Mining Conveyor Systems Components And Manufacturers
A mining conveyor is a specialized transportation system used in the mining industry to move large quantities of raw materials, such as coal, iron ore, and other minerals, from the extraction site to processing facilities or storage areas. These systems are designed to handle heavy loads and operate in harsh mining environments. Key components include belts, motors, rollers, and control systems, which work together to ensure efficient and continuous material flow. Mining conveyors are essential for improving productivity, reducing operational costs, and enhancing safety in mining operations. They come in various designs, including high angle and underground conveyor systems.Mining conveyor systems are evolving to known for their high availability and continuous efficiency, and increasingly used in underground applications.
Types of Mining Conveyors
Mining conveyors come in various types, each designed for specific applications and material handling requirements. Here are the main types of mining conveyors:
Each type of mining conveyor has its specific advantages and is chosen based on the requirements of the mining operation, including the type of material, distance, terrain, and operational constraints.
Mining Conveyor Applications
Mining conveyors are critical components in mining operations, used primarily to transport materials like ore, coal, and other mined products. These conveyors improve efficiency, reduce manual labor, and enhance safety in mining environments. Here are some key applications and aspects of mining conveyors:
Key Applications
- Material Transport:
- Bulk Material Handling: Conveyors transport large quantities of mined material from the excavation site to processing plants or storage facilities.
- Overburden Removal: In surface mining, conveyors are used to remove overburden (the layer of soil and rock overlying a mineral deposit).
- Processing and Sorting:
- Crushing and Screening: Conveyors feed materials into crushers and screening systems for size reduction and sorting.
- Separation Processes: Conveyors are used in conjunction with magnetic separators, flotation systems, and other separation equipment.
- Stockpiling and Storage:
- Stockpile Management: Conveyors help create and manage stockpiles of processed materials, ensuring efficient space utilization.
- Reclaiming Systems: Reclaiming conveyors retrieve materials from stockpiles for further processing or shipment.
- Underground Mining:
- Belt Conveyors: In underground mines, belt conveyors are used to transport ore from the mining face to the surface or processing plant.
- Shuttle Conveyors: These are used to move materials along fixed paths, often in confined underground spaces.
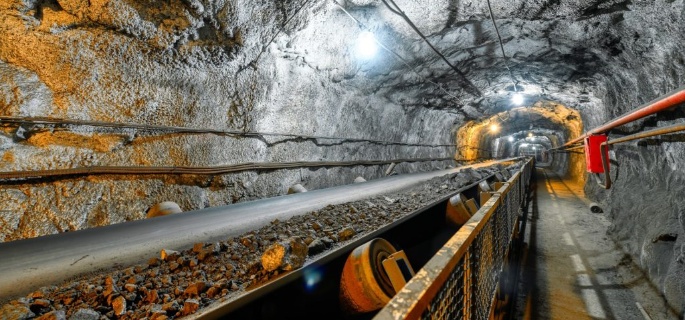
Mining Conveyor Price
The mining conveyor price is a critical factor that influences the overall budget of mining operations. Several elements contribute to the cost of a mining conveyor, and understanding these factors can help mining companies make informed decisions.
Material Costs
The primary determinant of mining conveyor price is the cost of materials used in its construction. Conveyors are typically made from high-quality materials to ensure durability and longevity in the harsh mining environment. The most common materials include:
- Steel: Steel is widely used for the framework, rollers, and other structural components of mining conveyors due to its strength and durability. The price of steel can fluctuate based on market conditions, affecting the overall cost of the conveyor.
- Rubber: The conveyor belt itself is often made from rubber, which needs to be robust enough to handle heavy loads and abrasive materials. The quality and thickness of the rubber can influence the conveyor’s price.
- Polymers and composites: Advanced materials like polymers and composites are sometimes used to enhance the durability and performance of conveyor components, but these materials can also increase the cost.
Specifications
The specific requirements of a mining conveyor system also play a significant role in determining its price. Customization based on operational needs can lead to variations in cost. Key specifications include:
- Length and width: Longer and wider conveyors require more materials and labor, increasing the overall price.
- Load capacity: Conveyors designed to handle heavier loads need stronger materials and components, which can drive up costs.
- Speed: High-speed conveyors require advanced motors and control systems, which can be more expensive.
