Conveyor Pulleys:Belt Conveyor Head Pulley
Belt conveyors are essential in various industries, including mining, manufacturing, and logistics, for efficiently transporting materials over long distances. They are critical in optimizing production processes and enhancing overall operational efficiency. At the heart of these systems is the belt conveyor head pulley, a vital component responsible for driving the conveyor belt and ensuring smooth and continuous movement. The belt conveyor head pulley plays a crucial role in maintaining the tension and alignment of the belt, making it indispensable for reliable and effective conveyor operations. Understanding the significance of the belt conveyor head pulley is fundamental for anyone involved in the design, maintenance, or operation of conveyor systems.
What Is Conveyor Belt Pulleys
Conveyor belt pulleys are integral components of a conveyor system, each serving a specific function to ensure the efficient movement of materials. Here’s a closer look at the different types of conveyor belt pulleys and their roles:
Drive Pulley:
- Function: This pulley is connected to the motor and provides the driving force needed to move the belt and its load.
- Characteristics: It is typically located at the discharge end of the conveyor and may be equipped with a lagging surface to improve grip and reduce slippage.
- Function: Idler pulleys support the belt and help maintain proper belt tension and alignment.
- Characteristics: They do not drive the belt but are crucial for guiding it along the conveyor path. They are usually located along the length of the conveyor.
Return Pulley:
- Function: Positioned at the end of the conveyor system, it guides the belt as it returns to the drive pulley.
- Characteristics: Helps in the smooth return of the belt and supports it as it travels back.
Snub Pulley:
- Function: Increases the contact angle between the belt and the drive pulley to improve the grip and efficiency of the conveyor system.
- Characteristics: Typically positioned near the drive pulley to adjust the belt tension and enhance performance.
Take-Up Pulley:
- Function: Used to adjust the tension of the conveyor belt to ensure proper operation and prevent slipping.
- Characteristics: Can be either manual or automatic, allowing for tension adjustments as needed.
Wing Pulley:
- Function: Designed to help with the discharge of material from the belt and to prevent material build-up around the pulley.
- Characteristics: It has a set of wings or fins that extend outward, allowing material to be thrown off as the belt moves.
Tail Pulley:
- Function: Located at the opposite end of the drive pulley, it supports the belt and maintains tension as it travels back to the start of the conveyor.
- Characteristics: Helps in the smooth return of the belt and may also aid in conveyor belt tracking.
Proper maintenance of these pulleys is essential for the longevity and efficient operation of a conveyor system. Regular inspections for wear, alignment issues, and proper tension are crucial for avoiding operational problems.

What is Belt Conveyor Head Pulley
A belt conveyor head pulley is a fundamental component of a belt conveyor system. It is the pulley located at the discharge end of the conveyor, responsible for driving and guiding the conveyor belt. The primary function of the head pulley belt conveyor is to drive the conveyor belt, ensuring the smooth movement of materials from one end of the conveyor to the other. This pulley is connected to a motor that provides the necessary rotational force to move the belt and the materials it carries. The head pulley also helps maintain the tension in the belt, preventing slippage and ensuring efficient operation.
The Significance of the Head Pulley in Driving the Conveyor Belt
The belt conveyor head pulley is crucial for the efficient operation of a conveyor system.
- Material Transport: The head pulley drives the conveyor belt, enabling the transportation of materials across various distances. Without the head pulley’s driving force, the belt would not move, rendering the conveyor system ineffective.
- Tension Maintenance: By maintaining proper tension in the belt, the head pulley prevents slippage and ensures the smooth movement of materials. This is essential for the consistent operation of the conveyor system.
- Direction Control: The head pulley determines the direction in which the belt moves. It ensures that materials are transported to the intended destination, enhancing the efficiency and accuracy of the material handling process.
- System Efficiency: A well-functioning head pulley contributes to the overall efficiency of the conveyor system. It minimizes downtime and maintenance requirements by ensuring the belt operates smoothly and reliably.
- Load Handling: The head pulley must handle the load of the materials being transported. Its design and construction must be robust enough to withstand the stress and strain of continuous operation, ensuring the longevity and reliability of the conveyor system.
Understanding the role and significance of the belt conveyor head pulley is essential for anyone involved in the design, maintenance, or operation of conveyor systems. Its ability to drive the belt, maintain tension, and ensure efficient material transport makes it a critical component in a wide range of industries.
