Jaw Crusher with Efficient Crusher Conveyor Belt
A crusher conveyor belt is essential for transporting crushed materials efficiently in stone crusher plants. These belts are designed to handle heavy loads and resist wear, making them ideal for rugged environments. Customizable options allow for seamless integration into existing systems, tailored to meet specific plant requirements. High-quality materials provide superior tensile strength and impact resistance, ensuring durability and flexibility. Using a crusher conveyor belt enhances productivity, reduces labor costs, and minimizes workplace injuries, making it a critical component in material transport and processing operations.
Crusher Conveyor Belt
Benefits of Choosing the Right Conveyor Belt
Selecting the appropriate crusher conveyor belt is crucial for maximizing efficiency, safety, and cost-effectiveness in industrial operations. The right conveyor belt can significantly enhance productivity, reduce labor costs, and improve safety, minimizing workplace injuries. Understanding these benefits can help industries make informed decisions about the best conveyor belt for their specific applications.
Increased Productivity and Reduced Labor Costs
One of the primary benefits of choosing the right crusher conveyor belt is the potential for increased productivity. The correct belt ensures efficient material handling, reducing downtime and facilitating smoother operations. Here’s how it contributes to productivity:
Optimized Material Flow:
A crusher conveyor belt designed specifically for your application ensures that materials are transported quickly and efficiently from the crusher to the next stage in the process. This optimized material flow reduces bottlenecks and delays, allowing for continuous production. The smooth and consistent movement of materials enhances overall productivity, as the system can operate at maximum capacity without interruptions.
Reduced Downtime:
Selecting a high-quality crusher conveyor belt reduces the likelihood of unexpected breakdowns and malfunctions. A durable and reliable belt can withstand the rigors of crushing operations, including exposure to sharp, heavy materials and abrasive conditions. By minimizing the risk of belt failures, industries can maintain continuous operation, avoiding costly downtime and ensuring that production targets are met.
Improved Efficiency:
The right conveyor belt can improve the efficiency of the crushing process by ensuring that materials are handled with precision. Features such as anti-slip surfaces and proper tensioning mechanisms help maintain optimal belt performance, preventing material spillage and reducing the need for manual adjustments. This efficiency translates into higher output rates and better utilization of resources.
Reduced Labor Costs:
Using an appropriate crusher conveyor belt can lead to significant labor cost savings. Efficient material handling reduces the need for manual intervention, as the belt can handle larger volumes of materials with minimal supervision. This automation allows workers to focus on other critical tasks, improving overall operational efficiency. Additionally, a reliable conveyor belt reduces the frequency of maintenance and repairs, lowering labor costs associated with these activities.
Enhanced Safety and Minimized Workplace Injuries
Safety is a paramount concern in industrial operations, and choosing the right crusher conveyor belt plays a vital role in minimizing workplace injuries. The appropriate belt can enhance safety in several ways:
Stability and Control:
A well-designed crusher conveyor belt provides excellent stability and control over the materials being transported. Features such as proper grip surfaces and sidewalls prevent materials from slipping or falling off the belt, reducing the risk of accidents. This stability ensures that materials are conveyed safely from one point to another without posing a hazard to workers.
Minimized Manual Handling:
Manual handling of heavy and sharp materials poses significant risks of injuries to workers. An efficient conveyor belt system automates the material handling process, minimizing the need for manual intervention. By reducing the physical strain on workers, the likelihood of musculoskeletal injuries, cuts, and other workplace accidents is significantly decreased. This automation also ensures that materials are handled consistently and safely, further enhancing workplace safety.
Proper Guarding and Safety Features:
The right crusher conveyor belt comes with built-in safety features such as guards, emergency stop mechanisms, and sensors. These features protect workers from potential hazards by preventing accidental contact with moving parts and providing immediate response options in case of emergencies. Properly guarded conveyor belts create a safer working environment, reducing the risk of injuries and ensuring compliance with safety regulations.
Reduced Risk of Fires:
Conveyor belts in crushing operations are exposed to various environmental factors that can increase the risk of fires, such as friction, heat, and the presence of flammable materials. Choosing a conveyor belt made from fire-resistant materials can mitigate this risk. Fire-resistant belts are designed to withstand high temperatures and prevent the ignition of combustible materials, ensuring a safer working environment.
