Conveyor Belt 4 Ply: 8 to 20 mm Thick
Conveyor belt 4 ply is crucial for selecting the right belt for demanding industrial applications. A conveyor belt 4 ply consists of four layers of fabric reinforcement, each coated with rubber or a polymer. This construction provides enhanced strength, durability, and flexibility, making it suitable for heavy-duty operations. The thickness of a conveyor belt 4 ply typically ranges from 7 millimeters to 15 millimeters, ensuring it can handle significant loads and resist wear and tear. These belts are ideal for industries like mining, construction, and bulk material handling, where robust and reliable performance is essential.
About 4 Ply Conveyor Belt Thickness
The thickness of a conveyor belt 4 ply is a critical parameter that significantly influences its performance, durability, and suitability for various applications. Understanding the typical thickness range for these belts and the factors that contribute to their overall thickness is essential for selecting the right belt for specific industrial needs. This section will explore the typical thickness range for 4 ply conveyor belts and the factors that influence their overall thickness, including fabric and coating materials.
Typical Thickness Range for 4 Ply Conveyor Belts
A conveyor belt 4 ply typically ranges in thickness from around 8 mm to 20 mm. This range provides a balance between strength and flexibility, making these belts suitable for a variety of heavy-duty applications. The exact thickness required depends on the specific needs of the application, including the type of materials being transported, the operational environment, and the mechanical demands placed on the belt.
- Light-Duty Applications: For lighter-duty applications, such as packaging or light manufacturing, a 4 ply belt on the thinner end of the spectrum (around 8-12 mm) may be sufficient. These belts offer the necessary strength and flexibility without adding unnecessary bulk.
- Heavy-Duty Applications: In more demanding environments, such as mining, construction, or bulk material handling, thicker belts (15-20 mm) are often required. The additional thickness provides enhanced durability and load-bearing capacity, ensuring reliable performance under heavy loads and harsh conditions.
Factors That Influence the Overall Thickness
The overall thickness of a 4 ply conveyor belt is determined by several factors, including the type and number of fabric layers, the materials used for coatings, and any additional features designed to enhance performance.
Fabric Layers
The primary determinant of a 4 ply conveyor belt’s thickness is the four layers of fabric reinforcement. These layers provide the belt with its structural integrity and load-bearing capacity. The type of fabric used can vary, with common options including polyester, nylon, and cotton. Each material offers different properties that influence the belt’s thickness and performance.
- Polyester: Known for its high tensile strength and low stretch, polyester is a popular choice for 4 ply belts. It provides a robust foundation without adding excessive thickness, making it ideal for applications requiring strong yet flexible belts.
- Nylon: Nylon offers excellent flexibility and resistance to fatigue, making it suitable for applications with frequent bending and movement. Nylon-reinforced belts may be slightly thicker due to the material’s properties, but they provide superior durability in dynamic environments.
- Cotton: Although less common in modern conveyor belts, cotton can still be used in some applications. Cotton is relatively thick and offers good grip and flexibility, but it may not provide the same level of strength and durability as synthetic materials.
Coating Materials
In addition to the fabric layers, the materials used for the outer coatings of a conveyor belt 4 ply also contribute to its overall thickness. Coatings protect the fabric layers, enhance performance, and extend the belt’s lifespan. Common coating materials include rubber, PVC, and polyurethane.
- Rubber: Rubber coatings are widely used for their durability, abrasion resistance, and ability to handle heavy loads. The thickness of the rubber coating can vary depending on the application, with thicker coatings providing more protection and durability.
- PVC (Polyvinyl Chloride): PVC coatings offer good chemical resistance and are often used in applications requiring food-grade belts or exposure to harsh chemicals. PVC-coated belts are generally thinner than rubber-coated belts but still provide adequate protection and durability.
- Polyurethane: Known for its excellent wear resistance and flexibility, polyurethane coatings are used in applications where the belt needs to withstand frequent bending and high abrasion. Polyurethane coatings are typically thinner than rubber but offer superior performance in dynamic environments.
Additional Features
Some conveyor belt 4 ply designs include additional features that can influence the overall thickness. These features are added to enhance specific properties or address particular challenges in the application environment.
- Reinforcement Layers: Additional reinforcement layers, such as steel cords or extra fabric plies, can be added to increase the belt’s strength and load capacity. These layers add to the overall thickness but provide significant benefits in terms of performance and durability.
- Special Coatings: In applications requiring high levels of chemical resistance, flame retardancy, or extreme temperature tolerance, special coatings can be applied to the belt. These coatings can increase the thickness but ensure the belt performs reliably under challenging conditions.