How Head Pulleys Differ from Other Types of Conveyor Pulleys
While the head pulley is critical for driving the belt, other pulleys in the conveyor system play different roles.
- Tail Pulley: Located at the opposite end of the conveyor from the head pulley, the tail pulley serves as a return point for the belt. It is not driven by a motor and primarily helps to redirect the belt back to the head pulley. Unlike the head pulley, it does not drive the belt.
- Drive Pulley: While the head pulley is a type of drive pulley, not all drive pulleys are head pulleys. Drive pulleys can be positioned in different locations along the conveyor system to provide additional driving force. They work in conjunction with the head pulley to ensure the belt moves efficiently, especially in longer conveyor systems.
- Snub Pulley: The snub pulley is positioned close to the head pulley and serves to increase the belt’s wrap angle around the head pulley. This increased contact improves the friction between the belt and the pulley, enhancing the head pulley’s ability to drive the belt.
- Take-Up Pulley: Located at various points along the conveyor, take-up pulleys help maintain proper tension in the belt. They are typically adjustable, allowing for tension adjustments as the belt stretches or contracts over time. Unlike the head pulley, they do not drive the belt but ensure it remains taut.
- Bend Pulley: Bend pulleys are used to change the direction of the belt in the conveyor system. They help guide the belt around corners and obstacles, ensuring a smooth and continuous flow of materials. These pulleys do not contribute to driving the belt like the head pulley.
Types of Belt Conveyor Head Pulley
Conveyor Belt Pulley Types Including Head, Tail, and Drive Pulleys
Conveyor belt systems rely on various types of pulleys to ensure efficient and smooth operation. Each type of pulley has a specific function that contributes to the overall performance of the conveyor system. The primary types of conveyor belt pulleys include head pulleys, tail pulleys, and drive pulleys.
- Head Pulley: The belt conveyor head pulley is located at the discharge end of the conveyor and is responsible for driving the belt. It is typically connected to a motor that provides the necessary rotational force to move the belt and the materials it carries.
- Tail Pulley: Positioned at the opposite end of the conveyor from the head pulley, the tail pulley serves as a return point for the belt. It is not driven by a motor and primarily helps to redirect the belt back to the head pulley.
- Drive Pulley: Drive pulleys can be located in various positions along the conveyor system. They provide additional driving force to assist the head pulley, especially in longer or more complex conveyor setups.
- Snub Pulley: The snub pulley is located close to the head pulley and increases the belt’s wrap angle around the head pulley. This enhanced contact improves friction between the belt and the pulley, aiding in the head pulley’s ability to drive the belt.
- Take-Up Pulley: Take-up pulleys are adjustable and help maintain proper tension in the belt. They are crucial for compensating for belt stretch and ensuring the belt remains taut during operation.
- Bend Pulley: Bend pulleys are used to change the direction of the belt within the conveyor system. They guide the belt around corners and obstacles, ensuring smooth and continuous material flow.
Specific Focus on Head Pulleys and Their Unique Features
The belt conveyor head pulley is critical for the efficient operation of conveyor systems. It possesses several unique features and that distinguish it from other types of pulleys.
- Driving Force: The head pulley provides the driving force needed to move the conveyor belt. It is connected to a motor that imparts rotational motion, propelling the belt and the materials it carries.
- Tension Maintenance: Head pulleys help maintain the necessary tension in the conveyor belt, preventing slippage and ensuring smooth material transport.
- Material Discharge: Located at the discharge end, the head pulley ensures that materials are effectively unloaded from the conveyor system at the intended location.
- Durability: Head pulleys are designed to withstand the stresses of continuous operation. They are constructed from robust materials to handle the load and ensure long-term reliability.
- Alignment: Proper alignment of the head pulley is crucial for the smooth operation of the conveyor system. Misalignment can lead to belt tracking issues and decreased efficiency.
Head Pulleys with Tail and Drive Pulleys to Highlight Their Distinct Functions
While the head pulley conveyor is essential for driving the belt, tail and drive pulleys also play significant roles in the conveyor system.
- Driving vs. Returning: The head pulley drives the belt, while the tail pulley serves as a return point, redirecting the belt back to the head pulley. The tail pulley does not contribute to driving the belt.
- Motor Connection: The head pulley is connected to a motor that provides the driving force. In contrast, the tail pulley is not motorized and simply helps in belt redirection.
