Basic Conveyor Belt Running Rules to Follow
Conveyor belt running is a critical aspect of the functionality of conveyor systems in various industries. It involves the continuous movement of a conveyor belt around a system of pulleys and rollers, driven typically by electric motors. The smooth and efficient running of a conveyor belt is paramount not only for operational efficiency but also for ensuring safety in the workplace. Proper conveyor belt running minimizes the risk of accidents, reduces wear and tear on the machinery, and ensures the timely transportation of materials, playing a vital role in maintaining the overall productivity of industrial operations.
Conveyor Belt Running Meaning
A running conveyor belt is a fundamental concept in the realm of material handling and industrial automation. It refers to the continuous motion of a conveyor belt around a system of rollers and pulleys, driven by motors, which facilitates the transport of materials from one point to another. This motion is the backbone of countless industrial and manufacturing processes, playing a crucial role in the efficiency and productivity of operations.
Definition and Explanation
- Basic Concept: Conveyor belt running is the action of a belt moving over a conveyor system. It involves the belt looping over a series of rollers and pulleys, with one or more of these pulleys being powered, usually by an electric motor. This movement is what transports materials placed on the belt.
- Mechanics Involved: The drive pulley, which is connected to the motor, transfers its rotational motion to the belt. The tension in the belt, maintained by idler or tail pulleys, keeps it in place and ensures a consistent movement.
Significance in Industrial and Manufacturing Settings
- Efficiency in Material Handling: Conveyor belt running is integral to industries where rapid and efficient transport of goods is essential. This includes sectors like manufacturing, mining, logistics, and packaging.
- Safety and Productivity: Proper running of the conveyor belt ensures safety in the workplace, reducing the risk of accidents. It also minimizes downtime and enhances overall productivity.
- Cost-Effectiveness: Efficient conveyor belt running reduces wear and tear, leading to lower maintenance costs and prolonged equipment life.
Conveyor belt running is not just about the movement of a belt — it’s about the seamless integration of mechanical and electrical components to create an efficient, safe, and cost-effective material handling solution.
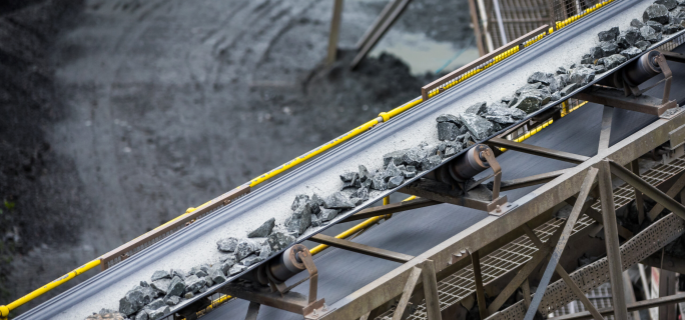
Conveyor Belt Running Diagram and Process
Conveyor belt running is best understood through a combination of visual aids and detailed explanations. This section provides a comprehensive understanding of how conveyor belts operate.
Visual Representation (Diagram) of Conveyor Belt Running
- Diagram Explanation: A conveyor belt running diagram typically illustrates the arrangement of the conveyor belt, drive and tail pulleys, idlers, and the direction of the belt’s movement. It may also show the motor placement and any tensioning devices.
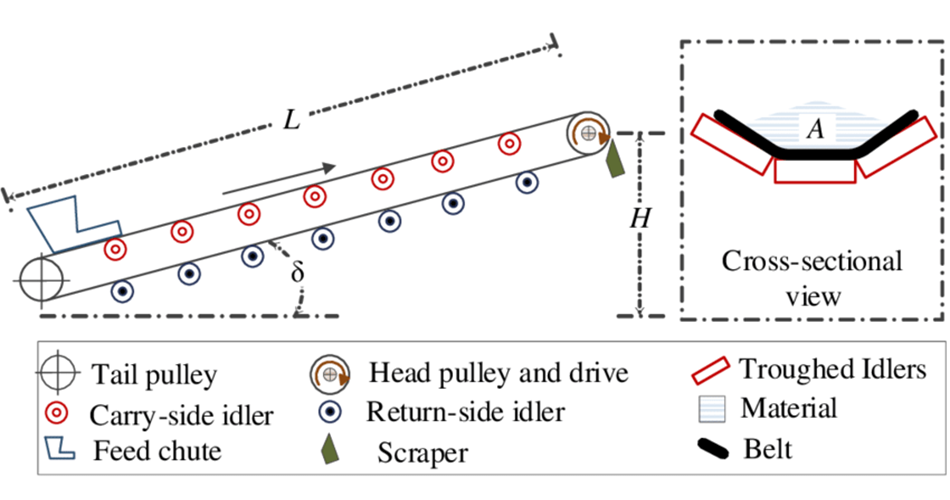
- Components Identification: The diagram helps in identifying key components and their roles in the conveyor system.
