Conveyor Belt Tear: Causes and Solutions
Conveyor belts play a pivotal role in the seamless operation of numerous industries, from manufacturing and mining to logistics and agriculture. These belts are the lifelines that ensure the efficient and continuous movement of goods and materials, making them indispensable for daily operations. However, despite their robustness and durability, conveyor belts are not immune to damage. One common issue that significantly disrupts productivity is a conveyor belt tear. This type of damage not only halts production but can also lead to substantial financial losses and safety hazards. Understanding the causes and impacts of conveyor belt rips is crucial for operators to implement effective preventive measures and maintain the operational integrity of their conveyor systems.
What is Conveyor Belt Tears
Conveyor belt tears are a critical issue that can compromise the efficiency and safety of conveyor systems. These tears not only disrupt operations but can also lead to significant downtime and repair costs. Discover essential tips to repair conveyor belt tears, reduce downtime, and maintain efficient operations with expert methods.
Understanding the differences between these types of damage is crucial for diagnosing issues correctly and applying the appropriate repair techniques. For instance, a transverse tear might require a different repair approach compared to a longitudinal conveyor belt tear or delamination. Recognizing the specific type of damage can also aid in identifying underlying issues with the conveyor system or operational practices, allowing for more targeted preventive measures to be implemented.
Causes of Conveyor Belt Tears
Understanding the causes of conveyor belt tears is essential for preventing these issues and maintaining the efficiency and safety of conveyor systems. Ripped conveyor belt can lead to significant operational disruptions, making it crucial to identify and address the underlying reasons promptly.
Related Causes of Conveyor Belt Tear
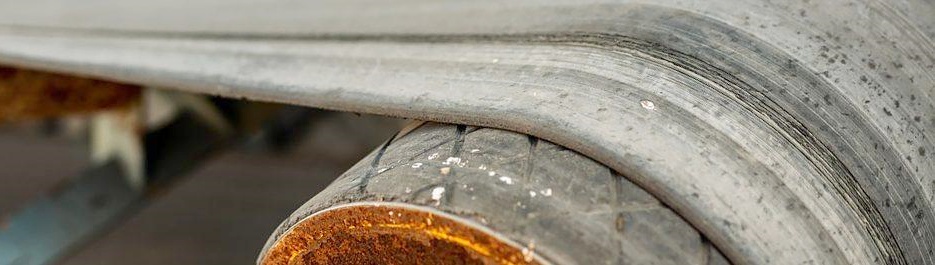
Several factors contribute to the occurrence of conveyor belt tears, each varying in its impact and the complexity of the resulting damage. The main reasons behind conveyor belt tears include:
Impurities in Conveyed Material: Sharp or oversized objects mixed with the conveyed materials can puncture and slice through the belt as they are transported. These impurities, such as metal shards, stones, or other abrasive elements, can cause immediate and severe conveyor belt tear, especially if the belt speed is high and the materials are dropped from a height.
Improper Installation of Auxiliary Equipment: Conveyor systems are often equipped with various auxiliary components designed to enhance their operation. However, incorrect installation of these parts, such as skirt boards, guides, and chutes, can lead to misalignment or excessive pressure at certain points on the belt, causing tears along those areas.
Structural Defects in the Conveyor System: Inherent flaws in the conveyor’s design or construction can create stress points or areas where materials are prone to accumulate and cause damage. These structural defects may result in repeated stress on the belt, leading to wear and eventual tearing.
Sharp Edges and Protrusions: The presence of sharp edges or protruding parts within the conveyor system can snag the belt as it moves. This snagging can initiate a small tear that, if unnoticed, can grow over time into a significant conveyor belt tear, compromising the belt’s structural integrity.