- Textured Surfaces: Textured or patterned surfaces can be added to improve grip and material handling efficiency. These textures can slightly increase the belt’s thickness but provide enhanced performance for specific applications, such as incline conveying or handling slippery materials.
Manufacturing Process of Conveyor Belt 4 Ply
The manufacturing process of a 4-ply conveyor belt involves several key steps, ensuring the final product meets the required specifications for durability, flexibility, and strength. Here’s a detailed overview of the process:
1. Material Selection:
- Rubber Compounds: The primary material for the belt is rubber, which can be natural or synthetic. The type of rubber used depends on the application, with options including SBR (Styrene-Butadiene Rubber), nitrile, and EPDM.
- Fabric Plies: The fabric plies provide the belt’s strength and flexibility. Typically, polyester, nylon, or cotton fabrics are used. In a 4-ply belt, four layers of fabric are stacked.
2. Calendering:
- The rubber compound is fed through a calender machine, which presses and shapes it into thin sheets. These sheets will serve as the covers for the conveyor belt.
- The calendering process also produces rubberized fabric plies, where the fabric is coated with a thin layer of rubber to ensure adhesion between the plies.
3. Layering/Building:
- The belt is built by layering the rubber sheets and fabric plies on top of each other. The process involves placing a layer of rubber, followed by a fabric ply, and repeating until four plies are stacked.
- The layers are carefully aligned to ensure uniform thickness and strength across the belt.
4. Compression:
- Once the layers are assembled, the belt undergoes a compression process in a large press. This step consolidates the layers and removes any air trapped between them, ensuring proper adhesion.
- The belt is subjected to heat and pressure during this stage, which activates the vulcanization process, curing the rubber and bonding the layers together.
5. Vulcanization:
- The belt is then moved to a vulcanizing press, where it is heated under controlled conditions. This process chemically bonds the rubber molecules, giving the belt its final properties like tensile strength, elasticity, and resistance to wear.
- Vulcanization time and temperature are carefully controlled to achieve the desired belt characteristics.
6. Finishing:
- After vulcanization, the belt is allowed to cool. It is then trimmed to the required width and length.
- The edges of the belt may be reinforced or sealed to prevent fraying.
- A final inspection is conducted to check for any defects, such as bubbles, cracks, or weak spots.
7. Quality Control:
- The finished belt undergoes rigorous testing for tensile strength, elongation, adhesion between plies, and wear resistance.
- Belts that pass the quality tests are labeled and prepared for shipment. Those that do not meet the standards are either reprocessed or discarded.
8. Packaging and Distribution:
- The belts are typically rolled up and packaged for transport.
- Proper labeling ensures the belts are easily identified and matched with customer specifications.
This process ensures that the 4-ply conveyor belts produced are durable and capable of handling the stresses of industrial use. Each stage of production is critical to maintaining the integrity and performance of the final product.

The Keys of Conveyor Belt 4 Ply
Advantages of 4 Ply Conveyor Belts
The 4 ply conveyor belt is an advanced solution designed to meet the high demands of various industrial applications. It offers several advantages over single ply, 2 ply, and 3 ply belts, particularly in terms of tensile strength, flexibility, and load-bearing capacity. Understanding these benefits can help industries make informed decisions about the best conveyor belt for their specific needs.
Benefits Such as Increased Tensile Strength, Flexibility, and Load-Bearing Capacity
Increased Tensile Strength:
The most significant advantage of a conveyor belt 4 ply is its increased tensile strength. This is due to the four layers of reinforcement materials, typically made from high-strength fabrics such as polyester or nylon. These materials provide exceptional resistance to stretching and tearing, ensuring that the belt can handle heavy loads without deforming. This high tensile strength is particularly beneficial in industries such as mining, construction, and bulk material handling, where the conveyor belt must transport large and heavy materials over long distances. The increased tensile strength also contributes to the belt’s overall durability, reducing the frequency of replacements and repairs.
Enhanced Flexibility:
Despite its robust construction, a conveyor belt 4 ply maintains excellent flexibility. This flexibility allows the belt to navigate complex conveyor systems that include curves, inclines, and declines. The ability to bend and flex without losing structural integrity is crucial for maintaining smooth and efficient operation in diverse applications. Flexibility also aids in the installation and maintenance processes, as the belt can be manipulated more easily without risking damage to its layers. This balance of strength and flexibility ensures that the conveyor belt can perform reliably in a wide range of operating conditions.
