure a strong, reliable connection that can withstand the operational stresses of the conveyor system.
Types of Belt Lacing Joints:
- Mechanical Fasteners:
Mechanical fasteners are the most common type of belt lacing joint. They consist of metal or plastic components that are mechanically attached to the belt ends. The fasteners are designed to penetrate the belt material and interlock with each other, creating a secure connection. Popular mechanical fasteners include alligator clips, staple fasteners, and hinged fasteners. - Splicing:
Splicing involves joining the belt ends using adhesives, heat, or vulcanization. This method creates a seamless joint that is often stronger than the original belt. Splicing is typically used for belts that require a permanent, high-strength connection and are less likely to be removed frequently. There are several splicing techniques, including hot vulcanizing, cold vulcanizing, and mechanical splicing. - Hinged Fasteners:
Hinged fasteners are a subset of mechanical fasteners that allow for easy installation and removal. They are particularly useful for belts that need to be frequently taken on and off the conveyor system. The hinged design allows the belt to be opened and closed like a hinge, providing flexibility and ease of maintenance.
Installation Process:
- Preparation:
The first step in installing belt lacing joints is to prepare the belt ends. This involves cutting the belt to the correct length and squaring the ends to ensure a precise fit. Any rough edges or frayed sections should be trimmed to prevent uneven wear and ensure a smooth connection. - Aligning the Fasteners:
The next step is to align the fasteners with the belt ends. This involves positioning the fasteners so that they are evenly spaced and centered on the belt. Proper alignment is crucial for ensuring a strong, even connection that can withstand the operational stresses of the conveyor system. - Securing the Fasteners:
Once the fasteners are aligned, they are secured to the belt ends using specialized tools. For mechanical fasteners, this typically involves using a hammer or a press to drive the fasteners into the belt material. For splicing, the belt ends are treated with adhesives or heat to create a seamless bond. - Connecting the Belt Ends:
The final step is to connect the belt ends. This involves interlocking the fasteners or aligning the spliced sections to form a continuous loop. Once the connection is secure, the belt is tensioned and aligned on the conveyor system.
Importance in Conveyor Systems
Belt lacing joints play a crucial role in the overall performance and reliability of conveyor systems. Here are some key reasons why they are so important:
1. Ensuring Belt Integrity:
Belt lacing joints are essential for maintaining the integrity of the conveyor belt. A strong, reliable joint ensures that the belt can withstand the operational stresses of the conveyor system without failing. This is particularly important in applications where the belt is subjected to heavy loads, high speeds, or abrasive materials.
2. Facilitating Maintenance and Repairs:
Belt lacing joints make it easy to remove and replace the conveyor belt for maintenance and repairs. Mechanical fasteners, in particular, allow the belt to be quickly taken on and off the conveyor system, minimizing downtime and reducing the overall cost of maintenance. This is especially important in industries where conveyor systems are critical to the production process and any downtime can result in significant losses.
3. Enhancing Conveyor Performance:
A properly installed belt lacing joint ensures that the conveyor belt runs smoothly and efficiently. Misaligned or poorly secured joints can cause the belt to track improperly, leading to uneven wear, material spillage, and increased energy consumption. By ensuring a strong, even connection, belt lacing joints help to optimize the performance of the conveyor system.
4. Increasing Belt Lifespan:
Properly installed belt lacing joints can significantly increase the lifespan of the conveyor belt. By preventing premature wear and ensuring that the belt runs smoothly, these joints help to extend the operational life of the belt, reducing the need for frequent replacements and lowering the overall cost of ownership.
5. Providing Flexibility and Versatility:
Belt lacing joints provide flexibility and versatility in conveyor system design and operation. They allow for easy installation and removal of the belt, making it possible to quickly adapt the conveyor system to changing production needs. This is particularly important in industries where production requirements can vary widely and the ability to quickly change belts is a key advantage.
