Rubber Conveyor Belt Weight Calculation Methods and Chart
Rubber conveyor belt weight is essential for the design, operation, and maintenance of conveyor systems. Accurately measuring the weight of a conveyor belt helps in selecting the right belt for your specific application, ensuring optimal performance and longevity. The weight of a conveyor belt affects the load on the conveyor system, impacting energy consumption and wear and tear on mechanical components. Safety is another critical aspect, as knowing the exact weight can help prevent overloading and potential accidents. By using precise calculations and reliable tools, industries can ensure that their conveyor systems operate efficiently and safely, minimizing downtime and maintenance costs.
Rubber Conveyor Belt Weight Specification Standards PDF
Importance of Standardized Specifications for Conveyor Belts
Standardized specifications for conveyor belts play a pivotal role in ensuring the optimal performance, safety, and reliability of conveyor systems used in various industries. These specifications provide a comprehensive set of guidelines and requirements that manufacturers and users must adhere to, ensuring that the conveyor belts meet the necessary quality and performance standards.
One of the primary reasons standardized specifications are crucial is that they ensure consistency across different conveyor belt products. With standardized specifications, manufacturers can produce conveyor belts with uniform characteristics such as tensile strength, abrasion resistance, and load-carrying capacity. This uniformity is essential for industries that rely on conveyor belts to handle heavy loads and operate under challenging conditions.
Moreover, standardized specifications help in maintaining the safety of conveyor belt systems. By adhering to these guidelines, manufacturers can design and produce conveyor belts that minimize the risk of accidents and failures. For example, specifications related to the rubber conveyor belt weight ensure that the belts are strong enough to handle the intended loads without excessive stretching or breaking, which could lead to hazardous situations.
In addition to safety and consistency, standardized specifications also facilitate easier maintenance and replacement of conveyor belts. When conveyor belts conform to standard specifications, it becomes simpler to identify and procure the right replacement belts. This reduces downtime and ensures that the conveyor systems remain operational with minimal disruptions.
Overall, the importance of standardized specifications for conveyor belts cannot be overstated. They provide a framework that ensures the quality, safety, and reliability of conveyor belt systems, benefiting both manufacturers and end-users across various industries.
Guide to Accessing and Interpreting Conveyor Belt Specification Standards PDFs
Accessing and interpreting conveyor belt specification standards PDFs is essential for manufacturers, engineers, and users who need to ensure that their conveyor belts meet the required standards. These PDFs contain detailed information on the specifications, guidelines, and requirements that must be followed.
To access conveyor belt specification standards PDFs, one can visit the websites of standardization organizations such as the International Organization for Standardization (ISO), the American Society for Testing and Materials (ASTM), or other relevant industry bodies. These organizations often provide downloadable PDFs of the standards, which can be accessed either for free or for a fee.
When interpreting these specification standards PDFs, it is important to focus on key sections that provide information on the physical and mechanical properties of conveyor belts. For instance, sections detailing the rubber conveyor belt weight will provide insights into the weight per unit length or area of the belt. This information is crucial for determining the load-carrying capacity and overall performance of the conveyor belt.
Additionally, the specification standards PDFs will include sections on tensile strength, elongation, abrasion resistance, and other important properties. It is essential to thoroughly review these sections to understand how the conveyor belt is expected to perform under different conditions. The standards may also include testing methods and procedures that should be followed to verify the compliance of the conveyor belts with the specified requirements.
Furthermore, interpreting these standards requires a good understanding of the technical terminology and measurement units used in the documents. It may be helpful to consult with industry experts or seek guidance from professionals who are familiar with the standards to ensure accurate interpretation and application.
By accessing and correctly interpreting conveyor belt specification standards PDFs, manufacturers and users can ensure that their conveyor belts meet the necessary quality and performance standards, leading to improved safety, reliability, and efficiency of their conveyor systems.
