Bulk Conveyor Belt – Bulk Material Handling
Bulk conveyor belt is essential components in the material handling sector, designed to transport large volumes of bulk materials such as sand, gravel, coal, and minerals over both short and long distances. These belts play a crucial role in industries ranging from mining and construction to agriculture and manufacturing, enabling efficient and continuous movement of raw materials and finished products. The term “bulk” in this context refers to materials that are handled in large quantities at a time, often in loose form. The ability of bulk conveyor belts to move substantial amounts of material efficiently not only optimizes production processes but also significantly reduces labor costs and increases safety by minimizing manual handling of potentially hazardous materials.
The Evolution of Bulk Conveyor Belt Technology
The development of bulk conveyor belt technology is a fascinating journey that showcases human innovation and the drive to optimize industrial processes. This evolution has transformed the way materials are moved in various sectors, making operations more efficient, safer, and less labor-intensive.
Key Innovations in Bulk Conveyor Belt Technology
- The Inception of Conveyor Belts: The earliest conveyor belts were simple and made from leather, canvas, or rubber, moving over a flat wooden bed. This basic concept was revolutionary in moving goods more efficiently than manual labor.
- Introduction of Synthetic Materials: The 1920s and 1930s saw the introduction of synthetic materials like nylon and polyester, which offered enhanced strength, flexibility, and resistance to water and chemicals, significantly improving the durability and efficiency of conveyor belts.
- Steel Cord Conveyor Belts: By the 1940s, steel cord conveyor belts were developed, providing the strength needed to transport heavy loads over long distances. This innovation was crucial for the mining and quarrying industries, where bulk materials needed to be moved from deep within the earth.
- Automated Conveyor Systems: The 1950s and 1960s introduced automation into conveyor systems, with belts now being able to start, stop, and control the speed automatically. This period also saw the advent of the first computer-controlled conveyor systems, marking the beginning of modern bulk material handling.
- Energy Efficiency and Sustainability: The late 20th and early 21st centuries have focused on making conveyor belts more energy-efficient and environmentally friendly. Innovations include the use of renewable materials, low-friction rollers, and systems designed to minimize energy consumption while maximizing productivity.
- Smart Conveyor Technologies: Today, the integration of IoT (Internet of Things) technologies, sensors, and real-time data analytics into bulk conveyor belt systems allows for unprecedented monitoring and optimization. These smart systems can predict maintenance needs, adjust speeds based on load requirements, and even integrate with other automated systems for seamless operations.
BEUMER Group: A Pioneer in Conveyor Technology
The BEUMER Group stands as a testament to the evolution of bulk conveyor belt technology. With nearly 90 years of experience, BEUMER has been at the forefront of this technological journey, pioneering many of the advancements that have become standard in the industry today. From their early work in developing robust belt systems for conveyor belt bulk material handling to their current innovations in automated and sustainable conveyor solutions, BEUMER Group’s history reflects the broader trends and technological advancements in conveyor belt technology.
Their commitment to innovation, quality, and customer service has made them a leader in the design and manufacture of conveyor systems that meet the complex and varied needs of industries worldwide. The BEUMER Group’s ongoing research and development efforts ensure that bulk conveyor belt technology will continue to evolve, offering more efficient, reliable, and sustainable solutions for material handling challenges.
The evolution of bulk conveyor belt technology is a clear indicator of how continuous innovation can lead to significant improvements in industrial operations. As we look to the future, the potential for further advancements in conveyor technology promises even greater efficiency and sustainability in the movement of bulk materials.
Types of Bulk Conveyor Belts
The advancement in bulk conveyor belt technology has significantly contributed to the efficiency of material handling across various industries. Below is a detailed overview of the types of bulk conveyor belts, highlighting their characteristics and applications in a structured format.
Each type of bulk conveyor belt offers unique benefits tailored to specific material handling needs, ensuring that industries can choose the most efficient and effective solution for their operations. The evolution of conveyor belt technology, particularly in the realm of bulk materials, underscores the ongoing innovations aimed at improving productivity, safety, and environmental sustainability in material handling processes.