Enhanced Durability and Reliability:
A durable and reliable crusher conveyor belt reduces the risk of sudden failures that could pose safety hazards. High-quality belts are designed to endure harsh operating conditions, including exposure to abrasive materials and extreme temperatures. Their robust construction ensures consistent performance, minimizing the likelihood of accidents caused by belt malfunctions.
Improved Visibility and Monitoring:
Modern crusher conveyor belts often come equipped with advanced monitoring and control systems. These systems provide real-time data on the belt’s condition, performance, and any potential issues. Improved visibility allows for proactive maintenance and timely interventions, preventing small problems from escalating into major safety concerns. Additionally, monitoring systems can alert operators to potential hazards, enabling them to take immediate action to mitigate risks.
Durability and Maintenance of Crusher Conveyor Belts
A crusher conveyor belt is an essential component in various industrial applications, especially in mining, quarrying, and recycling operations. These belts are designed to handle the demanding conditions of transporting crushed materials and need to be extremely durable and well-maintained to ensure efficient operation. This section will discuss the heavy-duty nature of crusher conveyor belts, their suitability for different industrial applications, and provide tips on regular maintenance and best practices to ensure a long service life.
Heavy-Duty Belts Suitable for Various Industrial Applications
Crusher conveyor belts are specifically engineered to withstand the harsh environments they operate in. These belts must endure constant wear and tear, high impact loads, and exposure to abrasive materials. The following attributes make them suitable for heavy-duty applications:
Robust Construction
A crusher conveyor belt is constructed from high-strength materials that provide exceptional durability and resistance to abrasion. The core of these belts is typically made from multiple layers of synthetic fabrics such as polyester or nylon, which are known for their high tensile strength and flexibility.
- Reinforcement Layers: The belts often have additional reinforcement layers, such as steel cords or extra fabric plies, to enhance their strength and durability. These reinforcement layers help the belt withstand the heavy loads and impacts associated with transporting crushed materials.
- Thick Rubber Cover: The outer layer of the belt is coated with thick rubber, which provides excellent resistance to wear, cutting, and tearing. This rubber cover protects the inner fabric layers from damage and ensures the belt can handle abrasive materials effectively.
High Impact Resistance
Crusher conveyor belts are designed to absorb and dissipate the high impact forces generated when large, heavy materials are dropped onto the belt. This impact resistance is crucial for preventing damage and ensuring the belt’s longevity.
- Shock Absorption: The belts are equipped with shock-absorbing features, such as specially formulated rubber compounds and cushioning layers, to reduce the impact forces transmitted to the belt structure.
- Durable Joints: The joints or splices of the belts are designed to be as strong as the rest of the belt. High-quality splicing methods, such as vulcanized splicing or mechanical fasteners, ensure the joints can withstand the same impact and load as the belt itself.
Versatility in Applications
The crusher conveyor belt is versatile and can be used in a variety of industrial applications beyond just crushing operations. These belts are suitable for transporting a wide range of materials, including rocks, ores, coal, aggregates, and recycled materials.
- Mining and Quarrying: In mining and quarrying operations, crusher conveyor belts are used to transport crushed stone, gravel, and other extracted materials. These belts must be able to handle the abrasive nature of these materials and the harsh conditions of the mining environment.
- Recycling: In recycling facilities, crusher conveyor belts are used to move recycled materials such as concrete, asphalt, and metals. The belts must be durable enough to handle the sharp edges and heavy weights of these materials.
- Construction: In construction sites, crusher conveyor belts are used to transport construction debris and materials. These belts need to be robust enough to withstand the heavy loads and abrasive conditions of construction operations.
Tips on Regular Maintenance and Best Practices for Ensuring Long Service Life
Regular maintenance is essential for ensuring the long service life and efficient operation of a crusher conveyor belt. Here are some tips and best practices for maintaining these belts:
Routine Inspections
Conducting routine inspections is the first step in effective maintenance. Regularly check the entire length of the conveyor belt for signs of wear, damage, or misalignment. Look for any fraying edges, cuts, or punctures that could indicate underlying issues.
- Visual Inspection: Examine the belt surface for any visible damage or wear. Ensure that the belt is tracking correctly and not deviating from its path.
- Mechanical Inspection: Check the conveyor system’s components, such as rollers, pulleys, and tensioners, for any signs of wear or misalignment. Ensure that all components are functioning correctly and smoothly.
Cleaning
Keeping the crusher conveyor belt clean is vital to prevent material build-up, which can lead to belt slippage, misalignment, and increased wear. Regular cleaning helps maintain the belt’s performance and extends its life.
