Conveyor Belt Teeth: Enhancing Industrial Operations
Conveyor belts play a pivotal role in various industries, streamlining the transportation and handling of materials in sectors ranging from mining and manufacturing to packaging and distribution. These belts, often the backbone of large-scale production and logistics operations, ensure efficiency, safety, and reliability in material handling. Among the critical components of these systems are “conveyor belt teeth” – a feature that significantly enhances the precision and grip of the belt. Conveyor belt teeth are integral in maintaining the synchronization and alignment necessary for the smooth operation of the conveyor system. Their design and material composition are tailored to meet the specific demands of different industrial environments, making them a key factor in the functionality and efficiency of conveyor belt systems. Understanding the significance of conveyor belt teeth is essential for optimizing the performance and longevity of these indispensable industrial tools.
Types of Conveyor Belt Teeth
Understanding the various types of conveyor belt teeth is crucial for selecting the right conveyor system for specific industrial needs. Each type of tooth design on conveyor belts offers unique benefits and is suited for different environments and applications.
Plastic Conveyor Belts
Plastic conveyor belts, equipped with conveyor belt teeth, are widely used in industries like food processing, pharmaceuticals, and packaging. These belts are made from durable, food-grade plastic materials, making them ideal for environments where hygiene and easy cleaning are paramount. The advantages of using plastic conveyor belts include:
Hygienic Properties: Their non-porous surface prevents bacterial growth and contamination, essential in food and pharmaceutical industries.
Corrosion Resistance: Plastic belts resist corrosion from chemicals and moisture, making them suitable for harsh chemical environments or outdoor applications.
Low Maintenance: These belts require minimal maintenance, as they are less prone to wear and tear compared to metal or fabric belts.
Flexibility in Design: Plastic conveyor belts can be easily customized with different conveyor belt teeth profiles to suit specific product handling requirements.
Modular Belts
Modular belts are a type of plastic conveyor belt but with a unique design. They consist of individual plastic modules linked together, allowing for easy repair and customization. The conveyor belt teeth on these belts are integral to their design, providing enhanced grip and movement control. Compared to traditional conveyor belt designs, modular belts offer:
Increased Durability: The modular design allows for damaged sections to be replaced easily, extending the overall lifespan of the belt.
Versatility: They can be used in a wide range of applications, from light to heavy-duty material handling.
Improved Belt Tracking: The design of the conveyor belt with teeth ensures better tracking and alignment, reducing downtime due to belt misalignment.
Customization: Modular belts can be customized with various types of conveyor belt teeth, widths, and materials to meet specific application needs.
Heavy Duty Conveyor Belts
High Load Capacity: They are capable of handling heavy loads and sharp, abrasive materials without significant wear and tear.
Enhanced Durability: The conveyor belt teeth on heavy-duty belts are designed to withstand harsh conditions, including extreme temperatures and impacts.
Reduced Downtime: Their strength and durability lead to less frequent maintenance and replacements, ensuring continuous operation.
Application-Specific Design: Heavy-duty conveyor belts and their teeth can be tailored to specific industrial applications, ensuring optimal performance and longevity.
Heavy-duty conveyor belts are designed to handle the toughest industrial applications, such as mining, construction, and heavy manufacturing. These belts are characterized by their robust construction and the strength of their conveyor belt with teeth. Key aspects include:
The type of conveyor belt teeth chosen should align with the specific requirements of the industry and application, considering factors like material, durability, maintenance needs, and environmental conditions.
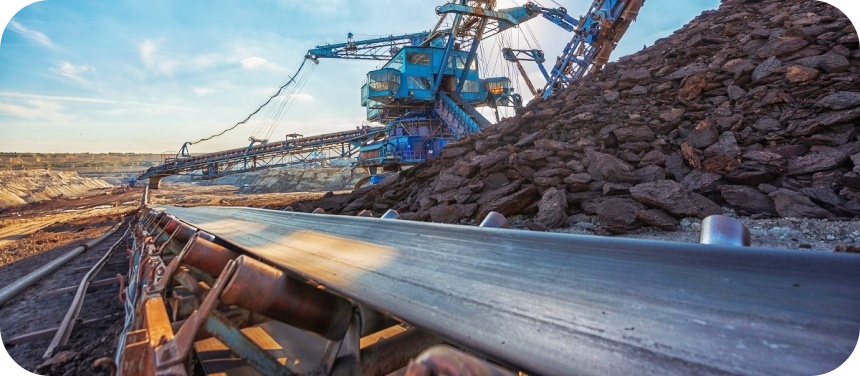
Conveyor Belt Teeth Design and Technical Aspects
The design and technical aspects of conveyor belt teeth are pivotal in determining the efficiency and suitability of conveyor belts for various industrial applications. This section explores the critical elements that define the functionality and adaptability of conveyor belts with teeth.
