Safety Protocols for Discharge Conveyor Belt Operations
In the realm of industrial and manufacturing processes, the discharge conveyor belt plays an indispensable role. These belts are pivotal in efficiently moving materials from one stage of production to the next, often acting as the backbone of material handling systems. A discharge conveyor belt is specifically designed to transport and offload products or raw materials to designated areas or subsequent processing equipment. Its importance lies in its ability to streamline operations, reduce manual labor, and enhance the overall efficiency of production lines. Understanding the functionality and significance of discharge conveyor belts is key to optimizing any material handling operation.
Discharge Conveyor Belt Basics
The discharge conveyor belt is a specialized component in the vast array of conveyor systems, designed with a specific and crucial function in material handling and processing lines. This section aims to define the discharge conveyor belt and compare it with other types of conveyor systems, shedding light on its unique features and applications.
Definition and Primary Function
A discharge conveyor belt is essentially a conveyor system used for the efficient removal or discharge of materials from one stage of a process to another. It is typically located at the end of a production line or in between different stages of a processing system. The primary function of a discharge belt conveyor is to transport finished products, waste materials, or bulk commodities from the main conveyor line to designated areas such as storage, packaging stations, or onto other transport systems. This type of conveyor is vital in ensuring a seamless transition and continuous flow in various industrial processes, ranging from manufacturing and mining to agriculture and recycling.
Comparison with Other Conveyor Systems
- Functionality: Unlike general-purpose conveyor belts that may be used for a variety of tasks within a production line, discharge conveyor belts are specifically designed for the end-of-line or transitional phases of material handling.
- Design: Discharge conveyor belts often have features tailored to the type of material they handle at the end of the process, such as high-temperature resistance for hot products, or special linings for abrasive materials.
- Integration with Processing Equipment: These belts are frequently integrated with other processing equipment, such as crushers, shredders, or screening machines, making them an integral part of the overall system rather than standalone units.
- Material Flow Control: Discharge conveyor belts may include advanced features for controlling the flow of materials, such as gates, chutes, or variable speed settings, which are not as common in standard conveyor systems.
- Orientation and Space Efficiency: They are often designed to save space and can be oriented in various directions (vertical, inclined, or horizontal) to suit the layout of the processing plant and efficiently move materials to the next stage or for storage.
Discharge conveyor belts are specialized conveyor systems with distinct features and designs, tailored to efficiently handle the end-of-line or transitional phases in material handling and processing industries. Their role is crucial in ensuring the smooth operation and efficiency of the entire production or processing line.
Dimensions and Specifications of the Discharge Conveyor Belt
Discharge conveyor belts play a pivotal role in material handling and transportation processes. In this section, we will delve into the dimensions and specifications of discharge conveyor belts, shedding light on how these factors profoundly affect their performance and efficiency. We will also explore the essential considerations when determining the size and capacity of a discharge conveyor belt, providing valuable insights for various industrial applications.
What are Discharge Conveyor Belt Dimensions
Belt Width: The width of a discharge conveyor belt is a critical dimension that directly impacts its capacity and throughput. Wider belts can accommodate larger volumes of material, making them suitable for applications where high throughput is essential.
Belt Length: The length of the conveyor belt is another crucial dimension. Longer belts are suitable for transporting materials over greater distances or elevations, making them ideal for applications such as loading ships or stockpiling materials.
Cleat Height and Spacing: Cleats are protrusions on the conveyor belt that help prevent material from sliding or falling off. Understanding the cleat height and spacing is essential for ensuring the secure transport of specific materials, especially those with irregular shapes or high flowability.
Factors Influencing Belt Size Selection
Material Type: The nature and characteristics of the material being conveyed influence the choice of belt size. Materials with different sizes, shapes, and flow properties may require different belt dimensions to ensure efficient transport.
Throughput Requirements: Determining the desired material throughput is crucial. Higher throughput often necessitates wider and longer conveyor belts to meet production demands.
Conveyor Angle: The angle at which the conveyor operates, whether horizontal or inclined, affects the choice of belt size. Inclined conveyors typically require larger belts to prevent material spillage.
