High Quality HR Rubber Belt for Heat Resistance
HR (Heat Resistant) rubber belts are specially designed conveyor belts manufactured using high-performance rubber compounds that provide exceptional resistance to both heat and oil. These belts are ideal for transporting a wide variety of materials that are exposed to high temperatures or may contain oil residues. HR rubber belts are commonly used in industries where materials such as sinter, coke, phosphate, and clinker need to be conveyed at elevated temperatures, typically over 60°C.
The heat-resistant properties of HR belts allow them to handle materials with temperatures exceeding 65°C, making them suitable for applications where the temperature of the conveyed material can reach up to 150°C for coarse materials, and up to 110°C for finer materials. These belts are widely recognized across industries such as cement, steel, mining, and power generation, where high-temperature environments are common.
Manufacturers of HR rubber conveyor belt ensure that their products meet the stringent requirements for bulk material handling, offering robust performance and longevity. These belts are designed not only to withstand high heat but also to provide excellent durability, ensuring efficient material transportation even under the most challenging conditions. Whether it’s hot slag, clinker, or other high-temperature materials, HR rubber belts provide reliable, safe, and efficient conveyance solutions for various industrial applications.
Types of HR Rubber Belts and Their Applications
Heat-resistant (HR) rubber belts are designed specifically to withstand high temperatures, making them essential in industries where materials are transported at elevated temperatures. These belts are categorized based on their temperature resistance and are used in various industrial applications that involve handling hot materials.
HR Belt Grades
HR – T1: Suitable for Temperatures Up to 120°C
Description: HR – T1 grade belts are the most basic heat-resistant belts, capable of handling material temperatures up to 120°C. They are typically used in industries where the materials are moderately hot but not exposed to extreme temperatures.
Applications:
HR – T2 / SHR (Super Heat Resistant): Suitable for Temperatures Up to 150°C
Description: HR – T2 and SHR belts are designed for environments where materials exceed the heat tolerance of the T1 grade, but still remain within a high-heat range. These belts are built with enhanced heat resistance properties and durability.
Applications:
HR – T3 / UHR (Ultra Heat Resistant): Suitable for Temperatures Up to 200°C
Description: HR – T3 or UHR belts are designed for extremely high-temperature applications. They provide superior heat resistance, capable of handling materials at temperatures up to 200°C without compromising belt integrity.
Applications:
HR Rubber Belt Sizes: Choosing the Right Size for Your Application
When selecting an HR (Heat Resistant) rubber belt for industrial applications, it is essential to consider the correct size to ensure maximum performance, efficiency, and durability. HR rubber belts come in a variety of standard sizes, but custom sizes are also available to suit specific requirements. Here’s an in-depth look at the common sizes, how to choose the right size, and the benefits of tailored solutions.
Common Sizes of HR Belts
HR rubber belts are available in different widths, thicknesses, and lengths. The size of the belt is crucial as it determines how much material can be transported, the efficiency of the conveyor system, and the durability of the belt itself.
- Width:
Standard Widths: Common HR belt widths range from 300 mm (12 inches) to 2400 mm (96 inches), with increments in between. The width of the belt is typically chosen based on the volume of materials to be conveyed and the width of the conveyor system.
Typical Applications: For smaller, low-volume operations, narrower belts (300 mm to 600 mm) may be sufficient, while wider belts (1200 mm to 2400 mm) are required in industries with higher throughput, such as mining or cement plants.
- Thickness:
Standard Thicknesses: HR belts generally come in thicknesses ranging from 6 mm to 20 mm, depending on the material and the specific needs of the application. Thicker belts are typically used in environments where the materials being conveyed are heavy or abrasive, or when the belt will be exposed to higher temperatures and stress.
Choosing the Right Thickness: The thickness of the HR rubber belt should match the weight of the material being conveyed, as well as the expected wear and tear. For example, a belt conveying hot clinker at 200°C will require a thicker, more durable rubber to withstand the constant heat and abrasiveness.
- Length:
Standard Lengths: The length of HR rubber belts can vary greatly, typically ranging from 20 meters to 100 meters or more. Belt lengths are often determined by the dimensions of the conveyor system, including the distance between loading and unloading points. Understanding the uses of belt conveyor system is crucial in selecting the appropriate belt length to ensure smooth material transport.