Superior Load-Bearing Capacity:
The 4 ply construction significantly enhances the belt’s load-bearing capacity. Each layer contributes to the belt’s ability to support heavy weights, distributing the load evenly across the entire surface. This is particularly important in applications that require the transport of bulk materials such as ores, coal, and aggregates. The increased load-bearing capacity ensures that the belt can operate continuously without sagging or breaking, even under the strain of heavy loads. This feature is critical for industries that rely on the uninterrupted flow of materials to maintain productivity.
Comparison of Conveyor Belt 4 Ply with Single Ply, 2 Ply, and 3 Ply Belts
Single Ply Conveyor Belts:
Single ply conveyor belts consist of a single layer of fabric or other reinforcing material. While they offer some advantages, such as lower cost and lighter weight, they lack the strength and durability of multi-ply belts. Single ply belts are generally used in light-duty applications where the load and operational demands are minimal. However, they are not suitable for heavy-duty industrial applications due to their limited tensile strength and load-bearing capacity.
2 Ply Conveyor Belts:
2 ply conveyor belts offer a step up in terms of strength and durability compared to single ply belts. The additional layer provides extra reinforcement, making them suitable for moderate-duty applications. However, 2 ply belts still fall short when it comes to handling extremely heavy loads or operating in harsh environments. They offer better flexibility than single ply belts but do not match the robustness of 3 ply or 4 ply belts.
3 Ply Conveyor Belts:
3 ply conveyor belts are commonly used in heavy-duty applications due to their increased strength and durability. The three layers of reinforcement provide a good balance of tensile strength, flexibility, and load-bearing capacity. These belts are suitable for a wide range of industrial applications, including mining, construction, and bulk material handling. However, while 3 ply belts offer significant advantages, they may still not be sufficient for the most demanding environments where maximum strength and durability are required.
4 Ply Conveyor Belts:
Conveyor belt 4 ply is the most robust and durable option among the multi-ply belts. The four layers of reinforcement materials provide unmatched tensile strength, flexibility, and load-bearing capacity. These belts are designed to handle the toughest industrial applications, including those involving heavy, abrasive materials and harsh operating conditions. The 4 ply construction ensures that the belt can withstand significant wear and tear, reducing the need for frequent maintenance and replacements. Additionally, the increased flexibility of 4 ply belts allows them to navigate complex conveyor systems more efficiently, enhancing overall operational efficiency.
Key Comparisons:
- Strength and Durability: 4 ply belts offer the highest tensile strength and durability compared to single ply, 2 ply, and 3 ply belts. This makes them ideal for heavy-duty applications where maximum reliability is essential.
- Flexibility: While all multi-ply belts offer better flexibility than single ply belts, 4 ply belts provide the best balance of strength and flexibility, allowing them to perform well in complex conveyor systems.
- Load-Bearing Capacity: The load-bearing capacity of 4 ply belts far exceeds that of single ply, 2 ply, and 3 ply belts, making them suitable for transporting heavy and bulky materials over long distances.
- Cost: Although 4 ply belts are more expensive than single ply, 2 ply, and 3 ply belts, their superior performance and longevity justify the higher initial investment. The reduced need for maintenance and replacements can result in lower overall costs in the long run.

The Price of Conveyor Belt 4 Ply
The price of a 4-ply conveyor belt can vary significantly depending on several factors, including the material used, the belt width, thickness, length, and the specific application requirements. Here are some general considerations:
1. Material Composition:
- Standard Rubber: Typically less expensive, commonly used for general-purpose belts.
- Specialty Compounds (e.g., Heat Resistant, Oil Resistant): These can increase the cost, sometimes significantly.
2. Belt Dimensions:
- Width: Wider belts generally cost more due to the increased material usage.
- Thickness: Thicker belts use more material and may require more complex manufacturing processes, adding to the cost.
- Length: Longer belts will naturally be more expensive.
3. Customization and Special Features:
- Custom Reinforcements: Additional features like extra reinforcement, edge sealing, or custom patterns can add to the cost.
- Special Applications: Belts designed for specific industries (e.g., mining, high-temperature environments) tend to be more expensive.
4. Market and Regional Variations:
- Prices can vary based on the region, the manufacturer, and the current market conditions, such as raw material costs.
General Price Range
- Basic 4-Ply Conveyor Belt: The price can range from approximately $10 to $20 per linear foot for standard rubber belts.
- Specialty 4-Ply Conveyor Belt: For belts with specialized materials or custom features, prices can range from $25 to $50 per linear foot or more.