Environmental Conditions: Harsh environmental conditions, such as extreme temperatures or moisture levels, can impact the choice of belt size and material to ensure durability and longevity.
Reference to Technical Specifications
For in-depth technical specifications and guidelines on choosing the right discharge conveyor belt dimensions, we recommend referring to a downloadable PDF guide provided by conveyor belt manufacturers or industry experts. These guides offer comprehensive insights into belt selection, ensuring that you make informed decisions tailored to your specific application.
Understanding the dimensions and specifications of discharge conveyor belts is essential for optimizing material handling processes in various industries. Factors such as belt width, length, cleat height, and spacing play a pivotal role in determining the belt’s performance and suitability for specific applications. By considering material characteristics, throughput requirements, conveyor angles, and environmental conditions, you can select the ideal discharge conveyor belt dimensions to enhance efficiency and productivity in your operations.
Exploring the Types of the Discharge Conveyor Belt
Discharge conveyor belts are integral components in various industrial processes, and they come in several types, each designed to meet specific operational needs. Understanding these variations is crucial for selecting the right conveyor belt for your application.
- Modular Discharge Conveyor Belts: These belts are known for their versatility and durability. Composed of interlocking plastic modules, they are easy to clean and maintain, making them ideal for food processing, pharmaceuticals, and other industries where hygiene is a priority. Their modular nature allows for easy customization in length and width, catering to different space and process requirements.
- Slat Discharge Conveyor Belts: Slat conveyors are characterized by their flat, solid surfaces made of wood, metal, or plastic, attached to a chain. Their robust design makes them suitable for heavy or bulky items, often used in assembly lines, bottling plants, and similar settings. They are particularly effective in handling items that require a stable and firm support during transport.
- Portable Discharge Conveyor Belts: These conveyors offer the advantage of mobility and flexibility. They are ideal for temporary setups or where the conveyor needs to be moved between different parts of a facility. Portable discharge conveyor belts are commonly used in construction sites, warehouses, and agricultural applications. They are typically lighter in weight and can be easily set up and dismantled as required.
Each type of discharge conveyor belt has its unique features and ideal applications. When choosing a discharge conveyor belt, it’s important to consider the specific needs of your operation, including the nature of the materials being transported, the required speed and efficiency of the process, and the physical constraints of the workspace. By selecting the appropriate type of discharge conveyor belt, businesses can ensure smoother, more efficient, and cost-effective operations.
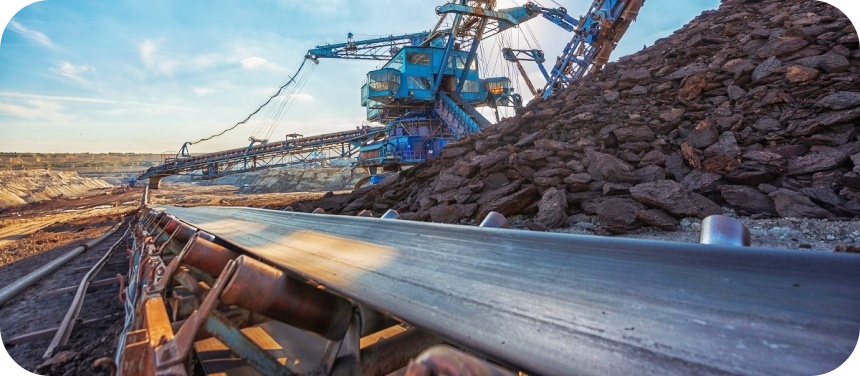
Discharge Conveyor Belt in Various Industries
The discharge conveyor belt plays a pivotal role in numerous industries, showcasing its versatility and adaptability in handling diverse materials and operational environments. This section explores the application of discharge conveyor belts in various sectors such as mining, agriculture, and manufacturing, supplemented by case studies and real-world examples.
Mining Industry
In the mining industry, discharge conveyor belts are essential for transporting extracted materials from the mining site to processing areas or storage facilities. They are particularly crucial in handling bulk materials like coal, ore, and minerals. These belts are designed to withstand harsh conditions, including abrasive materials and outdoor environments, ensuring the efficient and continuous flow of resources from the extraction point.