6. Improving Safety:
Ensuring that the conveyor belt is securely joined is critical for maintaining a safe working environment. Loose or poorly secured belts can pose a significant safety risk, potentially leading to accidents and injuries. Belt lacing joints help to prevent these risks by ensuring that the belt remains securely connected at all times.
7. Supporting Efficient Material Handling:
In industries such as mining, agriculture, and manufacturing, efficient material handling is essential for maintaining productivity and profitability. Belt lacing joints play a key role in ensuring that materials are transported smoothly and efficiently along the conveyor system, helping to optimize the overall efficiency of the production process.
How about Flexco Belt Fasteners
In industrial conveyor systems, ensuring the integrity and reliability of belt splicing is crucial for maintaining efficient operations. Flexco belt fasteners are renowned for their robust design and ease of installation, making them an ideal choice for various applications, including use in belt scales. This section provides an introduction to Flexco belt fasteners and highlights the advantages of using these fasteners in belt scales.
Introduction to Flexco Belt Fasteners
Flexco has been a leading provider of conveyor belt fasteners and splicing solutions for over a century. Their extensive range of belt fasteners is designed to meet the needs of different industries, from mining and quarrying to food processing and package handling. Flexco belt fasteners are engineered to provide secure, durable, and efficient splices, ensuring that conveyor systems run smoothly and reliably.
The Flexco belt fasteners product line includes several popular models, such as the Alligator® Ready Set™ Staple Fastening System, the Clipper® Wire Hook Fastening System, and the Rivet Hinged Fastening System. Each of these fasteners is tailored to specific applications and belt types, offering unique benefits and features.
- Alligator® Ready Set™ Staple Fastening System: This system is designed for quick and easy installation, using a single tool to install a continuous strip of fasteners across the belt end. The Alligator® system is suitable for a wide range of light- to medium-duty applications, providing a strong and flexible splice that can withstand the demands of various operating conditions.
- Clipper® Wire Hook Fastening System: Known for its low-profile design, the Clipper® system uses individual wire hooks to create a smooth, seamless splice. This fastening system is ideal for applications that require frequent belt adjustments or replacements, such as in the food processing and packaging industries.
- Rivet Hinged Fastening System: The Rivet Hinged system is built for heavy-duty applications, offering unmatched strength and durability. Self-setting rivets penetrate the belt and the fastener plate, creating a secure and permanent splice. This system is particularly well-suited for mining, quarrying, and other demanding environments where belts are subject to heavy loads and harsh conditions.
Advantages of Using Flexco Fasteners in Belt Scales
Belt scales are essential for measuring the flow rate and total quantity of material transported on conveyor belts. Accurate and reliable belt scale system depend on maintaining the integrity of the conveyor belt, making the choice of belt fasteners critically important. Flexco belt fasteners offer several advantages when used in conjunction with belt scales:
Maintaining Belt Integrity: Flexco belt fasteners are designed to create strong and durable splices that maintain the integrity of the conveyor belt. This is crucial for belt scales, as any disruption in the belt’s surface can affect the accuracy of weight measurements. By providing secure and seamless splices, Flexco fasteners ensure that the belt scale can deliver precise and consistent readings.
Minimizing Downtime: One of the key advantages of using Flexco fasteners is their ease of installation and maintenance. Quick and straightforward installation reduces downtime during belt repairs or replacements, ensuring that conveyor systems and belt scales remain operational. This efficiency is particularly important in industries where continuous production is critical, as it minimizes disruptions and maintains productivity.
Durability and Longevity: The robust construction of Flexco belt fasteners ensures that they can withstand the rigors of industrial environments. This durability is essential for maintaining the performance of belt scales, as it reduces the need for frequent repairs or replacements. By using Flexco fasteners, companies can extend the lifespan of their conveyor belts and belt scales, resulting in lower maintenance costs and improved reliability.
Consistent Belt Tracking: Proper belt tracking is vital for the accuracy of belt scales. Misaligned belts can lead to incorrect weight measurements and operational inefficiencies. Flexco belt fasteners are designed to maintain consistent belt tracking, ensuring that the conveyor belt runs smoothly and stays aligned. This consistency helps to ensure accurate readings from the belt scale and reduces the risk of errors.