How These Standards Help in Determining Accurate Belt Weights and Ensuring Compliance
Conveyor belt specification standards play a crucial role in determining the accurate weight of industrial rubber conveyor belt requirements. The rubber conveyor belt weight is a key parameter that influences the performance and suitability of the belt for specific applications.
One of the ways these standards help in determining accurate belt weights is by providing precise guidelines on the materials and construction of the conveyor belts. For example, the standards may specify the type and grade of rubber used, the thickness of the rubber layers, and the reinforcement materials such as fabric or steel cords. By following these guidelines, manufacturers can produce conveyor belts with consistent weights that meet the specified requirements.
The standards also include detailed formulas and methods for calculating the weight of conveyor belts. These calculations take into account factors such as the belt width, length, thickness, and the density of the materials used. By using these standardized formulas, manufacturers can accurately determine the weight of the conveyor belts, ensuring that they are suitable for the intended applications.
In addition to helping manufacturers determine the accurate weight of conveyor belts, these standards also ensure compliance with industry requirements. Compliance with the standards is often a prerequisite for certification and acceptance in various industries. By adhering to the specified requirements, manufacturers can demonstrate that their conveyor belts meet the necessary quality and performance standards.
Moreover, compliance with the standards helps in gaining the trust and confidence of customers and end-users. When customers know that the conveyor belts they are purchasing conform to recognized standards, they can be assured of the quality and reliability of the products. This is particularly important in industries where conveyor belts are subjected to heavy loads and harsh operating conditions.
Furthermore, ensuring compliance with the standards can help manufacturers avoid legal and regulatory issues. Non-compliance with industry standards can lead to penalties, recalls, and damage to the company’s reputation. By adhering to the standards, manufacturers can mitigate these risks and maintain a positive standing in the industry.
How Much Does a Rubber Conveyor Belt Weight in Lbs
The rubber conveyor belt weight is crucial for various industrial applications, as it impacts the efficiency and performance of the conveyor system. Several factors influence the weight of a conveyor belt, including material type, belt width, and construction. This section explores these factors in detail, providing insights into common conveyor belt weights in pounds and offering examples of typical weight ranges for various belt types.

Discussion on Common Conveyor Belt Weights in Pounds
The weight of a conveyor belt can vary significantly depending on its design and application. On average, a standard rubber conveyor belt can weigh anywhere from a few pounds to several hundred pounds per foot. With a conveyor belt weight calculator, easily determine the rubber conveyor belt weight per foot, simplifying transport planning for various belts. This wide range reflects the diversity of conveyor belt designs used across different industries.
For example, a lightweight conveyor belt used in food processing might weigh as little as 2-3 pounds per foot, while a heavy-duty mining conveyor belt can weigh upwards of 25 pounds per foot. The weight of a conveyor belt is often specified by its weight per unit length, typically in pounds per foot (lbs/ft).
Factors Affecting Weight in Lbs
Several factors influence the rubber conveyor belt weight:
Material Type
The type of material used in the construction of the conveyor belt is a significant determinant of its weight. Common materials include natural rubber, synthetic rubber, PVC, and other polymers. Rubber belts are generally heavier than their PVC counterparts due to the density of the rubber material.
- Natural Rubber Conveyor Belt: These belts are known for their durability and flexibility. They typically weigh more than synthetic options due to the density of natural rubber.
- Synthetic Rubber Belts: Often made from materials such as neoprene or nitrile, these belts are designed to offer similar durability with potentially reduced weight.
- PVC Belts: PVC (polyvinyl chloride) belts are lighter and often used in applications where weight is a critical factor.
Belt Width
The width of the conveyor belt is another critical factor affecting its weight. Wider belts naturally weigh more than narrower belts, assuming the same material and thickness. For instance, a 24-inch wide belt will weigh more per foot than a 12-inch wide belt made from the same material.

Belt Thickness and Ply
The thickness of the belt and the number of plies (layers) also play a crucial role in determining the rubber conveyor belt weight. A thicker belt with more plies will be heavier due to the additional material. Conveyor belts can range from a single ply to multiple plies, with each additional ply adding to the overall weight.