- Tension Maintenance: Both head and drive pulleys help maintain belt tension. However, the head pulley plays a more direct role in preventing slippage, while drive pulleys assist by providing additional driving force in longer systems.
- Belt Wrap Angle: Snub pulleys increase the belt wrap angle around the head pulley, enhancing friction and driving efficiency. This is a unique interaction between the head pulley and snub pulleys, not typically seen with tail pulleys.
- Material Handling: The head pulley is crucial for material discharge at the end of the conveyor. Tail pulleys, positioned at the opposite end, help in the initial loading and return of the belt, ensuring continuous operation.
The belt conveyor head pulley is a vital component that drives the conveyor belt and ensures efficient material transport. Its unique features set it apart from other types of pulleys, each playing distinct roles to maintain the overall functionality and efficiency of the conveyor system.

Applications of Belt Conveyor Head Pulley
Belt conveyor head pulleys are versatile components used in various industries and applications. Here are some common applications:
Material Handling
- Bulk Material Handling: Used in industries like mining, construction, and agriculture to transport bulk materials such as coal, ores, grains, and sand.
- Manufacturing: Facilitates the movement of raw materials, components, and finished products along production lines.
Processing and Sorting
- Recycling Plants: Head pulleys are used in recycling facilities to transport and sort recyclable materials like paper, plastics, and metals.
- Food Processing: Applied in food processing plants to move and process raw ingredients and packaged products.
Warehousing and Distribution
- Logistics: Employed in warehouses and distribution centers to transport packages and goods between different areas of the facility.
- Sorting Systems: Utilized in automated sorting systems to direct items to specific destinations based on size, weight, or type.
Mining and Quarrying
- Mining Operations: Essential in mining operations for transporting extracted ores and minerals from the mining site to processing or storage areas.
- Quarrying: Used to move quarried materials like limestone, granite, and gravel.
Agriculture
- Crop Handling: Used in agricultural operations to move harvested crops, such as grains and vegetables, from fields to storage or processing facilities.
- Feed Mills: Applied in feed mills to transport animal feed ingredients and finished feed products.
Construction
- Material Transport: Used on construction sites to move building materials such as concrete, sand, and gravel to different areas of the site.
- Bulk Material Transfer: Facilitates the transfer of bulk materials from storage bins to construction equipment.
Ports and Shipping
- Bulk Cargo Handling: Utilized in ports for handling bulk cargoes such as coal, grain, and minerals, transferring them from ships to storage or processing areas.
Energy Sector
- Power Plants: Employed in power plants to transport coal, biomass, or other fuel materials to the boilers or storage facilities.
Automotive Industry
- Assembly Lines: Used in automotive manufacturing plants to move parts and components along assembly lines for vehicle production.
In all these applications, the head pulley is crucial for driving the conveyor belt, ensuring efficient material handling, and enabling smooth operation of the conveyor system.
Belt Conveyor Head Pulley and Tail Dynamics
The Relationship Between Head Pulleys and Tail Pulleys in Conveyor Systems
In a conveyor system, the relationship between the belt conveyor head pulley and the tail pulley is crucial for efficient and smooth operations. The belt conveyor head pulley, located at the discharge end, is primarily responsible for driving the belt and ensuring the movement of materials along the conveyor. The tail pulley, on the other hand, is situated at the opposite end of the conveyor system and acts as a return point for the belt, redirecting it back to the head pulley.
The synergy between the conveyor belt head pulley and the tail pulley is essential for maintaining the proper tension and alignment of the conveyor belt. The head pulley drives the belt, creating the necessary force to move the materials. Simultaneously, the tail pulley helps to guide the belt back into position for continuous operation. This dynamic relationship ensures that the belt remains taut and runs smoothly without slippage or misalignment, which are critical factors for the efficient performance of the conveyor system.
The Complementary Roles They Play in Ensuring Efficient and Smooth Operations
The belt conveyor head pulley and tail pulley play complementary roles that are vital for the smooth operation of the conveyor system. Their coordinated functions help achieve the following:
- Belt Tension Maintenance: The head pulley ensures that the belt is driven forward with sufficient force, while the tail pulley provides the necessary tension to keep the belt taut. This balance prevents belt slippage and maintains efficient material transport.
- Belt Alignment: Proper alignment of the belt is crucial for avoiding operational issues. The head pulley drives the belt in the correct direction, and the tail pulley guides it back, ensuring the belt remains aligned with the conveyor structure.