These prices are rough estimates and can vary widely based on the specific requirements and market conditions. For exact pricing, it’s best to consult with manufacturers or suppliers, providing them with detailed specifications for an accurate quote.
How about Conveyor Belt 4 Ply
Features of 4 Ply Conveyor Belts
The conveyor belt 4 ply is designed to meet the rigorous demands of heavy-duty industrial applications. Its construction, consisting of four layers of fabric or other materials, provides exceptional strength, durability, and flexibility. Understanding the key features of a conveyor belt 4 ply and how they contribute to its performance and longevity is essential for selecting the right belt for specific applications.
Key Features Including Abrasion Resistance, Tensile Strength, and Flexibility
Abrasion Resistance:
Abrasion resistance is one of the most critical features of a conveyor belt 4 ply. In many industrial settings, the belt must transport abrasive materials such as minerals, ores, and other rough substances. The four-layer construction provides a thick, robust surface that can withstand constant friction and wear. The top layer, often made from high-grade rubber, is designed to resist cuts, gouges, and general wear, ensuring the belt maintains its integrity and functionality over time. This feature is particularly important in industries like mining and quarrying, where the belt is exposed to harsh conditions and abrasive materials on a daily basis.
Tensile Strength:
Tensile strength refers to the belt’s ability to resist breaking under tension. The conveyor belt 4 ply excels in this area due to its multiple layers of reinforcement. Each ply is typically made from strong materials such as polyester or nylon, which provide excellent tensile strength. These materials ensure that the belt can handle heavy loads without stretching or tearing. This is crucial in applications where the belt must support substantial weight, such as in bulk material handling and heavy manufacturing processes. High tensile strength also contributes to the belt’s overall stability and reliability, reducing the risk of unexpected failures that could lead to costly downtime.
Flexibility:
Despite its robust construction, the conveyor belt 4 ply maintains a high degree of flexibility. This flexibility is essential for the belt to navigate complex conveyor systems that include curves, inclines, and declines. Flexible belts can adapt to various conveyor configurations without compromising performance. The four-ply construction ensures that while the belt is strong and durable, it can still bend and flex as needed. This balance of strength and flexibility is vital for ensuring smooth operation and preventing damage to the belt and the conveyor system. Flexibility also aids in the ease of installation and maintenance, as the belt can be manipulated without difficulty.
Explanation of How These Features Contribute to the Belt’s Performance and Longevity
The combination of abrasion resistance, tensile strength, and flexibility makes the conveyor belt 4 ply an ideal choice for demanding industrial environments. Here’s how these features enhance the belt’s performance and longevity:
Enhanced Durability:
The abrasion-resistant properties of the 4 ply conveyor belt mean it can handle rough and abrasive materials without significant wear. This durability reduces the frequency of belt replacements and repairs, leading to lower maintenance costs and less downtime. A durable belt ensures continuous operation, which is critical for industries that rely on conveyor systems for their production processes.
High Load Capacity:
The exceptional conveyor belt tensile strength of the 4 ply allows it to support heavy loads without stretching or breaking. This capability is crucial for industries such as mining, construction, and bulk material handling, where the belt must transport large quantities of heavy materials. By maintaining its structural integrity under heavy loads, the belt ensures reliable performance and reduces the risk of operational disruptions.
Operational Efficiency:
Flexibility is key to the operational efficiency of a conveyor system. The ability of the 4 ply conveyor belt to navigate complex paths and adapt to various configurations ensures smooth and efficient material transport. This flexibility helps prevent jams and reduces the stress on the conveyor components, prolonging their lifespan and enhancing the overall efficiency of the system.
Safety and Reliability:
A conveyor belt 4 ply that combines abrasion resistance, tensile strength, and flexibility offers a safer and more reliable solution for material handling. The belt’s robust construction minimizes the risk of sudden failures, which can lead to accidents and injuries. Reliable performance also means that the conveyor system can operate consistently, meeting production targets and maintaining workflow continuity.
Applications for Conveyor Belt 4 Ply
The conveyor belt 4 ply is a highly durable and versatile component used in various heavy-duty industrial applications. Its construction, which includes four layers of reinforcing fabric, provides enhanced strength and resilience, making it suitable for challenging environments. This section will explore the industries and applications where 4 ply conveyor belts are commonly used and highlight the importance of these belts in heavy-duty operations such as mining and bulk material handling.