- Single Ply Belts: These are thinner and lighter, suitable for light-duty applications.
- Multi-Ply Belts: These are thicker and heavier, designed for heavy-duty applications and providing greater strength and durability.
Reinforcement and Construction
The type of reinforcement used in the belt’s construction can also affect its weight. Belts may be reinforced with materials such as steel cords, textile fabrics, or other fibers to enhance their strength and durability.
- Steel Cord Reinforcement: Steel-reinforced belts are among the heaviest, providing superior strength and durability for high-stress applications.
- Textile Fabric Reinforcement: These belts are lighter than steel-reinforced belts and are used in medium to heavy-duty applications.
Examples of Typical Weight Ranges for Various Belt Types
Here are some typical weight ranges for different types of conveyor belts:

Lightweight Belts
- Food Processing Belts: These belts are often made from lightweight materials like PVC or polyurethane. They typically weigh between 2-5 pounds per foot.
- Agricultural Belts: Used in farming equipment, these belts might weigh around 3-6 pounds per foot, depending on the material and design.
Medium-Weight Belts
- General Manufacturing Belts: These belts, made from synthetic rubber or a combination of materials, generally weigh between 6-10 pounds per foot.
- Package Handling Belts: Common in distribution centers, these belts weigh between 5-8 pounds per foot.
Heavy-Duty Belts
- Mining Belts: These heavy-duty belts, often reinforced with steel cords, can weigh between 15-30 pounds per foot, depending on the width and thickness.
- Construction Belts: Used in construction equipment, these belts typically weigh around 12-20 pounds per foot.
Rubber Conveyor Belt Weight Per Meter
Explanation of Weight Measurements in Metric Units (Per Meter)
Understanding the weight measurements of a rubber conveyor belt in metric units is essential for various industrial applications. The weight of a conveyor belt per meter is a crucial factor in determining its load-bearing capacity, installation requirements, and overall efficiency. The metric system, widely used in most parts of the world, provides a standardized way to measure and compare the weights of different conveyor belts.
The rubber conveyor belt weight is typically measured in kilograms per meter (kg/m). This measurement indicates the weight of the belt for every meter of its length. To calculate this weight, manufacturers consider several factors, including the thickness and density of the rubber, the type of reinforcement materials used, and the overall construction of the belt.
For example, a standard rubber conveyor belt might consist of multiple layers of rubber and reinforcement materials such as fabric or steel cords. Each layer contributes to the total weight of the belt. The thickness of these layers and the density of the rubber compound are critical parameters that affect the rubber conveyor belt weight. By standardizing these measurements, manufacturers can produce conveyor belts with consistent properties, ensuring they meet the specific requirements of different industries.
Additionally, knowing the rubber conveyor belt weight per meter helps in the design and engineering of conveyor systems. Engineers use this information to calculate the total weight that the conveyor structure needs to support, including the weight of the belt and the materials being transported. This calculation is vital for ensuring the structural integrity and safety of the conveyor system.
Conversion Examples from Foot to Meter Measurements
In regions where the imperial system is still in use, it’s often necessary to convert weight measurements from feet to meters. Understanding these conversions is essential for industries that operate globally and need to comply with different measurement standards.
To convert the weight of a rubber conveyor belt from feet to meters, one must first understand the conversion factor between these units of length. One meter is approximately equal to 3.28084 feet. Using this conversion factor, we can easily convert measurements from one unit to the other.
For instance, if a rubber conveyor belt weighs 15 pounds per foot, we can convert this to kilograms per meter using the following steps:
- Convert pounds to kilograms: Since 1 pound is approximately equal to 0.453592 kilograms, 15 pounds is approximately equal to 6.80388 kilograms.
- Convert feet to meters: Since 1 foot is approximately equal to 0.3048 meters, the weight per meter would be calculated by dividing the weight in kilograms by the conversion factor for length (3.28084).
