Enhancing Efficiency with Superior Belt Cleaners
Belt cleaners are essential for maintaining efficient conveyor operations by preventing material carryback, which can cause various operational issues. Belt cleaners are designed to keep the conveyor belt clean, reducing downtime and maintenance costs. There are different types of belt cleaners, including primary and secondary cleaners, each serving a specific role. Primary belt cleaners are installed at the head pulley and remove the bulk of the material, while secondary cleaners are positioned further along the conveyor to eliminate any remaining residues. These belt cleaners play a crucial role in ensuring the smooth and efficient functioning of conveyor systems across various industries, such as mining, cement, and recycling.
Comprehensive Solutions for Belt Cleaners
Overview of Belt Cleaners for Various Industries
Belt cleaners are an essential component in numerous industries, providing vital maintenance and efficiency improvements for conveyor systems. These devices are designed to remove residual material from conveyor belts, ensuring smooth operation and minimizing downtime. Different industries, such as mining, cement, and recycling, have specific requirements and challenges that belt cleaners can address effectively.
Belt Cleaners in the Mining Industry
The mining industry is one of the most demanding environments for conveyor belt systems. The abrasive and heavy nature of mined materials can quickly wear down belts, leading to frequent maintenance and replacements. Belt cleaners play a crucial role in extending the lifespan of conveyor belts by removing debris and preventing material buildup.
In mining, the challenges include handling large volumes of bulk material, dealing with abrasive particles, and maintaining continuous operations. Effective belt cleaners in this sector need to be robust and capable of handling these harsh conditions. Primary belt cleaners, typically made from high-grade polyurethane or carbide-tipped blades, are used to remove the bulk of the material. Secondary belt cleaners, often positioned further along the conveyor, provide additional cleaning to ensure that even the smallest particles are removed.
Tailored Belt Cleaning Solutions for Mining
To address the unique operational needs of the mining industry, customized belt cleaning solutions are often necessary. This can include selecting the right type of cleaner, adjusting blade tension, and ensuring proper alignment with the belt. Regular maintenance and inspection of belt cleaners are also crucial to prevent excessive wear and tear, thereby reducing downtime and maintaining productivity.
Belt Cleaners in the Cement Industry
The cement industry presents a different set of challenges for conveyor belt systems. The fine, powdery nature of cement can cause significant issues with material buildup on belts and other equipment. Belt cleaners are essential to prevent clogging and ensure smooth transportation of cement through the production process.
In this industry, the primary concerns include managing dust, maintaining equipment cleanliness, and ensuring precise material handling. Belt cleaners must be effective at removing fine particles without damaging the belt surface. High-performance urethane or composite blade cleaners are commonly used in this setting to achieve optimal results.
Tailored Belt Cleaning Solutions for Cement Production
Custom belt cleaning solutions for the cement industry often involve integrating dust suppression systems and selecting cleaners that can withstand the fine, abrasive nature of cement. Regular inspections and adjustments are necessary to maintain the effectiveness of belt cleaners and prevent excessive material buildup.
Belt Cleaners in the Recycling Industry
The recycling industry relies heavily on conveyor systems to transport a variety of materials, from plastics to metals and paper. These materials can vary significantly in size, shape, and consistency, posing unique challenges for belt cleaning.
In recycling facilities, belt cleaners must be versatile and adaptable to handle the diverse range of materials. The main challenges include preventing cross-contamination, managing varying material types, and ensuring efficient material flow. Effective belt cleaners in this sector are often modular, allowing for easy adjustments and replacements as needed.
Tailored Belt Cleaning Solutions for Recycling
To address the specific needs of the recycling industry, tailored belt cleaning solutions might include multi-stage cleaning systems, where primary and secondary cleaners work in tandem to ensure thorough material removal. Additionally, selecting cleaners with interchangeable blades can provide flexibility to handle different types of materials efficiently.
The Importance of Regular Maintenance and Inspection
Regardless of the industry, regular maintenance and inspection of belt cleaners are vital to ensure their optimal performance. Over time, even the best belt cleaners can experience wear and tear, reducing their effectiveness. Regularly checking for signs of wear, adjusting blade tension, and replacing worn-out components can help maintain the efficiency of belt cleaning systems.
