Innovative Uses: Application of Belt Conveyor Across Sectors
Belt conveyors have become an indispensable part of modern industries, serving as the backbone for material handling across various sectors. These sophisticated systems, characterized by a long, continuous belt looped around a series of rollers, efficiently transport goods and materials from one point to another with minimal human intervention. Their significance cannot be overstated, as they enhance productivity, reduce labor costs, and improve safety in workplaces. This blog aims to delve into the application of belt conveyor systems, shedding light on their diverse applications that span from the intricate assembly lines of manufacturing plants to the rugged terrains of mining operations. We will explore the myriad advantages these systems offer and the different types available, providing a comprehensive understanding of their role in streamlining operations and fostering growth in today’s fast-paced industrial landscape.
To Explore the Application of Belt Conveyor Systems: Components and Mechanisms
Belt conveyors are integral to the seamless operation of various industrial sectors, offering a reliable method for transporting materials over short and long distances. The application of belt conveyor systems spans across numerous fields, from packaging and distribution to mining and construction, highlighting their versatility and critical role in enhancing efficiency and productivity. This section aims to dissect the fundamental mechanism and key components that constitute belt conveyors, providing insights into how they are tailored to meet the diverse requirements of their application.
The Basic Mechanism of Belt Conveyors
The fundamental operation of belt conveyors is elegantly simple, yet it underpins the efficiency of myriad industrial processes. Here’s a closer look at the mechanism that drives these indispensable systems:
- Looped Belt Configuration: At the heart of every conveyor is a looped belt, made from durable materials like rubber, fabric, or metal, designed to withstand the specific demands of its application. This belt forms a continuous loop that cycles between two or more pulleys.
- Drive Pulley System: One of the pulleys, known as the drive pulley, is connected to a motor. When the motor activates, it imparts rotational force to the pulley, which in turn moves the belt. This movement is the primary force that drives materials from one end of the conveyor to the other.
- Idler Pulleys: Positioned along the conveyor path, idler pulleys serve to guide and support the belt. They ensure the belt maintains a consistent path and tension, preventing sagging and misalignment, which are crucial for the smooth operation of the conveyor.
- Powered Movement: The application of belt conveyor systems relies on the powered movement provided by the drive pulley. This movement can be adjusted in speed to suit the specific needs of the materials being transported, whether they require rapid transport or a slower, more controlled movement to prevent damage.
- Material Transport: As the belt moves, it carries materials placed upon it from the loading point to the discharge point. The design of the belt surface—whether flat, textured, or fitted with cleats—helps in efficiently moving different types of materials, including those that are bulky, heavy, or might otherwise slip off a less suitable conveyor belt.
- Tensioning Mechanism: To ensure the belt operates smoothly, a tensioning mechanism is employed to keep the belt tight. Proper tension is essential to prevent slippage at the drive pulley and to ensure the belt moves evenly over the idler pulleys.
- Reversibility and Control: Modern belt conveyors are designed with controls that allow for reversibility, speed adjustment, and immediate stoppage in case of an emergency. These features enhance the versatility and safety of belt conveyor systems, making them adaptable to a wide range of industrial applications.
Understanding these points elucidates how belt conveyors efficiently transport materials across distances, embodying a simple yet powerful solution to the challenges of material handling in various sectors.
Key Components and Their Functions
- Conveyor Belt: The primary medium for material transport, available in various materials and designs to suit different applications.
- Pulleys (Drive and Idler): The drive pulley powers the conveyor belt’s movement, while the idler pulleys provide support and guide the belt.
- Motor: The power source for the drive pulley, which can vary in size and capacity depending on the conveyor’s application.
- Belt Support System: Ensures smooth operation of the belt, which can be rollers for reducing friction or a flat pan for stability.
- Frame: The structural component that holds all other parts in place, designed to withstand the load and the operational stresses.
- Tensioning Mechanism: Adjusts the tension on the belt to prevent slippage and ensure efficient operation.
