Conveyor System Parts:Conveyor Belt Components
Conveyor system parts are essential components that ensure the efficient operation of conveyor systems. These parts include belts, rollers, motors, pulleys, bearings, and frames. Each part plays a critical role in the system’s functionality, enabling smooth material handling and transportation. Understanding these parts and their functions helps in maintaining and troubleshooting conveyor systems. Accessories like guides, sensors, and controllers further enhance the system’s performance. Proper maintenance and timely replacement of these parts are crucial for minimizing downtime and maximizing operational efficiency.
Conveyor System Parts List
Conveyor systems parts are integral to the efficient operation of any conveyor system, ensuring smooth and reliable material handling.Conveyor system parts include belts、rollers、pulleys、motors、bearings、frames、sensors and controls、accessories. This section will provide a detailed enumeration of the essential parts in a conveyor system, the importance of each part in the overall system, and the common materials and specifications for each part.
Detailed Enumeration of Essential Parts in a Conveyor System
- Belts: The belt is the most visible and crucial part of a conveyor system. It carries the material and moves it from one point to another. Conveyor belts can be made of various materials, including rubber, plastic, and metal, depending on the application.
- Rollers: Rollers support and guide the conveyor belt along its path. They are typically made of metal or plastic and are designed to rotate, reducing friction and wear on the belt.
- Pulleys: Pulleys drive the conveyor belt and change its direction. There are two main types of pulleys: drive pulleys, which are powered to move the belt, and conveyor idler pulleys, which guide the belt.
- Motors: Motors provide the necessary power to move the conveyor belt. They are usually electric and can vary in size and power output based on the conveyor’s requirements.
- Bearings: Bearings reduce friction and wear on the rotating parts of the conveyor system, such as rollers and pulleys. They are essential for ensuring smooth and efficient operation.
- Frames: The frame provides structural support for the conveyor system. It is typically made of steel or aluminum and is designed to withstand the operational loads and environmental conditions.
- Sensors and Controls: These conveyor system components monitor and control the operation of the conveyor system, ensuring it runs smoothly and efficiently. Sensors can detect the presence of materials, while control systems regulate the speed and direction of the conveyor belt.
- Accessories: Accessories such as guides, chutes, and diverters help manage the flow of materials on the conveyor system, improving efficiency and preventing jams.
Importance of Each Part in the Overall System
Each part of a conveyor system plays a vital role in its overall functionality:
- Belts: The belt is crucial for material transport, directly impacting the system’s efficiency and reliability.
- Rollers and Pulleys: These components ensure the belt moves smoothly, reducing friction and wear.
- Motors: Motors provide the power necessary to move the belt, making them essential for the system’s operation.
- Bearings: Bearings minimize friction and wear, extending the lifespan of rotating parts.
- Frames: The frame supports the entire system, ensuring it can handle the operational loads.
- Sensors and Controls: These components ensure the system operates efficiently and safely, preventing accidents and downtime.
- Accessories: Accessories enhance the system’s functionality, improving material handling and preventing issues such as jams.
Common Materials and Specifications for Each Part
- Belts: Made from rubber, plastic, or metal. Specifications include tensile strength, abrasion resistance, and temperature tolerance.
- Rollers: Typically made of steel or plastic. Specifications include diameter, width, and load capacity.
- Pulleys: Made from steel or aluminum. Specifications include diameter, width, and surface finish (e.g., grooved or smooth).
- Motors: Usually electric, with specifications including power output, voltage, and speed control options.
- Bearings: Made from steel or ceramic. Specifications include load capacity, rotational speed, and lubrication requirements.
- Frames: Made from steel or aluminum. Specifications include dimensions, weight capacity, and corrosion resistance.
- Sensors and Controls: Various materials and specifications based on application. Specifications include sensitivity, range, and compatibility with control systems.
- Accessories: Made from various materials depending on application. Specifications include dimensions, material compatibility, and operational features.
Conveyor System Parts: Conveyor Belt Parts and Accessories
Essential Conveyor Belt Parts and Accessories
Conveyor belts are equipped with various parts and accessories that enhance their performance and ensure smooth operation. This section will list critical parts and accessories, discuss their importance in enhancing conveyor belt performance, and provide recommendations for sourcing high-quality components of conveyor system.
List of Critical Parts and Accessories for Conveyor Belts
Belt Cleaners
- Description: Devices installed to remove material sticking to the belt, preventing build-up and carryback.
