How Trough Belt Conveyor Enhances Waste Recycling
A trough belt conveyor is an essential tool in industries that require the efficient handling of bulk materials. These conveyors feature a belt that forms a trough shape, created by angled rollers or idlers, which helps contain the transported materials. The design ensures minimal spillage and efficient movement of items such as grains, waste, and recyclables. Trough belt conveyors are widely used in industries like agriculture, waste management, and mining due to their ability to transport large volumes of bulk materials smoothly and efficiently. By preventing material loss and reducing manual handling, these conveyors enhance productivity and operational efficiency in various industrial applications.
Trough Belt Conveyor
A trough belt conveyor is a type of conveyor system designed to transport bulk materials by forming the belt into a trough shape. This design increases the carrying capacity and prevents material spillage, making it ideal for transporting loose or granular materials such as grains, coal, ore, and sand. Optimizing the performance of a trough belt conveyor is essential for ensuring efficient and reliable operation in various industrial applications.
Optimizing Trough Belt Conveyor Performance
Optimizing the performance of a trough belt conveyor involves several best practices and maintenance strategies. These measures are crucial for enhancing efficiency, reducing downtime, and extending the conveyor’s lifespan.
Tips and Best Practices for Maintaining and Optimizing the Performance of Trough Belt Conveyors
Proper Belt Alignment:
- Ensuring the conveyor belt is correctly aligned is fundamental to the efficient operation of a trough belt conveyor. Misalignment can cause uneven wear, material spillage, and increased energy consumption.
- Regularly check and adjust the alignment of the belt. Utilize alignment tools and sensors to detect and correct any deviations promptly.
Regular Cleaning:
- Accumulated debris and material build-up on the belt and components can hinder performance and cause wear. Regular cleaning prevents these issues and ensures smooth operation.
- Implement a routine cleaning schedule, focusing on both the belt surface and the conveyor components such as rollers and idlers.
Lubrication of Moving Parts:
- Proper lubrication of moving parts, such as bearings and rollers, reduces friction and wear, thereby enhancing the conveyor’s efficiency and lifespan.
- Use appropriate lubricants and follow the manufacturer’s recommendations for lubrication intervals and methods.
Inspection and Replacement of Worn Parts:
- Regular inspection of the conveyor components is essential to identify and replace worn or damaged parts before they cause significant issues.
- Pay special attention to the belt, rollers, idlers, and pulleys. Replace any parts showing signs of excessive wear or damage.
Tension Adjustment:
- Maintaining the correct belt tension is crucial for preventing slippage, reducing wear, and ensuring efficient material transport.
- Regularly check the belt tension and adjust it according to the manufacturer’s specifications. Use tensioning devices and tools to achieve the desired tension level.
Monitoring and Control Systems:
- Implementing monitoring and control systems can enhance the performance of a trough belt conveyor. These systems provide real-time data on the conveyor’s operation and help identify potential issues before they escalate.
- Use sensors and automated controls to monitor parameters such as belt speed, load, and alignment. Integrate these systems with maintenance schedules for proactive management.
Training and Safety Practices:
- Proper training for operators and maintenance personnel is essential for safe and efficient conveyor operation. Ensure that all staff members are familiar with the best practices and safety protocols.
- Conduct regular training sessions and safety drills to reinforce the importance of proper handling and maintenance procedures.
Importance of Regular Maintenance and Inspection to Ensure Longevity and Efficiency
Regular maintenance and inspection are vital for the longevity and efficiency of a trough belt conveyor. Neglecting these aspects can lead to several issues, including increased downtime, higher operational costs, and reduced equipment lifespan.
Preventing Unscheduled Downtime:
- Unscheduled downtime due to equipment failure can be costly and disruptive. Regular maintenance helps identify potential issues early, allowing for timely repairs and preventing unexpected breakdowns.
- Implement a preventive maintenance program that includes scheduled inspections, cleaning, lubrication, and part replacements.
Enhancing Equipment Lifespan:
- Proper maintenance practices, such as regular cleaning, lubrication, and part replacement, significantly extend the lifespan of the conveyor components.
- A well-maintained trough belt conveyor operates more efficiently and with less wear and tear, reducing the need for frequent replacements and repairs.
Improving Energy Efficiency:
- An efficiently operating conveyor system consumes less energy, reducing operational costs. Regular maintenance ensures that the conveyor runs smoothly and without unnecessary friction or resistance.