Therefore, the weight per meter would be approximately 6.80388 kg / 3.28084 = 2.073 kg/m.
These conversion examples are crucial for ensuring accurate measurements and comparisons when working with international standards and specifications. By understanding and correctly applying these conversions, industries can maintain consistency and compliance in their operations.
Use Cases and Industry Standards for Metric Weight Measurements
The rubber conveyor belt weight per meter is a critical parameter in various use cases and is governed by industry standards to ensure quality and performance. Different industries have specific requirements for the weight and construction of conveyor belts, depending on the materials being transported and the operating conditions.
In the mining industry, for example, conveyor belts must be capable of carrying heavy loads of ore and rock. The rubber conveyor belt weight is a significant factor in determining the belt’s durability and load-carrying capacity. Heavier belts, constructed with multiple layers of reinforcement, can withstand the abrasive and heavy nature of the materials commonly transported in mining operations. Industry standards such as those set by the International Organization for Standardization (ISO) and the American Society for Testing and Materials (ASTM) provide guidelines for the acceptable weight and construction of conveyor belts used in mining.
In the manufacturing and logistics sectors, conveyor belts are used to transport goods and materials through various stages of production and distribution. The rubber conveyor belt weight per meter helps determine the efficiency and energy consumption of the conveyor system. Lighter belts may be suitable for transporting lightweight materials, whereas heavier belts are necessary for handling heavier loads. Industry standards ensure that conveyor belts are designed and manufactured to meet the specific needs of these sectors, ensuring smooth and efficient operations.
The food processing industry also relies heavily on conveyor belts for the transportation of food products. In this industry, the rubber conveyor belt weight is important for ensuring the proper handling of food items without causing damage or contamination. Industry standards for food-grade conveyor belts include specifications for weight, material composition, and cleanliness to ensure the safety and quality of food products.
Furthermore, the recycling industry uses conveyor belts to transport recyclable materials through sorting and processing facilities. The rubber conveyor belt weight per meter is a critical factor in designing conveyor systems that can handle the varying weights and types of recyclable materials. Industry standards help ensure that conveyor belts used in recycling are durable, efficient, and capable of handling the demands of the recycling process.
Rubber Conveyor Belt Weight Calculation Method and Tools
The rubber conveyor belt weight per foot is a critical specification that plays a significant role in determining the overall efficiency and suitability of a conveyor system for various industrial applications. In this section, we will provide a detailed breakdown of weight measurements per foot for different types of conveyor belts and examples of how to calculate and interpret these measurements. We also provide a tool for the online calculation of rubber conveyor belt weight.

How to Calculate and Interpret These Measurements
Calculating the weight per foot of a conveyor belt involves determining the belt’s volume and then multiplying by the material’s density. Here are the steps to calculate the weight per foot:
- Measure the Belt Dimensions: Determine the width, thickness, and length of the belt. For example, a belt might be 24 inches wide and 0.25 inches thick.
- Calculate the Volume: For a one-foot length, the volume can be calculated using the formula: Volume (cubic feet) = Width (feet) × Thickness (feet) × Length (feet) For the example belt: Volume = (24 inches / 12) feet × (0.25 inches / 12) feet × 1 foot
= 2 feet × 0.0208 feet × 1 foot
= 0.0416 cubic feet - Determine the Material Density: The density of the belt material must be known. For instance, the density of rubber is approximately 95 pounds per cubic foot.
- Calculate the Weight: Multiply the volume by the density to get the weight per foot: Weight (pounds) = Volume (cubic feet) × Density (pounds per cubic foot) For the example belt: Weight = 0.0416 cubic feet × 95 pounds per cubic foot
= 3.95 pounds per foot
By following these steps, the weight per foot for any conveyor belt can be determined. This information is vital for selecting the right belt for specific applications and ensuring that the conveyor system can support the belt’s weight.
Conveyor Belt Weight Calculator
Calculating the rubber conveyor belt weight per meter is a critical aspect of designing and maintaining an efficient conveyor system. Various tools and methods can be used to determine this weight, ensuring that the conveyor belts meet the necessary specifications and perform optimally in their respective applications.