Conveyor Belt Technical Data Sheet
Technical data sheets are vital tools for understanding the specifications of conveyor belts, especially those with conveyor belt teeth. These sheets provide a comprehensive overview of the belt’s capabilities and limitations, guiding users in making informed decisions. Key parameters typically included in a conveyor belt technical data sheet are:
Wide Conveyor Belts
Wide conveyor belts are designed to handle substantial volumes of materials, making them ideal for specific scenarios. The width of the belt is a critical factor in determining the conveyor’s efficiency and application. Wide belts are preferable in situations such as:
Bulk Material Handling: In industries like mining or construction where large amounts of material need to be moved efficiently.
High-Volume Production Lines: In manufacturing settings where products are produced or packaged in large quantities.
Stability for Large Loads: Wider belts provide more surface area, offering stability for large or irregularly shaped items.
Lightweight Conveyor Belts
Lightweight conveyor belts, often equipped with specialized conveyor belt teeth, are tailored for industries where flexibility and ease of handling are paramount. The benefits of using lightweight belts include:
Energy Efficiency: They require less energy to operate due to their reduced weight.
Ease of Installation and Maintenance: Lightweight belts are simpler to install and maintain, leading to reduced downtime.
Adaptability: These belts can easily conform to various conveyor configurations and are ideal for systems with tight turns and complex paths.
However, there are trade-offs to consider:
Reduced Durability: Lightweight belts may not withstand harsh conditions as effectively as heavier belts.
Lower Load Capacity: They might not be suitable for heavy-duty applications due to lower load-bearing capabilities.
The design and technical aspects of conveyor belt teeth play a crucial role in determining the appropriate conveyor belt for specific industrial needs. Understanding these aspects is key to optimizing conveyor belt performance, balancing factors such as efficiency, durability, and operational requirements.
Maintenance and Replacement of Conveyor Belt Teeth
Proper maintenance and timely replacement of conveyor belt teeth are crucial for the longevity and efficiency of conveyor systems. This section focuses on recognizing when replacements are needed and how to effectively implement them, as well as exploring the advantages of custom conveyor belts for unique industrial requirements.
Conveyor Belt Teeth Replacement
Regular inspection and maintenance are key to ensuring the longevity and proper functioning of conveyor belts. The replacement of conveyor belt with teeth is a critical aspect of this maintenance. Signs that indicate the need for belt teeth replacement include:
Visible Wear and Tear: Excessive wear on the teeth, such as cracks, fraying, or missing sections.
Slippage and Misalignment: Frequent slippage or misalignment of the belt, indicating that the teeth are no longer effectively engaging with the pulleys.
Noise and Vibration: Unusual noises or vibrations during operation can signal that the teeth are damaged or worn out.
Decreased Efficiency: A noticeable decrease in conveyor efficiency or increased energy consumption.
A step-by-step guide on replacing conveyor belt teeth involves:
- Safety Precautions: Ensure the conveyor system is turned off and locked out before starting the replacement process.
- Removal of the Old Belt: Carefully remove the old belt from the conveyor system, paying attention to how it was installed.
- Inspection of Pulleys and Rollers: Check for wear or damage on pulleys and rollers that could affect the new belt.
- Installation of the New Belt: Place the new belt onto the conveyor system, ensuring that the teeth properly align with the pulleys.
- Tension Adjustment: Adjust the tension of the belt according to manufacturer specifications to ensure optimal performance.
- Test Run: Conduct a test run to verify that the belt is functioning correctly and make any necessary adjustments.
Custom Conveyor Belts
Custom conveyor belts are designed to meet specific industrial needs and can significantly enhance efficiency and reduce maintenance requirements. The discussion on custom solutions includes:
Tailored Design: Custom belts are designed to fit unique conveyor configurations and specific operational requirements, such as weight, speed, and environmental conditions.
Material Selection: Custom belts allow for the selection of specific materials that are best suited for the application, whether it’s for temperature resistance, chemical exposure, or abrasion resistance.
Innovative Features: Incorporation of features like reinforced teeth, specialized coatings, or unique tooth profiles to improve performance and longevity.
Reduced Downtime: Custom belts are often easier to maintain and replace, leading to reduced downtime and increased productivity.
Custom conveyor belts, with their tailored design and specialized features, offer a solution for challenging industrial applications, ensuring that conveyor systems operate at peak efficiency with minimal maintenance requirements.
Choosing the Right Conveyor Belt with Appropriate Conveyor Belt Teeth
Selecting the right conveyor belt, especially considering the conveyor belt teeth, is crucial for ensuring optimal performance, efficiency, and longevity of the conveyor system. This section provides guidance on choosing the right conveyor belt material and factors to consider for specific applications.
Conveyor Belt Material
The material of the conveyor belt, including the conveyor belt teeth, plays a significant role in its performance and suitability for various applications. Different materials offer distinct properties:
Rubber Belts: Commonly used for general purpose applications; they are flexible and have good grip but may not be suitable for high-temperature environments.