- Monitor energy consumption and make adjustments to improve efficiency, such as optimizing belt tension and alignment.
Ensuring Safety:
- Regular inspection and maintenance of the trough belt conveyor ensure that safety hazards are identified and addressed promptly. This reduces the risk of accidents and injuries.
- Adhere to safety standards and protocols, and conduct regular safety audits to ensure compliance.
Optimizing Performance:
- A well-maintained trough belt conveyor performs optimally, with minimal interruptions and maximum efficiency. Regular maintenance ensures that the conveyor can handle the required load and operate at the desired speed.
- Use performance metrics to monitor and optimize the conveyor’s operation continuously.
What is Trough Belt Conveyor
A trough belt conveyor is an essential piece of equipment in many industrial operations, providing a reliable and efficient means of transporting bulk materials. Its design features a belt that forms a trough shape, which helps contain and support the materials being conveyed. This detailed discussion will explore the intricacies of trough belt conveyors, including their structure, benefits, and integration with other conveyor types such as cleated belt conveyors.
Cleated Belt Conveyor
Introduction to Cleated Belt Conveyors and Their Unique Features
Cleated belt conveyors are specialized types of conveyors designed to handle materials on steep inclines and declines. The unique feature of cleated belt conveyors is the addition of cleats, which are raised dividers on the surface of the belt. These cleats help in preventing the material from sliding back, ensuring efficient and consistent transport even on steep slopes.
Key Features of Cleated Belt Conveyors:
- Cleats: The primary feature, cleats are spaced at regular intervals along the belt and come in various shapes and sizes depending on the application. They can be straight, curved, or V-shaped, tailored to handle different types of materials and transport needs.
- Belt Material: Cleated belts are typically made from durable materials such as rubber, PVC, or metal, designed to withstand heavy loads and harsh conditions. The material choice depends on the specific requirements of the application, including temperature resistance, chemical resistance, and abrasion resistance.
- Modularity: Many cleated belt conveyors are modular, allowing for easy customization and reconfiguration. This flexibility makes them suitable for a wide range of industrial applications, from food processing to mining.
Use Cases Where Cleated Belts Provide Enhanced Material Transport, Especially on Inclines
Cleated belt conveyors excel in scenarios where materials need to be transported on inclines or declines. The addition of cleats prevents the material from sliding, ensuring a steady and efficient flow. Here are some common use cases:
Inclined Conveying in Manufacturing
In manufacturing plants, materials often need to be transported between different levels of the facility. Cleated belt conveyors are ideal for these tasks, as they can handle steep inclines without the risk of material slippage. This capability is particularly useful in assembly lines where components must be moved efficiently and reliably.
Agricultural Applications
In the agricultural sector, cleated belt conveyors are used to transport bulk materials such as grains, seeds, and fertilizers. The cleats ensure that these materials are moved smoothly up steep inclines, such as those found in grain elevators or storage facilities. This efficient transport system helps in maintaining a consistent flow of materials, reducing downtime and increasing productivity.
Mining and Quarrying
In mining and quarrying operations, transporting materials like ores, rocks, and minerals often involves navigating challenging terrains with steep inclines. Cleated belt conveyors provide the necessary grip and stability to move these heavy materials efficiently. The robust construction of these conveyors ensures they can withstand the harsh conditions typically found in mining environments.
Food Processing
The food processing industry benefits greatly from cleated belt conveyors, especially in applications where products need to be transported at an angle. For instance, in vegetable and fruit processing plants, cleated belts can be used to move produce from washing stations to packaging areas. The cleats prevent the produce from rolling back, ensuring a smooth and continuous flow through the processing line.
Integration of Cleated Belts with Trough Belt Conveyors
Integrating cleated belts with trough belt conveyors can provide a comprehensive material handling solution that maximizes efficiency and versatility. Trough belt conveyors, with their ability to form a trough shape, are excellent for containing bulk materials, while cleated belts excel at transporting materials on inclines.
Benefits of Integration:
- Enhanced Containment: The trough shape of the conveyor belt helps to contain materials, preventing spillage and loss. When combined with cleats, this design ensures that materials are not only contained but also securely transported up or down inclines.