Adaptability to Different Belt Types: Flexco offers a wide range of fasteners that are compatible with various belt types and thicknesses. This adaptability allows for the use of Flexco fasteners in different belt scale applications, whether in light-duty or heavy-duty environments. The ability to customize the splicing solution to the specific needs of the conveyor system ensures optimal performance and accuracy of the belt scale.
Improved Safety: Safety is a critical concern in any industrial setting. Flexco belt fasteners are designed with safety in mind, featuring rounded edges and secure fastening mechanisms that reduce the risk of injury during installation and maintenance. Additionally, the reliability of Flexco fasteners minimizes the likelihood of belt failures and accidents, contributing to a safer working environment.
Cost-Effectiveness: While the initial investment in high-quality belt fasteners may be higher, the long-term benefits far outweigh the costs. Flexco fasteners help reduce maintenance expenses, minimize downtime, and extend the life of conveyor belts and belt scales. These cost savings, combined with the fasteners’ durability and performance, make Flexco belt fasteners a cost-effective solution for businesses looking to optimize their conveyor operations.
Enhanced Performance in Harsh Environments: Conveyor systems in industries such as mining and quarrying often operate in harsh conditions, where belts are exposed to abrasive materials, extreme temperatures, and heavy loads. Flexco belt fasteners are engineered to perform reliably in these environments, maintaining their strength and effectiveness despite challenging conditions. This resilience ensures that belt scales continue to function accurately, even in the most demanding settings.
The Key of Belt Scale
Types of Conveyor Belt Splices
In the realm of conveyor systems, the integrity and reliability of the conveyor belt are paramount. One of the key aspects ensuring the seamless operation of a conveyor belt is the method used to splice it. Various splicing methods are available, each with its own set of advantages and disadvantages. This section provides an overview of different splicing methods and examines the benefits and drawbacks of each type.
Overview of Different Splicing Methods
Conveyor belt splicing is the process of joining two ends of a conveyor belt to make it endless. The choice of splicing method depends on the type of belt, the working conditions, and the specific requirements of the application. Here are the most common splicing methods:
1. Mechanical Splicing:
Mechanical splicing involves using metal or plastic fasteners to join the belt ends. These fasteners are inserted into the belt material and then interlocked to form a continuous loop. Common types of mechanical splicing include alligator clips, hinged fasteners, and plate fasteners.
2. Vulcanized Splicing:
Vulcanized splicing is a process where heat, pressure, and chemicals are applied to the belt ends to create a seamless joint. This method can be done in two ways: hot vulcanization and cold vulcanization. Hot vulcanization uses heat and pressure to bond the belt ends, while cold vulcanization uses a chemical bonding agent.
3. Cold Bonding:
Cold bonding, or chemical bonding, involves the use of adhesives to join the belt ends. This method does not require heat or special equipment, making it a convenient option for many applications. The adhesive is applied to the belt ends, which are then pressed together until the bond is secure.
4. Scarfed Splicing:
Scarfed splicing involves cutting the belt ends at an angle and overlapping them before bonding. This method increases the surface area of the splice, providing a stronger and more durable joint. Scarfed splicing can be done using mechanical fasteners or vulcanization.
5. Finger Splicing:
Finger splicing is a type of vulcanized splice where the belt ends are cut into a series of fingers, which are then interlocked and bonded. This method provides a strong and flexible splice that is less likely to fail under high tension.
Benefits and Drawbacks of Each Splicing Type
Each splicing method has its own set of advantages and disadvantages. Understanding these can help in selecting the most appropriate method for a given application.
1. Mechanical Splicing:
Benefits:
- Ease of Installation: Mechanical splicing is quick and easy to install, requiring minimal special tools or equipment. This makes it ideal for on-site repairs and temporary splices.
