EP 400 3 Conveyor Belt – Industrial Strength and Durability
Conveyor belts are essential in various industrial applications, providing efficient material handling solutions. They are used in manufacturing, mining, and logistics to transport goods seamlessly. Among the different types of conveyor belts, EP (Polyester/Nylon) conveyor belts stand out due to their durability and flexibility. This blog will focus on the EP 400 3 conveyor belt, a popular choice in many industries. The EP 400 3 conveyor belt combines high tensile strength and low elongation, making it ideal for heavy-duty operations. We will explore its features, benefits, and applications, highlighting why the EP 400 3 conveyor belt is a preferred option for industrial material handling needs.
What is an EP 400 3 Conveyor Belt
The EP 400/3 conveyor belt is a specialized type of conveyor belt designed for industrial applications. “EP” stands for Polyester in the warp direction and Nylon in the weft direction, combining the strengths of both materials to create a durable and flexible belt. The “400/3” designation indicates that the belt has a tensile strength of 400 N/mm and is constructed with 3 plies. This combination ensures that the EP 400/3 conveyor belt can handle significant loads and maintain performance under various conditions.
Key Features
The EP 400 3 conveyor belt is renowned for its outstanding performance characteristics, making it a preferred choice for demanding industrial environments. Below are the key features that contribute to its effectiveness and reliability:
- High Strength and Durability: The EP 400 3 conveyor belt offers exceptional tensile strength, making it suitable for heavy-duty applications.
- Excellent Flexibility and Elongation Properties: The polyester and nylon composition provides the belt with the flexibility needed to navigate complex conveyor systems while maintaining its structural integrity.
- Resistance to Moisture and Mildew: The materials used in the EP 400 3 conveyor belt are resistant to moisture and mildew, ensuring longevity even in damp environments.
- Low Stretch Characteristics: The belt’s construction minimizes stretching, which helps maintain consistent performance and reduces the need for frequent adjustments.
- Temperature Resistance: It can operate effectively in a wide range of temperatures, making it versatile for various industrial settings.
- Abrasion Resistance: The EP 400 3 conveyor belt is designed to withstand wear and tear, ensuring a longer service life.
- Chemical Resistance: It is resistant to various chemicals, which makes it suitable for industries where exposure to corrosive substances is common.
- Ease of Maintenance: The belt’s robust construction and material properties reduce the frequency of maintenance and downtime, contributing to improved operational efficiency.
The EP 400 3 conveyor belt is a robust and versatile solution for industrial material handling, offering high strength, durability, and resistance to environmental factors. Its composition and key features make it a reliable choice for various applications, ensuring efficient and uninterrupted operations.
Detailed Insights into the EP 400 3 Conveyor Belt
The EP 400 3 conveyor belt is designed to meet the rigorous demands of various industrial applications. Below is a detailed breakdown of its specifications, highlighting its superior performance characteristics.
- Tensile Strength: The EP 400 3 conveyor belt has a tensile strength of 400 N/mm. This high tensile strength ensures that the belt can handle significant loads and withstand heavy usage without compromising its integrity.
- Number of Plies: This conveyor belt is constructed with 3 plies. The multi-ply construction enhances its durability and provides additional strength, making it suitable for demanding industrial environments.
- Width Options: The EP 400 3 conveyor belt is available in various width options, typically ranging from 500mm to 2200mm. This range of widths allows for customization based on the specific requirements of different applications.
- Cover Thickness: The cover thickness of the EP 400 3 conveyor belt varies from 1mm to 25mm, depending on the application. Thicker covers provide better protection against abrasion and impact, while thinner covers offer greater flexibility.
Comparative Analysis with Other EP Belts
To provide a clearer understanding of the EP 400 3 conveyor belt’s capabilities, let’s compare its specifications with those of other EP belts such as EP 200/2 and EP 800/4.
Key Comparisons:
- Tensile Strength: The EP 400 3 conveyor belt offers a tensile strength of 400 N/mm, which is double that of the EP 200/2 and half of the EP 800/4. This makes it a balanced option for applications requiring moderate to high strength.
- Number of Plies: With 3 plies, the EP 400/3 provides enhanced durability compared to the 2-ply EP 200/2, while still being more flexible than the 4-ply EP 800/4.
- Width Options: The EP 400/3 conveyor belt’s width range of 500mm to 2200mm makes it versatile and adaptable to a wide variety of applications, offering more options than the narrower EP 200/2.