- Versatility: The combination of trough and cleated belt conveyors provides a versatile solution that can handle a wide range of materials and transport requirements. This versatility makes it easier to design systems that can efficiently manage different stages of material handling, from horizontal transport to steep inclines.
- Increased Efficiency: Integrating cleated belts with trough conveyors can significantly increase the efficiency of material transport systems. The cleats ensure that materials are moved steadily without sliding, while the trough shape provides stability and containment, reducing the risk of spillage and waste.
How about Trough Belt Conveyor
A trough belt conveyor is designed to transport bulk materials by forming the belt into a trough shape, which increases its carrying capacity and prevents material spillage. This type of conveyor is ideal for handling loose or granular materials such as grains, coal, ore, and sand. For optimal performance and reliability, it’s essential to understand the various components and their roles, including roller bed belt conveyors.
Roller Bed Belt Conveyor
Roller bed belt conveyors are a specific type of conveyor system where the belt is supported by rollers instead of a flat surface. This design reduces friction and allows for smoother and more efficient material handling, especially over longer distances and with heavier loads.
Description of Roller Bed Belt Conveyors and Their Role in Supporting and Guiding the Belt
Roller bed belt conveyors consist of a series of rollers arranged horizontally along the length of the conveyor. The belt runs over these rollers, which support the belt and the load it carries. The rollers are typically spaced at regular intervals to provide consistent support and minimize sagging.
The primary roles of roller bed belt conveyors in a troughed belt conveyor system include:
- Support: The rollers support the weight of the belt and the material being transported. This support is crucial for maintaining the belt’s shape and preventing it from sagging, which can lead to misalignment and increased wear.
- Guidance: The rollers help guide the belt along its path, ensuring that it runs smoothly and remains properly aligned. This guidance reduces the risk of the belt slipping off track and minimizes the potential for material spillage.
- Reduced Friction: By supporting the belt on rollers, rather than a flat surface, roller bed belt conveyors significantly reduce friction. This reduction in friction lowers the power required to move the belt, resulting in energy savings and less wear on the conveyor components.
- Load Distribution: The rollers distribute the load evenly across the belt, reducing stress on any single point and enhancing the overall durability of the conveyor system. This even distribution is particularly important when handling heavy or bulky materials.
Benefits of Using Roller Bed Belt Conveyors in Material Handling
The use of roller bed belt conveyors in material handling offers several advantages that enhance the efficiency, durability, and overall performance of the conveyor system.
Increased Efficiency:
- The reduced friction between the belt and the supporting structure means that roller bed belt conveyors require less energy to operate. This increased efficiency can result in significant energy savings, particularly in large-scale industrial operations where conveyors run continuously.
Enhanced Durability:
- By reducing friction and evenly distributing the load, roller bed belt conveyors experience less wear and tear. This enhanced durability translates to a longer lifespan for the belt and rollers, reducing the frequency and cost of maintenance and replacements.
Smooth Operation:
- The rollers provide a smooth surface for the belt to glide over, which minimizes vibrations and noise during operation. This smooth operation is beneficial in environments where reducing noise pollution is important for worker comfort and safety.
Versatility:
- Roller bed belt conveyors are versatile and can be used in a wide range of applications, from light to heavy-duty material handling. They are suitable for transporting various types of materials, including loose bulk items, packaged goods, and fragile items that require gentle handling.
Scalability:
- These conveyors can be easily scaled up or down to meet the specific needs of an operation. Additional rollers can be added to accommodate longer distances or heavier loads, making roller bed belt conveyors adaptable to changing production requirements.
Reduced Maintenance:
- The reduced friction and even load distribution lead to less wear on the belt and rollers, decreasing the need for frequent maintenance. When maintenance is required, the modular design of roller bed conveyors allows for quick and easy replacement of individual rollers or sections of the belt.
Improved Safety:
- With smoother operation and less wear, roller bed belt conveyors contribute to a safer working environment. The risk of belt slippage, misalignment, and material spillage is minimized, reducing the likelihood of accidents and injuries.
The Keys of Trough Belt Conveyor
The trough belt conveyor is an essential tool in many industries for the efficient transportation of bulk materials. Its unique design, featuring a belt that forms a trough shape, helps contain and support materials during transport, making it especially useful for handling loose or bulk items. To fully appreciate the benefits of a trough belt conveyor, it is helpful to compare it with the flat belt conveyor, another common type of conveyor system.
