Conveyor Belt Regulations: OSHA Standards
Conveyor belt regulations stand as the cornerstone of safety and efficiency in countless industrial operations. Conveyor Belt Regulations:Conveyors must have easily accessible emergency stop devices for workers to quickly stop machinery in emergencies.These regulations, meticulously set and enforced by authoritative bodies like OSHA, are not just guidelines but essential protocols that ensure the smooth and safe functioning of conveyor systems. They are designed to protect the workforce from potential hazards and to maintain the operational integrity of conveyor systems, thereby playing a pivotal role in industrial productivity and worker safety.
Conveyor Belt Regulations PDF
Navigating the Framework of Safety
In the industrial landscape, conveyor belts are the lifelines of myriad operations, moving goods and materials with efficiency and precision. However, the safety and efficacy of these systems are not incidental but are the result of stringent adherence to conveyor belt regulations. These regulations, meticulously documented in various PDF resources, serve as the bedrock of operational safety and efficiency.
These PDFs are comprehensive repositories of information, detailing every facet of conveyor belt regulations. They encompass a wide array of topics, including but not limited to, the design and installation of conveyor systems, the proper maintenance and inspection routines, and the necessary safety measures to protect workers from potential hazards. They also delve into the specifics of different types of conveyor belts, each with its unique properties and compliance requirements.
For industry professionals, these documents are invaluable. They provide a clear and detailed understanding of legal requirements, ensuring that operations are not just efficient but also in strict adherence to safety protocols. They serve as a guide for best practices in conveyor belt operations, offering insights into the latest technologies and methodologies that can enhance the longevity and functionality of conveyor systems.
Moreover, these PDFs are not static; they are regularly updated to reflect the latest in industry standards and technological advancements. This ensures that businesses are not just meeting the current benchmarks but are also prepared for future developments in conveyor belt technology.
In essence, conveyor belt regulations PDFs are more than just documents; they are a dynamic and essential resource for maintaining the highest standards of safety, efficiency, and compliance in conveyor belt operations.

OSHA Conveyor Safety 1910: What are Conveyor Belt Regulations
OSHA Conveyor Safety 1910: Upholding the Highest Standards of Safety
The Occupational Safety and Health Administration (OSHA) is a beacon of safety in the industrial world, and its standards under the 1910 regulation are specifically tailored to ensure the safety and efficiency of conveyor belt operations. Conveyor belt regulations are not mere guidelines but are stringent requirements that safeguard the workforce and ensure the seamless operation of conveyor systems.
Understanding these standards is crucial for any business that operates conveyor belts. They cover a broad spectrum of requirements, from the structural integrity of the conveyor system to the training and protective measures that must be in place for workers. For instance, the standards stipulate the proper installation and maintenance routines for conveyor systems, ensuring that they are not just functional but also safe for every worker involved in the operation.
Moreover, these standards delve into the specifics of emergency stop mechanisms, guardrails, and warning signs, among other safety features. They outline the necessary steps to mitigate risks and prevent accidents, creating a safe working environment for everyone. They also emphasize the importance of regular conveyor belt inspections and audits, ensuring that conveyor systems are not just compliant at a single point in time but maintain the highest safety standards consistently.
Compliance with these standards is not just about meeting legal requirements; it’s about fostering a culture of safety and responsibility. It’s about ensuring that every worker returns home safely at the end of the day and that the operations run smoothly and efficiently without any untoward incidents.
The OSHA Conveyor Safety 1910 standards are the cornerstone of safety in conveyor belt operations. Understanding and adhering to these standards is paramount for any business that seeks to not just thrive but also ensure the safety and well-being of its workforce. They are not just regulations; they are the principles that underpin the very essence of a safe, efficient, and responsible industrial operation.
OSHA’s Role in Conveyor Safety
OSHA (Occupational Safety and Health Administration) plays a crucial role in ensuring conveyor safety in workplaces across the United States. OSHA’s regulations and guidelines are designed to protect workers from the various hazards associated with conveyor systems. Here are the key aspects of OSHA’s role in conveyor safety:
1. Regulations and Standards
OSHA has established several standards that apply to conveyor systems, primarily under the General Industry Standards (29 CFR 1910). Key sections include:
- 29 CFR 1910.212 – General requirements for all machines, including conveyor safety.