- Versatility: Mechanical splices can be used on a wide range of belt types and materials, making them suitable for various applications.
- Reusability: Some mechanical fasteners can be removed and reused, providing a cost-effective solution for short-term or temporary needs.
Drawbacks:
- Reduced Strength: Mechanical splices are generally not as strong as vulcanized splices, making them less suitable for high-tension applications.
- Potential for Damage: The metal or plastic fasteners can cause damage to the belt and other conveyor components, leading to increased maintenance needs.
- Bulkiness: Mechanical splices can be bulkier than other types, which may cause issues with belt tracking and smooth operation.
2. Vulcanized Splicing:
Benefits:
- High Strength: Vulcanized splices are very strong and durable, making them ideal for high-tension and heavy-duty applications.
- Seamless Joint: The seamless joint created by vulcanization reduces the risk of failure and ensures smooth belt operation.
- Long Lifespan: Vulcanized splices typically have a longer lifespan than mechanical splices, reducing the need for frequent replacements.
Drawbacks:
- Complex Process: Vulcanized splicing requires specialized equipment and expertise, making it more complex and time-consuming to install.
- Higher Cost: The materials and labor required for vulcanized splicing can be more expensive than other methods.
- Environmental Sensitivity: Vulcanized splices can be sensitive to environmental factors such as temperature and humidity, which may affect their performance.
3. Cold Bonding:
Benefits:
- Simplicity: Cold bonding is relatively simple and does not require heat or special equipment, making it easy to perform on-site.
- Flexibility: This method provides a flexible splice that can accommodate belt movement and bending.
- Cost-Effective: Cold bonding can be a more cost-effective option compared to vulcanized splicing, especially for smaller or less critical belts.
Drawbacks:
- Lower Strength: Cold-bonded splices are generally not as strong as vulcanized splices, making them less suitable for high-tension applications.
- Bonding Quality: The quality of the bond can be affected by factors such as adhesive quality and application technique, potentially leading to splice failure.
- Limited Durability: Cold-bonded splices may have a shorter lifespan compared to vulcanized splices, requiring more frequent maintenance and replacement.
4. Scarfed Splicing:
Benefits:
- Increased Surface Area: The angled cut of scarfed splices increases the bonding surface area, providing a stronger and more durable joint.
- Reduced Stress Concentration: The overlap design helps to distribute stress more evenly, reducing the risk of splice failure.
- Flexibility: Scarfed splices offer flexibility, making them suitable for belts that need to navigate curves and pulleys.
Drawbacks:
- Complex Installation: The precise cutting and alignment required for scarfed splicing can make it more complex and time-consuming to install.
- Specialized Equipment: Scarfed splicing may require specialized equipment and expertise, increasing the installation cost.
- Potential for Misalignment: Improper alignment during installation can lead to uneven stress distribution and premature splice failure.
5. Finger Splicing:
Benefits:
- High Strength: Finger splices provide a very strong and reliable joint, suitable for high-tension applications.
- Flexibility: The interlocking fingers offer flexibility, allowing the belt to bend and flex without compromising the splice integrity.
- Smooth Operation: The seamless design of finger splices ensures smooth belt operation, reducing the risk of catching or snagging.
Drawbacks:
- Labor-Intensive: Finger splicing is labor-intensive and requires precise cutting and alignment, making it more time-consuming to install.
- Specialized Skills: This method requires specialized skills and equipment, potentially increasing the cost and complexity of the installation process.
- Environmental Factors: Like vulcanized splices, finger splices can be sensitive to environmental conditions, which may affect their performance and longevity.
Why choose Belt Scale
Benefits of Using Belt Scales
In the world of industrial operations, accurate measurement and control of material flow are crucial for maintaining efficiency and productivity. Belt scales are integral tools that help achieve these goals by providing precise measurements of the material being transported on conveyor belts. This section explores the benefits of using belt scales, focusing on improved accuracy in material handling and enhanced efficiency and productivity.