- Environment: Conveyors intended for use in harsh environments, such as underground mines, may need additional protective features, which can add to the cost.
Manufacturing Processes
The complexity of the manufacturing process also affects the mining conveyor price. Advanced manufacturing techniques and the quality of craftsmanship can influence the final cost. Factors include:
- Engineering and design: Custom-designed conveyors tailored to specific mining operations require detailed engineering and design work, which can be costly.
- Fabrication: The fabrication process, including cutting, welding, and assembling the components, impacts the price. High-precision fabrication ensures better performance and durability but can be more expensive.
- Installation: The installation process, especially in challenging environments like underground mines, can add to the overall cost. Skilled labor and specialized equipment may be required for proper installation.
Market Demand and Supply Chain
Market conditions and the supply chain also play a role in determining the mining conveyor price. High demand for mining conveyors, coupled with supply chain disruptions, can lead to increased prices. Conversely, a stable supply chain and lower demand can help reduce costs.
Additional Features
Advanced features and technologies integrated into mining conveyors for sale can also affect their price. These features might include:
- Automation and control systems: Automated systems for monitoring and controlling the conveyor can enhance efficiency but add to the cost.
- Safety features: Enhanced safety features, such as emergency stop mechanisms and protective guards, can increase the price but are essential for safe operations.
- Energy efficiency: Energy-efficient motors and components can reduce operational costs over time but may have a higher initial price.
The mining conveyor price is influenced by various factors, including material costs, specifications, manufacturing processes, market demand, and additional features. Understanding these factors can help mining companies select the most cost-effective and suitable conveyor system for their operations.
Open-pit Mining Conveyor Applications
Open-pit mining conveyor systems are essential for the efficient transportation of materials from the mining site to processing plants or storage areas. These systems are specifically designed to handle the unique challenges of open-pit mining, including transporting large volumes of materials over long distances and varying terrain. Here are some key applications and benefits of open-pit mining conveyors:
Key Applications
Material Transport:
- Overburden Removal: Conveyors are used to remove the overburden layer (soil and rock) to access the mineral deposits.
- Ore Transport: Transporting extracted ore from the mining face to processing plants.
- Waste Rock Transport: Moving waste rock to designated disposal areas.
Processing and Sorting:
- Feeding Crushers and Screens: Conveyors transport materials to crushers and screens for size reduction and sorting.
- Stockpile Management: Creating and managing stockpiles of processed or raw materials.
Stacking and Reclaiming:
- Stacking Systems: Automated stacking systems for creating stockpiles of mined material.
- Reclaiming Systems: Conveyors that reclaim materials from stockpiles for further processing or shipment.
Benefits of Open-Pit Mining Conveyors
- Increased Efficiency: Automated transport of materials increases overall operational efficiency and reduces cycle times.
- Cost Reduction: Reduces the need for haul trucks, lowering fuel and maintenance costs.
- Safety Improvement: Reduces the risk of accidents associated with truck haulage and manual handling of materials.
- Environmental Protection: Enclosed conveyor systems can minimize dust and spillage, reducing environmental impact.
- Scalability: Conveyors can be scaled up or down to match production rates, offering flexibility in mining operations.
- Energy Efficiency: Modern conveyor systems are designed to be energy-efficient, often incorporating regenerative braking systems.
Types of Conveyors in Open-Pit Mining
Belt Conveyors:
- Fixed Belt Conveyors: Permanent installations for long-term use in transporting materials.
- Portable Belt Conveyors: Movable units that can be repositioned as the mining face advances.
Overland Conveyors:
- Designed for long-distance transport, often spanning several kilometers, to connect the mining site with processing plants or storage facilities.
In-Pit Crushing and Conveying (IPCC) Systems:
- Integrates crushing and conveyor systems to reduce the need for truck haulage. Crushed material is directly fed into conveyors for transport out of the pit.
High-Angle Conveyors:
- Used to transport materials at steep angles, allowing for efficient use of space and reducing the number of conveyor systems required.
Stacker and Reclaimer Systems:
- Stackers: Automated systems for building stockpiles.
- Reclaimers: Machines that retrieve materials from stockpiles for further processing or transport.