- Cover Thickness: The EP 400/3 conveyor belt’s cover thickness range of 1mm to 25mm provides a good balance between protection and flexibility, catering to different industrial needs better than the EP 200/2 but not as extensively as the EP 800/4.
The EP 400/3 conveyor belt stands out for its robust tensile strength, versatile width options, and adaptable cover thickness. These specifications make it a reliable choice for a wide range of industrial applications, offering an optimal balance between strength, durability, and flexibility.
To Explore the EP 400 3 Conveyor Belt: Sizes and Dimensions
The EP 400/3 conveyor belt is renowned for its versatility and adaptability to various industrial applications. Its design allows for multiple sizes and customization options to meet specific operational requirements. Understanding the available sizes, customization possibilities, and the importance of selecting the right dimensions is crucial for optimizing efficiency and extending the belt’s lifespan. This section delves into these aspects, providing a comprehensive overview to help you make informed decisions.
Common Sizes Available in the Market
The EP 400/3 conveyor belt is available in a variety of sizes to accommodate different industrial applications. Below are seven common sizes that are frequently used:
- 500mm Width: Suitable for smaller operations or where space is limited.
- 800mm Width: Ideal for medium-sized operations requiring moderate load capacities.
- 1000mm Width: Commonly used in larger industrial settings with higher load demands.
- 1200mm Width: Suitable for heavy-duty operations with significant material handling needs.
- 1400mm Width: Often used in mining and heavy manufacturing industries.
- 1600mm Width: Appropriate for operations requiring wide belts for large volumes of materials.
- 2000mm Width: Typically used in specialized applications where very wide belts are necessary.
Customization Options for Specific Industrial Needs
The EP 400/3 conveyor belt can be customized to meet specific requirements of various industries. Here are seven key customization options:
- Length Adjustments: Belts can be manufactured to specific lengths to fit particular conveyor systems.
- Thickness Variations: Customizable cover thickness from 1mm to 25mm to suit different abrasion and impact resistance needs.
- Edge Profiles: Options for cut or molded edges to improve longevity and performance.
- Temperature Resistance: Special materials can be used to enhance the belt’s resistance to extreme temperatures.
- Chemical Resistance: Custom coatings can be applied for enhanced resistance to chemicals.
- Surface Patterns: Different surface patterns, such as rough top or diamond, can be chosen to improve material handling.
- Color Options: Belts can be manufactured in various colors for easy identification and differentiation in multi-belt systems.
Importance of Choosing the Right Size for Efficiency and Longevity
Selecting the correct size of the EP 400/3 conveyor belt is crucial for ensuring operational efficiency and extending the belt’s lifespan. Here are eight important considerations:
- Load Capacity: Ensuring the belt width and thickness can handle the maximum load to prevent excessive wear.
- Conveyor System Compatibility: Matching the belt size with the conveyor system to avoid misalignment and operational issues.
- Material Type: Choosing a belt width that accommodates the type and volume of material being transported.
- Operational Environment: Considering environmental factors, such as temperature and humidity, that may affect belt performance.
- Speed Requirements: Ensuring the belt size supports the required conveyor speed without causing slippage or damage.
- Maintenance Needs: Selecting a belt size that facilitates easy maintenance and replacement to reduce downtime.
- Durability: Opting for the appropriate thickness and edge profile to enhance durability and reduce the risk of tears and punctures.
- Cost Efficiency: Balancing the initial cost with the expected lifespan and maintenance costs to ensure overall cost-effectiveness.
The EP 400/3 conveyor belt offers a wide range of sizes and customization options to meet the diverse needs of various industries. Choosing the right size and specifications is essential for maximizing efficiency, ensuring operational longevity, and achieving cost-effective material handling solutions.
EP 400 3 Conveyor Belt Specifications and Standards
The EP 400/3 conveyor belt is designed to meet stringent international standards, ensuring high quality, safety, and performance across various industrial applications. Compliance with these standards is crucial for maintaining reliability and operational efficiency.
Adherence to International Standards
The EP 400/3 conveyor belt adheres to several key international standards, which are essential for ensuring its quality and performance:
- DIN (Germany): The Deutsche Institut für Normung (DIN) standards are widely recognized for their rigorous requirements, ensuring the belt’s durability and performance in demanding environments.
- RMA and ARPM (USA): The Rubber Manufacturers Association (RMA) and the Association for Rubber Products Manufacturers (ARPM) set standards for the physical properties and performance of conveyor belts in the United States.