Several tools and methods are available to accurately calculate the rubber conveyor belt weight per meter. These tools range from simple online calculators to more sophisticated software programs used by engineers and manufacturers.
Online calculators are among the most accessible tools for quickly determining the weight of a conveyor belt. These calculators typically require inputs such as the belt width, thickness, and material type. Based on these inputs, the calculator provides an estimate of the belt’s weight per meter. These tools are convenient for preliminary calculations and are often used by sales and support teams to provide quick answers to customer inquiries.

For more precise calculations, specialized software programs are used. These programs can account for additional factors such as the type and density of reinforcement materials, specific rubber compounds, and the overall construction of the belt. By inputting detailed specifications, these programs can provide highly accurate weight calculations, essential for engineering and design purposes.
Another method involves manual calculations using standard formulas. This approach requires a thorough understanding of the belt’s construction and the properties of the materials used. The basic formula for calculating the weight per meter of a conveyor belt involves multiplying the belt’s volume per meter by the density of the materials. This method is often used by experienced engineers who need to verify or cross-check the results obtained from online calculators or software programs.
Step-by-Step Guide on Using a Conveyor Belt Weight Calculator
Using a conveyor belt weight calculator is a straightforward process, but it requires accurate input data to ensure the results are reliable. Here is a step-by-step guide on how to use an online conveyor belt weight calculator:
- Gather Required Information: Before using the calculator, collect all the necessary belt conveyor details. This includes the belt width, thickness, and material specifications. If the belt has reinforcement layers, gather information about the type and density of these materials as well.
- Access the Calculator: Open the conveyor belt weight calculator on a computer or mobile device. Many manufacturers and industry websites offer these calculators for free.
- Input Belt Specifications: Enter the gathered information into the calculator. Typically, this will involve selecting the material type from a dropdown menu and inputting the belt width and thickness in the appropriate fields. If the calculator allows, input details about the reinforcement materials as well.
- Review and Verify Inputs: Double-check the entered information to ensure accuracy. Incorrect inputs can lead to erroneous weight calculations, affecting the design and performance of the conveyor system.
- Calculate the Weight: Click the calculate button to generate the rubber conveyor belt weight per meter. The calculator will process the inputs and provide the estimated weight.
- Analyze the Results: Review the calculated weight and compare it with the specifications required for the intended application. If the results meet the necessary criteria, proceed with the design or procurement process. If adjustments are needed, modify the inputs accordingly and recalculate.
Using a conveyor belt weight calculator simplifies the process of determining the weight of a conveyor belt, making it easier for engineers and designers to ensure their systems are correctly specified.
Benefits of Accurate Weight Calculations for System Performance
Accurate calculations of the weight of rubber conveyor belt
per meter offer numerous benefits for the performance and efficiency of conveyor systems. These benefits extend across various aspects of system design, installation, and operation.
Firstly, accurate weight calculations are essential for ensuring the structural integrity of the conveyor system. Knowing the exact weight of the conveyor belt helps engineers design supporting structures that can safely handle the load without risk of failure. This is particularly important in applications where the conveyor system is subjected to heavy loads or operates in challenging environments.
Secondly, precise weight calculations contribute to the optimization of motor and drive systems. The weight of the conveyor belt directly impacts the power requirements for moving the belt and the materials it carries. By accurately determining the belt weight, engineers can select the appropriate motors and drive components, ensuring efficient energy consumption and reducing operational costs.
Additionally, accurate weight calculations are crucial for maintaining the longevity and reliability of the conveyor system. Overloading the system with a belt that is heavier than specified can lead to premature wear and tear, increased maintenance requirements, and potential system failures. By adhering to precise weight specifications, the overall lifespan of the conveyor system can be extended, resulting in lower maintenance costs and improved operational reliability.