Innovations in Belt Cleaner Technology
Advancements in belt cleaner technology continue to improve their efficiency and durability. Innovations such as self-adjusting tensioners, enhanced blade materials, and modular designs are making belt cleaners more effective and easier to maintain. These improvements help industries reduce downtime, increase productivity, and lower maintenance costs.
Innovative Conveyor Belt Cleaners
Introduction to Conveyor Belt Wiper Blades and Their Purpose
In the world of material handling, maintaining clean conveyor belts is crucial for efficient and safe operations. One of the essential tools in achieving this is the conveyor belt wiper blade. Conveyor belt wiper blades, commonly referred to as belt cleaners, play a significant role in removing excess material and debris from conveyor belts. They ensure the smooth operation of the conveyor system by preventing material build-up, which can lead to various operational issues such as belt misalignment, increased wear and tear, and even potential breakdowns.
Key Features of Effective Wiper Blades
Effective conveyor belt wiper blades are designed with specific features that make them highly efficient in cleaning and maintaining the conveyor system. Here are some key features to look for in high-quality wiper blades:
- Durable Materials: Wiper blades are often exposed to harsh conditions, including abrasive materials and extreme temperatures. Therefore, they need to be made from durable materials such as polyurethane, which offers excellent resistance to wear and tear.
- Optimal Blade Design: The design of the wiper blade is crucial for its effectiveness. A good blade will have a flexible yet firm edge that maintains consistent contact with the belt, ensuring thorough cleaning without damaging the belt surface.
- Adjustability: Effective wiper blades should be adjustable to maintain optimal contact with the belt as it wears down over time. This adjustability extends the blade’s lifespan and ensures consistent cleaning performance.
- Compatibility: Wiper blades should be compatible with various conveyor systems and easy to install. This flexibility allows for seamless integration into existing systems without requiring extensive modifications.
- Easy Maintenance: Regular maintenance is essential for the longevity of wiper blades. High-quality blades are designed for easy maintenance, allowing quick inspections, adjustments, and replacements.
How Conveyor Belt Wiper Blades Enhance the Cleaning Process and Improve Overall System Efficiency
Conveyor belt wiper blades are instrumental in enhancing the cleaning process and improving the overall efficiency of conveyor systems. Here’s how they achieve this:
Enhanced Cleaning Efficiency
By effectively removing excess material from the conveyor belt, wiper blades prevent material build-up that can lead to operational inefficiencies. Clean belts minimize the risk of material spillage and ensure that the conveyor system operates smoothly without interruptions. This efficiency is particularly important in industries such as mining, construction, and agriculture, where the handling of bulk materials is common.
Reduced Maintenance Costs
Regular use of high-quality conveyor belt wiper blades can significantly reduce maintenance costs. By preventing material build-up and reducing wear and tear on the belt, wiper blades extend the lifespan of both the belt and other conveyor components. This reduction in maintenance needs translates to lower operational costs and less downtime for repairs.
Improved Safety
Safety is a critical concern in any material handling operation. Conveyor belt wiper blades enhance safety by ensuring that belts remain clean and free of debris, reducing the risk of accidents caused by material spillage or belt slippage. A clean belt also improves visibility, allowing operators to identify and address potential issues promptly.
Enhanced Productivity
A well-maintained conveyor system operates more efficiently, leading to increased productivity. Conveyor belt wiper blades contribute to this by ensuring that the belt remains clean and functions optimally. This continuous cleaning action helps maintain a steady flow of materials, reducing delays and maximizing throughput.
Environmental Benefits
In addition to operational benefits, conveyor belt wiper blades also offer environmental advantages. By minimizing material spillage and reducing the need for frequent cleaning with water or chemicals, wiper blades contribute to a more sustainable operation. This reduction in water and chemical use is particularly beneficial in industries where environmental regulations are stringent.
Versatility and Adaptability
Modern conveyor belt wiper blades are designed to be versatile and adaptable to various conveyor systems. This adaptability ensures that they can be used across different industries and applications, providing a consistent and reliable cleaning solution. Whether used in mining, food processing, or manufacturing, wiper blades are essential components for maintaining clean and efficient conveyor systems.