Examples of Industries and Applications Where 4 Ply Conveyor Belts Are Commonly Used
The conveyor belt 4 ply is favored in many industries due to its ability to handle heavy loads and harsh conditions. Below are some of the key industries and specific applications where these belts are commonly employed:
Mining
In the mining industry, the conveyor belt 4 ply is indispensable for the transportation of extracted materials such as ores, coal, and aggregates. The belts must endure the tough conditions of mining operations, including exposure to sharp materials, heavy loads, and constant use.
- Open-Pit Mining: In open-pit mining, 4 ply conveyor belts are used to transport raw materials from the mining site to processing facilities. These belts must be robust enough to handle the large volumes of material and the abrasive nature of the rocks and minerals.
- Underground Mining: For underground mining operations, 4 ply conveyor belts are essential for moving extracted materials through narrow and confined spaces. These belts must be flexible yet strong to navigate the complex layouts of underground mines.
Bulk Material Handling
The conveyor belt 4 ply is crucial in bulk material handling operations, where large quantities of materials need to be moved efficiently and safely. Industries such as agriculture, construction, and waste management rely on these belts for their heavy-duty capabilities.
- Grain Handling: In the agricultural sector, 4 ply conveyor belts are used to transport grains and other bulk agricultural products. These belts must be able to handle the weight and volume of the materials while preventing spillage and ensuring smooth movement.
- Construction Materials: The construction industry uses 4 ply conveyor belts to move materials such as sand, gravel, and cement. The belts must withstand the abrasive nature of these materials and the heavy loads involved in construction operations.
- Waste Management: In waste management facilities, 4 ply conveyor belts are used to transport various types of waste, including recyclables and non-recyclables. These belts must be durable and resistant to tearing and punctures caused by sharp objects and heavy loads.
Manufacturing
In manufacturing environments, the conveyor belt 4 ply plays a vital role in the production and assembly processes. These belts are used to move raw materials, components, and finished products along the production line.
- Automotive Industry: In automotive manufacturing plants, 4 ply conveyor belts are used to transport car parts and assemblies. The belts must be strong enough to handle the weight of the components and provide reliable movement throughout the assembly process.
- Food Processing: The food processing industry uses 4 ply conveyor belts to move raw ingredients and finished products. These belts must be food-grade and able to withstand regular cleaning and sanitization processes.
Importance of 4 Ply Belts in Heavy-Duty Operations Like Mining and Bulk Material Handling
The conveyor belt 4 ply is particularly important in heavy-duty operations where the demands on the conveyor system are intense. Here are some reasons why 4 ply belts are crucial in these environments:
Enhanced Durability
The multiple layers of reinforcement in a 4 ply conveyor belt provide exceptional durability. This is essential in heavy-duty operations where belts are exposed to abrasive materials, high impacts, and continuous use.
- Abrasion Resistance: The additional layers offer superior resistance to wear and tear, extending the belt’s lifespan and reducing the need for frequent replacements. This is particularly important in mining and construction, where materials are highly abrasive.
- Impact Resistance: The reinforced structure of a 4 ply belt can absorb and dissipate impact forces more effectively than single or 2 ply belts. This reduces the risk of damage from heavy or sharp objects, which are common in bulk material handling and mining operations.
Higher Load Capacity
A conveyor belt 4 ply has a higher load capacity compared to belts with fewer layers. This makes it ideal for transporting heavy and bulky materials in industries like mining and agriculture.
- Increased Strength: The tensile strength of a 4 ply belt allows it to carry heavier loads without stretching or failing. This is crucial for maintaining efficiency and safety in operations that involve large volumes of material.
- Stable Performance: The robust construction of a 4 ply belt provides greater stability under heavy loads, ensuring consistent and reliable performance. This is important for preventing belt sagging and misalignment, which can lead to operational disruptions.
Versatility and Flexibility
Despite their strength, 4 ply conveyor belts maintain a degree of flexibility that allows them to navigate complex conveyor systems. This versatility is beneficial in industries with intricate layouts and varying operational demands.
- Complex Systems: The flexibility of 4 ply belts makes them suitable for use in conveyor systems with tight curves and varying elevations. This is essential in underground mining and other applications where the conveyor path is not straightforward.
- Adaptability: 4 ply belts can be customized to meet specific operational requirements, such as additional coatings for chemical resistance or modifications for extreme temperatures. This adaptability ensures that the belts can perform effectively in diverse environments.

Maintenance of 4 Ply Conveyor Belts
Proper maintenance of 4 ply conveyor belts is crucial for ensuring their longevity and optimal performance. The conveyor belt 4 ply design offers superior strength and durability, making it suitable for heavy-duty applications. However, to maximize its lifespan and prevent downtime, regular maintenance practices must be followed. This includes regular inspections, cleaning, and timely repairs.