Detailed Explanation of the Conveyor Belt Running Process
- Start-Up and Operation: The process begins with the motor powering the drive pulley. The belt, which is looped around the drive pulley and idlers, starts moving due to the friction between it and the pulley.
- Material Transportation: As the belt moves, it carries materials placed on it from the loading point to the discharge point.
- Tension Maintenance: Idler pulleys maintain the necessary tension in the belt to prevent slippage and ensure smooth operation.
Incorporation of a Conveyor Belt Running Video
- Practical Understanding: A video of a conveyor belt in operation can provide practical insights into the dynamics of conveyor belt running. It helps in visualizing the movement, the interaction between different components, and the overall operation of the system.
Through diagrams and videos, the concept of conveyor belt running becomes clearer, providing a solid foundation for understanding the more technical aspects of conveyor systems.
5 Basic Conveyor Belt Running Rules To Follow
Here are five basic rules to follow for running a conveyor belt system efficiently and safely:
Regular Maintenance and Inspection:
- Schedule routine inspections to check for wear and tear, misalignment, and other issues.
- Ensure all parts are lubricated and free from debris.
- Replace worn-out components promptly to prevent breakdowns.
Proper Loading Techniques:
- Load the conveyor belt evenly to prevent stress and potential damage.
- Avoid overloading, which can lead to mechanical failure and safety hazards.
- Ensure materials are placed on the belt in the correct orientation and position.
Ensure Belt Alignment:
- Regularly check and adjust the belt alignment to prevent conveyor belt tracking issues.
- Misalignment can cause belt wear, increased energy consumption, and system inefficiency.
- Use alignment tools and devices to maintain proper belt tracking.
Safety Measures and Training:
- Provide comprehensive training for all operators and maintenance personnel on proper conveyor belt usage and safety protocols.
- Implement safety guards and emergency stop mechanisms.
- Conduct regular safety drills and inspections to ensure compliance with safety standards.
Monitor Belt Tension and Speed:
- Maintain proper belt tension to avoid slippage and excessive wear.
- Adjust the belt speed according to the material being transported and the system’s capacity.
- Use monitoring devices to keep track of tension and speed, making adjustments as needed to optimize performance.
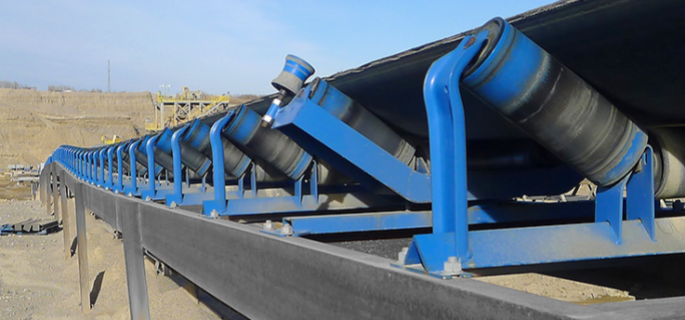
Conveyor Belt Running Alignment and Tracking
Proper alignment and tracking are crucial for the optimal running of a conveyor belt. Misalignment can lead to several issues, including belt damage, decreased efficiency, and increased maintenance costs.
Overview of Conveyor Belt Alignment Procedure
- Alignment Basics: Conveyor belt alignment involves adjusting the belt and the conveyor structure to ensure the belt runs straight and true. This process is essential to prevent the belt from drifting off to the sides.
- Procedure Steps: The alignment process typically includes checking and adjusting the idlers and pulleys to ensure they are perfectly perpendicular to the belt’s path. It also involves ensuring that the conveyor frame is level and square.