- Load Distribution: The head pulley handles the driving force, which is particularly important when the belt is loaded with materials. The tail pulley, although not driven, supports the return of the unloaded belt, distributing the operational load across the system.
- Minimizing Wear and Tear: By maintaining proper tension and alignment, the head and tail pulleys minimize the wear and tear on the conveyor belt and other components. This prolongs the lifespan of the conveyor system and reduces maintenance requirements.
- Energy Efficiency: Efficient operation of the head and tail pulleys ensures that the conveyor system operates smoothly, reducing the energy required to drive the belt. This leads to cost savings and improved system efficiency.
Impact of Pulley Design and Material on Conveyor Performance
The design and material of both the belt conveyor head pulley and the tail pulley significantly impact the performance and efficiency of the conveyor system. Key considerations include:
- Material Selection: The pulleys are typically made from materials such as steel or aluminum, chosen for their strength and durability. Steel pulleys offer high strength and are suitable for heavy-duty applications, while aluminum pulleys are lighter and suitable for less demanding environments.
- Surface Finish: The surface finish of the pulleys affects their grip on the belt. A rougher surface provides better traction, reducing the risk of slippage. Rubber lagging can be applied to the surface of the head pulley to enhance friction and drive efficiency.
- Pulley Diameter: The diameter of the pulleys influences the belt’s tension and the overall performance of the conveyor system. Larger diameters are typically used for heavy loads, providing better tension distribution and reducing belt stress.
- Pulley Alignment: Proper alignment of the pulleys is essential for preventing belt misalignment and ensuring smooth operation. Misaligned pulleys can cause the belt to track incorrectly, leading to increased wear and potential system failure.
- Maintenance and Adjustability: The design of the pulleys should allow for easy maintenance and adjustability. Tail pulleys often feature tensioning mechanisms to adjust the belt tension as needed, ensuring continuous optimal performance.
The belt conveyor head pulley and the tail pulley work together to maintain the efficient and smooth operation of conveyor systems. Their complementary roles in driving, tensioning, and aligning the belt are crucial for the overall performance and longevity of the system. The design and material choices for these pulleys play a significant role in optimizing conveyor performance, reducing wear and tear, and enhancing energy efficiency. Understanding the dynamics between the head and tail pulleys is essential for anyone involved in the operation and maintenance of conveyor systems.

Belt Conveyor Head Pulley Replacement
When and Why Replacement of a Belt Conveyor Head Pulley Is Necessary
The belt conveyor head pulley is a critical component in conveyor systems, playing a significant role in driving the belt and ensuring smooth material transport. Over time, wear and tear, operational stress, and environmental factors can affect its performance, necessitating replacement. Here are some common scenarios and reasons why the replacement of a belt conveyor head pulley becomes necessary:
- Wear and Tear: Continuous operation leads to wear and tear on the head pulley, especially if it handles abrasive materials. Grooves, surface wear, and material buildup can compromise its efficiency and necessitate replacement.
- Damage: Physical damage, such as dents, cracks, or deformities, can occur due to heavy loads, impact, or operational mishaps. Such damage can impair the pulley’s ability to drive the belt effectively.
- Slippage: Over time, the surface of the head pulley may lose its grip, leading to belt slippage. This reduces the efficiency of the conveyor system and can cause operational delays.
- Misalignment: Misaligned pulleys can cause uneven wear on the belt and other components, leading to frequent maintenance issues. Replacing a misaligned pulley can restore optimal system performance.
- Upgrades: Technological advancements and changes in operational requirements may necessitate upgrading the head pulley to a more advanced or efficient model to improve overall system performance.
Key Considerations in Selecting a Replacement Pulley
When selecting a replacement conveyor belt head pulley, several factors need to be considered to ensure compatibility and optimal performance.
- Size: The size of the replacement head pulley must match the original specifications to maintain proper tension and alignment. Measure the diameter and width accurately to ensure a perfect fit.
- Material: The material of the pulley should be chosen based on the operational environment and the materials being transported. Common materials include steel, which offers high durability and strength, and aluminum, which is lighter but less robust.
- Surface Finish: The surface finish of the head pulley affects its grip on the belt. Rubber lagging can be applied to enhance traction and reduce slippage. The choice of lagging material should match the operational conditions.
- Design Features: Consider any additional design features that may enhance performance. For instance, crowned pulleys help in maintaining belt alignment, while wing pulleys can prevent material buildup and reduce maintenance requirements.