Case Study: A coal mining operation uses a series of discharge conveyor belts to transport coal from the extraction face to the surface. The belts are equipped with robust features to handle the heavy load and abrasive nature of coal, significantly reducing manual labor and transportation time.
Agriculture Industry
Agriculture extensively utilizes discharge conveyor belts for the handling and processing of various crops and produce. These belts are used in applications ranging from the transportation of grains from storage silos to processing units, to the movement of fruits and vegetables in packing facilities.
Real-World Application: In a grain processing facility, discharge conveyor belts are used to efficiently move harvested grains from storage units to milling machines. The belts are designed to minimize damage to the grains, ensuring quality and reducing waste.
Manufacturing Industry
In manufacturing, discharge conveyor belts are integral in assembly lines, where they are used to transport components and finished products between different stages of the manufacturing process. They are tailored to suit the specific requirements of the products being manufactured, whether it be electronics, automobiles, or consumer goods.
Case Study: An automobile assembly plant uses discharge conveyor belts to move car parts from the assembly line to the painting and finishing section. The belts are customized to handle various sizes and weights of car parts, streamlining the assembly process.
Versatility Across Industries
Discharge conveyor belts are not limited to these industries; they are also prevalent in sectors like recycling, pharmaceuticals, and food processing. Their design varies to suit the specific needs of each industry, whether it’s handling delicate pharmaceutical products or rugged recycling materials.
Discharge conveyor belts are versatile systems crucial in a wide range of industries. They are tailored to meet the specific needs of different sectors, proving their indispensability in efficient and effective material handling and processing. These case studies and applications demonstrate how discharge conveyor belts adapt to various industrial challenges, enhancing productivity and operational efficiency.
Guidelines for Purchasing a Discharge Conveyor Belt
When it comes to acquiring a discharge conveyor belt, making an informed decision is crucial for ensuring efficiency and longevity in your operations. Here are key considerations and tips for purchasing the right discharge conveyor belt:
- Assessing Your Needs: Before purchasing, clearly define what you need from a discharge conveyor belt. Consider the type of materials it will transport, the required speed, load capacity, and the environmental conditions it will operate in. These factors will influence the choice of material, size, and design of the conveyor belt.
- New vs. Used Discharge Conveyor Belts: Deciding between new and used conveyor belts depends on your budget and requirements. New belts offer the latest technology and typically come with a warranty, but they are more expensive. Used belts can be cost-effective but may have less lifespan and no warranty. Ensure to inspect used belts thoroughly for any wear and tear.
- Finding Discharge Conveyor Belts for Sale: Discharge conveyor belts can be purchased from various sources including direct from manufacturers, through distributors, or from online marketplaces. Attending industry trade shows can also provide opportunities to see different models and talk to manufacturers directly.
- Evaluating Vendors and Manufacturers: When selecting a vendor or manufacturer, consider their reputation, experience in the industry, and the quality of their products. Look for reviews or ask for references. It’s also important to consider the level of after-sales support and services they offer, such as installation, maintenance, and repair services.
- Cost vs. Quality: While cost is a significant factor, it should not be the only consideration. A cheaper discharge conveyor belt might save money upfront but could lead to higher maintenance costs and less efficiency over time. Invest in a quality conveyor belt that offers durability and meets your specific needs.
- Warranty and Support: Check the warranty terms and what it covers. A good warranty can save significant costs in case of defects or issues. Additionally, ensure the manufacturer or vendor offers adequate support for installation, troubleshooting, and maintenance.
By carefully considering these aspects, you can make a well-informed decision that ensures you purchase a discharge conveyor belt that is efficient, durable, and suitable for your specific industrial needs.
Maintenance and Safety Considerations for Discharge Conveyor Belt
Maintenance and safety are integral aspects of operating discharge conveyor belts effectively and responsibly. In this section, we will explore best practices for maintaining discharge conveyor belts to ensure their longevity and continued efficiency. Additionally, we will highlight critical safety protocols and features that should be considered to promote safe operations in industrial settings.