- Importance: Maintain belt cleanliness, reduce maintenance needs, and improve efficiency.
- Sourcing: Look for high-quality materials and adjustable designs for optimal performance.
Skirting Systems
- Description: Skirting systems prevent material spillage at loading points by sealing the sides of the conveyor belt.
- Importance: Reduce material loss, prevent build-up, and enhance safety.
- Sourcing: Opt for durable materials and easy-to-install designs.
Impact Beds
- Description: Installed at loading points to absorb the impact of falling materials, protecting the belt from damage.
- Importance: Extend belt life, reduce maintenance, and prevent material spillage.
- Sourcing: Choose robust designs with shock-absorbing materials.
Tracking Devices
- Description: Devices that help keep the conveyor belt aligned and centered.
- Importance: Prevent belt misalignment, reduce wear, and ensure smooth operation.
- Sourcing: Look for reliable and adjustable tracking solutions.
Belt Fasteners
- Description: Used to join the ends of a conveyor belt, ensuring a continuous loop.
- Importance: Provide a strong and durable connection, essential for belt integrity.
- Sourcing: Select high-quality, corrosion-resistant fasteners.
Vulcanizing Kits
- Description: Kits used for splicing conveyor belts through a vulcanization process.
- Importance: Create strong, seamless belt joints, enhancing belt strength and durability.
- Sourcing: Ensure the kits contain high-quality materials and tools for effective splicing.
Wear Liners
- Description: Protective liners installed on basic components of a conveyor system to reduce wear and extend their lifespan.
- Importance: Protect against abrasion, reduce maintenance, and improve component longevity.
- Sourcing: Choose high-durability materials suitable for the specific application.
Chutes and Hoppers
- Description: Chutes and hoppers guide and control the flow of materials onto the conveyor belt.
- Importance: Prevent material spillage, reduce dust, and ensure controlled material flow.
- Sourcing: Opt for robust designs that match the material handling requirements.
Dust Control Systems
- Description: Systems designed to capture and suppress dust generated during material handling.
- Importance: Improve air quality, enhance safety, and reduce maintenance needs.
- Sourcing: Look for efficient and reliable dust control solutions.
Importance of Accessories in Enhancing Conveyor Belt Performance
Accessories play a crucial role in enhancing the performance of conveyor belts by addressing specific operational challenges and improving efficiency. Belt cleaners maintain cleanliness, reducing the risk of carryback and build-up. Skirting systems and impact beds prevent material spillage and protect the belt from damage, extending its lifespan. Tracking devices ensure the belt remains aligned, reducing wear and operational disruptions. Belt fasteners and vulcanizing kits provide strong and durable connections, essential for belt integrity.
By investing in high-quality accessories, operators can enhance the overall performance of their conveyor belts, reduce maintenance needs, and ensure smooth and efficient operation. Accessories tailored to the specific requirements of the conveyor system can significantly improve productivity and reliability.
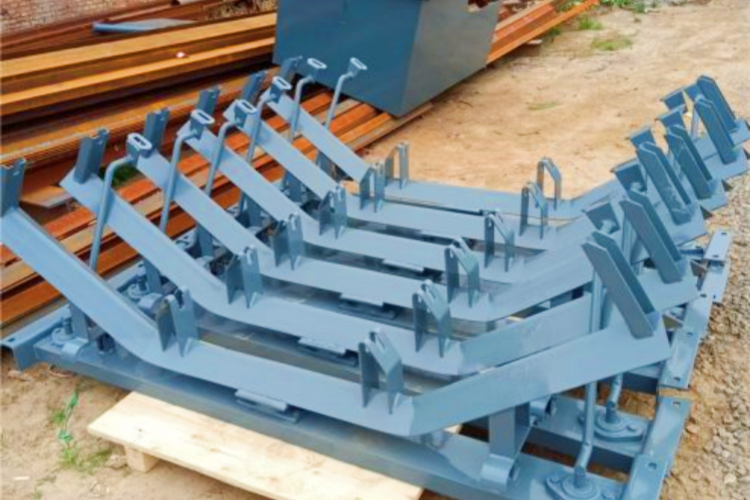
Conveyor System Parts and Functions
Explanation of Conveyor System Parts and Functions
Conveyor systems are integral to various industries, ensuring the efficient and seamless transportation of materials. Understanding the conveyor system parts and functions is crucial for optimizing performance and minimizing downtime. This section will delve into the detailed description of each part, how they contribute to the system’s efficiency and reliability, and maintenance tips to ensure optimal functionality.