Usage Suggestions for Different Types of Conveyor Belts
When selecting and utilizing the various types of bulk conveyor belts, considering their unique characteristics and applications is crucial for optimizing efficiency and safety in material handling. Here are six key points to guide the usage of these conveyor belts effectively:
- Assess Material Characteristics: Before choosing a conveyor belt, evaluate the physical and chemical properties of the material to be transported, including weight, size, abrasiveness, and corrosiveness. This assessment will help in selecting a belt that is best suited for the material’s nature, ensuring durability and reducing maintenance needs.
- Consider Environmental Conditions: The operating environment plays a significant role in selecting the appropriate type of conveyor belt. For outdoor operations or in areas with extreme temperatures, heavy-duty conveyor belts with high resistance to weather conditions are preferable. In contrast, enclosed systems like tube belt conveyors are ideal for indoor or sensitive environments where material containment is crucial.
- Evaluate Space Constraints: Space availability can significantly influence the choice of conveyor belt. Flexible wall belt conveyors, which can transport materials at steep inclines or declines, are suitable for tight spaces or when vertical transport is required, minimizing the system’s footprint.
- Determine Load Capacity and Distance: The volume and weight of the material to be transported, along with the distance over which it needs to be moved, are critical factors in selecting a conveyor belt. Heavy-duty and trough belt conveyors are well-suited for moving large volumes of heavy materials over long distances, while tube and pipe conveyors are ideal for longer distances where material protection is necessary.
- Understand Maintenance and Operational Requirements: Each type of conveyor belt has specific maintenance needs and operational requirements. For instance, heavy-duty belts may require regular inspections for wear and tear, while tube belt conveyors might need additional checks to ensure the enclosed system remains sealed and intact.
- Compliance with Safety and Environmental Regulations: Ensure that the chosen conveyor belt system complies with all relevant safety and environmental regulations. Enclosed systems like tube belt conveyors offer advantages in terms of reducing dust emissions and spillage, contributing to a safer and more environmentally friendly operation.
By carefully considering these points, businesses can make informed decisions about the most appropriate type of bulk conveyor belt for their specific needs, leading to improved operational efficiency, safety, and cost-effectiveness in material handling processes.
The Size of Bulk Conveyor Belts
Bulk conveyor belts come in various sizes to accommodate different material handling needs across industries. The size of a conveyor belt can be defined by its width, length, thickness, and other dimensions, all of which are tailored to specific applications and load requirements.Bulk conveyor belt Continuous conveying of bulk materials at high rates. widths ranging from 18 inches (450 mm) to 72 inches (1800 mm). thicknesses typically range from 1/4 inch (6 mm) to 1 inch (25 mm) or more.
Width
- Standard Widths: Conveyor belts are commonly available in standard widths ranging from 18 inches (450 mm) to 72 inches (1800 mm). Some specialized applications may require belts with widths up to 96 inches (2400 mm) or more.
- Selection Criteria: The width is chosen based on the type of material being transported and the volume of material flow. Wider belts are used for larger, bulkier materials, while narrower belts are suitable for smaller, more compact items.
Length
- Variable Lengths: Conveyor belt lengths can vary significantly depending on the distance materials need to be transported. They can be as short as a few feet for localized material handling or extend to several miles for long-distance transportation.
- Custom Lengths: Many manufacturers offer custom belt lengths to meet specific operational requirements, ensuring efficient material transport over the desired distance.
Thickness
- Common Thicknesses: Conveyor belt thicknesses typically range from 1/4 inch (6 mm) to 1 inch (25 mm) or more. The thickness is determined by the belt’s construction and the materials used, such as rubber, PVC, or fabric reinforcements.
- Application-Dependent: Thicker belts are designed for heavy-duty applications where they must withstand higher loads and abrasive materials, while thinner belts are used for lighter-duty applications.
Additional Dimensions
- Edge Types: Conveyor belts may have different edge types, such as cut or molded edges, to suit specific operational environments and reduce the risk of fraying.
- Profiles and Cleats: Some bulk conveyor belts feature profiles or cleats to prevent material slippage and ensure efficient transport on inclined or declined surfaces.
Customization
- Tailored Solutions: Conveyor belt sizes can be customized to fit unique industrial needs, including specific widths, lengths, and thicknesses. Manufacturers work closely with clients to design and produce belts that meet exact specifications.