Best Practices for Conveyor Belt Maintenance
Regular Inspections: Implement a routine inspection schedule to identify and address potential issues promptly. Inspect the belt for signs of wear, damage, or misalignment. Regular inspections can help prevent minor problems from escalating into costly repairs.
Cleaning Procedures: Keep the discharge conveyor belt clean and free from debris. Material buildup or spillage can lead to belt slippage and reduced efficiency. Establish cleaning procedures to maintain optimal belt performance.
Belt Tensioning: Proper tensioning of the conveyor belt is crucial. Over-tightening or under-tightening can lead to premature wear and reduced belt life. Follow manufacturer recommendations for belt tensioning to ensure optimal performance.
Lubrication: Some conveyor systems may require lubrication for components like pulleys, bearings, and rollers. Regularly lubricate these components according to manufacturer guidelines to reduce friction and wear.
Spare Parts Inventory: Maintain an inventory of essential spare parts to quickly replace worn or damaged components. This minimizes downtime and ensures that the conveyor belt remains operational.
Safety Protocols for Discharge Conveyor Belt Operation
Training: Ensure that all personnel operating discharge conveyor belts receive proper training on safe operation procedures. Training should cover emergency shutdown protocols, material handling guidelines, and awareness of potential hazards.
Emergency Stop Systems: Install emergency stop buttons and systems along the conveyor’s length for quick shutdown in case of emergencies or safety concerns. Regularly test these systems to ensure their effectiveness.
Guarding and Safety Barriers: Implement guarding and safety barriers around conveyor belts to prevent unauthorized access and protect workers from moving parts. Guards should be in compliance with safety standards.
Emergency Response Plan: Develop a comprehensive emergency response plan that outlines procedures for addressing accidents, spills, or equipment malfunctions. Ensure that all personnel are familiar with the plan and know their roles in case of emergencies.
Safety Signage: Use clear and visible safety signage to communicate hazards, restricted areas, and safety protocols. This helps raise awareness among employees and visitors working near the discharge conveyor belt.
Regular Safety Audits: Conduct regular safety audits and inspections to identify and rectify potential safety hazards. Address any issues promptly to maintain a safe working environment.
Prioritizing maintenance and safety considerations is essential when operating discharge conveyor belts. Implementing best practices for belt maintenance, such as inspections, cleaning, tensioning, and lubrication, can extend the belt’s lifespan and optimize its performance. Additionally, strict adherence to safety protocols, including proper training, emergency stop systems, guarding, and emergency response planning, is crucial to ensure the well-being of personnel and the safe operation of discharge conveyor belts in industrial settings.
Innovations and Future Trends in Discharge Conveyor Belt Technology
In this section, we delve into the exciting realm of innovations and future trends in discharge conveyor belt technology. The conveyor belt industry is constantly evolving, driven by technological advancements and changing industrial needs. Here, we provide insights into the latest developments and offer predictions for the future of conveyor belt systems.
Automation and Robotics Integration
One of the most significant trends in discharge conveyor belt technology is the integration of automation and robotics. Conveyor systems are becoming smarter, with the capability to interact seamlessly with other machinery and processes. Automated conveyor belts can efficiently handle tasks like sorting, packaging, and material transfer, increasing productivity and reducing labor costs.
Enhanced Efficiency and Sustainability
As industries focus more on sustainability, discharge conveyor belts are evolving to be more energy-efficient and environmentally friendly. Manufacturers are developing conveyor belts with improved power transmission systems, reducing energy consumption. Additionally, eco-friendly materials and manufacturing processes are being adopted to minimize environmental impact.
Advanced Materials and Coatings
The materials used in conveyor belts are continually improving to enhance performance and durability. Innovations in composite materials and coatings provide benefits such as increased resistance to wear, abrasion, and harsh environmental conditions. These advancements contribute to longer conveyor belt lifespans and reduced maintenance requirements.