Moreover, accurate rubber conveyor belt weight calculations enhance safety in the workplace. Conveyor systems that are correctly specified and operated within their designed weight limits are less likely to experience mechanical failures that could pose safety hazards to workers. Ensuring the correct belt weight helps in maintaining a safe working environment and complying with safety regulations.
In the context of procurement and inventory management, accurate weight calculations enable better planning and cost control. Knowing the exact weight of the conveyor belts allows for precise budgeting and ordering, reducing the risk of overstocking or shortages. This leads to more efficient inventory management and cost savings.
Lastly, accurate weight calculations facilitate compliance with industry standards and regulations. Many industries have specific requirements for the construction and performance of conveyor belts. By ensuring that the rubber conveyor belt weight per meter meets these standards, manufacturers and users can avoid compliance issues and ensure their systems are certified for use in their respective applications.
Importance of Knowing Rubber Conveyor Belt Weight
Understanding the rubber conveyor belt weight is essential for several reasons. It plays a critical role in the design, efficiency, and safety of conveyor systems used in various industries. This section will delve into why knowing the weight of a conveyor belt is crucial, its impact on system design and efficiency, and the safety considerations and maintenance implications involved.
Explanation of Why Understanding the Weight of a Conveyor Belt is Crucial for Various Industries
Conveyor belts are integral components in numerous industrial applications, from manufacturing and mining to food processing and logistics. The rubber conveyor belt weight is a key factor that influences many aspects of conveyor system performance. Here are some reasons why understanding this weight is crucial:
- Load Capacity: The weight of the conveyor belt affects the total load capacity of the system. Overloading the system can lead to mechanical failures, increased wear and tear, and potential downtime. Knowing the belt’s weight helps in calculating the total load the system can handle without compromising its structural integrity.
- Power Requirements: The weight of the conveyor belt influences the power requirements of the drive system. Heavier belts require more energy to move, affecting the selection of motors and other drive components. Accurate knowledge of the belt weight ensures that the system is designed with adequate power to operate efficiently.
- Material Handling: Different industries handle a variety of materials, each with unique properties. The weight of the conveyor belt must be compatible with the type of material being transported to ensure smooth and efficient operation. For example, lightweight belts are suitable for delicate materials, while heavier belts are needed for bulk materials like ores and aggregates.
Impact of Belt Weight on System Design and Efficiency
The rubber conveyor belt weight significantly impacts the overall design and efficiency of a conveyor system. Here are some key aspects to consider:
Structural Design
The conveyor structure must be designed to support the weight of the belt and the materials being transported. This includes the framework, rollers, and support structures. If the belt is too heavy, it can strain the system, leading to structural damage or failure. Therefore, engineers must consider the belt weight during the design phase to ensure the system can handle the intended loads.
Energy Consumption
Heavier conveyor belts require more energy to move, impacting the overall energy consumption of the system. This affects the operational costs and the environmental footprint of the facility. By selecting a belt with an appropriate weight, industries can optimize energy usage and reduce operational costs.
Speed and Efficiency
The weight of the conveyor belt influences the speed at which materials can be transported. Heavier belts may require slower speeds to prevent excessive strain on the system, while lighter belts can operate at higher speeds, improving overall efficiency. Understanding the belt weight helps in setting the optimal operating parameters for the system.
Safety Considerations and Maintenance Implications
Safety is a paramount concern in any industrial setting. The rubber conveyor belt weight has several safety implications that must be considered:
Load Stability
A conveyor belt that is too heavy for the system can cause instability, leading to accidents and injuries. Ensuring that the belt weight is within the system’s capacity helps maintain stability and safety during operation.
Wear and Tear
The weight of the conveyor belt affects the wear and tear on various components, including the drive system, rollers, and support structures. Heavier belts exert more force on these components, leading to faster wear and potentially higher maintenance costs. Regularly monitoring the belt weight and adjusting maintenance schedules accordingly can help mitigate these issues.
