Conveyor Belt Regulations South Africa: Industry Compliance
The importance of adhering to conveyor belt regulations South Africa cannot be overstated. These regulations are not just guidelines but are crucial mandates that ensure the safety of workers and the operational efficiency of industries. South Africa, with its extensive mining and industrial activities, has a set of specific legal frameworks and standards governing the use of conveyor belts. Understanding and complying with these regulations is paramount for businesses to maintain safety standards, minimize risks, and ensure smooth operations.
Conveyor Belt Regulations South Africa PDF: A Comprehensive Guide
Conveyor Belt Regulations South Africa PDF: Navigating the Legal Landscape
In South Africa, the conveyor belt industry is governed by a comprehensive set of regulations, ensuring that operations are safe, efficient, and compliant with the law. These regulations are meticulously detailed in various PDF guides, which serve as invaluable resources for businesses and safety professionals. These documents cover a wide spectrum of topics, including the design, installation, and maintenance of conveyor systems, safety measures for workers, and environmental considerations.
These PDF guides are more than just documents; they are a blueprint for maintaining the highest standards of safety and efficiency in conveyor belt operations. They provide clear and detailed instructions on complying with legal requirements, implementing safety protocols, and adopting best practices in conveyor belt operations. Moreover, they are regularly updated to reflect the latest in industry standards and technological advancements, ensuring that businesses are not just meeting the current benchmarks but are also prepared for future developments in conveyor belt technology.
The conveyor belt regulations PDFs are an essential tool for businesses operating in South Africa, guiding them in maintaining compliance, ensuring worker safety, and achieving operational excellence.
Conveyor Belt Regulations South Africa: Key Aspects of Safety
Conveyor Belt Safety Regulations: Upholding Standards in South Africa
Conveyor belt regulations South Africa of safety are a cornerstone of industrial operations, especially in sectors like mining, manufacturing, and logistics. These regulations encompass a broad range of safety measures, designed to protect workers from potential hazards associated with conveyor belt operations. The key aspects of these safety regulations include:
- Mandatory Safety Features: Regulations stipulate the installation of safety features such as guards, emergency stop mechanisms, and warning signs. These features are crucial in preventing accidents and ensuring quick response in case of emergencies.
- Operational Protocols: The regulations outline specific operational protocols to ensure that conveyor belts are used safely. This includes guidelines on the maximum load capacity, speed limits, and the proper handling of materials.
- Regular Inspections and Maintenance: To ensure that conveyor belts remain safe and functional, regular inspections and maintenance are mandated. This includes checking the integrity of the belt, the alignment of the rollers, and the functionality of the safety features.
- Training and Awareness: Regulations emphasize the need for comprehensive training for all personnel involved in the operation, maintenance, or repair of conveyor belts. This ensures that everyone is aware of the potential hazards and knows how to operate the belts safely.
Adhering to these safety regulations is not just about compliance; it’s about fostering a culture of safety and responsibility. It’s about ensuring that every worker is protected, and every operation runs smoothly and efficiently. In South Africa, where conveyor belts are integral to numerous industries, understanding and implementing these safety regulations is paramount for the well-being of workers and the success of businesses.
Conveyor Belt Regulations South Africa:Training and Certification
In South Africa, stringent training and certification requirements are in place for personnel operating or maintaining conveyor belt systems. These requirements aim to ensure that individuals handling these systems are well-equipped with necessary knowledge and skills to operate safely and efficiently. Here’s a detailed look at these training and certification processes:
- Mandatory Training Programs: Operators and maintenance personnel must undergo mandatory training programs that cover various aspects of conveyor belt operation and maintenance. These programs typically include instruction on the mechanics of conveyor systems, understanding conveyor components like belts, rollers, and motors, and the basics of conveyor belt installation and troubleshooting.
- Safety Training: Given the potential hazards associated with conveyor belts, including entanglement, slips, and falls, safety training is a critical component. This training encompasses proper operational practices, emergency stop procedures, the use of personal protective equipment (PPE), and guidelines for performing maintenance tasks safely.
- Certification Process: After completing the required training, personnel must often pass a certification test to demonstrate their knowledge and ability to safely operate and maintain conveyor belt systems. This certification might be required to be renewed periodically through additional training or refresher courses to ensure that all personnel are up to date with the latest safety standards and technology.
