Different Types of Conveyor Belt Pulley Explained
Conveyor belt pulleys play a crucial role in the efficiency and functionality of conveyor belt systems, widely used in various industrial applications. These pulleys, positioned at strategic points within the system, are responsible for driving, redirecting, and tensioning the conveyor belt. The significance of a conveyor belt pulley lies in its ability to ensure smooth and continuous movement of materials, contributing to increased productivity and reduced downtime. Understanding the role of a conveyor belt pulley is essential for optimizing the performance of conveyor systems. By effectively managing the belt’s motion, pulleys help in maintaining consistent speed and direction, making them indispensable components in industries such as mining, manufacturing, and logistics.
Conveyor Belt Pulley Types
Different Types of Conveyor Belt Pulleys
Conveyor belt pulleys are integral components in conveyor systems, each type designed to serve specific functions and applications. Understanding the various types of belt conveyor pulleys and their unique features can help in selecting the right pulley for your industrial needs, enhancing efficiency and productivity. Here, we explore the main types of conveyor belt pulleys, including drum pulleys, wing pulleys, and turbine pulleys, along with specialized pulleys for specific applications.
Drum Pulleys
Drum pulleys, also known as cylindrical pulleys, are the most common type of belt conveyor pulley. They are used at both the head and tail of the conveyor system to drive and support the belt. Drum pulleys are typically constructed from rolled shells with welded end discs and are designed to withstand high stress and heavy loads.
Characteristics of Drum Pulleys:
- Structure: Drum pulleys have a smooth, cylindrical surface, which provides excellent contact with the conveyor belt, ensuring efficient transmission of power.
- Materials: They are usually made from steel or aluminum, chosen for their strength and durability.
- Applications: Drum pulleys are used in various industries, including mining, aggregate, and bulk material handling, where robust performance is essential.
Benefits of Drum Pulleys:
- Durability: Due to their solid construction, drum pulleys can handle high loads and are resistant to wear and tear.
- Maintenance: They require minimal maintenance compared to other types of pulleys, reducing downtime and operational costs.
- Versatility: Drum pulleys can be used in both heavy-duty and light-duty applications, making them highly versatile.
Wing Pulleys
Wing pulleys, also known as self-cleaning pulleys, are designed to operate in challenging environments where debris and buildup can occur. They feature a series of wings or fins that extend from the hub to the edge of the pulley, creating gaps that allow material to escape.
Characteristics of Wing Pulleys:
- Structure: The unique design with wings helps to shed material that could otherwise cause belt mistracking or damage.
- Materials: Wing pulleys are commonly made from high-strength steel to endure harsh conditions and abrasive materials.
- Applications: They are ideal for environments such as mining, construction, and recycling, where materials like dirt, mud, and rocks are prevalent.
Benefits of Wing Pulleys:
- Self-Cleaning: The wing design prevents buildup, ensuring continuous operation and reducing the risk of belt damage.
- Reduced Wear: By allowing debris to escape, wing pulleys reduce the wear on both the pulley and the conveyor belt.
- Improved Tracking: Wing pulleys help maintain proper belt alignment, improving overall system efficiency.
Turbine Pulleys
Turbine pulleys are less common but highly effective in specific applications. These pulleys have a series of radial fins or blades that provide additional grip and cooling effects.
Characteristics of Turbine Pulleys:
- Structure: Turbine pulleys feature radial fins that increase surface area and enhance cooling.
- Materials: They are typically made from high-grade materials such as stainless steel or aluminum, designed to resist corrosion and heat.
- Applications: Turbine pulleys are used in high-temperature environments or applications requiring enhanced belt grip, such as in power generation or high-speed conveyors.
Benefits of Turbine Pulleys:
- Enhanced Grip: The fins provide better traction, reducing slippage and improving power transmission.
- Cooling Effect: The design promotes air circulation, helping to dissipate heat and extend the life of the pulley and belt.