- Loading and Unloading Points: Specifically designed areas for efficient and safe loading and unloading of materials.
- Control System: Includes sensors and switches to manage the conveyor’s operation, ensuring safety and efficiency.
- Safety Features: Emergency stops, guards, and other devices to protect workers and the conveyor itself.
By understanding these components and their pivotal roles, it becomes clear how the application of belt conveyor systems can be optimized for various industrial tasks, making them a cornerstone of modern manufacturing and material handling processes.
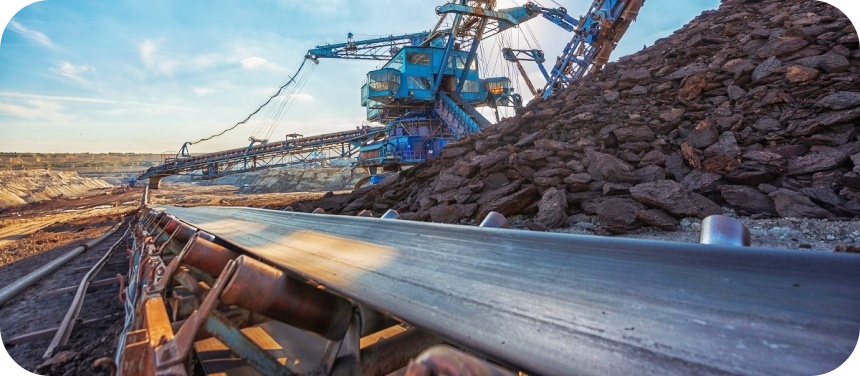
The Application of Belt Conveyor Systems: Diverse Types and Uses
The application of belt conveyor systems is vast and varied, spanning across numerous industries and fulfilling a wide range of material handling needs. From the intricate assembly lines in manufacturing facilities to the rugged landscapes of mining operations, belt conveyors are tailored to meet specific operational requirements. This section delves into at least eight different types of belt conveyors, each designed with unique features and functionalities to cater to the specific demands of various applications. For a more detailed classification, readers are encouraged to refer to “types of belt conveyor pdf” documents that provide comprehensive insights into each type.
Modular Belt Conveyors
Modular belt conveyors are known for their versatility, featuring belts made of individual interlocking plastic modules. This design allows for easy repair and replacement, making them ideal for applications requiring frequent cleaning or transporting sharp or abrasive materials.
Slat Conveyors
Slat conveyors utilize a series of slats attached to a chain, offering a solid platform for transporting heavy or unevenly shaped objects. Their robust construction makes them suitable for heavy-duty applications, including assembly lines and product sorting systems.
Portable Conveyor Belts
Portable conveyor belts are designed for temporary setups and flexibility, often used in construction sites or material loading and unloading areas. Their mobility allows for easy relocation to meet changing operational needs.
Swan Neck Conveyors
Swan neck conveyors, with their distinctive inclined design, are used to transport materials upward, making them perfect for applications where space is limited. They are commonly found in recycling plants and manufacturing facilities where different processing stages are located at varying height levels.
Metering Conveyors
Metering conveyors are designed to regulate the flow of materials, ensuring a consistent and controlled feed into processing equipment. They are essential in applications where precise material handling is critical, such as in food processing and packaging lines.
Sandwich Belt Conveyors
Sandwich belt conveyors employ two belts that firmly grip material between them, allowing for the transportation of materials at steep angles. This design is particularly useful in mining and construction projects for moving materials up or down steep inclines.
Pipe Conveyors
Pipe conveyors feature a unique belt design that rolls into a pipe shape to enclose the material being transported. This enclosed design protects the material from environmental elements and prevents spillage, making it ideal for handling sensitive or hazardous materials.
Trough Conveyors
Trough conveyors have a belt that forms a trough to contain the material, reducing spillage and providing a more secure way to transport loose bulk materials, such as grains, sand, or coal. They are widely used in agriculture and mining industries for bulk material handling.