- Role-Specific Training: The training is often tailored to the specific roles of the personnel. For example, operators might receive more in-depth training on the operational aspects, while maintenance staff might focus more on repair and troubleshooting skills.
- Accredited Training Providers: Training must be delivered by accredited providers who are recognized by relevant South African authorities, such as the Mining Qualifications Authority (MQA) or the Manufacturing, Engineering and Related Services Sector Education and Training Authority (MERSETA). These bodies ensure that the training adheres to the national standards and that the trainers themselves are qualified to teach.
- Continuing Professional Development: To cope with changing technologies and improvements in conveyor system design, ongoing professional development is encouraged. This may include workshops, seminars, and courses that cover new techniques, technologies, and regulations affecting conveyor system operation and maintenance.
- Record Keeping and Audits: Employers are required to keep detailed records of all training and certification for their employees. These records are crucial during inspections and audits by regulatory bodies to ensure compliance with national training standards.
- Impact of Non-Compliance: Failure to comply with training and certification requirements can lead to severe consequences for businesses, including fines, legal penalties, and increased liability in the event of workplace accidents. Therefore, compliance is not only regulatory but also crucial for protecting the safety of employees and the operational integrity of the business.
This structured approach to training and certification ensures that conveyor belt systems in South Africa are operated by knowledgeable and skilled personnel, thereby enhancing the safety and efficiency of operations across industries.

Conveyor Belt Regulations South Africa of Safety Checklist: A Tool for Compliance
Introduction to Conveyor Belt Safety Checklist
Adhering to conveyor belt regulations South Africa is crucial for maintaining workplace safety. A comprehensive safety checklist serves as a vital tool for businesses to ensure their conveyor systems meet the required safety standards. This checklist encompasses various aspects of conveyor belt operation, maintenance, and emergency procedures.
Components of the Safety Checklist
- Inspection of Physical Components: Regular inspection of conveyor belts, pulleys, motors, and other mechanical parts for wear and tear.
- Guarding: Verification that all necessary guards are in place and in good condition to prevent accidental contact with moving parts.
- Emergency Stops: Ensuring that emergency stop mechanisms are accessible, functional, and clearly marked.
- Training Records: Keeping up-to-date records of employee training on conveyor operation and safety procedures.
Implementing the Checklist
- Regular Reviews: Conducting routine checks using the checklist to identify and rectify potential hazards.
- Employee Involvement: Involving employees in safety checks to foster a culture of safety and awareness.
- Record-Keeping: Documenting the findings and actions taken during each safety check for compliance and audit purposes.
Updating the Checklist
- Regulatory Changes: Updating the checklist in response to changes in conveyor belt regulations in South Africa.
- Technological Advancements: Incorporating new safety features or practices as conveyor technology evolves.
- Feedback and Continuous Improvement: Adjusting the checklist based on feedback from safety audits and incident investigations.
Upgrade your operations with our high-quality, durable conveyor belts. Act now!
Conveyor Belt Regulations South Africa
In South Africa, ensuring compliance with conveyor belt regulations is critical for maintaining safety and operational efficiency in various industries. Non-compliance can lead to severe penalties, both to safeguard worker safety and to enforce adherence to established standards. Here is a detailed exploration of compliance requirements and the penalties for failing to meet them:
Regulatory Oversight: The Department of Mineral Resources and Energy (DMRE), along with other relevant bodies like the Department of Labour, plays a significant role in overseeing and enforcing compliance with conveyor belt regulations. These bodies conduct regular inspections and audits to ensure that all operational and safety standards are being met.
Compliance Requirements:
Safety Measures: All conveyor systems must be equipped with necessary safety features, such as emergency stop controls, guardrails, and warning signs. Regular safety drills and the presence of safety officers are also required to ensure that safety protocols are understood and followed by all staff.
Maintenance and Inspections: Conveyor systems must undergo regular maintenance and inspections. These inspections should be documented meticulously, with reports on any repairs or replacements made to ensure the system’s integrity and safety.
Training and Certification: Operators and maintenance personnel must undergo prescribed training and obtain certification that qualifies them to handle conveyor systems safely. This training must be updated periodically, and records of training sessions must be maintained.
Penalties for Non-Compliance:
- Fines: Businesses found non-compliant with conveyor belt regulations may face hefty fines. The size of the fine typically depends on the severity and frequency of the infractions.
- Operational Shutdowns: In cases where non-compliance poses significant risks to safety, regulatory bodies may order the temporary shutdown of operations until all issues are rectified.