Related Causes of Conveyor Belt Failure
In addition to the specific causes of tears, several broader factors contribute to overall conveyor belt failure, which may include or lead to tearing:
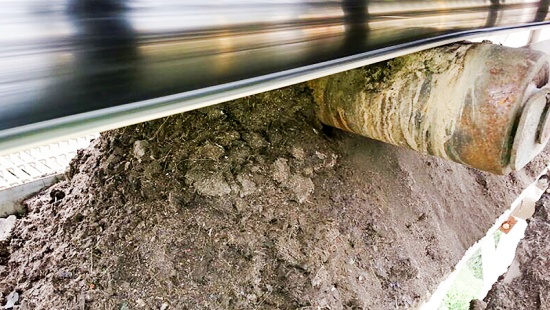
Material Blocking: Blockages in the conveyor, such as those caused by jammed materials at transfer points or chutes, can exert undue stress on the belt. This stress can cause stretching, tearing, or complete belt failure if the blockage is not quickly resolved.
Falling of the Intermediate Idler: The intermediate idler supports the belt’s weight and the transported materials. Should an idler fail or fall out of position, it can create a gap that leads to sagging or snapping of the belt under the weight, potentially causing a tear.
Conveyor Parts Failure: Critical components of the conveyor system, like rollers, bearings, or the belt splice, can fail due to wear, improper maintenance, or manufacturing defects. Such failures can lead to misalignment, excessive tension, or other conditions conducive to conveyor belt tear.
Environmental and Operational Conditions: Extreme temperatures, exposure to chemicals, and operational conditions like overloading or excessive speed can weaken the belt material over time. These conditions make the belt more susceptible to tears and other forms of damage.
By identifying and addressing these causes of conveyor belt tears and failures, operators can significantly reduce the risk of unexpected downtime and extend the life of their conveyor systems. Regular inspections, proper maintenance, and adherence to operational guidelines are critical in preventing conveyor belt tear and ensuring the longevity and reliability of conveyor systems.
Preventive Measures for Conveyor Belt Tear
To mitigate the risk of ripped conveyor belt and ensure the longevity and efficiency of conveyor systems, it is crucial to implement strategic preventive measures. These strategies not only help in avoiding the immediate disruptions caused by conveyor belt tears but also contribute to the overall reliability and safety of the conveyor system.
Conveyor Belt Problems and Solutions
Several proactive steps can be taken to prevent conveyor belt tears, focusing on material control, structural improvements, and the use of specialized belts:
Strengthening Material Control: One of the primary strategies to prevent conveyor belt tears is to ensure that the materials being conveyed are free of sharp or oversized objects that could damage the belt. Implementing rigorous screening processes to remove such impurities before they enter the conveyor can significantly reduce the risk of tears. Additionally, controlling the drop height at loading zones can minimize the impact force of falling materials, thereby protecting the belt from potential damage.
Improving Conveyor Structure: Enhancing the design and structure of the conveyor system can also play a significant role in preventing conveyor belt tears. This includes ensuring proper installation and alignment of all conveyor components, such as idlers, rollers, and skirt boards, to reduce undue stress on the belt. Regular inspections and maintenance of the conveyor structure can identify and rectify potential issues before they lead to belt damage.
Using Tear-Resistant Belts: Investing in high-quality, tear-resistant conveyor belts is a direct approach to minimizing the risk of torn conveyor belt. These belts are designed with reinforced materials and structures that can withstand harsh conditions and the impact of sharp or heavy objects. While the initial cost may be higher, the long-term benefits of reduced downtime and maintenance needs can make tear-resistant belts a cost-effective solution.
Conveyor Belt Tear Detection
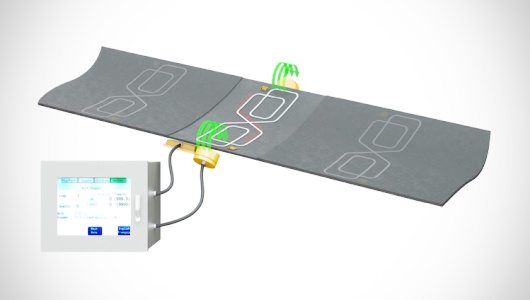
Early detection of conveyor belt tears is essential for timely intervention and repair, preventing further damage and possible system failure. It is important to pay attention to conveyor belt rip detection. Modern technology offers several methods and tools for detecting tears in conveyor belts:
Sensors and Monitoring Systems: Advanced sensor technologies can be installed along the conveyor belt to monitor its condition in real time. These sensors can detect irregularities, such as vibrations or changes in belt tension, that may indicate a tear. Upon detection, the system can alert operators to the exact location of the tear, allowing for quick and targeted repair actions.