Case Studies and Examples
Rio Tinto’s Kennecott Utah Copper (KUC) Mine:
- Utilizes a comprehensive conveyor system for material handling, reducing truck traffic and improving operational efficiency.
Codelco’s Chuquicamata Mine:
- Employs an extensive IPCC system to handle the vast quantities of copper ore mined from the world’s largest open-pit copper mine.
BHP’s Escondida Mine:
- Uses overland conveyors to transport copper ore over long distances to processing plants, optimizing logistics and reducing environmental impact.
Challenges and Considerations
- Terrain and Topography: Designing conveyor systems to navigate the varying terrain of open-pit mines.
- Maintenance and Reliability: Ensuring regular maintenance to prevent downtime and extend the lifespan of conveyor systems.
- Load Variability: Handling fluctuations in material loads without compromising performance.
- Integration with Other Systems: Ensuring seamless integration with crushing, screening, and processing equipment.
Open-pit mining conveyors are a vital component of modern mining operations, offering numerous benefits in terms of efficiency, cost savings, safety, and environmental protection.
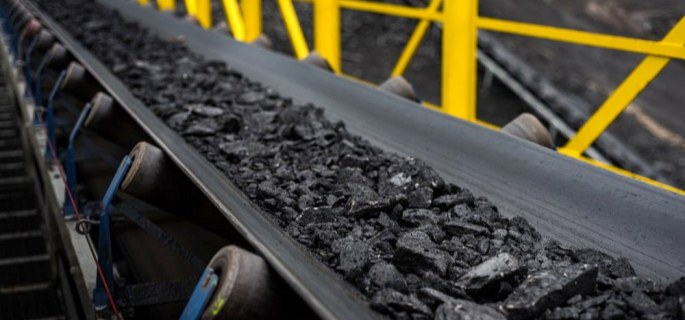
Mining Conveyor: Conveyor Belt Systems Mining PDF
Conveyor belt systems mining PDF resources are invaluable tools for mining professionals. These documents provide detailed information on the design, installation, operation, and maintenance of mining conveyor systems. Accessing and utilizing these resources can greatly enhance the efficiency and effectiveness of mining operations.
Importance of Conveyor Belt Systems Mining PDF
Conveyor belt systems mining PDFs offer comprehensive insights into the various aspects of mining conveyor systems. These documents are essential for several reasons:
- Design guidelines: PDFs often include detailed design guidelines, helping engineers and planners create efficient and reliable conveyor systems tailored to specific mining operations.
- Technical specifications: They provide technical specifications and standards, ensuring that the conveyor systems meet industry requirements and safety regulations.
- Installation procedures: Detailed installation procedures help ensure that the conveyor systems are set up correctly, minimizing the risk of operational issues and enhancing safety.
- Maintenance schedules: Regular maintenance is crucial for the longevity and performance of mining conveyors. PDFs often include maintenance schedules and checklists to help operators keep the systems in optimal condition.
- Troubleshooting guides: Troubleshooting guides included in these PDFs can assist in identifying and resolving common issues that may arise during the operation of mining conveyors.
Accessing Conveyor Belt Systems Mining PDF
Mining professionals can access conveyor belt systems mining PDFs through various sources. These documents are typically available from:
- Manufacturer websites: Many mining conveyor manufacturers provide PDFs on their websites, offering detailed information about their products and services.
- Industry associations: Industry associations and organizations often publish guidelines and standards in PDF format, which can be accessed by their members.
- Educational institutions: Universities and technical colleges with mining engineering programs may offer access to PDF resources as part of their educational materials.
- Online databases: Several online databases and libraries provide access to a wide range of technical documents, including conveyor belt systems mining PDFs.
Utilizing Conveyor Belt Systems Mining PDF
Effectively utilizing conveyor belt systems mining PDFs involves several steps:
- Reviewing design guidelines: Before planning a new conveyor system, it is essential to review the design guidelines provided in the PDFs. This ensures that the system will meet the specific needs of the mining operation and comply with industry standards.
- Following installation procedures: Proper installation is critical for the efficient operation of mining conveyors. Following the procedures outlined in the PDFs helps ensure that the system is installed correctly, minimizing the risk of operational issues.
- Implementing maintenance schedules: Regular maintenance is key to the longevity and performance of mining conveyors. Utilizing the maintenance schedules and checklists provided in the PDFs helps keep the systems in optimal condition.