Detailed Description of Conveyor System Parts
Conveyor Belts
- Function: Conveyor belts are the primary component, responsible for the actual movement of materials from one point to another.
- Contribution: They facilitate the continuous flow of materials, enhancing productivity and reducing manual handling.
- Maintenance: Regular inspections for wear and tear, prompt replacement of damaged sections, and ensuring proper tensioning to prevent slippage.
Pulleys
- Function: Pulleys guide and drive the conveyor belt, with drive pulleys powered to move the belt and idler pulleys supporting the belt’s return.
- Contribution: They ensure the smooth and controlled movement of the belt, crucial for maintaining the desired speed and direction.
- Maintenance: Regular lubrication of bearings, checking for alignment, and replacing worn-out pulleys to avoid belt misalignment.
Rollers
- Function: Rollers support the belt and materials, reducing friction and facilitating easy movement.
- Contribution: They enhance the belt’s stability and reduce energy consumption by minimizing friction.
- Maintenance: Regular cleaning to remove debris, inspecting for uneven wear, and replacing damaged rollers to maintain smooth operation.
Motors and Drives
- Function: Motors power the drive pulley, while drives control the speed and torque.
- Contribution: They are essential for the controlled and consistent movement of the conveyor belt, directly impacting the system’s efficiency.
- Maintenance: Regular inspection of electrical connections, monitoring motor temperature, and ensuring drives are properly calibrated.
Frames and Supports
- Function: Frames and supports provide the structural integrity and foundation for the conveyor system.
- Contribution: They ensure the system remains stable and securely positioned, which is critical for safe and efficient operation.
- Maintenance: Checking for structural damage, ensuring proper leveling, and tightening any loose bolts or connections.
Belting Accessories
- Function: Accessories such as belt cleaners, skirting, and tracking devices enhance the belt’s performance and longevity.
- Contribution: They help maintain the belt’s cleanliness, prevent material spillage, and ensure the belt stays aligned.
- Maintenance: Regular inspection and replacement of worn accessories to prevent conveyor belt damage and operational issues.
How Each Part Contributes to Efficiency and Reliability
Each component of a conveyor system plays a vital role in ensuring the overall efficiency and reliability of the operation. The conveyor belt is the backbone of the system, directly impacting the speed and flow of materials. Pulleys and rollers reduce friction and guide the belt, ensuring smooth and controlled movement. Motors and drives provide the necessary power and control, while frames and supports maintain the system’s structural integrity. Belting accessories further enhance performance by preventing issues such as material spillage and belt misalignment.
By understanding the functions and contributions of these conveyor system parts, operators can implement effective maintenance strategies to minimize downtime and extend the system’s lifespan. Regular inspections, timely replacements, and proper lubrication are essential practices that ensure each part functions optimally, contributing to the overall efficiency and reliability of the conveyor system.
Conveyor System Parts PDF
Accessibility of Conveyor System Parts PDF
Having a comprehensive parts list in PDF format is beneficial for maintenance and troubleshooting. This section will explore the benefits of having a conveyor system parts PDF, how to use it effectively, and sources for obtaining reliable PDFs.
Benefits of Having a Comprehensive Parts List in PDF Format
- Easy Access and Portability: PDFs can be easily accessed on various devices, including smartphones, tablets, and computers. This portability allows maintenance personnel to have the parts list readily available at all times.
- Consistent Formatting: PDFs maintain consistent formatting across different devices and platforms, ensuring that the parts list is easy to read and understand.
- Detailed Information: A comprehensive PDF can include detailed information about each part, including specifications, maintenance instructions, and part numbers, making it easier to identify and order replacement parts.
- Searchability: PDFs are searchable, allowing users to quickly find specific parts or information within the document, saving time and effort during maintenance and troubleshooting.
- Documentation and Record-Keeping: Keeping a digital parts list in PDF format provides a reliable and easily accessible record for future reference, ensuring that all necessary information is documented and readily available.
How to Use a Conveyor System Parts PDF for Maintenance and Troubleshooting
- Identify Parts: Use the PDF to identify the parts needed for maintenance or repair. Detailed descriptions and images can help ensure the correct parts are selected.
- Check Specifications: Verify the specifications of the parts to ensure compatibility with the existing system. This includes checking dimensions, materials, and load capacities.