Flat Belt Conveyor vs. Trough Belt Conveyor
Comparison between Flat Belt Conveyors and Trough Belt Conveyors
The Types of Trough Belt Conveyor
A conveyor belt trough is a versatile and efficient means of transporting bulk materials. Its design involves forming the conveyor belt into a trough shape, which increases the carrying capacity and prevents material spillage, making it suitable for transporting loose or granular materials such as grains, coal, ore, and sand. To further enhance the effectiveness of these systems, closed belt conveyor systems can be integrated.
Closed Belt Conveyor Systems
Closed belt conveyor systems are an advanced variation of traditional conveyors designed to prevent material spillage and contamination. These systems enclose the conveyor belt and the transported material, providing a sealed environment that offers several operational advantages.
Explanation of Closed Belt Conveyor Systems and Their Benefits
Closed belt conveyor systems are designed to encapsulate the material being transported, thereby creating a sealed environment that minimizes material loss and environmental contamination. This design can be implemented in various forms, such as tube conveyors, where the belt itself forms a closed loop, or covered conveyors, where the belt runs under a protective cover.
Key Benefits of Closed Belt Conveyor Systems:
Prevention of Material Spillage:
- One of the primary benefits of closed belt conveyor systems is the prevention of material spillage. By enclosing the belt and the material, these systems ensure that even fine or powdery substances are contained within the conveyor, reducing loss and keeping the surrounding area clean.
Environmental Protection:
- Closed belt conveyors offer significant environmental protection. They prevent dust and fine particles from escaping into the air, which is particularly important in industries handling hazardous or toxic materials. This containment helps to maintain air quality and comply with environmental regulations.
Protection from External Contaminants:
- The sealed design of closed belt conveyors protects the transported material from external contaminants such as dust, moisture, and debris. This is crucial in industries where the purity of the material is essential, such as food processing or pharmaceuticals.
Enhanced Safety:
- Enclosing the conveyor belt and material enhances workplace safety by reducing the risk of accidents related to material spillage. It also protects workers from exposure to hazardous materials and minimizes the risk of respiratory issues caused by airborne particles.
Reduced Maintenance Requirements:
- By preventing material spillage and contamination, closed belt conveyors reduce the amount of maintenance required to clean the surrounding area and the conveyor itself. This leads to lower maintenance costs and less downtime for cleaning and repairs.
Longer Equipment Lifespan:
- The enclosed design protects the conveyor components from wear and tear caused by abrasive materials and environmental factors. This protection extends the lifespan of the conveyor system and reduces the frequency of part replacements.
Operational Efficiency:
- Closed belt conveyors operate more efficiently by maintaining a consistent flow of material without interruptions caused by spillage or contamination. This consistent flow enhances productivity and ensures that the conveyor system meets production targets.
Applications Where Closed Belt Conveyors Are Preferable for Preventing Material Spillage
Closed belt conveyor systems are particularly beneficial in industries and applications where preventing material spillage and maintaining a clean environment are critical.
1. Mining and Quarrying:
- In mining and quarrying operations, closed belt conveyors are used to transport bulk materials such as coal, ore, and aggregates. The enclosed design prevents material loss during transportation and protects the environment from dust and debris.
2. Chemical Processing:
- Chemical plants often handle hazardous materials that require containment to prevent environmental contamination and ensure worker safety. Closed belt conveyors provide the necessary protection by enclosing the material and preventing exposure to harmful substances.
3. Food Processing:
- In the food processing industry, maintaining the purity and quality of the product is paramount. Closed belt conveyors prevent contamination from external sources and ensure that the food products remain clean and safe for consumption. They are used to transport ingredients, raw materials, and finished products in a hygienic environment.
4. Cement and Building Materials:
- The production and transportation of cement and building materials generate a significant amount of dust and fine particles. Closed belt conveyors are used to contain these materials, preventing dust from escaping and maintaining a clean working environment. This containment also ensures that valuable material is not lost during transportation.
5. Power Plants:
- In power plants, particularly those that use coal, closed belt conveyors are used to transport fuel and by-products such as ash. The enclosed design prevents the release of dust and fine particles, protecting the environment and ensuring efficient fuel handling.