How about The Role of Belt Cleaners in Belt Cleaning Systems
Belt Fasteners and Their Significance in Conveyor Systems
Belt fasteners play a crucial role in maintaining the integrity and functionality of conveyor systems. These components are used to join the ends of conveyor belts together, ensuring a continuous loop that allows for efficient material transport. The significance of belt fasteners extends beyond merely connecting the belt; they are integral to the overall performance and reliability of the conveyor system.
In the context of belt cleaning systems, the role of belt fasteners becomes even more pronounced. Properly installed belt fasteners help maintain the alignment and tension of the conveyor belt, which are critical factors in ensuring the effectiveness of belt cleaners. Misaligned or loose belts can lead to uneven wear and reduced cleaning efficiency, ultimately impacting the productivity and longevity of the conveyor system.
How Belt Fasteners Contribute to the Effectiveness of Belt Cleaners
Belt fasteners contribute significantly to the effectiveness of belt cleaners by providing a stable and secure connection between the ends of the conveyor belt. This stability is essential for the proper operation of belt cleaners, which rely on consistent contact with the belt surface to remove residual material effectively. Here are a few ways belt fasteners enhance the performance of belt cleaners:
- Maintaining Belt Alignment: Properly installed belt fasteners ensure that the belt remains aligned as it moves over the conveyor system. This alignment is crucial for belt cleaners to maintain consistent pressure and contact with the belt surface, thereby enhancing their cleaning efficiency.
- Ensuring Belt Tension: Belt fasteners help maintain the appropriate tension in the conveyor belt. Adequate tension prevents slippage and sagging, which can cause gaps and uneven cleaning. Consistent tension allows belt cleaners to function optimally, removing material buildup and reducing wear on the belt.
- Facilitating Smooth Belt Movement: Belt fasteners contribute to the smooth movement of the conveyor belt by providing a seamless connection. This smooth movement is essential for belt cleaners to operate effectively without encountering interruptions or obstacles that could impair their performance.
- Reducing Downtime: Well-maintained belt fasteners reduce the risk of belt failures and breakdowns. This reliability minimizes downtime for maintenance and repairs, ensuring that belt cleaners can operate continuously and efficiently.
Types of Belt Fasteners and Their Specific Applications
There are several types of belt fasteners, each designed to meet specific operational needs and conditions. The choice of belt fasteners depends on factors such as the type of material being transported, the operating environment, and the specific requirements of the conveyor system. Here are some common types of belt fasteners and their applications:
Mechanical Belt Fasteners
Mechanical belt fasteners are widely used due to their ease of installation and versatility. These fasteners are typically made of metal and are designed to be installed quickly without the need for specialized tools. Mechanical belt fasteners are ideal for applications where rapid belt repairs and replacements are necessary, such as in mining, quarrying, and construction industries.
- Bolt Hinged Fasteners: These fasteners consist of individual plates secured by bolts, allowing for a flexible connection that can withstand high tension and impact. They are commonly used in heavy-duty applications where the conveyor belt is subjected to rigorous conditions.
- Plate Fasteners: Plate fasteners feature overlapping plates that provide a secure and durable connection. They are suitable for medium to heavy-duty applications, offering a balance between strength and flexibility.
Vulcanized Belt Fasteners
Vulcanized belt fasteners involve chemically bonding the ends of the conveyor belt using heat and pressure. This method creates a seamless and permanent joint, offering superior strength and durability. Vulcanized fasteners are preferred in applications where a smooth belt surface is essential, such as in food processing, packaging, and manufacturing industries.
- Hot Vulcanization: Hot vulcanization uses heat and pressure to bond the belt ends, resulting in a strong and durable joint. This method is ideal for high-tension applications and environments where a smooth, continuous belt surface is required.
- Cold Vulcanization: Cold vulcanization uses a chemical adhesive to bond the belt ends without the need for heat. This method is suitable for applications where quick repairs are needed and where the use of heat is impractical.
Hinged Belt Fasteners
Hinged belt fasteners are designed for belts that require frequent adjustments or replacements. These fasteners feature a hinge mechanism that allows for easy opening and closing of the belt joint. Hinged fasteners are commonly used in applications where the conveyor belt needs to be regularly shortened or lengthened, such as in agricultural and recycling industries.