- Follow Maintenance Instructions: Many parts lists in PDF format include maintenance instructions. Follow these instructions to perform routine maintenance and ensure the longevity of the system.
- Order Replacement Parts: Use the part numbers and supplier information provided in the PDF to order replacement parts. This ensures that the correct parts are obtained quickly and efficiently.
- Troubleshoot Issues: Use the PDF to troubleshoot issues by identifying potential problem areas and following recommended solutions. Detailed diagrams and descriptions can help pinpoint the source of the problem.
Sources for Obtaining Reliable Conveyor System Parts PDFs
- Manufacturer Websites: Many manufacturers provide comprehensive parts lists in PDF format on their websites. These documents are often the most reliable source of information.
- Industry Publications: Industry publications and technical manuals often include detailed parts lists for various conveyor systems. These can be a valuable resource for maintenance personnel.
- Equipment Suppliers: Suppliers of conveyor systems and components often provide parts lists in PDF format as part of their product documentation. These documents can be obtained directly from the supplier or through their websites.
- Maintenance and Repair Services: Companies that specialize in conveyor system maintenance and repair may offer parts lists in PDF format as part of their service documentation. These can be a useful resource for maintenance teams.
- Online Databases: There are several online databases and repositories that provide access to technical manuals and parts lists for a wide range of equipment, including conveyor systems. These databases can be a valuable source of information.
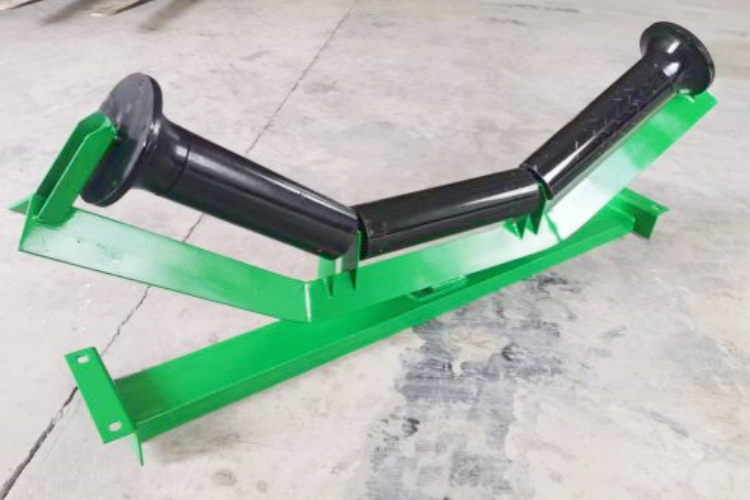
Conveyor System Parts Diagram
Detailed Conveyor System Parts Diagram
A detailed conveyor system parts diagram is an invaluable tool for maintenance, troubleshooting, and installation. This section will explain a typical conveyor system parts diagram, how to interpret it, and provide examples of diagrams for different types of conveyor systems.
Explanation of a Typical Conveyor System Parts Diagram
A conveyor system parts diagram provides a visual representation of the various components within a conveyor system and how they interact. Key elements typically included in the diagram are:
- Belt: The belt is depicted as the continuous loop that transports materials. Its path and direction of movement are shown clearly.
- Rollers: Rollers are shown supporting the belt along its path. They are usually illustrated as cylindrical shapes positioned at intervals.
- Pulleys: Pulleys, both drive and idler, are depicted at points where the belt changes direction or is driven.
- Motors: Motors are shown connected to the drive pulleys, indicating their role in powering the belt.
- Bearings: Bearings are represented at points where rotational parts are supported, such as rollers and pulleys.
- Frame: The frame is illustrated as the structural backbone of the system, showing how it supports all components.
- Sensors and Controls: Sensors and control units are depicted at strategic points for monitoring and controlling the conveyor’s operation.
- Accessories: Accessories such as guides, chutes, and diverters are included to show additional functionalities.
How to Interpret the Diagram for Maintenance and Installation
- Identifying Components: Use the diagram to identify all components of the conveyor system. Each part is usually labeled with a reference number or name.
- Understanding Connections: Observe how parts are connected and interact with each other. This helps in understanding the flow of materials and the mechanical relationships.
- Locating Issues: When troubleshooting, use the diagram to locate specific components and their positions within the system. This can help identify potential problem areas.
- Guiding Installation: During installation, follow the diagram to correctly assemble the conveyor system. Ensure that all parts are positioned and connected as shown to avoid errors.