- PDF Resource: A detailed PDF guide on conveyor belt alignment procedures can be a valuable resource for maintenance personnel. This guide would offer step-by-step instructions, diagrams, and tips for effective alignment.
Detailed Conveyor Belt Tracking Diagram
- Visual Guide: A conveyor belt tracking diagram visually represents how to correctly align and track a conveyor belt. It shows the correct positioning of rollers, idlers, and other components.
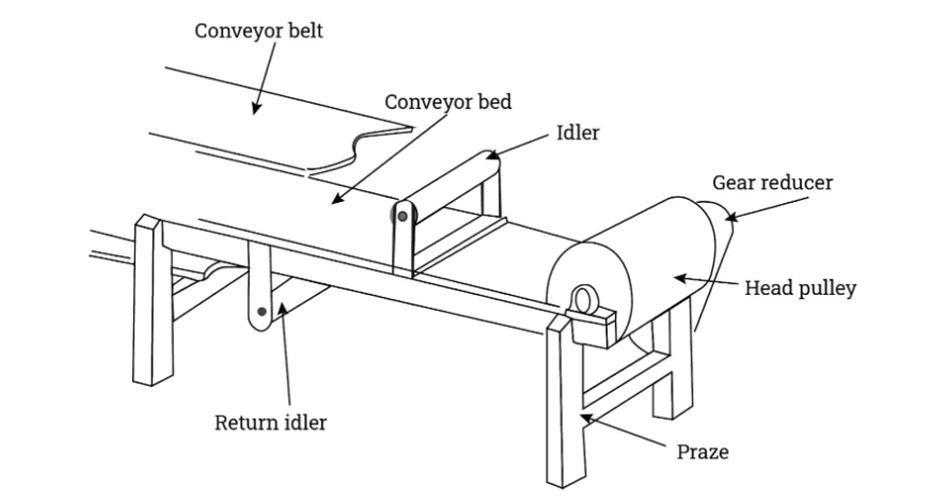
- Key Points: The diagram highlights critical areas to monitor, such as the edges of the belt and the contact points with rollers.
Step-by-Step Guide on Conveyor Belt Tracking Methods
- Tracking Techniques: The guide would detail methods to adjust the belt’s path, such as adjusting the tension or angling the idlers.
- Troubleshooting Tips: It would also include troubleshooting tips for common tracking problems, like belt misalignment or uneven wear.
Troubleshooting Common Conveyor Belt Tracking Issues
- Problem Identification: This involves identifying common issues like belt slipping, irregular wear, or drift.
- Solution Strategies: The section would provide strategies to rectify these issues, ensuring the belt runs smoothly and efficiently.
Effective alignment and tracking are vital for the longevity and performance of conveyor belt running, making this knowledge essential for those managing and maintaining conveyor belt systems.
Get the perfect conveyor belts for your needs. Contact us now!
Re-conveyor Belt Running to One Side
When a conveyor belt runs to one side, it can cause a host of operational issues. Here are some steps to troubleshoot and correct a conveyor belt that is running off-center:
1. Check for Obstructions and Debris
- Inspect the Belt Path:
- Ensure there is no debris or material build-up along the belt path that might be pushing the belt to one side.
- Clean Pulleys and Rollers:
- Remove any dirt or debris from pulleys and rollers, as this can cause misalignment.
2. Verify and Adjust Belt Tension
- Check Tension Uniformity:
- Ensure that the belt tension is even across its width. Unequal tension can cause the belt to track to one side.
- Adjust Tension:
- Use the tensioning device to make small, incremental adjustments. Tighten or loosen the belt on one side as needed to correct its path.
3. Align Pulleys and Rollers
- Inspect Alignment:
- Check that all pulleys and rollers are properly aligned and parallel to the conveyor frame.
- Adjust Pulleys:
- Make slight adjustments to the position of the pulleys, especially the end pulleys, to correct the belt’s tracking.
- Loosen the pulley mounting bolts and shift the pulley in small increments. Tighten the bolts and observe the belt tracking.
4. Correct Conveyor Frame Alignment
- Ensure Frame Squareness:
- Verify that the conveyor frame is level and square. Use a carpenter’s level and measuring tape to check for squareness.
- Adjust Frame:
- If the frame is out of alignment, make necessary adjustments to square it up. This might involve adjusting support structures or frame components.