PVC Belts: Offer good resistance to chemicals and are suitable for food processing industries due to their non-toxic nature.
Polyurethane Belts: Known for their excellent chemical and abrasion resistance; ideal for pharmaceutical and food industries.
Metal Belts: Best for high-temperature applications and situations requiring high strength and durability.
When choosing the right material, consider the following:
Industry Requirements: Food processing industries often require non-toxic and easy-to-clean materials like PVC or polyurethane.
Environmental Conditions: For high-temperature or chemically aggressive environments, metal or polyurethane belts are preferable.
Durability Needs: Heavy-duty applications may require metal belts, while lighter applications can use rubber or PVC.
Selecting a Conveyor Belt for Specific Applications
Choosing the right conveyor belt with the appropriate conveyor belt teeth involves considering several factors:
- Load Capacity: The belt must be capable of handling the weight and volume of materials being transported.
- Speed Requirements: High-speed applications may require belts with specific tooth designs for better grip and control.
- Operating Environment: Belts used in outdoor or harsh environments should have high resistance to weather, chemicals, and temperature variations.
- Maintenance and Durability: Consider the ease of maintenance and the expected lifespan of the belt in the given application.
Case studies and examples of successful conveyor belt implementations include:
Food Processing Industry: Use of PVC conveyor belts with specific tooth designs for gentle handling of food products and compliance with hygiene standards.
Mining Industry: Implementation of heavy-duty metal conveyor belts with robust teeth for transporting large volumes of materials in rugged conditions.
Packaging Industry: Utilization of high-speed polyurethane belts with precision teeth for efficient and accurate packaging processes.
Selecting the right conveyor belt with suitable conveyor belt teeth is a critical decision that impacts the efficiency and effectiveness of a conveyor system. Understanding the material properties, application requirements, and environmental conditions is essential for making an informed choice that meets the specific needs of the industry.
Optimize your production with our expert conveyor belt solutions.
FAQs about Conveyor Belt Teeth
The teeth on a belt are an essential feature in various types of belts used in mechanical systems, and they are commonly referred to as “belt teeth” or “sprockets.” These teeth are strategically placed on the inner surface of the belt and are designed to mesh with corresponding grooves in a pulley. This design is crucial for preventing slippage and ensuring a synchronized movement between the belt and the pulley system. In conveyor systems, these teeth play a vital role in maintaining the precision and efficiency of material handling, as they provide a secure grip that facilitates the smooth and controlled movement of goods.
A toothed belt, characterized by the presence of teeth along its inner surface, is commonly known as a “timing belt” or a “synchronous belt.” These belts are integral to various mechanical systems where precise timing and synchronization between the belt and pulley are required. The design of a toothed belt ensures that there is no slippage during operation, which is crucial for applications that demand exact timing, such as in automotive engines where the belt synchronizes the rotation of the crankshaft and camshaft. In industrial and manufacturing settings, toothed belts are used in machinery and conveyor systems for accurate and efficient operations.
A pulley equipped with teeth is typically referred to as a “toothed pulley” or “gear pulley.” These pulleys are designed to work in tandem with toothed or cogged belts, ensuring a secure and slip-free engagement between the belt and the pulley. The teeth on the pulley are shaped to fit perfectly with the belt teeth, allowing for precise control over the movement of the belt. This setup is crucial in applications where accurate positioning and timing are essential. Toothed pulleys are commonly used in various mechanical devices, including conveyor systems, where they contribute to the efficient and controlled transportation of materials.
Deciding whether a cogged belt is better than a toothed belt depends largely on the specific requirements of the application. Cogged belts, known for their notched or grooved design, offer increased flexibility and can operate more efficiently under lower temperatures. This makes them suitable for applications that require bending around smaller pulleys or in compact spaces. On the other hand, toothed belts, also known as synchronous belts, are designed for applications that require precise timing and synchronization. They are ideal for situations where exact alignment of shaft rotation is necessary. The choice between the two types of belts should be based on factors such as the nature of the load, operational speed, temperature conditions, and the specific mechanical requirements of the system.
Last Updated on July 18, 2024 by Jordan Smith
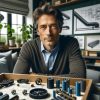
Jordan Smith, a seasoned professional with over 20 years of experience in the conveyor system industry. Jordan’s expertise lies in providing comprehensive solutions for conveyor rollers, belts, and accessories, catering to a wide range of industrial needs. From initial design and configuration to installation and meticulous troubleshooting, Jordan is adept at handling all aspects of conveyor system management. Whether you’re looking to upgrade your production line with efficient conveyor belts, require custom conveyor rollers for specific operations, or need expert advice on selecting the right conveyor accessories for your facility, Jordan is your reliable consultant. For any inquiries or assistance with conveyor system optimization, Jordan is available to share his wealth of knowledge and experience. Feel free to reach out at any time for professional guidance on all matters related to conveyor rollers, belts, and accessories.