- Daily Cleaning: Remove any debris or material build-up from the belt surface and conveyor components. Use appropriate cleaning methods and tools to avoid damaging the belt.
- Deep Cleaning: Periodically perform a more thorough cleaning to remove any ingrained dirt or contaminants. This may involve shutting down the conveyor system and using specialized cleaning equipment.
Proper Tensioning
Maintaining the correct tension in a crusher conveyor belt is critical to its performance and longevity. Incorrect tension can lead to excessive wear, slippage, and potential belt damage.
- Tension Adjustment: Regularly check and adjust the belt tension according to the manufacturer’s recommendations. Ensure that the belt is neither too tight nor too loose, as both conditions can cause issues.
- Tension Monitoring: Use tension monitoring devices to maintain consistent tension throughout the belt’s operation. These devices can help identify and correct any tension-related issues before they lead to significant problems.
Lubrication
Lubricating the moving parts of the conveyor system is essential to reduce friction, prevent wear, and ensure smooth operation. However, it’s important to use the correct type of lubricant to avoid damaging the belt.
- Lubricant Selection: Choose lubricants that are compatible with the belt material and the operating environment. Avoid using lubricants that can degrade the belt or cause contamination.
- Lubrication Schedule: Follow a regular lubrication schedule to keep the conveyor system running smoothly. Lubricate bearings, rollers, and other moving parts as specified by the manufacturer.
Preventive Maintenance
Implementing a preventive maintenance program can help identify and address potential issues before they become major problems. This approach involves regularly scheduled maintenance tasks designed to keep the conveyor system in optimal condition.
- Scheduled Maintenance: Develop a maintenance schedule that includes routine inspections, cleaning, lubrication, and tension adjustments. Adhering to this schedule helps ensure that maintenance tasks are performed consistently and on time.
- Record Keeping: Maintain detailed records of all maintenance activities, including inspections, repairs, and replacements. These records can help track the belt’s condition and identify patterns or recurring issues.
Training and Safety
Proper training and adherence to safety protocols are crucial for maintaining a conveyor belt crusher. Ensuring that all personnel are knowledgeable about the belt’s operation and maintenance requirements can prevent accidents and prolong the belt’s service life.
- Operator Training: Provide comprehensive training for all conveyor system operators, covering topics such as belt operation, maintenance procedures, and safety protocols. Well-trained operators are more likely to identify and address issues before they escalate.
- Safety Measures: Implement and enforce safety measures to protect personnel working with the conveyor system. This includes using protective equipment, following lockout/tagout procedures, and adhering to manufacturer guidelines.
How about Crusher Conveyor Belt
Applications in Stone Crusher Plants
The crusher conveyor belt plays a pivotal role in the efficient operation of stone crusher plants. It is an essential component designed to move crushed stones from one stage of the crushing process to the next, ensuring continuous and efficient material flow. Understanding the applications of a crusher conveyor belt in stone crusher plants highlights its importance in handling large volumes of material and operating under extreme weather conditions.
Essential for Moving Crushed Stones
In stone crusher plants, the conveyor belt for crusher is crucial for moving crushed stones between different stages of the crushing process. The workflow in a typical stone crusher plant involves several key stages, including primary crushing, secondary crushing, and screening. Each stage requires the seamless transfer of materials to maintain efficiency and productivity.
Primary Crushing:
During the primary crushing stage, large rocks and stones are fed into the crusher, where they are broken down into smaller, more manageable sizes. The crusher conveyor belt is used to transport these crushed stones from the primary crusher to the next processing stage. This movement is critical as it ensures a steady flow of material, preventing bottlenecks and maintaining the pace of production.
Secondary Crushing:
After primary crushing, the materials are conveyed to the secondary crushers, where further reduction in size takes place. The crusher conveyor belt efficiently transfers the crushed stones from the primary crusher output to the secondary crusher input. This stage often involves multiple crushers working in tandem, and the conveyor belt’s role is vital in synchronizing the operations to achieve consistent output sizes.
Screening and Sorting:
Following the secondary crushing, the materials are typically transported to screening and sorting units. Here, the crushed stones are separated based on size and quality. The crusher conveyor belt ensures that materials are delivered to the appropriate screens and sorters, facilitating the efficient separation and classification of crushed stones. This step is essential for producing aggregate products that meet specific size and quality standards.