- Legal Action: Severe violations, especially those resulting in accidents or injuries, might lead to legal proceedings against the company or responsible individuals. This could include charges of negligence or other criminal charges.
- Reputational Damage: Non-compliance can also lead to reputational damage, affecting the company’s relationships with clients, investors, and the public. This indirect penalty can have long-term financial implications.
Encouraging Compliance:
- Regular Audits and Feedback: Regular audits help ensure ongoing compliance and provide companies with feedback on potential areas for improvement.
- Incentives for Good Compliance: Some regulatory frameworks offer incentives for good compliance records, such as reduced inspection frequencies or public recognition of safety standards.
- Support and Training: Providing access to training resources and compliance guidelines helps businesses meet regulatory requirements more effectively.
Documentation and Record Keeping: Meticulous record-keeping of maintenance, inspections, training, and safety drills is crucial. These documents must be readily available during inspections and audits to demonstrate compliance.
Compliance with conveyor belt regulations in South Africa is enforced through a combination of regular inspections, stringent safety and operational standards, and severe penalties for non-compliance. These measures ensure that conveyor systems are used safely and efficiently, protecting workers and the operational integrity of the industries that rely on these systems.
Conveyor Belt Regulations South Africa of Risk Assessment Example: Identifying Hazards
Sample Risk Assessment for Conveyor Belts
A risk assessment for conveyor belt regulations South Africa involves a systematic examination of all aspects of the conveyor system to identify potential hazards. This process includes assessing the likelihood and severity of risks and implementing measures to mitigate them.
Key Areas of Focus in Risk Assessment
- Mechanical and Electrical Hazards: Identifying risks related to moving parts, electrical components, and machine failures.
- Environmental Factors: Assessing risks posed by the operational environment, such as dust, moisture, or chemical exposure.
- Human Factors: Considering risks related to human error, inadequate training, or poor ergonomics.
Mitigation Strategies
- Engineering Controls: Implementing physical modifications to the conveyor system to reduce risks.
- Administrative Controls: Establishing safety protocols, regular training, and emergency response procedures.
- Personal Protective Equipment (PPE): Ensuring the availability and use of appropriate PPE.
Role of Risk Assessments
- Proactive Safety Management: Identifying potential hazards before they result in accidents or injuries.
- Regulatory Compliance: Ensuring adherence to South African conveyor belt safety regulations.
- Continuous Safety Improvement: Using findings from risk assessments to enhance safety measures continuously.
Conveyor Belt Regulations South Africa: Tail Pulley Location and Safety Measures
Location and Significance of the Tail Pulley
The tail pulley, typically found at the loading end of a conveyor belt, plays a crucial role in the conveyor system. It provides tension to the belt and is instrumental in the belt’s alignment and smooth operation.
Safety Measures Around the Tail Pulley
- Guarding: Installing guards around the tail pulley to prevent accidental contact.
- Regular Inspections: Conducting frequent inspections to ensure the tail pulley and its guards are in good condition.
- Clearance and Accessibility: Maintaining adequate clearance around the tail pulley for safe access during maintenance.
- Training: Educating employees about the hazards associated with the tail pulley and the importance of following safety procedures.
Preventing Accidents
- Lockout/Tagout Procedures: Implementing lockout/tagout procedures during maintenance to prevent accidental startup.
- Emergency Procedures: Establishing clear emergency response procedures in case of incidents involving the tail pulley.
- Signage: Placing warning signs near the tail pulley area to alert workers of potential hazards.
Conveyor Belt Regulations South Africa encompass a comprehensive approach to ensuring the safety and efficiency of conveyor systems. From detailed safety checklists and risk assessments to specific measures around critical components like the tail pulley, these regulations aim to protect workers and maintain high operational standards in the conveyor belt industry.