- 29 CFR 1910.219 – Mechanical power-transmission apparatus, which includes specific requirements for guarding conveyor belts and their components.
2. Hazard Identification and Assessment
OSHA mandates that employers conduct a thorough hazard assessment of their conveyor systems. This involves identifying potential risks such as:
- Pinch points
- Nip points
- Shear points
- Entanglement areas
- Falling materials
3. Machine Guarding
Proper guarding is essential to prevent workers from coming into contact with moving parts. OSHA requires:
- Fixed Guards – To protect against nip points and rotating parts.
- Interlocked Guards – That shut down the machine if the guard is removed.
- Adjustable Guards – That can be customized to fit specific machinery configurations.
4. Lockout/Tagout Procedures
OSHA’s Lockout/Tagout standard (29 CFR 1910.147) ensures that machinery, including conveyors, is properly shut off and not started up again before maintenance or servicing is completed. This prevents accidental startup, which could lead to injury.
5. Training and Education
Employers must provide training to all workers who operate or work near conveyors. Training should cover:
- Recognizing hazards
- Proper use of safety devices and guards
- Emergency procedures
- Lockout/Tagout practices
6. Inspections and Maintenance
Regular inspections and maintenance are critical for conveyor safety. OSHA requires:
- Frequent inspections of conveyor components.
- Immediate repairs of identified issues.
- Keeping maintenance records.
7. Emergency Stop Devices
OSHA requires that conveyors be equipped with readily accessible emergency stop devices to allow workers to quickly stop the machinery in case of an emergency.
8. Housekeeping
Good housekeeping practices are essential to maintain conveyor safety. OSHA guidelines emphasize:
- Keeping conveyor areas free of debris.
- Ensuring proper lighting around conveyors.
- Marking and maintaining clear walkways and workspaces.
OSHA’s comprehensive approach to conveyor safety ensures that employers implement necessary safeguards to protect workers. Compliance with OSHA standards not only helps in avoiding penalties but, more importantly, ensures a safer working environment. Regular training, maintenance, and adherence to established guidelines are key components of effective conveyor safety management.
For more detailed information, employers and safety officers should refer to OSHA’s official publications and resources on conveyor safety.

OSHA’s Requirements for Conveyor Belt Regulations
OSHA’s regulations for conveyor belts focus on ensuring safety in the workplace by addressing potential hazards and establishing clear guidelines for the use and maintenance of these systems. Here are the general requirements outlined by OSHA:
1. Guarding of Moving Parts (29 CFR 1910.212)
This regulation mandates that any moving parts of the conveyor system that could pose a hazard must be adequately guarded. This includes:
- Belts and Pulleys: Guarding of belts, pulleys, gears, and other moving parts to prevent contact.
- Nip Points: Guarding nip points where belts come into contact with pulleys or other machinery.
- Shafts and Couplings: Guarding exposed shafts and couplings.
2. Conveyor Belt Safety Devices
Conveyors must be equipped with safety devices to protect workers, including:
- Emergency Stop Devices: Accessible emergency stop buttons or pull cords along the conveyor.
- Warning Devices: Audible or visual warning devices to alert workers of the conveyor’s operation.
3. Lockout/Tagout Procedures (29 CFR 1910.147)
Before maintenance or servicing, conveyors must be properly shut down and locked out to prevent accidental startup. This includes:
- Energy Isolation: Disconnecting and isolating all energy sources.
- Lockout Devices: Applying lockout devices to energy-isolating devices.
- Tagout Devices: Using tags to indicate that the machinery should not be operated.
4. Training and Education
Employers are responsible for ensuring that workers are properly trained in conveyor safety, including:
- Hazard Recognition: Identifying and understanding conveyor hazards.
- Safe Operating Procedures: Proper operation and maintenance of conveyor systems.
- Emergency Procedures: Actions to take in case of an emergency.
5. Inspections and Maintenance
Regular inspections and maintenance are essential to ensure conveyor safety. OSHA requires:
- Routine Inspections: Frequent inspections to identify potential hazards or wear.
- Maintenance Records: Keeping detailed records of inspections, maintenance, and repairs.
- Timely Repairs: Promptly addressing any issues found during inspections.
6. Housekeeping and Environmental Controls
Good housekeeping practices help prevent accidents and injuries. OSHA guidelines include:
- Clear Walkways: Keeping conveyor areas free of obstructions and debris.
