Innovative Conveyor Belt Tape: Revolutionizing Repairs
Conveyor belt tape plays a pivotal role in the repair and maintenance of conveyor systems, offering a practical and efficient solution for extending the life of conveyor belts. These tapes come in various types, each designed to address specific issues in industrial settings. From quick fixes to more substantial repairs, conveyor belt tape is an essential tool in maintaining the continuous and effective operation of conveyor systems. Its versatility and ease of use make it a go-to solution for emergency and routine maintenance tasks.
Conveyor Belt Tape: A Quick Fix Solution
A conveyor belt tape is a vital component in the toolkit for maintaining the integrity and continuity of conveyor systems. This specialized tape is designed to provide quick, efficient repairs to damaged conveyor belts, thereby reducing downtime and maintaining productivity. Its unique properties include strong adhesive strength, durability, and flexibility, making it suitable for a wide range of repair scenarios.
Types of Damages Addressed
- Surface Cuts and Abrasions: Repair tape effectively seals cuts and abrasions, preventing further deterioration.
- Small Tears and Punctures: It provides a quick fix for minor tears and punctures, ensuring the belt remains functional.
- Edge Damages: The tape can be used to repair frayed or damaged edges, a common issue with conveyor belts.
Advantages of Using Conveyor Belt Repair Tape
- Speed: Enables rapid repairs, minimizing downtime.
- Cost-Effectiveness: A more affordable solution compared to replacing entire sections of the conveyor belt.
- Ease of Application: Can be applied quickly and easily without the need for specialized equipment.
- Flexibility: Accommodates the movement and flexing of the conveyor belt during operation.
Application Process
- Surface Preparation: The damaged area is cleaned and prepared to ensure the tape adheres properly.
- Tape Application: The tape is applied over the damaged area, providing a secure and durable bond.
- Curing Time: After application, the tape requires a short curing time to achieve maximum adhesive strength.
Conveyor Belt Tape Sizes and Selection
Selecting the right size and type of conveyor belt tape is crucial for effective repair and maintenance. The market offers a variety of tape sizes, each suited to different types of damage and conveyor belt widths.
Factors in Tape Size Selection
- Extent of Damage: Larger damages require wider tapes to provide adequate coverage and strength.
- Belt Width: The tape width should be proportional to the belt width to ensure a balanced repair.
- Type of Conveyor System: Different systems may require specific tape types and sizes based on their operational demands.
Available Sizes and Types
- Standard Sizes: Commonly range from narrow strips for minor repairs to wider tapes for significant damages.
- Custom Sizes: Some manufacturers offer custom-sized tapes for unique or large-scale repair needs.
Guidelines for Tape Selection
- Assess the Damage: Evaluate the size and nature of the damage to determine the appropriate tape size.
- Consider Operational Conditions: Factors such as belt speed, load, and environmental conditions should influence the tape choice.
- Manufacturer Specifications: Refer to manufacturer guidelines for recommended tape sizes based on specific conveyor belt models.
Importance of Proper Selection
- Ensuring Repair Effectiveness: The right size and type of tape ensure the repair is effective and durable.
- Preventing Further Damage: Incorrect tape size or type can lead to inadequate repairs, potentially causing further damage to the belt.
- Maintaining System Efficiency: Proper repairs maintain the efficiency and longevity of the conveyor system.
Understanding the available sizes and types of conveyor belt tape and selecting the appropriate one based on specific repair needs is essential for effective maintenance and prolonged conveyor belt life.