6. Pharmaceuticals:
- The pharmaceutical industry requires stringent control over the handling and transportation of raw materials and finished products. Closed belt conveyors provide the necessary containment to protect these sensitive materials from contamination and ensure compliance with regulatory standards.
7. Agriculture:
- In agricultural operations, closed belt conveyors are used to transport grains, seeds, and other bulk materials. The enclosed design prevents loss of material during transportation and protects the product from external contaminants such as dust and moisture.
How to Choose Trough Belt Conveyor
A trough belt conveyor is a crucial piece of equipment in many industries, designed to efficiently transport bulk materials. Its unique design, featuring a belt that forms a trough shape, helps contain and support materials during transport, minimizing spillage and ensuring smooth operation. This detailed discussion explores the key design principles of trough belt conveyors, the differences between open and closed designs, and the advantages of using design PDF resources for planning and implementation.
Trough Belt Conveyor Design
Key Design Principles of Trough Belt Conveyors
The design of a trough belt conveyor revolves around several core principles that ensure efficient material handling and longevity of the system. These principles include:
- Belt Troughing: The primary feature of a trough belt conveyor is its ability to form a trough shape. This is achieved using a series of idlers, typically set at angles of 20°, 35°, or 45°, which support the belt and create the desired trough profile. This shape helps contain the bulk material, reducing spillage and improving the overall efficiency of material transport.
- Idler Spacing: The spacing of idlers along the conveyor is crucial for providing adequate support to the belt and the transported materials. Closer idler spacing is generally used in areas with heavy loads or where the material being transported is particularly dense.
- Belt Width and Speed: The width and speed of the belt are designed based on the volume and type of material to be transported. Wider belts can carry larger volumes, while the speed of the belt determines the rate of material transport. These parameters must be carefully calculated to balance capacity and efficiency.
- Load Capacity: The design must account for the maximum load the conveyor will carry. This includes considering the weight and bulk density of the materials, as well as the potential for material surges that could overload the system.
- Material Properties: The physical characteristics of the materials being transported, such as abrasiveness, moisture content, and particle size, influence the choice of belt material and the overall conveyor design. For example, abrasive materials may require belts with reinforced surfaces to withstand wear and tear.
- Drive and Tension Systems: The conveyor’s drive system, typically powered by electric motors, must be robust enough to handle the load. Additionally, proper tensioning mechanisms are essential to maintain belt alignment and prevent slippage.
Differences Between Open and Closed Belt Conveyor Designs
Trough belt conveyors can be designed with either open or closed configurations, each offering distinct advantages based on the application.
Open Belt Conveyor Design
- Accessibility: Open belt conveyors are designed without an enclosing cover, making them easily accessible for maintenance and inspection. This design is suitable for applications where regular monitoring and quick access to the belt and components are required.
- Cost-Effective: The open design tends to be more cost-effective in terms of initial construction and maintenance. It is simpler to build and does not require additional materials for enclosures.
- Suitability for Non-Hazardous Materials: Open conveyors are typically used for transporting non-hazardous materials where environmental exposure does not pose significant risks. They are common in industries such as mining and agriculture where bulk materials like ore, grain, and aggregates are transported.
Closed Belt Conveyor Design
- Containment: Closed belt conveyors, also known as enclosed belt conveyors, feature a cover that encases the entire conveyor system. This design provides superior containment of the transported materials, preventing spillage and reducing dust emissions.
- Protection from Elements: The closed design protects the materials and the conveyor components from external elements such as weather, reducing the risk of contamination and wear due to environmental factors.
- Safety and Environmental Control: Closed conveyors are ideal for transporting hazardous or sensitive materials that must be contained to prevent environmental contamination or protect worker safety. They are commonly used in industries such as chemicals, food processing, and pharmaceuticals.
Advantages of Using Trough Belt Conveyor Design PDF Resources for Planning and Implementation
Utilizing trough belt conveyor design PDF resources offers several advantages for the planning and implementation of conveyor systems:
- Comprehensive Information: Design PDFs provide detailed information on all aspects of trough belt conveyor design, including component specifications, installation guidelines, and maintenance procedures. This comprehensive documentation helps ensure that all design considerations are thoroughly addressed.
- Standardization: Design PDFs often adhere to industry standards and best practices, ensuring that the conveyor systems meet regulatory requirements and perform reliably. This standardization helps avoid design flaws and operational issues.