Improved Accuracy in Material Handling
Accurate measurement is essential in various industries to ensure that processes run smoothly and that resources are used efficiently. Belt scales offer several advantages in terms of accuracy in material handling:
1. Real-Time Monitoring:
Belt scales provide real-time data on the amount of material being transported. This immediate feedback allows operators to make quick adjustments to the conveyor system, ensuring that the correct amount of material is being moved. Real-time monitoring helps in maintaining consistent production rates and reduces the risk of overloading or underloading the conveyor.
2. Precision Measurement:
Modern belt scales are equipped with advanced sensors and technology that deliver highly precise measurements. This precision is crucial for industries such as mining, aggregate, and food processing, where even small discrepancies in material measurement can lead to significant financial losses or product quality issues.
3. Consistent Product Quality:
In industries where the quality of the end product depends on the precise amount of material used, belt scales ensure consistency. For example, in the food processing industry, maintaining the exact proportion of ingredients is vital for product quality. Belt scales help in achieving this by providing accurate weight measurements of the ingredients being conveyed.
4. Inventory Management:
Accurate measurement of materials is also essential for effective inventory management. Belt scales provide detailed data on the amount of material entering and leaving the production process, helping businesses maintain optimal inventory levels. This accuracy prevents stockouts and overstock situations, leading to better resource utilization and cost savings.
5. Regulatory Compliance:
Many industries are subject to strict regulations regarding material handling and reporting. Belt scales help businesses comply with these regulations by providing accurate and verifiable data. This compliance is particularly important in industries such as mining, where accurate reporting of material extracted and processed is mandatory.
Enhanced Efficiency and Productivity
Belt scales contribute significantly to the efficiency and productivity of industrial operations. Here are some ways in which they achieve this:
1. Optimized Conveyor Performance:
By providing precise measurements, belt scales enable operators to optimize the performance of conveyor systems. Operators can adjust the speed and load of the conveyor to ensure that it operates at peak efficiency. This optimization reduces energy consumption and minimizes wear and tear on the equipment, leading to longer service life and lower maintenance costs.
2. Reduced Material Waste:
Accurate measurement of materials helps in reducing waste. Belt scales ensure that the exact amount of material required for the production process is delivered, minimizing excess and reducing waste. This efficiency is crucial in industries where raw materials are costly or scarce.
3. Streamlined Production Processes:
Belt scales integrate seamlessly with other automated systems, streamlining the production process. They can be linked to control systems that adjust conveyor speed and load based on real-time data. This integration ensures a smooth and continuous flow of materials, reducing bottlenecks and increasing overall productivity.
4. Data-Driven Decision Making:
The data collected by belt scales can be analyzed to identify trends and patterns in material handling. This analysis provides valuable insights that can be used to improve processes, reduce costs, and increase efficiency. Data-driven decision-making allows businesses to adapt quickly to changes in demand or production conditions.
5. Enhanced Operational Control:
Belt scales provide operators with greater control over the production process. With accurate and timely data, operators can make informed decisions to adjust operations as needed. This control is particularly important in dynamic environments where material flow can vary significantly.
6. Cost Savings:
The combined benefits of improved accuracy and enhanced efficiency translate into significant cost savings for businesses. Reduced waste, optimized equipment performance, and better inventory management all contribute to lower operational costs. Additionally, the ability to comply with regulatory requirements without incurring fines further enhances cost savings.
7. Scalability:
Belt scales are scalable solutions that can be adapted to different sizes and types of conveyor systems. This scalability makes them suitable for a wide range of applications, from small-scale operations to large industrial facilities. Businesses can start with basic belt scale systems and expand them as their needs grow.
8. Environmental Benefits:
By optimizing material handling and reducing waste, belt scales also contribute to environmental sustainability. Efficient use of resources minimizes the environmental impact of industrial operations. Additionally, accurate measurement and reporting help businesses adhere to environmental regulations and standards.