Emergency Situations
In emergency situations, such as a belt jam or mechanical failure, the weight of the conveyor belt can influence the ease of handling and resolution. Lighter belts are generally easier to manage and replace, while heavier belts may require additional equipment and manpower.
Maintenance Implications
Understanding the rubber conveyor belt weight also has implications for maintenance practices. Heavier belts may require more frequent inspections and maintenance to ensure they remain in good condition. This includes checking for signs of wear, ensuring proper tension, and lubricating moving parts. By considering the belt weight in maintenance planning, industries can extend the lifespan of their conveyor systems and reduce downtime.
FAQS about Rubber Conveyor Belt Weight
The weight of a PVC conveyor belt per meter depends on its dimensions and construction. On average, a standard PVC conveyor belt weighs between 2 to 5 kilograms per square meter. To determine the weight per meter, you need to consider the belt’s width and thickness. For example, a 1-meter-wide PVC belt with a thickness of 2 millimeters typically weighs around 2.4 kilograms per meter. If the thickness increases to 5 millimeters, the weight can rise to approximately 6 kilograms per meter. The exact weight can vary based on the specific type of PVC material and any additional reinforcements or coatings applied to the belt.
The density of a rubber conveyor belt typically ranges from 1.2 to 1.5 grams per cubic centimeter (g/cm³), equivalent to 75 to 94 pounds per cubic foot (lb/ft³). This density depends on the type of rubber used and any additional reinforcements, such as fabric layers or steel cords, which can alter the overall density. The specific density value is crucial for calculating the belt’s weight and understanding its suitability for various applications. High-density rubber belts are more durable and suitable for heavy-duty applications, while lower-density belts are lighter and used in less demanding environments.
The weight of a rubber conveyor belt varies significantly depending on its dimensions and material composition. On average, a standard rubber conveyor belt can weigh between 5 to 15 pounds per square foot. The exact weight depends on factors such as the belt’s thickness, width, and length. For instance, a thicker belt designed for heavy-duty applications will weigh more compared to a thinner belt used for light-duty purposes. Additionally, belts reinforced with materials like steel cords or fabric layers will have a higher weight. To determine the specific weight of a rubber conveyor belt, it’s crucial to consider its technical specifications provided by the manufacturer.
The average weight of a conveyor belt varies depending on its width, length, and thickness. For example, a standard 3-ply conveyor belt that is 24 inches wide and 1/8 inch thick can weigh around 0.4 pounds per square foot. For larger belts, such as a 48-inch wide belt that is 1/4 inch thick, the weight can be approximately 1.6 pounds per square foot. Thus, the weight of a conveyor belt can range from a few hundred pounds to several tons depending on its dimensions and construction.
To calculate the weight of a conveyor belt, you need to know its length, width, thickness, and the material’s density. The formula is:
Weight=Length×Width×Thickness×Density
The density of a rubber conveyor belt typically ranges between 80 and 120 pounds per cubic foot, depending on the specific type and composition of the rubber used. Standard industrial rubber belts, often reinforced with layers of fabric or steel cords, generally have a density around 85 to 90 pounds per cubic foot. This density allows the belts to provide the necessary strength and durability for various conveyor applications while maintaining flexibility and resistance to wear and tear.
Last Updated on July 22, 2024 by Jordan Smith
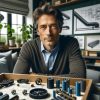
Jordan Smith, a seasoned professional with over 20 years of experience in the conveyor system industry. Jordan’s expertise lies in providing comprehensive solutions for conveyor rollers, belts, and accessories, catering to a wide range of industrial needs. From initial design and configuration to installation and meticulous troubleshooting, Jordan is adept at handling all aspects of conveyor system management. Whether you’re looking to upgrade your production line with efficient conveyor belts, require custom conveyor rollers for specific operations, or need expert advice on selecting the right conveyor accessories for your facility, Jordan is your reliable consultant. For any inquiries or assistance with conveyor system optimization, Jordan is available to share his wealth of knowledge and experience. Feel free to reach out at any time for professional guidance on all matters related to conveyor rollers, belts, and accessories.