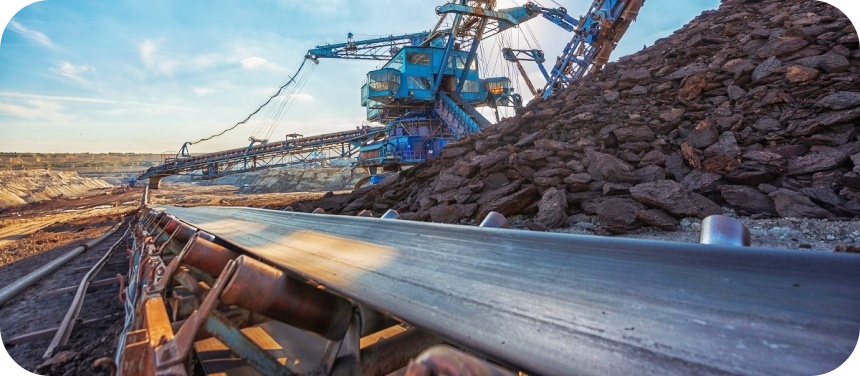
Conveyor Belt Tape Sizes and Selection
Conveyor Belt Tape: Tailoring Repairs with Precision
In the intricate world of conveyor belt maintenance, conveyor belt tape emerges as a pivotal component, offering a swift and reliable solution for reinforcing and repairing minor damages. Understanding the various sizes of conveyor belt tapes available in the market and selecting the appropriate size based on the extent and nature of the conveyor belt damage is crucial for maintaining the integrity and longevity of the conveyor system.
1. The Spectrum of Conveyor Belt Tape Sizes
Conveyor belt tapes come in a wide array of sizes, each designed to cater to specific repair needs. From narrow tapes for minor nicks and cuts to wider tapes for more substantial damages, the market offers a solution for virtually every scenario. The width and length of the tape determine the area it can cover, making it essential to understand the dimensions of the damage before selecting a tape.
2. Assessing the Damage: The First Step in Tape Selection
The process of selecting the right conveyor belt tape begins with a thorough assessment of the damage. Factors such as the length, width, and depth of the cut or wear, the location of the damage on the belt, and the operational load the belt carries play a crucial role in this decision-making process. It’s not just about covering the damage; it’s about reinforcing the area to withstand the operational stress.
3. Matching Tape Size to Damage Extent
Once the damage is assessed, the next step is to match the tape size to the extent of the damage. For minor damages, a narrow tape might suffice, effectively sealing the cut and preventing further deterioration. For larger or more complex damages, a wider tape or multiple strips might be necessary to provide ample coverage and reinforcement. The key is to ensure that the tape not only covers the damaged area but also extends beyond it, offering a buffer zone that enhances the repair’s durability.
4. The Role of Tape Thickness
Apart from the width and length, the thickness of the conveyor belt tape is also a significant factor. Thicker tapes offer more substantial reinforcement, making them suitable for areas that undergo higher stress or where the belt has a critical role in the operation. However, thicker tapes might also affect the flexibility of the belt, a factor that needs consideration, especially in systems with smaller pulleys or intricate pathways.
Selecting the right size of conveyor belt tape is a nuanced process that requires a keen understanding of the damage, the operational demands of the system, and the properties of the tape itself. It’s a balance between providing adequate coverage and reinforcement while maintaining the belt’s integrity and operational efficiency.
Conveyor Belt Tape Patch: Reinforcing Damaged Areas
Conveyor Belt Tape: The Art of Reinforcement with Patches
Conveyor belt tape patches are more than just a quick fix; they are a strategic reinforcement for damaged areas, ensuring that the repair is not just temporary but durable and reliable. Understanding how conveyor belt patches work and applying them correctly is paramount for achieving optimal results and prolonging the belt’s operational life.
1. The Mechanism of Conveyor Belt Patches
Conveyor belt patches are specially designed to adhere to the belt’s surface, offering a strong and resilient layer over the damaged area. These patches are typically made from materials that mimic the belt’s properties, ensuring that the repair integrates seamlessly with the belt’s structure and function. The patches come in various sizes and shapes, each tailored to address specific types of damage.
2. Preparing the Damaged Area: The Foundation of Effective Patching
The effectiveness of a conveyor belt patch hinges on the preparation of the damaged area. The area must be cleaned thoroughly, removing any debris, dust, or contaminants that might hinder the patch’s adhesion. The edges of the damage should be defined clearly, creating a clean area for the patch to adhere to.
3. Applying the Patch: Precision and Patience
Applying the conveyor belt patch is a process that demands precision and patience. The patch must be aligned perfectly with the damaged area, ensuring that it covers the entire extent of the damage and adheres uniformly to the belt’s surface. Pressure must be applied evenly across the patch, ensuring that it bonds securely without any air pockets or weak spots.