Each of these types of belt conveyors plays a pivotal role in the application of belt conveyor systems, offering solutions tailored to the unique demands of different industrial and commercial environments. By understanding the specific features and advantages of each type, businesses can select the most appropriate conveyor system to enhance their operational efficiency and productivity.
The Pivotal Role of Belt Conveyors in Industry: Exploring the Application of Belt Conveyor Systems
Belt conveyors are integral to the operational efficiency of a myriad of industries, serving as the circulatory system for the global economy. They facilitate the movement of materials and products with remarkable efficiency and reliability. This versatility makes the application of belt conveyor systems critical across various sectors, from the extraction of raw materials to the delivery of finished products to consumers. Let’s delve deeper into the general applications of these systems and explore their specific uses in key industries.
General Applications of Belt Conveyor Systems
The applications of conveyor belt systems extends across a wide range of industries, proving to be a critical component in the seamless operation and success of various sectors. These systems are not just about transporting items; they are about enhancing efficiency, ensuring safety, and optimizing processes. Below, we delve deeper into the indispensable role of belt conveyors in several key industries:
Mining
- Efficient Ore Transportation: In mining, belt conveyors are vital for the efficient transport of ores and minerals from mining sites to processing facilities. Their ability to handle large volumes of material over long distances and rugged terrain reduces operational costs and time.
- Safety and Reliability: These conveyors offer a safer alternative to traditional truck transportation, minimizing the risk of accidents and ensuring consistent material flow without interruptions.
- Environmental Impact: Compared to truck haulage, belt conveyors have a lower environmental footprint, producing fewer emissions and reducing energy consumption per ton of material transported.
Agriculture
- Versatile Crop Handling: Belt conveyors play a versatile role in agriculture, from transporting grain and seeds to moving hay bales and other bulk products. They are designed to handle delicate agricultural products gently, reducing loss and damage.
- Seasonal Efficiency: Especially crucial during harvest seasons, conveyors streamline the processing and distribution of agricultural products, ensuring that crops are moved swiftly from fields to storage or market.
- Adaptability: Agricultural conveyors are adaptable to various environmental conditions, including outdoor, dusty, and moist conditions, making them suitable for different agricultural needs.
Pharmaceuticals
- Contamination-Free Transport: In the pharmaceutical industry, the cleanliness and contamination-free transport of materials are paramount. Belt conveyors designed for this sector are made from materials that are easy to clean and resist contamination, ensuring that products meet strict hygiene standards.
- Precision and Control: These conveyors offer precise control over the movement of pharmaceutical products through production lines, allowing for accurate sorting, packaging, and inspection processes.
- Integration with Cleanrooms: Belt conveyors can be integrated into cleanroom environments, essential for the production of sterile pharmaceutical products, without compromising the controlled conditions.
Manufacturing
- Streamlined Production Lines: Belt conveyors are the backbone of manufacturing operations, moving components and finished goods along production lines with efficiency and speed. They are crucial for maintaining a continuous flow in assembly operations, minimizing downtime.
- Customization for Specific Needs: Manufacturing conveyors can be customized with various belt materials, widths, and speeds to accommodate different products and processes, from electronics assembly to automotive manufacturing.
- Integration with Automation: In modern manufacturing, belt conveyors are often integrated with automated systems and robotics, enhancing precision and productivity while reducing labor costs.
Across these industries, the application of belt conveyor systems demonstrates their versatility and essential role in ensuring operational efficiency, safety, and environmental sustainability. By adapting to the specific needs of each sector, belt conveyors continue to be a fundamental part of industrial success.
Specific Applications of Belt Conveyor Systems
The application of belt conveyor systems has revolutionized not just the construction industry but has also made significant impacts in warehousing, distribution, and food processing sectors. Each of these fields benefits uniquely from the integration of conveyor systems, showcasing the adaptability and efficiency of belt conveyors to meet specific operational needs. Let’s explore how these systems are applied across these diverse sectors, enhancing productivity, safety, and operational efficiency.