Stockpiling and Transport:
Once the stones are crushed, screened, and sorted, they need to be moved to stockpile areas or directly to transport vehicles for delivery to customers. The crusher conveyor belt is responsible for moving the final products to these locations, ensuring that large volumes of crushed stones are handled efficiently and safely.
Designed for Extreme Weather Conditions and Large Volume Carrying Capacity
Stone crusher plants often operate in harsh environments and under extreme weather conditions. Therefore, the crusher conveyor belt must be designed to withstand these challenges while maintaining high performance and durability.
Extreme Weather Conditions:
Stone crusher plants can be located in areas with extreme temperatures, ranging from scorching heat to freezing cold. The crusher conveyor belt must be able to operate reliably in these conditions without compromising its integrity or performance.
- Heat Resistance: In high-temperature environments, the conveyor belt is exposed to intense heat from the sun and the friction generated by the continuous movement of heavy materials. Heat-resistant conveyor belts are designed to withstand these conditions, ensuring they do not degrade or lose strength over time.
- Cold Resistance: In cold environments, the conveyor belt must remain flexible and functional despite low temperatures. Cold-resistant belts are made from materials that retain their flexibility and strength even in freezing conditions, preventing cracking and brittleness.
Weatherproofing:
To ensure longevity and reliability, the crusher conveyor belt must be weatherproof. This involves using materials and coatings that protect the belt from environmental factors such as moisture, UV radiation, and chemical exposure. Weatherproof belts are less susceptible to degradation, maintaining their performance over extended periods.
Large Volume Carrying Capacity:
Stone crusher plants handle massive volumes of materials daily. The crusher conveyor belt must be capable of carrying large loads efficiently and safely. This requires a design that combines strength, durability, and ample carrying capacity.
- High Tensile Strength: The conveyor belt needs to have high tensile strength to support the weight of large volumes of crushed stones. Reinforced with materials like polyester, nylon, or steel cords, these belts can handle the stress and strain of heavy loads without stretching or breaking.
- Wide and Thick Belts: To accommodate the volume of materials, crusher conveyor belts are often wider and thicker than standard belts. This design provides a larger surface area for transporting materials and enhances the belt’s durability.
- Heavy-Duty Construction: Crusher conveyor belts are built to endure the harsh conditions of stone crusher plants. They are made from robust materials that resist wear and tear, ensuring long service life and minimal maintenance requirements.
Efficiency and Productivity:
The efficiency of a stone crusher plant heavily relies on the performance of its conveyor belt system. A well-designed crusher conveyor belt ensures smooth and continuous material flow, reducing the likelihood of bottlenecks and operational interruptions. This efficiency directly translates to higher productivity and profitability for the plant.
- Reduced Downtime: Reliable conveyor belts reduce the frequency of breakdowns and maintenance needs. This minimizes downtime, allowing the plant to operate at full capacity and meet production targets consistently.
- Consistent Material Handling: The ability to handle large volumes of material consistently ensures that all stages of the crushing process are synchronized. This consistency improves the quality of the final product and enhances overall operational efficiency.
Safety Considerations:
Safety is paramount in stone crusher plants, and the crusher conveyor belt plays a crucial role in ensuring a safe working environment.
- Stability and Control: A stable and well-controlled conveyor belt system reduces the risk of material spillage and accidents. Proper tensioning and alignment prevent the belt from drifting or sagging, maintaining a safe and orderly material flow.
- Safety Features: Modern crusher conveyor belts come equipped with safety features such as emergency stop mechanisms, guards, and sensors. These features protect workers from potential hazards and provide quick response options in case of emergencies.
The Keys of Crusher Conveyor Belt
Customization and Design
Crusher conveyor belts are critical components in the efficient operation of stone crusher plants. They must be designed and customized to meet the specific needs of each plant, ensuring optimal performance and seamless integration with existing systems. Customizable conveyor belt systems and expert consultation are essential for achieving these goals, providing tailored solutions that enhance productivity and reliability.
Customizable Conveyor Belt Systems to Meet Unique Plant Requirements
Every stone crusher plant has unique operational requirements, influenced by factors such as the type of material being processed, production capacity, and the layout of the plant. Therefore, off-the-shelf conveyor belt solutions may not always be adequate. Customizable crusher conveyor belt systems are essential to address these unique needs effectively.