- Specialized Performance: Turbine pulleys are suited for high-speed and high-temperature operations, offering specialized performance where needed.
Specialized Pulleys for Specific Applications
In addition to the standard types of conveyor belt pulleys, there are specialized pulleys designed for specific applications. These include:
Magnetic Pulleys:
- Purpose: Used to remove ferrous contaminants from material streams.
- Applications: Commonly found in recycling and waste management systems.
Snub Pulleys:
- Purpose: Increase the wrap angle of the belt around the drive pulley for better traction.
- Applications: Used in high-tension applications where additional belt support is needed.
Tension Pulleys:
- Purpose: Maintain proper belt tension, preventing slippage and ensuring smooth operation.
- Applications: Used in systems where precise tension control is critical, such as in packaging or textile industries.
Understanding the various types of pulley for conveyor belts and their specific applications helps in selecting the right pulley for your conveyor system. Each type offers unique benefits, whether it’s the durability of drum pulleys, the self-cleaning properties of wing pulleys, the specialized performance of turbine pulleys, or the targeted functions of magnetic, snub, and tension pulleys. Proper selection and maintenance of conveyor belt pulleys ensure optimal performance, longevity, and efficiency of the conveyor system.
Head and Tail Conveyor Belt Pulley
Head and Tail Pulleys in the Conveyor System
Conveyor belt pulleys, particularly head and tail pulleys, are fundamental components of conveyor systems, each serving distinct yet complementary roles that ensure the seamless operation of the entire system. The head pulley is located at the discharge end of the conveyor, driving the belt and controlling its speed, while the tail pulley is situated at the loading end, providing tension to keep the belt tight and on track.
Head Pulley
The head pulley, often referred to as the drive pulley, is crucial as it powers the conveyor belt. It is connected to a motor which generates the necessary force to move the belt and transport materials along the conveyor. The head pulley is typically larger in diameter than other pulleys to maximize the grip and minimize slippage.
Roles and Importance:
- Driving the Belt: The primary function of the head pulley is to drive the conveyor belt. The motor attached to the head pulley ensures that the belt moves consistently and at the desired speed, essential for maintaining the workflow in various industrial applications.
- Speed Control: The head pulley controls the speed of the belt, which is vital for processes that require precise timing and coordination. Adjusting the speed can help in optimizing the throughput and efficiency of the conveyor system.
- Discharge Point: As the belt reaches the head pulley, it discharges the materials being transported. Proper design and alignment of the head pulley are essential to ensure that the materials are discharged smoothly and accurately to the next stage of processing.
- Tension Maintenance: The head pulley helps in maintaining the necessary tension in the belt, ensuring that it remains tight and does not sag or slip. Proper tension is crucial for the efficient operation of the conveyor system.
- Load Management: The head pulley must be robust and well-constructed to handle the load of the materials being transported. It plays a vital role in managing the load and ensuring that the belt can carry materials without excessive wear or damage.
Tail Pulley
The tail pulley, located at the opposite end of the conveyor system, is equally important. While it does not drive the belt, its role in maintaining tension and tracking is crucial for the system’s overall performance.
Roles and Importance:
- Tension Adjustment: The tail pulley is adjustable, allowing for the tension of the conveyor belt to be maintained or adjusted as needed. Proper tension ensures that the belt remains in alignment and prevents issues such as belt sagging or slipping.
- Belt Tracking: The tail pulley helps in guiding the belt and keeping it centered on the conveyor structure. Misalignment can lead to uneven wear, material spillage, and reduced efficiency, making the tail pulley essential for proper belt tracking.
- Load Support: Like the head pulley, the tail pulley supports the load of the materials being transported. It must be sturdy and well-maintained to ensure that it can handle the weight and stress of the materials on the conveyor.
- Direction Change: The tail pulley can also change the direction of the belt’s movement, allowing for flexibility in conveyor system design. This feature is particularly useful in systems that require multiple conveyors working in tandem.