In Construction: Expanding the Application of Belt Conveyor Systems
The applications of conveyor belt systems in the construction industry marks a significant leap towards achieving operational excellence, safety, and efficiency on construction sites. These systems are ingeniously designed to handle the rigorous demands of construction work, proving indispensable in various aspects of the construction process. Here’s an expanded look into the multifaceted roles belt conveyors play in construction:
- Material Handling: Belt conveyors excel in transporting a diverse array of building materials, including not just bricks, concrete, steel, and lumber, but also glass, roofing materials, and prefabricated parts. This versatility ensures that regardless of the construction material’s nature or size, conveyors can move it efficiently, contributing to faster construction processes and the ability to meet tight deadlines.
- Debris Removal: Beyond just removing rubble and waste, belt conveyors facilitate the continuous clean-up of sites, handling materials like dust, small particles, and hazardous materials safely away from the work area. This capability is crucial for maintaining not only cleanliness but also compliance with environmental and safety regulations.
- Precise Material Placement: The strategic use of belt conveyors allows for the precise placement of materials at high elevations or specific locations that are otherwise challenging to reach with traditional material handling methods. This precision supports the efficient use of resources and reduces the time spent repositioning materials.
- Cost Reduction: Belt conveyors contribute to cost reduction by optimizing the material flow, which in turn reduces the time to complete tasks. They also lower the reliance on heavy machinery and the fuel costs associated with operating such equipment, further driving down project expenses.
- Enhanced Safety: The automation of material transport through conveyors minimizes human interaction with potentially hazardous materials and machinery, significantly reducing the risk of accidents and injuries. This enhancement of safety is complemented by the reduction of strain-related injuries, as workers are less involved in the physical moving of heavy materials.
- Environmental Impact: Belt conveyors have a lower environmental impact compared to other material transport methods. Their efficiency and reduced need for heavy machinery contribute to lower emissions on construction sites, aligning with green construction principles.
- Flexibility and Adaptability: Belt conveyor systems can be easily adapted and reconfigured to suit the changing needs of a construction project, making them a flexible solution for material transport. This adaptability ensures that as projects evolve, the conveyor system can continue to meet its demands without significant modifications.
- Integration with Other Systems: Belt conveyors can be integrated with other construction technologies, such as automated building information modeling (BIM) systems, to further streamline the construction process. This integration allows for real-time tracking of materials and enhances project management capabilities.
The application of belt conveyor systems in construction is a testament to their transformative impact on the industry. By enhancing efficiency, safety, and cost-effectiveness, belt conveyors not only support the operational needs of construction projects but also contribute to the advancement of construction methodologies.
In Warehousing and Distribution
Belt conveyors optimize operations within warehousing and distribution centers through the following applications:
- Improving Sorting and Packaging: Automated conveyor systems efficiently sort and route goods to designated areas for packaging or direct shipment, enhancing operational flow.
- Streamlining Loading and Unloading: They significantly expedite the process of loading and unloading goods from trucks or containers, improving throughput and reducing manual labor.
- Inventory Management: Conveyors facilitate the movement of goods through inventory management processes, aiding in stock control and order fulfillment accuracy.
- Reducing Product Damage: By providing a smooth and controlled transport method, conveyors minimize the risk of product damage during handling.
- Maximizing Space Utilization: The strategic implementation of conveyor systems can help optimize the use of warehouse space, allowing for more efficient storage and retrieval processes.
In Food Processing
In the food industry, the application of belt conveyor systems is paramount for maintaining hygiene and operational efficiency, with their use extending to:
- Ensuring Hygiene: Specifically designed for easy cleaning and sanitization, conveyors prevent cross-contamination and ensure compliance with food safety regulations.
- Handling Products Gently: They facilitate the gentle movement of food products through various stages of processing and packaging, preserving the integrity and quality of the products.
- Temperature Control: Certain conveyor systems are equipped to handle temperature-sensitive products, either by being resistant to high temperatures for cooking processes or by incorporating cooling systems for chilled products.