- Compatibility: Ensure that the replacement pulley is compatible with the existing conveyor system components, including the motor and belt. Compatibility is crucial for maintaining system efficiency and preventing operational disruptions.
Steps Involved in Replacing a Conveyor Head Pulley
Replacing a belt conveyor head pulley involves several steps to ensure safety and efficiency. Here is a detailed guide:
- Shutdown and Lockout: Before starting the replacement process, shut down the conveyor system and follow lockout/tagout procedures to ensure that the machinery is not accidentally activated.
- Remove the Belt: Loosen the tension on the conveyor belt and remove it from the system. This may involve detaching the belt from the tail pulley and any other intermediate pulleys.
- Disconnect the Pulley: Disconnect the head pulley from the motor and any mounting brackets. This may involve removing bolts, nuts, or other fasteners that secure the pulley in place.
- Inspect and Prepare: Inspect the mounting brackets, motor, and other components for any signs of wear or damage. Clean and prepare the area for installing the new pulley.
- Install the New Pulley: Position the replacement head pulley and secure it in place using the appropriate fasteners. Ensure that the pulley is aligned correctly with the other components to prevent misalignment issues.
- Reconnect the Belt: Reattach the conveyor belt to the head pulley, tail pulley, and any other intermediate pulleys. Adjust the tension to the required specifications to ensure proper operation.
- Test and Verify: Once the new pulley is installed and the belt is reattached, test the conveyor system to ensure that everything is functioning correctly. Check for any signs of misalignment, slippage, or unusual noises.
- Maintenance and Monitoring: After the replacement, implement a regular maintenance and monitoring schedule to ensure the longevity and optimal performance of the new head pulley. Regular inspections can help identify any potential issues early and prevent costly downtime.
The belt conveyor head pulley is a vital component that requires careful consideration and proper maintenance. Understanding when and why to replace it, key factors in selecting a suitable replacement, and the steps involved in the replacement process are crucial for maintaining the efficiency and reliability of conveyor systems.
Drive Belt Conveyor Head Pulley Mechanics
The Critical Role of the Drive Pulley in a Conveyor Belt System
The drive pulley is a fundamental component in conveyor belt systems, responsible for transmitting the mechanical power necessary to move the belt and its load. Positioned at various points along the conveyor system, drive pulleys work to provide additional driving force, especially in longer or more complex conveyor setups. The primary function of the drive pulley is to convert the rotational motion provided by a motor into the linear motion needed to move the belt. By doing so, the drive pulley ensures that materials are transported efficiently and reliably across the conveyor system.
In essence, the drive pulley is crucial for maintaining the desired speed and direction of the conveyor belt. It ensures that the belt operates smoothly, preventing issues such as slippage, misalignment, and uneven wear. The effectiveness of the drive pulley directly impacts the overall performance and efficiency of the conveyor system, making it a critical element in various industrial applications.
How Drive Pulleys Work in Conjunction with Head Pulleys to Move the Belt
The interaction between drive pulleys and the belt conveyor head pulley is essential for the effective operation of a conveyor system. While the belt conveyor head pulley is primarily responsible for driving the belt at the discharge end, drive pulleys located along the conveyor line provide supplementary driving force. This collaboration ensures that the belt maintains consistent speed and tension, even in long or heavily loaded conveyor systems.
- Enhanced Traction: Drive pulleys increase the contact area between the belt and the pulley, enhancing traction and reducing the likelihood of slippage. This is particularly important in systems with high loads or long distances, where a single head pulley might not provide sufficient driving force.
- Load Distribution: By strategically placing drive pulleys along the conveyor, the load is distributed more evenly across the system. This reduces the strain on the belt conveyor head pulley, preventing excessive wear and extending the lifespan of the belt and pulleys.
- Tension Maintenance: Drive pulleys help maintain the proper tension in the conveyor belt. This is critical for preventing belt sagging and misalignment, which can lead to operational inefficiencies and increased maintenance costs.
- Direction Control: In systems with multiple drive pulleys, the direction and speed of the belt can be controlled more precisely. This is particularly useful in applications where the conveyor needs to navigate complex paths or variable speeds.
- Synchronization: Drive pulleys work in sync with the belt conveyor head pulley to ensure that the entire system operates harmoniously. This synchronization minimizes the risk of conveyor belt damage and ensures smooth material transport.