- Special Features: Custom belts may also include additional features such as heat resistance, oil resistance, anti-static properties, and other characteristics to enhance performance in specific conditions.
The size of bulk conveyor belts is a critical factor in ensuring efficient material handling across various industries. By understanding the specific requirements of the application, including material type, load capacity, and operational environment, appropriate belt dimensions can be selected or customized to optimize performance and reliability.
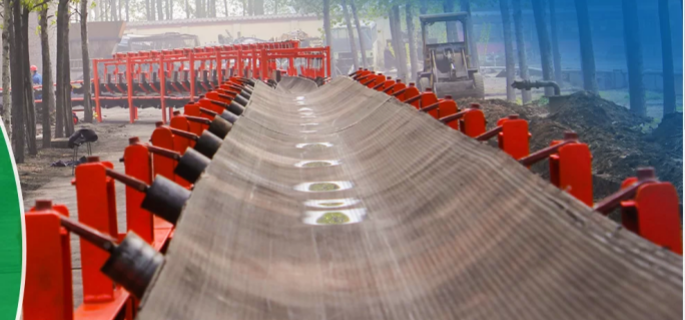
Key Manufacturers and Brands of Bulk Conveyor Belts
The bulk conveyor belt industry is characterized by its innovative and diverse range of manufacturers, each contributing unique technologies and solutions to the field. These companies are pivotal in driving forward the capabilities and applications of bulk conveyor belts across various industries.
GRAM Conveyor
Overview: A leading manufacturer of conveyor belts with a strong reputation for quality and innovation.
Unique Features:Known for their durability and performance, including specialized belts for high-temperature and oil-resistant applications.Provides high-performance belts designed for maximum durability and efficiency.Used in mining, construction, and material handling.
BEUMER Group
Overview: The BEUMER Group is a global leader in the design and manufacture of advanced bulk conveyor belt systems. With a rich history spanning nearly 90 years, BEUMER has established itself as a provider of sophisticated material handling solutions, including pipe conveyors, troughed belt conveyors, and high-capacity loading systems.
Unique Features: BEUMER’s pipe conveyor system exemplifies their innovation, offering an enclosed transport solution that significantly reduces environmental impact and protects the conveyed material from external elements. Their commitment to sustainability and efficiency is evident in their continuous pursuit of energy-efficient designs and eco-friendly materials.
Kase Conveyors
Overview: Specializing in custom-engineered belt conveyors for bulk material handling, Kase Conveyors offers a wide array of solutions tailored to meet specific operational needs. Their expertise extends to various conveyor types, including screw conveyors and bucket elevators.
Unique Features: What sets Kase Conveyors apart is their dedication to customization. They excel in designing conveyors that fit unique material handling requirements, ensuring optimal performance and reliability. Their ability to adapt and innovate according to customer needs makes them a valuable partner in the bulk material handling sector.
Continental Conveyor
Overview: Continental Conveyor stands out for its comprehensive range of bulk material handling equipment. Their product lineup includes belt conveyors, screw conveyors, and a variety of conveyor components, making them a one-stop-shop for conveyor solutions.
What Sets Them Apart: Continental’s dedication to quality and customer service has cemented their position in the market. Their products are designed with reliability and durability in mind, catering to a broad spectrum of industrial applications.
Fenner Dunlop
Overview: As a leading name in the conveyor belting industry, Fenner Dunlop specializes in producing high-quality conveyor belts for mining and industrial applications. Their focus on safety and performance is unparalleled, offering belts that meet the highest standards of fire resistance and anti-static properties.
What Sets Them Apart: Fenner Dunlop’s commitment to safety and innovation is evident in their development of fire-resistant and anti-static belts, addressing the critical safety needs of the mining industry. Their belts are engineered to perform in the most challenging environments, ensuring operational safety and efficiency.
Martin Engineering
Overview: Martin Engineering is renowned for its bulk material handling solutions that enhance the efficiency and safety of conveyor systems. Their product range includes innovative conveyor belt cleaning systems and dust management technologies.