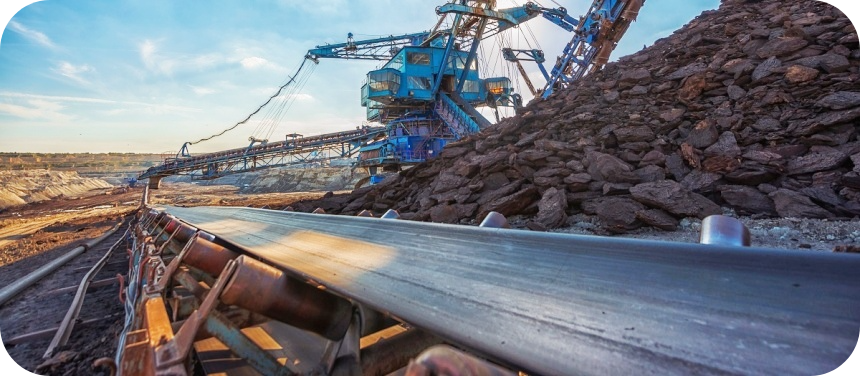
Conveyor Belt Safety Switches: Essential Safety Devices
Overview of Conveyor Belt Safety Switches
In the realm of conveyor belt operations, particularly under the stringent conveyor belt regulations South Africa, safety switches play a pivotal role. These devices are engineered to ensure the safety of the conveyor system by detecting anomalies and triggering preventive actions. Understanding the types, functions, and installation requirements of these safety switches is crucial for compliance and operational safety.
Types of Safety Switches and Their Functions
- Emergency Stop Switches: Positioned along the length of the conveyor belt, these switches can halt the conveyor’s operation in case of an emergency.
- Belt Misalignment Switches: Detect when the conveyor belt has moved off its intended track, preventing potential damage or accidents.
- Speed Monitoring Switches: Monitor the conveyor belt’s speed, triggering an alert if the belt moves too slowly or too quickly, indicating a potential issue.
- Pull Cord Switches: Allow operators to stop the conveyor from any point along its length, enhancing safety and accessibility.
Installation Requirements
- Accessibility: Safety switches must be easily accessible for regular testing and in case of an emergency.
- Visibility: Clearly marked and identifiable to ensure quick and effective use.
- Regular Testing and Maintenance: To ensure reliability, safety switches should be regularly tested and maintained as part of the conveyor system’s safety protocol.
Contribution to Safety and Compliance
- Preventive Safety: These switches act as a preventive safety measure, identifying potential hazards before they lead to accidents.
- Regulatory Compliance: Adhering to South African conveyor belt regulations, these switches are a mandatory component of conveyor belt systems, ensuring operational safety.
Conveyor Belt Regulations South Africa:Recent Changes and Updates
In recent years, South Africa has seen several changes and updates to the regulations governing conveyor belts, reflecting ongoing efforts to improve safety, efficiency, and environmental sustainability in industries that use these systems. Here’s a detailed exploration of these recent changes and updates:
- Increased Safety Standards: There has been a strong emphasis on improving safety measures around conveyor belts. This includes the introduction of stricter regulations on the installation of safety guards and emergency stop systems along the conveyor belt. These updates aim to prevent accidents and injuries that can occur from entanglements or other mechanical failures.
- Environmental Compliance: Recent updates have also focused on the environmental impact of conveyor operations. This includes regulations aimed at reducing dust and noise pollution, which are common issues with conveyor systems in mining and industrial settings. Companies are now required to implement dust suppression systems and noise reduction technologies to comply with these newer environmental standards.
- Enhanced Training Requirements: The updates have included more rigorous training and certification requirements for operators and maintenance personnel. These changes are designed to ensure that all personnel are fully trained in the latest safety practices and operational technologies. The updated regulations require more comprehensive training programs and periodic recertification to maintain high standards of operation and safety.
- Regular Maintenance and Inspection Protocols: There have been revisions to the maintenance and inspection schedules required for conveyor belts. These updates mandate more frequent and detailed inspections to ensure that all components of the conveyor system are in optimal working condition. This includes regular checks on belt alignment, wear and tear on rollers, and the integrity of the belt itself.
- Implementation of Advanced Monitoring Technologies: The new regulations encourage the use of advanced monitoring technologies, such as sensors and real-time data analytics, to enhance the safety and efficiency of conveyor systems. These technologies can detect potential issues before they lead to failures, thereby reducing downtime and maintenance costs.
- Record-Keeping and Documentation: There have been updates to the requirements for record-keeping and documentation of all maintenance, inspections, and training activities. This ensures that there is a transparent and traceable record that can be audited by regulatory bodies to confirm compliance with all applicable regulations.
- Penalties for Non-Compliance: The recent changes have also included updates to the penalties for non-compliance with conveyor belt regulations. These penalties are now more severe, which reflects the government’s commitment to enforcing these regulations rigorously. The aim is to deter non-compliance and ensure that all businesses adhere to the highest standards for safety and operational efficiency.