5. Check Load Distribution
- Even Loading:
- Ensure that the load is evenly distributed on the belt. Uneven loading can cause the belt to drift to one side.
- Loading Position:
- Place the load in the center of the belt to maintain balance and avoid skewing.
6. Inspect and Adjust Tracking Devices
- Tracking Idlers:
- Some conveyor systems have tracking idlers or guide rollers that help keep the belt centered. Inspect these devices to ensure they are functioning correctly.
- Guide Rollers:
- Adjust the position of guide rollers to steer the belt back to the center.
By systematically addressing these areas, you can identify and correct the cause of a conveyor belt running to one side, ensuring smooth and efficient operation.
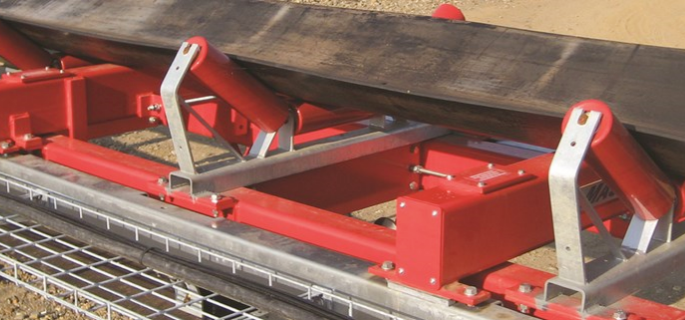
3 Easy Steps to Repairing Conveyor Belt Tracking
Repairing conveyor belt tracking involves ensuring that the belt runs straight and true along the conveyor system. Here are three easy steps to help you repair conveyor belt tracking:
1. Inspect the Conveyor System
- Check for Obstructions and Debris:
- Remove any material or debris that might be causing misalignment.
- Inspect Pulleys and Rollers:
- Ensure that all pulleys and rollers are free from damage and properly aligned.
- Assess Belt Condition:
- Look for wear, tear, or damage on the belt itself, which could be affecting its tracking.
2. Adjust the Conveyor Belt
- Tension Adjustment:
- Check and adjust the tension on both sides of the conveyor belt. Unequal tension can cause the belt to track improperly.
- Use a tensioning tool to ensure even tension across the belt.
- Tracking Adjustment:
- Locate the tracking adjustment screws on the conveyor system, typically found near the end pulleys.
- Make small incremental adjustments to the screws, tightening or loosening as necessary to correct the belt’s path.
- Run the conveyor belt at a slow speed and observe the tracking, making further adjustments as needed.
3. Realign Conveyor Components
- Align Pulleys and Rollers:
- Use a straight edge or a laser alignment tool to check that all pulleys and rollers are parallel and properly aligned with the conveyor frame.
- Adjust the position of pulleys and rollers as needed to ensure they are in the correct alignment.
- Check Frame Alignment:
- Ensure the conveyor frame is level and square. An uneven frame can cause tracking issues.
- Make necessary adjustments to the frame to achieve proper alignment.
By following these steps, you can effectively repair conveyor belt tracking and maintain optimal performance of your conveyor system.
Advanced Conveyor Belt Running Tracking Solutions
As conveyor technology advances, so do the methods and systems used for ensuring optimal belt tracking. Advanced solutions can significantly reduce the need for manual adjustments and increase overall system efficiency.
Introduction to Advanced Conveyor Belt Tracking Systems
- Automatic Tracking: Modern conveyor systems often include automatic tracking features that continuously monitor and adjust the belt’s position. These systems use sensors and control mechanisms to maintain alignment.
- Benefits: Automatic tracking reduces the need for manual intervention, lowers maintenance costs, and increases the lifespan of the belt.
Discussion on the Role of Conveyor Belt Tracking Rollers
- Functionality: Tracking rollers are specially designed to maintain the belt’s alignment. They can pivot and tilt to guide the belt back to its central path if it starts to drift.
- Design Variations: There are various designs of tracking rollers, each suited to different types of conveyor systems and belt materials.
Analysis of the Question: “Does a Belt Track to the Tight or Loose Side?”
- Tension’s Impact: The direction in which a belt tracks can be influenced by its tension. Typically, a conveyor belt will tend to track towards the tighter side.