Custom Lengths: Depending on the conveyor system, custom lengths can be manufactured to ensure a seamless fit. Long conveyor systems, such as those in mining or bulk material handling, may require continuous belts of greater length.
Custom Sizes and Tailoring Based on Industrial Needs
While standard sizes meet most basic needs, there are many instances where customized HR rubber belts are required. Industrial operations often have specific needs based on their material types, temperature conditions, and conveyor system configurations.
How to Choose the Right Size for Your Application
Choosing the correct size HR rubber belt for your application is crucial for ensuring optimal performance and longevity. Here are the key factors to consider:
- Material and Temperature:
Determine the type of material being conveyed (e.g., clinker, coke, molten metal, etc.) and the temperature of the material. The higher the temperature and abrasiveness, the thicker and more durable the belt needs to be. For instance, conveying materials at temperatures above 200°C requires belts with thicker layers of heat-resistant rubber. - Conveyor System Design:
The dimensions of your conveyor system, including the width, length, and distance between loading and unloading points, will influence the size of the HR rubber belt needed. Ensure that the belt’s width matches the trough or conveyor frame size, and that the length matches the required distance for material transport. - Material Handling Capacity:
Evaluate the material handling capacity of your conveyor system. Heavier and more abrasive materials typically require wider, thicker belts to prevent slippage, excessive wear, and potential breakdowns. If the material volume is high, selecting a wider belt is essential for efficient material handling. - Environmental Conditions:
Consider the environment in which the belt will be operating. High-temperature environments, exposure to chemicals, or outdoor operations where moisture and dust are prevalent can influence the type and size of the HR belt needed. For example, conveyor belt used in steel mills or power plants may require belts designed not only for heat resistance but also for impact resistance and flexibility. - Speed of Operation:
The speed at which the conveyor operates can also impact the size of the HR belt. Faster conveyor systems may require stronger, more flexible belts to ensure material is conveyed effectively without excessive wear.
HR Rubber Belt Price: Understanding Cost Factors and Price Estimates
When purchasing HR (Heat Resistant) rubber belts for industrial applications, it’s essential to understand the factors that influence their price. The price of an HR rubber belt can vary significantly based on several key factors, including material quality, size, temperature resistance, and any customizations required. Here’s a detailed breakdown of what affects the price of HR rubber belts and how to estimate costs.
Factors Affecting Price
Several factors contribute to the overall cost of HR rubber belts, and understanding these variables will help you make informed purchasing decisions.
The quality of the rubber used in the manufacturing of the belt is one of the most significant factors affecting price. Higher-quality materials, such as premium natural rubber and heat-resistant compounds, will cost more but offer better durability, flexibility, and resistance to heat and abrasion. Belts with high-quality materials are more effective in extreme environments and have a longer lifespan, reducing the overall maintenance costs.
Higher-grade belts: These typically feature superior heat resistance and impact protection, making them more expensive, but they can handle more demanding applications (e.g., industrial environments with extreme temperatures).
The size of the HR rubber belt is another crucial price determinant. Wider belts (e.g., 1200 mm to 2400 mm) typically cost more than narrower belts (e.g., 300 mm to 600 mm) due to the increased amount of raw material required to manufacture them.
Thickness and length: Thicker belts (6 mm to 20 mm) or longer belts (more than 100 meters) also tend to be more expensive. These belts are designed to withstand higher levels of wear and tear, and their production often requires more materials and labor.
HR rubber belts come in different grades, each designed to withstand specific temperature ranges. Belts designed for higher temperature resistance will be priced higher due to the specialized materials and manufacturing processes used to produce them.
Higher-grade belts: For example, belts rated for higher temperature ranges require advanced heat-resistant compounds and enhanced durability, making them more expensive than those designed for lower temperature environments.
Customization of HR rubber belts, such as adjusting the width, length, thickness, or adding special coatings, can add to the price. Belts designed to handle unique materials or environments—such as belts with additional reinforcements, impact resistance, or chemical-resistant coatings—are generally more expensive.
Bespoke options: Some applications may require custom-shaped belts, special edging, or specific fabric grades, which further increases the cost. Tailored solutions are ideal for industries with specific requirements (e.g., foundries, steel mills) but are more expensive than off-the-shelf products.
Price Ranges and Cost Considerations
HR rubber belts come in a wide price range depending on the specifications and supplier. Here’s an overview of what to expect in terms of cost.