What Sets Them Apart: The company’s focus on solving common conveyor system challenges, such as spillage and dust control, through innovative solutions, sets them apart. Martin Engineering’s products are designed to improve the operational environment, reduce maintenance costs, and increase system longevity.
Flexco
Overview: Flexco provides a broad selection of conveyor belt maintenance tools and products designed to maximize productivity and minimize downtime in conveyor systems. Their offerings include belt fastening solutions, belt maintenance tools, and conveyor accessories.
What Sets Them Apart: Flexco’s strength lies in their comprehensive range of maintenance solutions that ensure conveyor belts operate smoothly and efficiently. Their focus on developing products that simplify the maintenance process, from belt splicing to cleaning and tracking, demonstrates their commitment to operational excellence.
These key manufacturers and brands have significantly shaped the bulk conveyor belt industry through their commitment to innovation, quality, and customer service. Their contributions have not only advanced the technology behind bulk conveyor belts but have also broadened the scope of their applications, making bulk material handling more efficient, safe, and sustainable.
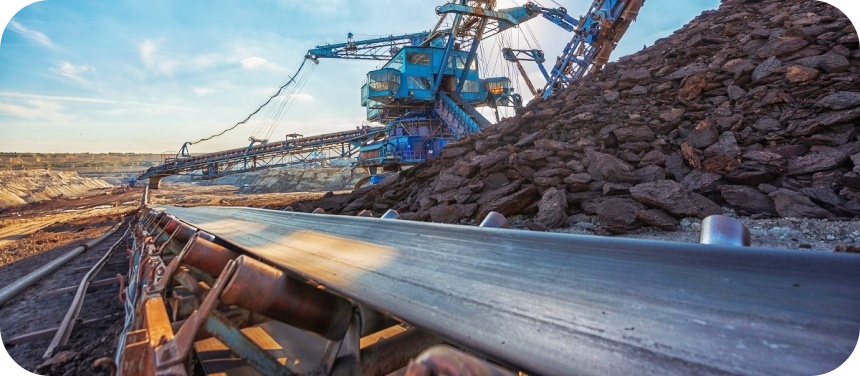
Design and Features of Bulk Conveyor Belts
The design and features of bulk conveyor belts are critical to their performance, durability, and suitability for various industrial applications. These belts are engineered to transport bulk materials efficiently over both short and long distances, catering to industries such as mining, agriculture, construction, and many others. Understanding the material and construction, special features, and customization options of bulk belt conveyor is essential for selecting the right conveyor system.
Key Components
- Belt: Made of durable materials like rubber or PVC, it is designed to withstand the weight and abrasive nature of bulk materials.
- Pulleys: These include drive pulleys, which power the belt, and idler pulleys, which support and guide it.
- Drive System: Consists of motors and gears that provide the necessary power to move the belt.
- Support Structure: Includes frames and rollers that hold the belt in place and ensure smooth operation.
Material and Construction
Innovations in Bulk Conveyor Belt Technology: A Closer Look
- 2 Ply and Poly/Nylon Materials: Bulk conveyor belts are often constructed from multiple layers, or plies, of material that provide strength and flexibility. A common configuration is the 2 Ply construction, which consists of two layers of fabric bonded together. Poly/Nylon materials combine polyester fabric in the warp (lengthwise) direction for strength and nylon fabric in the weft (widthwise) direction for flexibility. This combination offers excellent resistance to abrasion and tearing, making it suitable for handling rough materials.
- Other Materials Used: Besides Poly/Nylon, other materials such as steel cords are used for added strength in heavy-duty applications. Rubber covers are applied to protect the belt’s carcass and provide the necessary grip on the material being transported. The choice of cover material, including natural rubber, SBR, and specialized compounds, is determined by the belt’s intended use and the properties of the material being handled.
Special Features
- Abrasion-Resistant Belting: To extend the life of bulk conveyor belts, especially in applications involving sharp or abrasive materials, belts with high abrasion resistance are used. These belts are designed to withstand wear and tear, reducing the need for frequent replacements.
- Heavy-Duty Idlers: Supporting the conveyor belt and the material carried on it, heavy-duty idlers are designed to endure the weight and impact of bulk materials. They are constructed from durable materials and often feature anti-friction bearings to reduce wear and extend service life.