- ISO: The International Organization for Standardization (ISO) provides globally recognized standards that ensure the belt’s quality and interoperability across different regions.
- AS (Australia): The Australian Standards (AS) ensure that the conveyor belts meet the specific requirements of the Australian market, focusing on safety and durability.
- SANS (South Africa): The South African National Standards (SANS) provide guidelines for conveyor belts, ensuring they can withstand the unique conditions found in South Africa’s industrial sectors.
- BS (UK): The British Standards (BS) are renowned for their rigorous testing and quality assurance processes, ensuring the conveyor belts perform reliably in various applications.
- IS (India): The Indian Standards (IS) ensure that the conveyor belts meet the specific needs of the Indian market, focusing on local conditions and requirements.
- JIS (Japan): The Japanese Industrial Standards (JIS) provide guidelines for manufacturing and testing conveyor belts to ensure high performance and quality.
Explanation of Key Specification Standards in the Industry
Understanding the key specification standards in the industry is essential for appreciating the quality and performance of the EP 400/3 conveyor belt:
- Tensile Strength: This standard measures the maximum stress the conveyor belt can withstand without breaking. For the EP 400/3 conveyor belt, the tensile strength is 400 N/mm.
- Elongation at Break: This indicates the extent to which the belt can be stretched before it breaks, ensuring it can handle operational stresses without failure.
- Abrasion Resistance: This standard measures the belt’s ability to resist wear and tear from constant friction, ensuring a longer lifespan.
- Heat Resistance: Ensures that the belt can operate effectively at high temperatures without degrading.
- Fire Resistance: This specification is crucial for belts used in environments where fire hazards are present, ensuring safety and compliance with regulations.
- Oil and Chemical Resistance: Ensures that the belt can withstand exposure to oils and chemicals, maintaining its integrity and performance in harsh environments.
Importance of Compliance for Safety and Performance
Compliance with international standards is vital for several reasons:
- Safety: Adhering to standards ensures that the EP 400/3 conveyor belt operates safely, reducing the risk of accidents and injuries in the workplace.
- Performance: Standards guarantee that the conveyor belt performs reliably under various conditions, maintaining efficiency and productivity.
- Durability: Compliance with abrasion, heat, and chemical resistance standards ensures the belt’s longevity, reducing maintenance costs and downtime.
- Quality Assurance: Meeting international standards provides assurance of the belt’s quality, giving customers confidence in their purchase.
- Regulatory Compliance: Many industries are subject to regulations that require adherence to specific standards, making compliance necessary for legal operation.
- Global Compatibility: Adhering to ISO and other international standards ensures that the conveyor belt can be used globally, facilitating international trade and operations.
- Environmental Protection: Some standards include requirements for environmentally friendly materials and processes, ensuring that the conveyor belt is sustainable.
The EP 400/3 conveyor belt’s adherence to various international standards ensures its high quality, safety, and performance. Understanding and complying with these standards is essential for optimizing the belt’s efficiency and longevity in industrial applications.
EP 400 3 Conveyor Belt Safety Factors
Safety is a critical consideration in the design and operation of conveyor belts, ensuring that they can handle the stresses and demands of various industrial applications without failure. The EP 400/3 conveyor belt is engineered with robust safety factors to guarantee operational reliability and longevity. This section delves into the concept of safety factors, their recommended values for different applications, and how the high initial modulus of EP belts allows for lower safety factors without compromising safety or performance.
Definition of Safety Factor in the Context of Conveyor Belts
In the context of conveyor belts, the safety factor is a crucial parameter that ensures the belt operates well within its maximum capacity, providing a buffer against unexpected stresses and enhancing durability. Understanding the safety factor helps in designing and selecting the appropriate belt for specific applications.
- Load Bearing Capacity: The safety factor represents the ratio between the maximum load the conveyor belt can withstand and the actual operational load. This ensures that the belt operates safely below its breaking point, providing a margin for unexpected load increases.
- Durability Assurance: By incorporating a safety factor, the conveyor belt is designed to endure additional stresses that may occur during operation, thus enhancing its overall durability and lifespan.
- Operational Security: The safety factor ensures that the belt will not fail under normal working conditions, providing a buffer against overloads and operational anomalies.
- Design Considerations: Engineers use safety factors to account for uncertainties in load estimations and to design belts that can withstand higher-than-expected loads without failure.