Visual Inspection Systems: Automated visual inspection systems use cameras and image processing software to continuously monitor the surface of the conveyor belt for signs of wear or damage. These conveyor belt rip detector can identify potential tears and other defects that might not be visible to the naked eye, providing an efficient and non-invasive means of belt inspection.
Implementing these preventive measures and introducing conveyor belt tear detector can significantly reduce the incidence of conveyor belt rip, ensuring smoother operations and extending the lifespan of the conveyor system. Regular training for personnel on the importance of maintenance and the correct handling of the conveyor belt can further enhance the effectiveness of these preventive strategies.
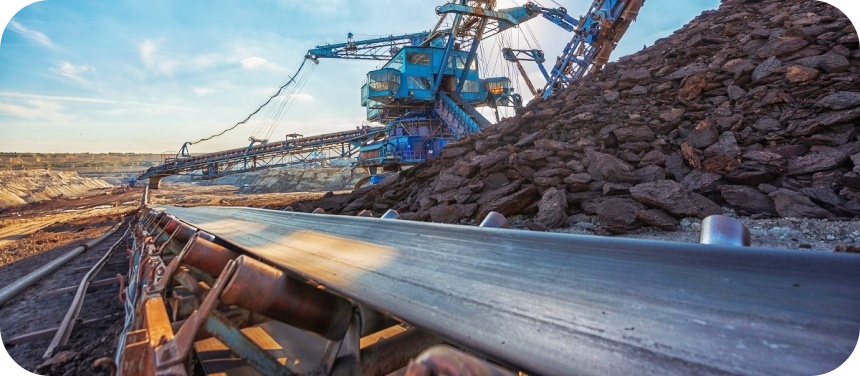
Repairing Conveyor Belt Tears
When faced with a conveyor belt tear, the urgency and method of repair are critical decisions that can significantly impact operational efficiency and safety. Understanding the options for repairing ripped conveyor belt, the tools required, and how to secure expert services are essential steps in restoring conveyor belt functionality with minimal downtime.
Conveyor Belt Repair Kit and Tools
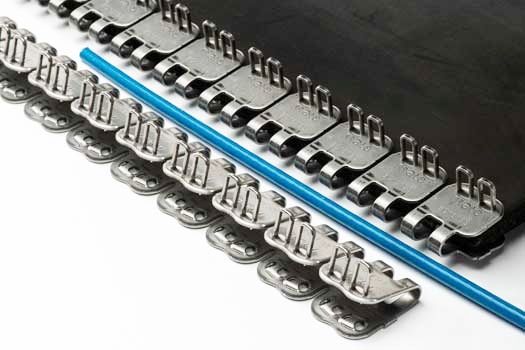
For effective repair of a conveyor belt tear, a variety of specialized tools and kits are available, designed to address different types and severities of damage. These repair kits typically include:
Metal Fasteners: Metal fasteners are a common solution for quickly joining torn sections of a belt. They are particularly useful for repairing small to medium-sized tears and can be applied using simple hand tools.
Overlays: For larger tears or areas with significant wear, overlays made from durable materials can be bonded to the belt’s surface, providing a reinforced patch that extends the life of the belt.
Vulcanizing Equipment: For a more permanent repair, especially on critical high-tension belts, vulcanizing equipment can be used to splice damaged sections. This process involves the application of heat and pressure to bond repair materials to the original belt, restoring its strength and flexibility.