- Dust-Tight Construction: For applications where dust emission is a concern, such as in food processing or chemical industries, bulk conveyor belts can be designed with dust-tight constructions. This feature minimizes the escape of dust and protects the material from contamination.
- High Torque Drive Units: To ensure the efficient movement of bulk materials, especially over inclines or long distances, conveyor systems are equipped with high torque drive units. These units provide the necessary power to maintain belt speed under varying load conditions.
- Speed and Capacity: Bulk conveyor belts are designed to handle high speeds and large volumes of materials, enhancing productivity.
- Automation: Many conveyor systems are integrated with automation technologies, enabling precise control and monitoring.
- Versatility: These belts can transport a wide range of materials, from fine powders to large rocks, making them versatile for various applications.
Customization and Configuration
- Tailoring to Industrial Needs: Bulk belt conveyor can be customized in various ways to meet specific operational requirements. This includes adjusting the belt width, length, and speed, as well as selecting the appropriate belt material and cover type based on the material being transported.
- Application-Specific Configurations: Depending on the application, conveyor belts can be configured with special features such as sidewalls for containing material, cleats for incline conveying, and impact beds to absorb shock at loading points. The ability to customize these aspects of the conveyor belt ensures that the system is optimized for the specific needs of each industrial application.
- Safety Features: Safety is paramount in all industrial applications. Customization options such as emergency stop systems, guardrails, and safety switches can be integrated into the conveyor system design to protect workers and the materials being transported. Additionally, features like anti-slip surfaces and fire-resistant materials can further enhance safety.
- Integration with Other Systems: For optimal efficiency, bulk conveyor belts can be designed to integrate seamlessly with other material handling systems and processes within the facility. This includes synchronization with automated loading and unloading systems, sorting systems, and data management platforms to ensure a cohesive and efficient operation.
The design and features of bulk conveyor belt are integral to their functionality and efficiency in transporting materials across diverse industries. By carefully selecting the material and construction, incorporating special features, and tailoring the belt to specific industrial needs, businesses can achieve optimal material handling solutions that enhance productivity and safety.
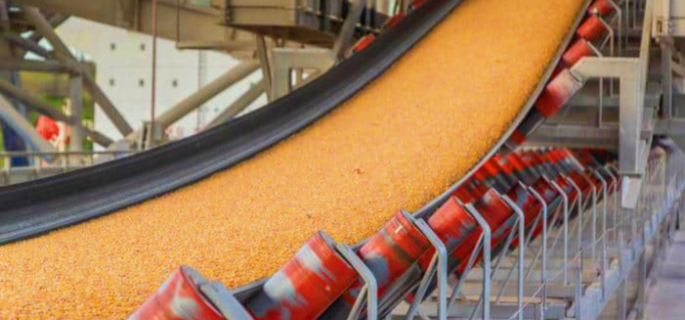
Advantages of Belt Conveyors for Bulk Material
Efficiency
Belt conveyors can move large quantities of materials quickly and efficiently. They are capable of handling high capacities and long distances, making them ideal for bulk material transportation.
Cost-Effectiveness
Belt conveyors offer a cost-effective solution for bulk material handling. They require minimal maintenance and have lower operational costs compared to other transport methods.
Versatility
Belt conveyors are highly versatile and can be adapted to different types of materials and operational requirements. They can be customized with various features like variable speed drives, automation, and safety mechanisms.
Safety
Belt conveyors are designed with safety in mind. They can be equipped with emergency stop switches, guards, and other safety features to protect workers and prevent accidents.
Used Bulk Conveyor Belts: Pros and Cons
Opting for used bulk conveyor belts can be a cost-effective solution for many industries. However, it’s essential to weigh the advantages and disadvantages before making a decision. Here’s a detailed examination of the viability of choosing used conveyor belts, along with tips on what to look for and potential pitfalls to avoid.
Viability of Opting for Used Conveyor Belts
Pros:
- Cost Savings: The most apparent advantage of purchasing used bulk conveyor belts is the significant cost savings compared to buying new equipment. This can be particularly beneficial for small to medium-sized operations or for companies in the startup phase.
- Environmental Sustainability: Choosing used conveyor belts contributes to environmental sustainability by recycling and reusing materials, thereby reducing waste and the demand for new raw materials.