Material Specifications:
The type of material being processed significantly influences the design of the crusher conveyor belt. For example, processing hard and abrasive materials like granite or basalt requires a belt with high abrasion resistance and durability. In contrast, softer materials like limestone may not need such robust specifications. Customizable conveyor belts can be designed with specific materials and coatings to match the wear resistance, tensile strength, and flexibility required for different types of crushed stone.
Size and Length:
The dimensions of the conveyor belt system, including its width and length, must be tailored to fit the specific layout and capacity of the stone crusher plant. Customizable systems allow for precise adjustments to belt size, ensuring that they can handle the required volume of material efficiently. This customization also helps in optimizing the space within the plant, allowing for better organization and workflow.
Load-Bearing Capacity:
Crusher conveyor belts must be designed to handle the significant loads imposed by the materials they transport. Customizable belts can be reinforced with additional layers or materials to enhance their load-bearing capacity. This ensures that the belt can support the weight of the crushed stones without stretching or breaking, maintaining consistent performance even under heavy loads.
Speed and Control:
The speed at which the conveyor belt operates is another critical factor. Different stages of the crushing process may require varying conveyor speeds to ensure efficient material handling. Customizable conveyor belt systems can be equipped with adjustable speed controls, allowing operators to fine-tune the belt’s operation to match the needs of each stage. This flexibility enhances overall efficiency and prevents bottlenecks in the production line.
Environmental Conditions:
Stone crusher plants often operate in harsh environmental conditions, including extreme temperatures, humidity, and exposure to chemicals or UV radiation. Customizable crusher conveyor belts can be designed with specific environmental resistance features, such as heat-resistant or cold-resistant materials, to ensure reliable performance in these conditions. This customization helps in prolonging the lifespan of the conveyor belt and maintaining consistent operation.
Expert Consultation for Tailored Design and Seamless Integration with Existing Operations
Achieving the best performance from a crusher conveyor belt requires more than just selecting the right materials and dimensions. Expert consultation plays a crucial role in designing and integrating the conveyor belt system into existing operations. Experienced professionals can provide valuable insights and recommendations, ensuring that the customized conveyor belt system meets all operational requirements and integrates seamlessly with other components of the plant.
Site Assessment and Analysis:
Expert consultants begin by conducting a thorough assessment of the stone crusher plant. This includes analyzing the layout, material flow, production capacity, and specific operational challenges. By understanding these factors, consultants can identify the most effective design and customization options for the crusher conveyor belt.
Tailored Design Solutions:
Based on the site assessment, consultants work with plant operators to develop tailored design solutions. This involves selecting the appropriate materials, dimensions, and features for the conveyor belt system. Consultants also consider factors such as the angle of incline, belt tension, and the type of drive system needed to ensure optimal performance.
Integration with Existing Systems:
Seamless integration with existing operations is critical for the successful implementation of a customized crusher conveyor belt system. Consultants provide detailed plans for integrating the new conveyor belt with existing crushers, screens, and other equipment. This includes ensuring compatibility with current control systems and optimizing the overall workflow to enhance efficiency.
Installation and Commissioning:
Expert consultants oversee the installation and commissioning of the customized conveyor belt system. This includes supervising the installation process to ensure that all components are correctly assembled and aligned. Consultants also conduct testing and adjustments to verify that the system operates as intended, addressing any issues that may arise during the initial startup phase.
Ongoing Support and Maintenance:
After the installation, expert consultants continue to provide support and maintenance services. This includes regular inspections, preventive maintenance, and prompt repairs to ensure that the conveyor belt system remains in optimal condition. Consultants also offer training for plant personnel, equipping them with the knowledge and skills needed to operate and maintain the customized conveyor belt system effectively.
Performance Optimization:
To maximize the benefits of a customized crusher conveyor belt system, ongoing performance optimization is essential. Consultants use advanced monitoring tools and data analysis to track the system’s performance over time. By identifying areas for improvement and implementing necessary adjustments, consultants help plant operators achieve higher efficiency, reduced downtime, and increased productivity.
Features of Crusher Conveyor Belts
A crusher conveyor belt is a crucial component in various industrial applications, particularly in mining, quarrying, and recycling operations. These belts are designed to handle the demanding conditions of transporting crushed materials efficiently and reliably. This section will discuss the key features of crusher conveyor belts, including efficient material transfer, high-quality materials with high tensile strength and impact resistance, and the use of multiple layers for durability and flexibility.
Efficient Material Transfer from One Point to Another
One of the primary functions of a crusher conveyor belt is to ensure the efficient transfer of materials from one point to another within the processing system. Efficiency in material transfer is essential for maintaining productivity and reducing operational costs.