Temporary vs. Permanent Repairs
Deciding between temporary and permanent repairs depends on the extent of the conveyor belt tear, the belt’s overall condition, and operational demands:
Temporary Repairs: Utilizing repair clips or metal fasteners for temporary fixes is advisable when the goal is to quickly resume operations until a more comprehensive repair can be performed. These solutions are suitable for minor to moderate tears where the belt’s structural integrity is largely intact.
Permanent Repairs: For severe tears or when the conveyor belt is a critical part of the production process, permanent repairs using vulcanization or heavy-duty bonding agents are recommended. These repairs restore the belt to near-original condition, ensuring reliability and longevity.
Finding Conveyor Belt Repair Services
Securing professional and reliable conveyor belt repair services is crucial for effective repair, especially for complex or severe conveyor belt rips. Here are some tips for finding the right service provider:
Research and Recommendations: Look for service providers with a strong reputation in the industry. Recommendations from other businesses or online reviews can provide valuable insights.
Expertise and Experience: Choose a repair service with extensive experience in handling conveyor belt tears, particularly those with knowledge of your specific type of conveyor belt and its operational requirements.
Availability and Response Time: In many cases, the speed of response can be critical. Opt for repair services that offer 24/7 availability and have a proven track record of timely and efficient repairs.
Comprehensive Services: A dependable supplier should not only provide emergency repair services but also offer ongoing maintenance and support to prevent future conveyor belt torn.
By selecting the appropriate repair method and partnering with a reliable repair service, businesses can effectively manage conveyor belt tears, minimizing downtime and ensuring the continuous, safe operation of their conveyor systems.
Best Practices for Effective Conveyor Belt Rip Repair
Immediate Action
When a conveyor belt tears, immediate action is crucial to minimize downtime and prevent further damage. Promptly addressing belt damage can significantly reduce the risk of prolonged operational disruptions and the associated costs. Quick repairs help maintain the efficiency and safety of the conveyor system, ensuring that production schedules remain on track. It is essential to have a well-defined response plan that includes immediate inspection, damage assessment, and initial repair steps to mitigate the impact of the tear.
Assessment
Proper assessment of the damage is a critical step in effective conveyor belt rip repair. For transverse tears that extend more than 25% across the belt width, it is recommended to cut out the damaged section and create a new splice. This approach ensures the integrity and strength of the repaired belt. Accurate assessment involves measuring the extent of the tear, evaluating the condition of the surrounding belt area, and determining the most suitable repair method. Detailed documentation of the damage can also aid in future preventive measures and maintenance planning.
Rip Repair Kit
Having a well-equipped rip repair kit on hand is essential for quick and effective responses to conveyor belt damage. A comprehensive repair kit should include various sized fasteners, installation tools, and other necessary materials to address different types of tears and punctures. By keeping a rip repair kit readily available, maintenance teams can promptly initiate repairs, minimizing downtime and ensuring the conveyor system’s continued operation. Regularly checking and replenishing the kit’s contents ensures preparedness for any unexpected belt damage.
Choosing the Right Fasteners
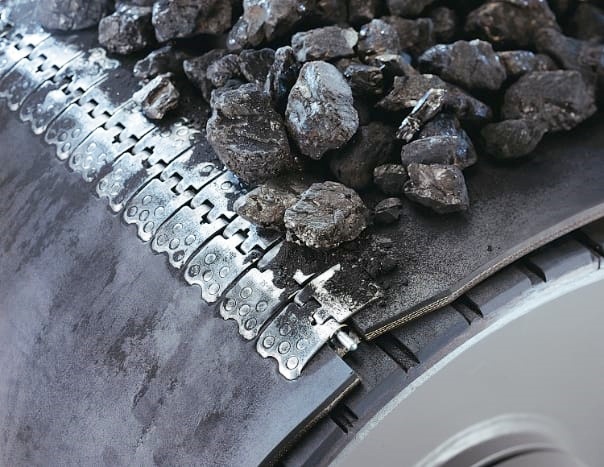
Selecting the appropriate fasteners is vital for the durability and effectiveness of conveyor belt repairs. Bolt Solid Plate Fasteners are recommended for their robustness and ease of installation. These fasteners feature high-tensile-strength bolts and top-and-bottom plate compression, which provide secure and stable repairs even under heavy-duty conditions. The specially-formed teeth of Bolt Solid Plate Fasteners penetrate well into the belt carcass, ensuring a firm grip and reliable repair. Choosing high-quality fasteners tailored to the specific belt type and operational demands enhances the longevity of the repaired belt and prevents future issues.