- Quick Availability: Used conveyor belts are often available for immediate purchase and installation, unlike new belts that may require a lead time for manufacturing and delivery.
- Proven Performance: A used conveyor belt that has been well-maintained can offer proven performance and reliability, especially if it comes from a reputable source that has ensured its condition and suitability for further use.
- Flexibility in Application: Used belts may offer more flexibility for customization and adaptation to specific needs, as they can be modified or repurposed without the concern of voiding warranties or altering original specifications.
- Opportunity for Upgrades: The savings realized from purchasing used equipment can be allocated towards upgrades or enhancements to the conveyor system, potentially increasing efficiency or extending its service life.
Cons:
- Wear and Tear: Used conveyor belts have experienced wear and tear, which may reduce their lifespan and efficiency compared to new belts. This can lead to increased maintenance costs and downtime.
- Limited Warranty: Unlike new equipment, used conveyor belts typically come with limited or no warranty, increasing the risk if the belt fails or does not perform as expected.
- Compatibility Issues: There may be challenges in integrating used conveyor belts with existing systems or machinery due to differences in specifications, technology, or design.
- Hidden Defects: Used belts may have hidden defects or damage that is not immediately apparent, potentially leading to unexpected failures or the need for repairs.
- Lack of Documentation: There may be a lack of comprehensive documentation or history of maintenance and repairs, making it difficult to assess the belt’s condition accurately.
Tips on What to Look For and Potential Pitfalls
- Inspect for Physical Damage: Carefully inspect the used bulk conveyor belt for signs of wear, such as cracks, cuts, or fraying edges, which could indicate deeper issues.
- Verify Age and Usage: Obtain as much information as possible about the belt’s age, history of use, and maintenance records to gauge its condition and remaining lifespan.
- Assess Compatibility: Ensure that the belt’s specifications, such as width, length, and material, are compatible with your existing system and the materials you intend to transport.
- Consider Retrofitting Costs: Evaluate the cost of any necessary modifications or retrofitting to make the used belt suitable for your application, as this can impact the overall cost-effectiveness.
- Check for Environmental Exposure: Determine if the belt has been exposed to harsh environmental conditions, such as chemicals or extreme temperatures, which could affect its integrity.
- Seek Professional Evaluation: If possible, have a professional inspect the belt to assess its condition and suitability for your needs.
- Negotiate a Return Policy: Try to negotiate a return policy or warranty with the seller to mitigate risks in case the belt does not meet expectations.
- Beware of Too-Good-To-Be-True Deals: Extremely low prices may indicate potential issues with the belt’s condition. Thorough due diligence is essential to avoid costly mistakes.
Choosing a used bulk conveyor belt can offer significant advantages, particularly in terms of cost savings and environmental sustainability. However, it’s crucial to conduct thorough research and evaluation to ensure that the belt meets your operational needs and offers reliable performance.

Installation and Maintenance of Bulk Conveyor Belts
Proper installation and maintenance are crucial for the longevity and efficiency of bulk conveyor belts. These processes ensure that the conveyor system operates smoothly, minimizing downtime and extending the life of the belt. Here are some basic guidelines for installing bulk conveyor belts, followed by maintenance tips to keep them running efficiently.
Installation Guidelines for Bulk Conveyor Belts
- Pre-Installation Checks: Before installation, inspect the conveyor frame and idlers to ensure they are level and aligned. Any structural issues should be corrected to prevent problems with belt tracking and tension.
- Unroll and Precondition the Belt: Unroll the new belt alongside the conveyor structure and let it rest to eliminate any twists or curls that occurred during shipping. This helps in easier handling and installation.
- Square the Belt Ends: Ensure the ends of the belt are cut square to each other. Misaligned ends can lead to tracking issues and uneven wear on the belt edges.
- Install the Belt: Position the belt over the conveyor structure, starting at the tail end. Use a cable or a suitable mechanism to pull the belt onto the system. Ensure that the belt is fed onto the conveyor in the direction of belt travel.
- Splice the Belt: Once the belt is in place, splice the ends together. The splicing method—whether mechanical fasteners or vulcanization—depends on the belt type and application. Proper splicing is critical for the strength and durability of the conveyor belt.