- Adjustment Implications: Understanding this behavior is crucial for making accurate adjustments to the belt’s tension and alignment.
Advanced tracking solutions represent a significant step forward in conveyor belt technology, offering more reliable and efficient ways to ensure smooth conveyor belt running.
Practical Insights from Industry Experts
Gaining insights from industry experts can significantly enhance understanding and management of conveyor belt systems. This section delves into expert advice and real-world applications.
Insights from Span Tech’s Guide on Manual Conveyor Belt Tracking
- Expert Techniques: Span Tech’s guide offers valuable techniques for manually tracking conveyor belts, emphasizing the importance of regular inspections and precise adjustments.
- Best Practices: It includes best practices for maintaining belt alignment, such as routine checks of idler alignment and ensuring load distribution is even.
Overview of Kana Electromechs’ Belt Sway Switches
- Safety and Alignment: Kana Electromechs’ Belt Sway Switches play a crucial role in ensuring conveyor belt safety and proper alignment. These switches are designed to detect and correct belt sway, preventing potential accidents and material spillage.
- Application and Functionality: The switches are typically installed on both sides of the conveyor belt and help in maintaining the belt’s alignment by detecting deviations and signaling for corrective action.
Real-World Examples and Case Studies of Conveyor Belt Running and Tracking
- Industry Applications: This section would present case studies from various industries, showcasing challenges and solutions in conveyor belt tracking.
- Learning from Experience: Real-world examples provide practical insights into the complexities of conveyor belt running and the effectiveness of different tracking strategies.
Practical insights from industry experts and real-world examples are invaluable for understanding the nuances of conveyor belt running and implementing effective tracking solutions.
Maintenance and Regular Checks of Conveyor Belt Running
Regular maintenance and checks are essential for the smooth operation of conveyor belts. This section outlines the importance of maintenance and provides a checklist for routine inspections.
Importance of Regular Maintenance
- Preventing Downtime: Regular maintenance helps in early identification and resolution of potential issues, preventing unexpected downtime.
- Extending Belt Life: Consistent checks and maintenance extend the life of the conveyor belt and reduce the need for costly repairs or replacements.
Checklist for Routine Conveyor Belt Inspections and Maintenance
- Visual Inspections: Regular visual checks for signs of wear, tear, or damage on the belt, idlers, and pulleys.
- Alignment Checks: Ensuring the belt is properly aligned and tracking correctly.
- Tension Adjustments: Regularly checking and adjusting the belt’s tension to prevent slippage and misalignment.
- Lubrication and Cleaning: Keeping the conveyor components lubricated and clean to ensure smooth operation.
- Record Keeping: Maintaining a log of inspections and maintenance activities for future reference and compliance.
Regular maintenance is not just about fixing problems; it’s about proactively managing the conveyor system to ensure optimal performance and longevity of the conveyor belt.
This comprehensive approach to understanding and managing conveyor belt running encompasses everything from basic concepts to advanced technologies and practical insights, providing a valuable resource for anyone involved in conveyor system operation and maintenance.
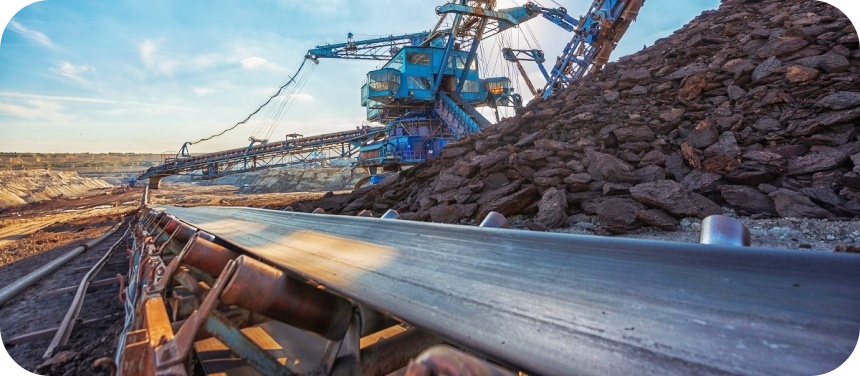
FAQs about Conveyor Belt Running
Conveyor belts are typically driven by electric motors or engines. The motor powers a drive pulley, which in turn moves the conveyor belt. The belt is often looped over additional pulleys, known as idlers or rollers, which help to maintain its tension and guide its path. The friction between the belt and the drive pulley ensures that when the pulley rotates, the belt moves along with it, thus transporting materials placed on the belt from one location to another.