- Longevity: A higher safety factor contributes to the extended life of the belt by minimizing the risk of fatigue and wear, ensuring consistent performance over time.
- Maintenance Reduction: By ensuring the belt operates within safe limits, the safety factor reduces the need for frequent maintenance and repairs, leading to lower operational costs.
- Compliance with Standards: Adhering to recommended safety factors is often a requirement of industry standards and regulations, ensuring that the belt meets quality and safety benchmarks.
- Risk Management: The safety factor helps in mitigating the risk of accidents and operational downtime, ensuring continuous and safe operations in industrial environments.
Recommended Safety Factors for Different Applications
Different industrial applications have varying demands and stress levels, requiring specific safety factors to ensure optimal performance and safety. The following points outline the recommended safety factors for various applications, tailored to their unique requirements.
- General Manufacturing: A safety factor of 6:1 is recommended for general manufacturing environments, balancing load capacity and operational demands.
- Mining Operations: Given the heavy and abrasive nature of materials in mining, a higher safety factor of 7:1 is advisable to ensure durability and reliability.
- Agricultural Applications: For agricultural use, a safety factor of 5:1 is suitable, considering the moderate load and environmental conditions typically encountered.
- Food Processing: A safety factor of 6:1 ensures hygienic and safe handling of food products, accommodating the specific needs of the food processing industry.
- Chemical Industry: Due to potential exposure to corrosive materials, a safety factor of 8:1 is recommended for chemical industry applications, ensuring the belt’s longevity and resistance.
- Heavy Industrial Use: For extremely heavy loads and continuous use, a safety factor of 8:1 provides the necessary durability and operational security.
- Warehousing and Logistics: A safety factor of 5:1 is typically sufficient for the varied loads and conditions in warehousing and logistics, ensuring efficient material handling.
- Construction: Handling construction materials requires a safety factor of 7:1, accommodating the weight and rough handling associated with this industry.
- Textile Industry: A safety factor of 6:1 ensures that the belt can manage the continuous and varied loads typical in textile manufacturing, maintaining consistent performance.
How the High Initial Modulus of EP Belts Allows for a Lower Safety Factor
EP (Polyester/Nylon) belts, including the EP 400 3 conveyor belt, have a high initial modulus, meaning they are less likely to stretch under load. This characteristic allows for a lower safety factor while maintaining safety and performance standards.
- High Initial Modulus: EP belts possess a high initial modulus, indicating a higher resistance to elongation under load. This reduces the need for frequent adjustments and ensures consistent tension during operation.
- Reduced Elongation: The lower elongation characteristic of EP belts minimizes the risk of excessive stretching, maintaining the belt’s integrity and performance under varying loads.
- Enhanced Load Bearing: The high initial modulus allows the belt to bear higher loads with less deformation, providing greater reliability in demanding applications.
- Operational Efficiency: By maintaining consistent tension and reducing the need for frequent adjustments, EP belts contribute to higher operational efficiency and reduced downtime.
- Consistent Performance: The inherent stability of EP belts ensures consistent performance even under varying load conditions, enhancing overall operational reliability.
- Material Stability: The combination of polyester and nylon in EP belts offers superior stability and durability, supporting a lower safety factor without compromising safety.
- Cost-Effectiveness: A lower safety factor translates to less material usage, reducing costs while maintaining high safety and performance standards.
- Improved Safety Margins: Despite the lower safety factor, the high initial modulus of EP belts ensures a high safety margin, balancing performance and safety effectively.
Understanding the safety factors and their application to the EP 400/3 conveyor belt is crucial for ensuring reliable and safe operations across various industrial applications. The high initial modulus of EP belts provides significant advantages, allowing for lower safety factors while maintaining high standards of safety and performance.
Pricing of EP 400 3 Conveyor Belt
Understanding the pricing structure of the EP 400/3 conveyor belt is crucial for making informed purchasing decisions. Various factors influence the cost, and a thorough cost-benefit analysis compared to other conveyor belt types can highlight the advantages of choosing the EP 400/3 model. Several factors determine the pricing of EP 400/3 conveyor belts, ranging from raw material costs to customization requirements. Here are the key factors:
- Material Costs: The primary materials, polyester and nylon, significantly affect the cost due to their quality and market prices. The type and quality of rubber used for the cover also play a crucial role in pricing.