- Proper Lighting: Ensuring adequate lighting around conveyors.
- Spill Management: Addressing spills and leaks immediately to prevent slip hazards.
7. Load Capacity
Conveyors must be designed and operated within their load capacity to prevent mechanical failures and ensure safety. This involves:
- Load Limits: Clearly marking and adhering to the conveyor’s load capacity.
- Even Loading: Distributing loads evenly to prevent overloading.
8. Emergency Planning
Employers must have emergency plans in place for potential conveyor-related incidents, including:
- Emergency Stops: Clearly marked and easily accessible emergency stop controls.
- First Aid: Availability of first aid supplies and trained personnel.
- Evacuation Procedures: Clear evacuation procedures in case of fire or other emergencies.
Compliance with OSHA’s conveyor belt regulations is critical to maintaining a safe workplace. These general requirements ensure that hazards are minimized, workers are trained and equipped to handle emergencies, and conveyor systems are maintained in a safe operating condition. Regular training, maintenance, and adherence to these guidelines are essential components of a comprehensive safety program. For specific details and updates, employers should refer to OSHA’s official resources and publications.

Conveyor Belt Regulations General Requirements
Conveyor belt systems are commonly used in various industries to transport materials efficiently. Regulations and standards are in place to ensure the safety and efficiency of these systems. Here are some general requirements and regulations for conveyor belts:
Safety Standards
- Guarding: All moving parts, such as pulleys, belts, and gears, must be adequately guarded to prevent accidental contact.
- Emergency Stop Devices: Conveyor systems must have emergency stop devices that are easily accessible and capable of stopping the conveyor immediately.
- Start-Up Alarms: Audible and visual alarms should warn personnel before the conveyor starts.
- Regular Inspections and Maintenance: Regular inspections and maintenance are required to ensure that the conveyor is in safe operating condition.
- Training: Personnel must be trained in the safe operation and maintenance of conveyor systems.
Design and Construction
- Load Capacity: Conveyors must be designed to handle the maximum load they will be subjected to.
- Belt Strength and Durability: Belts must be strong and durable enough to handle the material they will transport without excessive wear or failure.
- Safety Labels: Conveyors should have safety labels indicating potential hazards and proper operation procedures.
Fire Safety
- Fire-Resistant Belts: In certain industries, conveyor belts must be made from fire-resistant materials to prevent the spread of fire.
- Fire Suppression Systems: Conveyor systems may need to be equipped with fire suppression systems, especially in environments with a high risk of fire.
Electrical Safety
- Proper Wiring and Grounding: All electrical components of the conveyor system must be properly wired and grounded.
- Overload Protection: Electrical systems should have overload protection to prevent damage and fire hazards.
Ergonomics and Accessibility
- Height and Reach: Conveyor systems should be designed to minimize the need for workers to bend, reach, or stretch excessively.
- Walkways and Platforms: Safe walkways and platforms should be provided for maintenance and inspection activities.
Regulatory Bodies and Standards
- OSHA (Occupational Safety and Health Administration): In the United States, OSHA provides guidelines and standards for conveyor safety.
- CEMA (Conveyor Equipment Manufacturers Association): CEMA provides standards for the design, manufacturing, and safety of conveyor equipment.
- ISO (International Organization for Standardization): ISO 9001 and other related standards may apply to the quality management of conveyor systems.
Environmental Considerations
- Dust and Noise Control: Measures should be taken to control dust and noise generated by conveyor systems.
- Energy Efficiency: Conveyor systems should be designed to operate efficiently, minimizing energy consumption.
Industry-Specific Requirements
Different industries may have specific requirements for conveyor systems based on the materials being transported and the operating environment. For example:
- Mining: Conveyor belts used in mining must be flame-resistant and antistatic.
- Food Industry: Conveyors in the food industry must be made of materials that are safe for food contact and easy to clean.
Documentation and Record-Keeping
- Operation Manuals: Detailed operation manuals must be provided for conveyor systems.
- Maintenance Logs: Accurate maintenance logs should be kept to document all inspections, repairs, and modifications.
These general requirements help ensure the safe and efficient operation of conveyor belt systems in various industrial settings. Specific regulations may vary by country and industry, so it’s essential to consult relevant local standards and guidelines.