- Standard HR Rubber Belts:
For lower temperature resistance grades (up to 120°C), basic HR belts can start at around $5 to $15 per meter, depending on the size and thickness.
Medium-Grade HR Belts (up to 150°C): Prices for these belts generally range from $10 to $30 per meter, depending on the width, length, and thickness. - High-Temperature Resistant HR Belts (up to 200°C):
For HR belts designed for high temperatures, prices typically range from $20 to $50 per meter. These belts are often used in environments like steel manufacturing, foundries, or cement production. - Ultra-Heat Resistant Belts (up to 300°C):
HR rubber belts designed to withstand the highest temperatures can cost anywhere from $50 to $100+ per meter depending on the grade, customization, and quantity ordered. These belts offer the highest level of protection against heat and abrasion, making them ideal for the most demanding environments. - Additional Costs:
Shipping and Handling: The shipping cost for HR rubber belts can vary based on the size of the order, delivery location, and urgency of delivery. Large orders or international shipping can increase the total cost significantly. - Installation and Maintenance: If your supplier provides installation services, these costs will also need to be factored into the total price. Additionally, the maintenance of HR rubber belts may require periodic checks or replacements, which adds to the long-term cost.
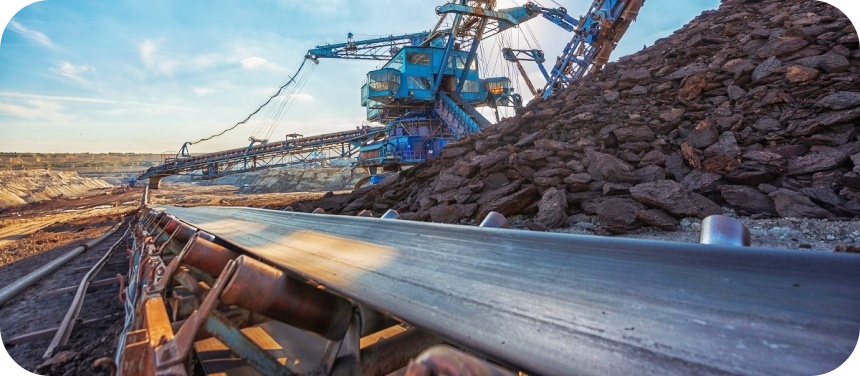
How to Get a Quote from Suppliers
To obtain an accurate price quote for HR rubber belts, it’s essential to reach out to suppliers with detailed information about your requirements. Here’s a simple guide on how to get a quote:
Provide Specific Requirements:
- Material Type: Specify the type of HR rubber belt you need (e.g., up to 120°C, 150°C, or higher temperature resistance).
- Dimensions: Include the required width, thickness, and length of the belt. Be as precise as possible to ensure that the quote reflects the correct specifications.
- Temperature Resistance: Indicate the temperature range that the belt needs to withstand.
- Quantity: Provide an estimate of the quantity required, as larger orders often qualify for discounts.
- Customizations: If you require special customizations (e.g., special coatings, fabric reinforcements), mention them upfront to get an accurate price.
-
Request Bulk Discounts:
If you are ordering HR rubber belts in bulk, inquire about discounts. Suppliers often offer price reductions for large orders or long-term contracts, which can significantly lower the cost per unit. - Shipping and Delivery Terms:
Request information on shipping options, delivery times, and associated costs. Some suppliers may include free shipping for large orders, while others may offer expedited shipping for an additional charge. - Warranty and After-Sales Service:
Ask about warranty terms and after-sales support. A good warranty can provide peace of mind, especially when dealing with high-temperature, high-performance products. - Comparison Shopping:
It’s always a good idea to compare quotes from multiple suppliers to ensure you’re getting the best price. Make sure to evaluate the overall value, including material quality, customization options, and after-sales services, rather than just the initial price.
HR Rubber Belt for Sale: Where to Buy and What to Consider
When you’re in the market for HR (Heat Resistant) rubber belts, finding a reliable supplier is crucial to ensure that you get the best quality product for your application. Whether you’re purchasing belts for bulk material handling, high-temperature environments, or any other industrial use, understanding where to buy and the benefits of purchasing from trusted suppliers can make a significant difference in both product performance and cost-effectiveness.