- Ease of Access and Sharing: PDF resources are easily accessible and can be shared among team members, contractors, and stakeholders. This facilitates collaboration and ensures that everyone involved in the project has access to the same information.
- Customization and Scalability: Many design PDFs offer templates and customizable options that can be tailored to specific project needs. This flexibility allows engineers to adapt the designs to different applications and scale them according to the project’s requirements.
- Visualization and Planning: Design PDFs often include diagrams, charts, and illustrations that help visualize the conveyor system. These visual aids are invaluable for planning, enabling engineers to identify potential issues and optimize the design before construction begins.
- Training and Reference: Detailed design PDFs serve as valuable reference materials for training personnel on the operation and maintenance of the conveyor system. This ensures that staff are well-equipped to manage the system effectively, reducing the likelihood of operational disruptions.
FAQS about Trough Belt Conveyors
The three primary types of conveyors are belt conveyors, roller conveyors, and chain conveyors.
Belt Conveyors: These are the most common type, using a continuous belt made of fabric, rubber, or metal to move materials from one point to another. They are versatile and used in a wide range of industries, including manufacturing, mining, and logistics.
Roller Conveyors: These conveyors use a series of rollers, either powered or gravity-driven, to transport items. They are often used in warehouses and distribution centers for moving packages, pallets, and other items that have a flat bottom. Roller conveyors are ideal for sorting, packing, and assembly applications.
Chain Conveyors: These systems use chains to move heavy loads, often found in industries like automotive, where they transport car parts through assembly lines. Chain conveyors are robust and capable of handling large, heavy items that are unsuitable for belt or roller conveyors.
Each type of conveyor offers unique benefits and is suited to specific applications, making them essential components in modern material handling and logistics operations.
Trough belt conveyors offer several advantages over other types of conveyor systems. Firstly, their design allows for efficient transportation of bulk materials by containing the load within the trough, reducing spillage and waste. This makes them ideal for industries such as mining, agriculture, and construction, where large quantities of loose materials need to be moved. Secondly, trough belt conveyors can handle a variety of materials, from fine powders to large rocks, providing versatility in application. Additionally, they can operate over long distances and across challenging terrains, thanks to their ability to handle inclines and declines. The curved design also helps in evenly distributing the load, reducing wear and tear on the belt and extending its lifespan. Overall, trough belt conveyors are a reliable and cost-effective solution for bulk material handling.
The primary difference between a flat belt conveyor and a troughed belt conveyor lies in the shape and function of the belt. A flat belt conveyor features a flat, horizontal belt that is ideal for transporting lightweight, uniform items or products on a level surface. In contrast, a troughed belt conveyor has a curved or concave belt, supported by angled idlers or rollers, which creates a trough-like shape. This design is specifically suited for carrying bulk materials and preventing spillage. While flat belt conveyors are commonly used in manufacturing and packaging industries, troughed belt conveyors are favored in industries that handle bulk, loose materials, such as mining, agriculture, and construction, due to their ability to contain and transport large volumes efficiently.
A trough belt conveyor is a type of conveyor system that features a belt with a curved or “troughed” shape, formed by rollers or idlers placed in a way that creates a concave profile. This design allows the belt to carry bulk materials more efficiently by preventing spillage and containing the load within the trough. Trough belt conveyors are commonly used in industries such as mining, agriculture, and construction, where they transport loose or bulk materials like sand, gravel, grain, or coal. The trough shape can vary in angle, typically ranging from 20 to 45 degrees, depending on the material being conveyed and the desired capacity.
Last Updated on August 9, 2024 by Jordan Smith
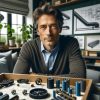
Jordan Smith, a seasoned professional with over 20 years of experience in the conveyor system industry. Jordan’s expertise lies in providing comprehensive solutions for conveyor rollers, belts, and accessories, catering to a wide range of industrial needs. From initial design and configuration to installation and meticulous troubleshooting, Jordan is adept at handling all aspects of conveyor system management. Whether you’re looking to upgrade your production line with efficient conveyor belts, require custom conveyor rollers for specific operations, or need expert advice on selecting the right conveyor accessories for your facility, Jordan is your reliable consultant. For any inquiries or assistance with conveyor system optimization, Jordan is available to share his wealth of knowledge and experience. Feel free to reach out at any time for professional guidance on all matters related to conveyor rollers, belts, and accessories.