4. Post-Application: Ensuring a Strong Bond
Once the patch is applied, it’s crucial to allow ample time for the adhesive to cure and the patch to bond securely with the belt. This curing time varies based on the adhesive used and the environmental conditions. During this period, the belt should not be subjected to operational stress, allowing the patch to integrate fully and form a strong, resilient repair.
Conveyor belt tape patches offer a robust solution for reinforcing damaged areas, but their effectiveness relies heavily on the correct application. From assessing the damage and preparing the area to applying the patch and allowing it to cure, each step is crucial in ensuring that the repair not only covers the damage but also enhances the belt’s strength and longevity.
Conveyor Belt Tape Repair Glue: Ensuring Strong Bonds
Conveyor Belt Tape: The Role of Repair Glue in Ensuring Durability
While conveyor belt tape and patches provide the physical reinforcement needed for repairs, it’s the conveyor belt repair glue that ensures these components bond securely with the belt, offering a repair that’s both strong and lasting. Selecting the right type of glue and applying it correctly is paramount for the success of the repair.
1. The Importance of Choosing the Right Glue
Not all glues are suitable for conveyor belt repairs. The right glue must be compatible with the belt’s material, capable of withstanding the operational conditions, and able to form a strong bond that resists wear, pressure, and environmental factors. Specialized conveyor belt repair glues are formulated to meet these requirements, offering a bond that’s as resilient as the belt itself.
2. Preparing the Surface: The Key to Strong Adhesion
The strength of the bond formed by the repair glue depends significantly on the preparation of the surface. The area must be clean, dry, and free from any contaminants. Roughening the surface slightly can also enhance the glue’s adhesion, creating a stronger bond between the tape or patch and the belt.
3. Applying the Glue: Precision in Every Drop
Applying the conveyor belt repair glue requires precision. The glue must be spread evenly across the surface, ensuring that it covers the entire area where the tape or patch will be applied. Too little glue might lead to weak spots, while too much glue can cause messy overflow that hinders the repair’s integrity.
4. Curing Time: Patience for Optimal Strength
After applying the glue and the tape or patch, it’s crucial to allow sufficient time for the glue to cure fully. This curing time ensures that the glue forms a bond that’s strong and capable of handling the operational demands of the conveyor system. Rushing this process can compromise the repair’s durability and effectiveness.
Conveyor belt repair glue is a critical component in the repair process, offering the adhesive strength needed to ensure that tapes and patches bond securely with the belt. From selecting the right glue to preparing the surface, applying the glue, and allowing it to cure, each step is vital in ensuring that the repair not only covers the damage but also restores the belt’s integrity and operational capability.
Flexco Belt Tape: A Premium Repair Solution
Introduction to Flexco Belt Tape
Flexco conveyor belt tape represents a significant advancement in conveyor belt repair technology. Known for its durability and strength, Flexco conveyor belt tape is designed to offer a superior solution for repairing conveyor belts in demanding industrial environments. Unlike standard tapes, Flexco’s product is engineered to withstand harsh conditions, ensuring long-lasting repairs and minimal downtime.
Unique Features of Flexco Belt Tape
- High Tensile Strength: Flexco belt tape is manufactured with materials that provide exceptional tensile strength, making it suitable for heavy-duty applications.
- Enhanced Adhesive Properties: The tape features advanced adhesive technology that ensures a strong bond to the conveyor belt surface, resisting peeling or lifting under stress.
- Resistance to Wear and Tear: It is highly resistant to abrasion, cuts, and tears, maintaining its integrity even in the presence of sharp or abrasive materials.
- Flexibility: Despite its strength, the tape retains flexibility, allowing it to move with the conveyor belt without cracking or breaking.
Advantages Over Standard Tapes
- Longer Lifespan: Flexco belt tape lasts significantly longer than standard tapes, reducing the frequency of repairs.
- Better Performance in Extreme Conditions: It performs reliably in extreme temperatures and in the presence of oils, chemicals, and other corrosive substances.
- Ease of Application: The tape can be applied quickly and easily, reducing repair time and labor costs.