Best Practices for Maintaining 4 Ply Conveyor Belts to Ensure Long Service Life
To ensure the long service life of a conveyor belt 4 ply, it is essential to implement a comprehensive maintenance program. This program should include routine inspections, proper cleaning methods, and prompt repairs of any detected issues. Here are some best practices to follow:
Regular Inspections:
Routine inspections are the cornerstone of effective maintenance. Regularly examining the conveyor belt for signs of wear and damage can help identify potential problems before they become severe. Inspections should focus on the following aspects:
- Surface Condition: Check for cuts, abrasions, and any other surface damage. Look for signs of excessive wear that could indicate misalignment or overloading.
- Belt Alignment: Ensure that the belt is tracking correctly and not drifting off-center. Misalignment can cause uneven wear and damage to the belt edges.
- Tension: Verify that the belt tension is appropriate. Over-tensioning can lead to excessive stress on the belt and conveyor components, while under-tensioning can cause slippage and inefficient operation.
- Splice Condition: Inspect the splices for signs of separation or wear. Splices are critical points on the belt and should be maintained in good condition to prevent breakdowns.
Proper Cleaning:
Maintaining a clean conveyor belt is essential for preventing the buildup of debris that can cause damage and reduce efficiency. Here are some cleaning tips:
- Scheduled Cleaning: Establish a regular cleaning schedule based on the operating environment. More frequent cleaning may be necessary in dusty or dirty environments.
- Appropriate Tools: Use brushes, scrapers, and suitable cleaning agents to remove dirt and debris from the belt surface. Avoid using harsh chemicals that can degrade the rubber or fabric layers of the conveyor belt 4 ply.
- Debris Removal: Ensure that debris does not accumulate on the conveyor system’s components, such as rollers and pulleys. Accumulated debris can cause misalignment and increased wear.
Timely Repairs:
Addressing minor issues promptly can prevent them from escalating into major problems. Here are some tips for effective repairs:
- Patch Small Damages: Use appropriate repair kits to patch small cuts and abrasions on the belt surface. This prevents further damage and extends the belt’s lifespan.
- Splice Repairs: Ensure that splices are properly maintained and repaired if necessary. A weak splice can lead to belt failure, causing significant downtime.
- Professional Assistance: For significant damages or complex repairs, seek professional assistance. Experienced technicians can perform repairs correctly, ensuring the belt’s integrity and performance.
Tips on Regular Inspections, Cleaning, and Repairs to Prevent Downtime and Extend Belt Lifespan
Implementing a structured maintenance routine that includes regular inspections, cleaning, and repairs is vital for preventing downtime and extending the lifespan of a conveyor belt 4 ply. Here are some detailed tips to guide these maintenance activities:
Regular Inspections:
- Visual Inspections: Conduct visual inspections at least once a week to identify any visible signs of wear or damage. Pay special attention to high-stress areas and points where the belt interacts with other components.
- Feel for Irregularities: Run your hand along the belt’s surface to detect any irregularities, such as rough spots or areas where the fabric layers might be exposed.
- Check for Proper Tracking: Ensure that the belt is properly aligned and tracking straight along the conveyor system. Misaligned belts can cause uneven wear and increase the risk of damage.
- Inspect the Underside: Don’t forget to inspect the underside of the belt, as this area can also show signs of wear and damage that are not visible from the top.
Proper Cleaning:
- Daily Cleaning: In environments with high levels of dust or debris, perform daily cleaning to prevent buildup. Use soft brushes or air blowers to remove loose particles.
- Weekly Deep Cleaning: Perform a more thorough cleaning once a week, using water and mild detergents if necessary. Make sure the belt is completely dry before restarting the conveyor system to prevent slippage.
- Avoid Harsh Chemicals: Always use cleaning agents that are compatible with the belt’s material. Harsh chemicals can degrade the rubber and fabric, leading to premature wear.
Timely Repairs:
- Monitor Splice Integrity: Regularly check the condition of splices and make any necessary repairs immediately. Weak or damaged splices can cause the belt to break under load, leading to significant downtime.
- Repair Small Damages Promptly: Address minor damages, such as small cuts or abrasions, as soon as they are detected. Use repair kits designed for conveyor belts to patch these areas effectively.
- Professional Repairs for Major Issues: For larger or more complex damages, seek professional repair services. Expert technicians have the tools and knowledge to perform repairs that ensure the belt’s continued performance and safety.