Seamless Integration
Crusher conveyor belts are designed to integrate seamlessly with other components of the crushing and material handling system. This integration ensures a smooth and continuous flow of materials, minimizing downtime and enhancing overall efficiency.
- Optimized Layout: The layout of the conveyor system is optimized to reduce the distance materials need to travel and minimize the number of transfer points. This reduces the risk of material loss and wear on the belt.
- Customizable Design: Crusher conveyor belts can be customized to fit specific system requirements, including varying lengths, widths, and angles. This customization ensures that the belt meets the unique needs of the operation, enhancing material transfer efficiency.
High Throughput
A well-designed crusher conveyor belt is capable of handling high throughput, allowing large volumes of material to be processed quickly and efficiently. High throughput is crucial for meeting production targets and maintaining the profitability of the operation.
- Wide Belts: Wider belts can accommodate more material, increasing the system’s overall throughput. This is particularly important in high-capacity operations such as mining and quarrying.
- High-Speed Operation: Conveyor belts designed for high-speed operation ensure that materials are moved quickly from one stage of the process to the next. This reduces bottlenecks and enhances the overall efficiency of the system.
High-Quality Materials with High Tensile Strength and Impact Resistance
The durability and performance of a crusher conveyor belt are heavily influenced by the quality of materials used in its construction. High-quality materials with high tensile strength and impact resistance are essential for ensuring the belt can withstand the demanding conditions of crushing operations.
High Tensile Strength
Tensile strength refers to the maximum amount of tensile (stretching) stress a material can withstand before breaking. High tensile strength is crucial for conveyor belts used in heavy-duty applications, as it ensures the belt can handle the weight and force of the transported materials without failing.
- Reinforced Fabrics: Crusher conveyor belts are typically reinforced with multiple layers of high-strength fabrics such as polyester or nylon. These materials provide the necessary tensile strength to handle heavy loads and resist stretching.
- Steel Cord Reinforcement: In some cases, steel cords are used to reinforce the belt, providing even greater tensile strength and durability. Steel-reinforced belts are particularly suitable for extremely heavy-duty applications.
Impact Resistance
Crusher conveyor belts must also be able to withstand the high impact forces generated when large, heavy materials are dropped onto the belt. Impact resistance is crucial for preventing damage and ensuring the belt’s longevity.
- Thick Rubber Covers: The outer layer of the belt is typically made of thick rubber, which provides excellent resistance to impact, cutting, and abrasion. This rubber cover protects the inner fabric layers from damage.
- Shock-Absorbing Features: Some belts are designed with additional shock-absorbing features, such as specially formulated rubber compounds or cushioning layers, to further enhance their impact resistance.
Multiple Layers for Durability and Flexibility
The use of multiple layers in the construction of a crusher conveyor belt provides a balance of durability and flexibility, ensuring the belt can withstand harsh conditions while maintaining efficient operation.
Layered Construction
A typical crusher conveyor belt consists of multiple layers of fabric and rubber, each serving a specific purpose. This layered construction enhances the belt’s overall durability and performance.
- Fabric Layers: The fabric layers, usually made of materials like polyester or nylon, provide the belt with its structural integrity and tensile strength. These layers are designed to resist stretching and tearing.
- Rubber Covers: The rubber covers protect the fabric layers from external damage and provide additional durability. The top cover is typically thicker to withstand the impact and abrasion from the transported materials, while the bottom cover provides resistance to wear from the conveyor rollers and pulleys.
- Intermediate Layers: Some belts include intermediate layers of rubber or other materials to enhance specific properties, such as flexibility or shock absorption. These layers help distribute the forces acting on the belt more evenly, reducing stress and extending the belt’s lifespan.
Flexibility
Flexibility is an important feature for a crusher conveyor belt, as it allows the belt to navigate the various curves and angles of the conveyor system without cracking or losing integrity.
- Bending Resistance: The layered construction of the belt ensures it can bend and flex as needed without compromising its structural integrity. This is particularly important in complex conveyor layouts with tight curves.
- Adaptability: Flexible belts can adapt to different operational conditions, such as changes in load or speed, without requiring significant adjustments. This adaptability ensures consistent performance across various scenarios.