- Alligator Hinged Fasteners: Alligator hinged fasteners are made of metal and feature a flexible hinge design. They are easy to install and remove, making them ideal for applications where quick belt changes are necessary.
- Staple Hinged Fasteners: Staple hinged fasteners use metal staples to secure the belt ends. They provide a strong and flexible connection, suitable for medium-duty applications where frequent belt adjustments are required.
Effective Belt Cleaners: Materials and Design
Importance of High-Quality Belt Scraper Blades
In any conveyor system, the efficiency and longevity of operations heavily rely on the effectiveness of the belt cleaners. Belt cleaners are essential components designed to remove unwanted material from conveyor belts, preventing build-up that can lead to operational issues such as belt misalignment, increased wear and tear, and even potential system failures. High-quality belt scraper blades, a crucial type of belt cleaner, play a vital role in maintaining the cleanliness and efficiency of the conveyor system.
The importance of high-quality belt scraper blades cannot be overstated. They ensure that the conveyor belts remain free of debris and excess material, which in turn enhances the overall efficiency of the system. By effectively cleaning the belt surface, these scraper blades help reduce the risk of material spillage, minimize maintenance requirements, and extend the lifespan of the conveyor components. Investing in top-notch belt scraper blades is a proactive measure that saves time, reduces costs, and enhances productivity.
Different Materials Used for Belt Scraper Blades and Their Advantages
The materials used in the manufacturing of belt scraper blades are critical to their performance and durability. Different materials offer various benefits, making them suitable for specific applications and operating conditions. Here are some commonly used materials for belt scraper blades and their advantages:
- Polyurethane: Polyurethane is one of the most popular materials for belt scraper blades due to its excellent wear resistance and flexibility. It can withstand harsh conditions and abrasive materials, making it ideal for heavy-duty applications. Polyurethane blades are known for their ability to maintain a consistent edge, ensuring efficient cleaning over prolonged periods. Additionally, they are resistant to chemicals and can operate effectively in extreme temperatures.
- Carbide: Carbide blades are renowned for their exceptional hardness and durability. They are particularly suitable for applications involving highly abrasive materials, such as mining and quarrying. Carbide blades offer superior cutting and scraping capabilities, ensuring thorough cleaning even under the most demanding conditions. Their robustness reduces the frequency of replacements, thereby lowering maintenance costs.
- Stainless Steel: Stainless steel blades are highly resistant to corrosion, making them ideal for environments where moisture and corrosive substances are prevalent. They are commonly used in industries such as food processing and pharmaceuticals, where hygiene and cleanliness are paramount. Stainless steel blades provide effective cleaning while ensuring compliance with stringent sanitary standards.
- Composite Materials: Composite blades combine the benefits of multiple materials to deliver enhanced performance. These blades often feature a core material for strength and durability, coated with a wear-resistant outer layer. Composite blades offer a balance of flexibility, wear resistance, and cleaning efficiency, making them versatile for various applications.
How the Design of Scraper Blades Impacts Their Performance and Durability
The design of belt scraper blades significantly influences their performance and durability. A well-designed scraper blade ensures effective cleaning, reduces wear on the conveyor belt, and extends the blade’s lifespan. Key design aspects to consider include:
- Blade Profile: The profile of the scraper blade determines its contact with the conveyor belt. A blade with an optimal profile ensures consistent pressure and coverage across the belt surface, maximizing cleaning efficiency. Profiles can be straight, curved, or segmented, each offering unique benefits for specific applications.
- Edge Geometry: The geometry of the blade edge plays a crucial role in its scraping ability. Sharp edges provide precise cleaning, while rounded edges reduce the risk of damaging the belt. Some blades feature dual edges, allowing for reversible use and extended lifespan.
- Tensioning Mechanism: Effective belt cleaners require a reliable tensioning mechanism to maintain consistent contact with the belt. This mechanism can be spring-loaded, hydraulic, or pneumatic, each offering different levels of adjustability and control. Proper tensioning ensures optimal cleaning performance and reduces wear on both the blade and the belt.