These recent changes and updates in South Africa’s conveyor belt regulations are part of a broader effort to ensure that these systems are safe, environmentally friendly, and operated by well-trained personnel. By staying informed about these updates, businesses can better comply with the regulations and improve their operational practices.

Conveyor Belt Code of Practice: Adhering to Best Practices
The Conveyor Belt Code of Practice in South Africa
Conveyor belt regulations South Africa code of practice sets the standard for the safe installation, operation, and maintenance of conveyor systems. It encompasses a comprehensive set of guidelines designed to ensure conveyor belts are used in a way that prioritizes safety and efficiency.
Key Aspects of the Code of Practice
- Installation Guidelines: Detailed instructions on the proper installation of conveyor belts, ensuring they meet safety standards from the outset.
- Operational Procedures: Best practices for operating conveyor belts, including speed regulations, load limits, and operator training.
- Maintenance and Inspection: Regular maintenance schedules and inspection protocols to identify and rectify potential issues before they escalate.
Importance of Adherence
- Legal Compliance: Following the code of practice is not just a matter of best practice but a legal requirement under South African law.
- Operational Efficiency: Adherence leads to smoother, more efficient conveyor belt operations, reducing downtime and maintenance costs.
- Worker Safety: The primary goal of the code of practice is to protect workers from conveyor belt-related hazards.
Conveyor Belt Regulations South Africa:Maintenance Requirements
In South Africa, the maintenance requirements for conveyor belts are rigorously stipulated to ensure the safety and efficiency of operations across various industries, such as mining, manufacturing, and logistics. Here’s a detailed discussion of these maintenance requirements:
- Routine Inspections: Conveyor belts must undergo routine inspections to ensure they are in good working condition. These inspections typically focus on checking the belt’s integrity, alignment, and tension. Wear and tear on rollers, bearings, and other moving parts are also assessed. The frequency of these inspections depends on the usage intensity of the conveyor system but is generally recommended to be monthly or quarterly.
- Preventive Maintenance: This proactive approach involves regularly scheduled maintenance activities designed to prevent breakdowns and extend the lifespan of the conveyor belt. Preventive maintenance tasks may include lubricating moving parts, adjusting belt tensions, and replacing worn parts before they fail.
- Record Keeping: Under South African regulations, it is mandatory for businesses to keep detailed records of all maintenance activities. These records should include dates of inspections, details of any issues identified, repairs made, and parts replaced. This documentation helps in tracking the history of the conveyor system, facilitates future maintenance planning, and is crucial during safety audits.
- Compliance with Standards: Maintenance activities must comply with South African National Standards (SANS) and other relevant standards, such as those from the Conveyor Equipment Manufacturers Association (CEMA). These standards provide guidelines on the minimum acceptable conditions for conveyor operation, including safety measures, quality of replacement parts, and professional conduct of maintenance personnel.
- Emergency Response and Repair: Facilities must have a plan in place for responding to and repairing any significant malfunctions or breakdowns of conveyor systems. This includes having on-site or readily available maintenance teams skilled in conveyor system repair and access to necessary spare parts to minimize downtime.
- Training of Maintenance Staff: Properly trained maintenance staff are essential for the effective upkeep of conveyor belts. Training programs should cover the specific types of conveyors used in the facility, safety procedures, and troubleshooting techniques. Ongoing training updates are recommended to keep pace with new technologies and maintenance practices.
- Audit and Review: Periodic audits of maintenance practices are recommended to ensure ongoing compliance with regulations and standards. These audits can help identify areas for improvement in the maintenance regime and ensure that the conveyor systems are safe, reliable, and efficient.
By adhering to these detailed maintenance requirements, businesses in South Africa can enhance the operational reliability of their conveyor systems, ensure compliance with national safety standards, and protect the well-being of their workforce.
Conveyor Belt Regulations South Africa of Safety Precautions: Preventive Measures
Comprehensive Safety Precautions for Conveyor Belts
In line with South Africa’s conveyor belt regulations, implementing comprehensive safety precautions is essential for the safe operation of conveyor systems. These precautions encompass various aspects of conveyor belt usage, from training and maintenance to emergency response.
Training and Awareness
- Operator Training: Ensuring all operators are thoroughly trained in the safe use of conveyor belts, including emergency procedures.
- Safety Awareness: Regular safety briefings and updates to keep safety at the forefront of operators’ minds.