- Belt Cleaning: The tail pulley often incorporates belt cleaning devices such as scrapers or brushes. These devices help in removing any debris or buildup on the belt, ensuring that the conveyor system remains clean and operates efficiently.
Understanding the distinct roles and importance of head and tail pulleys in conveyor belt pulley systems is crucial for maintaining the efficiency and reliability of conveyor operations across various industries. Proper selection, installation, and maintenance of these pulleys ensure optimal performance and longevity of the conveyor system.
Conveyor Belt Pulley Sizes
The Variety of Sizes Available and Their Applications
Conveyor belt pulleys come in a wide range of sizes, each tailored to meet specific requirements and applications within industrial settings. The size of conveyor belt pulleys can significantly impact the efficiency and functionality of the conveyor system. This section explores the various sizes of conveyor belt pulleys, their specific applications, and how to determine the right size for your system.
Standard Pulley Sizes and Their Applications
Conveyor belt pulleys are available in various diameters and widths. The size of the pulley affects the belt’s tension, speed, and the overall efficiency of the conveyor system. Below is a table summarizing standard pulley sizes and their typical applications:
How to Determine the Right Size for Your Conveyor System
Selecting the correct conveyor belt pulley size is crucial for the optimal performance of your conveyor system.
- Load Capacity: The size of the pulley should be compatible with the load capacity requirements of the conveyor system. Larger pulleys are better suited for heavy loads, while smaller pulleys are adequate for lighter loads.
- Belt Speed: The pulley size affects the belt speed. A larger diameter pulley will reduce the belt speed, which may be beneficial for delicate or precise handling applications. Conversely, smaller pulleys increase belt speed, suitable for faster material transport.
- Belt Width: The width of the pulley should match the width of the conveyor belt. Ensuring that the belt and pulley widths are compatible is essential to avoid misalignment and uneven wear.
- Application Environment: Consider the operating environment when selecting pulley size. For example, harsh environments such as mining require more robust and larger pulleys to withstand extreme conditions.
- System Design: The overall design and layout of the conveyor system influence pulley size selection. Ensure the pulley size fits within the spatial constraints and integrates seamlessly with other system components.
- Maintenance and Durability: Larger pulleys generally offer better durability and require less frequent maintenance. However, they may also be more challenging to install and replace. Evaluate the maintenance capabilities and requirements of your operation when choosing pulley size.
Steps to Determine the Right Pulley Size
- Assess Load Requirements: Determine the maximum load the conveyor will handle. Use this information to guide your choice of pulley size, ensuring it can support the load without excessive strain.
- Evaluate Belt Speed Needs: Decide on the desired belt speed for your application. Calculate the pulley diameter required to achieve this speed based on the motor’s RPM and the conveyor belt’s operational requirements.
- Match Belt and Pulley Widths: Ensure that the pulley width matches the conveyor belt width to maintain proper alignment and efficient operation.
- Consider Environmental Factors: Analyze the operating environment, including temperature, humidity, and exposure to corrosive materials. Select a pulley size that can withstand these conditions.
- Consult with Manufacturers: Engage with conveyor pulley manufacturers to get expert advice and recommendations. They can provide insights into the best pulley sizes for your specific application and operational conditions.
- Plan for Maintenance: Factor in the ease of maintenance and the expected lifespan of the pulley. Choose a size that balances performance with maintenance requirements to optimize system uptime and longevity.
By carefully considering these factors and following these steps, you can determine the appropriate conveyor belt pulley size for your specific application, ensuring efficient and reliable conveyor system operation.
Conveyor Belt Pulley Manufacturers
Overview of Leading Manufacturers
In the world of pulley in conveyor belt manufacturing, several companies stand out due to their commitment to quality, innovation, and customer satisfaction. Among these industry leaders are Martin Sprocket & Gear, Dodge (a division of ABB), PPI (Precision Pulley & Idler), and Fenner Dunlop. These manufacturers are known for producing high-quality conveyor belt pulleys that meet the rigorous demands of various industrial applications. Below, we provide an overview of these leading manufacturers and what sets them apart in terms of quality and innovation.