Conveyor Belt Regulations: Emergency Stop Requirements
Overview of OSHA’s Conveyor Emergency Stop Requirements
The Occupational Safety and Health Administration (OSHA) mandates stringent emergency stop requirements for conveyor systems to ensure worker safety. These conveyor belt regulations are designed to provide an immediate response mechanism in the event of a hazardous situation. The presence of easily accessible and functional emergency controls is crucial in preventing accidents and mitigating risks associated with conveyor operation.
Importance of Emergency Controls
- Rapid Response: Emergency stops allow for the quick cessation of conveyor operations, crucial in preventing accidents and injuries.
- Accessibility: Emergency controls must be conveniently located so that they can be activated swiftly in case of an emergency.
Implementation of Emergency Stop Systems
- Strategic Placement: Emergency stops should be placed at regular intervals along the conveyor and at key points where operators are stationed.
- Visibility: Controls must be clearly marked and visible to all operators.
- Design Considerations: The design of emergency stops should ensure that they can be activated quickly and easily, without causing additional hazards.
Regular Maintenance Checks
- Inspections: Regular inspections are necessary to ensure that emergency stops are in working order.
- Testing: Frequent testing of the emergency stop mechanism is crucial to ensure functionality.
- Training: Operators should be trained on the location and use of emergency stops, as well as the appropriate response to conveyor emergencies.
Compliance and Best Practices
- Documentation: Maintain records of inspections and tests for compliance purposes.
- Continuous Improvement: Regularly review and update emergency response procedures based on operational changes or incidents.
Get the perfect conveyor belts for your needs. Contact us now!
Conveyor Belt Regulations in California: State-Specific Standards
California’s Unique Conveyor Belt Regulations
California often implements additional or unique regulations for conveyor belt safety, supplementing federal OSHA standards. Safety devices in conveyor belt systems are a key focus of these regulations. These state-specific standards aim to address local industrial environments and worker safety concerns more comprehensively.
Navigating Federal and State Regulations
- Understanding Differences: Businesses must understand the differences between federal OSHA regulations and California-specific conveyor belt safety standards.
- Compliance Strategy: Develop a compliance strategy that adheres to both sets of regulations, prioritizing worker safety and legal requirements.
Key Areas of Focus in California
- Environmental Considerations: California regulations may include specific provisions related to environmental factors like seismic activity.
- Worker Training: Enhanced training requirements focusing on the unique aspects of conveyor operation in California’s diverse industrial landscape.
- Reporting and Documentation: Stricter reporting and documentation requirements for conveyor-related incidents and maintenance.
Resources for Compliance
- State Agencies: Consult with California’s state safety agencies for guidance on specific regulations.
- Legal Consultation: Engage with legal experts specializing in California’s industrial safety laws.
- Industry Associations: Collaborate with industry associations for best practices and compliance resources.
Conveyor Guarding Requirements: Protecting Workers
OSHA’s Conveyor Guarding Requirements
OSHA’s regulations mandate comprehensive guarding for conveyor systems to protect workers from potential hazards. These requirements focus on preventing contact with moving parts, reducing the risk of entanglement, and avoiding material spillage.
Role of Guards in Accident Prevention
- Preventing Contact: Guards prevent workers from coming into contact with moving parts of the conveyor.
- Mitigating Hazards: Well-designed guards can significantly reduce the risk of accidents and injuries.
Selecting Appropriate Conveyor Guards
- Types of Guards: Choose guards based on the type of conveyor and the specific hazards it presents.
- Material and Design: Ensure that guards are made from durable materials and designed to withstand the operational demands of the conveyor.
Installation and Maintenance
- Proper Installation: Guards should be installed securely and in a way that does not impede conveyor operation.
- Regular Inspections: Conduct regular inspections to ensure guards are intact and functioning correctly.
- Maintenance and Repairs: Promptly repair or replace damaged guards to maintain their effectiveness.
Training and Awareness
- Educating Workers: Train workers on the importance of guards and the risks associated with tampering or removing them.
- Promoting Safety Culture: Foster a safety culture where guarding regulations are respected and adhered to.
Documentation and Compliance
- Record-Keeping: Keep detailed records of guard installations, inspections, and maintenance.
- Regulatory Compliance: Regularly review and update guarding practices to remain compliant with OSHA standards and industry best practices.
Conveyor belt regulations, particularly those related to emergency stops and guarding, play a vital role in ensuring the safety of workers. Adhering to these regulations not only complies with legal requirements but also fosters a safer and more efficient working environment.