- Customization for Specific Foods: Conveyors can be customized with coatings or attachments to handle specific food products, such as sticky confectioneries or delicate fruits, without causing damage.
- Efficiency in Production Lines: They streamline the production process by ensuring a continuous flow of ingredients and products, significantly enhancing productivity and reducing bottlenecks.
The application of belt conveyor systems across these sectors highlights their indispensable role in modern industry, enhancing productivity, safety, and efficiency. By leveraging the specific features and advantages of belt conveyors, businesses can select the most suitable system to meet their operational needs, ensuring optimal performance and cost-effectiveness.
To Unveil the Advantages of Belt Conveyors in the Application of Belt Conveyor Systems
The application of belt conveyor systems across various industries has revolutionized the way materials and goods are transported, offering a myriad of advantages that contribute to operational efficiency, safety, versatility, and cost-effectiveness. These systems are not just about moving items from point A to point B; they are about optimizing the entire process flow, reducing operational costs, and enhancing productivity. Here, we delve into the significant advantages of belt conveyors, highlighting their pivotal role in modern industry.
- Efficiency: Belt conveyors are designed for continuous operation, allowing for the seamless transport of materials with minimal downtime. Their ability to move large volumes of goods over significant distances at high speeds significantly enhances productivity, making them an efficient solution for material handling needs.
- Safety: The application of belt conveyor systems has been instrumental in improving workplace safety. By automating the transport of heavy and potentially hazardous materials, they reduce the need for manual handling, thereby minimizing the risk of injuries. Additionally, modern conveyor systems are equipped with safety features like emergency stops and guards, further ensuring the safety of operators.
- Versatility: One of the most notable advantages of belt conveyors is their versatility. They can be customized with various belt materials and configurations to handle a wide range of products, from bulky materials to delicate items, across different industries. Whether it’s mining, agriculture, pharmaceuticals, or food processing, there’s a belt conveyor solution tailored to meet the specific requirements of each application.
- Cost-Effectiveness: Belt conveyors offer a cost-effective solution for transporting materials. Their durability and low maintenance requirements reduce long-term operational costs. Additionally, by streamlining material handling processes, they can significantly cut labor costs and enhance overall efficiency.
- Reduced Labor Requirements: Automating the movement of materials with belt conveyors minimizes the need for manual labor, allowing businesses to allocate human resources to more critical tasks. This not only reduces labor costs but also enhances operational efficiency.
- Scalability: Belt conveyor systems can be easily expanded or modified to accommodate changing operational needs. This scalability ensures that businesses can adapt their material handling processes as they grow, without incurring significant additional costs.
- Environmental Impact: Compared to motorized transport vehicles, belt conveyors have a lower environmental impact. They are energy-efficient and can be powered by renewable energy sources, contributing to a reduction in greenhouse gas emissions and promoting sustainable operational practices.
- Ease of Installation and Integration: Belt conveyors can be easily installed and integrated into existing operational setups, allowing for a smooth transition and minimal disruption to ongoing processes. Their modular design enables quick assembly and disassembly, providing flexibility in how and where they are used.
The application of belt conveyor systems offers a comprehensive solution to material handling challenges, providing efficiency, safety, versatility, and cost-effectiveness. By leveraging these advantages, industries can enhance their operational processes, reduce costs, and improve overall productivity, underscoring the indispensable role of belt conveyors in modern industrial applications.
Detailed Insights into Belt Conveyor Parts and Their Functions in the Application of Belt Conveyor Systems
The application of belt conveyor systems across various industries is a testament to their versatility and efficiency in material handling. Understanding the components that make up these systems is crucial for optimizing their operation and maintenance. Here, we explore the essential parts of a belt conveyor and their functions, shedding light on how each contributes to the effective application of belt conveyor systems.
- Conveyor Belt: The core component, the conveyor belt, is the medium that carries materials from one point to another. Its material—be it rubber, fabric, or metal—is selected based on the application, considering factors like the type of materials being transported and the environment in which the conveyor operates.