- Planning Maintenance: Use the diagram to plan maintenance activities. Identify which parts need regular inspection, lubrication, or replacement.
Examples of Diagrams for Different Types of Conveyor Systems
- Belt Conveyor Systems: Diagrams for belt conveyor systems typically show the belt loop, rollers, drive and idler pulleys, motor, and frame. Additional components like sensors and guides may also be included.
- Roller Conveyor Systems: These diagrams highlight the arrangement of rollers along the conveyor path, the drive mechanism (if motorized), and the supporting frame.
- Chain Conveyor Systems: Chain conveyor diagrams focus on the chain loop, sprockets, motor, and supporting frame. They also show the interaction between the chain and the load carriers.
- Modular Belt Conveyor Systems: Diagrams for modular belt conveyor systems include the modular belt sections, support rollers, drive components, and the structural frame. They may also depict accessories like side guards and transfer modules.
- Plastic Parts Conveyor Systems: These diagrams illustrate plastic parts such as modular plastic belts, plastic rollers, and guides. They emphasize the use of plastic components for specific applications like food processing or clean environments.
By understanding the role and detailed enumeration of conveyor system parts, the benefits of having a parts list in PDF format, and how to interpret parts of a conveyor system diagrams, maintenance personnel can ensure efficient operation and longevity of conveyor systems. This comprehensive approach provides valuable insights into the essential components and their functions within the system.
Conveyor System Parts: Belt Conveyor Parts and Functions
In-Depth Look at Belt Conveyor Parts and Functions
Belt conveyors are among the most commonly used types of conveyor systems, renowned for their versatility and efficiency. This section provides an in-depth look at the key components specific to belt conveyors, their roles in the movement and control of the conveyor belt, and common issues along with maintenance practices.
Key Components Specific to Belt Conveyors
Head Pulley
- Role: The head pulley is the drive pulley that drives the belt, typically located at the discharge end of the conveyor.
- Function: It propels the belt, enabling the movement of materials along the conveyor.
- Common Issues: Wear on the pulley surface, misalignment, and slippage.
- Maintenance: Regular inspection for wear, ensuring proper alignment, and replacing worn pulleys.
Tail Pulley
- Role: The tail pulley is located at the loading end of the conveyor, providing tension and support to the belt.
- Function: It ensures the belt remains tight and aligned.
- Common Issues: Build-up of materials, misalignment, and wear.
- Maintenance: Cleaning to prevent material build-up, checking for alignment, and ensuring proper tension.
Snub Pulley
- Role: Snub pulleys are used to increase the wrap angle of the belt on the drive pulley.
- Function: They enhance the friction between the belt and drive pulley, improving traction.
- Common Issues: Wear and misalignment.
- Maintenance: Regular inspection for wear, ensuring proper alignment, and replacing if necessary.
Return Idlers
- Role: Return idlers support the belt on its return run and maintain belt alignment.
- Function: They reduce friction and support the empty belt.
- Common Issues: Wear, misalignment, and build-up of materials.
- Maintenance: Regular cleaning, checking for wear, and ensuring alignment.
Impact Beds
- Role: Impact beds are installed at the loading points to absorb the impact of falling materials.
- Function: They protect the belt from damage and reduce material spillage.
- Common Issues: Wear and damage from heavy impacts.
- Maintenance: Regular inspection for damage, replacing worn components, and ensuring proper installation.
Belt Cleaners
- Role: Belt cleaners remove material sticking to the belt to prevent build-up and carryback.
- Function: They maintain belt cleanliness and improve efficiency.
- Common Issues: Wear on the cleaning blades and improper installation.
- Maintenance: Regular inspection and replacement of cleaning blades, ensuring proper tension and installation.
The Role of Each Part in the Movement and Control of the Conveyor Belt
Each part of a belt conveyor system plays a crucial role in ensuring the smooth and efficient movement of the conveyor belt. The head pulley drives the belt, while the tail pulley maintains tension. Snub pulleys increase friction and traction, ensuring the belt moves efficiently. Return idlers support the belt on its return run, reducing friction and maintaining alignment. Impact beds protect the belt from damage at loading points, and belt cleaners prevent material build-up.
By understanding the specific roles and functions of these components, operators can better manage and maintain their belt part conveyor systems, ensuring continuous and reliable operation.
Common Issues and Maintenance Practices for Belt Conveyor Parts
Belt Wear and Tear
- Common Issues: Cracks, fraying, and cuts on the belt surface.