- Referencing troubleshooting guides: In the event of operational issues, referencing the troubleshooting guides in the PDFs can help identify and resolve problems quickly, minimizing downtime and maintaining productivity.
Benefits of Conveyor Belt Systems Mining PDF
Utilizing conveyor belt systems mining PDFs offers several benefits:
- Enhanced efficiency: Detailed design guidelines and technical specifications help create efficient conveyor systems, improving the overall productivity of mining operations.
- Improved safety: Following the installation procedures and maintenance schedules outlined in the PDFs helps ensure that the conveyor systems operate safely, reducing the risk of accidents and injuries.
- Cost savings: Proper installation and regular maintenance, as guided by the PDFs, can reduce the risk of costly breakdowns and repairs, leading to significant cost savings over time.
- Knowledge sharing: Access to comprehensive information in PDF format facilitates knowledge sharing among mining professionals, promoting best practices and continuous improvement in the industry.
Conveyor belt systems mining PDF resources are essential tools for mining professionals. They provide detailed information on the design, installation, operation, and maintenance of mining conveyor systems, enhancing efficiency, safety, and cost-effectiveness in mining operations.
Mining Conveyor: Underground Conveyor Belt System
Overview of Underground Conveyor Belt Systems
Underground conveyor belt systems play a crucial role in the efficient transport of materials in mining operations. These systems are designed to operate in challenging underground environments, ensuring the safe and reliable movement of mined materials to the surface or processing facilities. In this section, we will delve into the design, functionality, and significance of underground conveyor belt systems.
Design and Components of Underground Conveyor Belt Systems
Underground conveyor belt systems are engineered to withstand the harsh conditions of underground mining. Key design features and components include:
- Robust Belt Materials: Underground conveyor belts are made from durable materials, such as steel-cord or fabric-reinforced belts, to withstand high loads and abrasive conditions. These belts are designed to handle various materials, including coal, ore, and rock.
- Heavy-Duty Rollers and Idlers: The rollers and idlers used in underground conveyor systems are built to endure heavy loads and harsh environments. They provide smooth belt movement and reduce friction, ensuring efficient operation.
- High-Strength Frames and Structures: The frames and structures of underground conveyor systems are constructed from high-strength materials to support the weight of the belt and transported materials. These structures are designed for stability and durability.
- Dust and Fire Protection: Underground conveyor systems often include dust suppression and fire protection features to enhance safety. These features help minimize the risk of explosions and fires in underground mines.
Functionality and Operation
Underground conveyor belt systems function by continuously transporting materials from the mining face to the surface or processing facilities. Key operational aspects include:
- Loading and Unloading Stations: Underground conveyor systems have designated loading and unloading stations where materials are fed onto the belt and offloaded at the surface or processing sites. These stations are designed for efficient material transfer.
- Control and Monitoring Systems: Advanced control and monitoring systems ensure the smooth operation of underground conveyors. These systems provide real-time data on belt speed, load, and condition, allowing for optimal performance and quick response to any issues.
- Maintenance and Inspection: Regular maintenance and inspection are critical for the reliable operation of underground conveyor systems. Maintenance activities include belt cleaning, roller and idler checks, and structural inspections to ensure the system remains in good working condition.
Advantages of Underground Conveyor Belt Systems
Underground conveyor belt systems offer several advantages, including:
- Efficiency: Underground conveyors provide continuous and efficient material transport, reducing the need for manual handling and haulage equipment. This leads to increased productivity and lower operational costs.
- Safety: By reducing the reliance on manual labor and haulage equipment, underground conveyor systems enhance safety in mining operations. They minimize the risk of accidents and injuries associated with material transport.
- Environmental Impact: Underground conveyor systems have a lower environmental impact compared to traditional haulage methods. They produce less noise, dust, and emissions, contributing to a cleaner and safer mining environment.
Case Studies: Successful Implementation of Underground Conveyor Systems
Numerous mining operations have successfully implemented underground conveyor belt systems. For example, coal mine conveyor systems have significantly improved the efficiency and safety of coal transport in underground mines. Similarly, iron ore conveyor systems have enhanced the productivity of iron ore mining operations, ensuring reliable material transport from the mining face to processing facilities.