Martin Sprocket & Gear
Martin Sprocket & Gear, commonly referred to as Martin, has been a prominent name in the power transmission, material handling, and conveying industries since 1951. They are renowned for their extensive range of conveyor belt and pulley designed to meet various industrial needs.
- Customization: Martin offers customized pulley solutions tailored to specific application requirements.
- Materials: Their pulleys are made from high-quality materials, including steel and aluminum, ensuring durability and longevity.
- Engineering Expertise: Martin’s engineering team provides advanced design services, ensuring optimal pulley performance and integration into conveyor systems.
- Customer Support: They offer excellent customer support, with a focus on helping clients select the right pulley for their needs.
Dodge (a division of ABB)
Dodge, a division of ABB, is a global leader in mechanical power transmission products, including conveyor belt pulleys. They are known for their robust and reliable products that cater to heavy-duty industrial applications.
- Severe Duty Pulley Line: Dodge offers a severe duty pulley line designed for harsh environments, featuring reinforced construction for increased resilience.
- Maintenance-Friendly Designs: Their pulleys are designed for easy maintenance, reducing downtime and operational costs.
- Global Reach: With a global distribution network, Dodge provides comprehensive support and service worldwide.
- Advanced Coating Technologies: Dodge uses advanced coating technologies to enhance pulley resistance to corrosion and wear.
Precision Pulley & Idler (PPI)
Precision Pulley & Idler, commonly known as PPI, has been a leading manufacturer of conveyor components since 1977. They focus on producing innovative and high-quality pulleys and idlers for various industries.
- Engineering Excellence: PPI is known for its engineering excellence, offering pulleys designed to optimize conveyor system performance.
- Product Testing: They implement rigorous testing procedures to ensure product reliability and durability.
- Wide Product Range: PPI provides a broad range of pulley sizes and types, catering to diverse industrial applications.
- Customer-Focused Approach: PPI emphasizes customer satisfaction, providing detailed technical support and customized solutions.
Fenner Dunlop
Fenner Dunlop, a division of Fenner PLC, is a globally recognized manufacturer of conveyor systems and components, including conveyor belt pulleys. They are renowned for their innovative solutions and commitment to quality.
- High-Performance Materials: Fenner Dunlop uses high-performance materials to manufacture pulleys that withstand extreme conditions and heavy loads.
- Innovation: They continuously invest in research and development to introduce cutting-edge technologies in pulley design.
- Global Service Network: Fenner Dunlop has an extensive global service network, ensuring prompt support and availability of products.
- Sustainability Initiatives: They focus on sustainability, using environmentally friendly processes and materials.
Comparison of Leading Conveyor Belt Pulley Manufacturers
What Sets These Manufacturers Apart
The leading manufacturers of conveyor belt pulleys distinguish themselves through a combination of quality, innovation, and customer-focused approaches. Here’s a deeper look at what sets them apart:
- Martin Sprocket & Gear: Known for their customization capabilities, Martin excels in providing tailored pulley solutions to meet specific industrial needs. Their use of high-quality materials and advanced design services ensures that their pulleys deliver optimal performance and durability.
- Dodge (ABB): Dodge stands out with their severe duty pulley line, designed to endure harsh environments and heavy loads. Their focus on maintenance-friendly designs and advanced coating technologies enhances the lifespan and reliability of their pulleys. Dodge’s global reach ensures that customers receive comprehensive support and service worldwide.
- Precision Pulley & Idler (PPI): PPI’s engineering excellence and rigorous product testing set them apart. They offer a wide range of pulley sizes and types, ensuring that customers can find the perfect fit for their applications. PPI’s customer-focused approach and detailed technical support make them a preferred choice in the industry.