- Maintenance: Regular inspections, timely replacements, and ensuring proper tensioning to prevent excessive wear.
Pulley Slippage
- Common Issues: Reduced traction between the belt and drive pulley.
- Maintenance: Ensuring proper belt tension, replacing worn pulleys, and using snub pulleys to increase wrap angle.
Misalignment
- Common Issues: Belt running off-center, leading to uneven wear and potential damage.
- Maintenance: Regular alignment checks, adjusting idlers and pulleys, and using tracking devices.
Material Build-Up
- Common Issues: Accumulation of materials on pulleys, idlers, and the belt.
- Maintenance: Regular cleaning, using belt cleaners, and ensuring proper skirting to prevent spillage.
Bearing Failure
- Common Issues: Overheating, noise, and increased friction.
- Maintenance: Regular lubrication, monitoring temperature, and replacing worn bearings.
By addressing these common issues through proactive maintenance practices, operators can extend the lifespan of their belt conveyor parts, ensuring efficient and reliable operation.
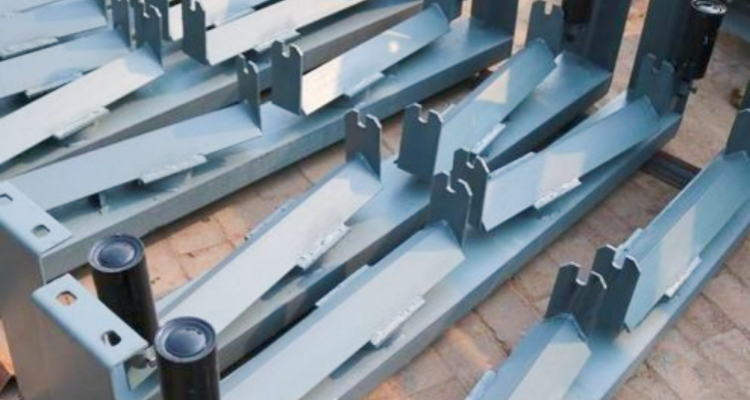
Replacement of Conveyor System Parts
Identify Worn or Damaged Parts
- Visual Inspections: Regularly check for visible signs of wear, damage, or deformation on belts, rollers, pulleys, and other components.
- Performance Monitoring: Track performance indicators such as increased noise, vibration, or decreased efficiency, which may signal the need for replacement.
- Scheduled Maintenance: Conduct thorough inspections during scheduled maintenance checks to identify parts that are nearing the end of their lifespan.
Plan for Replacement
- Replacement Schedule: Develop a replacement schedule based on the expected lifespan of components and the operational demands of the conveyor system.
- Inventory Management: Maintain a well-organized inventory of essential spare parts to ensure quick access when replacements are needed.
- Supplier Coordination: Establish strong relationships with suppliers to ensure the timely availability of replacement parts.
Prepare for Replacement
- Safety First: Ensure all safety protocols are followed, including shutting down the conveyor system and locking out/tagging out energy sources.
- Gather Tools and Equipment: Assemble all necessary tools and equipment required for the replacement process.
- Technical Documentation: Have technical manuals and replacement guides readily available for reference during the replacement process.
Replacement Procedure
- Remove Old Parts:
- Disassembly: Carefully disassemble the worn or damaged part, following the manufacturer’s guidelines to avoid causing further damage.
- Inspection: Inspect adjacent components for potential damage or wear that may have been caused by the faulty part.
- Install New Parts:
- Alignment and Tension: Ensure proper alignment and tension of belts, pulleys, and rollers during installation to avoid misalignment and operational issues.
- Secure Fastenings: Tighten all bolts, screws, and fastenings securely to prevent loosening during operation.
- Lubrication: Apply appropriate lubricants to moving parts as specified by the manufacturer.
Post-Replacement Checks
- Functionality Testing: Run the conveyor system at a low speed to check for proper installation and functionality of the new part.
- Adjustments: Make any necessary adjustments to alignment, tension, or lubrication based on the initial test run.
- Performance Monitoring: Monitor the performance of the conveyor system closely after replacement to ensure the new part is functioning correctly and efficiently.
Documentation and Record Keeping
- Maintenance Records: Update maintenance logs with details of the replacement, including the date, part replaced, and any observations or issues encountered.
- Warranty Information: Keep records of warranty information for new parts to facilitate claims if any issues arise.
- Future Planning: Use replacement records to refine future maintenance and replacement schedules, ensuring continuous improvement in system reliability and efficiency.