Case Studies
- Mining Industry Application: In a case where a mining conveyor belt suffered frequent abrasions, Flexco belt tape provided a durable repair solution, significantly extending the belt’s service life.
- Food Processing Plant: A food processing plant used Flexco belt tape to repair a conveyor belt that was exposed to high moisture and varying temperatures, with the tape maintaining its adhesive strength and integrity.
- Logistics and Distribution Center: In a high-traffic conveyor system, Flexco belt tape was used to repair surface damages, demonstrating its ability to withstand continuous use without degradation.
Grip Face Conveyor Belt Tape: Enhancing Traction and Stability
Exploring Grip Face Conveyor Belts
A grip face conveyor belt tape is a specialized type of conveyor belt designed to enhance traction and stability during material handling. These belts feature a textured surface that provides additional grip, preventing slippage and ensuring the secure transport of materials, especially in inclined or high-speed applications.
Role in Improving Traction and Stability
- Increased Grip: The textured surface increases friction between the belt and the materials being transported, reducing the risk of slippage.
- Stability in Inclined Applications: Grip face belts are particularly effective in inclined conveyors, where the risk of material rollback is higher.
- Enhanced Safety: By preventing slippage, these belts contribute to safer operations, especially when transporting heavy or uneven loads.
Comparison with Standard Conveyor Belts
- Performance: Grip face belts often outperform standard belts in applications where additional traction is required.
- Application Suitability: While standard belts are sufficient for flat and low-speed conveyors, grip face belts are preferred for steep inclines, high-speed applications, and environments where materials are prone to slipping.
- Durability: These belts are typically more durable in specific applications, as the added grip reduces the strain on the belt caused by slippage.
Advantages of Grip Face Conveyor Belts
- Reduced Material Loss: The enhanced grip minimizes material loss due to slippage, particularly in the transport of granular or particulate materials.
- Improved Efficiency: By ensuring stable material transport, these belts contribute to the overall efficiency of the conveyor system.
- Versatility: Grip face belts can be used in a variety of industries, including agriculture, mining, and packaging, where secure material handling is crucial.
Grip face conveyor belts offer a significant advantage in applications requiring enhanced traction and stability. Their specialized design improves safety and efficiency, making them a valuable choice for industries with specific material handling challenges.
Speak with our team about custom conveyor belt options.
Teflon Belt Manufacturers and Tefsil Tape: High-Temperature Solutions
Conveyor Belt Tape: Navigating High-Temperature Challenges with Teflon and Tefsil
In the demanding world of industrial operations, certain applications require conveyor solutions that can withstand extreme temperatures. This is where Teflon belts and Tefsil tape come into play, offering unparalleled performance in high-temperature environments. This section provides an overview of these specialized conveyor belt tapes, shedding light on their design, applications, and the meticulous process manufacturers undergo to ensure these belts meet the rigorous demands of high-temperature operations.
1. The Essence of Teflon Belts and Tefsil Tape
Teflon belts and Tefsil tape are renowned for their exceptional heat resistance, making them ideal for applications where conventional conveyor belts would falter. These materials can withstand temperatures that range from as low as -73°C to as high as 260°C, maintaining their integrity and functionality even in the most challenging conditions. The key to their performance lies in the unique properties of Teflon (PTFE), which offers not only heat resistance but also chemical resistance and low friction.
2. Applications in High-Temperature Environments
Teflon belts and Tefsil tape find their applications in a myriad of industries where high temperatures are a norm. From food processing and packaging, where they come in contact with hot products, to chemical processing plants where they are exposed to corrosive substances and high heat, these belts ensure continuous operation without degradation. Their non-stick surface also makes them ideal for applications where product release is critical, such as in baking or drying processes.
3. Designing for Extreme Conditions
Manufacturers of Teflon belts and Tefsil tape employ advanced technology and materials science to engineer these products. The process involves selecting the right grade of Teflon and constructing the belt or tape to maximize its tensile strength, durability, and thermal stability. The thickness, width, and structure of the belts are meticulously designed to ensure they can handle the operational load, resist wear and tear, and provide a long service life, even under extreme conditions.