- Tension the Belt: Adjust the belt tension according to the manufacturer’s specifications. Proper tension is essential for optimal performance and to prevent slippage and excessive wear.
Maintenance Tips for Bulk Conveyor Belts
- Regular Inspections: Conduct regular inspections of the bulk conveyor belt and its components. Look for signs of wear, damage, or misalignment. Early detection of issues can prevent costly repairs and downtime.
- Cleanliness: Keep the conveyor belt and the area around it clean. Accumulation of debris can cause the belt to misalign, and material buildup on rollers can lead to increased friction and wear.
- Lubrication: Ensure that all moving parts, especially rollers and pulleys, are adequately lubricated. This reduces wear and tear and keeps the conveyor running smoothly.
- Monitor Belt Tension: Periodically check and adjust the belt tension. Over-tensioning can lead to belt and bearing failures, while under-tensioning can cause slippage and misalignment.
- Track the Belt: Ensure that the conveyor belt is properly tracked and aligned. Misaligned belts can lead to uneven wear, increased energy consumption, and potential damage to the belt and conveyor structure.
- Scheduled Maintenance: Implement a scheduled maintenance program based on the manufacturer’s recommendations and the specific operating conditions. Scheduled maintenance should include replacing worn parts, checking and adjusting belt tension and alignment, and testing control systems.
By following these installation and maintenance guidelines, operators can ensure that their bulk conveyor belts operate efficiently and reliably, providing a long service life and minimizing operational costs. Proper care and attention to the conveyor system not only improve its performance but also enhance workplace safety.
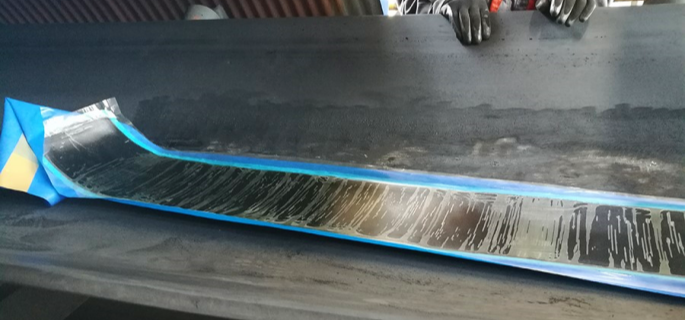
Future Trends in Conveyor Belt Technology
The landscape of bulk conveyor belt technology is poised for transformative changes, driven by innovation and a growing emphasis on sustainability. As industries continue to seek more efficient, reliable, and environmentally friendly material handling solutions, several key trends are emerging that will shape the future of conveyor belt technology.
Innovations on the Horizon
- Smart Conveyor Belts: The integration of IoT (Internet of Things) and AI (Artificial Intelligence) technologies into bulk conveyor belt systems is set to revolutionize how materials are transported. Smart conveyor belts equipped with sensors and monitoring devices will provide real-time data on belt health, material flow, and operational efficiency, enabling predictive maintenance and minimizing downtime.
- Energy-Efficient Designs: Future conveyor belts will prioritize energy efficiency, incorporating advanced materials and designs that reduce friction and energy consumption. Low-resistance belt materials and optimized drive systems will contribute to lower operational costs and a reduced carbon footprint.
- Advanced Materials: The development of new materials with enhanced properties—such as increased strength, durability, and resistance to extreme temperatures and chemicals—will allow conveyor belts to operate in more challenging environments and handle a wider range of materials.
- Modular and Flexible Systems: Modular conveyor belt designs that offer flexibility in configuration and scalability will become more prevalent. These systems can be easily adapted or expanded to meet changing operational needs, reducing the need for complete system overhauls.
- Increased Automation: Automation in conveyor belt systems will extend beyond smart monitoring, incorporating automated loading, unloading, and sorting processes. This will improve efficiency, accuracy, and safety in material handling operations.
- Wearable Technology for Maintenance: The use of wearable technology, such as AR (Augmented Reality) glasses for maintenance personnel, will facilitate quicker and more effective troubleshooting and repair of conveyor belt systems, further reducing downtime and enhancing productivity.