- Fenner Dunlop: Innovation and sustainability are at the core of Fenner Dunlop’s operations. Their use of high-performance materials and investment in cutting-edge technologies result in pulleys that can withstand extreme conditions. Fenner Dunlop’s global service network and commitment to environmentally friendly practices further enhance their reputation as a leading manufacturer.
By choosing a conveyor belt pulley from these reputable manufacturers, industries can ensure the efficiency, reliability, and longevity of their conveyor systems. The combination of high-quality materials, innovative designs, and exceptional customer support makes these manufacturers the top choices for conveyor belt pulleys in various industrial applications.
Drive Conveyor Belt Pulley
Drive Pulleys and How They Differ from Other Types
The drive pulley is a critical component of the conveyor belt system. Unlike other pulleys, the drive pulley is directly connected to a power source, such as an electric motor, which generates the force needed to move the conveyor belt. Understanding the unique features and functions of drive pulleys is essential for optimizing the performance of a conveyor belt system.
Key Differences Between Drive Pulleys and Other Types of Conveyor Belt Pulleys
Drive pulleys are unique in that they provide the driving force for the entire conveyor system. This makes them the most important pulley type in terms of operational control and efficiency.
Unique Role in Moving the Conveyor Belt and Controlling Speed and Tension
Drive pulleys play a pivotal role in ensuring the smooth and efficient operation of conveyor belts. Here’s a detailed look at their unique functions:
Power Transmission
The drive pulley is connected to a motor, which supplies the necessary power to move the conveyor belt. The motor converts electrical energy into mechanical energy, transmitted through the drive pulley to the belt. This power transmission is crucial for maintaining consistent belt movement, especially in heavy-duty applications such as mining, manufacturing, and logistics.
Speed Control
One of the primary functions of the drive pulley is to control the speed of the conveyor belt. The speed at which the motor rotates the drive pulley determines the belt speed. By adjusting the motor’s speed, operators can control the conveyor belt’s speed, ensuring that materials are transported at the desired rate. This is particularly important in applications where precise timing and coordination are essential, such as packaging and assembly lines.
Tension Management
Maintaining the correct tension in the conveyor belt is vital for preventing slippage and ensuring smooth operation. The drive pulley helps manage belt tension by providing a firm grip on the belt, reducing the risk of slippage. Proper tension management is crucial for prolonging the lifespan of both the belt and the pulley, reducing maintenance costs and downtime.
Enhanced Grip and Traction
Drive pulleys often feature a lagging material, such as rubber or ceramic, on their surface. This lagging enhances the grip between the pulley and the conveyor belt, improving traction and reducing slippage. Enhanced grip is essential for efficient power transmission, especially in environments where the belt might be exposed to moisture or other factors that can reduce traction.
Load Handling
Drive pulleys are designed to handle significant loads, making them suitable for applications that involve transporting heavy or bulky materials. The robust construction of drive pulleys ensures that they can withstand the stresses and strains associated with heavy-duty conveyor operations. This durability is essential for maintaining consistent performance in demanding industrial environments.
Operational Efficiency
By controlling the speed and tension of the conveyor belt, drive pulleys contribute to the overall operational efficiency of the conveyor system. Properly functioning drive pulleys ensure that materials are transported smoothly and efficiently, minimizing delays and disruptions. This efficiency translates into increased productivity and reduced operational costs.
Drive pulleys are indispensable components of conveyor belt systems. Their ability to transmit power, control speed, and manage tension ensures the smooth and efficient operation of the conveyor, making them crucial for the productivity and reliability of various industrial processes. Understanding the unique roles and functions of drive pulleys can help in optimizing conveyor systems for better performance and longevity.