Factors Affecting the Choice of a Drive Pulley for Optimal System Performance
Selecting the appropriate drive pulley is essential for achieving optimal performance in a conveyor system.
- Pulley Size: The size of the drive pulley affects the speed and torque of the conveyor system. Larger pulleys provide greater torque but lower speed, while smaller pulleys offer higher speed but less torque. The choice depends on the specific requirements of the application.
- Material: The material of the drive pulley impacts its durability and suitability for different environments. Common materials include steel, which offers high strength and durability, and aluminum, which is lighter and suitable for less demanding applications. The operating environment and the nature of the materials being transported should guide the material selection.
- Surface Finish: The surface finish of the drive pulley affects its grip on the belt. A rougher surface provides better traction, reducing the likelihood of slippage. Rubber lagging can be applied to the pulley surface to enhance grip and improve driving efficiency.
- Design Features: Consider additional design features that can enhance performance. For example, crowned pulleys help maintain belt alignment, while wing pulleys prevent material buildup and reduce maintenance requirements. The specific needs of the conveyor system should dictate the design features.
- Compatibility: The drive pulley must be compatible with the existing components of the conveyor system, including the belt conveyor head pulley, motor, and belt. Ensuring compatibility helps maintain system efficiency and prevents operational disruptions.
The drive pulley plays a critical role in the mechanics of a conveyor belt system. Its interaction with the belt conveyor head pulley is essential for maintaining the desired speed, tension, and direction of the belt. By considering factors such as pulley size, material, surface finish, design features, and compatibility, one can select the appropriate drive pulley to achieve optimal performance in a conveyor system. Understanding the mechanics of drive pulleys and their relationship with head pulleys is crucial for anyone involved in the design, operation, and maintenance of conveyor systems.
Belt Conveyor Head Pulley for Sale
Tips on Selecting the Right Belt Conveyor Head Pulley for Specific Applications
Selecting the right belt conveyor head pulley is crucial for ensuring the efficiency and reliability of your conveyor system.
- Load Requirements: Determine the load requirements of your conveyor system. For heavy-duty applications, such as in mining or bulk material handling, a robust head pulley made from high-strength steel is necessary to withstand the high load and stress.
- Environmental Conditions: Consider the environmental conditions where the conveyor system will operate. For instance, if the system is exposed to corrosive materials or harsh weather conditions, selecting a head pulley with anti-corrosive coatings or made from corrosion-resistant materials like stainless steel is essential.
- Belt Speed: The speed at which your conveyor belt operates will influence the type of head pulley you need. High-speed belts require pulleys with superior balancing and precise alignment to prevent vibration and ensure smooth operation.
- Material Type: The type of material being transported can impact the choice of head pulley. For example, if you are moving abrasive materials like sand or gravel, selecting a pulley with a durable rubber lagging can enhance grip and extend the pulley’s lifespan.
- Maintenance Requirements: Consider the maintenance requirements and ease of installation. A head pulley designed for easy access and replacement can reduce downtime and maintenance costs, ensuring continuous and efficient operation.
Features to Look for When Purchasing a Head Pulley
When purchasing a belt conveyor head pulley, several key features should be considered to ensure optimal performance and longevity:
- Material and Construction: The material and construction of the head pulley are critical for its durability and performance. Look for pulleys made from high-strength materials such as steel or aluminum, and consider options with anti-corrosive coatings for enhanced durability in harsh environments.
- Lagging: Lagging is the material covering the surface of the pulley, which enhances the grip on the belt and reduces slippage. Rubber lagging is commonly used for its excellent grip and wear resistance. Ceramic lagging can be used for high-abrasion applications for extended life and performance.
- Balancing and Alignment: A well-balanced head pulley ensures smooth operation and reduces wear on the belt and other conveyor components. Precision balancing and alignment are essential features to look for, as they minimize vibration and enhance the overall efficiency of the conveyor system.
- Bearing Quality: High-quality bearings are crucial for the smooth rotation and longevity of the head pulley. Look for pulleys with sealed bearings to protect against dust and moisture, ensuring reliable operation and reducing maintenance requirements.
- Design Features: Additional design features such as crowned surfaces can help in maintaining belt alignment, while wing pulleys can prevent material buildup and enhance the pulley’s self-cleaning capabilities. These features contribute to the efficient operation and extended life of the head pulley.