Preventive Maintenance:
- Develop a Maintenance Schedule: Create a detailed maintenance schedule that includes regular inspections, cleaning, and repairs. Adhering to this schedule helps ensure that all maintenance tasks are performed consistently and thoroughly.
- Training: Train maintenance personnel on the specific requirements and techniques for maintaining a conveyor belt 4 ply. Proper training ensures that maintenance tasks are carried out correctly and efficiently.
- Documentation: Maintain detailed records of all inspections, cleaning, and repairs. Documenting these activities helps track the belt’s condition over time and identify recurring issues that may need addressing.
By following these best practices and tips for regular inspections, cleaning, and repairs, industries can significantly extend the lifespan of conveyor belt 4 ply. This proactive approach to maintenance not only enhances the belt’s durability and performance but also reduces downtime, lowers operational costs, and ensures the safe and efficient operation of conveyor systems.

Selecting the Applications for Heavy-Duty Conveyor Belt 4 Ply
Choosing the appropriate conveyor belt 4 ply is essential for ensuring efficient and reliable operation in various industrial applications. A 4 ply conveyor belt offers increased strength, durability, and flexibility, making it suitable for heavy-duty tasks. This section will outline the criteria for selecting the right 4 ply conveyor belt, including considerations such as load capacity, environmental conditions, and belt speed.
Criteria for Choosing the Appropriate 4 Ply Conveyor Belt for Different Applications
When selecting a conveyor belt 4 ply, it is important to evaluate the specific needs of your application. Here are the key criteria to consider:
Load Capacity
Load capacity is a critical factor in choosing the right conveyor belt. A 4 ply conveyor belt is designed to handle heavier loads due to its multiple layers of reinforcement. However, it is essential to ensure that the belt’s load capacity matches the demands of your application.
- Maximum Load: Determine the maximum load the belt will need to carry. This includes the weight of the materials being transported and any additional forces exerted by the conveyor system.
- Belt Strength: Ensure the belt has the necessary tensile strength to withstand the load without stretching or failing. The tensile strength is typically specified by the manufacturer and should be checked against your application requirements.
Environmental Conditions
The environment in which the conveyor belt 4 ply will operate plays a significant role in its selection. Different environments present unique challenges that the belt must be able to withstand.
- Temperature: Consider the temperature range of the operating environment. High temperatures can cause some belt materials to degrade, while low temperatures can make them brittle. Choose a belt material that can handle the temperature extremes of your application.
- Chemical Exposure: If the belt will be exposed to chemicals, choose a material that offers chemical resistance. This is particularly important in industries such as chemical processing, food processing, and pharmaceuticals.
- Moisture and Corrosion: In environments with high humidity or exposure to water, selecting a belt with moisture resistance is crucial. Additionally, if the belt will be exposed to corrosive substances, ensure it has appropriate protective coatings or is made from corrosion-resistant materials.
Belt Speed
The speed at which the conveyor belt 4 ply operates is another important consideration. Higher speeds can increase wear and tear on the belt, so it is essential to choose a belt that can handle the intended speed without compromising performance.
- Optimal Speed Range: Check the manufacturer’s specifications for the optimal speed range of the belt. Operating outside this range can reduce the belt’s lifespan and increase the risk of failure.
- Speed Variability: If your application requires variable speeds, ensure the belt can handle the range of speeds it will encounter. This includes considering the effects of acceleration and deceleration on the belt.
Considerations Such as Load Capacity, Environmental Conditions, and Belt Speed
In addition to the primary criteria mentioned above, several other considerations can influence the selection of a conveyor belt 4 ply.
Abrasion Resistance
A 4 ply conveyor belt with high abrasion resistance is essential for applications involving rough or abrasive materials. This quality helps extend the belt’s life and reduces maintenance costs.
- Material Composition: Choose a belt material that offers high abrasion resistance. Natural rubber and synthetic rubbers like neoprene or nitrile are known for their durability in abrasive conditions.
- Surface Coatings: Some belts come with special surface coatings that enhance abrasion resistance. These coatings can provide additional protection and extend the belt’s service life.
Flexibility and Bending
The flexibility of a conveyor belt 4 ply is important for systems with tight curves or small pulleys. A belt that is too rigid may not perform well in such conditions.
- Bending Stress: Consider the belt’s ability to bend without cracking or losing strength. The belt should maintain its structural integrity while navigating the curves of the conveyor system.
- Flexibility Rating: Manufacturers often provide a flexibility rating or minimum pulley diameter for their belts. Ensure that the belt’s flexibility is suitable for your conveyor belt system’s design.