Conveyor Belt Pulley Replacement
Guidelines for Recognizing When a Pulley Needs to Be Replaced
Regular maintenance and timely replacement of conveyor belt pulleys are crucial to ensure the smooth operation of conveyor systems. Recognizing the signs that indicate a pulley needs to be replaced can prevent unexpected breakdowns and extend the lifespan of the entire conveyor system. Here are key guidelines to help identify when a conveyor belt pulley requires replacement:
Signs of Wear and Tear
- Surface Damage: Inspect the pulley surface for signs of wear, such as grooves, cracks, or material buildup. Lagging material that is worn out or missing can lead to reduced traction and increased slippage, indicating the need for replacement.
- Abnormal Noise: Unusual noises, such as grinding, squeaking, or rattling, can indicate internal damage or misalignment of the pulley. These sounds often signal that the bearings or other components are worn out and need replacement.
- Vibration: Excessive vibration during operation can be a sign of imbalance or bearing failure in the pulley. Persistent vibration can cause further damage to the conveyor system and should be addressed promptly.
- Reduced Performance: If the conveyor system experiences frequent belt slippage, misalignment, or reduced speed, it may be due to a worn-out pulley. Reduced performance can lead to increased operational costs and downtime.
- Visible Deformation: Any visible signs of deformation, such as bent or warped pulleys, indicate that the pulley can no longer maintain proper belt tension and alignment. Such deformations necessitate immediate replacement.
Steps for Replacing a Conveyor Belt Pulley Efficiently to Minimize Downtime
Replacing a conveyor belt pulley requires careful planning and execution to minimize downtime and ensure a smooth transition. Here are the steps to replace a conveyor belt pulley efficiently:
Preparation
- Safety First: Ensure that all safety protocols are followed. Disconnect power to the conveyor system and lock out/tag out (LOTO) procedures to prevent accidental startup during replacement.
- Gather Tools and Equipment: Assemble the necessary tools and equipment, such as wrenches, screwdrivers, lifting devices, and replacement pulleys. Having everything ready will streamline the replacement process.
- Inspect the Replacement Pulley: Before installation, inspect the replacement pulley to ensure it meets the specifications of the existing pulley and is free from any defects.
Removal of the Old Pulley
- Loosen Belt Tension: Reduce the tension on the conveyor belt by adjusting the tensioning mechanism. This will make it easier to remove the old pulley.
- Remove Belt from Pulley: Carefully slide the conveyor belt off the old pulley. If the belt is too tight, use a belt jack or similar tool to create enough slack for removal.
- Detach the Pulley: Use appropriate tools to remove the mounting bolts or fasteners that secure the pulley to the conveyor frame. Carefully detach the pulley from the shaft, taking care not to damage other components.
Installation of the New Pulley
- Position the New Pulley: Align the new pulley with the shaft and slide it into place. Ensure that the pulley is positioned correctly to maintain proper belt alignment.
- Secure the Pulley: Tighten the mounting bolts or fasteners to secure the pulley to the conveyor frame. Use a torque wrench to apply the recommended torque settings, ensuring the pulley is firmly attached.
- Reinstall the Belt: Slide the conveyor belt back onto the new pulley. Adjust the belt tensioning mechanism to restore the proper tension. Ensure the belt is aligned correctly with the pulley to prevent misalignment issues.
Final Adjustments and Testing
- Check Alignment: Verify that the new pulley is aligned with the other pulleys in the conveyor system. Misalignment can cause uneven wear and reduced efficiency.
- Tension the Belt: Adjust the belt tension to the manufacturer’s specifications. Proper tensioning is crucial for optimal performance and longevity of the conveyor system.
- Perform a Test Run: Reconnect the power and perform a test run of the conveyor system. Monitor the new pulley for any unusual noises, vibrations, or performance issues. Make any necessary adjustments to ensure smooth operation.
Conveyor Belt Pulley: Drum Pulley
Deep Dive into Conveyor Drum Pulleys and Their Specifications
A conveyor drum pulley, often referred to as a head pulley or driving pulley, is a critical component in conveyor belt systems. These pulleys are cylindrical and are used to drive the conveyor belt, playing a pivotal role in the system’s functionality. Here, we explore the specifications of conveyor drum pulleys and their significance in industrial applications.