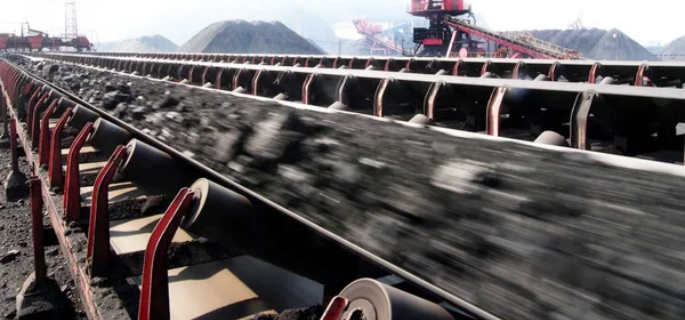
Mining Conveyor: Mining Components of Conveyor Systems
Conveyor systems in mining operations consist of various components that work together to ensure efficient material transport. Understanding the role and importance of each component is crucial for optimizing conveyor performance and ensuring reliable operation. In this section, we will cover the essential mining components of conveyor systems.
Key Components of Mining Conveyor Systems
- Belts: The conveyor belt is the most critical component of a mining conveyor system. It serves as the medium for material transport, and its durability and reliability are essential for efficient operation. Conveyor belts used in mining applications are typically made from high-strength materials, such as steel-cord or fabric-reinforced belts, to withstand heavy loads and abrasive conditions.
- Idlers and Rollers: Idlers and rollers support the conveyor belt and facilitate its smooth movement. They are designed to reduce friction and wear on the belt, ensuring efficient operation. In mining conveyor systems, idlers and rollers must be robust and capable of handling the harsh conditions of mining environments.
- Drive Systems: The drive system powers the conveyor belt and controls its speed and direction. It includes motors, gearboxes, and drive pulleys. In mining applications, drive systems must be powerful and reliable to handle the high demands of material transport.
- Pulleys: Pulleys are used to guide and tension the conveyor belt. They include head pulleys, tail pulleys, and snub pulleys. Properly designed and maintained pulleys are essential for the smooth operation of mining conveyor systems.
- Frames and Structures: The frames and structures of conveyor systems provide support and stability. They are constructed from high-strength materials to withstand the weight of the belt and transported materials. In mining applications, frames and structures must be durable and capable of withstanding the harsh conditions of mining environments.
- Scrapers and Cleaners: Scrapers and cleaners are used to remove material buildup on the conveyor belt. They help maintain belt cleanliness and prevent material spillage, ensuring efficient operation and reducing maintenance requirements.
- Safety Devices: Safety devices, such as emergency stop switches, belt misalignment detectors, and fire suppression systems, are critical for ensuring the safe operation of mining conveyor systems. These devices help prevent accidents and minimize the risk of injuries.
The Role of Each Component in Mining Conveyor Systems
- Belts: The belt is the backbone of the conveyor system, providing the surface for material transport. Its durability and reliability are crucial for continuous operation, especially in demanding mining environments.
- Idlers and Rollers: Idlers and rollers support the belt and facilitate its movement. They reduce friction and wear, ensuring the belt moves smoothly and efficiently. Properly maintained idlers and rollers are essential for minimizing downtime and extending the life of the conveyor system.
- Drive Systems: The drive system powers the belt and controls its speed and direction. It ensures the conveyor operates at the optimal speed for material transport, maximizing efficiency and productivity. Reliable drive systems are crucial for handling the high demands of mining operations.
- Pulleys: Pulleys guide and tension the belt, ensuring it runs smoothly and stays aligned. Properly designed and maintained pulleys are essential for preventing belt misalignment and minimizing wear and tear.
- Frames and Structures: The frames and structures provide support and stability to the conveyor system. They must be strong and durable to handle the weight of the belt and transported materials, especially in the harsh conditions of mining environments.
- Scrapers and Cleaners: Scrapers and cleaners maintain belt cleanliness and prevent material buildup. They are essential for efficient operation and reducing maintenance requirements. Properly functioning scrapers and cleaners help prevent material spillage and ensure the conveyor system runs smoothly.
- Safety Devices: Safety devices are critical for ensuring the safe operation of mining conveyor systems. They help prevent accidents and minimize the risk of injuries, ensuring a safe working environment for miners.