- Manufacturing Process: Advanced manufacturing techniques and machinery can raise production costs, reflecting in the final price. The cost of skilled labor involved in the production process and the amount of energy consumed during manufacturing also influence the cost.
- Customization and Specifications: Customizing the belt size to fit specific conveyor systems can lead to higher costs. Special coatings for enhanced chemical or heat resistance, specific edge profiles, surface patterns, and color options can all raise the overall cost.
Average Price Range in the Market
The average price range for the EP 400/3 conveyor belt in the market varies based on the factors mentioned above. Generally, these belts can range from $20 to $50 per meter, depending on the specific requirements and customizations. Bulk orders and long-term contracts may offer discounts, reducing the cost per meter. A detailed cost-benefit analysis can help in understanding the value proposition of the EP 400/3 conveyor belt compared to other types.
- Initial Cost vs. Longevity: While the initial cost of the EP 400/3 conveyor belt may be higher than some alternatives, its longer lifespan often makes it more cost-effective in the long run.
- Maintenance Requirements: The high-quality materials and construction of the EP 400/3 conveyor belt reduce the need for frequent maintenance, leading to lower overall maintenance costs.
- Operational Efficiency: Enhanced performance and reduced downtime with the EP 400/3 conveyor belt can increase operational efficiency, contributing to higher productivity.
- Durability: The EP 400/3 conveyor belt’s superior durability means fewer replacements and less operational disruption.
- Energy Consumption: Efficient design and materials reduce the energy consumption required to operate the conveyor system, leading to lower energy costs.
- Versatility: The ability to customize the EP 400/3 conveyor belt for specific needs enhances its versatility, making it suitable for various applications and reducing the need for multiple belt types.
- Compliance with Standards: Adherence to international standards ensures reliability and safety, potentially reducing liability and regulatory compliance costs.
- Resale Value: The robust construction and durability of the EP 400/3 conveyor belt can maintain a higher resale value compared to other belt types.
While the EP 400/3 conveyor belt may have a higher initial cost, its numerous benefits in terms of durability, efficiency, and reduced maintenance make it a cost-effective choice in the long run. Understanding the factors influencing its price and conducting a thorough cost-benefit analysis can help in making an informed decision, ensuring that the investment in the EP 400/3 conveyor belt delivers optimal value.
Applications of EP 400 3 Conveyor Belt
The EP 400/3 conveyor belt is renowned for its versatility and durability, making it a preferred choice across various industries. Its robust construction and adaptability ensure efficient performance in demanding environments, providing numerous benefits tailored to specific applications.
Industries Where EP 400/3 Belts Are Commonly Used
The EP 400 3 conveyor belt’s versatility and durability make it a valuable asset in multiple industries. Each industry benefits from the belt’s unique properties, ensuring efficient and reliable operations.
Mining
The mining industry relies heavily on the EP 400 3 conveyor belt for its superior strength and durability. These belts are ideal for transporting heavy and abrasive materials, such as ores and minerals, over long distances. Their resistance to wear and tear ensures they can withstand the harsh conditions typical of mining environments.
Agriculture
In agriculture, the EP 400/3 conveyor belt is used for handling various materials, including grains, seeds, and fertilizers. The belt’s flexibility and ability to operate under different environmental conditions make it suitable for both indoor and outdoor applications. Its durability helps in reducing downtime and maintenance costs, crucial for continuous agricultural operations.
Construction
The construction industry benefits from the EP 400/3 conveyor belt’s ability to transport construction materials like sand, gravel, and cement. Its high tensile strength and resistance to impact and abrasion ensure it can handle heavy loads and rough materials without compromising performance.
Material Handling
In material handling, the EP 400/3 conveyor belt is essential for moving goods within warehouses, distribution centers, and manufacturing facilities. Its versatility allows it to handle a wide range of materials, from packaged goods to bulk items, ensuring efficient and reliable operations.
Benefits in Specific Applications
The EP 400/3 conveyor belt offers numerous benefits in specific applications, enhancing operational efficiency and reliability. These benefits are crucial for industries that rely on effective material transport.
Bulk Material Transport
- High Load-Bearing Capacity: Ensures efficient transportation of large quantities of bulk materials.
- Durability: Withstands heavy loads without compromising performance.
- Long-Distance Transport: Ideal for moving materials over extensive distances with minimal wear and tear.
Resistance to Harsh Conditions
- Temperature Resistance: Performs reliably in extreme temperatures, both hot and cold.