The Role of Sustainability in Future Conveyor Belt Manufacturing and Design
Sustainability will play a pivotal role in the evolution of bulk conveyor belt technology. Manufacturers and designers are increasingly focusing on creating products that are not only efficient and cost-effective but also environmentally responsible. This includes:
- Recyclable and Biodegradable Materials: The use of recyclable materials in the construction of conveyor belts, as well as the development of biodegradable belt materials, will help reduce waste and the environmental impact of conveyor system operations.
- Reduced Environmental Impact: Future designs will aim to minimize the environmental footprint of conveyor operations, focusing on reducing emissions, dust, and noise. This will be achieved through cleaner, more efficient drive systems and the use of dust suppression and noise reduction technologies.
- Lifecycle Management: Emphasis will be placed on the entire lifecycle of the conveyor belt, from design and manufacturing to operation and end-of-life recycling. This approach will ensure that environmental considerations are integrated at every stage, promoting sustainability throughout the conveyor belt’s lifecycle.
As the bulk conveyor belt industry moves forward, these trends highlight a shift towards smarter, more efficient, and sustainable material handling solutions. By embracing innovation and prioritizing environmental responsibility, the future of conveyor belt technology promises to meet the evolving needs of industries worldwide, driving productivity and sustainability in equal measure.
Your ideal conveyor belts await. Contact us for details!
FAQs about Bulk Conveyor Belt
The cost of a conveyor belt per foot can vary widely depending on the type, material, and specifications. Generally, a basic conveyor belt used in light-duty applications may cost around $1 to $5 per foot. For medium-duty belts, the price might range from $5 to $10 per foot. Heavy-duty conveyor belts, used in more demanding industrial applications, can cost between $10 and $20 per foot or even higher. Specialized belts, such as those with heat resistance, oil resistance, or unique materials like PVC or rubber, can increase the price further. It’s important to consider additional costs for accessories, installation, and maintenance when budgeting for a conveyor belt system. Consulting with suppliers and comparing quotes can help in finding the best deal for the specific needs of the application.
WA bulk conveyor is a type of conveyor system designed to transport large quantities of materials over long distances. These conveyors are commonly used in industries such as mining, agriculture, and construction, where they move materials like ores, coal, grains, and aggregates. The system typically consists of a continuous belt made from durable materials such as rubber or PVC, supported by rollers and driven by pulleys. Bulk conveyors are essential for improving efficiency and reducing manual labor in material handling processes. They can handle heavy loads and are capable of transporting materials in various forms, including powders, granules, and large chunks. Bulk conveyors are integral to operations where high-volume material transport is required, ensuring smooth and continuous flow within production lines or between different stages of processing.
Alternatives to conveyor belts include various material handling systems that can transport goods or materials efficiently. One common alternative is pneumatic conveying, which uses air pressure to move bulk materials through pipes. This method is ideal for handling powders and small granules. Another alternative is screw conveyors, which utilize a rotating helical screw blade to move materials within a tube or trough. Bucket elevators are used to vertically lift bulk materials and are suitable for applications where space is limited. Chain conveyors are another option, using a chain-driven system to transport heavy loads. Automated guided vehicles (AGVs) can transport materials along predefined paths without the need for fixed conveyors. These alternatives offer flexibility and can be tailored to specific industrial needs, providing efficient solutions for material handling.
Last Updated on June 21, 2024 by Jordan Smith
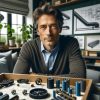
Jordan Smith, a seasoned professional with over 20 years of experience in the conveyor system industry. Jordan’s expertise lies in providing comprehensive solutions for conveyor rollers, belts, and accessories, catering to a wide range of industrial needs. From initial design and configuration to installation and meticulous troubleshooting, Jordan is adept at handling all aspects of conveyor system management. Whether you’re looking to upgrade your production line with efficient conveyor belts, require custom conveyor rollers for specific operations, or need expert advice on selecting the right conveyor accessories for your facility, Jordan is your reliable consultant. For any inquiries or assistance with conveyor system optimization, Jordan is available to share his wealth of knowledge and experience. Feel free to reach out at any time for professional guidance on all matters related to conveyor rollers, belts, and accessories.