Impact Resistance
In applications where the belt may be subject to heavy impacts, such as loading and unloading areas, choosing a belt with high impact resistance is crucial.
- Reinforcement Layers: The multiple layers in a 4 ply conveyor belt provide enhanced impact resistance. Ensure that the belt’s construction includes materials that can absorb and dissipate impact forces.
- Shock Absorption: Some belts are designed with additional shock-absorbing layers or features to handle heavy impacts. These belts are ideal for applications involving heavy or sharp materials.
FAQS about Conveyor Belt 4 Ply
In the context of a flat belt, “ply” refers to the number of fabric layers used to construct the belt. Each ply is a layer of fabric, such as polyester, nylon, or cotton, which is coated with rubber or another elastomer to provide strength and durability. The number of plies in a flat belt affects its tensile strength, flexibility, and load-carrying capacity. For example, a single-ply belt has one layer of fabric, while a multi-ply belt has multiple layers. The more plies a flat belt has, the stronger and more resistant to stretching it is, making it suitable for heavier and more demanding applications. Ply also influences the belt’s ability to withstand wear and environmental factors.
A 2 ply conveyor belt typically has a thickness ranging from approximately 4 millimeters to 8 millimeters. This thickness is determined by the two layers of fabric and the rubber or polymer coatings that cover them. The exact thickness can vary based on the manufacturer and the specific requirements of the application, such as the type of material being transported and the environmental conditions. Thicker belts are generally more durable and can handle heavier loads, while thinner belts may be preferred for lighter applications or where greater flexibility is required. Understanding the specific needs of your operation will help in selecting the appropriate thickness for a 2 ply conveyor belt.
In a conveyor belt, “ply” refers to the number of layers of fabric or other reinforcement materials that are bonded together to form the belt. Each ply consists of a fabric layer, typically made from polyester, nylon, or cotton, which is coated with rubber, polymer, or elastomer. The number of plies in a belt indicates its overall strength and load-carrying capacity. For instance, a 2 ply belt has two layers of fabric, while a 4 ply belt has four layers. The more plies a belt has, the stronger and more durable it is, allowing it to handle heavier loads and more demanding applications. Ply also affects the flexibility and stretch of the belt.
The thickness of a 4 ply conveyor belt can vary depending on the manufacturer and the specific application it is designed for. Generally, a 4 ply conveyor belt ranges from approximately 7 millimeters to 15 millimeters thick. This thickness includes the combined layers of fabric and the rubber or polymer coatings on both the top and bottom surfaces. The actual thickness can be influenced by the individual ply materials and the type of rubber or elastomer used. A thicker belt provides greater strength and durability, making it suitable for heavy-duty applications where the belt must withstand significant wear and tear, such as in mining or bulk material handling.
The primary difference between 3 ply and 4 ply conveyor belts lies in the number of layers (plies) of fabric or material that make up the belt. A 3 ply conveyor belt has three layers of fabric, while a 4 ply conveyor belt has four. The additional ply in the 4 ply belt generally makes it stronger, more durable, and better suited for heavy-duty applications. The choice between the two depends on the specific requirements of the conveyor system, including the load it needs to carry and the operating conditions.
The number of plies in a conveyor belt can vary depending on its design and intended use. Conveyor belts typically have anywhere from 1 to 8 plies, with 2, 3, 4, and 5 ply belts being the most common. The number of plies affects the belt’s strength, flexibility, and overall performance.
The thickness of a 3 ply conveyor belt can vary depending on the specific materials used and the design of the belt. However, a typical 3 ply conveyor belt might have a thickness ranging from around 4.5 mm to 7 mm. The exact thickness will depend on factors such as the type of fabric or material used in the plies and any additional coatings or covers applied to the belt.
Last Updated on August 16, 2024 by Jordan Smith
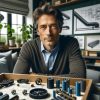
Jordan Smith, a seasoned professional with over 20 years of experience in the conveyor system industry. Jordan’s expertise lies in providing comprehensive solutions for conveyor rollers, belts, and accessories, catering to a wide range of industrial needs. From initial design and configuration to installation and meticulous troubleshooting, Jordan is adept at handling all aspects of conveyor system management. Whether you’re looking to upgrade your production line with efficient conveyor belts, require custom conveyor rollers for specific operations, or need expert advice on selecting the right conveyor accessories for your facility, Jordan is your reliable consultant. For any inquiries or assistance with conveyor system optimization, Jordan is available to share his wealth of knowledge and experience. Feel free to reach out at any time for professional guidance on all matters related to conveyor rollers, belts, and accessories.