Where to Buy HR Rubber Belts
Leading Manufacturers and Suppliers:
The best place to start when looking to buy HR rubber belts is directly from reputable manufacturers and suppliers. Leading manufacturers of HR rubber belts often offer high-quality products that meet industry standards and can be customized to fit specific needs. These suppliers typically produce belts designed to withstand varying temperature ranges, ensuring that you get a belt that suits your specific industrial applications.
Some key suppliers are known for their expertise in rubber belt manufacturing, offering a range of products that meet specific performance criteria, such as heat resistance and abrasion resistance. Many of these manufacturers have years of experience serving industries like mining, cement, steel, and power plants, where durable, heat-resistant conveyor belts are a necessity.
Online and Offline Purchasing Options:
Local and International Suppliers:
Depending on your location, you may find that purchasing HR rubber belts from a local supplier is more convenient and cost-effective, especially for smaller orders or when fast delivery is necessary. Local suppliers can offer reduced shipping costs and quicker delivery times.
For larger industrial projects, international suppliers may offer competitive prices or higher-quality belts, but shipping times and costs can be higher. Be sure to check for any import duties or regulations that could impact the total cost of the belts when ordering from abroad.
Benefits of Buying from Trusted Suppliers
When selecting a supplier for your HR rubber belts, buying from a trusted and reliable source can offer several key benefits that contribute to both the short-term success and long-term durability of your investment.
Trusted suppliers will ensure that their HR rubber belts meet high industry standards for heat resistance, durability, and performance. They typically follow recognized manufacturing standards and use quality raw materials to ensure the belts last in challenging industrial environments.
Established suppliers often provide certifications or guarantees that their products meet national or international quality standards, which helps to reassure customers that they are purchasing reliable, high-quality products.
A warranty is one of the most significant advantages of purchasing from a trusted supplier. A warranty assures you that if there is any issue with the HR rubber belt—such as manufacturing defects, early wear, or performance issues—you can return or replace the product without incurring additional costs.
Warranties also offer peace of mind, especially when purchasing high-temperature-resistant belts, which may be used in harsh environments where performance is critical.
Reputable suppliers usually provide strong customer support throughout the purchasing process and beyond. This includes providing technical assistance, helping you select the right belt for your application, and offering after-sales support such as installation advice or maintenance recommendations.
Additionally, trusted suppliers often have dedicated customer service teams that can assist with troubleshooting issues, processing returns, and providing guidance on belt maintenance to ensure long-term product longevity.
Purchasing from a well-known supplier usually means you can expect more reliable delivery times. These suppliers often have established logistics networks, which ensures that products arrive on time and in the correct condition.
On-time delivery is particularly important in industrial settings where downtime can be costly. Working with a supplier that has a reputation for delivering products quickly and efficiently can help reduce potential delays in production.
Establishing a long-term relationship with a trusted supplier can lead to several additional benefits. For example, suppliers who understand your specific needs can offer personalized recommendations for future purchases, provide discounts for repeat business, or even offer priority service for urgent orders.
Over time, building a relationship with a supplier allows you to gain insight into new product developments, alternative solutions, and future innovations in HR rubber belts and related technologies.
Where to Find Trusted HR Rubber Belt Suppliers
Attending industry-specific trade shows or expos is a great way to meet trusted suppliers face-to-face. These events allow you to learn more about the latest products, innovations, and trends in HR rubber belts, while also establishing direct connections with manufacturers and distributors.
Industry Associations and Directories:
Many industries have associations or directories where reputable suppliers of HR rubber belts are listed. These associations often maintain lists of approved or certified suppliers, making it easier to find trusted vendors who meet industry standards.
Well-established online marketplaces can connect you with verified suppliers of HR rubber belts. Many of these platforms allow you to check the supplier’s reviews, ratings, and past customer feedback before making a purchase.
Referrals and Recommendations:
One of the best ways to find a reliable supplier is through recommendations from other businesses or industry peers who have experience with HR rubber belts. Referrals from companies with similar industrial needs can help you find suppliers who are proven to deliver quality products and services.