Importance of Each Component in Mining Conveyor Systems
Each component of a mining conveyor system plays a crucial role in ensuring efficient and reliable operation. The durability and reliability of these components are essential for minimizing downtime, reducing maintenance costs, and maximizing productivity. Properly designed and maintained conveyor components are critical for handling the high demands of mining operations and ensuring the safe and efficient transport of materials.
Case Studies: Effective Use of Conveyor Components in Mining Operations
Several mining operations have successfully implemented and optimized their conveyor systems by focusing on the key components. For example, high angle conveyor mining systems have been enhanced by using durable belts, robust idlers and rollers, and reliable drive systems. These improvements have resulted in increased efficiency and productivity, ensuring the smooth and reliable transport of materials in challenging mining environments.
Understanding the essential mining components of conveyor systems and their role in ensuring efficient and reliable operation is crucial for optimizing conveyor performance in mining operations. By focusing on the durability and reliability of these components, mining companies can achieve significant improvements in productivity, safety, and cost-efficiency.
Mining Conveyor Belt Manufacturers
Mining conveyor belt manufacturers play a crucial role in the mining industry by providing high-quality conveyor belts that ensure the efficient transportation of raw materials. This section will highlight some of the leading manufacturers, their products, and their contributions to the industry.
Leading Mining Conveyor Belt Manufacturers
Several companies are renowned for their expertise in manufacturing mining conveyor belts. These manufacturers are known for their commitment to quality, innovation, and customer satisfaction. Some of the leading mining conveyor belt manufacturers include:
- GRAM Conveyor: GRAM Conveyor is a distinguished manufacturer in the conveyor belt industry, particularly known for its high-quality products tailored for mining applications. Their conveyor belts are engineered for exceptional durability, outstanding performance, and resistance to the harshest mining conditions, ensuring reliable and efficient material transport.
- Fenner Dunlop: Fenner Dunlop is a global leader in conveyor belt manufacturing, offering a wide range of products designed for the mining industry. Their belts are known for their durability, performance, and resistance to wear and tear.
- ContiTech: ContiTech, a subsidiary of Continental AG, is a leading manufacturer of conveyor belts for various industries, including mining. Their products are designed to withstand the harsh conditions of mining environments and ensure reliable material transport.
- Bridgestone: Bridgestone is another prominent name in the conveyor belt for mining industry, offering high-quality belts for mining applications. Their belts are engineered to provide superior performance and longevity in demanding mining operations.
- Goodyear: Goodyear’s conveyor belts are widely used in the mining industry for their durability and reliability. The company offers a range of products tailored to meet the specific needs of mining operations.
- Phoenix Conveyor Belt Systems: Phoenix Conveyor Belt Systems, part of the BEUMER Group, specializes in manufacturing high-performance conveyor belts for mining applications. Their belts are designed to handle heavy loads and harsh conditions.
Products and Innovations
Mining conveyor belt manufacturers continuously innovate to improve the performance, durability, and efficiency of their products. Some of the key innovations in the industry include:
- Advanced materials: Manufacturers are using advanced materials, such as synthetic fabrics and polymers, to enhance the strength and durability of conveyor belts. These materials are designed to withstand the abrasive and heavy-duty nature of mining operations.
- Fire-resistant belts: Safety is a top priority in the mining industry, and many manufacturers offer fire-resistant conveyor belts to reduce the risk of fire hazards. These belts are made from materials that can withstand high temperatures and prevent the spread of fire.
- Energy-efficient belts: To reduce energy consumption and operational costs, manufacturers are developing energy-efficient conveyor belts. These belts are designed to minimize friction and improve the overall efficiency of the conveyor system.
- Customizable designs: Recognizing that each mining operation has unique requirements, manufacturers offer customizable conveyor belt designs. This allows mining companies to select belts that are tailored to their specific needs, ensuring optimal performance and efficiency.