- Mounting System: The mounting system of the scraper blade affects its stability and ease of maintenance. A robust mounting system minimizes blade movement and vibration, ensuring consistent cleaning. Quick-release or easy-access mounting systems facilitate blade replacement and maintenance, reducing downtime.
Belt Cleaners: A Solution for Challenging Conditions
Introduction to BMS Cleaners and Their Unique Features
BMS cleaners, or Belt Maintenance System cleaners, are specialized devices designed to tackle the rigorous demands of industrial conveyor systems operating under harsh conditions. These belt cleaners are engineered to provide robust, efficient, and reliable cleaning solutions, ensuring that conveyor belts remain free of material buildup and operate at peak efficiency. BMS cleaners are distinguished by their unique features, which make them particularly suited for challenging environments.
One of the defining characteristics of BMS cleaners is their construction from high-quality materials that withstand extreme temperatures, abrasive materials, and high levels of moisture. Typically made from stainless steel, high-grade polyurethane, and other durable composites, these cleaners are built to last. Their design often includes adjustable tensioners and modular components, allowing for easy installation, maintenance, and replacement.
Benefits of Using BMS Cleaners in Harsh Environments
The implementation of BMS cleaners in harsh environments offers numerous benefits, which contribute to the overall efficiency and longevity of conveyor systems. These advantages include:
- Enhanced Durability: BMS cleaners are designed to withstand the most extreme conditions, from high-temperature environments to abrasive materials like sand, gravel, and ores. Their robust construction ensures that they can operate effectively without frequent replacements or maintenance.
- Improved Cleaning Efficiency: The primary function of belt cleaning is to remove residual material from conveyor belts, preventing buildup that can cause belt misalignment, increased wear, and operational inefficiencies. BMS cleaners excel in this role, providing thorough cleaning that minimizes downtime and enhances productivity.
- Reduced Maintenance Costs: By maintaining cleaner belts and reducing material buildup, BMS cleaners help extend the lifespan of both the conveyor belts and the entire system. This leads to fewer repairs and replacements, ultimately lowering maintenance costs.
- Adaptability to Various Conditions: BMS cleaners are highly adaptable and can be customized to suit the specific needs of different industries. Whether dealing with wet, sticky materials or dry, abrasive substances, these cleaners can be adjusted to provide optimal performance.
- Safety Improvements: Cleaner conveyor belts mean fewer hazards associated with material spillage and buildup. This contributes to a safer working environment, reducing the risk of accidents and injuries.
Case Studies of Successful BMS Cleaner Implementations
Mining Industry: Copper Mine in Chile
A large copper mine in Chile faced significant challenges with material buildup on their conveyor belts. The abrasive nature of the copper ore, combined with the high humidity of the underground environment, caused frequent belt wear and operational disruptions. The mine implemented BMS cleaners to address these issues.
The BMS cleaners, equipped with carbide-tipped blades and robust tensioning systems, were able to withstand the harsh conditions and provide effective cleaning. The result was a significant reduction in material buildup, leading to smoother belt operation and fewer maintenance interruptions. The mine reported a 30% increase in belt lifespan and a 20% decrease in maintenance costs.
Cement Industry: Cement Plant in India
A cement plant in India struggled with the fine, powdery nature of cement, which caused persistent buildup on their conveyor belts. This buildup not only affected belt performance but also created dust hazards and increased the risk of fires. The plant decided to implement BMS cleaners to mitigate these issues.
The BMS cleaners used at the cement plant featured high-performance urethane blades and integrated dust suppression systems. These cleaners were able to effectively remove cement particles from the belts, reducing material buildup and dust generation. As a result, the plant saw a marked improvement in operational efficiency, with a significant reduction in downtime and maintenance needs.
Recycling Industry: Material Recovery Facility in Germany
A material recovery facility (MRF) in Germany faced unique challenges due to the diverse range of materials processed on their conveyor belts. From plastics and metals to paper and glass, the varying sizes and consistencies of the materials made effective belt cleaning difficult. The facility opted for BMS cleaners to improve their belt cleaning processes.
BMS cleaners, with their modular design and adjustable components, proved to be an ideal solution for the MRF. The cleaners were able to handle the diverse materials effectively, ensuring that the belts remained free of debris and operated efficiently. The facility reported improved material sorting accuracy and a reduction in belt wear, leading to cost savings and enhanced productivity.