- Drive Pulley: This pulley, connected to the motor, provides the force that drives the conveyor belt. It’s critical for initiating the movement of the belt and can be coated or textured to improve grip with the belt, ensuring efficient transfer of power.
- Tail Pulley: Located at the opposite end of the drive pulley, the tail pulley functions as a return point for the belt. It can also be adjustable to maintain tension on the belt, crucial for smooth operation and preventing slippage.
- Idler Rollers: These support the conveyor belt along its length, reducing friction and wear. Positioned strategically, idler rollers help maintain the belt’s shape and alignment, ensuring efficient material transport.
- Motor: The motor powers the drive pulley, dictating the speed and torque of the conveyor belt. The selection of the motor is based on the conveyor’s required speed, the load it needs to carry, and the duration of operation.
- Belt Tensioning System: This system adjusts the tension on the conveyor belt, essential for optimal performance and preventing belt slippage or excessive wear. It can be a mechanical screw adjustment or a weighted system.
- Conveyor Frame: The structure that supports all the conveyor components. It must be robust enough to handle the load and the stress of operation, often made from steel or aluminum for durability.
- Loading Chute: The point where materials are loaded onto the conveyor belt. Designed to minimize spillage and ensure even distribution of materials on the belt, the loading chute’s design is critical for preventing material wastage and ensuring efficiency.
- Discharge End: The area where materials are offloaded from the belt. It may include features like scrapers or plows to clean the belt and ensure precise material discharge, critical for maintaining the cleanliness and efficiency of the conveyor.
- Control System: Incorporates sensors, switches, and a control panel to manage the conveyor’s operation. This system allows for adjustments in speed, monitoring of the conveyor’s status, and quick responses to any issues, ensuring the conveyor operates within optimal parameters.
- Safety Features: Essential for protecting operators and the conveyor itself, safety features include emergency stop buttons, guards, and safety switches. These components are designed to halt the conveyor immediately in case of an emergency, minimizing the risk of accidents.
- Cleaning Devices: Such as belt scrapers and brushes, these devices maintain the cleanliness of the conveyor belt, especially crucial in applications where material residue can affect the conveyor’s operation.
Understanding the functions of these components is vital in the application of belt conveyor systems, ensuring they are designed, operated, and maintained for maximum efficiency and reliability. Each part plays a specific role in the conveyor’s overall performance, highlighting the importance of comprehensive knowledge in the successful application of belt conveyor systems.
The Types of Conveyor Belt Joints in the Application of Belt Conveyor Systems
The application of belt conveyor systems across various industries necessitates an understanding of the different types of conveyor belt joints. These joints are crucial for the maintenance, longevity, and efficiency of belt conveyors, ensuring that they can withstand the operational demands placed upon them. Here, we delve into the various types of conveyor belt joints, highlighting their importance and applications.
- Mechanical Fasteners: This type of joint involves metal fasteners or clips to join the ends of the belt. It’s a versatile and quick solution for belt repair, suitable for temporary or permanent fixes. Mechanical fasteners are ideal for belts that carry small to medium-sized loads and can be easily installed on-site.
- Vulcanization: Vulcanized joints create a seamless and strong bond by using heat and pressure to fuse the belt ends together. This method is preferred for high-strength applications, offering excellent durability and minimal risk of the joint separating under tension.
- Cold Bonding: Similar to vulcanization but without the need for heat, cold bonding uses adhesives to join the belt ends. This method is suitable for applications where heat cannot be applied, providing a strong bond that is resistant to wear and tear.
- Finger Joints: In this method, the ends of the belt are cut in a finger pattern and then bonded together, either by vulcanization or cold bonding. Finger joints offer a high-strength connection that is flexible and less prone to fatigue, making them suitable for belts with high tension.
- Skived Joints: The belt ends are thinned (skived) and overlapped, then bonded together. This type of joint is flat and smooth, reducing the risk of snagging or catching on conveyed materials. Skived joints are commonly used in light-duty applications.