By following these steps, operators can effectively manage the replacement of conveyor system parts, ensuring minimal downtime and maintaining optimal performance and reliability of the conveyor system.
Recommendations for Sourcing High-Quality Conveyor System Parts
Choose Reputable Suppliers
- Research Supplier Reputation: Partner with suppliers known for their high-quality products and reliable service. Look for certifications such as ISO standards, which indicate adherence to quality management systems.
- Check Reviews and Testimonials: Customer reviews and testimonials can provide insight into the supplier’s reliability and product quality. Platforms like LinkedIn, industry forums, and supplier websites can be valuable resources.
- Industry Experience: Opt for suppliers with extensive experience in the conveyor industry, as they are likely to understand specific needs and challenges better.
Consider Material Compatibility
- Assess Application Needs: Select parts and accessories made from materials compatible with the specific conveyor application. For example:
- Corrosion-Resistant Materials: Stainless steel or plastic components for wet or chemical environments.
- Abrasion-Resistant Materials: Hardened steel or rubber components for heavy-duty or abrasive applications.
- Environmental Factors: Consider factors such as temperature, humidity, and exposure to chemicals when choosing materials.
Prioritize Durability and Performance
- Long-Lasting Materials: Opt for parts and accessories designed to withstand the operational demands of the conveyor system. Look for features such as:
- Wear Resistance: Components that can endure continuous use without significant degradation.
- Adjustability: Parts that can be easily adjusted to accommodate different products and operational changes.
- Ease of Maintenance: Components that are easy to clean, inspect, and replace.
Evaluate Customization Options
- Tailored Solutions: Consider suppliers that offer customized solutions tailored to the unique requirements of your conveyor system. Custom parts and accessories can enhance performance and address specific challenges.
- Design Support: Suppliers that provide design and engineering support can help create parts that perfectly fit your needs.
Ensure Easy Installation and Maintenance
- Simplified Processes: Choose parts and accessories that are easy to install and maintain. Simplified installation and maintenance processes can reduce downtime and improve operational efficiency.
- Tool-Free Maintenance: Components that can be maintained without the need for specialized tools can save time and reduce the risk of errors.
- Clear Documentation: Ensure that suppliers provide clear installation and maintenance instructions, as well as support for troubleshooting and repairs.
By focusing on these key areas, you can source high-quality conveyor parts and accessories that meet your operational needs and contribute to the efficiency and longevity of your conveyor systems.
Maintenance Tips for Ensuring Optimal Functionality of Conveyor Systems Parts
Scheduled Inspections
- Regular Check-Ups: Conduct routine inspections to identify potential issues before they escalate into significant problems.
- Signs to Watch For: Look for wear and tear, misalignment, and unusual noises that could indicate underlying issues.
- Inspection Log: Maintain a log of inspections and findings to track the condition of the conveyor system over time.
Proper Lubrication
- Lubricant Selection: Use recommended lubricants specific to the type of conveyor components.
- Lubrication Schedule: Follow the manufacturer’s guidelines on lubrication frequency and quantity.
- Focus Areas: Ensure all moving parts, such as pulleys, rollers, and bearings, are adequately lubricated to reduce friction and wear.
Timely Replacements
- Monitor Component Lifespan: Keep track of the expected lifespan of critical components and plan replacements accordingly.
- Spare Parts Inventory: Maintain a stock of essential spare parts to minimize downtime during replacements.
- Replacement Protocol: Replace worn-out or damaged parts promptly to prevent cascading failures.
Alignment Checks
- Regular Alignment Audits: Regularly check and adjust the alignment of the belt, pulleys, and rollers to ensure smooth operation.
- Alignment Tools: Use appropriate tools and methods to verify and correct misalignments.
- Impact of Misalignment: Understand that misalignment can lead to increased wear, reduced efficiency, and potential breakdowns.
Cleaning and Debris Removal
- Routine Cleaning: Implement a regular cleaning schedule to keep the conveyor system free of dirt and debris.
- Cleaning Methods: Use appropriate cleaning methods and tools to prevent damage to the belt and rollers.
- Debris Impact: Recognize that accumulated dirt can cause friction, wear, and operational issues.
By adhering to these maintenance tips, operators can ensure optimal functionality, enhanced performance, and increased reliability of the conveyor system. Regular maintenance not only extends the lifespan of components but also contributes to the overall efficiency and safety of the operation.