Superior Belt Cleaners: Enhancing Conveyor Performance
Explanation of What Makes Superior Belt Cleaners Stand Out
In the realm of material handling, the effectiveness of belt cleaners is paramount to the smooth operation of conveyor systems. Superior cleaners belts are distinguished by their ability to efficiently remove unwanted material from conveyor belts, thereby preventing issues such as material build-up, belt misalignment, and system inefficiencies. Several factors contribute to making a belt cleaner superior:
- High-Quality Materials: Superior belt cleaners are constructed from robust materials such as polyurethane, carbide, and stainless steel. These materials offer excellent wear resistance, durability, and adaptability to various operating conditions, ensuring long-lasting performance.
- Innovative Design: The design of superior belt cleaners incorporates advanced features such as flexible yet firm edges, optimal blade profiles, and effective tensioning mechanisms. These design elements ensure consistent contact with the belt, thorough cleaning, and minimal wear on both the cleaner and the belt.
- Ease of Maintenance: Superior belt cleaners are designed for easy maintenance, allowing for quick inspections, adjustments, and replacements. Features such as quick-release mounting systems and adjustable tensioning mechanisms facilitate hassle-free upkeep, reducing downtime and operational costs.
- Customizability: The ability to customize belt cleaners to suit specific conveyor systems and operational needs is a hallmark of superior products. This adaptability ensures optimal performance across different industries and applications, making superior belt cleaners a versatile solution for material handling challenges.
Key Benefits: Increased Productivity, Reduced Maintenance Costs, and Improved Safety
The deployment of superior belt cleaners offers several key benefits that significantly enhance conveyor performance:
Increased Productivity
By effectively removing debris and excess material from conveyor belts, superior belt cleaners ensure that the system operates smoothly and without interruptions. Clean belts minimize the risk of material spillage and blockages, which can cause delays and reduce throughput. Consequently, the use of superior belt cleaners leads to increased productivity, allowing for a more efficient and consistent flow of materials.
Reduced Maintenance Costs
One of the most significant advantages of using superior belt cleaners is the reduction in maintenance costs. By preventing material build-up and reducing wear and tear on conveyor components, these cleaners extend the lifespan of both the belt and other system parts. This longevity translates to fewer replacements and repairs, resulting in lower maintenance expenses. Additionally, the ease of maintenance associated with superior belt cleaners further contributes to cost savings by minimizing downtime and labor costs.
Improved Safety
Safety is a critical concern in any material handling operation. Superior belt cleaners enhance safety by ensuring that conveyor belts remain clean and free of debris. This cleanliness reduces the risk of accidents caused by material spillage, belt slippage, or equipment malfunction. Furthermore, clean belts improve visibility, allowing operators to identify and address potential issues promptly. By maintaining a safer working environment, superior belt cleaners help prevent injuries and ensure compliance with safety regulations.
Industries That Benefit the Most from Superior Belt Cleaners
Several industries stand to gain significant advantages from the implementation of superior belt cleaners. These industries typically involve the handling of bulk materials and require efficient, reliable conveyor systems to maintain operational effectiveness. The following sectors benefit the most from superior belt cleaners:
Mining and Quarrying
The mining and quarrying industry deals with highly abrasive materials such as ores, minerals, and aggregates. Superior belt cleaners are essential in these environments to prevent material build-up, reduce wear on conveyor belts, and ensure efficient material handling. The durability and effectiveness of superior belt cleaners help maintain productivity and reduce the frequency of costly maintenance and downtime.
Agriculture
In agriculture, conveyor systems are used to transport a variety of bulk materials, including grains, seeds, and fertilizers. Superior belt cleaners help keep these conveyor systems running smoothly by removing debris and preventing material build-up. This ensures that agricultural products are handled efficiently, reducing the risk of contamination and spoilage.
Food Processing
The food processing industry requires stringent hygiene standards to ensure product safety and quality. Superior belt cleaners, particularly those made from stainless steel, are ideal for these applications due to their resistance to corrosion and ease of cleaning. By maintaining clean conveyor belts, these cleaners help prevent cross-contamination and ensure compliance with food safety regulations.