- Step Joints: The ends of the belt are cut in steps and then bonded together. This method provides a strong and durable joint, suitable for medium to heavy-duty applications where a smooth transition over the joint is necessary.
- Peel and Stick Joints: A simple method where the belt ends are prepared with adhesive strips that can be peeled and stuck together. While not as strong as other methods, peel and stick joints are quick and easy to apply, making them suitable for emergency repairs.
- Welded Joints: For thermoplastic belts, the ends can be welded together using heat and pressure. This method creates a very strong and durable joint, ideal for belts that need to withstand high temperatures or chemical exposure.
- Overlap Joints: The belt ends are overlapped and then bonded together, either mechanically or with adhesives. Overlap joints are simple to create and provide a decent level of strength, suitable for light to medium-duty applications.
Each type of conveyor belt joint has its specific applications and benefits, contributing to the overall performance and longevity of belt conveyor systems. The choice of joint method depends on various factors, including the type of belt material, the operational environment, the load being conveyed, and the need for durability and maintenance. Understanding these options is crucial in the application of belt conveyor systems, ensuring that the chosen joint type meets the operational demands and contributes to efficient and reliable material handling.
Design and Safety Considerations in the Application of Belt Conveyor Systems
The application of belt conveyor systems in industries requires meticulous design and stringent safety measures to ensure efficient and safe operations. This section delves into the critical aspects of design considerations and safety protocols that are fundamental to the application of belt conveyor systems.
How to Design a Belt Conveyor Diagram
A belt conveyor diagram serves as an invaluable tool in illustrating the design and layout of a typical belt conveyor system. It provides a visual representation of the system’s components and their configuration, aiding in understanding how each part contributes to the conveyor’s operation. Key points illustrated in a belt conveyor diagram include:
- Conveyor Belt Path: Shows the direction and path of the belt movement, highlighting the drive and tail pulleys’ positions.
- Drive Mechanism: Details the location of the motor and drive pulley, illustrating how power is transmitted to the belt.
- Idler Rollers: Depicts the placement of idler rollers that support the belt and maintain its tension and alignment.
- Loading and Discharge Points: Identifies where materials are loaded onto and discharged from the conveyor, crucial for understanding material flow.
- Control System: Illustrates the control panel and any associated sensors or switches, showing how the conveyor’s operation is managed.
- Safety Features: Highlights the incorporation of safety devices, such as emergency stops and guards, emphasizing their importance in the system’s design.
- Tensioning Device: Shows the mechanism for adjusting belt tension, ensuring optimal performance and preventing slippage.
Safety Measures
Ensuring the safe operation of belt conveyors involves implementing a series of safety measures and adhering to specific regulations. These precautions are designed to protect operators and the integrity of the conveyor system. Key safety measures include:
- Emergency Stop Controls: Strategically placed along the conveyor to allow immediate shutdown in case of an emergency, minimizing potential hazards.
- Guardrails and Barriers: Installed around moving parts to prevent accidental contact with the conveyor belt and rollers, reducing the risk of injury.
- Regular Maintenance and Inspections: Scheduled checks to identify and rectify potential issues before they lead to accidents, ensuring the conveyor’s safe operation.
- Training for Operators: Comprehensive training programs for all personnel involved in the operation and maintenance of the conveyor, emphasizing the importance of safety protocols.
- Safety Signage: Clear and visible signs warning of potential dangers and instructing on proper behavior near the conveyor.
- Lockout/Tagout Procedures: Established protocols for safely isolating the conveyor from power sources during maintenance, preventing accidental startup.
- Belt Misalignment Switches: Devices that detect and signal when the conveyor belt is off-track, allowing for quick correction to prevent damage or accidents.
- Speed Controls: The ability to adjust the conveyor’s speed according to the type of materials being transported and the operational conditions, enhancing safety and efficiency.