IoT and Real-time Monitoring
The Internet of Things (IoT) is making its mark in conveyor belt technology. IoT sensors and real-time monitoring systems are being integrated into conveyor systems to provide valuable data on performance, maintenance needs, and operational efficiency. Predictive maintenance can help reduce downtime and extend the life of discharge conveyor belts.
Modular and Customizable Designs
Conveyor belt manufacturers are offering more modular and customizable designs to meet specific industry requirements. Customers can now tailor conveyor systems to their unique needs, ensuring optimal performance in various applications. This flexibility is driving increased adoption across diverse industries.
Sustainability Initiatives
Sustainability is a driving force behind innovation in conveyor belt technology. Manufacturers are investing in research and development to create belts with recycled materials and lower carbon footprints. Sustainable practices, such as efficient belt design and reduced material waste, are becoming standard in the industry.
Predictions for the Future
Looking ahead, the future of discharge conveyor belt technology holds exciting possibilities. We can anticipate even greater integration of artificial intelligence (AI) and machine learning for predictive maintenance, further reducing downtime and enhancing operational efficiency. Conveyor belts may also become more adaptable to handle a wider range of materials and tasks.
The world of discharge conveyor belt technology is marked by constant innovation. From automation and sustainability to advanced materials and real-time monitoring, these advancements are shaping the future of conveyor systems. As industries continue to evolve, so will conveyor belts, providing more efficient, sustainable, and adaptable solutions for a wide range of applications. Stay tuned for the exciting developments on the horizon in the world of discharge conveyor belt technology.
Fill out the form below to receive a customized quote for your discharge conveyor belt needs.
FAQs about Discharge Conveyor Belt
A discharge conveyor belt is a specific type of conveyor system designed to efficiently remove or discharge materials from a processing or production line. These belts are typically positioned at the end of a conveyor line and are used to transport finished products or materials to storage areas, packaging stations, or onto additional transport systems. They are crucial in ensuring a smooth and continuous flow in the production process.
Belt Conveyors: These are the most common type, consisting of a continuous belt that moves over rollers or a flat pan. They are versatile and can transport a wide range of materials.
Roller Conveyors: These use a series of rollers to move goods. They can be gravity-driven or powered and are ideal for handling solid items like boxes and pallets.
Overhead Conveyors: These systems are installed above the floor and are used to move goods along a fixed path. Overhead conveyors are often used in industries where floor space is at a premium.
A conveyor belt delivery system is an automated system used to transport goods and materials from one location to another within a facility or between different facilities. This system typically involves a series of conveyor belts that move items along a predetermined path, facilitating efficient and continuous movement of products. It’s commonly used in manufacturing, warehousing, and distribution centers to streamline the handling and delivery of products.
Servicing a conveyor belt involves several key steps to ensure it operates efficiently and safely:
Regular Inspections: Conduct frequent inspections to identify any signs of wear, damage, or misalignment.
Cleaning: Keep the conveyor belt and its components clean to prevent material buildup that can cause damage or inefficiency.
Lubrication: Regularly lubricate moving parts like rollers and bearings to reduce friction and wear.
Tension Adjustment: Ensure the belt is properly tensioned to prevent slippage and extend its lifespan.
Replacement of Worn Parts: Replace any worn or damaged parts promptly to maintain optimal performance.
Professional Maintenance: Schedule regular maintenance checks by professionals to ensure all components are functioning correctly.
Last Updated on July 29, 2024 by Jordan Smith
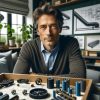
Jordan Smith, a seasoned professional with over 20 years of experience in the conveyor system industry. Jordan’s expertise lies in providing comprehensive solutions for conveyor rollers, belts, and accessories, catering to a wide range of industrial needs. From initial design and configuration to installation and meticulous troubleshooting, Jordan is adept at handling all aspects of conveyor system management. Whether you’re looking to upgrade your production line with efficient conveyor belts, require custom conveyor rollers for specific operations, or need expert advice on selecting the right conveyor accessories for your facility, Jordan is your reliable consultant. For any inquiries or assistance with conveyor system optimization, Jordan is available to share his wealth of knowledge and experience. Feel free to reach out at any time for professional guidance on all matters related to conveyor rollers, belts, and accessories.