Conveyor Belt Regulations: Conveyor Safety PDF as Comprehensive Safety Protocols
Availability of Comprehensive Safety Guidelines in PDF
Conveyor belt systems, integral to numerous industries, pose various safety risks. To mitigate these risks, comprehensive safety guidelines are often available in PDF format. These documents, which often detail the various uses of belt conveyor systems, serve as a crucial resource for ensuring the safe operation and maintenance of conveyor systems.
Content of Safety Guidelines
- Operational Safety: Detailed instructions on the safe operation of conveyor systems based on conveyor belt regulations, including start-up and shut-down procedures.
- Maintenance Protocols: Guidelines on routine maintenance, emergency repairs, and replacement of worn or damaged parts.
- Hazard Identification: Information on identifying potential hazards associated with conveyor belts, such as entanglement, slips, and falls.
- Emergency Procedures: Clear instructions on handling emergencies, including conveyor malfunctions and accidents.
Importance in Training Employees
- Skill Development: These documents are essential for training new employees and refreshing the knowledge of experienced workers.
- Standardization: They help standardize safety procedures across different departments and locations.
- Compliance: Ensure that all operations are in compliance with industry standards and legal requirements.
Use in Safety Audits
- Checklist: Safety PDFs often include checklists for regular safety audits, ensuring all aspects of conveyor safety are regularly assessed and addressed.
- Record-Keeping: They assist in maintaining records of safety inspections and audits, which are crucial for regulatory compliance and internal reviews.
Maintaining a Culture of Safety
- Awareness: Regular distribution and discussion of these guidelines help maintain a high level of safety awareness among employees.
- Best Practices: Encourage the adoption of industry best practices in everyday operations.
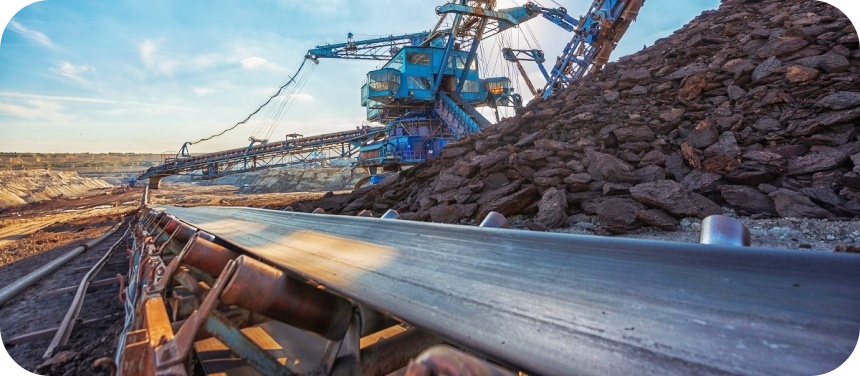
Conveyor Belt Regulations: Identifying and Mitigating Conveyor Belt Hazards
Common Conveyor Belt Hazards
- Pinch Points: Areas where two or more parts move together, with at least one moving in a rotary or circular motion, creating a pinch point.
- Entanglement: Risks associated with rotating parts where loose clothing, hair, or body parts may become entangled.
- Slip and Fall Risks: Due to spillage of materials or improper maintenance, slip and fall hazards are prevalent around conveyor belts.
Strategies for Hazard Identification Based on Conveyor Belt Regulations
- Regular Inspections: Conducting thorough inspections of conveyor systems to identify potential hazards.
- Employee Feedback: Encouraging employees to report potential hazards they observe in their daily operations.
- Risk Assessment: Performing risk assessments to evaluate the severity and likelihood of identified hazards.
Implementation of Preventive Measures
- Guarding: Installing guards at pinch points and around rotating parts to prevent entanglement.
- Housekeeping: Maintaining cleanliness around conveyor belts to prevent slip and fall accidents.
- Training: Regular training sessions for employees on hazard awareness and safe practices.
Conveyor Walkway Standards: Ensuring Safe Access
Standards for Conveyor Walkways
Conveyor walkways are essential for providing safe access to conveyor systems for maintenance, inspection, and emergency response. Adhering to specific standards and best practices in the design and maintenance of these walkways is crucial for worker safety.