FAQs about Conveyor System Parts
A conveyor system consists of several key components that work together to transport materials from one location to another. The main parts include:
Conveyor Belt: The surface on which materials are transported.
Pulleys: Used to drive and redirect the belt. The drive pulley is powered, while the idler pulley helps in maintaining tension.
Motor: Provides the necessary power to move the conveyor belt.
Rollers: Support the belt and reduce friction.
Frame: The structure that supports the entire system and provides stability.
Bearings: Reduce friction between moving parts and support the rollers.
Controls: Include sensors, switches, and other devices to control the conveyor’s operation.
Cleats and Sidewalls: Used for transporting loose or granular materials, ensuring they stay on the belt.
Each of these components is crucial for the efficient operation of a conveyor system, ensuring smooth and reliable material handling.
Conveyor systems come in various types, each designed to suit specific applications and industries. The main types include:
Belt Conveyors: Use a continuous belt to transport materials. They are ideal for moving large volumes over long distances.
Roller Conveyors: Consist of rollers that allow materials to move easily. Suitable for heavy loads and accumulation applications.
Chain Conveyors: Use chains to move heavy or bulky items. Common in automotive and heavy manufacturing industries.
Slat Conveyors: Utilize slats or plates to transport items. Ideal for assembly lines and heavy-duty tasks.
Modular Belt Conveyors: Made of interlocking plastic segments. They offer flexibility and are easy to maintain, ideal for food processing and packaging.
Overhead Conveyors: Use a network of overhead tracks to transport materials. Common in paint lines and car assembly plants.
Screw Conveyors: Use a helical screw element to move materials. Suitable for granular or powdery substances.
Pneumatic Conveyors: Use air pressure to move materials through tubes. Ideal for bulk materials and fine particles.
A conveyor system is a mechanical handling device used to transport materials from one location to another efficiently. These systems are widely used in various industries, including manufacturing, packaging, mining, and logistics, to streamline processes and improve productivity.
Conveyor systems consist of several key components such as belts, rollers, motors, pulleys, and controls that work together to move materials smoothly and continuously. They can transport a wide range of items, including raw materials, finished products, and bulk goods, across short or long distances within a facility.
The main benefits of using a conveyor system include increased efficiency, reduced labor costs, enhanced safety, and the ability to handle heavy loads and continuous operation. Conveyor systems can be customized to meet specific industry needs, making them a versatile and essential tool in modern industrial operations.
Designing a conveyor system involves several critical steps to ensure it meets the operational requirements and integrates seamlessly with existing processes. Here are the main steps:
Determine Requirements: Identify the type of materials to be transported, their size, weight, and the distance they need to travel. Consider the required speed and the overall volume of materials.
Select the Conveyor Type: Choose the appropriate type of conveyor (e.g., belt, roller, modular) based on the material characteristics and application.
Layout Design: Plan the conveyor path, considering space constraints, workflow, and integration with other equipment. Optimize the layout for efficient material flow.
Component Selection: Choose the appropriate components, including the conveyor belt, pulleys, rollers, motor, and control systems. Ensure they are compatible and capable of handling the load.
Structural Design: Design the supporting structure to provide stability and safety. Consider factors like load distribution, material strength, and environmental conditions.
Control Systems: Integrate sensors, switches, and automation controls to manage the conveyor’s operation. This includes start/stop controls, speed regulation, and safety mechanisms.
Safety Features: Implement safety features such as guards, emergency stops, and warning signals to protect workers and equipment.
Testing and Validation: Once the design is complete, conduct testing to ensure the conveyor system operates as intended. Make any necessary adjustments to optimize performance.
Last Updated on August 8, 2024 by Jordan Smith
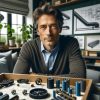
Jordan Smith, a seasoned professional with over 20 years of experience in the conveyor system industry. Jordan’s expertise lies in providing comprehensive solutions for conveyor rollers, belts, and accessories, catering to a wide range of industrial needs. From initial design and configuration to installation and meticulous troubleshooting, Jordan is adept at handling all aspects of conveyor system management. Whether you’re looking to upgrade your production line with efficient conveyor belts, require custom conveyor rollers for specific operations, or need expert advice on selecting the right conveyor accessories for your facility, Jordan is your reliable consultant. For any inquiries or assistance with conveyor system optimization, Jordan is available to share his wealth of knowledge and experience. Feel free to reach out at any time for professional guidance on all matters related to conveyor rollers, belts, and accessories.