Case Studies and Solutions for Conveyor Belt Tear
The challenge of addressing a conveyor belt tear is multifaceted, impacting not only the immediate operational capacity but also long-term productivity and safety. Through detailed case studies and the exploration of innovative repair techniques, we can uncover effective strategies for both responding to and preventing these issues.
Conveyor Belt Problems and Solutions
A wealth of knowledge can be found in resources that compile case studies focusing on conveyor belt tear issues. These documents provide a detailed examination of three common problems associated with torn conveyor belts and offer actionable solutions tailored to address the nuances of different types of tears and their underlying causes.
Sharp Object Penetration: One case study from ConveyorTech Inc. details an incident where a sharp object penetrated the conveyor belt, causing a significant tear. This issue was identified during routine operations when the belt suddenly halted. Upon inspection, maintenance teams discovered that a piece of metal debris had lodged itself into the belt, creating a large tear. The solution involved implementing a scheduled inspection regime to identify and remove potential hazards from the belt’s path. Additionally, the company installed metal detectors at key points along the conveyor to catch foreign objects before they could cause damage.
Overloading: Another case from BeltMaster Industries explores how excessive load caused the belt to stretch and tear. In this instance, the conveyor belt was regularly subjected to loads beyond its specified capacity, leading to gradual wear and eventually a catastrophic tear. The solution focused on optimizing load distribution and installing sensors to monitor for overloading conditions. The company recalibrated its loading protocols, ensuring that each load was within safe limits, and installed real-time load monitoring systems to provide early warnings of potential overloads.
Material Build-up: A third study from TransBelt Solutions examines how material build-up at transfer points led to belt misalignment and subsequent tearing. In this scenario, accumulation of materials at transfer points caused the belt to deviate from its intended path, creating friction and eventual tears. The solutions implemented included the installation of improved cleaning systems to regularly clear build-up and redesigning transfer points to minimize accumulation. Maintenance teams also received training on the importance of keeping these areas clean and regularly inspecting for potential build-up.
Each case study from these companies provides insights into the diagnostic process, the selection of repair methods, and the outcomes of the implemented solutions, offering valuable lessons for maintenance teams. These detailed accounts highlight the importance of proactive maintenance and the implementation of preventive measures to ensure the longevity and efficiency of conveyor belt systems.
Innovative Repair Techniques
In response to the persistent issue of conveyor belt tears, several innovative repair techniques have been developed, focusing on efficiency, durability, and minimal operational disruption.
Conveyor Belt Repair Clips: These clips offer a fast and reliable method for bridging tears in the belt. Easy to install, they can significantly reduce downtime by providing a temporary or even semi-permanent fix until a more comprehensive repair can be undertaken.
High-Durability Materials: Utilizing materials engineered to withstand the rigors of conveyor operations can prevent tears from occurring in the first place. For example, belts made from reinforced rubber or with a high-grade polyurethane cover can offer enhanced resistance to sharp objects and heavy loads.
Advanced Adhesive Techniques: Modern adhesives and sealants provide a strong, flexible bond that can seal tears and prevent them from spreading. These materials are designed to cure quickly and adhere strongly to a variety of belt materials, ensuring a durable repair that can withstand the demands of continuous operation.
By examining these case studies and innovative repair techniques, organizations can better understand the complexities of conveyor belt torn issues and adopt effective strategies to mitigate risks, enhance safety, and improve operational efficiency.