Design Considerations
- Width and Clearance: Ensuring the walkway is wide enough for safe passage, with adequate headroom and clearance from moving parts.
- Non-Slip Surfaces: Using materials that provide traction to prevent slips, especially in outdoor or wet environments.
- Handrails and Guardrails: Installing handrails and guardrails where necessary to prevent falls.
Maintenance of Walkways
- Regular Inspections: Conducting regular inspections to ensure walkways are in good condition and free from obstructions.
- Prompt Repairs: Addressing any damage or wear promptly to maintain the integrity of the walkway.
- Clear Signage: Providing clear signage to indicate the purpose of the walkway and any potential hazards.
Importance in Preventing Accidents
- Safe Access: Ensuring workers have safe access to perform maintenance and inspections.
- Emergency Situations: Facilitating quick and safe evacuation or response in emergency situations.
- Compliance: Adhering to walkway standards is not only a safety measure but also a compliance requirement in many jurisdictions.
Conveyor belt regulations encompass a wide range of safety aspects, from emergency stop requirements to walkway standards. Adhering to these regulations is essential for the safe operation of conveyor systems, protecting workers from potential hazards, and ensuring compliance with legal and industry standards.
FAQs about Conveyor Belt Regulations
OSHA (Occupational Safety and Health Administration) sets specific rules for conveyor belt safety to prevent workplace injuries. Key OSHA rules include:
Guarding: Conveyor belts must have adequate guarding to prevent employee contact with moving parts. This includes nip points, rotating parts, and flying sparks or material.
Emergency Stops: Conveyors must have easily accessible emergency stop mechanisms.
Regular Inspections: Regular safety inspections and maintenance of conveyor systems are required to ensure safe operation.
Training: Employees working with or around conveyor belts must receive proper training on safe operation and emergency procedures.
Warning Signs: Appropriate warning signs should be placed near conveyor belts to alert workers of potential hazards.
The requirements for a conveyor belt typically focus on safety, efficiency, and suitability for the intended use. These include:
Material and Design: The belt material and design should be suitable for the type of goods it will carry and the environment in which it operates.
Strength and Durability: Conveyor belts must have the necessary strength and durability to handle the load and operational speed.
Safety Features: Safety features like guards, emergency stops, and warning signs are essential.
Compliance with Standards: Compliance with industry standards and regulations, such as those set by OSHA, is crucial.
Conveyor rules generally refer to the safety and operational guidelines that must be followed to ensure safe and efficient use of conveyor systems. These rules include:
Proper Guarding: Ensuring all moving parts are properly guarded to prevent accidents.
Regular Maintenance: Conducting regular maintenance to keep the conveyor in good working condition.
Safe Operation: Following safe operating procedures, including not overloading the conveyor and using emergency stops when necessary.
Training: Providing adequate training to all personnel who operate or work near the conveyor.
Yes, conveyor belts must be guarded to ensure safety. OSHA and other safety standards require that conveyor belts have proper guarding to protect workers from hazards such as getting caught in the machinery, entanglement, and other risks associated with moving parts. Guards are used to cover nip points, rotating components, and other dangerous areas of the conveyor system. The type and extent of guarding depend on the conveyor’s design and the potential hazards it presents.
Belt conveyor guarding is essential for worker safety. Guards should fully cover all moving parts, be made of durable materials, and be easily removable for maintenance. They must allow visibility for inspection, have small openings to prevent contact, and comply with industry standards like OSHA and ANSI. Warning signs should be placed on guards, and interlocks should be used to stop the conveyor if guards are removed.
Last Updated on July 29, 2024 by Jordan Smith
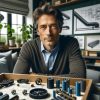
Jordan Smith, a seasoned professional with over 20 years of experience in the conveyor system industry. Jordan’s expertise lies in providing comprehensive solutions for conveyor rollers, belts, and accessories, catering to a wide range of industrial needs. From initial design and configuration to installation and meticulous troubleshooting, Jordan is adept at handling all aspects of conveyor system management. Whether you’re looking to upgrade your production line with efficient conveyor belts, require custom conveyor rollers for specific operations, or need expert advice on selecting the right conveyor accessories for your facility, Jordan is your reliable consultant. For any inquiries or assistance with conveyor system optimization, Jordan is available to share his wealth of knowledge and experience. Feel free to reach out at any time for professional guidance on all matters related to conveyor rollers, belts, and accessories.