- Moisture Resistance: Maintains functionality in wet and humid environments.
- Abrasive Resistance: Resists damage from abrasive materials, prolonging belt life.
- Chemical Resistance: Suitable for environments with exposure to various chemicals, ensuring durability and safety.
Versatility in Handling Various Materials
- Fine Powders: Efficiently handles fine materials without leakage or spillage.
- Large Lumps: Capable of transporting large and heavy materials without damage.
- Consistency: Maintains performance across different material types and operational conditions.
- Flexibility: Adapts to various conveyor system configurations and material handling requirements.
- Operational Adaptability: Suitable for different operational needs, from light to heavy-duty applications.
- Efficiency: Ensures smooth and efficient material flow, enhancing overall productivity.
- Customization: Can be tailored to specific requirements, such as special coatings or sizes.
- Environmental Compatibility: Performs well in diverse environmental conditions, ensuring reliable operation across various settings.
The EP 400/3 conveyor belt is a versatile and reliable solution for various industrial applications. Its use in industries such as mining, agriculture, construction, and material handling highlights its adaptability and durability. The belt’s benefits in bulk material transport, resistance to harsh conditions, and versatility in handling different materials make it an indispensable component in ensuring efficient and continuous operations across these sectors.
Additional Resources for EP 400 3 Conveyor Belt
Understanding the importance of reliable suppliers and proper maintenance is crucial for getting the most out of your EP 400/3 conveyor belt. This section provides recommendations for manufacturers and suppliers, along with essential guidelines for maintaining and extending the life of your conveyor belt.
Recommended Manufacturers and Suppliers
When sourcing the EP 400 3 conveyor belt, it’s important to choose reputable manufacturers and suppliers to ensure quality and reliability. Here are seven recommended companies:
- ContiTech AG: A leading global manufacturer offering a range of high-quality conveyor belts, including the EP 400/3 model.
- Fenner Dunlop: Known for their durable and high-performance conveyor belts, Fenner Dunlop provides excellent customer support and technical assistance.
- Bridgestone Corporation: Offers a variety of conveyor belts with a reputation for quality and innovation, suitable for various industrial applications.
- Yokohama Rubber Co., Ltd.: Provides robust and reliable conveyor belts, including the EP 400/3, with a focus on advanced materials and technology.
- Goodyear Engineered Products: Supplies a wide range of conveyor belts known for their durability and performance, ideal for heavy-duty applications.
- SAVA: Specializes in industrial rubber products, including high-quality EP conveyor belts, offering custom solutions to meet specific needs.
- Dunlop Conveyor Belting: Renowned for their extensive range of high-quality conveyor belts and excellent after-sales support.
Guidelines for Maintenance and Care to Extend Belt Life
Proper maintenance and care are essential for extending the life of your EP 400 3 conveyor belt. Here are eight key guidelines:
- Regular Inspections: Conduct regular inspections to check for signs of wear, damage, or misalignment. Early detection of issues can prevent major breakdowns.
- Proper Cleaning: Keep the conveyor belt clean from debris and spillage. Accumulated materials can cause unnecessary wear and reduce the belt’s efficiency.
- Tension Adjustment: Ensure that the belt tension is correctly adjusted. Over-tensioning can cause excessive wear, while under-tensioning can lead to slippage and misalignment.
- Lubrication: Regularly lubricate the moving parts of the conveyor system to reduce friction and wear. Use appropriate lubricants recommended by the manufacturer.
- Belt Alignment: Check and maintain proper belt alignment to prevent edge wear and ensure smooth operation. Misalignment can cause uneven wear and reduce belt life.
- Load Management: Avoid overloading the conveyor belt. Excessive loads can cause stretching and damage, reducing the belt’s operational life.
- Storage Conditions: Store the conveyor belt in a cool, dry place away from direct sunlight and chemicals. Proper storage prevents premature aging and deterioration.
- Professional Maintenance: Schedule regular maintenance by qualified professionals who can perform detailed checks and repairs. Professional servicing ensures that the belt operates at peak efficiency.
Selecting reputable manufacturers and adhering to proper maintenance guidelines are key to maximizing the performance and lifespan of your EP 400 3 conveyor belt. Regular inspections, proper cleaning, tension adjustment, lubrication, alignment, load management, appropriate storage, and professional maintenance collectively ensure that the belt remains efficient and durable over its operational life.