4. Ensuring Quality and Performance
Quality assurance is paramount in the manufacturing of Teflon belts and Tefsil tape. Rigorous testing is conducted to ensure that these products meet the highest standards of quality and performance. Tests include temperature resistance checks, tensile strength assessments, and chemical compatibility evaluations. Manufacturers also focus on continuous improvement, seeking feedback from the field and innovating their products to meet the evolving needs of industries.
Teflon belts and Tefsil tape represent the pinnacle of high-temperature conveyor belt solutions. Their ability to withstand extreme temperatures, coupled with their durability and low maintenance requirements, make them an indispensable part of operations in industries where heat is a constant challenge. Manufacturers of these belts and tapes play a crucial role, not just in producing these products, but in driving innovation and setting new benchmarks in the field of high-temperature conveyor technology.
Conveyor Belt Tape Rollers: Supporting the Tape and Belt System
Conveyor Belt Tape: The Integral Role of Rollers in Conveyor Systems
Conveyor belt rollers are more than just components; they are the backbone of any conveyor system, providing the necessary support and facilitating smooth and efficient movement of the conveyor belt. This section delves into the importance of conveyor belt rollers, their interaction with conveyor belt tapes and patches during repairs and maintenance, and how they contribute to the overall functionality of the conveyor system.
1. The Critical Role of Conveyor Belt Rollers
Conveyor belt rollers are strategically placed to support the belt, reduce friction, and facilitate the movement of materials. They are designed to withstand the weight of the materials being transported and the operational stress exerted by the moving belt. The proper functioning of these rollers is crucial for the efficiency of the conveyor system, as any malfunction can lead to increased friction, wear and tear on the belt, and ultimately, system downtime.
2. Interaction with Conveyor Belt Tapes and Patches
During repairs and maintenance, the interaction between the conveyor belt rollers and the tapes or patches used for repair is of paramount importance. The rollers must provide a smooth and even surface for the repaired sections of the belt to pass over. Any irregularities or misalignments can compromise the integrity of the repair, leading to potential weak spots or further damage to the belt. Therefore, ensuring that the rollers are in optimal condition is a critical aspect of conveyor belt maintenance.
3. Ensuring Smooth Operation and Longevity
The longevity and smooth operation of a conveyor system are directly influenced by the condition and quality of the conveyor belt rollers. Regular inspections, timely maintenance, and immediate replacement of worn or damaged rollers are essential practices. These actions prevent undue stress on the conveyor belt, ensure that repairs such as tapes and patches perform as intended, and ultimately extend the service life of the entire conveyor system.
4. Choosing the Right Rollers for the System
Selecting the right conveyor belt rollers involves considering factors such as the weight of the materials being transported, the speed of the conveyor, the environmental conditions, and the type of conveyor belt in use. Rollers come in various materials, diameters, and designs, each suited for specific applications and operational requirements. Understanding these factors and making an informed choice can significantly impact the efficiency, safety, and longevity of the conveyor system.
Conveyor belt rollers play a pivotal role in the functionality and efficiency of conveyor systems. Their interaction with a conveyor belt tape and patches during repairs, their contribution to reducing operational stress, and their influence on the longevity of the system underscore their importance. Ensuring that these rollers are well-maintained, correctly aligned, and suitably chosen for the specific requirements of the system is crucial for the smooth and efficient operation of any conveyor belt system.
Last Updated on July 16, 2024 by Jordan Smith
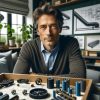
Jordan Smith, a seasoned professional with over 20 years of experience in the conveyor system industry. Jordan’s expertise lies in providing comprehensive solutions for conveyor rollers, belts, and accessories, catering to a wide range of industrial needs. From initial design and configuration to installation and meticulous troubleshooting, Jordan is adept at handling all aspects of conveyor system management. Whether you’re looking to upgrade your production line with efficient conveyor belts, require custom conveyor rollers for specific operations, or need expert advice on selecting the right conveyor accessories for your facility, Jordan is your reliable consultant. For any inquiries or assistance with conveyor system optimization, Jordan is available to share his wealth of knowledge and experience. Feel free to reach out at any time for professional guidance on all matters related to conveyor rollers, belts, and accessories.