- Fire and Explosion Prevention: For conveyors used in potentially hazardous environments, measures such as fire-resistant belts and explosion-proof motors are essential for safety.
Incorporating these design and safety considerations into the application of belt conveyor systems is crucial for ensuring not only the efficiency and productivity of operations but also the well-being of the workforce and the longevity of the conveyor system itself. By adhering to these principles, industries can leverage the full potential of belt conveyors while maintaining a safe working environment.
Get a detailed quote for our conveyor belts by filling out the form below.
FAQs about Application of Belt Conveyor
Flat belt conveyors are versatile systems used across various industries due to their simplicity and efficiency in transporting goods. These conveyors are particularly beneficial for moving items from one point to another in a straight line over short to medium distances. They are widely used in material handling, packaging, and assembly lines where smooth and continuous flow is essential. Flat belt conveyors are ideal for handling light to medium-weight products, including but not limited to boxes, bags, parcels, food items, and small parts. Their flat surface provides a stable platform for goods, minimizing the risk of items falling off or getting damaged during transit. Additionally, these conveyors can be customized with sidewalls, cleats, or guides to handle specific types of products or applications, enhancing their versatility in various operational settings.
A conveyor belt is a critical component in conveyor systems, designed to transport materials and goods efficiently across a facility or site. Its primary use is to move items from one location to another in a continuous, automated manner, reducing the need for manual handling and thereby increasing productivity and safety. Conveyor belts are used in a wide range of industries, including manufacturing, warehousing, mining, agriculture, pharmaceuticals, food processing, and more. They are essential for assembly lines, packaging operations, bulk material handling, and the transportation of heavy or bulky items. The specific use of a conveyor belt can vary greatly depending on the industry and application, ranging from transporting raw materials like coal and ores in mining to moving finished products and packages in distribution centers.
Belt conveyors are used in virtually every industry that requires the efficient transport of materials or products. In manufacturing, they facilitate the movement of parts and products through various stages of production and assembly. In mining and quarrying, belt conveyors are used to transport raw materials and aggregates over long distances. Warehousing and logistics operations rely on belt conveyors for sorting, packaging, and distributing goods. The agricultural sector uses them to handle grain, feed, and other bulk materials. Food processing industries utilize belt conveyors for the hygienic handling and processing of food products. Additionally, belt conveyors are employed in airports for baggage handling, in recycling plants for sorting waste, and in the chemical industry for safely transporting chemicals and raw materials.
In the chemical industry, belt conveyors play a crucial role in the safe and efficient transport of raw materials, intermediates, and finished chemical products. They are used for moving bulk chemicals, powders, and granules between different stages of production, from initial processing to packaging and distribution. Belt conveyors in this sector are often designed with special materials and coatings to resist corrosion, abrasion, and the effects of aggressive chemicals. They may also be equipped with enclosed designs or dust-proof covers to prevent contamination and ensure the safety of workers and the environment. The precise control offered by belt conveyors allows for the careful handling of sensitive chemical products, minimizing spillage and waste. Their application in the chemical industry is vital for maintaining a streamlined production process, adhering to strict safety standards, and ensuring the quality and purity of chemical products.
Last Updated on August 1, 2024 by Jordan Smith
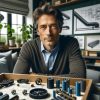
Jordan Smith, a seasoned professional with over 20 years of experience in the conveyor system industry. Jordan’s expertise lies in providing comprehensive solutions for conveyor rollers, belts, and accessories, catering to a wide range of industrial needs. From initial design and configuration to installation and meticulous troubleshooting, Jordan is adept at handling all aspects of conveyor system management. Whether you’re looking to upgrade your production line with efficient conveyor belts, require custom conveyor rollers for specific operations, or need expert advice on selecting the right conveyor accessories for your facility, Jordan is your reliable consultant. For any inquiries or assistance with conveyor system optimization, Jordan is available to share his wealth of knowledge and experience. Feel free to reach out at any time for professional guidance on all matters related to conveyor rollers, belts, and accessories.