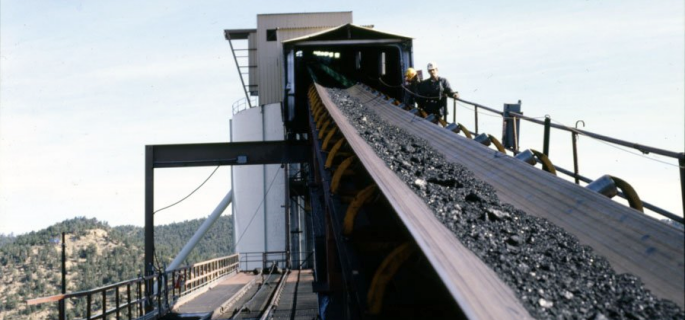
Contributions to the Mining Industry
Mining conveyor belt manufacturers play a vital role in supporting the mining industry by providing products that enhance the efficiency and safety of material transport. Some of the key contributions include:
- Improved productivity: High-quality conveyor belts ensure the smooth and continuous transport of raw materials, improving the overall productivity of mining operations.
- Enhanced safety: Manufacturers prioritize safety by offering fire-resistant and durable belts that reduce the risk of accidents and injuries in mining environments.
- Cost savings: Durable and energy-efficient conveyor belts help mining companies reduce operational costs and extend the lifespan of their equipment.
- Environmental sustainability: By developing energy-efficient and environmentally friendly products, manufacturers contribute to the sustainability of the mining industry.
Mining conveyor belt manufacturers play a crucial role in the mining industry by providing high-quality, innovative products that enhance the efficiency, safety, and sustainability of material transport. Their commitment to quality and customer satisfaction ensures that mining operations can rely on their conveyor belts for optimal performance and longevity.
Mining Conveyor: ABB Conveyor in Mining
ABB, a global leader in industrial technology, offers cutting-edge conveyor solutions tailored for the mining sector. Their advanced technologies and innovative designs provide numerous benefits, enhancing operational efficiency, safety, and productivity in mining operations. In this section, we will explore the various ABB conveyor solutions, their technologies, and the advantages they offer to mining operations.
ABB Conveyor Technologies
ABB’s conveyor solutions incorporate several advanced technologies designed to optimize mining conveyor operations. These technologies include:
- Variable Speed Drives (VSDs): ABB’s VSDs enable precise control of conveyor speeds, allowing for adjustments based on load requirements and operational conditions. This results in improved energy efficiency and reduced wear and tear on conveyor components.
- Automation and Control Systems: ABB’s automation solutions integrate seamlessly with mining conveyor systems, providing real-time monitoring, diagnostics, and control. This ensures optimal performance, reduces downtime, and enhances safety.
- Condition Monitoring Systems: ABB offers advanced condition monitoring solutions that continuously assess the health of conveyor components. These systems detect potential issues early, allowing for proactive maintenance and minimizing unplanned downtime.
- Gearless Conveyor Drives: ABB’s gearless conveyor drives eliminate the need for gearboxes, reducing maintenance requirements and improving efficiency. These drives are ideal for high-capacity mining conveyor systems, providing reliable and efficient operation.
Benefits of ABB Conveyor Solutions
ABB’s conveyor solutions offer several benefits to mining operations, including:
- Enhanced Efficiency: ABB’s advanced technologies optimize the performance of mining conveyor systems, improving throughput and reducing energy consumption. This leads to cost savings and increased productivity.
- Improved Safety: ABB’s automation and control systems enhance safety by providing real-time monitoring and diagnostics. This helps prevent accidents and ensures the safe operation of mining conveyor systems.
- Reduced Maintenance Costs: ABB’s condition monitoring systems detect potential issues early, allowing for timely maintenance and reducing the risk of costly breakdowns. Gearless conveyor drives further reduce maintenance requirements by eliminating the need for gearboxes.
- Scalability and Flexibility: ABB’s conveyor solutions are scalable and adaptable to various mining applications. Whether it’s a coal conveyor, coal mine conveyor, or iron ore conveyor, ABB’s technologies can be customized to meet specific operational requirements.
Case Studies: ABB Conveyor Solutions in Action
Several mining operations worldwide have successfully implemented ABB conveyor solutions. For instance, ABB’s gearless conveyor drives have been deployed in large-scale iron ore conveyor systems, resulting in significant improvements in efficiency and reliability. Additionally, ABB’s automation and control systems have been instrumental in optimizing the performance of coal conveyors and coal mine conveyors, ensuring smooth and efficient material transport.
FAQs about Mining Conveyor
The speed of a mining conveyor belt can vary depending on the application, but typically, conveyor belts in mining operations can travel at speeds ranging from 1 to 6 meters per second (approximately 3 to 20 feet per second).