Specifications of Conveyor Drum Pulleys
Material Construction:
- Steel: Most drum pulleys are made of steel, which offers high strength and durability. Steel pulleys can withstand heavy loads and harsh environments, making them ideal for industrial applications.
- Aluminum: For lighter-duty applications, aluminum drum pulleys are used due to their lower weight and adequate strength.
- Stainless Steel: In environments where corrosion resistance is critical, such as food processing or chemical industries, stainless steel drum pulleys are preferred.
Diameter and Width:
- Diameter: The diameter of a drum pulley typically ranges from 4 inches to 48 inches, depending on the application requirements. Larger diameters provide better belt support and reduce wear.
- Width: The width of the pulley must match the width of the conveyor belt. Common widths range from 18 inches to 60 inches or more.
Lagging:
- Rubber Lagging: Rubber lagging is applied to the surface of drum pulleys to increase traction and reduce belt slippage. It also helps extend the life of the pulley and the belt.
- Ceramic Lagging: For more demanding applications, ceramic lagging is used due to its superior grip and wear resistance.
Shaft Mounting:
- Keyed Shaft: A keyed shaft ensures a secure fit between the pulley and the conveyor belt shaft, preventing slippage during operation.
- Tapered Bore: Tapered bore designs allow for easy installation and removal, reducing maintenance time.
Bearings:
- Sealed Bearings: Sealed bearings are used to prevent contamination from dust and moisture, ensuring smooth operation and long service life.
- Self-Aligning Bearings: These bearings compensate for minor misalignments, reducing wear and extending the life of the pulley and belt.
Applications in Various Industries and Why They Are Preferred
Conveyor drum pulleys are used in a wide range of industries due to their versatility, durability, and efficiency. Here are five examples of how drum pulleys are applied across different sectors:
Mining Industry:
- Application: In mining operations, drum pulleys are essential for transporting extracted minerals such as coal, ore, and other bulk materials.
- Why Preferred: Their robust construction and ability to handle heavy loads make drum pulleys ideal for the demanding conditions of mining operations. Steel drum pulleys with rubber lagging provide the necessary traction and durability.
Aggregate Processing:
- Application: Drum pulleys are used to move materials such as sand, gravel, and crushed stone in aggregate processing plants.
- Why Preferred: The durability of drum pulleys ensures they can handle the abrasive nature of aggregate materials. Ceramic lagging is often used to enhance wear resistance and extend the pulley’s lifespan.
Food Processing:
- Application: In food processing, conveyor systems transport ingredients and finished products through various stages of production.
- Why Preferred: Stainless steel drum pulleys are favored for their corrosion resistance and ease of cleaning, which are crucial for maintaining hygiene standards in food processing facilities.
Logistics and Warehousing:
- Application: Drum pulleys are integral to conveyor systems used in sorting, packaging, and transporting goods in logistics and warehousing operations.
- Why Preferred: Their ability to handle varying loads and maintain consistent performance is essential for the efficiency and reliability of logistics operations. Rubber lagging helps prevent belt slippage, ensuring smooth material flow.
Chemical Industry:
- Application: Conveyor systems in the chemical industry move raw materials and finished products through various processing stages.
- Why Preferred: Stainless steel drum pulleys are used for their chemical resistance, ensuring that they can withstand exposure to corrosive substances. The robust design of these pulleys ensures longevity and reliable performance in harsh environments.
Benefits of Conveyor Drum Pulleys
- Durability: The robust construction of drum pulleys allows them to handle heavy loads and endure harsh operating conditions, reducing the frequency of replacements and maintenance.
- Efficiency: Drum pulleys provide excellent traction and drive efficiency, ensuring smooth and consistent belt movement. This is crucial for maintaining high productivity levels in various industrial applications.