FAQS about Belt Scale
Cleaning a PU (polyurethane) belt requires specific steps to ensure its longevity and performance. Here’s a guide on how to effectively clean a PU belt:
Regular Cleaning: Use a soft brush or cloth to remove loose debris and particles from the belt surface. This prevents buildup and keeps the belt running smoothly.
Washing: For more thorough cleaning, use warm water and a mild detergent. Apply the solution with a sponge or cloth, scrubbing gently to avoid damaging the belt. Avoid harsh chemicals that could degrade the PU material.
Rinsing: After scrubbing, rinse the belt thoroughly with clean water to remove any soap residue.
Drying: Allow the belt to air dry completely before restarting the conveyor. Avoid direct sunlight or high heat, as this can cause the PU material to degrade.
Inspection: Regularly inspect the belt for signs of wear or damage. Address any issues promptly to prevent further deterioration. By following these steps, you can maintain the cleanliness and efficiency of your PU conveyor belt, ensuring its long-term reliability and performance.
Belt cleaners are devices installed on conveyor systems to remove material buildup from the conveyor belt. They are essential for maintaining the efficiency, safety, and longevity of the conveyor system. Belt cleaners are typically divided into two main categories:
Primary Cleaners: Installed at the head pulley, primary cleaners remove large debris from the belt. They are the first line of defense against material carryback.
Secondary Cleaners: Positioned further down the conveyor line, secondary cleaners remove finer particles that the primary cleaner might miss. They ensure a more thorough cleaning of the belt surface. Belt cleaners can be made from various materials, including polyurethane, rubber, and tungsten carbide, each selected based on the specific needs of the application. Proper installation and maintenance of belt cleaners are crucial for optimizing conveyor performance and reducing maintenance costs.
Belt scrapers are made from a variety of materials designed to meet the demands of different conveyor systems and material types:
Polyurethane: A flexible and durable material that resists abrasion and is suitable for a wide range of applications.
Rubber: Used for its elasticity and impact resistance, making it ideal for primary scrapers handling large debris.
Tungsten Carbide: Known for its hardness and wear resistance, tungsten carbide is used in secondary scrapers to remove fine particles and provide a clean belt surface.
Stainless Steel: Utilized in food-grade applications due to its corrosion resistance and ability to withstand cleaning agents. Choosing the right material depends on factors such as the type of material being conveyed, the operating environment, and the specific cleaning requirements of the conveyor system.
To clean a conveyor belt, you can use a variety of tools and methods depending on the type of belt and the material it transports. Here are some common options:
Scrapers: Install primary and secondary belt scrapers to remove large and fine debris. These can be made of polyurethane, rubber, or tungsten carbide, depending on the application.
Brushes: Use rotating or stationary brushes to sweep off finer particles from the belt surface.
Wash Stations: Employ water jets or steam cleaners for belts handling sticky or wet materials. Adding cleaning agents can enhance the effectiveness.
Vacuum Systems: Implement vacuum cleaners to remove dust and fine particles without water.
Manual Cleaning: Use cloths, sponges, or soft brushes for detailed manual cleaning, especially in hard-to-reach areas. Regular cleaning not only maintains the belt’s efficiency but also extends its lifespan by preventing material buildup and reducing wear.
Last Updated on June 12, 2024 by Jordan Smith
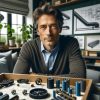
Jordan Smith, a seasoned professional with over 20 years of experience in the conveyor system industry. Jordan’s expertise lies in providing comprehensive solutions for conveyor rollers, belts, and accessories, catering to a wide range of industrial needs. From initial design and configuration to installation and meticulous troubleshooting, Jordan is adept at handling all aspects of conveyor system management. Whether you’re looking to upgrade your production line with efficient conveyor belts, require custom conveyor rollers for specific operations, or need expert advice on selecting the right conveyor accessories for your facility, Jordan is your reliable consultant. For any inquiries or assistance with conveyor system optimization, Jordan is available to share his wealth of knowledge and experience. Feel free to reach out at any time for professional guidance on all matters related to conveyor rollers, belts, and accessories.