Manufacturing
Manufacturing industries rely on conveyor systems to move raw materials, components, and finished products through various stages of production. Superior belt cleaners enhance the efficiency of these systems by keeping belts free of debris and material build-up. This leads to smoother operations, reduced downtime, and increased productivity, ultimately contributing to the overall efficiency of the manufacturing process.
Recycling
The recycling industry handles a wide range of materials, including metals, plastics, and paper. Superior belt cleaners are crucial in these operations to prevent material build-up and ensure that conveyor systems operate efficiently. By maintaining clean belts, these cleaners help improve the sorting and processing of recyclable materials, contributing to more effective recycling operations.
Construction
In construction, conveyor systems are used to transport materials such as sand, gravel, and concrete. Superior belt cleaners play a vital role in keeping these systems running smoothly by removing excess material and preventing build-up. This ensures efficient material handling, reduces maintenance costs, and enhances the overall productivity of construction projects.
Power Generation
Power generation facilities, particularly those that use coal or biomass as fuel, rely on conveyor systems to transport these materials to processing and combustion units. Superior belt cleaners help maintain the efficiency of these conveyor systems by removing debris and preventing material build-up. This contributes to the smooth operation of power generation processes and reduces the risk of system failures.
FAQS about Belt Cleaners
Cleaning belts is essential for maintaining the efficiency and longevity of belt conveyors. Unclean belts can lead to material carryback, where leftover material adheres to the belt and is transported back along the return path. This carryback can cause several problems, including increased wear on the belt and conveyor components, potential belt mistracking, and accumulation of material around the conveyor system, which can create safety hazards and operational inefficiencies. Regular cleaning minimizes these risks, reduces maintenance costs, and ensures smooth and reliable operation of the conveyor system. Additionally, clean belts improve product quality by preventing cross-contamination and ensuring that only the intended material is transported.
A belt scraper is a specific type of belt cleaner used to remove residual material from the surface of a conveyor belt. It is typically mounted at the head pulley, where the belt discharges material, and is designed to scrape off any remaining debris. Belt scrapers come in different designs and materials, such as tungsten carbide or polyurethane, to suit various applications and belt types. Their primary purpose is to enhance the efficiency of the conveyor system by preventing carryback, which can cause wear and tear on the belt and other components, leading to increased maintenance costs and potential operational disruptions.
Cleaning a conveyor belt typically involves using belt cleaners, scrapers, or brushes to remove debris and material buildup. The process can be automated or manual, depending on the conveyor system and the type of material being transported. Automated cleaning systems include primary and secondary belt cleaners that are installed at various points along the conveyor. These cleaners scrape off material as the belt moves. Manual cleaning may involve using brushes, water, and cleaning agents to scrub the belt. Regular maintenance and inspections are crucial to ensure the cleaning mechanisms function effectively and to prevent any potential downtime caused by material buildup.
Belt cleaners are devices designed to remove material that sticks to the conveyor belt after the material has been discharged. These cleaners ensure that the belt remains clean, reducing the risk of material buildup, which can lead to operational issues. Belt cleaners come in various designs and configurations, including primary and secondary cleaners, and can be made from different materials like polyurethane, tungsten carbide, and stainless steel. Their primary function is to maintain the efficiency and longevity of the conveyor system by preventing material carryback and minimizing the need for manual cleaning.
Last Updated on July 15, 2024 by Jordan Smith
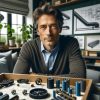
Jordan Smith, a seasoned professional with over 20 years of experience in the conveyor system industry. Jordan’s expertise lies in providing comprehensive solutions for conveyor rollers, belts, and accessories, catering to a wide range of industrial needs. From initial design and configuration to installation and meticulous troubleshooting, Jordan is adept at handling all aspects of conveyor system management. Whether you’re looking to upgrade your production line with efficient conveyor belts, require custom conveyor rollers for specific operations, or need expert advice on selecting the right conveyor accessories for your facility, Jordan is your reliable consultant. For any inquiries or assistance with conveyor system optimization, Jordan is available to share his wealth of knowledge and experience. Feel free to reach out at any time for professional guidance on all matters related to conveyor rollers, belts, and accessories.