Conveyor belt tracking refers to the method of managing and aligning the conveyor belt on its path. Proper tracking ensures that the belt runs straight and true on the conveyor system. It involves adjusting the conveyor structure, idlers, rollers, and other components to ensure the belt remains centered and does not drift off to one side. Misalignment can lead to belt damage, inefficient operation, and safety hazards.
Conveyor belt sway, also known as belt misalignment or drift, occurs when the belt shifts from its intended path. This can happen due to uneven loading of materials, worn or improperly aligned rollers and idlers, or issues with the belt tension. Belt sway can cause material spillage, increased wear and tear on the belt, and potential damage to the conveyor structure. It’s important to address belt sway promptly to maintain safe and efficient conveyor operation.
Conveyor belts are typically driven in one of the following ways:
Motor-Driven Pulleys: The most common method, where an electric motor is connected to a pulley. The motor’s rotation is transferred to the pulley, which moves the belt.
Chain Drive: In some systems, a chain is used to link a motor or gearbox to the conveyor’s drive pulley.
Direct Drive: Here, the motor is directly connected to the drive pulley, providing more efficient power transfer.
Hydraulic or Pneumatic Systems: In specific applications, hydraulic motors or pneumatic systems can be used to drive the conveyor belt, especially where electrical power is not suitable or available.
To get a conveyor belt to run straight, follow these steps:
Ensure Proper Alignment: Align all pulleys, rollers, and the conveyor frame to ensure they are parallel and square.
Adjust Belt Tension: Check that the belt tension is even across its width and make small, incremental adjustments to correct any misalignment.
Use Tracking Devices: Utilize tracking idlers or guide rollers to help keep the belt centered.
Load Evenly: Ensure the load is evenly distributed and placed centrally on the belt to avoid skewing.
Regular Maintenance: Perform regular inspections and maintenance to remove debris and check for wear and tear that could affect alignment.
Several factors can cause a conveyor belt to run off-center:
Misaligned Pulleys or Rollers: If the pulleys or rollers are not aligned properly, the belt will not run straight.
Uneven Belt Tension: Unequal tension across the width of the belt can cause it to track to one side.
Debris or Build-Up: Dirt, debris, or material build-up on pulleys, rollers, or the belt can cause misalignment.
Uneven Load Distribution: If the load is not evenly distributed or placed centrally, it can cause the belt to run off-center.
Frame Misalignment: A conveyor frame that is not level or square can lead to tracking issues.
Belt conveyor speeds can vary widely depending on the application and industry, but common speeds range from 0.5 meters per second (m/s) to 5 meters per second (m/s). Some high-speed conveyors can run at speeds exceeding 7 meters per second (m/s), while slower conveyors may operate below 0.5 meters per second (m/s).
If a conveyor belt runs out in the middle, it can be due to:
Belt Stretching: Uneven belt stretching or elongation can cause the belt to wander.
Load Impact: Sudden or uneven loading in the middle of the belt can cause misalignment.
Wear and Tear: Worn-out components, such as rollers or idlers, in the middle section can lead to the belt running out.
Poor Splicing: Incorrect or poor-quality splicing of the belt can cause uneven tension and tracking issues.
Last Updated on July 31, 2024 by Jordan Smith
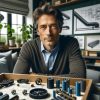
Jordan Smith, a seasoned professional with over 20 years of experience in the conveyor system industry. Jordan’s expertise lies in providing comprehensive solutions for conveyor rollers, belts, and accessories, catering to a wide range of industrial needs. From initial design and configuration to installation and meticulous troubleshooting, Jordan is adept at handling all aspects of conveyor system management. Whether you’re looking to upgrade your production line with efficient conveyor belts, require custom conveyor rollers for specific operations, or need expert advice on selecting the right conveyor accessories for your facility, Jordan is your reliable consultant. For any inquiries or assistance with conveyor system optimization, Jordan is available to share his wealth of knowledge and experience. Feel free to reach out at any time for professional guidance on all matters related to conveyor rollers, belts, and accessories.