- Versatility: Available in a range of sizes and materials, drum pulleys can be customized to meet the specific needs of different industries, from food processing to mining.
- Reduced Maintenance: Features such as sealed bearings and rubber or ceramic lagging help extend the life of the pulley and reduce maintenance requirements, leading to lower operational costs.
Conveyor drum pulleys are essential components of conveyor systems across various industries. Their ability to provide reliable and efficient power transmission makes them indispensable for applications ranging from mining and aggregate processing to food and chemical industries. Understanding the specifications and applications of drum pulleys can help in selecting the right pulley for your needs, ensuring optimal performance and longevity of your conveyor system.
FAQs About Conveyor Belt Pulley
Several types of pulleys are used in conveyor belt systems, each serving a unique function to ensure the efficient operation of the conveyor. The most common types are the head pulley, tail pulley, drive pulley, and snub pulley. The head pulley, located at the discharge end, drives the belt and is often the primary pulley. The tail pulley is found at the loading end and helps to maintain proper tension and alignment. Drive pulleys are typically the same as head pulleys but specifically refer to those connected to the power source. Snub pulleys increase the wrap angle of the belt around the drive pulley, enhancing grip and reducing slippage. Each of these pulleys plays a critical role in ensuring the conveyor system runs smoothly and efficiently.
A belt pulley is a wheel-like component used in conveyor systems and various types of machinery to transfer power and motion from one part to another using a belt. In the context of conveyor systems, a belt pulley is a key element that helps drive the conveyor belt, move materials, and maintain tension. Pulleys are usually made from durable materials like steel or aluminum to withstand the stresses of continuous operation. They come in different types, including drum pulleys, wing pulleys, and turbine pulleys, each designed for specific functions. Belt pulleys ensure smooth and efficient power transmission, reducing the wear and tear on both the belt and the machinery, and are essential for the effective functioning of conveyor systems.
The tail pulley is a crucial component of a conveyor belt system, located at the opposite end of the head or drive pulley. Its primary function is to provide tension and support to the conveyor belt, ensuring it remains taut and aligned as it moves. By maintaining proper tension, the tail pulley helps prevent belt slippage and ensures smooth operation. It also plays a significant role in guiding the belt, ensuring it stays on track and does not drift off course. In addition, tail pulleys can be used to change the direction of the belt’s movement in certain conveyor system designs. Overall, the tail pulley is essential for maintaining the efficiency and reliability of the conveyor belt system.
The head pulley, also known as the drive pulley, is one of the most critical components in a conveyor belt system. Positioned at the discharge end of the conveyor, its primary purpose is to drive the conveyor belt and ensure the continuous movement of materials along the belt. The head pulley is connected to a motor, which generates the necessary force to move the belt. It also helps control the speed of the conveyor belt, which is essential for maintaining consistent material flow and productivity. Additionally, the head pulley provides the tension needed to keep the belt tight and prevent slippage. By efficiently transmitting power and maintaining belt tension, the head pulley ensures the smooth and effective operation of the conveyor system.
Last Updated on August 1, 2024 by Jordan Smith
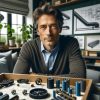
Jordan Smith, a seasoned professional with over 20 years of experience in the conveyor system industry. Jordan’s expertise lies in providing comprehensive solutions for conveyor rollers, belts, and accessories, catering to a wide range of industrial needs. From initial design and configuration to installation and meticulous troubleshooting, Jordan is adept at handling all aspects of conveyor system management. Whether you’re looking to upgrade your production line with efficient conveyor belts, require custom conveyor rollers for specific operations, or need expert advice on selecting the right conveyor accessories for your facility, Jordan is your reliable consultant. For any inquiries or assistance with conveyor system optimization, Jordan is available to share his wealth of knowledge and experience. Feel free to reach out at any time for professional guidance on all matters related to conveyor rollers, belts, and accessories.