Conveyor Belt Specification Standards: Importance, Compliance, and How to Access Detailed PDF Specifications
When it comes to purchasing HR (Heat Resistant) rubber belts, understanding and adhering to conveyor belt specification standards is crucial for ensuring performance, safety, and reliability. Conveyor belt standards are designed to provide guidelines for the construction, material composition, and application of belts used in various industries, particularly those subjected to high temperatures or abrasive environments. This section provides an overview of key conveyor belt specification standards, why they matter, and how you can access detailed specifications for HR rubber belts.
Key Conveyor Belt Specification Standards (IS 1891 Part II)
One of the most widely recognized and accepted standards for heat-resistant conveyor belts is IS 1891 Part II, which is an Indian Standard that defines the requirements for heat-resistant belts. This standard is especially important for belts used in industries dealing with high-temperature materials such as cement, steel, and power plants.
IS 1891 Part II – HR Belts:
- Scope: This part of the standard specifies the construction, testing methods, and performance characteristics for heat-resistant conveyor belts. It applies to belts designed to convey materials at elevated temperatures, which may be exposed to conditions of heat and abrasion during operation.
- Grades of Heat Resistance: The standard categorizes HR belts into different grades based on their maximum heat tolerance, such as:
- HR (Heat Resistant) Type T1: Suitable for temperatures up to 120°C.
- HR (Heat Resistant) Type T2: Suitable for temperatures up to 150°C.
- HR (Heat Resistant) Type T3: Suitable for temperatures up to 200°C.
- Material and Construction Requirements: The standard outlines the specific materials used for manufacturing the belts, including natural rubber and synthetic compounds, designed to resist degradation due to high heat exposure.
- Testing: The standard defines testing methods for performance characteristics like heat resistance, tensile strength, elongation at break, and abrasion resistance.
Other Relevant Standards:
Different industries may have specific standards or regulations that further detail the requirements for conveyor belts used in their operations. For example, the mining, cement, and steel industries may have additional performance criteria due to the harsh operating conditions in these sectors.
Compliance and Industry Standards for HR Rubber Belts
Compliance with international and national standards is essential to ensure that HR rubber belts perform efficiently, maintain safety, and last longer under extreme operating conditions. These standards help manufacturers design belts that can withstand high temperatures, heavy loads, and abrasion while minimizing the risk of breakdowns or accidents.
- Safety and Performance:
Belts manufactured in accordance with these standards are more reliable in terms of performance. For example, heat-resistant belts meeting the IS 1891 Part II standards are specifically engineered to handle temperatures beyond 65°C, reducing the risk of belt failure in environments where high heat is present.
The construction of HR rubber belts adhering to these standards ensures that belts can endure the mechanical stresses and temperature fluctuations typical in industries such as power generation, mining, and cement production. - Quality Assurance:
Compliance with recognized standards like IS 1891 Part II or ISO 9001 ensures that HR rubber belts undergo strict quality assurance tests. These tests verify the mechanical properties, heat resistance, and durability of the belts, which is critical in preventing costly downtime due to conveyor belt failure. Understanding the causes of conveyor belt failure helps in identifying potential weaknesses, ensuring better maintenance and performance over time.
Certified suppliers who adhere to these standards offer better reliability and product longevity, making them ideal partners for industries with demanding operations. - Industry-Specific Regulations:
Certain industries, such as food processing, pharmaceuticals, and hazardous material handling, may require additional regulatory compliance when it comes to selecting conveyor belts. In these cases, belts may need to meet hygiene, chemical resistance, or fire-retardant standards
Why Standards Matter for Performance and Safety
Adhering to conveyor belt specification standards plays a vital role in ensuring both the performance and safety of the equipment. Here are some of the key reasons why standards matter:
By following established standards, HR rubber belts maintain consistent performance across different suppliers and manufacturers. This helps ensure that the belts perform reliably under high temperatures, reducing the likelihood of unexpected failures or operational interruptions.
Heat-resistant belts used in high-temperature environments must meet stringent safety standards to prevent risks such as fire, belt rupture, or dangerous material spillage. Standards like IS 1891 Part II outline the minimum safety requirements for HR belts, ensuring they are safe to use in potentially hazardous environments.
HR rubber belts built to meet specific standards are more durable and have a longer service life. This reduces the overall cost of maintenance and replacement and ensures that belts perform optimally even in extreme conditions.
In many industries, meeting conveyor belt specification standards is not just about performance but also about regulatory compliance. Adhering to industry standards helps businesses avoid fines or regulatory issues, ensuring their operations remain legally compliant.