Ready to upgrade your conveyor system? Contact us for belt solutions.
FAQs about Conveyor Belt Tear
A conveyor belt rip refers to a longitudinal tear in the belt material, typically caused by the impact of sharp objects or the entrapment of materials between the belt and conveyor components. Unlike surface wear or punctures, a rip often runs parallel to the length of the belt and can cause significant operational disruptions. Conveyor belt rips pose a serious risk to the safety and efficiency of conveyor operations, as they can lead to sudden belt failures, resulting in unplanned downtime and potential damage to the conveyor system and the materials being transported. Identifying the causes and implementing effective preventive measures, such as regular inspections, proper alignment, and the use of rip detection systems, are critical for minimizing the risk of conveyor belt rips.
If a conveyor belt breaks, it can lead to immediate cessation of the conveyor system’s operations, causing disruptions in production and potential delays in the supply chain. Depending on the severity of the break, the conveyor system may require a complete shutdown to assess the damage and perform the necessary repairs or replacements. This can result in significant downtime, affecting productivity and potentially leading to financial losses. Additionally, a broken conveyor belt can pose safety risks to workers, especially if the break occurs suddenly and materials are dislodged or fall from the conveyor. In the worst-case scenario, a broken belt can also cause damage to other parts of the conveyor system, such as rollers, frames, and drive mechanisms, leading to more extensive repairs and higher costs. Prompt and effective response to a broken conveyor belt is crucial to minimize downtime, ensure safety, and maintain operational efficiency.
A conveyor belt can rip due to several factors, each contributing to the weakening and eventual tearing of the belt material. One of the primary causes is the impact from sharp or heavy objects that are dropped onto the belt, which can puncture or slice through the belt material, leading to a rip. Another common cause is the entrapment of materials or small objects between the conveyor belt and the pulleys or rollers, which can create a point of stress that eventually tears the belt. Over time, wear and tear from regular use can also degrade the belt material, making it more susceptible to ripping. Additionally, improper installation or alignment of the conveyor system can cause uneven wear on the belt, increasing the likelihood of a rip. Environmental factors, such as exposure to extreme temperatures, chemicals, or UV light, can also weaken the belt material over time. Understanding these causes is crucial for implementing preventive measures to reduce the risk of conveyor belt rips.
Fixing a tear in a conveyor belt involves several steps, depending on the size and severity of the tear. For small punctures or tears, a patch repair can be an effective solution. This involves cleaning the damaged area, applying a strong adhesive, and then placing a patch of the same conveyor belt material over the tear, ensuring it bonds well to prevent further damage. For larger tears, especially those that span a significant length of the belt, a more extensive repair may be necessary. This could involve the use of mechanical fasteners or vulcanization, a process where heat and pressure are applied to splice the torn sections together, creating a durable and seamless repair. In some cases, particularly when the damage is extensive or the belt is significantly worn, replacing the entire section of the belt may be the most practical solution. Regardless of the method chosen, it’s essential to address tears promptly to prevent further damage and ensure the safety and efficiency of the conveyor system.
Last Updated on June 20, 2024 by Jordan Smith
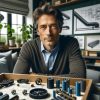
Jordan Smith, a seasoned professional with over 20 years of experience in the conveyor system industry. Jordan’s expertise lies in providing comprehensive solutions for conveyor rollers, belts, and accessories, catering to a wide range of industrial needs. From initial design and configuration to installation and meticulous troubleshooting, Jordan is adept at handling all aspects of conveyor system management. Whether you’re looking to upgrade your production line with efficient conveyor belts, require custom conveyor rollers for specific operations, or need expert advice on selecting the right conveyor accessories for your facility, Jordan is your reliable consultant. For any inquiries or assistance with conveyor system optimization, Jordan is available to share his wealth of knowledge and experience. Feel free to reach out at any time for professional guidance on all matters related to conveyor rollers, belts, and accessories.