Reliable Material Transport
The crusher conveyor belt is a vital component in stone crusher plants and other industrial operations that rely on efficient material handling. Ensuring reliable material transport is crucial for maintaining productivity, minimizing downtime, and ensuring the smooth operation of the entire processing system. This section provides an overview of the importance of conveyor belts in stone crusher plants and the benefits of using reliable and efficient material transport systems.
Overview of the Importance of Conveyor Belts in Stone Crusher Plants
In stone crusher plants, conveyor belts play a critical role in the material handling process. These belts are responsible for transporting raw materials from the extraction site to the crusher, and then moving the crushed materials to different stages of processing, storage, or transport. The efficiency and reliability of the crusher conveyor belt directly impact the overall productivity and operational efficiency of the plant.
Key Functions
The primary functions of conveyor belts in stone crusher plants include:
- Material Transport: Conveyor belts move raw materials from the extraction point to the crusher, where they are broken down into smaller pieces. After crushing, the belts transport the processed materials to subsequent stages of the operation, such as screening, sorting, or further crushing.
- Efficient Flow Management: Conveyor belts help manage the flow of materials within the plant, ensuring that the processing operations are continuous and uninterrupted. This efficient flow management is essential for maintaining high productivity levels and reducing bottlenecks.
- Automation and Control: Modern conveyor systems are often integrated with automated control systems that monitor and adjust the flow of materials. This automation enhances the efficiency and reliability of the material handling process, reducing the need for manual intervention and increasing overall productivity.
Benefits of Using Reliable and Efficient Material Transport Systems
Using reliable and efficient material transport systems, such as a high-quality crusher conveyor belt, offers several significant benefits to stone crusher plants and other industrial operations.
Increased Productivity
A reliable conveyor belt system ensures the continuous and smooth transport of materials, which is essential for maintaining high productivity levels. By minimizing interruptions and downtime, a well-designed conveyor system enables the plant to operate at its maximum capacity.
- Reduced Downtime: Reliable conveyor belts reduce the frequency of breakdowns and maintenance-related interruptions. This reduction in downtime translates to more consistent and efficient production cycles.
- Consistent Material Flow: Efficient material transport systems ensure a steady flow of materials through the various stages of processing. This consistency is crucial for optimizing the performance of crushers, screens, and other equipment, leading to higher overall productivity.
Cost Savings
Investing in a reliable crusher conveyor belt can result in significant cost savings over time. These savings come from reduced maintenance costs, lower energy consumption, and improved operational efficiency.
- Lower Maintenance Costs: High-quality conveyor belts are designed to withstand the rigors of heavy-duty applications, reducing the need for frequent repairs and replacements. This durability leads to lower maintenance costs and extends the lifespan of the conveyor system.
- Energy Efficiency: Efficient conveyor systems are optimized for energy consumption, reducing the overall energy costs associated with material transport. Energy-efficient belts and motors help lower the plant’s operational expenses.
- Reduced Labor Costs: Automated conveyor systems reduce the need for manual material handling, leading to lower labor costs and increased operational efficiency. Automation also minimizes the risk of human error and improves overall safety.
Enhanced Safety
A reliable crusher conveyor belt enhances the safety of the material handling process by minimizing the risk of accidents and injuries. Conveyor belts reduce the need for manual handling of heavy and potentially hazardous materials, protecting workers from physical strain and exposure to dangerous conditions.
- Improved Workplace Safety: Automated and well-maintained conveyor systems reduce the likelihood of accidents caused by material spills, equipment malfunctions, or manual handling. This improved safety leads to a healthier and more productive workforce.
- Compliance with Regulations: Reliable conveyor systems help plants comply with safety regulations and standards, avoiding potential fines and legal issues. Ensuring that the conveyor belts meet industry safety requirements is essential for maintaining a safe and compliant operation.
Optimized Performance
Using a high-quality crusher conveyor belt ensures that the material handling process operates at peak performance. Reliable conveyor belts are designed to handle the specific demands of stone crusher plants, providing optimal performance under challenging conditions.
- High Load Capacity: Crusher conveyor belts are built to handle the heavy loads and high impact forces associated with transporting crushed materials. Their robust construction ensures that they can withstand the demands of the application without compromising performance.
- Durability and Longevity: The durability of high-quality conveyor belts ensures that they can operate effectively over long periods, reducing the need for frequent replacements and minimizing downtime. This longevity contributes to the overall efficiency and reliability of the material handling process.
Environmental Benefits
Efficient and reliable material transport systems can also contribute to environmental sustainability by reducing energy consumption and minimizing waste. High-quality conveyor belts are designed to operate efficiently, reducing the environmental impact of the material handling process.