Downloading Conveyor Belt Standards (PDF)
Accessing detailed conveyor belt specification standards, including HR rubber belts, is simple and can usually be done through official standards organizations, manufacturers, or technical documentation platforms. Below are a few ways to access these standards in PDF format:
National standards bodies like the Bureau of Indian Standards (BIS), ISO, or DIN provide access to the latest specification documents in PDF format. These bodies typically charge a nominal fee for accessing their standards, but their official documents offer the most accurate and up-to-date specifications.
Many HR rubber belt manufacturers and suppliers provide detailed product specifications, including compliance with various industry standards, on their websites. These specifications may be available for download in PDF format for easy reference.
These documents can help you understand the specific grade of HR rubber belt that suits your needs and whether it complies with the relevant performance standards.
Industry associations for sectors like mining, cement, or steel often provide guidelines or specifications that reference relevant conveyor belt standards. Many of these associations make their standards available to members and non-members alike, usually in PDF format.
There are numerous online platforms and databases that offer access to standards documents, including PDF versions of various national and international specifications for conveyor belts.
Some suppliers provide technical documentation PDFs that include detailed specifications for HR rubber belts, including data on temperature resistance, tensile strength, and compliance with relevant standards. These documents are often available upon request or can be downloaded directly from the supplier’s product page.
How to Access Detailed PDF Specifications for Various HR Rubber Belts
FAQs about HR Rubber Belt
What is an HR conveyor belt?
An HR (Heat Resistant) conveyor belt is a type of industrial conveyor belt specifically designed to handle materials at elevated temperatures. These belts are made from materials that have enhanced heat-resistant properties, allowing them to convey hot materials without degrading or losing performance. HR conveyor belts are commonly used in industries like cement manufacturing, steel production, mining, and power generation, where conveyor systems are required to transport materials such as clinker, coke, or molten slag, which are exposed to high temperatures during processing.
HR belts are typically constructed using specially formulated rubber compounds that can withstand the stresses of high heat while maintaining their flexibility, strength, and resistance to abrasion. Depending on the grade, these belts can endure temperatures ranging from 120°C to 250°C, making them suitable for a wide range of applications involving hot material handling. It’s essential to choose the right grade of HR belt based on the specific temperature requirements of your operation to ensure optimal performance and avoid premature wear or failure of the belt.
What is the full form of HR rubber?
The full form of HR rubber is Heat Resistant rubber. It refers to a specialized type of rubber compound that is specifically engineered to withstand exposure to high temperatures without losing its structural integrity. Heat-resistant rubber is commonly used in the manufacturing of conveyor belts, gaskets, seals, and other components that need to function in environments where temperatures exceed the typical operational range for standard rubber products.
HR rubber is formulated with heat-resistant additives and compounds that prevent degradation, cracking, or hardening when subjected to elevated temperatures. It’s used in various industrial applications, including transporting hot materials, steam sealing, and equipment in furnaces, kilns, and ovens. HR rubber can handle temperatures ranging from 120°C to 250°C, depending on the grade and specific formulation. For conveyor belts, HR rubber plays a crucial role in ensuring that the belts can transport hot materials without failing due to heat exposure, thus improving the efficiency and safety of industrial operations.
What is the temperature range of HR belt?
The temperature range of an HR (Heat Resistant) conveyor belt depends on the specific grade and formulation of the rubber used. Typically, HR conveyor belts are classified into different grades based on their heat tolerance, which ensures that they can handle varying temperature conditions in industrial settings. The most common temperature ranges for HR belts are as follows:
HR Type T1: Suitable for temperatures up to 120°C. This grade is often used for materials that are exposed to moderate heat conditions, such as in cement plants or light industrial applications.
HR Type T2 (SHR): Suitable for temperatures up to 150°C. This grade is designed for industries where slightly higher heat exposure is expected, such as in the transportation of clinker, hot asphalt, or in some steel production processes.
HR Type T3 (UHR): Suitable for temperatures up to 200°C. This grade is used for more demanding applications where materials such as molten slag or hot minerals are being transported.
Special High-Temperature Grades (Pyroshield series): These belts can withstand even higher temperatures, up to 250°C and 300°C, and are used in extremely high-heat environments, such as in certain metal industries or waste incineration plants.
CONTACT US
Let us help you find a better solution!