FAQs about EP 400 3 Conveyor Belt
EP (Polyester/Nylon) belts and NN (Nylon/Nylon) belts are two types of fabric conveyor belts used in various industrial applications. The primary difference lies in the materials used for their construction. EP belts use polyester fibers in the warp (longitudinal) direction and nylon fibers in the weft (transverse) direction. This combination provides EP belts with excellent dimensional stability, low elongation, and high tensile strength. EP belts are also resistant to moisture and mildew, making them suitable for environments with varying humidity levels.
In contrast, NN belts use nylon fibers in both the warp and weft directions. Nylon’s elasticity provides NN belts with higher flexibility and impact resistance, but they can experience greater elongation under load compared to EP belts. NN belts are preferred in applications where high impact resistance and flexibility are critical, such as mining and heavy-duty material handling.
Overall, the choice between EP and NN belts depends on the specific requirements of the application, with EP belts being favored for their stability and low elongation, while NN belts are chosen for their flexibility and impact resistance.
EP in conveyor belts stands for Polyester (E) in the warp direction and Nylon (P) in the weft direction. This combination of materials results in a fabric carcass that offers a balance of strength, durability, and flexibility. EP belts are known for their excellent dimensional stability and low elongation properties, making them suitable for high-tension applications and long-distance conveying.
The use of polyester fibers in the warp direction provides the belt with high tensile strength and resistance to stretching, which helps maintain consistent performance over time. Nylon fibers in the weft direction contribute to the belt’s flexibility and resistance to impact and abrasion, ensuring durability in demanding environments.
EP conveyor belts are widely used in various industries, including mining, agriculture, construction, and material handling. Their ability to withstand harsh conditions, combined with their robust construction, makes them a reliable choice for transporting a wide range of materials efficiently and safely.
The elongation of an EP belt refers to the amount of stretch the belt undergoes when subjected to a load. EP belts are designed to have low elongation, typically around 1-2% at the maximum working tension. This low elongation is a key advantage of EP belts, as it ensures minimal stretching and consistent performance during operation.
Low elongation is particularly important in applications requiring precise material handling and long conveyor lengths. It helps maintain belt tension, reduces the need for frequent adjustments, and minimizes the risk of slippage and misalignment. The polyester fibers in the warp direction of EP belts contribute to this low elongation characteristic, providing high tensile strength and stability.
In contrast, belts with higher elongation may require more frequent tensioning and can experience greater wear and tear over time. The low elongation of EP belts, combined with their durability and resistance to environmental factors, makes them an ideal choice for various industrial applications.
Grade 1 and grade 2 conveyor belts refer to the quality and durability of the belt materials, specifically their resistance to abrasion. Grade 1 conveyor belts offer higher resistance to abrasion and are designed for applications where the belt is subjected to harsh and abrasive materials. These belts are ideal for heavy-duty operations such as mining, where sharp and coarse materials are frequently conveyed. The higher abrasion resistance of grade 1 belts ensures a longer lifespan and reduced maintenance costs, making them suitable for demanding environments.
Grade 2 conveyor belts, on the other hand, provide moderate abrasion resistance and are used in less demanding applications. They are suitable for transporting softer materials and are often used in industries like agriculture, food processing, and general material handling. While grade 2 belts may not offer the same level of durability as grade 1 belts, they are still effective and economical for applications where the belt is not exposed to extreme abrasion.
In summary, the primary difference between grade 1 and grade 2 conveyor belts lies in their abrasion resistance. Grade 1 belts are designed for high abrasion environments, offering superior durability, while grade 2 belts are suitable for moderate abrasion applications, providing a cost-effective solution for less demanding uses.
Last Updated on August 9, 2024 by Jordan Smith
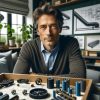
Jordan Smith, a seasoned professional with over 20 years of experience in the conveyor system industry. Jordan’s expertise lies in providing comprehensive solutions for conveyor rollers, belts, and accessories, catering to a wide range of industrial needs. From initial design and configuration to installation and meticulous troubleshooting, Jordan is adept at handling all aspects of conveyor system management. Whether you’re looking to upgrade your production line with efficient conveyor belts, require custom conveyor rollers for specific operations, or need expert advice on selecting the right conveyor accessories for your facility, Jordan is your reliable consultant. For any inquiries or assistance with conveyor system optimization, Jordan is available to share his wealth of knowledge and experience. Feel free to reach out at any time for professional guidance on all matters related to conveyor rollers, belts, and accessories.