Recommended Suppliers or Manufacturers Known for Quality Conveyor Components
When it comes to purchasing a belt conveyor head pulley, choosing a reputable supplier or manufacturer is essential to ensure quality and reliability. Here are some recommended suppliers known for their high-quality conveyor components:
- Dodge: Dodge is a well-known manufacturer of industrial conveyor components, offering a wide range of head pulleys designed for various applications. Their products are known for their durability, precision, and performance.
- Van Gorp: Van Gorp specializes in the design and manufacture of conveyor pulleys, including head pulleys. Their products are recognized for their robust construction, high-quality materials, and innovative design features.
- Superior Industries: Superior Industries is a leading supplier of conveyor components, including head pulleys. They offer a comprehensive range of pulleys designed to meet the needs of different industries, ensuring high performance and reliability.
- Precision Pulley and Idler (PPI): PPI is renowned for its high-quality conveyor pulleys and components. Their head pulleys are engineered for optimal performance, featuring advanced design and construction techniques.
- Martin Sprocket & Gear: Martin Sprocket & Gear is a trusted name in the conveyor component industry, offering a wide selection of head pulleys. Their products are known for their exceptional quality, durability, and engineering excellence.
Selecting the right belt conveyor head pulley requires careful consideration of load requirements, environmental conditions, belt speed, material type, and maintenance needs. Key features to look for include material and construction quality, lagging, balancing and alignment, bearing quality, and specific design features. Choosing a reputable supplier or manufacturer ensures that you get a high-quality product that meets your specific application needs, contributing to the efficiency and reliability of your conveyor system.
FAQs About Belt Conveyor Head Pulley
The head pulley in a belt conveyor is a critical component located at the discharge end of the conveyor. It is responsible for driving the conveyor belt, ensuring the continuous movement of materials along the conveyor system. The head pulley is typically connected to a motor, which provides the necessary rotational force to move the belt. This pulley also helps maintain the tension and alignment of the belt, preventing slippage and ensuring smooth operation. Its robust construction allows it to handle the load and stress associated with continuous material handling, making it essential for efficient conveyor system performance.
A magnetic head pulley is an innovative variation of the standard head pulley used in belt conveyors. It incorporates a powerful magnet that attracts and separates ferrous metal contaminants from the materials being conveyed. As the belt moves over the magnetic pulley, any ferrous metal pieces in the material stream are drawn to the pulley’s surface and held in place. When the belt reaches the underside of the pulley, the metal pieces are released from the magnetic field and fall into a separate collection area. This process ensures that the conveyed materials are free from metal contaminants, enhancing product quality and protecting downstream equipment from damage.
The tail pulley in a belt conveyor system is positioned at the opposite end of the conveyor from the head pulley. Its primary function is to provide a return point for the conveyor belt, guiding it back towards the head pulley for continuous operation. Unlike the head pulley, the tail pulley is not driven by a motor; it rotates freely, helping to maintain belt tension and alignment. The tail pulley also aids in load distribution by ensuring the belt runs smoothly without sagging or misalignment. Proper maintenance of the tail pulley is essential to prevent wear and tear on the belt and other conveyor components.
The head end and tail end are terms used to describe the two ends of a conveyor system. The head end, also known as the discharge end, is where the belt conveyor head pulley is located. This is the point where materials are unloaded from the conveyor system. The head end is driven by a motor that provides the necessary force to move the belt. The tail end, on the other hand, is the starting point of the conveyor, where materials are loaded onto the belt. The tail pulley is located at this end and helps in guiding the belt back to the head end for continuous movement. Understanding the roles of the head end and tail end is crucial for the efficient operation and maintenance of a conveyor system.
Last Updated on August 13, 2024 by Jordan Smith
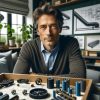
Jordan Smith, a seasoned professional with over 20 years of experience in the conveyor system industry. Jordan’s expertise lies in providing comprehensive solutions for conveyor rollers, belts, and accessories, catering to a wide range of industrial needs. From initial design and configuration to installation and meticulous troubleshooting, Jordan is adept at handling all aspects of conveyor system management. Whether you’re looking to upgrade your production line with efficient conveyor belts, require custom conveyor rollers for specific operations, or need expert advice on selecting the right conveyor accessories for your facility, Jordan is your reliable consultant. For any inquiries or assistance with conveyor system optimization, Jordan is available to share his wealth of knowledge and experience. Feel free to reach out at any time for professional guidance on all matters related to conveyor rollers, belts, and accessories.