Maintenance and Inspection
- Routine Checks: Regular inspections to identify the conveyor belt wear and tear or potential hazards.
- Preventive Maintenance: Scheduled maintenance to replace or repair parts before they fail.
Emergency Procedures
- Emergency Response Plan: A clear and practiced response plan for various emergency scenarios.
- Drills and Training: Regular drills to ensure all staff know how to act in an emergency.
Implementing Safety Devices
- Guarding: Installing guards in critical areas to prevent accidents.
- Safety Switches: Ensuring all safety switches are functional and accessible.
Creating a Safe Working Environment
- Housekeeping: Keeping the area around the conveyor belt clean and free from obstructions.
- PPE: Providing and enforcing the use of appropriate personal protective equipment.
Adhering to conveyor belt regulations South Africa involves a multi-faceted approach to safety. From implementing essential safety devices like switches to following a comprehensive code of practice and taking preventive measures, these regulations form the backbone of safe and efficient conveyor belt operations.
Maximize productivity with our customized conveyor belt solutions. Contact us today!
FAQs about Conveyor Belt Regulations South Africa
The requirements for a conveyor belt depend on its application but generally include:
Material Suitability: The belt material should be suitable for the type of goods it will carry, considering factors like weight, temperature, and potential chemical interactions.
Tensile Strength: The belt must have sufficient tensile strength to handle the load and the stress of operation without stretching or breaking.
Durability: The belt should be durable and resistant to wear, tear, and corrosion.
Flexibility: The belt should be flexible enough to conform to the conveyor system’s curves and inclines.
Traction: The belt’s surface should provide adequate traction for the items being conveyed.
Safety: The belt should meet safety standards, including resistance to fire and static electricity, if applicable.
OSHA (Occupational Safety and Health Administration) rules for conveyor belts are designed to protect workers from potential hazards. Key rules include:
Guarding: Conveyor belts must have guards installed to protect employees from moving parts, pinch points, and falling objects.
Lockout/Tagout Procedures: Procedures must be in place to ensure that conveyors are de-energized and cannot be started accidentally during maintenance.
Emergency Stops: Conveyor systems must have clearly marked emergency stop controls.
Regular Inspections: Conveyors should be regularly inspected and maintained to ensure they are in safe working condition.
Training: Employees working with or near conveyor belts should be trained on safe operation procedures and emergency response.
Conveyor rules are guidelines and regulations designed to ensure the safe and efficient operation of conveyor systems. These rules typically cover:
Design and Installation: Ensuring that conveyor systems are designed and installed correctly, with appropriate safety features.
Operation: Guidelines for the safe operation of conveyor systems, including speed limits and load restrictions.
Maintenance: Regular maintenance schedules to keep the conveyor in good working condition and prevent accidents.
Training: Ensuring that all personnel involved in the operation, maintenance, or repair of conveyor systems are properly trained.
Emergency Procedures: Clear procedures for handling emergencies, such as sudden stoppages or malfunctions.
The applicability of belt conveyors is broad and includes:
Material Handling: Belt conveyors are widely used in manufacturing, mining, agricultural, automotive, and other industries for transporting materials.
Bulk Handling: They are ideal for handling bulk materials like grains, coal, ores, etc.
Packaging Industries: Belt conveyors are used in packaging industries for moving products through different stages of packaging.
Food Processing: Specialized belt conveyors are used in food processing plants for handling food items in a hygienic manner.
Warehousing and Distribution: They are used for loading, unloading, and moving goods within warehouses and distribution centers.
Airport Baggage Handling: Belt conveyors are an essential part of airport baggage handling systems.
Last Updated on June 6, 2024 by Jordan Smith
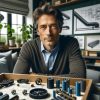
Jordan Smith, a seasoned professional with over 20 years of experience in the conveyor system industry. Jordan’s expertise lies in providing comprehensive solutions for conveyor rollers, belts, and accessories, catering to a wide range of industrial needs. From initial design and configuration to installation and meticulous troubleshooting, Jordan is adept at handling all aspects of conveyor system management. Whether you’re looking to upgrade your production line with efficient conveyor belts, require custom conveyor rollers for specific operations, or need expert advice on selecting the right conveyor accessories for your facility, Jordan is your reliable consultant. For any inquiries or assistance with conveyor system optimization, Jordan is available to share his wealth of knowledge and experience. Feel free to reach out at any time for professional guidance on all matters related to conveyor rollers, belts, and accessories.