- Energy Efficiency: Optimized conveyor systems use less energy to transport materials, reducing the plant’s overall carbon footprint. Energy-efficient belts and motors help conserve resources and lower greenhouse gas emissions.
- Waste Reduction: Reliable conveyor belts minimize material spills and losses during transport, reducing waste and improving resource utilization. This waste reduction contributes to more sustainable and environmentally friendly operations.
FAQS about Crusher Conveyor Belt
The phrase “difference between conveyor belt and conveyor belt” seems to imply a need to distinguish between two contexts or types of conveyor belts. Generally, the term “conveyor belt” refers to a single component in a conveyor system, which is the continuous loop of material used to transport goods. However, differences can arise based on specific characteristics or applications:
Material and Construction: Conveyor belts can differ in the materials used (e.g., rubber, PVC, PU, metal) and their construction (e.g., single ply vs. multi-ply, reinforced with fabric or steel).
Intended Use: Conveyor belts are designed for various applications, such as general-purpose transportation, food processing, heavy-duty mining, and specialized tasks like sorting or packaging.
Special Features: Some conveyor belts are designed with specific features, such as cleats for inclined transport, modular links for flexibility and easy cleaning, or metal reinforcements for high-temperature and abrasive conditions.
Conveyor belts are made from various materials, depending on their intended use and the type of materials they will transport. Common materials include:
Rubber: Often used for general-purpose belts, rubber offers flexibility, durability, and resistance to abrasion and impact. Reinforced with fabric layers or steel cords, rubber conveyor belts can handle heavy loads and harsh conditions.
PVC (Polyvinyl Chloride): PVC belts are lightweight, flexible, and resistant to chemicals, oils, and fats, making them suitable for food processing and packaging industries.
PU (Polyurethane): Known for its excellent abrasion resistance and durability, PU is used in conveyor belts for industries that require high wear resistance, such as automotive and metalworking.
Fabric: Materials like polyester, nylon, and cotton are used to reinforce conveyor belts, providing tensile strength and flexibility.
Metal: Stainless steel and other metals are used for conveyor belts in extreme conditions, such as high temperatures or when conveying sharp, heavy, or abrasive materials.
The three primary types of conveyor belts are flat belts, modular belts, and cleated belts.
Flat Belts: These are the most common type of conveyor belts, used for transporting items in a straight line. They consist of a continuous loop of material, such as rubber or fabric, and are used in various industries, including manufacturing, warehousing, and food processing.
Modular Belts: These belts are made from interlocking plastic modules, offering flexibility and easy maintenance. They are ideal for applications requiring frequent cleaning and high levels of hygiene, such as in the food and beverage industry. Modular belts can also navigate curves and inclines, making them versatile for complex conveyor systems.
Cleated Belts: These belts have raised sections or cleats that help in transporting materials up steep inclines or preventing them from rolling back. Cleated belts are commonly used in industries like agriculture, mining, and recycling, where materials need to be moved at an angle or require extra grip to prevent slipping.
A crusher conveyor belt is a specialized type of conveyor belt used primarily in the mining and construction industries. Its main function is to transport crushed materials, such as rocks, gravel, and sand, from a crusher to another processing or storage area. These belts are designed to handle heavy loads and resist abrasion, impact, and wear. Typically, they are made from durable materials like reinforced rubber with layers of fabric or steel cords for added strength. The robust construction of crusher conveyor belts ensures they can withstand the harsh conditions and heavy-duty requirements of transporting large, sharp, and abrasive materials.
Last Updated on August 23, 2024 by Jordan Smith
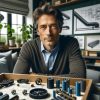
Jordan Smith, a seasoned professional with over 20 years of experience in the conveyor system industry. Jordan’s expertise lies in providing comprehensive solutions for conveyor rollers, belts, and accessories, catering to a wide range of industrial needs. From initial design and configuration to installation and meticulous troubleshooting, Jordan is adept at handling all aspects of conveyor system management. Whether you’re looking to upgrade your production line with efficient conveyor belts, require custom conveyor rollers for specific operations, or need expert advice on selecting the right conveyor accessories for your facility, Jordan is your reliable consultant. For any inquiries or assistance with conveyor system optimization, Jordan is available to share his wealth of knowledge and experience. Feel free to reach out at any time for professional guidance on all matters related to conveyor rollers, belts, and accessories.