The longest mining conveyor belt in the world is the conveyor belt at the Bou Craa phosphate mine in Western Sahara, which is approximately 98 kilometers (61 miles) long. This conveyor transports phosphate rock from the mine to the coast for shipment.
A conveyor works by using a motor to drive a system of pulleys and belts (or rollers) to move materials from one point to another. The motor powers the drive pulley, which in turn moves the belt. As the belt moves, it carries materials along its surface from the loading point to the discharge point. The system is designed to be efficient, continuous, and capable of handling various types of materials.
A mining mill works by grinding ore into fine particles to extract valuable minerals. The process typically involves crushing the ore to reduce its size, followed by grinding it in a mill using steel balls or rods. The ground ore is then processed using methods such as flotation, leaching, or magnetic separation to separate the desired minerals from the waste material. The extracted minerals are then further refined to produce the final product.
A mining shaft is called a “mine shaft.” It is a vertical or near-vertical tunnel that provides access to an underground mine. Mine shafts are used for the transportation of personnel, equipment, and extracted materials, as well as for ventilation purposes.
The purpose of a conveyor is to transport materials efficiently from one location to another. Conveyors are used in various industries, including mining, manufacturing, and logistics, to move bulk materials, products, or components along a predefined path. They improve efficiency, reduce manual labor, and enhance safety by automating the material handling process.
A mining conveyor is a type of conveyor system specifically designed for the transportation of minerals and other bulk materials in mining operations. These systems are crucial in the mining industry for moving large volumes of raw materials from mining sites to processing facilities. Mining conveyors can be found in both surface and underground mining operations, and they come in various configurations to handle the specific needs of the mining process. They are engineered to withstand harsh conditions and heavy loads, ensuring efficient and continuous movement of materials, which significantly boosts productivity and reduces manual labor costs.
There are three main types of conveyors commonly used across various industries, including mining:
Belt Conveyors: These are the most common type, using continuous belts to transport materials. They are highly versatile and can handle a wide range of bulk materials over long distances and various terrains.
Roller Conveyors: Utilizing rollers to move items, roller conveyors are often used in packaging and distribution. They are ideal for moving large, heavy items in a controlled manner and can be powered or gravity-driven.
Chain Conveyors: These conveyors use chains to move materials along the conveyor path. They are robust and suitable for heavy-duty applications, such as automotive assembly lines and pallet handling in warehouses.
A coal conveyor is a specific type of mining conveyor belt system designed to transport coal from the mining site to various locations such as processing plants, storage facilities, or directly to power generation units. Coal conveyors are built to handle the abrasive and dusty nature of coal, featuring reinforced belts, dust suppression systems, and heavy-duty components to ensure durability and efficiency. These conveyors are essential in the coal mining industry as they streamline the transportation process, reduce the need for manual handling, and improve safety by reducing the exposure of workers to hazardous conditions.
A conveyor is a mechanical system designed to move materials from one location to another efficiently and safely. Conveyors are widely used in various industries, including manufacturing, mining, logistics, and food processing, to automate the transportation of goods and materials. They can be configured in different ways to suit specific applications, such as horizontal, inclined, or vertical movement, and can handle a variety of materials, including bulk goods, packages, and individual items. By automating the movement of materials, conveyors increase productivity, reduce labor costs, and enhance workplace safety.
Last Updated on August 20, 2024 by Jordan Smith
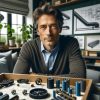
Jordan Smith, a seasoned professional with over 20 years of experience in the conveyor system industry. Jordan’s expertise lies in providing comprehensive solutions for conveyor rollers, belts, and accessories, catering to a wide range of industrial needs. From initial design and configuration to installation and meticulous troubleshooting, Jordan is adept at handling all aspects of conveyor system management. Whether you’re looking to upgrade your production line with efficient conveyor belts, require custom conveyor rollers for specific operations, or need expert advice on selecting the right conveyor accessories for your facility, Jordan is your reliable consultant. For any inquiries or assistance with conveyor system optimization, Jordan is available to share his wealth of knowledge and experience. Feel free to reach out at any time for professional guidance on all matters related to conveyor rollers, belts, and accessories.